Critical Component Failures Reliability-Centered Maintenance, Part 3
Total Page:16
File Type:pdf, Size:1020Kb
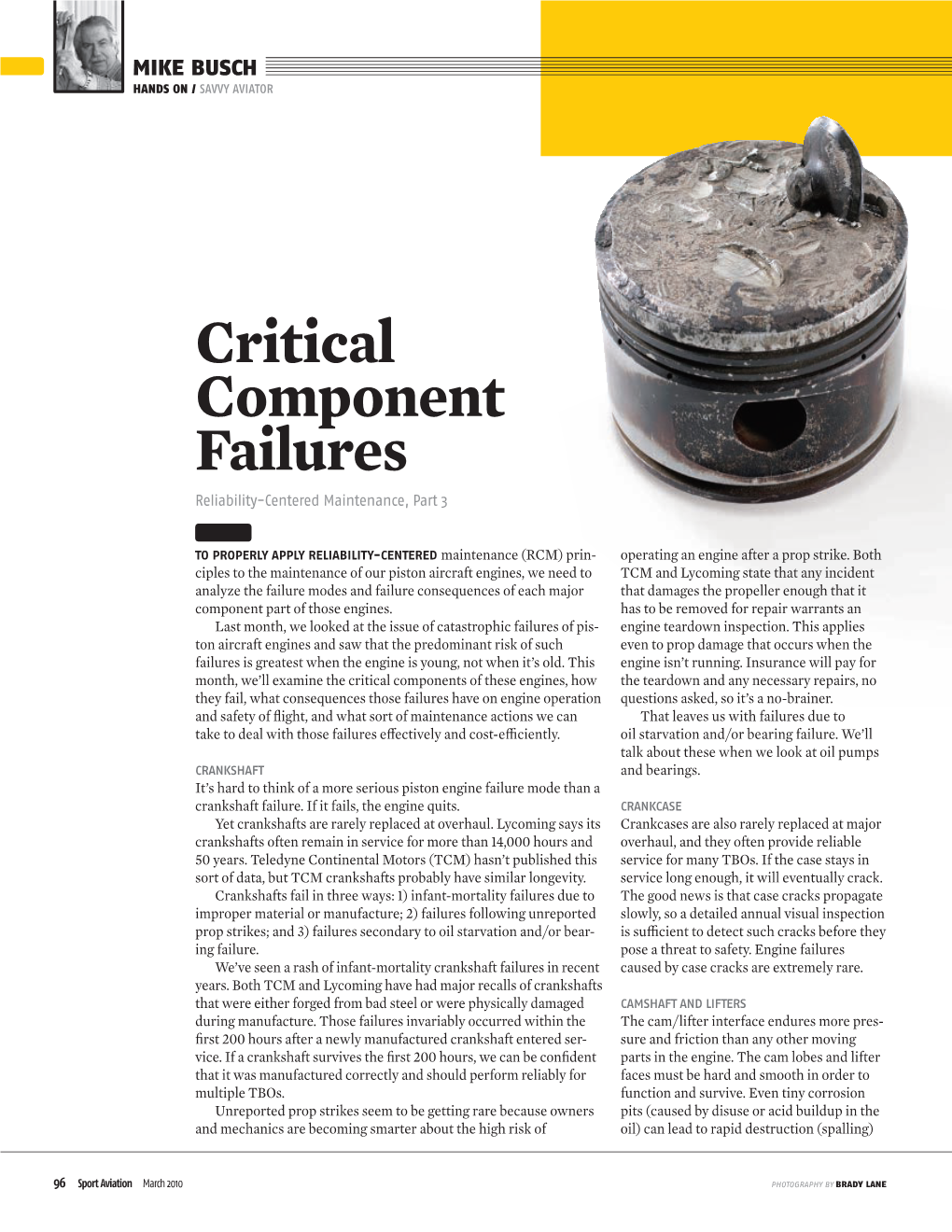
Load more
Recommended publications
-
MANUAL REVISION TRANSMITTAL Manual 146 (61-00-46) Propeller Owner's Manual and Logbook
HARTZELL PROPELLER INC. One Propeller Place Piqua, Ohio 45356-2634 U.S.A. Telephone: 937.778.4200 Fax: 937.778.4391 MANUAL REVISION TRANSMITTAL Manual 146 (61-00-46) Propeller Owner's Manual and Logbook REVISION 3 dated June 2012 Attached is a copy of Revision 3 to Hartzell Propeller Inc. Manual 146. Page Control Chart for Revision 3: Remove Insert Page No. Page No. COVER AND INSIDE COVER COVER AND INSIDE COVER REVISION HIGHLIGHTS REVISION HIGHLIGHTS pages 5 and 6 pages 5 and 6 SERVICE DOCUMENTS LIST SERVICE DOCUMENTS LIST pages 11 and 12 pages 11 and 12 LIST OF EFFECTIVE PAGES LIST OF EFFECTIVE PAGES pages 15 and 16 pages 15 and 16 TABLE OF CONTENTS TABLE OF CONTENTS pages 17 thru 24 pages 17 thru 26 INTRODUCTION INTRODUCTION pages 1-1 thru 1-14 pages 1-1 thru 1-16 DESCRIPTION AND DESCRIPTION AND OPERATION OPERATION pages 2-1 thru 2-20 pages 2-1 thru 2-24 INSTALLATION AND INSTALLATION AND REMOVAL REMOVAL pages 3-1 thru 3-22 pages 3-1 thru 3-24 TESTING AND TESTING AND TROUBLESHOOTING TROUBLESHOOTING pages 4-1 thru 4-10 pages 4-1 thru 4-10 continued on next page Page Control Chart for Revision 3 (continued): Remove Insert Page No. Page No. INSPECTION AND INSPECTION AND CHECK CHECK pages 5-1 thru 5-24 pages 5-1 thru 5-26 MAINTENANCE MAINTENANCE PRACTICES PRACTICES pages 6-1 thru 6-36 pages 6-1 thru 6-38 DE-ICE SYSTEMS DE-ICE SYSTEMS pages 7-1 thru 7-6 pages 7-1 thru 7-6 NOTE 1: When the manual revision has been inserted in the manual, record the information required on the Record of Revisions page in this manual. -
Service Instruction No
652 Oliver Street SERVICE Williamsport, PA. 17701 U.S.A. Telephone +1 (877) 839-7878 (U.S. and Canada) Telephone +1 (570) 327-7222 (International) Fax +1 (570) 327-7101 Email [email protected] INSTRUCTION www.lycoming.com DATE: April 24, 2020 Service Instruction No. 1009BE (Supersedes Service Instruction No. 1009BD) Engineering Aspects are FAA Approved SUBJECT: Time Between Overhaul (TBO) Schedules MODELS AFFECTED: Lycoming Engine Models Defined Herein REASON FOR REVISION: Added a new paragraph at the end of the Operating Hour Time Period TBO section. Added new engine model IO-390-D to Table 1. Revised Table 2 to include separate listings for engine model O-540-F1B5 for the Robinson R44 and R44 Cadet. Revised Note 10 to include reference to Note 6. Revised the paragraph after the CAUTION in the CALENDAR TIME PERIOD TBO section. Revised Note 15,c. NOTICE: Incomplete review of all the information in this document can cause errors. Read the entire Service Instruction to make sure you have a complete understanding of the requirements. This Service Instruction identifies the Calendar Time Period in years and the Operating Hour Time Period in hours of engine operation for the Time Between Overhaul (TBO) for certified Lycoming engine models operated and maintained in compliance with all applicable Lycoming Technical Publications and FAA Airworthiness Directives. The TBOs stated in this Service Instruction do not apply to engines that: a. Do not conform to the original engine model type certificate configuration; b. Have been assembled, repaired, or overhauled with FAA-PMA parts, where the FAA-PMA parts have not been approved for use by Lycoming (contact Lycoming for information regarding FAA-PMA parts approved for use by Lycoming); c. -
Service Bulletin P&Wc S.B
Caravan SERVICE LETTER CAL-72-01 TITLE ENGINE - TRANSMITTAL OF P&WC S.B. NO. 1903R2 EFFECTIVITY MODEL SERIAL NUMBERS 208B 208B5000 and On REASON The purpose of this service letter is to transmit P&WC S.B. No. 1903R2, Turboprop Engine Operating Time Between Overhauls and Hot Section Inspection Frequency. DESCRIPTION Pratt & Whitney Canada (P&WC) has issued P&WC S.B. No. 1903R2 to provide information on recommended basic operating Time Between Overhaul (TBO) and to specify a recommended initial Hot Section Inspection (HSI) frequency. The TBO and HSI intervals are the two major scheduled inspections, and are defined in S.B. No. 1903R2. Caravan EX operators should notice that P&WC S.B. No. 1903R2 specifies a life limit for the motive flow shut-off valve, P/N 3076615-04, of 100 hours. P&WC has stated that they will cover the warranty costs to replace the motive flow shut-off valve P/N 3076615-04 until such time as a newly designed valve with a new part number is specified for use by P&WC. Warranty claims for parts and labor should be filed through Cessna Service Parts and Programs in accordance with standard procedures. COMPLIANCE INFORMATIONAL. This service letter is for informational purposes only. MATERIAL AVAILABILITY P&WC S.B. No. 1903R2, Turboprop Engine Operating Time Between Overhauls and Hot Section Inspection Frequency REFERENCES P&WC S.B. No. 1903R2, Turboprop Engine Operating Time Between Overhauls and Hot Section Inspection Frequency CAL-72-01 March 14, 2013 Page1of1 Cessna Aircraft Company, Cessna Customer Service, P.O. -
Aeroshell Book
THE AEROSHELL BOOK Twentieth Edition 2021 Issued by: Shell Aviation Shell International Petroleum Co. Ltd. Shell Centre York Road London SE1 7NA www.shell.com/aviation 3 COPYRIGHT STATEMENT All rights reserved. Neither the whole nor any part of this document may be reproduced, stored in any retrieval system or transmitted in any form or by any means (electronic, mechanical, reprographic, recording or otherwise) without the prior written consent of the copyright owner. The companies in which Royal Dutch Shell plc directly and indirectly owns investments are separate entities. In this document the expressions “Shell”, “Group” and “Shell Group” are sometimes used for convenience where references are made to Group companies in general. Likewise, the words “we”, “us” and “our” are also used to refer to Group companies in general or those who work for them. These expressions are also used where there is no purpose in identifying specific companies. © 2021 Shell International Petroleum Company Limited. 4 DEFINITIONS & CAUTIONARY NOTE The companies in which Royal Dutch Shell plc directly and indirectly owns investments are separate legal entities. In this The AeroShell Book, “Shell”, “Shell Group” and “Royal Dutch Shell” are sometimes used for convenience where references are made to Royal Dutch Shell plc and its subsidiaries in general. Likewise, the words “we”, “us” and “our” are also used to refer to Royal Dutch Shell plc and its subsidiaries in general or to those who work for them. These terms are also used where no useful purpose is served by identifying the particular entity or entities. ‘‘Subsidiaries’’, “Shell subsidiaries” and “Shell companies” as used in this The AeroShell Book refer to entities over which Royal Dutch Shell plc either directly or indirectly has control. -
Rotax Service Interval Guide Not New News, but a Very Informative Summary
Rotax Service Interval Guide Not new news, but a very informative summary With growing numbers of 912 & 914 series engines in service these days Rotax have gathered a great deal of field experience and have been continually updating the maintenance procedures. Operators of 912 & 914 series engines can obtain current maintenance manuals free of charge, (yep I did say FREE) from the Rotax aircraft engines web site www.rotax-aircraft-engines.com – just click on the documentation tab & fill in the relevant search boxes to obtain the documents you require. You will find parts lists, line & heavy maintenance manuals, service bulletins, operator’s manuals, installation manuals, and a whole host of information you may not have known about. The system is not perfect, for example parts lists for early engines are not available, but it is pretty good & full of useful documentation. We do find that some Rotax owners find the documentation difficult to interpret and occasionally miss things - agreed it can be difficult to see the wood through the trees, especially after translation. As the maintenance & overhaul information has changed over the last couple of years it’s probably a good time to have a recap on how things are now. So before the flying season gets too busy why not take the opportunity to make sure your engine is ready for the new flying season – I’m assured its going to be a good one this year! Figure 1: Documentation page of the Rotax Aircraft Engines website (www.rotax-aircraft-engines.com) MAINTENANCE SCHEDULES The alterations to the maintenance schedules over the years have mainly been to reduce the work required and the parts replaced, so should you want to save a few pennies in these difficult times you better read on. -
Pratt & Whitney's R-4360
The Piston Engine Revolution Pratt & Whitney’s R-4360 Graham White Pratt & Whitney’s 28-cylinder, four-row radial, the R-4360, was the largest and most complex aircraft piston engine to enter production in the West. After cancellation of P & W’s liquid cooled sleeve valve efforts, the R-4360 was rushed into development with an initial rating of over 3000 hp. Although too late for WWII, it played a significant part in postwar military aviation and to a lesser degree, in commercial aviation. Topics covered are: cooling, vibration, bearings, superchargers (including turbocharging and variable discharge turbines), etc. Questions such as how to mount such a behemoth, cowl designs, nacelle design, cooling flow, oil cooling, propellers (including dual rotation) etc., will be addressed. Finally, how many R-4360s are still in service? KEYWORDS: Large aero-engines. Introduction If big is good, then bigger is better, right? Wrong!! The Pratt & Whitney R-4360 was the only aircraft piston engine displacing over 4,000 cubic inches that entered into series production. However, the landscape is littered with attempts at producing a large displacement, high horsepower aircraft engine. This includes air- cooled radials, liquid-cooled in-lines and even liquid-cooled radials. History has indicated that doubling the displacement of an engine causes the development problems to go up exponentially. These problems are associated with cooling, mechanical design, lubrication and weight control. Of course, engines were developed that could produce in excess of 4,000 horsepower, but for how long would they stay together? There is little point in developing a hot-rod that lasts 200 hours between overhauls. -
Manual 154 Revision 4 October 2013
Manual 154 Revision 4 October 2013 Propeller Owner's Manual & Log Book Series HC-A6( )-3( )( ) Six-Blade Lightweight Turbine Propeller Hartzell Propeller Inc. One Propeller Place Piqua, OH 45356 - 2634 U.S.A. Ph: 937-778-4200 (Hartzell Propeller Inc.) Ph: 937-778-4379 (Product Support) Product Support Fax: 937-778-4391 Propeller Owner's Manual 154 © 1987, 1992, 1994, 2013 - Hartzell Propeller Inc. - All rights reserved Inside Cover COVER Rev. 4 Oct/13 Propeller Owner's Manual 154 REVISION HIGHLIGHTS Revision 4, dated October 2013, incorporates the following: • Revised Cover for Revision 4 • Revised Revision Highlights section • Revised Record of Revisions section • Added Airworthiness Limitations Section • Revised List of Effective Pages section Page 1 REVISION HIGHLIGHTS Rev. 4 Oct/13 Propeller Owner's Manual 154 (This page is intentionally blank.) Page 2 REVISION HIGHLIGHTS Rev. 4 Oct/13 Propeller Owner's Manual 154 RECORD OF REVISIONS Rev. No. Issue Date Date Inserted Inserted By Rev 1 5/87 5/87 HPI Rev. 2 5/92 5/92 HPI Rev. 3 1/94 1/94 HPI Rev. 4 10/13 10/13 HPI Page 1 RECORD OF REVISIONS Rev. 4 Oct/13 Propeller Owner's Manual 154 RECORD OF REVISIONS Rev. No. Issue Date Date Inserted Inserted By Page 2 RECORD OF REVISIONS Rev. 4 Oct/13 Propeller Owner's Manual 154 AIRWORTHINESS LIMITATIONS The Airworthiness Limitations section is FAA approved and specifies maintenance required under 14 CFR §§ 43.16 and 91.403 of the Federal Aviation Regulations unless an alternative program has been FAA approved. FAA APPROVED by: ______________________________ date: ____________ Manager, Chicago Aircraft Certification Office, ACE-115C Federal Aviation Administration Rev. -
Methodology to Evaluate Aircraft Piston Engine Durability
METHODOLOGY TO EVALUATE AIRCRAFT PISTON ENGINE DURABILITY Luca Piancastelli, Leonardo Frizziero, Simone Marcoppido DIEM, University of Bologna viale Risorgimento, 2 - 40136 Bologna, Italy e-mail: [email protected] Eugenio Pezzuti University of Rome Tor Vergata Faculty of Engineering via del Politecnico, 1 – 00133 Rome, Italy e-mail: [email protected] ABSTRACT A main problem in aircraft engines is the evaluation of residual life to TBO. The algorithm described in this paper calculates with good reliability the residual life to TBO of a petrol piston engine. The method was tested on small last-generation naturally-aspirated-avio piston engine, and has demonstrated to be effective in several experimental tests. This method is implemented directly in the FADEC or ECU of the engine with very few lines of C-Code. The method can be used also in many industrial engines. This innovative method assumes that only two main factors (load and wear) affect engine durability or Time Between Overhauls (TBO). These two factors are considered as separate and combined with the worst case criteria. The load is assumed to follow a logarithmic law and a formula similar to the Miner‟s law for material fatigue is used, making possible to calculate the “load curve” with the knowledge of only two points. The “wear” curve is related to elapsed engine cycles, and is easy to implement since it is related to technological. The resulting algorithm is very simple and can be implemented in very few software lines with data collected from the already existing sensors. 1. 1. INTRODUCTION speed. In some modern automotive engine some sensors 2. -
About Oil Part 1: What You Should Know by MIKE BUSCH
MIKE BUSCH HANDS ON / SAVVY AVIATOR Some popular aircraft engine oils. All About Oil Part 1: What you should know BY MIKE BUSCH IF I ASKED YOU to explain the purpose of engine oil, you’d probably Last, but certainly not least, oil is say something like “to lubricate moving parts and reduce friction required to protect expensive components and wear.” That’s correct, but lubrication is only one of six key func- like crankshafts, camshafts, lifters, and cyl- tions that oil must perform in your piston aircraft engine. In fact, the inder barrels from rusting during periods lubrication needs of big displacement, slow-turning piston aircraft when the airplane is not fl own. Because we engines are really quite modest, compared to the high-revving tend to fl y our airplanes less often and more engines in our automobiles. Lubrication demands tend to vary with irregularly than we drive our cars, the pre- the square of rpm, so a car engine has far more demanding lubrica- servative requirements of our aircraft tion requirements than an airplane’s engine has. engines are far more demanding than for Oil also serves as a vital coolant for engine components that can’t automotive engines. be air-cooled. Pistons, for example, are exposed to just as much heat of combustion as cylinders, but they don’t have cooling fi ns or expo- sure to airfl ow. The only thing that keeps them from melting is the SIX KEY FUNCTIONS OF OIL large quantity of oil that is splashed and squirted onto the bottom of the pistons to carry away the heat. -
Gas Turbines in Simple Cycle and Combined Cycle Applications
GAS TURBINES IN SIMPLE CYCLE & COMBINED CYCLE APPLICATIONS* Gas Turbines in Simple Cycle Mode Introduction The gas turbine is the most versatile item of turbomachinery today. It can be used in several different modes in critical industries such as power generation, oil and gas, process plants, aviation, as well domestic and smaller related industries. A gas turbine essentially brings together air that it compresses in its compressor module, and fuel, that are then ignited. Resulting gases are expanded through a turbine. That turbine’s shaft continues to rotate and drive the compressor which is on the same shaft, and operation continues. A separate starter unit is used to provide the first rotor motion, until the turbine’s rotation is up to design speed and can keep the entire unit running. The compressor module, combustor module and turbine module connected by one or more shafts are collectively called the gas generator. The figures below (Figures 1 and 2) illustrate a typical gas generator in cutaway and schematic format. Fig. 1. Rolls Royce RB211 Dry Low Emissions Gas Generator (Source: Process Plant Machinery, 2nd edition, Bloch & Soares, C. pub: Butterworth Heinemann, 1998) * Condensed extracts from selected chapters of “Gas Turbines: A Handbook of Land, Sea and Air Applications” by Claire Soares, publisher Butterworth Heinemann, BH, (for release information see www.bh.com) Other references include Claire Soares’ other books for BH and McGraw Hill (see www.books.mcgraw-hill.com) and course notes from her courses on gas turbine systems. For any use of this material that involves profit or commercial use (including work by nonprofit organizations), prior written release will be required from the writer and publisher in question. -
Lycoming Recommended Overhaul Times
652 Oliver Street Williamsport, PA. 17701 U.S.A. SERVICE Tel. 570-323-6181 Fax. 570-327-7101 www.lycoming.textron.com INSTRUCTION DATE: May 25, 2006 Service Instruction No. 1009AS (Supersedes Service Instruction No. 1009AR) SUBJECT: Recommended Time Between Overhaul Periods MODELS AFFECTED: All Lycoming Piston Aircraft Engines The following chart shows the established time between overhaul (TBO) for Lycoming piston aircraft engines. TBO’s can be established on engines that incorporate GENUINE LYCOMING PARTS only, and are not applicable if the engine contains parts other than those supplied by Lycoming. Service experience, variations in operating conditions, and frequency of operation are some of the factors taken into consideration when a TBO is established. Because of variations in the manner in which engines are operated and maintained, Lycoming can give no assurance that any individual operator will achieve the recommended TBO. Continuous service assumes that the aircraft will not be out of service for any extended period of time. Refer to latest revision of Service Letter No. L180 if the aircraft is to be out of service for a period of time greater than 30 days. Engine deterioration in the form of corrosion (rust) and the drying out and hardening of composition materials such as gaskets, seals, flexible hoses and fuel pump diaphragms can occur if an engine is out of service for an extended period of time. Due to the loss of a protective oil film after an extended period of inactivity, abnormal wear on soft metal bearing surfaces can occur during engine start. Therefore, all engines that do not accumulate the hourly period of time between overhauls specified in this publication are recommended to be overhauled in the twelfth year. -
80 Hp (UL/A/F) AIRCRAFT ENGINES
ENGINE TYPE 912 | 80 hp (UL/A/F) AIRCRAFT ENGINES DESCRIPTION • 4-cylinder • 4-stroke liquid/air-cooled engine with opposed cylinders • dry sump forced lubrication with separate oil tank, automatic adjustment by hydraulic valve tappet • 2 carburetors • mechanical fuel pump • dual electronic ignition • electric starter • propeller speed reduction unit FACTS This series was BRP‘s first Rotax engine de- dicated for aircraft application only. The Rotax 912 series is well regarded for its reliability and efficiency and is primarily targeted as the entry level engine in the light aviation industry. The 80 hp version of the Rotax 912 series offers a time between overhauls of 2.000 hours and is available as non-certified (Rotax 912 UL) as well as certified version according to FAR 33 (Rotax 912 F) and JAR 22 (Rotax 912 A). ENGINE DATA WEIGHT kg lb engine with propeller speed reduction unit i = 2.27 (opt. i = 2.43) 55.4 122.0 overload clutch 1.7 3.7 exhaust system 4.0 8.8 external alternator 3.0 6.6 engine suspension frame 2.0 4.4 air guide hood 0.8 1.8 airbox 1.3 2.8 VERSION PERFORMANCE TORQUE MAX RPM kW ft. lb. 1/min Nm ft. lb. 1/min 1/min 912 UL1)/F2)/A3) 59.6 80 5800 103 75.9 4800 5800 Limited for max. 5 min. BORE STROKE DISPLACEMENT FUEL min. MON 83 RON 91* 79.5 mm 3.13 in 61 mm 2.4 in 1211.2 cm3 73.91 cu. in. min. AKI 87* * leaded, unleaded, AVGAS 100LL or Ethanol 10 1) UL = non certified 2) F = certified acc.