210R-93 Erosion of Concrete in Hydraulic Structures
Total Page:16
File Type:pdf, Size:1020Kb
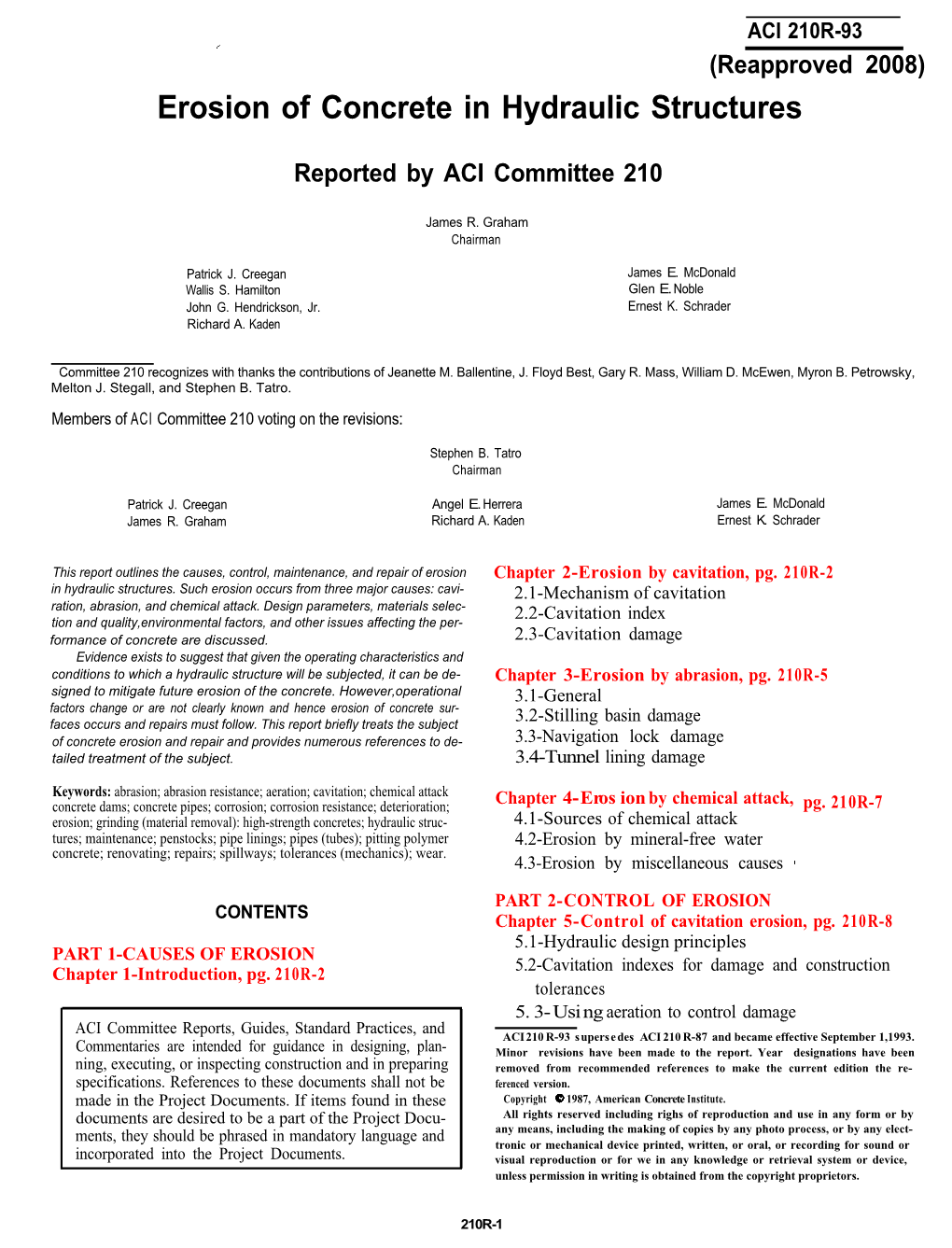
Load more
Recommended publications
-
Dolen, Timothy P
Historical Development of Durable Concrete for the Bureau of Reclamation Timothy P. Dolen Research Civil Engineer - Senior Technical Specialist Materials Engineering and Research Laboratory Technical Service Center - Denver, Colorado Introduction The Bureau of Reclamation infrastructure stretches across many different climates and environments in the seventeen western states. Many of the dams, spillways, pumping plants, power plants, canals, and tunnels are constructed with concrete. These structures were built from Arizona to Montana, across the plains and in the mountains and deserts. Concrete structures had to remain durable to resist both the design loads and the natural environments of the western climate zones. Many natural environments can be quite destructive to concrete and the earliest Reclamation projects were faced with a variety of durability problems. The state-of-the-art of concrete construction advanced from hand mixing and horse and wagon transporting operations to automated mixing plants, underwater canal construction, and pumping and conveyor placing. This paper first overviews the challenges facing concrete construction in the beginning of the 20th Century. It then traces the Bureau of Reclamation’s role in the development of durable concrete to resist the environments of the west. What is Concrete? Before we begin, we must first understand what is concrete, the most versatile building material. The American Concrete Institute defines concrete as “a composite material that consists essentially of a binding medium within which are embedded particles or fragments of aggregate, usually a combination of fine aggregate and coarse aggregate; in portland-cement concrete, the binder is a mixture of portland cement and water.”1 The earliest concretes date at least as far back as early Roman times including the aqueducts and the historic Pantheon in Rome. -
National Register of Historic Places Registration Form
NPS Form 10-900 OMB No. 10024-0018 (Oct. 1990) United States Department of the Interior ,C£$ PftRKSERVIC National Park Service National Register of Historic Places Registration Form This form is for use in nominating or requesting determinations for individual properties and districts. See instructions in How to Complete the National Register of Historic Pla Registration Form (National Register Bulletin 16A). Complete each item by marking "x" in the appropriate box or by entering the information requested. If an item does not ap property being documented, enter "N/A" for "not applicable." For functions, architectural classification, materials, and areas of significance, enter only categories and subcatei instructins. Place additional entries and narrative items on continuation sheets (NPS Form 10-900a). Use a typewriter, word processor, or computer, to complete all items. 1. Name of Property historic name: American Falls Reservoir Flooded Townsite other name/site number: 2. Location street & number American Falls Reservoir [ ] not for publication city or town American Falls ______ [ X ] vicinity state: Idaho code: ID county: Power code: 077 zip code: 83211 3. State/Federal Agency Certification As the designated authority under the National Historic Preservation Act, as amended, I hereby certify that this [X] nomination [ ] request for determination of eligibility meets the documentation standards for registering properties in the National Register of Historic Places and meets the procedural and professional requirements set forth in 36 -
Early Irrigation in the Boise Valley By, Paul L. Murphy Source
Early Irrigation in the Boise Valley By, Paul L. Murphy Source: Pacific Northwest Quarterly, XLIV (October, 1935), 177-184. Agriculture is the dominant feature of Idaho's economy and the major portion of Idaho's agricultural development is predicated upon irrigation. The early pioneering efforts, ambitious as they were, merely opened the door to the vast projects that followed. The difficulties faced and overcome by the early developers were legion: eastern capital had to be enlisted and fluctuations in the money market compounded this problem; the problems of trial-and-error methods in actual construction while the engineering science developed; increasing operational expenses; inadequate legislative statutes to determine the rights and use of the water and the ensuing litigation in the courts all hampered development. The story of how these problems were solved in the early development of irrigation in the Boise Valley is told in the following informative article by Professor Paul L. Murphy. Those interested in further reading will find considerable material available. A classic study is William E. Smythe, The Conquest of Arid America (1899, 1905; reprint ed., Seattle, 1969). George Thomas, Early Irrigation in the Western States (Salt lake City, 1948), is valuable. Mikel H. Williams, The History 6f Development and Current Status of the Carey Act in Idaho (Boise, 1970), is informative. Students should consult the Biennial Report of the Department of Reclamation to the Governor of Idaho, beginning in 1919-1920. A valuable survey of Idaho irrigation is in "Mineral and Water Resources of Idaho," a report prepared by the United States Geological Survey (Washington: 1964). -
Snake River Flow Augmentation Impact Analysis Appendix
SNAKE RIVER FLOW AUGMENTATION IMPACT ANALYSIS APPENDIX Prepared for the U.S. Army Corps of Engineers Walla Walla District’s Lower Snake River Juvenile Salmon Migration Feasibility Study and Environmental Impact Statement United States Department of the Interior Bureau of Reclamation Pacific Northwest Region Boise, Idaho February 1999 Acronyms and Abbreviations (Includes some common acronyms and abbreviations that may not appear in this document) 1427i A scenario in this analysis that provides up to 1,427,000 acre-feet of flow augmentation with large drawdown of Reclamation reservoirs. 1427r A scenario in this analysis that provides up to 1,427,000 acre-feet of flow augmentation with reservoir elevations maintained near current levels. BA Biological assessment BEA Bureau of Economic Analysis (U.S. Department of Commerce) BETTER Box Exchange Transport Temperature Ecology Reservoir (a water quality model) BIA Bureau of Indian Affairs BID Burley Irrigation District BIOP Biological opinion BLM Bureau of Land Management B.P. Before present BPA Bonneville Power Administration CES Conservation Extension Service cfs Cubic feet per second Corps U.S. Army Corps of Engineers CRFMP Columbia River Fish Mitigation Program CRP Conservation Reserve Program CVPIA Central Valley Project Improvement Act CWA Clean Water Act DO Dissolved Oxygen Acronyms and Abbreviations (Includes some common acronyms and abbreviations that may not appear in this document) DREW Drawdown Regional Economic Workgroup DDT Dichlorodiphenyltrichloroethane EIS Environmental Impact Statement EP Effective Precipitation EPA Environmental Protection Agency ESA Endangered Species Act ETAW Evapotranspiration of Applied Water FCRPS Federal Columbia River Power System FERC Federal Energy Regulatory Commission FIRE Finance, investment, and real estate HCNRA Hells Canyon National Recreation Area HUC Hydrologic unit code I.C. -
Chile, the Biobío, and the Future of the Columbia River Basin Jerrold A
Idaho Law Review Volume 53 | Number 1 Article 7 April 2017 Chile, the Biobío, and the Future of the Columbia River Basin Jerrold A. Long Shana Hirsch Jason Walters Follow this and additional works at: https://digitalcommons.law.uidaho.edu/idaho-law-review Recommended Citation Jerrold A. Long, Shana Hirsch & Jason Walters, Chile, the Biobío, and the Future of the Columbia River Basin, 53 Idaho L. Rev. 239 (2017). Available at: https://digitalcommons.law.uidaho.edu/idaho-law-review/vol53/iss1/7 This Article is brought to you for free and open access by Digital Commons @ UIdaho Law. It has been accepted for inclusion in Idaho Law Review by an authorized editor of Digital Commons @ UIdaho Law. For more information, please contact [email protected]. CHILE, THE BIOBÍO, AND THE FUTURE OF THE COLUMBIA RIVER BASIN JERROLD A. LONG,* SHANA HIRSCH,** JASON WALTERS*** TABLE OF CONTENTS I. INTRODUCTION ................................................................ 240 II. FINDING LESSONS IN THE DIFFERENCES: WHY COMPARING CHILE AND THE COLUMBIA RIVER BASIN MAKES SENSE .................................................. 242 A. Climate Change and Altered Hydrologic Regimes ..... 242 B. United States Analogues to the Biobío ....................... 244 III. WATER RESOURCE HISTORIES .................................. 247 A. “Redemption” of the arid lands—Water resource development in the Columbia River Basin ................ 247 B. Dams and the Engines of Economic Development in Chile ....................................................................... -
American Falls Reservoir Is the Largest Reservoir of the Project
Finding of No Significant Impact Final Environmental Assessment Maintenance and Rehabilitation of Spillway and Dam Structures at American Falls Dam, Minidoka Project, Power County, Idaho U.S. Department of the Interior Bureau of Reclamation Pacific Northwest Region Snake River Area Office PN FONSI # 19-4 Introduction The Bureau of Reclamation (Reclamation) has prepared this Finding of No Significant Impact (FONSI) to comply with the Council of Environmental Quality (CEQ) regulations for implementing procedural provisions of the National Environmental Policy Act (NEPA). This document briefly describes the proposed action, other alternatives considered, the scoping process, Reclamation’s consultation and coordination activities, mitigation, and Reclamation’s finding. The Final Environmental Assessment (EA) fully documents the analyses of the potential environmental effects of implementing the changes proposed. Location and Background The Minidoka Project (Project) was authorized by the Secretary of the Interior in 1904 and was the first Reclamation project constructed in Idaho. It is located in the Snake River Basin in the southeastern part of the state. American Falls Dam, completed in 1927, is a 94-foot-high composite concrete and earth gravity-type dam on river mile 714.7 of the Snake River near American Falls, Idaho. With a storage capacity of 1,700,000 acre-feet, American Falls Reservoir is the largest reservoir of the Project. The dam itself is located in Power County, Idaho, but the reservoir stretches northeast into both Bingham and Bannock Counties. American Falls Dam and Reservoir comprise a multi-purpose facility from which principle benefits include irrigation, power generation (through a powerplant owned and operated by Idaho Power), flood control, fish and wildlife resources, and recreation. -
Water Utilizatjq^ in the Snake Rivm Basin
UNITED STATES DEPARTMENT OF THE INTERIOR Harold L. Ickes, Secretary GEOLOGICAL SURVEY W. C. Mendenhall, Director Water-Supply Paper 657 WATER UTILIZATJQ^ IN THE SNAKE RIVM BASIN ""-^r B<5 °o ^ «-? %*-« ^t«4 ____ ^n -" wC> v r v*> ^ /-^ T"i --O ^ o f^* t TA ^-- ± BY ^^^ W. G. HOYT \, ^ r-^ Co WITH A PREFACE ^ -^ "^ o o. ^ HERMAN STABLER ' ^ ^ e 'r1 t<A to ^ ^ >Jt C---\ V*-O r&1 """^*_> ® p <,A -o xi CP ^3 P* O ^ y» * "^ 0V - f\ *"^ . , UNITED STATKS GOVERNMENT PRINTING OFFICE WASHINGTON: 1935 For sale by the Superintendent of Documents, Washington, D.C. - - - Price $1.00 (Paper cover) CONTENTS Page Preface, by Herman Stabler._______________________________________ ix Abstract _________________________________________________________ 1 Introduction__ _ _________________________________________________ 2 Purpose and scope of report.___________________________________ 2 Cooperation and base data.____________________________________ 3 Index system.._______________________________________________ 6 General features of Snake River Basin.______________________________ 6 Location and extent.__________________________________________ 6 Geographic and topographic features.___________________________ 7 Snake River system._____-_-----_____-_________-_____-_-__-_.._ 7 Tributaries to Snake River.____________________________________ 9 Historical review-__________________________________________________ 20 Scenic and recreational features.-...________________________________ 21 Climate____________________________A____ ___________________ 23 Natural vegetation_________________-_____-____________----__-_---._ -
(E.1-2) Geomorphology of the Hells Canyon Reach of the Snake River
Geomorphology of the Hells Canyon Reach of the Snake River Steve Miller, CH2M HILL Dick Glanzman, CH2M HILL Sherrill Doran, CH2M HILL Shaun Parkinson, Idaho Power Company John Buffington, University of Idaho and Jim Milligan, University of Idaho (Ret.) Technical Report Appendix E.1-2 May 2002 Revised July 2003 Hells Canyon Complex FERC No. 1971 Copyright © 2003 by Idaho Power Company Idaho Power Company Geomorphology of the Snake River Basin and Hells Canyon CONTENTS Chapter Page Definitions...................................................................................................................................... xi Acronyms.................................................................................................................................... xvii Executive Summary.....................................................................................................................C-1 Preface..........................................................................................................................................C-5 1. Introduction and Geologic and Geomorphic History............................................................... 1-1 1.1. Introduction ...................................................................................................................... 1-2 1.2. Current Physiographic Description .................................................................................. 1-3 1.3. Pre-Quaternary Geologic History.................................................................................... -
Water Supply Summary Presentation
May 2017 Water Supply Briefing National Weather Service, Northwest River Forecast Center Telephone Conference: 1-888-677-0012 Pass Code: 91999 Presentation available after brief at: www.nwrfc.noaa.gov/presentations/presentations.cgi Kevin Berghoff, NWRFC [email protected] (503) 326-7291 Water Supply Summary www.nwrfc.noaa.gov/ws/ . West of Cascades: . Well above normal . East of Cascades: . Well above normal throughout the Upper Columbia and Snake River basins . Primary drivers: . Snowpack distribution . Weather yet to come Volume Forecast Inputs . Observed Conditions: . Precipitation . Temperature Model “states” . Snowpack . Soil moisture . Future Conditions (Anticipated and Statistical): . 0, 5, or 10 days of QPF/QTF . Ensemble of precipitation Model and temperature climatology “ forcings ” appended thereafter Observed Monthly Precipitation www.nwrfc.noaa.gov/water_supply/wy_summary Observed Temperature Departures Water Year 2016 / 2017 comparison http://www.nwrfc.noaa.gov/water_supply/wy_summary/wy_summary.php?tab=2 Observed Wateryear Precipitation www.nwrfc.noaa.gov/water_supply/wy_summary WY 2016 WY 2017 DIVISION NAME % NORM % NORM Columbia River above Arrow Lakes 94 113 Kootenai River 102 135 Pend Oreille River 102 132 Spokane River 107 132 Columbia River above Grand Coulee 101 113 Snake River above Amercan Falls 93 152 Snake River above Ice Harbor 101 138 Columbia River above The Dalles 103 129 Western Washington 111 112 Western Oregon 113 141 Observed Snowpack Conditions www.nwrfc.noaa.gov/snow May 4, 2016 May 4, 2017 . May 2016 Snowpack . Warm temperatures in April – Record SWE loss throughout region . May 2017 Snowpack . Near record SWE in Snake – well above average in Upper Columbia . Observed snow water equivalent (SWE) values provided by: . -
By L.C. Kjelstrom Water-Resources Investigations Report 87-4063
ESTIMATES OF GAINS AND LOSSES FOR RESERVOIRS ON THE SNAKE RIVER FROM BLACKFOOT TO MILNER, IDAHO, FOR SELECTED PERIODS, 1912 TO 1983 By L.C. Kjelstrom U.S. GEOLOGICAL SURVEY Water-Resources Investigations Report 87-4063 Prepared in cooperation with IDAHO WATER DISTRICT 01 Boise, Idaho 1988 DEPARTMENT OF THE INTERIOR DONALD PAUL HODEL, Secretary U.S. GEOLOGICAL SURVEY Dallas L. Peck, Director For additional information Copies of this report can write to: be purchased from: District Chief U.S. Geological Survey U.S. Geological Survey, WRD Books and Open-File Reports 230 Collins Road Federal Center, Bldg. 810 Boise, ID 83702 Box 25425 (208) 334-1750 Denver, CO 80225 (303) 236-7476 CONTENTS Page Abstract............................................... ] Introduction........................................... 2 Purpose and scope................................. 4 Well-numbering system............................. 4 Gaging-station numbering system................... 6 Acknowledgments................................... 6 Previous work.......................................... 6 Geohydrologic setting.................................. 8 Gains and losses computed from water budgets........... 9 American Falls Reservoir.......................... 11 Ungaged inflow............................... 13 Reservoir storage............................ 29 Reservoir leakage............................ 31 Lake Walcott...................................... 38 Milner Lake....................................... 44 Gain and loss analysis....................... 44 Reservoir -
Swan Falls Dam Spanning Snake River Kuna Vicinity Owyhee County
Swan Falls Dam HAER No. ID-20 Spanning Snake River Kuna Vicinity Owyhee County (b.da County) Idaho K I- PHOTOGRAPHS WRITTEN HISTORICAL AND DESCRIPTIVE DAT A FIELD RECORDS Historic American Engineering Record Western Regional Office National Park Service U.S. Department of the Interior San Francisco, California 94102 HISTORIC AMERICAN ENGINEERING RECORD Swan Falls Dam HAER No. ID-20 Location: Spanning the Snake River, about 40 miles southwest of Boise, Idaho, and 18 miles south of Kuna, Idaho, in the SE 1/4of Section 18, Township 2 South, Range 1 East, Boise Meridian, UTM: 11/550520/478786C0wyhee County is on the southwest left bank; Ada County is on the northeast right bank Date of Construction: 1900-0l;altered in 1907, 1910, 1913, 1918021,1936, 1944, 1986 Designer: Andrew J. Wiley Builder: Trade Dollar Mining Company, Silver City, Idaho Present Owner: Idaho Power Company, 1220 Idaho Street, P.O. Box 70, Boise, Idaho 83707 Present Use: Hydroelectric power generation Significance: Swan Falls Dam was the first hydroelectric dam on Snake River in Idaho, and one of the earliest built in the Pacific Northwest. A J. Wiley, a brilliant western irrigation engineer and an. early assistant of engineer Arthur D. Foote, designed the project. The dam was built to supply power for the operation of gold mines in Silver City, Idaho, which has long previously run out of wood for fuel. It soon supplied power for Silver City, Nampa, Caldwell, and other Idaho towns. The Idaho Power Company, which acquired the dam in 1916 during a major consolidation of southern Idaho power companies in receivership, expanded the capacity of the dam and added new equipment in two phases. -
National Register of Historic Places Continuation Sheet Section No
NPS Form 10-900 OMB No. 10024-0018 (Oct. 1990) United States Department of the Interior ,C£$ PftRKSERVIC National Park Service National Register of Historic Places Registration Form This form is for use in nominating or requesting determinations for individual properties and districts. See instructions in How to Complete the National Register of Historic Pla Registration Form (National Register Bulletin 16A). Complete each item by marking "x" in the appropriate box or by entering the information requested. If an item does not ap property being documented, enter "N/A" for "not applicable." For functions, architectural classification, materials, and areas of significance, enter only categories and subcatei instructins. Place additional entries and narrative items on continuation sheets (NPS Form 10-900a). Use a typewriter, word processor, or computer, to complete all items. 1. Name of Property historic name: American Falls Reservoir Flooded Townsite other name/site number: 2. Location street & number American Falls Reservoir [ ] not for publication city or town American Falls ______ [ X ] vicinity state: Idaho code: ID county: Power code: 077 zip code: 83211 3. State/Federal Agency Certification As the designated authority under the National Historic Preservation Act, as amended, I hereby certify that this [X] nomination [ ] request for determination of eligibility meets the documentation standards for registering properties in the National Register of Historic Places and meets the procedural and professional requirements set forth in 36