Moisture Content Impact on Properties of Briquette Produced from Rice Husk Waste
Total Page:16
File Type:pdf, Size:1020Kb
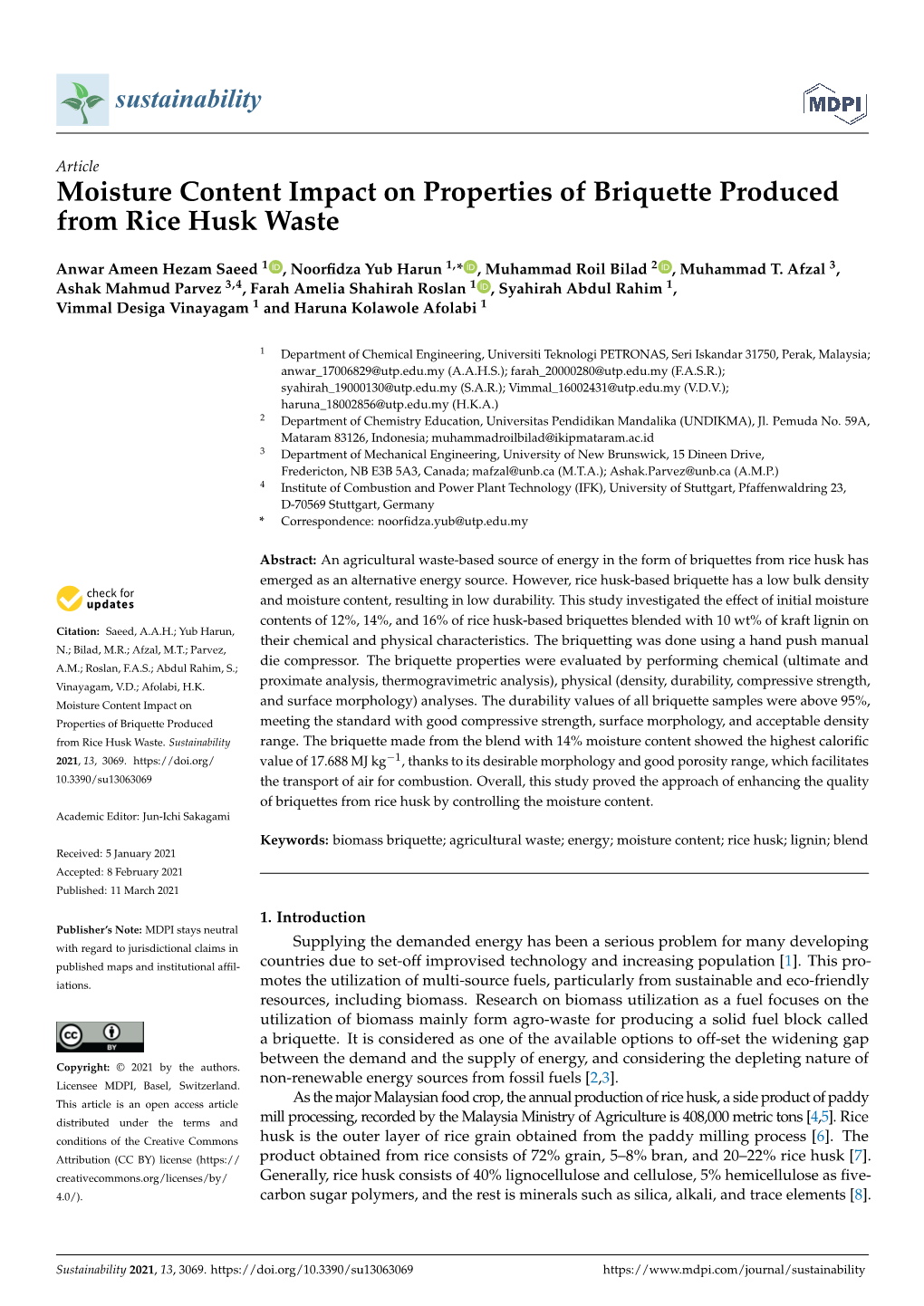
Load more
Recommended publications
-
Opportunities for Using Sawmill Residues in Australia PROCESSING
` PROCESSING PROJECT NUMBER: PNB280-1112 JUNE 2013 Opportunities for using Sawmill Residues in Australia This report can also be viewed on the FWPA website www.fwpa.com.au FWPA Level 4, 10-16 Queen Street, Melbourne VIC 3000, Australia T +61 (0)3 9927 3200 F +61 (0)3 9927 3288 E [email protected] W www.fwpa.com.au Opportunities for using Sawmill Residues in Australia Prepared for Forest & Wood Products Australia by Dean Goble, Malcolm Peck Publication: Opportunities for using Sawmill Residues in Australia Project No: PRB280-1112 This work is supported by funding provided to FWPA by the Australian Government Department of Agriculture, Fisheries and Forestry (DAFF). © 2012 Forest & Wood Products Australia Limited. All rights reserved. Whilst all care has been taken to ensure the accuracy of the information contained in this publication, Forest and Wood Products Australia Limited and all persons associated with them (FWPA) as well as any other contributors make no representations or give any warranty regarding the use, suitability, validity, accuracy, completeness, currency or reliability of the information, including any opinion or advice, contained in this publication. To the maximum extent permitted by law, FWPA disclaims all warranties of any kind, whether express or implied, including but not limited to any warranty that the information is up-to-date, complete, true, legally compliant, accurate, non-misleading or suitable. To the maximum extent permitted by law, FWPA excludes all liability in contract, tort (including negligence), or otherwise for any injury, loss or damage whatsoever (whether direct, indirect, special or consequential) arising out of or in connection with use or reliance on this publication (and any information, opinions or advice therein) and whether caused by any errors, defects, omissions or misrepresentations in this publication. -
Manorbloc Fact Sheet: • Burn at Intense Heat • Burn with Clean Blue
Park Road, Manorhamilton, Co. Leitrim P: 071 985 55075 E: [email protected] Manorbloc Fact Sheet: • Burn at Intense Heat • Burn with clean blue flame • Made from 100% recycled hard wood waste • 100% Irish - manufactured in Manorhamilton, Co. Leitrim • Very low Ash residue • Lower sulphur content than other fossil fuels. • Heat output better than Turf, Lignite Coal and Peat Briquette o Source: Certified by Fire SERT University of Ulster • Heat output figures 18.11 MJ/Kg o Source: Certified by FireSERT University of Ulster • 6% moisture content • Easy to light • Easy pack to carry • Guaranteed Irish • Must be kept in a clean and dry environment • Smokeless • Clean The advantages of the Manorbloc wood briquettes are that they have a lower Ash and/or sulphur content, compared to most other fossil fuels. The carbon dioxide (CO2) balance is even, because wood briquettes release just as much CO2 to the atmosphere as the tree absorbs through growth by photosynthesis. (Source: University of Ulster FireSERT Department) Park Road, Manorhamilton, Co. Leitrim P: 071 985 5075 E: [email protected] Manorbloc Technical Data Sheet: Comparison Chart of Common Fuel Types and Typical Specific Energy Fuel type Specific energy (MJ/kg) Coal, bituminous 24 Methanol 19.7 Manorbloc Wood Briquette, tested in closed container (eg 18.11 Stove) Wood 18.0 Peat briquette 17.7 Coal, lignite 14.0 Sod peat 12.8 Source: University of Ulster FireSERT Department Manorbloc Flammability and Ignition Data – Source: FireSERT Heat Flux (kW/m₂) Average Ignition Time (seconds) 50 21.5 40 38.3 30 66.3 20 171 • The above table explains that at a heat generation output of 50 (kW/m₂) (which is equivalent to heat generated by a large gas burner), Manorbloc wood briquettes will ignite in 21.5 seconds. -
Substituting Imported Fossil Fuels with Biomass Briquettes Can Ease Heavy Fuel Trade Deficits
1 Outline of the presentation • Overview of the project • Cooperation with CIRCOT • By-products selected for development • Biomass fuels as substitutes for wood and fossil fuels • Curbing deforestation • Reducing fuel trade deficits • Conclusions • Project next steps 2 Overview of the project Title Promoting cotton by-products in Eastern and Southern Africa (ESA) Funding source United Nations Development Account (Project 1617K) Countries United Republic of Tanzania, Uganda, Zambia and Zimbabwe Start date March 2016 End date December 2019 Total budget US$ 591,000 Implementing agency United Nations Conference on Trade and Development (UNCTAD) Partners United Nations Economic Commission for Africa (UNECA) Common Market for Eastern and Southern Africa (COMESA) 3 Our project assists countries in commercializing residues from the cotton value chain. COTTON PLANT Planting seed SEED COTTON LINT SEED COTTON STALKS Non-woven Spinning (yarns) (waste) - Medical uses Cake / meal Pulp - Ragtearing - Flour - Particle board - Feed - Fuel briquettes Sewing thread Textiles - Fertilizer - Substrate for - Towels Meat - Bed linens mushroom Oil Weaving yarn cultivation - Salad / cooking oil Industrial - Cosmetics - Canvas - Pharmaceuticals - Footwear - Waterproofing - Belts - Feed Textiles Hulls - Fertilizer - Sheets - Synthetic rubber - Curtains - Sleepwear Knitting yarn - Food packaging - Plastics Industrial Linters - Film - Gloves - Paper - Bags Focus area of UNCTAD project: Industrial "Promoting cotton by-products in Eastern and Southern Africa" Other - -
Biomass Briquette Production: a Propagation of Non-Convention Technology and Future of Pollution Free Thermal Energy Sources
American Journal of Engineering Research (AJER) 2015 American Journal of Engineering Research (AJER) e-ISSN: 2320-0847 p-ISSN: 2320-0936 Volume-04, Issue-02, pp-44-50 www.ajer.org Research Paper Open Access Biomass Briquette Production: A Propagation of Non-Convention Technology and Future of Pollution Free Thermal Energy Sources Manoj Kumar Sharma, Gohil Priyank, Nikita Sharma M.Tech. Scholar, Truba Institute of Engineering & Information Technology, Bhopal (M.P.) India M.Tech. Student, Truba Institute of Engineering & Information Technology, Bhopal (M.P.) India B.Sc. (Biotech), Student, Govt. P.G. College, BHEL, Bhopal (M.P.) India Abstract: Biomass briquettes are a biofuel substitute to coal and charcoal. Briquettes are mostly used in the developing world where cooking fuels are not as easily available. Briquettes are used to heat industrial boilers in order to produce electricity from steam. The briquettes are con-fired with coal in order to create the heat supplied to the boiler. People have been using biomass briquettes since before recorded history. Biomass briquettes are made from agriculture waste and are a replacement for fossils fuels such as oil or coal, and can be used to heat boiler in manufacturing plants. Biomass briquettes are a renewable source of energy and avoid adding fossils carbon to the atmosphere. The extrusion production technology of briquettes is the process of extrusion screw wastes (straw, sunflower husks, buckwheat, etc.) or finely shredded wood waste (sawdust) under high pressure. There is a tremendous scope to bring down the waste of convention energy sources to a considerable level through the development, propagation of non-convention briquettes technology i.e. -
Burn at Intense Heat • Burn with Clean Blue Flame • Made
Park Road, Manorhamilton, Co. Leitrim P: 071 985 5206 W: www.merenda.com/manorbloc E: [email protected] Manorbloc Fact Sheet: Burn at Intense Heat Burn with clean blue flame Made from 100% recycled hard wood waste 100% Irish - manufactured in Manorhamilton, Co. Leitrim Very low Ash residue Lower sulphur content than other fossil fuels. Heat output better than Turf, Lignite Coal and Peat Briquette o Source: Certified by Fire SERT University of Ulster Heat output figures 18.11 MJ/Kg o Source: Certified by FireSERT University of Ulster 6% moisture content Easy to light Easy pack to carry Guaranteed Irish Must be kept in a clean and dry environment Smokeless Clean The advantages of the Manorbloc wood briquettes are that they have a lower Ash and/or sulphur content, compared to most other fossil fuels. The carbon dioxide (CO2) balance is even, because wood briquettes release just as much CO2 to the atmosphere as the tree absorbs through growth by photosynthesis. (Source: University of Ulster FireSERT Department) Park Road, Manorhamilton, Co. Leitrim P: 071 985 5206 W: www.merenda.com/manorbloc E: [email protected] Manorbloc Technical Data Sheet: Comparison Chart of Common Fuel Types and Typical Specific Energy Fuel type Specific energy (MJ/kg) Coal, bituminous 24 Methanol 19.7 Manorbloc Wood Briquette, tested in closed container (eg 18.11 Stove) Wood 18.0 Peat briquette 17.7 Coal, lignite 14.0 Sod peat 12.8 Source: University of Ulster FireSERT Department Manorbloc Flammability and Ignition Data – Source: FireSERT Heat Flux (kW/m₂) Average Ignition Time (seconds) 50 21.5 40 38.3 30 66.3 20 171 The above table explains that at a heat generation output of 50 (kW/m₂) (which is equivalent to heat generated by a large gas burner), Manorbloc wood briquettes will ignite in 21.5 seconds. -
Determination of Flue Gas Emission Values of Cotton and Sesame Stalk Briquettes
Tarım Makinaları Bilimi Dergisi (Journal of Agricultural Machinery Science) 2010, 6 (1), 37 - 43 Determination of Flue Gas Emission Values of Cotton and Sesame Stalk Briquettes Sefai BİLGİN Bartın University, Vocational School of Bartın [email protected] Received (Geliş Tarihi): 19.07.2010 Accepted (Kabul Tarihi): 17.08.2010 Abstract: In this study, flue gas emission values of cotton and sesame stalk briquettes which were produced in a conical type briquetting machine were aimed to determine. In order to determine flue gas emission values, the briquettes were burned in a traditional bucket type stove used for household heating. In the study, flue gas emissions such as CO, CO2, SO2, NOx, H2S and O2, flue gas temperature and combustion efficiency were measured by means of flue gas analyzer. At the end of this study, when the combustion process had a steady-state condition, the flue gas emission values measured during burning of the briquettes were found to be very low. When the combustion process had a steady-state condition, the lowest CO emissions were 57 ppm and 160 ppm, average NOx emissions were 196 ppm and 146 ppm, H2S emissions were 37 ppm and 27 ppm, CO2 emissions were 7.92% and 7.41% and O2 emissions were 12.81% and 13.33% for cotton and sesame stalk briquettes, respectively. During the combustion process, cotton and sesame stalk briquettes had no SO2 emission. During the steady-state condition, the average flue gas temperature and combustion efficiency for cotton and sesame stalk briquettes were 400 C and 403 C, 70% and 69%, respectively. -
UNITED STATES PATENT OFFICE 2,164,933 PROCESS of BAKING FUEL BRIQUETTES Henry F
Patented July 4, 1939 2,164,933 UNITED STATES PATENT OFFICE 2,164,933 PROCESS OF BAKING FUEL BRIQUETTES Henry F. Maurel, Providence, It. I., assignor to Maurel Investment, Corporation, Providence, It. I., a, corporation of Ithode Island No Drawing. Application November 7, 1934, Serial No. I751,880 1 Claim. (Cl, 202-—19) formed of bituminous coal and any suitable This invention relates to a process of baking binder which may be preferably an asphalt base fuel briquettes. fuel oil or a similar hydrocarbon residuum. It The principal objects of this invention are to would seem unnecessary to add a binder for the provide for hardening at least the external sur the surface dust reason that bituminous coal already contains the 1' face of each briquette to make elements of the binder, but I ?nd that, if the less and clean as well as hard; to provide for binder is not used, the briquettes subjected to the coking at an indicated temperature much lower process to be described will swell up into all sorts than that actually required for coking; to secure of shapes and burst and useful briquettes will not. this result by providing for the extraction from be produced. 10 the briquettes themselves of the additional heat These briquettes are introduced into an oven necessary; to provide an effective procedure to in the same manner as in the aforementioned control the exothermic reaction for this purpose; patent and subjected immediately after entering to make this process applicable, with some modi the oven on an endless conveyor to an initial tem ?cations, to bituminous and anthracite coals as perature of about 1000° F. -
Are Peat and Sawdust Truly Improve Quality of Briquettes As Fuel Alternative?
Journal of Sustainable Development; Vol. 10, No. 5; 2017 ISSN 1913-9063 E-ISSN 1913-9071 Published by Canadian Center of Science and Education Are Peat and Sawdust Truly Improve Quality of Briquettes as Fuel Alternative? Andi Bustan1 & Muhammad Arsyad2 1 Faculty of Education, Palangkaraya University, Central Kalimantan, Indonesia 2 Department of Agricultural Socio-economics, Faculty of Agriculture, Hasanuddin University, Makassar, South Sulawesi, Indonesia Correspondence: Andi Bustan, Faculty of Education, Palangkaraya University, Central Kalimantan, 73111, Indonesia. Tel: 62-822-5511-3782. E-mail: [email protected] Received: May 17, 2017 Accepted: July 28, 2017 Online Published: September 29, 2017 doi:10.5539/jsd.v10n5p61 URL: https://doi.org/10.5539/jsd.v10n5p61 Abstract The availability of energy and fuel is always a critical issue, and currently the increasing scarcity and price of kerosene is causing problems for both households and businesses. For example, chicken farmers in Central Kalimantan need to maintain the room temperature when nursing chicks up to 12 days old, and currently have few alternatives to kerosene stoves. Non-carbonized briquettes made from a mix of peat and sawdust can provide an alternative fuel source. The sawdust is available from local sawmills, which is otherwise an unutilized waste product that is burnt off, so adding to local smoke pollution. This study was conducted to determine the optimal composition and manufacturing process to produce bricks that have a maximal calorific content whilst maintaining a long burning time and a reduced tendency to break. Analyses in the laboratory showed that the highest calorific content obtainable was 19 020.63 kJ/kg with a peat/sawdust ratio of 2:1 (20 kg of peat and 10 kg of sawdust). -
Haiti Coal Briquetting Feasibility Study Inventory of Resource Data and Collection of Samples
DEPARTMENT OF THE INTERIOR U.S. GEOLOGICAL SURVEY Haiti coal briquetting feasibility study Inventory of resource data and collection of samples by I/ Jean N. Weaver Open-File Report 86-566 A cooperative Coal Exploration Project with the Direction des Ressources Energetiques, Ministere des Mines et des Ressources Energetiques, Republique d'Haiti, under the auspices of the Agency for International Development This report is preliminary and has not been reviewed for conformity with U.S. Geological Survey editorial standards and stratigraphic nomenclature. V U.S. Geological Survey, Denver, CO 1986 CONTENTS ABSTRACT " 1 INTRODUCTION 2 Purpose 2 Location 3 Previous Work 3 GEOLOGY 7 FIELD TECHNIQUES 7 RECOMMENDATIONS 9 Project Activities 9 Equipment 10 SUMMARY AND ACKNOWLEDGMENTS 11 REFERENCES 12 ATTACHMENT 1 13 ILLUSTRATIONS FIGURE 1. Location Map 4 2a. Index Map of Haiti 5 2b. Location of coal fields 6 3. Schematic measured section 9 HAITI COAL BRIQUETTING FEASIBILITY STUDY INVENTORY OF RESOURCE DATA AND COLLECTION OF SAMPLES By Jean N. Weaver U.S. Geological Survey ABSTRACT The purpose of the project was twofold: 1) to evaluate the available coal resource data of Haiti from which a program of activities might be identified that could lead to an assessment of the coal resources 2) to supervise the collecting, packing, and shipping of a 500-pound coal sample for analyses in the United States by the University of North Dakota Energy Research Center. A site in the Maissade/5e coal field was selected for sampling. Analyses of the coal samples will focus on the possibility of converting the lignite into smokeless fuel briquettes. -
Wood Energy: Definition, Objectives and Challenges in South East Europe
Wood energy: definition, objectives and challenges in South East Europe Prof. Dr Branko Glavonjic, University of Belgrade Faculty of Forestry, Belgrade, Serbia Workshop on “Policy options for wood energy”, Dubrovnik 17 - 20 November 2009 CONTENT Primary energy production in SEE countries: current situation and RES participation Potentials of the South East European countries for the production of energy-generating products based on wood biomass Market of wood based energy-generating products in the selected SEE countries – current situation Wood energy:objectives and challenges in SEE countries Workshop on “Policy options for wood energy”, Dubrovnik 17 - 20 November 2009 Surveying countries Albania Bosnia and Herzegovina Croatia Macedonia Montenegro Serbia Workshop on “Policy options for wood energy”, Dubrovnik 17 - 20 November 2009 I. Primary energy production in SEE countries: current situation and RES participation Hydro Serbia, 2008. power Hydro Other Macedonia, 2008. Natural 9% Natural power 8% Gas Gas 3% 2% 3% Coal Oil Coal 52% 8% 79% RES Oil 2% 28% RES 6% Ist group Hydro Bosnia and Herzegovina, power 9% 2006. Natural Coal Gas 60% 6% Oil RES 22% 3% Workshop on “Policy options for wood energy”, Dubrovnik 17 - 20 November 2009 I. Primary energy production in SEE countries: current situation and RES participation RES Oil Croatia, Hydro Coal RES 8% 19% power 1% 20% Albania, 2007. 2007. 24% Hydro power Natural 22% Gas 2% Natural gas 51% Oil 53% IInd group Montenegro, 2004. Coal 32% RES 5% Other 1% Hydro power 62% Workshop on “Policy -
Bosnia and Herzegovina Investment Opportunities
BOSNIA AND HERZEGOVINA INVESTMENT OPPORTUNITIES TABLE OF CONTENTS BOSNIA AND HERZEGOVINA KEY FACTS..........................................................................6 GENERAL ECONOMIC INDICATORS....................................................................................7 REAL GDP GROWTH RATE....................................................................................................8 FOREIGN CURRENCY RESERVES.........................................................................................9 ANNUAL INFLATION RATE.................................................................................................10 VOLUME INDEX OF INDUSTRIAL PRODUCTION IN B&H...............................................11 ANNUAL UNEMPLOYMENT RATE.....................................................................................12 EXTERNAL TRADE..............................................................................................................13 MAJOR FOREIGN TRADE PARTNERS...............................................................................14 FOREIGN DIRECT INVESTMENT IN B&H.........................................................................15 TOP INVESTOR COUNTRIES IN B&H..............................................................................17 WHY INVEST IN BOSNIA AND HERZEGOVINA..............................................................18 TAXATION IN BOSNIA AND HERZEGOVINA..................................................................19 AGREEMENTS ON AVOIDANCE OF DOUBLE TAXATION...............................................25 -
Charcoal Briquette Production Using Orange Bagasse and Corn Starch
313 A publication of CHEMICAL ENGINEERING TRANSACTIONS VOL. 49, 2016 The Italian Association of Chemical Engineering Online at www.aidic.it/cet Guest Editors: Enrico Bardone, Marco Bravi, Tajalli Keshavarz Copyright © 2016, AIDIC Servizi S.r.l., ISBN 978-88-95608-40-2; ISSN 2283-9216 DOI: 10.3303/CET1649053 Charcoal Briquette Production Using Orange Bagasse and Corn Starch Karine Zanella*a, José L. Gonçalvesb, Osvaldir P. Tarantoa a School of Chemical Engineering, University of Campinas, 500, Albert Einsten Ave., Campinas – SP, Brazil, Zip Code 13083 -852 b Center of Semiconductor Components and Nanotechnologies, Univesity of Campinas, 90 João Pandiá Calógeras St., Campinas - SP, Brazil, Zip Code 13083-870 [email protected] Carbonization technique (muffle furnace at 450 °C) was applied on the orange bagasse (solid wastes) to produce charcoal briquettes, using corn starch as binder and a 1.0 ton-force manual hydraulic press. The tests applied on the orange charcoal powder and on the orange charcoal powder with corn starch (5, 10 and 15 % w/w) were the proximate analysis, the elemental analysis and the determination of the higher heating value HHV) . On the other hand, some tests were carried out on the orange charcoal briquettes, which were the determination of density and the mechanical strength (compressive strength and friability). The results showed that the obtained orange charcoal (OC) has a significant high heating value of 29,000 J/g, and can be used in different processes. When mixed with the binder, its HHV has a small decrease, 27,611 J/g to OC with 5 % of corn starch, 26,857 J/g to OC with 10 % of corn starch and 26,476 J/g to OC with 15 % of corn starch, but still they are considered high values.