Haeryong Jeon1, Jeyull Lee1, Seunghak Han1, Ji Hyung Kim2, Chang Ju Hyeon2, Ho Min Kim2, Yoon Do Chung3, Tae Kuk Ko1 and Yong S
Total Page:16
File Type:pdf, Size:1020Kb
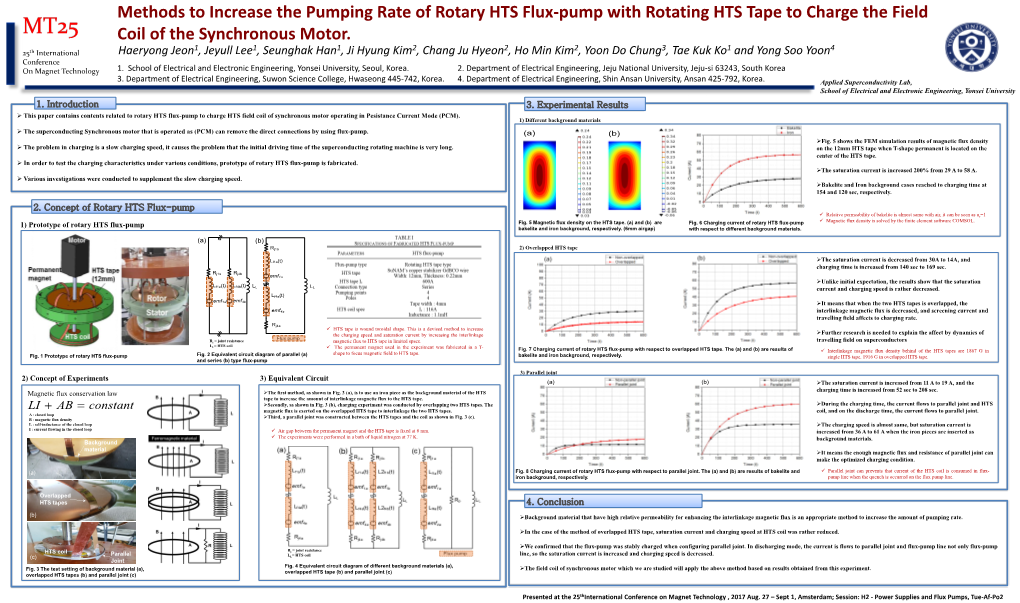
Load more
Recommended publications
-
Living in Korea
A Guide for International Scientists at the Institute for Basic Science Living in Korea A Guide for International Scientists at the Institute for Basic Science Contents ⅠOverview Chapter 1: IBS 1. The Institute for Basic Science 12 2. Centers and Affiliated Organizations 13 2.1 HQ Centers 13 2.1.1 Pioneer Research Centers 13 2.2 Campus Centers 13 2.3 Extramural Centers 13 2.4 Rare Isotope Science Project 13 2.5 National Institute for Mathematical Sciences 13 2.6 Location of IBS Centers 14 3. Career Path 15 4. Recruitment Procedure 16 Chapter 2: Visas and Immigration 1. Overview of Immigration 18 2. Visa Types 18 3. Applying for a Visa Outside of Korea 22 4. Alien Registration Card 23 5. Immigration Offices 27 5.1 Immigration Locations 27 Chapter 3: Korean Language 1. Historical Perspective 28 2. Hangul 28 2.1 Plain Consonants 29 2.2 Tense Consonants 30 2.3 Aspirated Consonants 30 2.4 Simple Vowels 30 2.5 Plus Y Vowels 30 2.6 Vowel Combinations 31 3. Romanizations 31 3.1 Vowels 32 3.2 Consonants 32 3.2.1 Special Phonetic Changes 33 3.3 Name Standards 34 4. Hanja 34 5. Konglish 35 6. Korean Language Classes 38 6.1 University Programs 38 6.2 Korean Immigration and Integration Program 39 6.3 Self-study 39 7. Certification 40 ⅡLiving in Korea Chapter 1: Housing 1. Measurement Standards 44 2. Types of Accommodations 45 2.1 Apartments/Flats 45 2.2 Officetels 46 2.3 Villas 46 2.4 Studio Apartments 46 2.5 Dormitories 47 2.6 Rooftop Room 47 3. -
Vol. 27 (T1) 2019 Vol
Pertanika Journal of Social Sciences & Humanities Vol. 27 (T1) 2019 Journal of Social Sciences & Humanities Contents Forward i Abu Bakar Salleh The Effect of Brand Equity and Perceived Value to Marketing Mix 1 Faransyah Jaya, Muhtosim Arief, Pantri Heriyati and Dyah Budiastuti Enhancing the Employability of Graduates through an Industry-led 11 Initiative Nora Zakaria and Ramesh Nair A Comparison of Customer Attendance Motivations at Victoria Park and 27 Manning Farmers’ Markets, Perth, Western Australia Mark Azavedo and John Walsh 45 Exploratory Approach Journal of Social Sciences & Humanities Sun-Hae Hyun, Moon-Kyo Seo and Se Kyung Choi Impact of Product Costing for Branding and Business Support on Small 59 and Medium Enterprises in Malaysia 27 (T1) 2019 Vol. Diana Rose Faizal, Zariyawati Mohd Ashhari, Norazlina Kamarohim and Annuar Md Nassir Establishing Green Practice Constructs among Secondary School 75 Hanifah Mahat, Nasir Nayan, Yazid Saleh, Mohmadisa Hashim and Siti Mariam Shahirah Haron Underlying Structure of Job Competency Scale in Climate-Smart 93 Agricultural Extension Service Sulaiman Umar, Norsida Man, Nolila Mohd Nawi, Ismail Abd. Latif and Bashir Garba Muktar Practiced Culture toward Firm Competitiveness Performance: Evidence 113 from Indonesia VOL. 27 (T1) 2019 Journal of Social Sciences & Humanities Prio Utomo and Dyah Budiastuti Thematic Edition Survival through Strategic Performance Measurement System in Coal 125 Mines Nandang Sukmana, Sri Bramantoro Abdinagoro and Dyah Budiastuti Management Studies Pertanika Editorial Oce, Journal Division Oce of the Deputy Vice Chancellor (R&I) 1st Floor, IDEA Tower II UPM-MTDC Technology Centre Universiti Putra Malaysia 43400 UPM Serdang Selangor Darul Ehsan Malaysia http://www.pertanika.upm.edu.my/ E-mail: [email protected] Tel: +603 8947 1622 Journal of Social Sciences & Humanities About the Journal Overview Pertanika Journal of Social Sciences & Humanities (JSSH) is the official journal of Universiti Putra Malaysia published by UPM Press. -
DAEJIN KIM Assistant Professor Department of Interior Design College of Design 158 College of Design Ames, IA, 50010-3091 352-226-4064 [email protected]
CURRICULUM VITAE DAEJIN KIM Assistant Professor Department of Interior Design College of Design 158 College of Design Ames, IA, 50010-3091 352-226-4064 [email protected] I. INFORMATION Education 2016 Doctor of Philosophy in Design, Construction and Planning Concentration in Interior Design, College of Design, Construction and Planning Minor in Research Evaluation Methodology Concentration in Quantitative Methods, College of Education University of Florida, Gainesville, FL, USA Dissertation: “Toward Design Strategies for Fall Prevention: A Case-Control Study of Home Safety in A Senior Living Community” 2010 Master of Science in Housing & Interior Design College of Human Ecology, Yonsei University, Seoul, South Korea Thesis: “Planning for Healing Environment Through Evidence-Based Design : Focusing on Geriatric Hospital” 2008 Bachelor of Science in Engineering (Architecture Engineering) College of Engineering, Inha University, Incheon, South Korea Professional Experience 2018- Assistant Professor Department of Interior Design, College of Design, Iowa State University, Ames, IA Gerontology Graduate Program (affiliated faculty) Human Computer Interaction Graduate Program (affiliated faculty) 2017- Post-Doctoral Research Fellow of Housing Research 2018 Department of Family and Consumer Sciences, North Carolina Agricultural and Technical State University, Greensboro, NC, USA DAEJIN KIM, PhD., CURRICULUM VITAE Page 1 of 12 2012 Lecturer Spring Department of Interior Design, Shin Ansan University, Ansan, South Korea 2010- Design Researcher 2012 Urban Research Lab, Seoul Housing & Communities Corporation, Seoul, South Korea 2001- Interior Designer 2003 Ol Design Studio, Seoul, South Korea Licensure / Certification Certified Aging in Place Specialist (CAPS) National Association of Home Builders Evidence-Based Design Accreditation & Certification (EDAC), CHD-102886 The Center for Health Design LEED Green Associate, # 0011090733 U.S. -
A Study on the Relationship Between the Community 生活-その実態と支援・相談の方向性-
Asian Journal of Printed 2012.0430 ISSN2186-3350 HUMAN Published by Asian Society of Human Services April 2012 SERVICES VOL.2 Asian Society of Human Services Human Asian Journal of Human Services , VOL.2 29-37 活の質(QOL)に関する研究-性別による活動群と非活動群からの比較検討-. 共栄 Services 学園短期大学研究紀要, 23, 111-125. ORIGINAL ARTICLE 3 5) 町田一男・原美智子・松田直・永井真紀・太田裕子 (2004) 知的障害養護学校卒業後の A Study on the Relationship between the Community 生活-その実態と支援・相談の方向性-. 群馬大学教育実践研究, 21, 261-273. Organizing Movement and the Emergence of Social 6) 宮本文雄・大野由三 (1996) 知的障害者(養護学校卒業生)の余暇活動に関する研究- 年齢の要因からの分析を通して-. 東京成徳大学研究紀要, 3, 163-176. Enterprise in Korea 7) 奥住秀之・國分充・橋本真規・北島善夫 (2008) 知的障害特別支援学校に通う高校生 -Focused on Relationship with Self-Sufficiency Project- における卒業後の労働と余暇に対する意識. SNE ジャーナル, 14, 90-107. 1) 8) 奥住秀之・國分充・北島善夫 (2010) 知的障害特別支援学校高等部生徒における卒業 Moon-Kuk LEE 後の労働と余暇に対する期待. SNE ジャーナル, 16, 85-96. 9) 奥住秀之・池田吉史・國分充 (2011) 知的障害特別支援学校生徒における労働期待感 1) Shin Ansan University, Dept. of Social Welfare. と学校生活充実度及び学習・生活スキルとの関連. アジア職業リハビリテーション研 671 Choji-dong, Danwon-gu, Ansan-city, Gyeonggi-do, Korea, 究, 1, 22-27. [email protected] ) 奥住秀之・國分充・北島善夫 知的障害特別支援学校高等部生徒の現在および 10 (2011) 卒業後の余暇活動 ジャーナル . SNE , 17, 161-173. 11) 高畑庄蔵・武蔵博文 (1997) 知的障害者の食生活,運動・スポーツ等の現状についての ABSTRACT 調査研究-本人・保護者のニーズの分析による地域生活支援のあり方-. 発達障害研 究, 19, 51-60. This article is intended to identify the relationship between various community organizing activities and the emergence of social enterprise in Korean society. That is to say, it is the emergence of social enterprise creating employment and supplying various social services in Korean society that is the historical outcome which has been created by community leaders' groups in the process of diverse community organizing activities. Their appearances are not in any sense an accident. -
Migration Profile of the Republic of Korea of Republic the of Profile Migration Migration Profile of the Migration Profile of the Republic of Korea Republic of Korea
Research Report IOM MRTC Research Report Series No. 2011-01 International Organization for Migration 2 0 1 1 - 0 1 IOM MRTC Research Report Series No. 2011-01 Migration Profile of the Republic of Korea Migration Profile of the Migration Profile of the Republic of Korea Republic of Korea Jung-Eun Oh·Dong Kwan Kang·Julia Jiwon Shin·Sang-lim Lee·Seung Bok Lee·Kiseon Chung www.iom-mrtc.org International Organization for Migration 9 3 3 0 0 1 3 9 7 8 8 9 9 7 1 1 8 1 6 8 9 7 7 2 2 3 3 8 9 2 0 0 4 ISBN 978-89-97118-16-8 ISSN 2233-8926 IOM 이민정책연구원 2010-2011년 IOM 이민정책연구원 연구보고서 시리즈 The Migration Research and Training Centre of the International Organization for Migration 2010-2011 IOM MRTC Research Report Series Republic of Korea 한국인의 국민정체성과 이민관련 태도 연구 (정기선, 이선미, 김석호, 이상림, 박성일) IOM 이민정책연구원(MRTC: Migration Research and Training Centre)은 대한민국정부와 국제이주기구(IOM)간 특별 2010 - 06 Korean National Identity and Migration-related Attitudes 협정에 의해 설립된 독립적인 연구교육기관입니다. 본원은 정부와 지역사회, 이민자 및 그 가족 모두에게 이익이 되도록 (Kiseon Chung, Seon Mi Lee, Seokho Kim, Sang-lim Lee, Seong Il Park) 정부의 이민정책 수립과 실행에 필요한 정보를 제공하고 개선하도록 돕습니다. 본원은 아시아 지역 및 세계 각국의 인구이동 대한민국 이민정책 프로파일 (오정은, 강동관, 신지원, 이상림, 이승복, 정기선) 추이와 시행중인 이민정책에 초점을 둠으로써 인적자원의 보다 자유로운 국제이동을 촉진하는데 기여할 것이며, 특히 한 2011 - 01 MigrationProfileoftheRepublicofKorea 국을 비롯한 아시아 지역에 대한 정책적 함의를 도출하고자 노력할 것입니다. 주요활동은 다음과 같습니다. -
Tue-Af-Po2.16-06 [20] with and Without Insulation Seunghak Han1, Haeryong Jeon1, Ho Min Kim2, Ji Hyung Kim2, Yoon Seok Chae2, Tae Kuk Ko1, and Yong Soo Yoon3 1
Charging Characteristics of HTS Coil by rotary HTS Flux Pump Tue-Af-Po2.16-06 [20] with and without Insulation Seunghak Han1, Haeryong Jeon1, Ho Min Kim2, Ji Hyung Kim2, Yoon Seok Chae2, Tae Kuk Ko1, and Yong Soo Yoon3 1. School of Electrical and Electronic Engineering, Yonsei University, Seoul, South Korea. 2. School of Electrical Engineering, Jeju National University, Jeju-si, South Korea. 3. School of Electrical Engineering, Shin Ansan University, Ansan-si, South Korea. September 24, 2019 from 14:00 PM to 16:00 PM Abstract III. Experimental Results • High-temperature superconducting (HTS) coils wound without turn-to-turn insulation (NI coils) show excellent electrical and thermal performance compared to HTS coils wound with Kapton tape (INS coils). However, charging the NI coils using a direct current (DC) power supply have a slower charging time than the INS coils. To A. Charging by power supply • overcome this slow charging time, research is underway to charge the NI coils using a flux pump, a DC voltage source, instead of a DC power supply. In this paper, we Fig. 4 shows the charging/discharging conducted experiments to compare the charging characteristics of INS and NI coils charging by a rotary HTS flux pump. A superconducting circuit consisting of the two experimental results of INS and NI coils using coils with the same magnitude of inductance is connected in series. As a result of the experiments, we compare the charging characteristics when a DC voltage source of P/S. • 퐈 was ramped at 0.5 and 1 A/s from 0 to the same value is applied to the two coils with a rotary HTS flux pump which is a contactless excitation rotary device. -
Cultural Laboratory Seoul
Research Collection Doctoral Thesis Cultural Laboratory Seoul. Emergence, Narrative and Impact of Culturally Related Landscape Meanings Author(s): Ahn, Susann Publication Date: 2019 Permanent Link: https://doi.org/10.3929/ethz-b-000415748 Rights / License: In Copyright - Non-Commercial Use Permitted This page was generated automatically upon download from the ETH Zurich Research Collection. For more information please consult the Terms of use. ETH Library CULTURAL LABORATORY SEOUL Emergence, Narrative and Impact of Culturally Related Landscape Meanings Susann Valerie Ahn Doctoral Thesis ETH Zürich 2019 2 Abstract The dissertation Cultural Laboratory Seoul examines landscape restoration projects in the South Korean capital Seoul, which have influenced the urban fabric of the Korean capital since the 1980s. The landscape restoration projects have been supported by a paradigm shift from growth-oriented to environment-oriented approaches in Korean urban planning. In this context, the Seoul Metropolitan Government has sought means to convey traditional, historical and natural values through landscape restoration. In consequence, Seoul’s landscape elements—mountains, rivers, and valleys—have been cleared of apartment buildings and urban infrastructure, and afterwards have been greened. The challenge in many of these landscape restoration projects, however, has been to convey the traditional landscape meaning of these sites while meeting today’s landscape architectural standards and requirements as well as the needs of citizens. In order to gain a deeper understanding of how to deal with these challenges, the dissertation examines existing landscape restoration projects such as the restoration of Namsan (1990–2000), the restoration of Naksan (1997–2002), and the restoration of Inwangsan’s Suseongdong Valley (2007–2012). -
Higher Education in Korea: Tradition and Adaptation Edited by John C
Higher Education in Korea garland studies in higher education volume 17 garland reference library of social sciences volume 1013 Garland Studies in Higher Education This series is published in cooperation with the Program in Higher Education, School of Education, Boston College, Chestnut Hill, Massachusetts. Philip G.Altbach, Series Editor Reform and Change The Liberal Arts College in Higher Education Adapting to Change International Perspectives The Survival of Small Schools edited by James E.Mauch by Gary Bonvillian and Paula L.W.Sabloff and Robert Murphy Higher Education in Crisis Higher Education in Canada New York in National Perspective Different Systems, edited by William C.Barba Different Perspectives China’s Universities, 1895–1995 edited by Glen A.Jones A Century of Cultural Conflict Sexual Harassment by Ruth Hayhoe in Higher Education Jesuit Education and Social Reflections and New Perspectives Change in El Salvador by Billie Wright Dziech by Charles J.Beirne and Michael W.Hawkins Dimensions of the University Teaching Community College International Perspectives International, Intercultural, edited by James J.F.Forest and Multicultural Perspectives Higher Education edited by Rosalind Latiner Rahy in the Post-Communist World and Norma Tarrow Case Studies of Eight Universities The Social Role edited by Paula L.W.Sabloff of Higher Education Two-Year Colleges Comparative Perspectives for Women and Minorities edited by Ken Kempner Enabling Access to the Baccalaureate and William Tierney Barbara Townsend Science and Technology in -
Use of PISA Results in Shaping Public Opinion on Education in South Korea 2000-2018
Use of PISA Results in Shaping Public Opinion on Education in South Korea 2000-2018 A Comparative Study of Two South Korean Newspapers Eunji Hyun Master’s Thesis in Comparative and International Education Department of Education Faculty of Educational Sciences UNIVERSITETET I OSLO June 2020 II Use of PISA Results in Shaping Public Opinion on Education in South Korea 2000-2018 A Comparative Study of Two South Korean Newspapers III © Eunji Hyun 2020 Use of PISA Results in Shaping Public Opinion on Education in South Korea 2000-2018: A Comparative Study of Two South Korean Newspapers Eunji Hyun http://www.duo.uio.no/ Print: Reprosentralen, University of Oslo IV Abstract The impact of International Large-Scale Assessments (ILSAs) is growing day by day around the world. Of these, the Programme for International Student Assessment (PISA) is particularly influential globally including in South Korea. Although the authority of PISA as a soft power is widespread and affects many countries, individual countries are not unconditionally affected but can consider and adopt PISA results according to their own logic and interests. This is the starting point for this thesis which focuses on South Korea. Of many local actors in South Korea, two leading newspapers were selected for analysis. From the perspective of externalization thesis, this thesis examines how the newspapers have utilized the PISA results in the debate on education in South Korea. This was done by comparing articles related to PISA published in two prominent newspapers of different political inclination since the first PISA cycle in 2000 and until the year of 2018 - the last time period that can be examined in full within the time limits of this thesis.