Unusual Regularities of Propylene Carbonate Obtained by Propylene Oxide Carboxylation in the + − Presence of Znbr2/Et4n Br System
Total Page:16
File Type:pdf, Size:1020Kb
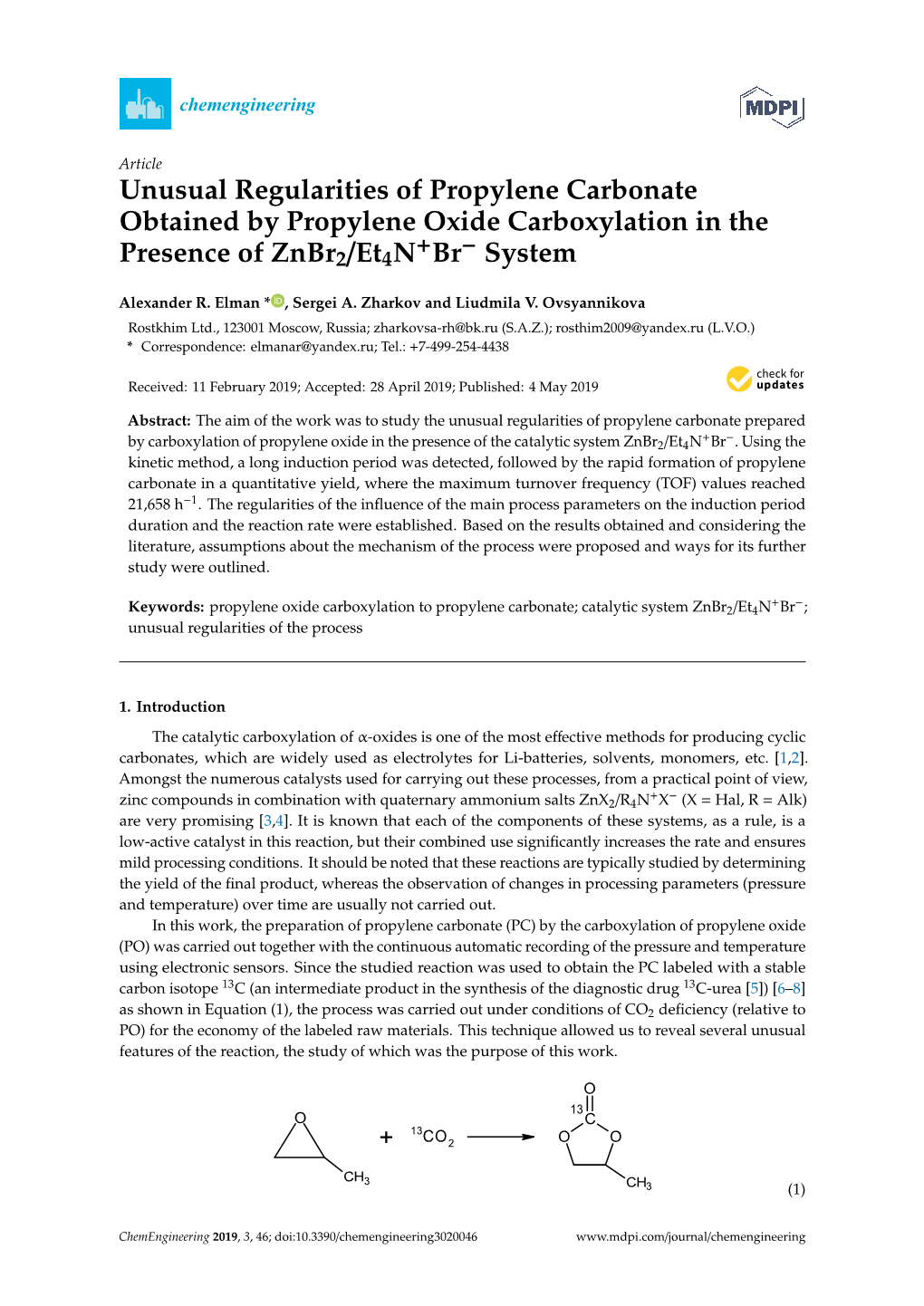
Load more
Recommended publications
-
Kinetic Modeling and Mechanistic Investigations of Transesterification of Propylene Carbonate with Methanol Over Fe-Mn Double Metal Cyanide Catalyst
Reaction Chemistry & Engineering Kinetic Modeling and Mechanistic Investigations of Transesterification of Propylene Carbonate with Methanol over Fe-Mn Double Metal Cyanide Catalyst Journal: Reaction Chemistry & Engineering Manuscript ID RE-ART-09-2019-000372.R1 Article Type: Paper Date Submitted by the 21-Oct-2019 Author: Complete List of Authors: Song, Ziwei; Yanshan University, Subramaniam, Bala; University of Kansas, Center for Environmentally Beneficial Catalysis Chaudhari, Raghunath; University of Kansas, Chemical & Petroleum Engineering Page 1 of 23 Reaction Chemistry & Engineering Kinetic Modeling and Mechanistic Investigations of Transesterification of Propylene Carbonate with Methanol over Fe-Mn Double Metal Cyanide Catalyst Ziwei Song, a,b,c Bala Subramaniam, a,b and Raghunath V. Chaudhari* a,b aCenter for Environmentally Beneficial Catalysis, University of Kansas, 1501 Wakarusa Dr. Lawrence, KS 66047, United States bDepartment of Chemical & Petroleum Engineering, University of Kansas, 1503 W 15th St. Lawrence, KS 66045, United States cDepartment of Chemical Engineering, College of Environmental and Chemical Engineering, Yanshan University, Qinhuangdao 066004, China *Corresponding author: [email protected] KEYWORDS: double metal cyanide, transesterification, dimethyl carbonate, microkinetic modeling 1 Reaction Chemistry & Engineering Page 2 of 23 Abstract Kinetic modeling of transesterification of propylene carbonate with methanol using Fe-Mn double metal cyanide catalyst has been investigated based on experimental data obtained under kinetically controlled conditions in a batch slurry reactor in the 140-200 °C range. A simple two-step power law model was found to represent the experimental data well. In addition, a detailed kinetic model based on a molecular level description of the reaction mechanism is also evaluated to provide better insight into the reaction mechanism. -
Propylene Carbonate Extraction for Recovery of Poly-3-Hydroxybutryate
1 Propylene Carbonate Extraction for Recovery of Poly-3-hydroxybutryate Abstract Propylene Carbonate Distillation Poly -3-hydroxybutryate (PHB) is a biopolymer produced Propylene Carbonate is an organic solvent produced as a storage molecule for energy and carbon under • Waste solution recovered after PHB by combining propylene oxide with carbon dioxide. It is poor growth conditions in certain organisms. PHB is a precipitation consisted of Propylene considered a polar aprotic solvent (no proton to donate) class of polyhydroxyalkanoates (PHAs), which have Carbonate and Ethanol Due to its characteristics (low vapor pressure, stability, similar properties to plastics derived from petroleum. PHB provides an environmentally friendly alternative to and high polarity) it is used in many applications. These include • Through distillation, both the Ethanol production of fibers and textiles, dyeing, personal care agents petroleum -based plastics due to its biodegradability and and Propylene Carbonate have been and cosmetics, and a component of some adhesives. It is also method of production. It can be produced by recovered. considered non-toxic making it more suitable to use at larger recombinant Escherichia coli, harvested from the cell, scales. and recovered. One of the major expenses of • Recovered 70% Propylene producing PHB is the extraction of the PHB from the Carbonate and nearly all Ethanol biomass. This study focused on evaluating different methods of PHB extraction for their ability to effectively • Preliminary experiments show no extract PHB from E. coli biomass and the feasibility of Propylene Carbonate Extraction Procedure Distillation apparatus to recover Propylene difference in the yield of PHB scaling up those processes. These processes provide a Carbonate and Ethanol from waste stream extracted with distilled Propylene 125 L Bioreactor way to produce PHB from growing E. -
US5349077.Pdf
|||||||||||||||| USOO5349077A United States Patent (19) 11 Patent Number: 5,349,077 Doya et al. 45 Date of Patent: Sep. 20, 1994 54 PROCESS FOR PRODUCING ALKYLENE 5,003,084 3/1991 Su et al. .............................. 549/230 CARBONATES FOREIGN PATENT DOCUMENTS 75 Inventors: Masaharu Doya; Takashi Ohkawa; Yutaka Kanbara; Aksushi Okamoto; 0443758 8/1991 European Pat. Off. Kenichi Kimizuka, all of Niigata, OTHER PUBLICATIONS Japan Chemical Abstracts, vol. 82, No. 23, Jun. 9, 1975, Co 73 Assignee: Mitsubishi Gas Chemical Company, lumbus, Ohio; Sergio Fumasoni et al. Inc., Tokyo, Japan Primary Examiner-José G. Dees 21 Appl. No.: 99,461 Assistant Examiner-Joseph M. Conrad, III 22 Filed: Jul. 30, 1993 Attorney, Agent, or Firm-Wenderoth, Lind & Ponack (30) Foreign Application Priority Data (57) ABSTRACT Jul. 31, 1992 JP Japan .................................. 4-205362 A process for producing alkylene carbonates which Jul. 31, 1992 (JP) Japan .......................... ... 4-205363 comprises reacting urea and glycols described by the Jul. 31, 1992 JP Japan .......................... ... 4-205364 general formula RCH(OH) CH2OH; wherein R repre Jun. 30, 1993 JP Japan .................................. 5-161857 sents hydrogen or an alkyl group containing 1 to 4 51) Int. Cl. .............................................. CO7C 69/96 carbons, using a catalyst containing zinc, magnesium, 52 U.S. Cl. .................................... 558/260; 549/229; lead or calcium at reduced pressures. The alkylene 549/230 carbonates are produced with high yield easily using 58 Field of Search ................. 558/260; 549/229, 230 raw materials which are comparatively inexpensive with a mild reaction that does not involve explosive or 56) References Cited hazardous materials. U.S. PATENT DOCUMENTS 2,773,881 12/1956 Dunn et al. -
Green Chemistry
Green Chemistry View Article Online PAPER View Journal | View Issue The greening of peptide synthesis† Cite this: Green Chem., 2017, 19, Stefan B. Lawrenson, Roy Arav and Michael North* 1685 The synthesis of peptides by amide bond formation between suitably protected amino acids is a funda- mental part of the drug discovery process. However, the required coupling and deprotection reactions are routinely carried out in dichloromethane and DMF, both of which have serious toxicity concerns and generate waste solvent which constitutes the vast majority of the waste generated during peptide syn- thesis. In this work, propylene carbonate has been shown to be a green polar aprotic solvent which can be used to replace dichloromethane and DMF in both solution- and solid-phase peptide synthesis. Solution-phase chemistry was carried out with Boc/benzyl protecting groups to the tetrapeptide stage, no epimerisation occurred during these syntheses and chemical yields for both coupling and de- Received 20th January 2017, protection reactions in propylene carbonate were at least comparable to those obtained in conventional Accepted 1st March 2017 solvents. Solid-phase peptide synthesis was carried out using Fmoc protected amino acids on a DOI: 10.1039/c7gc00247e ChemMatrix resin and was used to prepare the biologically relevant nonapeptide bradykinin with compar- Creative Commons Attribution 3.0 Unported Licence. rsc.li/greenchem able purity to a sample prepared in DMF. Introduction methane mixtures.8 These issues are amplified in solid-phase peptide synthesis7,9 where large excesses of reagents are used Peptides are central compounds in the pharmaceutical indus- and resins are washed multiple times with toxic solvents. -
These Two Workbooks Are Provided by As a Convenient Introduc
These two workbooks are provided by www.hansen-solubility.com as a convenient introduc They are Copyright © 2013 Prof Steven Abbott If you find bugs/issues or would like extra functionality, please email Steven Abbott [email protected] ction to some of the basic HSP methods HSP Sphere dD dP dH R Good 11 18.4 9.7 8.0 7.1 Bad 11 Test Value 16 7 8 Total 22 Delta 2.4 11.4 10.4 Distance 5.5 RED 0.77 Solvents dD dP dH MVol Score Distance Acetone 15.5 10.4 7 73.8 1 5.915773 Acetonitrile 15.3 18 6.1 52.9 0 10.52754 n-Amyl Acetate 15.8 3.3 6.1 148 0 n-Amyl Alcohol 15.9 5.9 13.9 108.6 0 Benzene 18.4 0 2 52.9 0 11.38507 Benzyl Alcohol 18.4 6.3 13.7 103.8 0 Benzyl Benzoate 20 5.1 5.2 190.3 0 1-Butanol 16 5.7 15.8 92 0 2-Butanol 15.8 5.7 14.5 92 0 n-Butyl Acetate 15.8 3.7 6.3 132.6 0 t-Butyl Acetate 15 3.7 6 134.8 0 t-Butyl Alcohol 15.2 5.1 14.7 96 0 Butyl Benzoate 18.3 5.6 5.5 178.1 0 Butyl Diglycol Acetate 16 4.1 8.2 208.2 0 Butyl Glycol Acetate 15.3 7.5 6.8 171.2 0 n-Butyl Propionate 15.7 5.5 5.9 149.3 0 Caprolactone (Epsilon) 19.7 15 7.4 110.8 0 Chloroform 17.8 3.1 5.7 80.5 1 7.075453 m-Cresol 18.5 6.5 13.7 105 1 6.563973 Cyclohexane 16.8 0 0.2 108.9 0 12.82752 Cyclohexanol 17.4 4.1 13.5 105.7 0 Cyclohexanone 17.8 8.4 5.1 104.2 0 Di-isoButyl Ketone 16 3.7 4.1 177.4 0 Diacetone Alcohol 15.8 8.2 10.8 124.3 0 Diethyl Ether 14.5 2.9 4.6 104.7 0 10.87429 Diethylene Glycol Monobut 16 7 10.6 170.4 0 Dimethyl Cyclohexane 16.1 0 1.1 140 0 Dimethyl Sulfoxide (DMSO) 18.4 16.4 10.2 71.3 1 7.066692 1,4-Dioxane 17.5 1.8 9 85.7 0 8.160898 1,3-Dioxolane -
Order of the State of Wisconsin Natural Resources Board Creating Rules
CR 10-012 ORDER OF THE STATE OF WISCONSIN NATURAL RESOURCES BOARD CREATING RULES The Wisconsin Natural Resources Board adopts an order to create NR 400.02(162)(a)51. and 52., relating to the definition of volatile organic compound. AM-27-09 Analysis Prepared by the Department of Natural Resources 1. Statute interpreted: Section 285.11(6), Stats. The State Implementation Plan developed under s. 285.11(6), Stats., is revised. 2. Statutory authority: Sections 227.11(2)(a) and 285.11(1) and (6), Stats. 3. Explanation of agency authority: Section 227.11(2)(a), Stats., gives state agencies general rule-making authority. Section 285.11(1), Stats., gives the Department the authority to promulgate rules implementing and consistent with ch. 285, Stats. Section 285.11(6), Stats., requires the Department to develop a plan for the prevention, abatement and control of air pollution. The plan must conform with the Clean Air Act and federal regulations for ozone control. Since volatile organic compounds (VOC) are a precursor to ozone, having the state definition of VOC conform to the federal definition is consistent with s. 285.11(6), Stats. 4. Related statute or rule: Chapters NR 401 – 499 reference the definitions presented in s. NR 400.02, Wis. Adm. Code. 5. Plain language analysis: The proposed rule amendment contained in this order reflects a recent conclusion by the United States Environmental Protection Agency (EPA) that dimethyl carbonate and propylene carbonate make a negligible contribution to tropospheric ozone formation. EPA excluded these two compounds from its regulatory definition of VOC through a January 21, 2009 Federal Register notice (74 FR 3437). -
Scope and Limitation of Propylene Carbonate As a Sustainable Solvent in the Suzuki–Miyaura Cite This: RSC Adv.,2019,9,37818 Reaction†
RSC Advances PAPER View Article Online View Journal | View Issue Scope and limitation of propylene carbonate as a sustainable solvent in the Suzuki–Miyaura Cite this: RSC Adv.,2019,9,37818 reaction† a a a b Andrea Czompa, Balazs´ Laszl´ oP´ asztor,´ Jennifer Alizadeh Sahar, Zoltan´ Mucsi, ac d e ac Dora´ Bogdan,´ Krisztina Ludanyi,´ Zoltan´ Varga and Istvan´ M. Mandity´ * The Suzuki–Miyaura reaction is one of the most used transformations in drug research. Thus making this reaction more sustainable is of considerable current interest. Here we show that propylene carbonate (PC) can be used as a solvent for the Suzuki–Miyaura reaction. PC is one of the greenest solvents since it is synthesized under green conditions by the use of carbon dioxide in the air. All reactions proceeded Received 3rd September 2019 well and good or excellent yields were observed for the biaryl products. Nonetheless in the case of Accepted 29th October 2019 pyridazinones, 2-hydroxypropyl- chain containing side-products were observed. Importantly, this fact DOI: 10.1039/c9ra07044c allowed the isolation of several novel compounds which were generated under prominently green Creative Commons Attribution 3.0 Unported Licence. rsc.li/rsc-advances conditions. Introduction propylene carbonate (PC) and various polar and nonpolar solvents on palladium-catalyzed Suzuki–Miyaura coupling of The Suzuki–Miyaura reaction is the palladium-catalysed cross- chloroaryl triates. They highlighted the similar selectivity of 21 coupling reaction of organoboranes with organic halides, -
The Solvation of Anions in Propylene Carbonate
The solvation of anions in propylene carbonate Niccolò Peruzzi,1 Pierandrea Lo Nostro,1,* Barry W. Ninham,2 Piero Baglioni1 1 Department of Chemistry “Ugo Schiff” and CSGI, University of Florence, 50019 Sesto Fiorentino (Firenze) - Italy 2 Research School of Physical Sciences and Engineering, Canberra, ACT0200 - Australia ______________________ * Corresponding author. e-mail: [email protected]. Tel.: +39 055 457-3010. Fax: +39 055 457-3036. 1 Abstract The solubility of some univalent potassium salts (KF, KCl, KBr, KI, KClO4, KSCN, and KCNO) in propylene carbonate (PC) was determined at different temperatures through Flame Emission Spectroscopy. From the solubility measurements, the thermodynamic parameters ∆G0, ∆H0 and ∆S0 of solution were calculated. Measurements were carried out via conductimetry and FTIR to investigate the formation of ion pairs, and the ion-solvent interactions. This study was motivated by the open question of whether specific ion (Hofmeister) effects are related to the structure of the solvent (i.e. hydrogen bonding). As for water the effects are due to solute induced solvent structure changes not accounted for by electrostatic forces. Keywords Hofmeister series; propylene carbonate; specific ion effects; ion solvation; solvent structure. 2 1 Introduction The expression “Hofmeister effect” refers to the specificity that ions exhibit on a plethora of phenomena. Some examples are colloidal interactions, surfactant dispersions, microemulsions stability, polymers, and biomacromolecules (proteins, enzymes, nucleic acids, -
Nail Polish Remover
^ ^ H ^ I H ^ H ^ H ^ II ^ II ^ ^ ^ ^ ^ ^ ^ ^ ^ ^ ^ ^ ^ I ^ European Patent Office Office europeen des brevets EP 0 701 811 A1 EUROPEAN PATENT APPLICATION (43) Date of publication: (51) |nt C|.6: A61 K 7/047 20.03.1996 Bulletin 1996/12 (21) Application number: 95305857.5 (22) Date of filing: 22.08.1995 (84) Designated Contracting States: (72) Inventors: CH DE ES FR GB IT LI NL SE • Faryniarz, Joseph Raymond Oxford, Connecticut 06478 (US) (30) Priority: 19.09.1994 US 308233 • Miner, Philip Edward Newton, Connecticut 06470 (US) (71) Applicants: • UNILEVER PLC (74) Representative: London EC4P 4BQ (GB) Mulder, Cornells Willem Reinier, Dr. et al Designated Contracting States: Unilever PLC, GB Patent Division, • UNILEVER N.V. Colworth House NL-3013 AL Rotterdam (NL) Sharnbrook, Bedford MK44 1 LQ (NL) Designated Contracting States: CH DE ES FR IT LI NL SE (54) Nail polish remover (57) A polish-lacquer remover is provided that in- alkylene carbonate. The compositions achieve low VOC, eludes a volatile organic solvent, a C4-C30 diester and excellent lacquer removal and exhibit improved condi- water. Preferably, the combination further includes an tioning for cuticles and nails. 00 o Is- o a. LU Printed by Jouve (FR), 18, rue Saint-Denis, 75001 PARIS EP0 701 811 A1 Description The invention relates to nail polish removers of low volatile organic chemical content that meet legislated environ- mental rules and that also have improved lacquer removal efficacy and conditioning properties. 5 Products have long been marketed for the removal of nail polish (lacquer) from fingernails and toenails. These products essentially contain only a solvent (with which to dissolve the lacquer). -
Rule 1020 (Definitions) February 21, 2013
SAN JOAQUIN VALLEY UNIFIED AIR POLLUTION CONTROL DISTRICT Final Draft Staff Report: Rule 1020 (Definitions) February 21, 2013 SAN JOAQUIN VALLEY UNIFIED AIR POLLUTION CONTROL DISTRICT FINAL DRAFT STAFF REPORT Proposed Amendments to Rule 1020 (Definitions) February 21, 2013 Prepared by: Lisa Van de Water, Air Quality Specialist Reviewed by: Brian Clerico, Air Quality Engineer Glenn Reed, Senior Air Quality Specialist Anna Myers, Senior Air Quality Specialist Leland Villalvazo, Supervising Air Quality Specialist Jessi Fierro, Supervising Air Quality Specialist Mike Oldershaw, Manager, Compliance Errol Villegas, Program Manager, Strategies and Incentives Samir Sheikh, Director, Strategies and Incentives I. SUMMARY Rule 1020 (Definitions) defines terms used throughout other San Joaquin Valley Air Pollution Control District (District) rules, including a list of compounds exempt from ozone regulations due to their low ozone forming potential. The District occasionally amends District Rule 1020 to update these definitions as they are revised by the Environmental Protection Agency (EPA). The District proposes to make several updates related to the list of exempt compounds, including adding several additional compounds and clarifying requirements for several existing compounds. The first proposed rule amendment is to add dimethyl carbonate (DMC) and propylene carbonate (PC) to the District’s list of exempt compounds within the definition of volatile organic compounds (VOC) (Section 3.53) as a response to EPA findings that DMC and PC have a low potential to form ozone in the atmosphere. EPA found that these compounds are less photo-chemically reactive than ethane and, thus, have a negligible contribution to ozone formation. EPA announced the exemption of DMC and PC in the Federal Register, effective February 2009 (included as Appendix B). -
Direct Synthesis of Dimethyl Carbonate and Propylene Glycol Using Potassium Bicarbonate As Catalyst in Supercritical CO2
62 Pol. J. Chem. Tech.,Polish Vol. Journal 17, No. of Chemical1, 2015 Technology, 17, 1, 62 — 65, 10.1515/pjct-2015-0010 Direct synthesis of dimethyl carbonate and propylene glycol using potassium bicarbonate as catalyst in supercritical CO2 Yicun Wen1, Rui Zhang1*, Yu Cang1, Jianchao Zhang1, Lixiao Liu1, Xuhong Guo1, Bin Fan2* 1 East China University of Science and Technology, State Key Laboratory of Chemical Engineering, Shanghai, 200237, P. R. China 2Chinese Academy of Sciences, State Key Laboratory of Environmental Aquatic Chemistry, Research Center for Eco- -Environmental Sciences, Beijing 100085, China *Corresponding authors: e-mail: [email protected], [email protected] The improved one-pot synthesis of dimethyl carbonate and propylene glycol from propylene oxide, supercritical carbon dioxide, and methanol with potassium bicarbonate as the catalyst has been reported in this paper. As far as we know, it is the fi rst time to use potassium bicarbonate only as the catalyst in the production process which is simple and cheap. Satisfactory conversion rate of propylene oxide and yield of the products could be achieved at the optimized conditions with quite a small amount of by-products. Our new method offers an attractive choice for the production of dimethyl carbonate in large-scale industry effi ciently and environmental friendly. Keywords: direct synthesis, dimethyl carbonate, carbon dioxide, potassium bicarbonate, supercritical fl uids. INTRODUCTION due to the noble metal catalyst. So the exploration of new clean ways for DMC synthesis is urgent. Because carbon dioxide (CO ) is an abundant, ine- 2 Direct synthesis routes of DMC from transesterifi cation xpensive, and nontoxic biorenewable resource, it is an of cyclic carbonates is a new proposal to this problem attractive raw material for incorporation into important which employs two original chemicals, CO and methanol, industrial processes. -
C7cp01203a1.Pdf
Electronic Supplementary Material (ESI) for Physical Chemistry Chemical Physics. This journal is © the Owner Societies 2017 Electronic Supplementary Information for A Density Functional Theory Study on the Thermodynamic and Dynamic Properties of Anthraquinone Analogues Cathode Materials for Rechargeable Lithium Ion Batteries Shu-Jing Yang,a Xiao-Ya Qin,a L. B. Zhao,*,a Rongxing He,a Wei Shen,a and Ming Li.a aDepartment of Chemistry, School of Chemistry and Chemical Engineering, Southwest University, Chongqing 400715, China Corresponding Authors *E-mail: [email protected]. Fig. S1. Comparison of reduction potential of AQ calculated by implicit solvent model (PCM + SMD) and explicit solvent model (PCM or SMD + propylene carbonate molecule). As shown in Fig. S1, the influence of explicit solvent molecule on the calculated reduction potential is very slight. By adding a propylene carbonate molecule in the reaction complex, the calculated reduction potentials decrease about 0.1 V by PCM model and 0.25 V by SMD model. Among all the solvation models, reduction potentials of AQ calculated by implicit PCM model matches best with experimental results. Fig. S2. Potential and Li+ concentration dependent equilibrium diagram for the charge and discharge processes in the electrochemical reaction of PPD. Fig. S3. Comparison of electrostatic potential (ESP) plots of AQ-Li and its derivatives. Fig. S4. Comparison of electrostatic potential (ESP) plots of AQ-Li2 and its derivatives. Fig. S5. The natural bond orbital (NBO) charges on lithium atom in three isomer pairs (PQD/PID, PCD/PPD, and BDOZD/BDIOZD). Fig. S6. The electrostatic potential (ESP) charges on lithium atom in three isomer pairs (PQD/PID, PCD/PPD, and BDOZD/BDIOZD).