Surface Modification of Materials by Ion Implantations for Industrial And
Total Page:16
File Type:pdf, Size:1020Kb
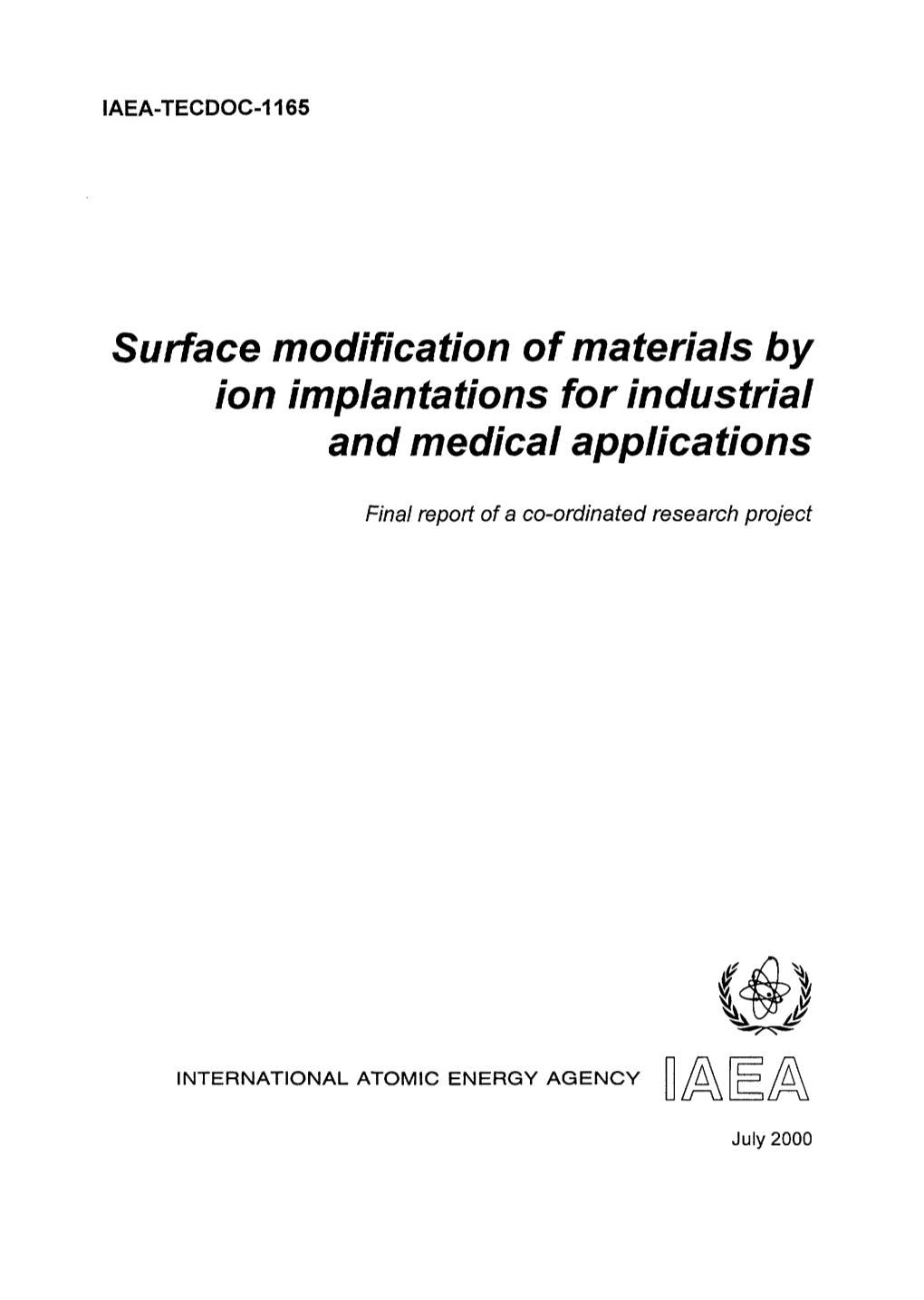
Load more
Recommended publications
-
Surface Modification on Soda Lime and Alumina Silicate Glass Surfaces By
Surface modification on soda lime and alumina silicate glass surfaces by Ion implantation – developments by AGC Amory Jacques, Benjamine Navet. AGC Plasma Technology Solutions, Rue Louis Blériot 12, 6041 Charleroi, Belgium 1. Introduction Ion implantation technologies have been used for many years in electronic industries but never on a large scale for materials surface treatment and especially for flat glass. This technology consists in bombarding in a vacuum chamber the surface of a material with highly energetic ions. The ions penetrate violently into the surface of the material, then stop and lose their energy because of a cascade of collisions. The surface reorganization and the implantation of ions into the surface of the material can modify the physico-chemical properties of various materials from polymers to metals, from glass to crystals. The judicious choice of the implanted ions allows obtaining re-alloying, amorphization or nano-restructuring of the surface, improving the material’s properties or adding new functionalities. 2. Ion source AGC uses the Hardion+ ion gun (Figure 1. left part) developed by its partner Ionics. This ion gun is based on the Electron Cyclotron Resonance (ECR) technology that allows the formation of multi-charged ions (dissociation of the molecule and up to 4 positive charges) thanks to the use of high frequency microwaves (10 GHz) and strong permanent magnets to confine the plasma. Since the ion kinetic energy is the product of its charge and the applied voltage, lower voltages are required to obtain high energy ions (40 kV to have N4+ ions with an energy of 160 keV) compared to ion gun generating mono-charged ions. -
Application of Ion Implantation to Fabricate Optical Waveguides
Kochi University of Technology Academic Resource Repository � Application of Ion Implantation to Fabrication o Title f Optical Waveguides Author(s) QIU, Feng Citation 高知工科大学, 博士論文. Date of issue 2011-09 URL http://hdl.handle.net/10173/774 Rights Text version author � � Kochi, JAPAN http://kutarr.lib.kochi-tech.ac.jp/dspace/ Application of Ion Implantation to Fabricate Optical Waveguides Feng Qiu August, 2011 Abstract This thesis describes the fabrication and characterization of ion implanted waveguides in chalcogenide glasses and neodymium-doped yttrium aluminum garnet (Nd:YAG) crystals. It is demonstrated that an optical waveguide can be obtained by a simple proton implantation in gallium lanthanum sulphide (GLS) glass. Two modes exist in the waveguide at a wavelength of 632.8 nm and the refractive index profile of the waveguide is reconstructed. The near-field pattern of the transmitted light is obtained, and the propagation loss is about 3.2 dB/cm. Based on the data of proton implanted waveguides, a titanium doped gallium lanthanum oxysulfide (Ti:GLSO) glass waveguide is fabricated by the double proton implantation. That waveguide does not exhibit tunneling effect, which is consistent with our design. Based on Raman analyses, we conclude that the glass matrix expansion due to nuclear damage causes the optical barrier formation. Little change in the guiding layer and low propagation loss present that Ti:GLSO glass waveguide may be a candidate of tunable lasers and has a possibility to take place of versatile but expensive Ti-sapphire lasers. Swift-heavy ion implantation (SHI), as a novel technique to fabricate waveguides, is explored to form waveguides in GLS and GLSO glasses. -
Metal-Ion Implanted Elastomers: Analysis of Microstructures and Characterization and Modeling of Electrical and Mechanical Properties
Metal-Ion Implanted Elastomers: Analysis of Microstructures and Characterization and Modeling of Electrical and Mechanical Properties THÈSE NO 4798 (2010) PRÉSENTÉE LE 17 SEPTEMBRE 2010 À LA FACULTÉ SCIENCES ET TECHNIQUES DE L'INGÉNIEUR LABORATOIRE DES MICROSYSTÈMES POUR LES TECHNOLOGIES SPATIALES PROGRAMME DOCTORAL EN MICROSYSTÈMES ET MICROÉLECTRONIQUE ÉCOLE POLYTECHNIQUE FÉDÉRALE DE LAUSANNE POUR L'OBTENTION DU GRADE DE DOCTEUR ÈS SCIENCES PAR Muhamed NIKLAUS acceptée sur proposition du jury: Prof. H. P. Herzig, président du jury Prof. H. Shea, directeur de thèse Dr M. Dadras, rapporteur Dr A. Karimi, rapporteur Dr G. Kofod, rapporteur Suisse 2010 Thought, a brief flash in the middle of night, but a flash which means … everything. Jules Henri Poincaré Abstract This thesis reports on the microstructural analysis of metal ion implanted Polydimethylsiloxane (PDMS), and on the characterization and modeling of its electrical and mechanical properties. Low energy (below 35 keV) metal ion implantation into PDMS forms metal nanoparticles in the top 10 nm to 120 nm of the polymer, creating a metal–insulator composite. Above a certain ion dose, the percolation threshold, the particles form a conductive path. By suitable choice of the volume-ratio between the two constituents (metal atoms and PDMS), one is able to create stretchable electrodes capable of sustaining uniaxial strains of up to 175% while remaining conductive, and remaining operational after 105 cycles at 30% strain. These outstanding properties are especially required for flexible electronic and for polymer actuators and sensors. Low energy metal ion implantation into 30 μm thick PDMS was performed at 10 keV and 35 keV with Low Energy Broad Beam Implanter (LEI), and at 2.5 keV, 5 keV and 10 keV with Filtered Cathode Vacuum Arc (FCVA). -
Application of Antimicrobial Nanoparticles in Dentistry
molecules Review Application of Antimicrobial Nanoparticles in Dentistry Wenjing Song 1,2 and Shaohua Ge 1,2,* 1 Shandong Provincial Key Laboratory of Oral Tissue Regeneration, School of Stomatology, Shandong University, Jinan 250012, China; [email protected] 2 Department of Periodontology, School of Stomatology, Shandong University, Jinan 250012, China * Correspondence: [email protected]; Tel.: +86-(0531)-8838-2123 Academic Editor: Franco Dosio Received: 20 February 2019; Accepted: 8 March 2019; Published: 15 March 2019 Abstract: Oral cavity incessantly encounters a plethora of microorganisms. Plaque biofilm—a major cause of caries, periodontitis and other dental diseases—is a complex community of bacteria or fungi that causes infection by protecting pathogenic microorganisms from external drug agents and escaping the host defense mechanisms. Antimicrobial nanoparticles are promising because of several advantages such as ultra-small sizes, large surface-area-to-mass ratio and special physical and chemical properties. To better summarize explorations of antimicrobial nanoparticles and provide directions for future studies, we present the following critical review. The keywords “nanoparticle,” “anti-infective or antibacterial or antimicrobial” and “dentistry” were retrieved from Pubmed, Scopus, Embase and Web of Science databases in the last five years. A total of 172 articles met the requirements were included and discussed in this review. The results show that superior antibacterial properties of nanoparticle biomaterials bring broad prospects in the oral field. This review presents the development, applications and underneath mechanisms of antibacterial nanoparticles in dentistry including restorative dentistry, endodontics, implantology, orthodontics, dental prostheses and periodontal field. Keywords: application; antimicrobial; nanoparticles; dentistry 1. Introduction The oral cavity constantly encounters a plethora of microorganisms [1]. -
Plasma-Based Ion Implantation and Deposition: a Review of Physics, Technology, and Applications
LBNL-57610 Invited Review for IEEE Transactions on Plasma Science Special Issue on Ion Sources (vol. 33, no.6, 2005) Plasma-based ion implantation and deposition: A review of physics, technology, and applications Jacques Pelletier Centre de Recherche Plasmas-Matériaux-Nanostructures, LPSC, 53 rue des Martyrs, 38036 Grenoble Cedex, France André Anders Lawrence Berkeley National Laboratory, University of California, Berkeley, 1 Cyclotron Road, California 94720, USA Original May 16, 2005 Revised July 4, 2005 Corresponding Author: Dr. André Anders Lawrence Berkeley National Laboratory 1 Cyclotron Road, MS 53 Berkeley, CA 94720, USA Tel. + (510) 486-6745 Fax + (510) 486-4374 e-mail [email protected] This work was supported by the Assistant Secretary for Energy Efficiency and Renewable Energy, Office of Building Technology, of the U.S. Department of Energy under Contract No. DE-AC02-05CH11231. IEEE TPS 0968 –LBNL-57610 – 1 Plasma-based ion implantation and deposition: A review of physics, technology, and applications Jacques Pelletier Centre de Recherche Plasmas-Matériaux-Nanostructures, LPSC, 53 rue des Martyrs, 38036 Grenoble Cedex, France André Anders Lawrence Berkeley National Laboratory, University of California, Berkeley, 1 Cyclotron Road, California 94720, USA Abstract After pioneering work in the 1980s, plasma-based ion implantation (PBII) and plasma-based ion implantation and deposition (PBIID) can now be considered mature technologies for surface modification and thin film deposition. This review starts by looking at the historical development and recalling the basic ideas of PBII. Advantages and disadvantages are compared to conventional ion beam implantation and physical vapor deposition for PBII and PBIID, respectively, followed by a summary of the physics of sheath dynamics, plasma and pulse specifications, plasma diagnostics, and process modelling. -
Using Ion Implantation for Figure Correction in Glass and Silicon Mirror Substrates for X-Ray Telescopes Brandon Chalifoux*A, Claire Burchb, Ralf K
Using ion implantation for figure correction in glass and silicon mirror substrates for X-ray telescopes Brandon Chalifoux*a, Claire Burchb, Ralf K. Heilmannc,Youwei Yaoc, Heng E. Zuod, Mark L. Schattenburgc aDept. of Mechanical Engineering, MIT, Cambridge, MA, USA 02139 bHarvard University, Cambridge, MA, USA 02139 cSpace Nanotechnology Lab, MIT Kavli Institute, Cambridge, MA, USA 02139 dDept. of Aeronautics and Astronautics, MIT, Cambridge, MA USA 02139 *[email protected]; phone: (617) 253-3130; snl.mit.edu ABSTRACT Ion implantation is a method of correcting figure errors in thin silicon or glass substrates. For future high-resolution, high- throughput x-ray observatories, such figure correction may be critical for thin mirror substrates. Ion implantation into both glass and silicon results in surface stress, which bends the substrate. We demonstrate that this stress may be used to improve the surface figure of flat glass wafers. We then describe three effects of ion implantation in glass and silicon. The first effect is the stress resulting from the implanted ions, and the implications for figure correction with each material. Second, each material studied also shows some relaxation after the ion beam is removed; we report on the magnitude of this relaxation and its implications. Finally, the surface stress may affect the strength of implanted materials. We report on ring-on-ring strength tests conducted on implanted glass samples. Keywords: X-ray telescope mirrors, figure correction, ion implantation, glass, silicon 1. INTRODUCTION The Lynx X-ray telescope mission concept1 calls for a sub-arcsecond half-power diameter (HPD) angular resolution with large effective area that requires thin mirrors, which have low stiffness. -
Recent Advanced Applications of Ion-Gel in Ionic-Gated Transistor ✉ ✉ Depeng Wang1, Shufang Zhao1, Ruiyang Yin1, Linlin Li1, Zheng Lou 1 and Guozhen Shen 1
www.nature.com/npjflexelectron REVIEW ARTICLE OPEN Recent advanced applications of ion-gel in ionic-gated transistor ✉ ✉ Depeng Wang1, Shufang Zhao1, Ruiyang Yin1, Linlin Li1, Zheng Lou 1 and Guozhen Shen 1 Diversified regulation of electrons have received much attention to realize a multi-functional transistor, and it is crucial to have a considerable control over the charge carriers in transistors. Ionic gel, as the dielectric material in transistors, facilitates a large capacitance, and high induced-carrier concentrations. This review presents the recent progress in ionic-gated transistors (IGTs) that have good mechanical stability as well as high physical and chemical stability. We first briefly introduce the various applications of IGTs in sensors, neuromorphic transistors, organic transistor circuits, and health detection. Finally, the future perspectives of IGTs are discussed and some possible solutions to the challenges are also proposed. npj Flexible Electronics (2021) 5:13 ; https://doi.org/10.1038/s41528-021-00110-2 INTRODUCTION As a kind of electrolyte, ionic gel not only has good physical/ In the past decade, with the rapid development of the Internet of chemical stability, but also has the characteristics of flexibility, Things and consumer electronics, human demand for high lightweight, and transparency. Therefore, in the field of wearable 1234567890():,; performance, portability, and wear-ability pushed the upgrade of electronic devices, IGT has demonstrated unquestionable adapt- transistor integration density. However, due to the tunneling ability, portability, and functionality. These characteristics have effect and other problems, this trend of continuing to use Moore’s aroused the research enthusiasm for the application of ionic-gel to Law will inevitably slow down. -
Category 2—Page 1
Commerce Control List Supplement No. 1 to Part 774 Category 2—page 1 CATEGORY 2 - MATERIALS PROCESSING LVS: $3000, N/A for MT GBS: Yes, for 2A001.a, Note: For quiet running bearings, see the N/A for MT U.S. Munitions List. List of Items Controlled A. “END ITEMS,” “EQUIPMENT,” “ACCESSORIES,” “ATTACHMENTS,” Related Controls: (1) See also 2A991. (2) “PARTS,” “COMPONENTS,” AND Quiet running bearings are “subject to the “SYSTEMS” ITAR” (see 22 CFR parts 120 through 130.) Related Definitions: Annular Bearing 2A001 Anti-friction bearings, bearing systems Engineers Committee (ABEC). and “components,” as follows, (see List of Items: Items Controlled). Note: 2A001.a includes ball bearing and License Requirements roller elements “specially designed” for the items specified therein. Reason for Control: NS, MT, AT a. Ball bearings and solid roller bearings, having Country Chart (See all tolerances specified by the manufacturer in Control(s) Supp. No. 1 to part accordance with ISO 492 Tolerance Class 2 or 738) Class 4 (or national equivalents), or better, and NS applies to entire entry NS Column 2 having both ‘rings’ and ‘rolling elements’, made MT applies to radial ball MT Column 1 from monel or beryllium; bearings having all tolerances specified in Note: 2A001.a does not control tapered accordance with ISO 492 roller bearings. Tolerance Class 2 (or ANSI/ABMA Std 20 Technical Notes: Tolerance Class ABEC-9, 1. ‘Ring’ - annular part of a radial or other national rolling bearing incorporating one or more equivalents) or better and raceways (ISO 5593:1997). having all the following characteristics: an inner 2. -
Use of Plasma Technologies for Antibacterial Surface Properties of Metals
molecules Review Use of Plasma Technologies for Antibacterial Surface Properties of Metals Metka Benˇcina , Matic Resnik , Pia Stariˇc and Ita Junkar * Department of Surface Engineering, Jožef Stefan Institute, Jamova 39, SI-1000 Ljubljana, Slovenia; [email protected] (M.B.); [email protected] (M.R.); [email protected] (P.S.) * Correspondence: [email protected]; Tel.: +386-1-477-3885 Abstract: Bacterial infections of medical devices present severe problems connected with long-term antibiotic treatment, implant failure, and high hospital costs. Therefore, there are enormous demands for innovative techniques which would improve the surface properties of implantable materials. Plasma technologies present one of the compelling ways to improve metal’s antibacterial activity; plasma treatment can significantly alter metal surfaces’ physicochemical properties, such as surface chemistry, roughness, wettability, surface charge, and crystallinity, which all play an important role in the biological response of medical materials. Herein, the most common plasma treatment techniques like plasma spraying, plasma immersion ion implantation, plasma vapor deposition, and plasma electrolytic oxidation as well as novel approaches based on gaseous plasma treatment of surfaces are gathered and presented. The latest results of different surface modification approaches and their influence on metals’ antibacterial surface properties are presented and critically discussed. The mechanisms involved in bactericidal effects of plasma-treated surfaces are discussed and novel results of surface modification of metal materials by highly reactive oxygen plasma are presented. Keywords: metal biomaterials; antibacterial properties; plasma treatment Citation: Benˇcina,M.; Resnik, M.; Stariˇc,P.; Junkar, I. Use of Plasma Technologies for Antibacterial Surface Properties of Metals. Molecules 2021, 1. -
Scientific Programme
Scientific Programme 20TH INTERNATIONAL CONFERENCE ON SURFACE MODIFICATION OF MATERIALS BY ION BEAMS Lisbon, 9-14 th of July 2017 1 2 Monday - July 10: Ion Beam Processing 08:30 Opening Cerimony by Professor Arlindo Oliveira, President of Instituto Superior Técnico, Universidade de Lisboa 09:00 PL: Leonard Feldman (USA) - Modern Materials and Ion Beams Session I 09:45 Chair: I: André Vantomme (Belgium) - Tailoring the nickel silicide reaction mechanism and texture by ion implantation William Weber 10:15 I: Jani Kotakoski (Austria) - Ion beam manipulation of graphene – from substitutional doping to amorphization 10:45 Coffee-break O01: Ye Yuan (Germany)* O04: Jerome Leveneur (New Zealand) 11:15 Application of Ion Beams to Fabricate and Modify Synthesis of multi-compound magnetic Properties of Dilute Ferromagnet Session IIb nanomaterials with successive ion implantation Session IIa O02: Kenta Kakitani (Japan)* Chair: O05: Marika Schleberger (Germany) 11:35 Chair: The interface between Platinum nanoparticle catalysts Nathalie Defect engineering in 2D materials by energetic ions and an Ar+- irradiated carbon Flyura Moncoffre Djurabekova O06: Alma Dauletbekova (Kazakhstan) O03: Miguel Sequeira (Portugal)* 11:55 Synthesis of nanoprecipitates in SiO2/Si track Swift Heavy Ion Track Morphology in Gallium Nitride templates by electrochemical depositions 12:15 Lunch I: Andrés Redondo-Cubero (Spain) I: Tieshan Wang (China) 14:00 Modulation of semiconductor surfaces and interfaces Surface and sub-surface evolution of Hydrogen ion-implanted at the -
Synthesis and Characterization of Ion-Implanted Gold Nanoparticles
Western Michigan University ScholarWorks at WMU Master's Theses Graduate College 12-2019 Synthesis and Characterization of Ion-Implanted Gold Nanoparticles Nurlathifah Fnu Follow this and additional works at: https://scholarworks.wmich.edu/masters_theses Part of the Physics Commons Recommended Citation Fnu, Nurlathifah, "Synthesis and Characterization of Ion-Implanted Gold Nanoparticles" (2019). Master's Theses. 5109. https://scholarworks.wmich.edu/masters_theses/5109 This Masters Thesis-Open Access is brought to you for free and open access by the Graduate College at ScholarWorks at WMU. It has been accepted for inclusion in Master's Theses by an authorized administrator of ScholarWorks at WMU. For more information, please contact [email protected]. SYNTHESIS AND CHARACTERIZATION OF ION-IMPLANTED GOLD NANOPARTICLES by Nurlathifah A Thesis submitted to the Graduate College in partial fulfillment of the requirements for the degree of Master of Arts Physics Western Michigan University December 2019 Thesis Committee: Asghar N. Kayani, Ph.D., Chair Paul Pancella, Ph.D. Ramakrishna Guda, Ph.D. © 2019 Nurlathifah ACKNOWLEDGEMENTS First and foremost, I would like to thank you for the presence of Allah SWT who has poured so many favors, gifts, faith, healthiness, and patience. So, I can finish this Master Thesis in a timely manner. I would like to especially thank to my research supervisor, Dr. Asghar N. Kayani, who has accepted and involved me in his research, mentoring patiently, taught me many new things about material science until this thesis can be completed. I also thank the thesis committee member, Dr. Paul Pancella and Dr. Ramakrishna Guda, who has been willing to discuss in order to improve my thesis. -
Surface Modification of Stainless Steel by Plasma-Based Fluorine and Silver Dual Ion Implantation and Deposition Yukari SHINONAGA and Kenji ARITA
Dental Materials Journal 2009; 28(6): 735–742 Surface modification of stainless steel by plasma-based fluorine and silver dual ion implantation and deposition Yukari SHINONAGA and Kenji ARITA Department of Pediatric Dentistry, Social and Environmental Medicine, Integrated Sciences of Translational Research, Institute of Health Biosciences, The University of Tokushima Graduate School, Tokushima, Japan Corresponding author, Yukari SHINONAGA; E-mail: [email protected] The aims of this study were to modify dental device surface with fluorine and silver and to examine the effectiveness of this new surface modification method. Stainless steel plates were modified by plasma-based fluorine and silver ion implantation-deposition method. The surface characteristics and brushing abrasion resistance were evaluated by XPS, contact angle and brushing abrasion test. XPS spectra of modified specimens showed the peaks of fluoride and silver. These peaks were detected even after brushing abrasion test. Water contact angle significantly increased due to implantation-deposition of both fluorine and silver ions. Moreover, the contact angle of the modified specimen was significantly higher than that of fluorine only deposited specimen with the same number of brushing strokes. This study indicates that this new surface modification method of fluorine and silver ion implantation- deposition improved the brushing abrasion resistance and hydrophobic property making it a potential antimicrobial device. Keywords: Plasma-based ion implantation-deposition, Fluorine, Silver Received May 7, 2009: Accepted Aug 17, 2009 a high negative potential relative to the chamber wall. INTRODUCTION Ions generated in the overlying plasma accelerate Bacterial colonization and subsequent device infection across the ion sheath formed around the samples and are common complications of medical and dental are implanted into their surfaces24).