View of Nanotechnology
Total Page:16
File Type:pdf, Size:1020Kb
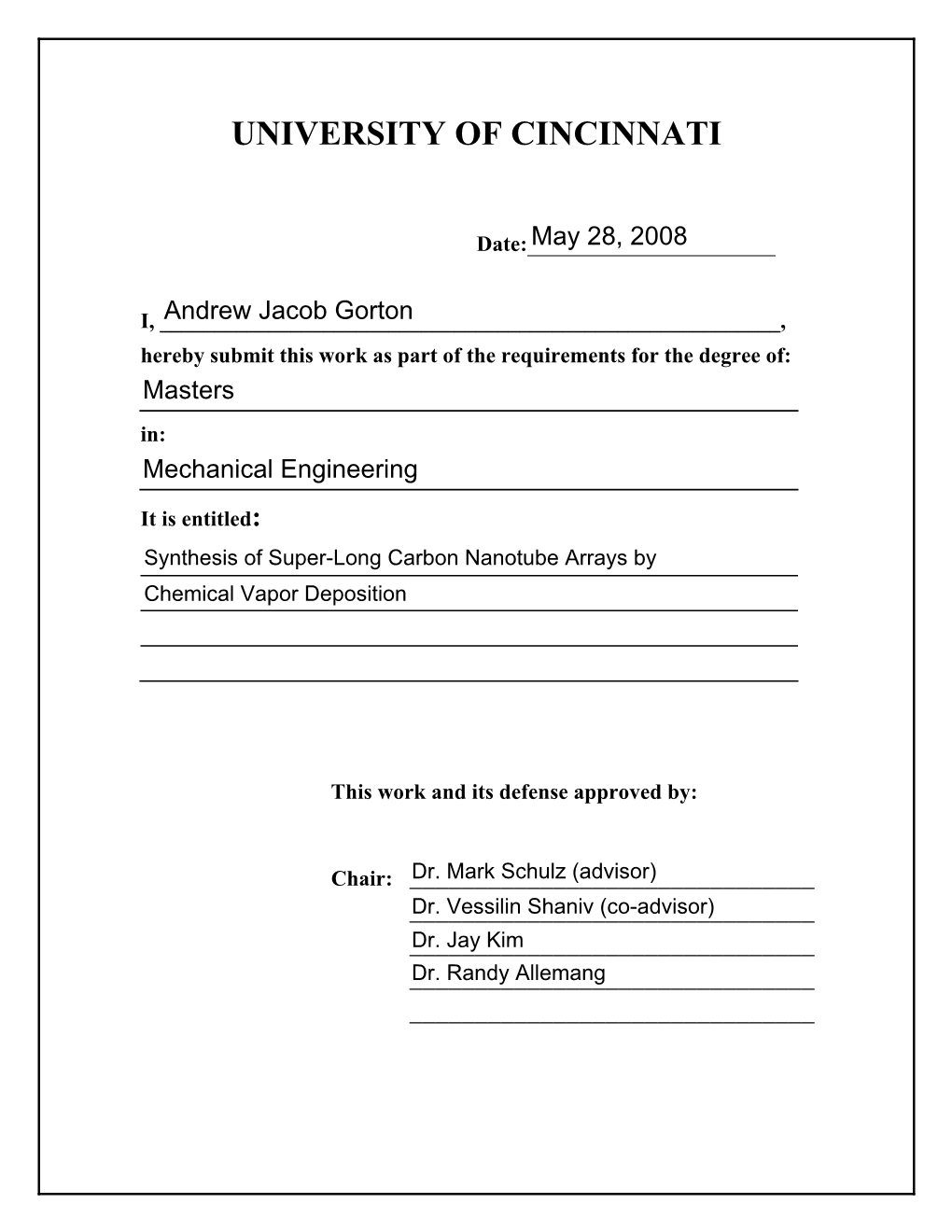
Load more
Recommended publications
-
Dr. Sumio Iijima's Research Accomplishments & Biography
Dr. Sumio Iijima’s Research Accomplishments & Biography last update October 1, 2021 Biography Name: Sumio Iijima Date of Birth: May 2, 1939 Contact: Meijo University, 1-501, Shiogamaguchi, Tenpaku, Nagoya, Aichi, 468-8502 +81-52-834-4001 [email protected] Professional Title and Affiliation: ・University Professor, Meijo University, ・Senior Research Fellow, NEC Corporation ・Honorary AIST Fellow, National Institute of Advanced Industrial Science and Technology (AIST) ・Distinguished Invited University Professor, Nagoya University Research Fields: Nano Science, Materials Science, Electron microscopy, Crystallography Education: 1959-1963: University of Electro-communications, Tokyo, Bachelor of Engineering 1963-1965: Tohoku University, Sendai, Majoring in Physics; M.S. 1965-1968: Tohoku University, Sendai, Majoring in Physics; Ph.D. Professional Record: 1968-1974 Research Associate, Research Institute for Scientific Measurements, Tohoku University, Sendai 1970-1977: Research Associate, Department of Physics, Arizona State University, Tempe, Arizona 1977-1982: Senior Research Associate, Center for Solid State Science, Arizona State University, Tempe, Arizona 1979: Visiting Senior Scientist, Department of Metallurgy and Materials Science, University of Cambridge, Cambridge 1982-1987: Group Leader, ERATO Program, Research Development Corporation of Japan, Nagoya 1987-Present: Senior Research Fellow, NEC Corporation, Tsukuba (Joined NEC in 1987 as Senior Principal Researcher) 1999-Present: University Professor, Meijo University, Nagoya (Visiting -
Nanoscience and Nanotechnologies: Opportunities and Uncertainties
ISBN 0 85403 604 0 © The Royal Society 2004 Apart from any fair dealing for the purposes of research or private study, or criticism or review, as permitted under the UK Copyright, Designs and Patents Act (1998), no part of this publication may be reproduced, stored or transmitted in any form or by any means, without the prior permission in writing of the publisher, or, in the case of reprographic reproduction, in accordance with the terms of licences issued by the Copyright Licensing Agency in the UK, or in accordance with the terms of licenses issued by the appropriate reproduction rights organization outside the UK. Enquiries concerning reproduction outside the terms stated here should be sent to: Science Policy Section The Royal Society 6–9 Carlton House Terrace London SW1Y 5AG email [email protected] Typeset in Frutiger by the Royal Society Proof reading and production management by the Clyvedon Press, Cardiff, UK Printed by Latimer Trend Ltd, Plymouth, UK ii | July 2004 | Nanoscience and nanotechnologies The Royal Society & The Royal Academy of Engineering Nanoscience and nanotechnologies: opportunities and uncertainties Contents page Summary vii 1 Introduction 1 1.1 Hopes and concerns about nanoscience and nanotechnologies 1 1.2 Terms of reference and conduct of the study 2 1.3 Report overview 2 1.4 Next steps 3 2 What are nanoscience and nanotechnologies? 5 3 Science and applications 7 3.1 Introduction 7 3.2 Nanomaterials 7 3.2.1 Introduction to nanomaterials 7 3.2.2 Nanoscience in this area 8 3.2.3 Applications 10 3.3 Nanometrology -
Photomechanical Actuation of Liquid Crystal Nanotube Elastomers. Xiaoming Fan University of Louisville
University of Louisville ThinkIR: The University of Louisville's Institutional Repository Electronic Theses and Dissertations 8-2014 Photomechanical actuation of liquid crystal nanotube elastomers. Xiaoming Fan University of Louisville Follow this and additional works at: https://ir.library.louisville.edu/etd Part of the Mechanical Engineering Commons Recommended Citation Fan, Xiaoming, "Photomechanical actuation of liquid crystal nanotube elastomers." (2014). Electronic Theses and Dissertations. Paper 422. https://doi.org/10.18297/etd/422 This Master's Thesis is brought to you for free and open access by ThinkIR: The nivU ersity of Louisville's Institutional Repository. It has been accepted for inclusion in Electronic Theses and Dissertations by an authorized administrator of ThinkIR: The nivU ersity of Louisville's Institutional Repository. This title appears here courtesy of the author, who has retained all other copyrights. For more information, please contact [email protected]. PHOTOMECHANICAL ACTUATION OF LIQUID CRYSTAL NANOTUBE ELASTOMERS By Xiaoming Fan B.Eng., Beijing University of Chemical Engineering, 2007 A Thesis Submitted to the Faculty of the J. B. Speed School of Engineering of the University of Louisville in Partial Fulfillment of the Requirements for the Degree of Master of Science Department of Mechanical Engineering University of Louisville Louisville, Kentucky August 2014 PHOTOMECHANICAL ACTUATION OF LIQUID CRYSTAL NANOTUBE ELASTOMERS By Xiaoming Fan B.Eng., Beijing University of Chemical Engineering, 2007 A Thesis Approved On July 11, 2014 by the following Thesis Committee : ____________________________________ Dr. Balaji Pachapakesan, Thesis Director ____________________________________ Dr. Robert W. Cohn _____________________________________ Dr. Stuart J. Williams ii ACKNOWLEDGEMENTS I would like to thank Dr. Baloo for his great help and support throughout the project. -
The Structural Biodegradation of Graphene Oxide in Vivo
The Structural Biodegradation of Graphene Oxide In Vivo A thesis submitted to the University of Manchester for the degree of Doctor of Philosophy in the Faculty of Biology, Medicine & Health Leon Newman School of Health Sciences, Division of Pharmacy and Optometry 2017 Table of Contents List of Figures ..................................................................................................................... 5 List of Tables ..................................................................................................................... 10 Abstract ............................................................................................................................. 12 Declaration ........................................................................................................................ 13 Declaration ..................................................................................................................... 13 Copyright statement ...................................................................................................... 13 Acknowledgements .......................................................................................................... 14 Rationale for the alternative thesis format ...................................................................... 15 List of abbreviations ......................................................................................................... 16 Chapter 1 .......................................................................................................................... -
Building Super Structures Through “Buckyballs and Buckytubes” Anuraag Boddupalli* Manipal Institute of Technology, India
Boddupalli, 1:8 http://dx.doi.org/10.4172/scientificreports.396 Open Access Open Access Scientific Reports Scientific Reports Rapid Communication OpenOpen Access Access Building Super Structures through “Buckyballs and Buckytubes” Anuraag Boddupalli* Manipal Institute of Technology, India Abstract Fullerenes or buck series of hollow carbon molecules that form either a closed cage (“buckyballs”) or a cylinder (carbon “nanotubes”) represent an exciting group of nanomaterials which have a beauty and elegance that excites the imagination of scientists and nonscientists alike, as they bridge aesthetic gaps between the sciences, architecture, mathematics, engineering, and the visual arts. Since the discovery of fullerenes in 1985, structural variations on fullerenes have evolved well beyond the individual clusters themselves. Their tremendous significance is related to their unique chemistry, super conductivity, and their technological applications, especially in materials science, electronics, and nanotechnology. Researchers are now slowly unraveling the multifaceted attributes of these molecules for improving society and environment. Keywords: Carbon; Geodesic dome; Fullerenes; Nanotubes; Nanomotors Introduction Nanotechnology represents a subject which is a synthesis of different sciences and technologies at the nanometer scale. In other words, it involves a different approach to the way we arrange and rearrange matter, which in turn can be harnessed to develop need based technologies. Until 1985, graphite and diamond were believed to be the only naturally occurring forms of carbon. In the year 1902, seven year old Buckminster Fuller, like all his other classmates was given a set of toothpicks and peas to design whatever he wanted in the class. The objective of that exercise was to judge the creativity and aptitude of the child, but it took several years for people to realize the immense significance of the truncated icosahedron structure that little Figure 1: A buckminsterfullerene or a ‘Buckyball’ showing inter-atomic linkages. -
INTER. Nb -DE30MM
LeMonde Job: WMQ2611--0001-0 WAS LMQ2611-1 Op.: XX Rev.: 25-11-99 T.: 10:13 S.: 111,06-Cmp.:25,10, Base : LMQPAG 23Fap: 100 No: 2043 Lcp: 700 CMYK 0123 FONDATEUR : HUBERT BEUVE-MÉRY 2000-2099 DIRECTEUR : JEAN-MARIE COLOMBANI 21 questions au XXIe siècle b La rédaction du « Monde » vous propose un voyage au cœur du siècle futur b Après le bilan du siècle, paru au premier semestre, une encyclopédie de l’avenir b France Info s’associe à cette enquête auprès des meilleurs spécialistes b Paul Rebeyrolle apporte sa vision de peintre sur chacun des thèmes traités CE NUMÉRO spécial a pour am- bition de traiter les grandes ques- LES GRANDS TÉMOINS tions – environnementales, biolo- giques, géopolitiques – auxquelles le siècle prochain sera confronté. Il Trois est le complément du Siècle, notre supplément paru au premier se- romanciers mestre, où la rédaction du Monde Irons-nous sur Mars ? Un troisième proposait son bilan d’une époque sexe va-t-il naître ? Travaillerons-nous à inaugurée tragiquement par la perpétuité ? Etc. Trois romanciers ré- guerre mondiale de 14-18. Le prin- pondent : Zoé Valdés, d’origine cipe adopté aujourd’hui est simple : cubaine, qui a publié récemment les journalistes sont partis à la ren- Compartiment fumeurs et La Douleur contre des meilleurs chercheurs, du dollar (Actes Sud), l’académicien scientifiques, sociologues, écrivains Erik Orsenna, auteur de L’Exposition sur chacun des thèmes traités. A partir de leurs informations et de coloniale et du Grand Amour (Seuil), et leurs interprétations naît une vision Norman Spinrad, auteur de science-fic- globale du siècle à venir. -
Non-Convalent Functionalization of Carbon Nanotubes : from the Organization of Surfactants to the Self-Assembly Ofporphyrins
Non-convalent functionalization of carbon nanotubes : From the organization of surfactants to the self-assembly ofporphyrins. Geraud Delport To cite this version: Geraud Delport. Non-convalent functionalization of carbon nanotubes : From the organization of surfactants to the self-assembly ofporphyrins.. Optics / Photonic. Université Paris Saclay (COmUE), 2016. English. NNT : 2016SACLN075. tel-01505288 HAL Id: tel-01505288 https://tel.archives-ouvertes.fr/tel-01505288 Submitted on 11 Apr 2017 HAL is a multi-disciplinary open access L’archive ouverte pluridisciplinaire HAL, est archive for the deposit and dissemination of sci- destinée au dépôt et à la diffusion de documents entific research documents, whether they are pub- scientifiques de niveau recherche, publiés ou non, lished or not. The documents may come from émanant des établissements d’enseignement et de teaching and research institutions in France or recherche français ou étrangers, des laboratoires abroad, or from public or private research centers. publics ou privés. NNTè1èxBGgSACLNBzF T HESEèDEèDOCTORAT DE L’UNIVERSITE P ARIS,SACLAY PREPAREEèA L:ECOLEèNORMALEèSUPERIEUREèDEèCACHAN hECOLE NORMALE SUPERIEUREèDE PARISèSACLAY h ECOLE DOCTORALEèN°èFzx OndesèetèMatière Spécialitéèdeèdoctoratè1èNanophysique P ar M.GéraudmDELPORT Nonzconvalentmfunctionalizationmofmcarbonmnanotubes. Fromètheèorganizationèofèsurfactantsètoètheèself,assemblyèofèporphyrinsf ThèsemprésentéemetmsoutenuemàmOrsayfmlem14mdécembrem2016m:m m m CompositionmdumJurym:mè è MmeèRachelèMEALLET,RENAULTmèè ProfesseuremèPrésidenteèduèJury -
Atomic Structure Details of Nano-Carbon Materials & Their
Atomic Structure Details of Nano-Carbon Materials & Their Implications Sumio Iijima Faculty of Science and Technology, Meijo University National Institute of Advanced Industrial Science and Technology Nanotube Research Center, SAINT and NEC, Meijo University, Nagoya, JAPAN A GEMSEC- CNT-CoE Sponsored Colloquium Host: Mehmet Sarikaya ([email protected]) Time 12:30 p.m., Tuesday, March 16th: Place: Mueller Hall (MSE) #153 Auditorium Nanoscience and nanotechnology deal with nano-scale structures of materials and, therefore, the knowledge and control of material structures at the atomic-resolution are essential. Modern electron microscopes facilitate characterization (via both imaging and spectroscopy) of materials at the atomic resolution. As examples, I demonstrate some latest results on structural characterization of carbon nanotubes,1-4 graphene,5 and boron nitride mono-layer films.6 I would also like to introduce some of industrial applications of nano-carbon materials. 1. K. Suenaga, et al. Nature Nanotech. 2, 358 (2007) 2. Y. Sato, et al., Nano Lett, 7, 3704 (2007). 3. C. H. Jin, et al., Nature Nanotech. 3, 17 (2008). 4. C. H. Jin, et al., PRL, 101, 176102(1)-(4) (2008). 5. Z. Liu, et al., PRL, 102, 015501 (1)-(4) (2009). 6. C. H. Jin, et al., PRL, 102, 195505 (1)-(4) (2009). Professor Sumio Iijima is the discoverer of carbon nanotubes (CNT) (see ref. below). He has contributed to the physics of nanostructured material since 1970s, well before nanotechnology” as a concept existed, and cquired some of the first atomic resolution images of inorganic materials during the late 1970s opening the ways for high resolution electron microscopy imaging that led to the developments of, e.g., heterostructural semiconductors, the bases of today’s microelectronics (integrated circuits used, e.g., in lop-tops, cell phones, etc.). -
Fisica De Lo Imposible
Física de lo imposible www.librosmaravillosos.com Michio Kaku Colaboración de Sergio Barros 1 Preparado por Patricio Barros Física de lo imposible www.librosmaravillosos.com Michio Kaku Prefacio Si una idea no parece absurda de entrada, pocas esperanzas hay para ella. Albert Einstein ¿Será posible algún día atravesar las paredes? ¿Construir naves espaciales que puedan viajar a una velocidad superior a la de la luz? ¿Leer la mente de otras personas? ¿Hacerse invisible? ¿Mover objetos con el poder de nuestra mente? ¿Transportar nuestro cuerpo de manera instantánea por el espacio exterior? Desde niño me han fascinado estas preguntas. Como muchos físicos, en mi adolescencia me sentía hipnotizado por la posibilidad de que hubiera viajes en el tiempo, pistolas de rayos, campos de fuerza, universos paralelos y cosas por el estilo. Magia, fantasía y ciencia ficción constituían un gigantesco campo de juego para mi imaginación. Con ellas empezó mi duradera relación amorosa con lo imposible. Recuerdo cómo veía las reposiciones del viejo Flash Gordon en televisión. Cada sábado me encontraba pegado a la pantalla del televisor, maravillado ante las aventuras de Flash, el doctor Zarkov y Dale Arden y su impresionante despliegue de tecnología futurista: naves a reacción, escudos de invisibilidad, pistolas de rayos y ciudades en el cielo. No me perdía un episodio. El programa me abrió un mundo completamente nuevo. Me fascinaba la idea de viajar un día a un planeta lejano y explorar su territorio. Una vez en la órbita de estas fantásticas invenciones, sabía que mi destino estaba ligado de algún modo a las maravillas de la ciencia que prometía la serie. -
Author Index
PHYSICAL REVIEW B VOLUME 70, NUMBER 24 15 DECEMBER 2004-II Cumulative Author Index All authors of papers published in this volume are listed alphabetically. Full titles are included in each first author’s entry. For Rapid Communi- cations an R precedes the page number. The letters (C) and (BR) following the page number indicate that a paper is a Comment or a Brief Report, respectively. References with (E) are to Errata. Aarab, H. — ͑see Mulazzi, E.͒ B 70, 155206͑15͒ and D. A. Shulyatev — First-order nature of the ferromagnetic ͑ ͒ ͑ ͒ ͒ ͑ ͒ Aarts, J. — see Rusanov, A. Yu. B 70, 024510 1 phase transition in ͑La-Ca MnO3 near optimal doping. B 70, 134414 1 ͑seeYang,Z.Q.͒ B 70, 174111͑1͒ Adams, E. M. — ͑see Nachimuthu, P.͒ B 70, 100101͑R͒͑1͒ ͑see Zhang, Y. Q.͒ B 70, 132407͑BR͒͑1͒ Adams, M. A. — ͑see Knafo, W.͒ B 70, 174401͑1͒ Abalmassov, Veniamin A. and Florian Marquardt — Electron-nuclei Adams, P. W. — ͑see Young, D. P.͒ B 70, 064508͑1͒ spin relaxation through phonon-assisted hyperfine interaction in a Adell, M., L. Ilver, J. Kanski, J. Sadowski, R. Mathieu, and V. quantum dot. B 70, 075313͑15͒ Stanciu — Photoemission studies of the annealing-induced ͑ ͒ Abanov, Ar. and Andrey V. Chubukov — Spin resonance and high- modifications of Ga0.95Mn0.05As. B 70, 125204 15 frequency optical properties of the cuprates. B 70, 100504͑R͒͑1͒ Adelmann, C., B. Daudin, R. A. Oliver, G. A. D. Briggs, and R. E. Abayev, I. — ͑see Kytin, V. G.͒ B 70, 193304͑BR͒͑15͒ Rudd — Nucleation and growth of GaN/AlN quantum dots. -
National Aeronautics and Space Administration Inspiration
National Aeronautics and Space Administration 2007 spinoff Inspiration Innovation Discovery Future Innovative Partnerships Program Developed by On the Cover: Photograph of the International Space Publications and Graphics Department Station taken from the Space Shuttle Atlantis on June 19 2007, at the end of STS-117. The mission NASA Center for AeroSpace Information (CASI) delivered the second and third starboard truss segments (S3/S4) and another pair of solar arrays to the station. Table of Contents 5 Foreword 7 Introduction 8 Executive Summary 18 NASA Technologies Benefiting Society Health and Medicine Circulation-Enhancing Device Improves CPR ........................................................................................................22 Noninvasive Test Detects Cardiovascular Disease ...................................................................................................26 Scheduling Accessory Assists Patients with Cognitive Disorders ..............................................................................30 Neurospinal Screening Evaluates Nerve Function * ..............................................................................................32 Hand-Held Instrument Fights Acne, Tops Over-the-Counter Market ....................................................................34 Multispectral Imaging Broadens Cellular Analysis ...................................................................................................36 Hierarchical Segmentation Enhances Diagnostic Imaging .......................................................................................40 -
June 3, 2021 Future Science Series Medical Nanobots
June 3, 2021 Future Science Series Medical Nanobots – Implications of the Wave Genome, Part I with Ulrike Granögger Introduction: Welcome to a new Solari Future Science Report. My name is Ulrike Granögger, and we will be talking about nanotechnology –medical nanotechnology or medical nanobots, to be precise. The questions are: How real are they, and is it all science fiction? How ‘nanoliterate’ do we need to become in this new age that has come upon us? (To see the visualizations that are mentioned in this report, please watch the video of this presentation on The Solari Report) For many of you, what I will be presenting may not be new because you follow many commentaries of Catherine (The Solari Report), as well as other researchers, journalists, doctors, and scientists who are speaking about the reality of something happening behind the scenes, and on the back of this global crisis that we are going through, namely a transhumanist trend, if not agenda, that is being manifested in our lives. For many of us, we get the feeling that something is happening, but perhaps, we don’t quite know where and what exactly is happening. That’s no wonder because it is happening on a very, very tiny or invisible scale. It is literally happening on the nanolevel. What I would like to give you is a bit of a notion or appreciation, an understanding that this nanoscale of reality that we are entering with new technologies, especially medical technologies, is more than simply a tiny, miniature form of material engineering. It is in fact, a phase transition.