Study of Liquid Metals by Electrostatic Levitation
Total Page:16
File Type:pdf, Size:1020Kb
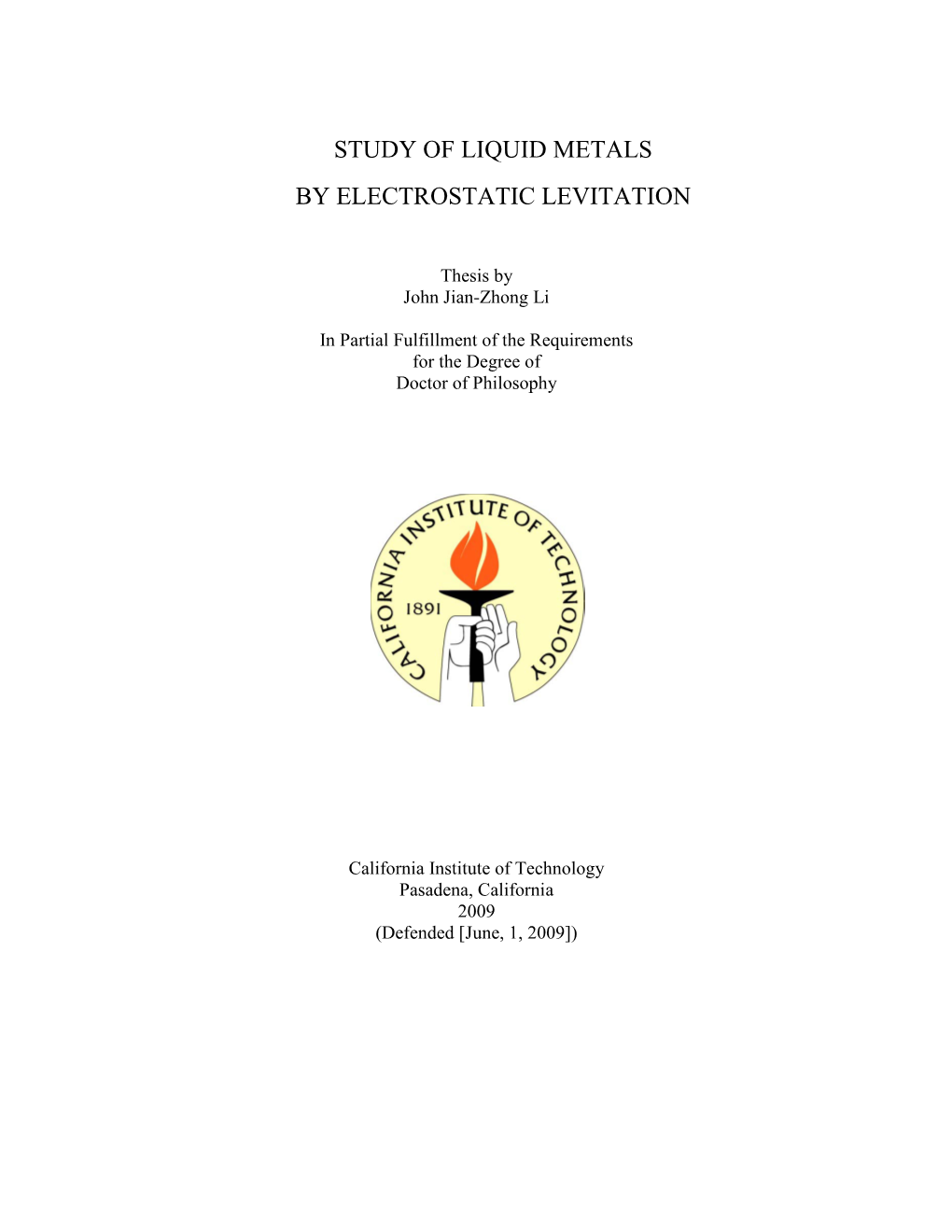
Load more
Recommended publications
-
1 Diamagnetic Levitation Using High-Temperature
Diamagnetic Levitation Using High-Temperature Superconducting Wires for Microgravity Research and Mitigation in Human Spaceflight Applications G. Bruhauga* aUniversity of Rochester, Department of Mechanical Engineering, 235 Hopeman Building, P. O Box 270132, Rochester, NY 14627 USA *[email protected] L. Beveridgeb bLANL Stop E557 PO Box 1663 Los Alamos, NM 87545 [email protected] Key Words: microgravity, diamagnetism, levitation, superconductors A novel use of high-temperature superconducting (HTS) electromagnets for human-sized microgravity research and mitigation is outlined. Recent advances in HTS technology have resulted in electromagnets that potentially could levitate large diamagnetic targets, such as human organs, for additive manufacturing or entire humans for microgravity training. These applications are then used as a springboard to discuss the possibility of active microgravity compensation and “inertial dampeners” for future space travel applications. Finite element simulations are used to check the validity of the designs and motivate future research. 1 1. Introduction The stable levitation of diamagnetic objects has been studied and demonstrated experimentally but has so far had limited applications. Diamagnetic materials weakly repel any magnetic fields that are applied to them [1], but the repulsion is much weaker than with other magnetic effects such as ferromagnetism. This natural phenomenon can be used to levitate any structure that is primarily diamagnetic, as long as the applied magnetic field is extremely strong. Until recently, magnets of the needed strength (of the order of several tesla or greater) were either nonexistent or extremely rare. However, the advent of low-temperature superconductors (LTS’s) as a commercial technology has made several-tesla magnets quite commonplace. -
Review of Magnetic Levitation (MAGLEV): a Technology to Propel Vehicles with Magnets by Monika Yadav, Nivritti Mehta, Aman Gupta, Akshay Chaudhary & D
Global Journal of Researches in Engineering Mechanical & Mechanics Volume 13 Issue 7 Version 1.0 Year 2013 Type: Double Blind Peer Reviewed International Research Journal Publisher: Global Journals Inc. (USA) Online ISSN: 2249-4596 & Print ISSN: 0975-5861 Review of Magnetic Levitation (MAGLEV): A Technology to Propel Vehicles with Magnets By Monika Yadav, Nivritti Mehta, Aman Gupta, Akshay Chaudhary & D. V. Mahindru SRMGPC, India Abstract - The term “Levitation” refers to a class of technologies that uses magnetic levitation to propel vehicles with magnets rather than with wheels, axles and bearings. Maglev (derived from magnetic levitation) uses magnetic levitation to propel vehicles. With maglev, a vehicle is levitated a short distance away from a “guide way” using magnets to create both lift and thrust. High-speed maglev trains promise dramatic improvements for human travel widespread adoption occurs. Maglev trains move more smoothly and somewhat more quietly than wheeled mass transit systems. Their nonreliance on friction means that acceleration and deceleration can surpass that of wheeled transports, and they are unaffected by weather. The power needed for levitation is typically not a large percentage of the overall energy consumption. Most of the power is used to overcome air resistance (drag). Although conventional wheeled transportation can go very fast, maglev allows routine use of higher top speeds than conventional rail, and this type holds the speed record for rail transportation. Vacuum tube train systems might hypothetically allow maglev trains to attain speeds in a different order of magnitude, but no such tracks have ever been built. Compared to conventional wheeled trains, differences in construction affect the economics of maglev trains. -
Introduction & Overview of Magnetic Levitation (MAGLEV) Train System
Volume 3, Issue 2, February – 2018 International Journal of Innovative Science and Research Technology ISSN No:-2456 –2165 Introduction & Overview of Magnetic Levitation (MAGLEV) Train System Mr. Abhijeet T. Tambe1 Prof. Dipak S. Patil2 Mechanical Department Mechanical Department Loknete Gopinathji Munde Institute of Engineering Loknete Gopinathji Munde Institute of Engineering Education & Research Education & Research Nashik, India Nashik, India Mr. Sanjay S. Avhad3 Mechanical Department Loknete Gopinathji Munde Institute of Engineering Education & Research Nashik, India Abstract - In this paper, we will discuss about Basics of I. INTRODUCTION magnetic levitation train system , its components and working. A German inventor named “Alfred Zehden” was Basically, the MAGLEV train stands for magnetic levitation awarded by United States Patent for a linear motor propelled train and is a system of high speed transportation as compared train. The inventor was awarded U.S. Patent 782,312 on 14 to conventional train system. February 1905 and U.S. Patent RE 12,700 on 21 August The term “MAGLEV” refers not only to the vehicles 1907. An Electromagnetic transportation system was but to the railway system as well specially design for magnetic discovered and developed in 1907 by F.S. Smith. In levitation and propulsion. The important concept of this system between 1937 & 1941 Herman Kemper was awarded by is to generate magnetic field obtained by using either serious of German patents for magnetic levitation train permanent magnets or electromagnets. As compared to propelled by linear motors. conventional train, maglev train system has no moving parts, the train travels along its guideway of magnets which controls Maglev is derived from magnetic levitation which means the train stability and speed therefore the maglev train are to lift a vehicle without any mechanical support with the quiter and smoother than conventional trains and have the help of magnetic field generated by either permanent potential for much higher speed. -
Understanding Stable Levitation of Superconductors from Intermediate Electromagnetics A
Understanding stable levitation of superconductors from intermediate electromagnetics A. Badía-Majósa͒ Departamento de Física de la Materia Condensada-I.C.M.A., C.P.S.U.Z., María de Luna 1, E-50018 Zaragoza, Spain ͑Received 15 February 2006; accepted 28 July 2006͒ Levitation experiments with superconductors in the Meissner state are hindered by low stability except for specifically designed configurations. In contrast, magnetic force experiments with strongly pinned superconductors and permanent magnets display high stability, allowing the demonstration of striking effects, such as lateral or inverted levitation. These facts are explained by using a variational theory. Illustrations based on calculated magnetic field lines for various configurations are presented. They provide a qualitative physical understanding of the stability features. © 2006 American Association of Physics Teachers. ͓DOI: 10.1119/1.2338548͔ I. INTRODUCTION A. Type-I superconductors Levitation experiments based on the repulsive ͑or attrac- We begin with the definition of the electric current density tive͒ force between permanent magnets and superconductors for conducting media are common. Almost everyone is fascinated and stimulated J = nqv, ͑1͒ by the observation of floating objects. When the setup in- cludes a high pinning ͑or high critical current͒ supercon- where n is the volume density of the charge carriers, q their ductor, the possibilities of lifting moderate weights and dis- effective charge, and v their velocity. If the underlying ma- playing lateral or inverted levitation are even more attractive. terial is such that charges can move without friction, New- Recent developments of vehicles capable of supporting sev- ton’s second law gives eral passengers1 have increased the interest in this topic. -
Anti-Gravity
First published at http://www.fe.up.pt/~feliz and YouTube on the 09 March 2014, and concepts registered with the Portuguese Society of Authors A n t i - g r a v i t y The jump out to anywhere? Two main proposals ready to be tested. Physics, Engineering, Modelling and Simulation [email protected] J. Manuel Feliz-Teixeira March 2014 KEYWORDS: gravitation, gravity, torque and force, changing ªaction-reactionº present in our day by day systems. angular momentum with minimal torque, flux of mass, action- reaction as a centre-of-mass conservation, creating acceleration In effect, what moves something is a reaction-force, from within a system, internal-mass-propulsion and anti-gravity. not an action-force, and this reaction-force is always applied upon the system by something external to the system: the surface of the ground impulses us ABSTRACT forward while walking; the fluid impulses the boat or aircraft forward when by means of a propeller one The physico-mathematical description of two systems forces it to move backward; the impulse of the mass that may probably generate internal thrust is presented in leaving at high speed in a jet propulsion system, this article. These are System-V and System-VII. We have impulses the craft in the opposite direction, etc. We reasons to believe such a thrust can probably be generated could even basically say that forces only exist in by means of adequately moving mass in the interior of pairs, not alone as single vectorial entities. these systems, and without any sort of expulsion of matter In order to better understand the difficulty of or energy. -
1 Evaluation of Simulated Microgravity Environments
EVALUATION OF SIMULATED MICROGRAVITY ENVIRONMENTS INDUCED BY DIAMAGNETIC LEVITATION OF PLANT CELL SUSPENSION CULTURES Khaled Y. Kamal1#,§, Raúl Herranz1#,*, Jack J.W.A. van Loon2,3, Peter C.M. Christianen4, F. Javier Medina1* 1Centro de Investigaciones Biológicas (CSIC), C/ Ramiro de Maeztu,7 CP 28040 Madrid, SPAIN; 2European Space Research & Technology Center - TEC-MMG Lab. – European Space Agency (ESTEC-ESA), NETHERLANDS; 3Dutch Experiment Support Center (DESC) @ Dept Oral and Maxillofacial Surgery/Oral Pathology, VU University Medical Center / Dept Oral Function and Restorative Dentistry, Academic Centre for Dentistry Amsterdam (ACTA), Gustav Mahlerlaan 3004, NL-1081 LA Amsterdam, NETHERLANDS; 4High Field Magnet Laboratory (HFML), Institute for Molecules and Materials, Radboud University Nijmegen, NETHERLANDS; #These authors have contributed equally to this work. §Dr. Kamal present address is Faculty of Agriculture, Zagazig University, EGYPT. *Corresponding authors: Dr. Raúl Herranz, Email: r.herranz@ csic.es and Dr. F. Javier Medina, Email: [email protected] Phone: +34 918373112 Ext. 4261 Fax: +34 915360432. Keywords: Simulated microgravity, Suspension cell culture, Magnetic Levitation, Ground-based facilities, Arabidopsis thaliana, Cell growth, Cell proliferation, Nucleolus RUNNING TITLE: Exposure of Plant Cell Suspensions to Magnetic Levitation 1 ABSTRACT Ground-Based Facilities (GBF) are essential tools to understand the physical and biological effects of the absence of gravity and they are necessary to prepare and complement space experiments. It has been shown previously that a real microgravity environment induces the dissociation of cell proliferation from cell growth in seedling root meristems, which are limited populations of proliferating cells. Plant cell cultures are large and homogeneous populations of proliferating cells, so that they are a convenient model to study the effects of altered gravity on cellular mechanisms regulating cell proliferation and associated cell growth. -
Arxiv:2010.07641V1 [Quant-Ph] 15 Oct 2020 Regime
Quantum experiments with microscale particles James Millen Department of Physics, King's College London, Strand, London, WC2R 2LS, United Kingdom∗ Benjamin A. Stickler Faculty of Physics, University of Duisburg-Essen, Lotharstraße 1, 47048 Duisburg, Germany and QOLS, Imperial College London, Exhibition Road, London SW72AZ, United Kingdom Quantum theory is incredibly successful, explaining the microscopic world with great accuracy, from the behaviour of subatomic particles to chemical reactions to solid-state electronics. There is not a single experimental finding challenging its predictions, and ever more quantum phenomena are exploited in technology, including interferometric sensing and quantum cryptography. In order to explore novel applications and test the validity of quantum physics at the macroscale researchers strive to prepare ever heavier and bigger objects in quantum superpositions. Experiments with levitated microscale particles are about to push this quest into uncharted waters. Time INTRODUCTION Section I: Levitation (optical, electrical, magnetic) Despite the incredible successes of quantum theory over the last 100 years, debates continue as to its univer- sal validity. Applying the predictions of quantum the- Section II: Cooling ory to macroscopic objects has always puzzled physicists (cavity, feedback, other) and philosophers alike [1]. While decoherence theories can explain the emergence of classicality [2], the fun- damental question remains as to whether basic quan- Section III: Interference tum phenomena, such as the archetypal superposition (grating, trapped, discrete principle, are universally valid [3]. This has been fa- system, rotational) mously acknowledged by Anthony Leggett, admitting that `by day, you would see me sitting at my desk solv- Figure 1. Macroscopic quantum interference experiments re- ing Schr¨odinger'sequation' while at night he is convinced quire three stages of particle manipulation: levitation, cool- that `at some point between the atom and the human ing, and interference/detection. -
Levitation/Guidance Coils of a Superconducting Oxford University
Session C12 Paper 8151 Disclaimer —This paper partially fulfills a writing requirement for first year (freshman) engineering students at the University of Pittsburgh Swanson School of Engineering. This paper is a student, not a professional, paper. This paper is based on publicly available information and may not be provide complete analyses of all relevant data. If this paper is used for any purpose other than these authors’ partial fulfillment of a writing requirement for first year (freshman) engineering students at the University of Pittsburgh Swanson School of Engineering, the user does so at his or her own risk. SUPERCONDUCTIVE LEVITATION AND PROPULSION COILS OF SCMAGLEV TRAINS Nicholas Hages, [email protected], Mandala, 2:00, Anthony Popovski, [email protected], Mena, 10:00 Abstract— The use of superconductive magnetic coils to Speed Transport by Magnetically Suspended Trains” was levitate and propel magnetic levitation (maglev) train systems presented [2]. This proposal was based on three main by Superconducting maglev (SCMAGLEV), developed by the concepts: “(1) superconducting coils are arranged on the Central Japan Railway Company, is revolutionizing vehicle while normal conducting coils are installed on the transportation. Placed in strategic locations on the bottom track; (2) the vehicle is lifted by electromagnetic induction…; and sides of train bodies and along tracks, these magnets and (3) null flux used for vehicle guidance” [2]. Essentially, repel each other, and levitation is achieved. Active coils of magnetic levitation (maglev) technology would replace the superconductive wire that does not resist high electric conventional form of locomotive train with magnetic currents allow a great magnetic field to be generated, and by repulsion to propel the train. -
Electromagnetic Levitation Thesis
ELECTROMAGNETIC LEVITATION THESIS 2005 COMPILED BY: LANCE WILLIAMS ACKNOWLEDGEMENTS I would like to acknowledge the help and support of Professor J. Greene in the formation and development of this thesis. I would also like to acknowledge my friends and fellow students for their willingness to assist with experiments and in lending advice. Lastly, I would like to acknowledge Bill Beaty for his excellent web site. It is very well organized and he provides several useful links for anyone interested in magnetic levitation. I would highly recommend his website to anyone interested in this fascinating topic. TERMS OF REFERENCE The aim of this thesis was to investigate magnetic levitation and to design a working system capable of levitating an object from below. The system should be able to levitate an object from below, clear of an array of electromagnets without any form of support. There shouldn’t be any object, structure or device assisting in levitation, on the same level of elevation as the levitating object. The control and circuit complexities should be investigated and recommendations for improving the designed system should be made. SUMMARY Magnetic levitation is the process of levitating an object by exploiting magnetic fields. If the magnetic force of attraction is used, it is known as magnetic suspension. If magnetic repulsion is used, it is known as magnetic levitation. In the past, magnetic levitation was attempted by using permanent magnets. Earnshaw’s theorem however, proves that this is mathematically impossible. There exists no arrangement of static magnets of charges that can stably levitate an object. There are however means of circumventing this theorem by altering its basic assumptions. -
Design and Superconducting Levitation
Downloaded from http://www.mitpressjournals.org/doi/pdf/10.1162/LEON_a_00870 by guest on 23 September 2021 G e n e r a l n o t e Design and Superconducting Levitation a b s t r a c t When specific metals are cooled to a very low tempera- Julien Bobroff, ture (typically colder than about -200°C), they become supercon- François Azambourg, ductive and can make magnets levitate. This paper reports on a Clémentine Chambon and collaboration between physicists and designers to exploit this Veronica Rodriguez quantum levitation. The main goal of this collaboration was to create artistic displays, experi- ments and videos to engage a large public with fundamental physics. Beyond its public suc- cess, this “SupraDesign” project evitation—whether it originates from a mag- Superconductivity enabled an encounter between L two communities: researchers netic, electric or mechanical source—has always been a great and Levitation source of fascination. However, its very unstable nature has in physics and designers. The Discovered in 1911, superconduc- collaboration revealed unex- made it difficult to use in everyday chores or even in works tivity is a phenomenon that appears pected similarities in working of art. In 1986, two physicists made a discovery that changed in many metals at a very low tem- methods, such as testing everything: They demonstrated that certain types of ceramics through experimentation, engag- perature. When a metal becomes ing in teamwork and making use become superconductive at -200˚C (about -300˚F) [1,2] and superconductive, it starts conduct- in such a supercooled state can make magnets levitate with of creativity in a constraining ing currents perfectly, without any environment. -
Arxiv:1912.10397V1 [Quant-Ph] 22 Dec 2019 Ment
Single-Spin Magnetomechanics with Levitated Micromagnets J. Gieseler,1 A. Kabcenell,1 E. Rosenfeld,1 J. D. Schaefer,1 A. Safira,1 M. J. A. Schuetz,1 C. Gonzalez-Ballestero,2, 3 C. C. Rusconi,4 O. Romero-Isart,2, 3 and M. D. Lukin1 1Physics Department, Harvard University, Cambridge, MA 02318, USA. 2Institute for Quantum Optics and Quantum Information of the Austrian Academy of sciences, A-6020 Innsbruck, Austria. 3Institute for Theoretical Physics, University of Innsbruck, A-6020 Innsbruck, Austria. 4Max-Planck-Institut für Quantenoptik, Hans-Kopfermann-Strasse 1, 85748 Garching, Germany. (Dated: December 24, 2019) We demonstrate a new mechanical transduction platform for individual spin qubits. In our ap- proach, single micro-magnets are trapped using a type-II superconductor in proximity of spin qubits, enabling direct magnetic coupling between the two systems. Controlling the distance between the magnet and the superconductor during cooldown, we demonstrate three dimensional trapping with quality factors around one million and kHz trapping frequencies. We further exploit the large mag- netic moment to mass ratio of this mechanical oscillator to couple its motion to the spin degree of freedom of an individual nitrogen vacancy center in diamond. Our approach provides a new path towards interfacing individual spin qubits with mechanical motion for testing quantum mechanics with mesoscopic objects, realization of quantum networks, and ultra-sensitive metrology. Realizing coherent coupling between individual spin in the solid state [3], quantum sensing [20–22] and quan- degrees of freedom and massive mechanical modes is an tum communication [23]. outstanding challenge in quantum science and engineer- Before proceeding, we note that low dissipation me- ing. -
Safety of High Speed Magnetic Levitation Transportation Systems, Titled, Review of German Safety Requirements for the Transrapid System
PB91129684 Safety of High Speed U.S. Department Magnetic Levitation of Transportation Federal Railroad Transportation Systems Administration Office of Research and Development Preliminary Safety Review of Washington, DC 20590 Transrapid Maglev System Robert M. Dorer William T. Hathaway REPRODUCED BY U.S. DEPARTMENT OF COMMERCE NATIONAL TECHNICAL INFORMATION SERVICE SPRINGFIELD, VA 22161 NOTICE This document is disseminated under the sponsorship of the Department of Transportation in the interest of information exchange. The United States Government assumes no liability for its contents or use thereof. NOTICE The United States Government does not endorse products or manufacturers. Trade or manufacturers' names appear herein solely because they are considered essential to the object of this report. Technical Repart Dacumentation Poge 1. Report No. , ,.._··-·----• ,1.,,.,.•••ion No. 3. Recipient' 1 C•tolo9 No. DOT/FRA/ORD-90/09 PB91-129684 •• Title ond Subtitl• 5. Ret1ort Cate Safety of High Speed Magnetic Levitation November 1990 Transportation Systems: Preliminary Safety 6. Performing Orgoni 1ation Code Review of the Transrapid Maglev System DTS-73 B. P•rfonnint OrgOftitatfon R•port No. 7. Author1 a) DOT-VNTSC-FRA-90-3 Robert M. Dorer and William T. Hathaway 9. fi••&'"'"~t Oll'i"l:'zat;ae_ N~of!ld Addrosa t t. 10. Wark Un;t No. (TRAIS) . p men o ranspor a 1on RR193/Rl019 Research and Special Programs Administration l I. Contract or Grant No. John A. Volpe National Transportation Systems Center Cambridge, MA 02142 13. Type of Re,ort encl Period Co•ered 12. Sponsoring Agency Nome and Addre11 Interim Report U.S. Department of Transportation Sept.