A Survey on the Application of Wirelesshart for Industrial Process Monitoring and Control
Total Page:16
File Type:pdf, Size:1020Kb
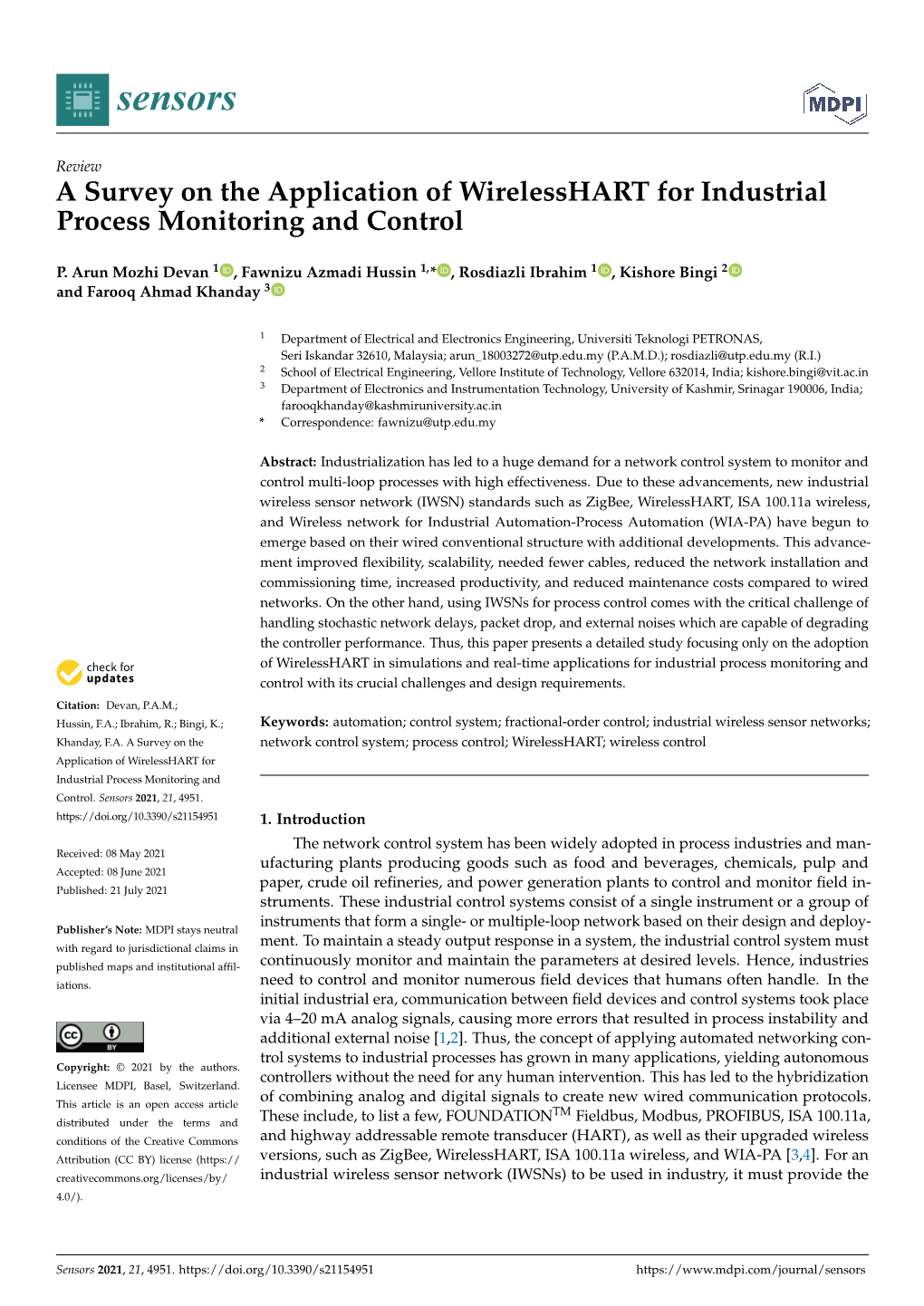
Load more
Recommended publications
-
Cracking Channel Hopping Sequences and Graph Routes in Industrial TSCH Networks
1 Cracking Channel Hopping Sequences and Graph Routes in Industrial TSCH Networks ∗ XIA CHENG, JUNYANG SHI, and MO SHA , State University of New York at Binghamton, USA Industrial networks typically connect hundreds or thousands of sensors and actuators in industrial facilities, such as manufacturing plants, steel mills, and oil refineries. Although the typical industrial Internet of Things (IoT) applications operate at low data rates, they pose unique challenges because of their critical demands for reliable and real-time communication in harsh industrial environments. IEEE 802.15.4-based wireless sensor-actuator networks (WSANs) technology is appealing for use to construct industrial networks because it does not require wired infrastructure and can be manufactured inexpensively. Battery-powered wireless modules easily and inexpensively retrofit existing sensors and actuators in industrial facilities without running cables for communication and power. To address the stringent real-time and reliability requirements, WSANs made a set of unique design choices such as employing the Time-Synchronized Channel Hopping (TSCH) technology. These designs distinguish WSANs from traditional wireless sensor networks (WSNs) that require only best effort services. The function-based channel hopping used in TSCH simplifies the network operations at the cost of security. Our study shows that an attacker can reverse engineer the channel hopping sequences and graph routes by silently observing the transmission activities and put the network in danger of selective jamming attacks. The cracked knowledge on the channel hopping sequences and graph routes is an important prerequisite for launching selective jamming attacks to TSCH networks. To our knowledge, this paper represents the first systematic study that investigates the security vulnerability of TSCH channel hopping and graph routing under realistic settings. -
Industrial Iot Monitoring: Technologies and Architecture Proposal
sensors Article Industrial IoT Monitoring: Technologies and Architecture Proposal Duarte Raposo 1,* , André Rodrigues 1,2 , Soraya Sinche 1,3 , Jorge Sá Silva 1 and Fernando Boavida 1 1 Centre of Informatics and Systems of the University of Coimbra, Coimbra 3030-290, Portugal; [email protected] (A.R.); [email protected] (S.S.); [email protected] (J.S.S.); [email protected] (F.B.) 2 Polytechnic Institute of Coimbra, ISCAC, Coimbra 3040-316, Portugal 3 DETRI, Escuela Politécnica Nacional, Quito 170517, Ecuador * Correspondence: [email protected]; Tel.: +351-239-790-000 Received: 12 September 2018; Accepted: 16 October 2018; Published: 21 October 2018 Abstract: Dependability and standardization are essential to the adoption of Wireless Sensor Networks (WSN) in industrial applications. Standards such as ZigBee, WirelessHART, ISA100.11a and WIA-PA are, nowadays, at the basis of the main process-automation technologies. However, despite the success of these standards, management of WSNs is still an open topic, which clearly is an obstacle to dependability. Existing diagnostic tools are mostly application- or problem-specific, and do not support standard-based multi-network monitoring. This paper proposes a WSN monitoring architecture for process-automation technologies that addresses the mentioned limitations. Specifically, the architecture has low impact on sensor node resources, uses network metrics already available in industrial standards, and takes advantage of widely used management standards to share the monitoring information. The proposed architecture was validated through prototyping, and the obtained performance results are presented and discussed in the final part of the paper. In addition to proposing a monitoring architecture, the paper provides an in-depth insight into metrics, techniques, management protocols, and standards applicable to industrial WSNs. -
Smart Dust and Sensory Swarms Kris Pister Prof
Smart Dust and Sensory Swarms Kris Pister Prof. EECS, UC Berkeley Founder & Chief Technologist Dust Networks, a Linear company The Swarm at The Edge of the Cloud TRILLIONS OF CONNECTED DEVICES InfrastructuralTHE CLOUD core THE SWARM [J. Rabaey, ASPDAC’08] 2 Micro Robots, 1995 Goal: Make silicon chips that walk. (Richard Yeh) 3 Smart Dust, 1997 4 Smart Dust, 2001 5 Building Energy System (ucb, 2001) . 50 temperature sensors on 4th floor . 5 electrical power monitors . 1 relay controlling a Trane rooSop chiller 6 Sensor Networks Take Off! $8.1B market for Wireless Sensor Networks in 2007 Source: InStat/MDR 11/2003 (Wireless); Wireless Data Research Group 2003; InStat/MDR 7/2004 (Handsets) 7 Celebrity Endorsement 8 Sensor Networks Take Off! Industry Analysts Take Off! $8.1B market for Wireless Sensor Networks in 2007 Source: InStat/MDR 11/2003 (Wireless); Wireless Data Research Group 2003; InStat/MDR 7/2004 (Handsets) 9 Barriers to AdopWon OnWorld, 2005 10 The Requirements . Deploy devices ANYWHERE . The data must be RELIABLE . No baery changes for ~ DECADE 11 Network Architecture Network & Security Management IEEE 802.15.4 Radio Time slotted and synchronized for low power and scalability Full mesh and channel hopping for wire-like reliability (>99.99% ) Every node can run on batteries (or energy harvester) for 10+ years Incorporated into WirelessHART (IEC62591), ISA100.11a, WIA-PA, and IEEE 802.15.4E standards 12 Wireless HART Architecture (from ABB) 13 Emerson offerings, 2007 (Dave Farr presentaon) 14 15 Emerson Process Managmenet, Extreme -
Smartmesh Wirelesshart User's Guide
SmartMesh WirelessHART User's Guide SmartMesh WirelessHART User's Guide Page 1 of 135 Table of Contents 1 About This Guide _________________________________________________________________________________ 5 1.1 Related Documents __________________________________________________________________________ 5 1.2 Conventions Used ___________________________________________________________________________ 7 1.3 Revision History _____________________________________________________________________________ 8 2 SmartMesh Glossary ______________________________________________________________________________ 9 3 The SmartMesh WirelessHART Network ______________________________________________________________ 13 3.1 Introduction _______________________________________________________________________________ 13 3.1.1 Network Overview ____________________________________________________________________ 13 3.1.2 SmartMesh Network Features ___________________________________________________________ 15 3.2 Network Formation __________________________________________________________________________ 16 3.2.1 Mote Joining ________________________________________________________________________ 17 3.2.2 Discovery ___________________________________________________________________________ 17 3.3 Bandwidth and Latency ______________________________________________________________________ 18 3.3.1 Base Bandwidth ______________________________________________________________________ 18 3.3.2 Services ____________________________________________________________________________ -
Low-Power Wireless for the Internet of Things: Standards and Applications Ali Nikoukar, Saleem Raza, Angelina Poole, Mesut Günes, Behnam Dezfouli
Low-Power Wireless for the Internet of Things: Standards and Applications Ali Nikoukar, Saleem Raza, Angelina Poole, Mesut Günes, Behnam Dezfouli To cite this version: Ali Nikoukar, Saleem Raza, Angelina Poole, Mesut Günes, Behnam Dezfouli. Low-Power Wireless for the Internet of Things: Standards and Applications: Internet of Things, IEEE 802.15.4, Bluetooth, Physical layer, Medium Access Control, coexistence, mesh networking, cyber-physical systems, WSN, M2M. IEEE Access, IEEE, 2018, 6, pp.67893-67926. 10.1109/ACCESS.2018.2879189. hal-02161803 HAL Id: hal-02161803 https://hal.archives-ouvertes.fr/hal-02161803 Submitted on 21 Jun 2019 HAL is a multi-disciplinary open access L’archive ouverte pluridisciplinaire HAL, est archive for the deposit and dissemination of sci- destinée au dépôt et à la diffusion de documents entific research documents, whether they are pub- scientifiques de niveau recherche, publiés ou non, lished or not. The documents may come from émanant des établissements d’enseignement et de teaching and research institutions in France or recherche français ou étrangers, des laboratoires abroad, or from public or private research centers. publics ou privés. Received August 13, 2018, accepted October 11, 2018, date of publication November 9, 2018, date of current version December 3, 2018. Digital Object Identifier 10.1109/ACCESS.2018.2879189 Low-Power Wireless for the Internet of Things: Standards and Applications ALI NIKOUKAR 1, SALEEM RAZA1, ANGELINA POOLE2, MESUT GÜNEŞ1, AND BEHNAM DEZFOULI 2 1Institute for Intelligent Cooperating Systems, Otto von Guericke University Magdeburg, 39106 Magdeburg, Germany 2Internet of Things Research Lab, Department of Computer Engineering, Santa Clara University, Santa Clara, CA 95053, USA Corresponding author: Ali Nikoukar ([email protected]) This work was supported by DAAD (Deutscher Akademischer Austauschdienst) and DAAD/HEC Scholarships. -
A Framework for Wirelesshart Simulations
View metadata, citation and similar papers at core.ac.uk brought to you by CORE provided by Swedish Institute of Computer Science Publications Database A Framework for WirelessHART Simulations Igor Konovalov < igor@sics:se > Swedish Institute of Computer Science Box 1263, SE-164 29 Kista, Sweden SICS Technical Report T2010:06 ISSN 1100-3154 June 15, 2010 Keywords: wirelessHART, hybrid simulations, time synchronization, protocol analyzer Abstract Due to stringent timing requirements of the WirelessHART protocol, we need to extend previously known hybrid simulation approaches with Wire- lessHART specific functionality. Because of intermediary devices that connect simulation and real environments a communication delay significantly exceeds time boundaries of a WirelessHART slot. Our solution is to add a Wire- lessHART -enabled intermediary device operating at the Physical and the Data Link layers that can handle time critical tasks of the WirelessHART protocol. This approach allows to evaluate the performance of a WirelessHART network and WirelessHART -enabled devices in a hybrid simulation environment. Acknowledgements I would like to thank my advisors Fredrik Osterlind} from SICS and Jonas Neander from ABB for their support and kind advices during my work. I would also like to thank all the Networked Embedded Systems group and my examiner Thomas Lindh from the Royal Institute of Technology. This thesis has been performed within the SICS Center for Networked Systems funded by ABB. iii Abbreviations ACK Acknowledgment APDU Application Layer -
Standards-Based Wireless Sensor Networking Protocols for Spaceflight Applications Raymond S
Standards-Based Wireless Sensor Networking Protocols for Spaceflight Applications Raymond S. Wagner, Ph.D. NASA Johnson Space Center 2101 NASA Parkway, Mail Code EV814/ESCG Houston, TX 77058 281-244-2428 [email protected] Abstract—Wireless sensor networks (WSNs) have the by re-locating a sensor from one panel to another, this is capacity to revolutionize data gathering in both easily accomplished. Similarly, additional sensors can be spaceflight and terrestrial applications. WSNs provide a easily added to the existing suite, providing a more huge advantage over traditional, wired instrumentation detailed measurement set without requiring more wires to since they do not require wiring trunks to connect sensors be strung behind bulkheads and through walls of pressure to a central hub. This allows for easy sensor installation shells. Finally, wireless sensors can be re-used between in hard to reach locations, easy expansion of the number vehicles once their initial missions have been ended. A of sensors or sensing modalities, and reduction in both WSN node can be relocated from a spent vehicle, such as system cost and weight. While this technology offers a lunar larder, to one currently in service, such as a lunar unprecedented flexibility and adaptability, implementing rover or habitat. The node can even be outfitted with a it in practice is not without its difficulties. Recent new set of sensors in the process, retaining the common advances in standards-based WSN protocols for industrial radio and networking hardware; to give a new functional control applications have come a long way to solving tilt built mostly from recycled parts. -
Internet of Things CSE 521S Wireless Sensor Networks
Internet of Things CSE 521S Wireless Sensor Networks Chenyang Lu Internet ofThings Ø Convergence of q Miniaturized devices: processor+sensors+radio, embedded OS. q Low-power wireless: connect millions of devices to the Internet. q Data analytics: make sense of sensor data. q Cloud and edge computing: scalable real-time data processing. Ø Real-time monitoring and control of physical systems q Smart *: house, healthcare, manufacturing, transportation, grid… Ø We are in the Golden Age of Internet of Things! q “A period in a field of endeavor when great tasks were accomplished.” 2 Revolutionizing Industry Ø Industrial control systems are embracing new technologies q Edge computing: on-premise computing resources q Wireless networks: flexibility and easy deployment Ø https://www.youtube.com/watch?v=LNMmmjz5nCo (Emerson) tank level temperature valve vibration motor pressure Controller https://www.automation.com 3 Saving Energy Ø https://www.youtube.com/watch?v=JwRTpWZReJk (DoE) Ø Communication between utility companies and household devices Ø Home-Area Network (HAN) connects meters, appliances, HVAC Ø Optimize energy efficiency while enhancing comfort 4 Improving Healthcare Ø Clinical deterioration in hospitalized patients q 4-17% suffer adverse events (e.g., cardiac or respiratory arrest). q Up to 70% of such events could have been prevented. q Clinical deterioration is often preceded by changes in vitals. Ø Goal: early warning of clinical deterioration à improved outcome Ø Real-time patient monitoring in general hospital wards q Current practice: collect vital signs manually every 5-10 hours q Wireless monitoring system: collects data every minute! Ø Large-scale, interdisciplinary research q Wireless sensor networks, data mining, medical informatics, clinical care 5 Wireless Clinical Monitoring Rapid Response R. -
Wireless Sensor Network Based Smart Grid Communications: Cyber Attacks, Intrusion Detection System and Topology Control
Preprints (www.preprints.org) | NOT PEER-REVIEWED | Posted: 27 October 2016 doi:10.20944/preprints201610.0092.v2 Review Wireless Sensor Network Based Smart Grid Communications: Cyber Attacks, Intrusion Detection System and Topology Control Lipi Chhaya 1,*, Paawan Sharma 1, Govind Bhagwatikar 2 and Adesh Kumar 1 1 University of Petroleum & Energy Studies, Dehradun 248007, India; PAAWAN.SHARMA@ ddn.upes.ac.in (P.S.); [email protected] (A.K.) 2 SANY Group, Pune, India; [email protected] * Correspondence: [email protected]; Tel.: +91-991-337-9801 Abstract: An existing power grid is going through a massive transformation. Smart grid technology is a radical approach for improvisation in prevailing power grid. Integration of electrical and communication infrastructure is inevitable for the deployment of Smart grid network. Smart grid technology is characterized by full duplex communication, automatic metering infrastructure, renewable energy integration, distribution automation and complete monitoring and control of entire power grid. Wireless sensor networks (WSNs) are small micro electrical mechanical systems which are accomplished to collect and communicate the data from surroundings. WSNs can be used for monitoring and control of smart grid assets. Security of wireless sensor based communication network is a major concern for researchers and developers. The limited processing capabilities of wireless sensor networks make them more vulnerable to cyber-attacks. The countermeasures against cyber-attacks must be less complex with an ability to offer confidentiality, data readiness and integrity. The address oriented design and development approach for usual communication network requires a paradigm shift to design data oriented WSN architecture. WSN security is an inevitable part of smart grid cyber security. -
Experimental Study of Thread Mesh Network for Wireless Building Automation Systems
EXAMENSARBETE INOM ELEKTROTEKNIK, AVANCERAD NIVÅ, 30 HP STOCKHOLM, SVERIGE 2016 Experimental Study of Thread Mesh Network for Wireless Building Automation Systems DAPENG LAN KTH SKOLAN FÖR ELEKTRO- OCH SYSTEMTEKNIK i KTH ROYAL INSTITUTE OF TECHNOLOGY Abstract Master of Science Experimental Study of Thread Mesh Network for Wireless Building Automation Systems by Dapeng LAN Wireless sensor network technologies have gained significant popularity in home automation due to their scalability, system mobility, wireless connec- tivity, inexpensive and easy commissioning. Thread, a new wireless pro- tocol aiming for home automation, is proposed by Google Nest and stan- dardized by Thread Group. This thesis presents a thorough experimental evaluation of Thread wire- less protocol with the hardware platform from NXP. The test plan, imple- mentation, and analysis of the experiments is discussed in details, including signal coverage, unicast and multicast latency, reliability, and availability. Furthermore, a system level model considering the delay in different layers for the latency of Thread mesh network is presented, and validated by the experimental results. Finally, a friendly tool was developed for installers to estimate the latency of Thread mesh network. ! ! ! ! ! ! ! ! ! Sammanfattning) ! Trådlösa) sensornätverk) har) fått) betydande) popularitet) för) hemautomation) på) grund) av) deras) skalbarhet,) systemmobilitet,) trådlösa) konnektivitet,) låga) prisnivå) och) enkla) implementation.) Thread,)ett)nytt)trådlöst)protokoll)avsett)för)hemautomation,)är) -
5G Warehouse, Workforce Enablement (B) Distribution Center
Wireless technologies and Use Cases in Industrial IOT Patrick Grossetete – Technical Marketing Stephen Goodman – Industrial Solutions Architect BRKIOT-1775 Cisco Webex Teams Questions? Use Cisco Webex Teams to chat with the speaker after the session How 1 Find this session in the Cisco Events Mobile App 2 Click “Join the Discussion” 3 Install Webex Teams or go directly to the team space 4 Enter messages/questions in the team space BRKIOT-1775 © 2020 Cisco and/or its affiliates. All rights reserved. Cisco Public 3 Agenda • Introduction • Understanding IOT wireless characteristics • IOT Wireless technology overview • IOT Wireless use cases • Conclusion BRKIOT-1775 © 2020 Cisco and/or its affiliates. All rights reserved. Cisco Public 4 Oil & Gas Warehouse Gas Station / Kiosk Manufacturing Parking Lot Utilities Wireless Technologies are key pillars of the Internet of Thing but… one size doesn’t fit all. Roadways Distribution Center Fleet Seaport Airport BRKIOT-1775 © 2020 Cisco and/or its affiliates. All rights reserved. Cisco Public 5 At the end of this session, you should be able to: • Understand that many domain- specific wireless network technologies are available as access and backhaul for the Key Learning Internet of Things. Objectives • Articulate the challenges of spectrum’s allocation, regulations, standard, architecture and use cases. • Evaluate your Use Cases in a context of Cisco IOT Wireless portfolio and future evolution. BRKIOT-1775 © 2020 Cisco and/or its affiliates. All rights reserved. Cisco Public 6 Industrial IOT Wireless Selection Criteria Public vs Private Licensed vs Unlicensed Indoor vs Outdoor Public vs Private Use Case Spectrum Backhaul vs Access Country’s regulations Fixed vs Mobile Powered vs Batteries IoT Wireless Technology Eco-system Transmit Power Device/Infrastructure Signal penetration Subscription Bandwidth capacity Distance TCO Operations Long/Medium/Short range Backward compatibility BRKIOT-1775 © 2020 Cisco and/or its affiliates. -
Distributed Graph Routing and Scheduling for Industrial Wireless Sensor-Actuator Networks Junyang Shi, Student Member, IEEE,Mosha , Member, IEEE, and Zhicheng Yang
This article has been accepted for inclusion in a future issue of this journal. Content is final as presented, with the exception of pagination. IEEE/ACM TRANSACTIONS ON NETWORKING 1 Distributed Graph Routing and Scheduling for Industrial Wireless Sensor-Actuator Networks Junyang Shi, Student Member, IEEE,MoSha , Member, IEEE, and Zhicheng Yang Abstract— Wireless sensor-actuator networks (WSANs) tech- 2025 (according to McKinsey’s report on future disruptive nology is appealing for use in the industrial Internet of technologies) [3]. Things (IoT) applications because it does not require wired Industrial networks, the underlying support of Industrial infrastructure. Battery-powered wireless modules easily and inex- pensively retrofit existing sensors and actuators in the industrial IoT (IIoT), typically connect hundreds or thousands of sensors facilities without running cabling for communication and power. and actuators in industrial facilities, such as steel mills, oil The IEEE 802.15.4-based WSANs operate at low-power and can refineries, chemical plants, and infrastructures implement- be manufactured inexpensively, which makes them ideal where ing complex monitoring and control processes. Although battery lifetime and costs are important. Almost, a decade of real- the typical process applications have low data rates, they world deployments of WirelessHART standard has demonstrated pose unique challenges because of their critical demands the feasibility of using its core techniques including reliable graph routing and time slotted channel hopping (TSCH) to achieve for reliable and real-time communication in harsh industrial reliable low-power wireless communication in the industrial environments. Failing to achieve such performance can lead facilities. Today, we are facing the fourth Industrial Revolution as to production inefficiency, safety threats, and financial loss.