Quality Council of India
Total Page:16
File Type:pdf, Size:1020Kb
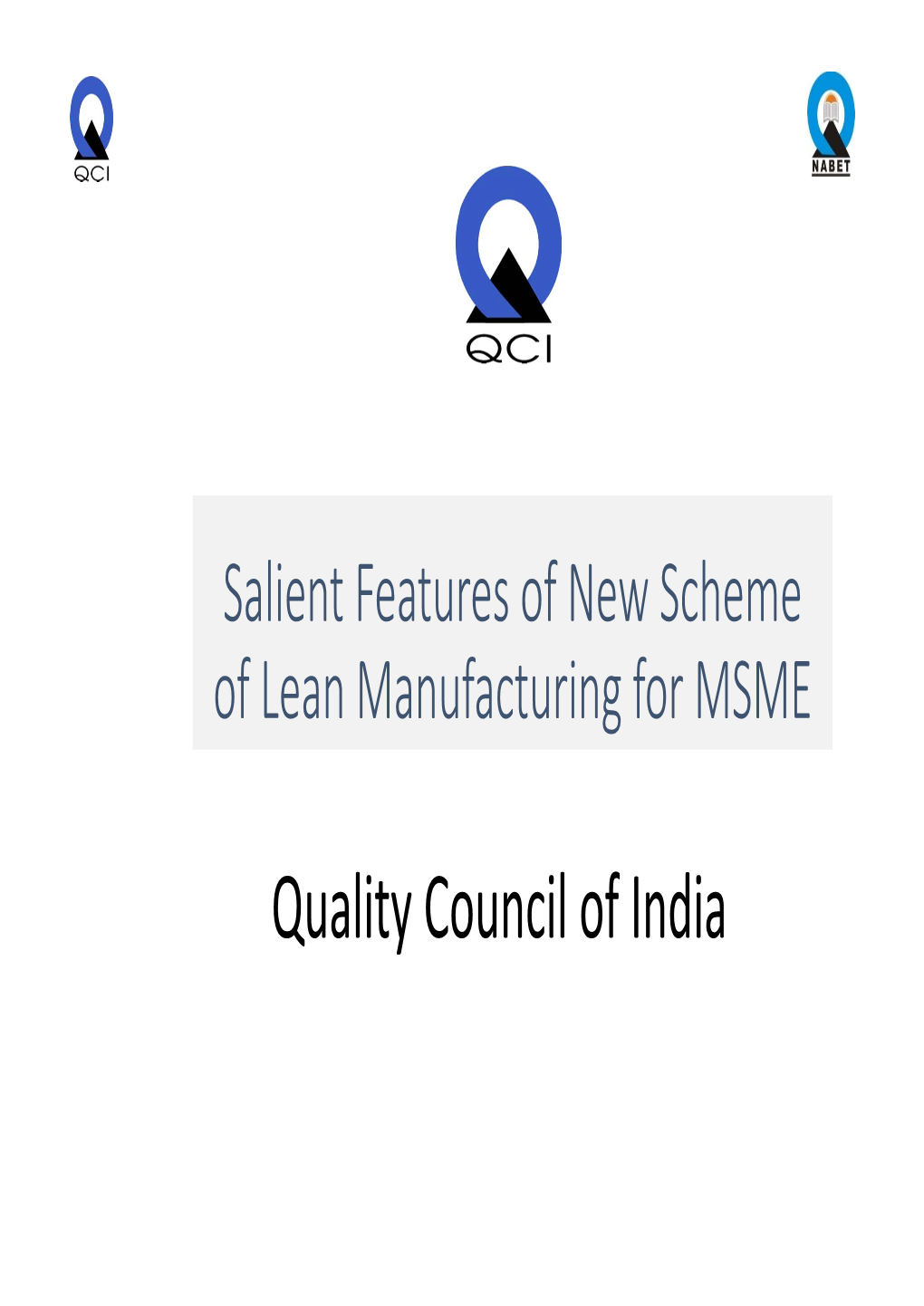
Load more
Recommended publications
-
Quality Council of India (QCI) National Accreditation Board for Education
E-monitoring of Websites of Teacher Education Institutions (TEIs) Recognized by the National Council for Teacher Education (NCTE) Website Template developed by Quality Council of India (QCI) National Accreditation Board for Education and Training (NABET), ITPI Building, 6th Floor, 4-A, I P Estate, Ring Road, New Delhi – 110002, India Website Template The website o f a TEl shall be in two parts. In the first part, the institution shall display the following information: Part-I: A. General Information: i. Name and address of the Institution M.E.S. TEACHERS COLLEGE, C.T.E., BANGALORE RURAL ‘Vidya Vihara’, #25/1, 17th Main, II Block, Rajajinagar, Bengaluru-560010 District: Benglauru State: Karnataka E-mail: [email protected] Telephone No with Code: 080-23321600 ii. Year of Establishment 1958 ii. Teacher Education Programme (s) offered in the Institution Sl. Number and Year of NCTE Programme Sanction Intake No. Recognition F.SRO/NCTE/APS0339/B.Ed/ 1. B.Ed KA/2015/16/79170 50 Dated: 01/01/2016 iv. Details of Affiliation Sl. Name of the Affiliating Number and Programme No. Body Affiliation ACA-3/A3/SHA.NO./MESTC/2015-2016 1 B.Ed Bangalore University Dated: 20/11/2015 F8-108/2004(CPP-1) 2 B.Ed UGC Dated: 06/08/2004 v. Status of Affiliation Permanent / Temporary Permanent In the case of Temporary Affiliation, it is valid up to…--… vi. Type of Management ( Mark which is applicable ) a. University Department (State University / Central University / Deemed University / Private University) b. Government Institution c. Government aided Institution d. Self-financing Institution vii. -
SS2016 Report
“There cannot be a bigger contributor than Mahatama Gandhi towards Swachh Bharat Mission. In the journey of one and a half years since the launch of the Mission, I would like to acknowledge the participation and involvement of citizens of the country - especially children, as also the positive and proactive role played by the media, in the Mission’s journey till date” Narendra Modi Prime Minister SWACHH SURVEKSHAN 3 FOREWORD M. Venkaiah Naidu, Minister of Urban Development, Housing & Urban Poverty Alleviation and Parliamentary Afairs As a mark of respect to the father of the nation, our govern- ment has taken an ambitious pledge to make India Open Defecation Free and clean by 2nd October, 2019 through the Swachh Bharat Mission. We have taken up a multi-pronged strategy for making this mission successful, and turning it into a people’s movement. In its second year since launch, it is heartening to note that the Swachh Bharat Mission has caught the imagination of cit- izens. The increased participation from citizens, be it as part of our thematic drives, or voluntary ‘swachhata’ activities from inspired individuals and organizations, is slowly but surely pushing the Mission towards becoming a ‘Jan Andolan’. The “Swachh Survekshan” was launched in January 2016 to assess the sanitation and solid waste management status in 73 major cities in India (comprising 40% of India’s total urban population) - including 53 cities with a population of above 10 lakhs each, and state capitals. This was the first survey since the launch of Swachh Bharat Mission in October 2014, and I would like to thank the Quality Council of India for carrying out this survey on behalf of my Ministry. -
Airports Authority of India Swami Vivekananda Airport Raipur - 492015
AIRPORTS AUTHORITY OF SWAMI VIVEKANANDA AIRPORT, RAIPUR (Tender No. AAI/RPR/IMS-01/2014) QUOTATION DOCUMENT FOR ENGAGEMENT OF CONSULTANT FOR PROVIDING SERVICES FOR INTEGRATED MANAGEMENT SYSTEM (IMS) (ISO9001:2008 and 14001:2004) CERTIFICATION OF SWAMI VIVEKANANDA AIRPORT) (ISO 14001: 2004) AIRPORTS AUTHORITY OF INDIA SWAMI VIVEKANANDA AIRPORT RAIPUR - 492015. Signature of Bidder 1 AIRPORTS AUTHORITY OF INDIA SWAMI VIVEKANANDA AIRPORT NOTICE INVITING QUOTATION Airport Director, Airports Authority of India, Swami Vivekananda Airport, Raipur on behalf of the Chairman, Airports Authority of India, invites quotations from eligible bodies for “Integrated Management System (IMS) certification (ISO 9001: 2008, ISO 14001:2004 standard) at Swami Vivekananda Airport, Airports Authority of India, Raipur. Swami Vivekananda Airport is already certified for ISO 9001:2008 and valid till 06th Jan 2015. Hence the employees are already trained for ISO 9001 standards Quotation shall be submitted in a sealed cover in two bid system and superscribed “IMS certification (ISO 9001: 2008, ISO 14001:2004)” and addressed to DY. GENERAL MANAGER (E-E) AIRPORTS AUTHORITY OF INDIA SWAMI VIVEKANANDA AIRPORT RAIPUR - 492015. for eligibility criteria, schedule of issue of quotation, quotation document submission and other details please visit our website www.airportsindia.org.in / www.aai.aero or contact at the office address / Tele No. 0771-2418600/ 09425504494. DY. GENERAL MANAGER (E-E) Signature of Bidder 2 AIRPORTS AUTHORITY OF SWAMI VIVEKANANDA AIRPORT, RAIPUR (Tender No. AAI/RPR/ISO/2014) SUMMARY 1 Name of work Engagement of Consultant for providing services for Integrated Management System (IMS) certification (ISO 9001: 2008, ISO 14001: 2004 Standard) of S.V. -
Dr. Umesh Chandra Kulshrestha
Biodata Name: Dr Umesh Chandra Kulshrestha Designation: Professor Director, Trans-Disciplinary Research Cluster, JNU (Honorary) Deputy Director, South Asia Nitrogen Center (Honorary) Address (O): School of Environmental Sciences Jawaharlal Nehru University New Delhi 110 067 INDIA Mobile: +91 9810611857 Email : [email protected], [email protected] Address (R): Flat# 8222 Sector C-8, Vasant Kunj, New Delhi 110070 INDIA Date of birth: December 01, 1968 Research interests: Air Pollution, Atmospheric Chemistry and Climate Change, Environmental Analytical Chemistry, Atmospheric Dust, Transport and Chemical Transformations, Chemistry of Rain and Snow, Reactive Nitrogen, Air Pollution Biomonitoring, Metal Aerosols, Carbonaceous aerosols, Atmospheric Mercury, Socioeconomic impact of air pollution, Environmental Impact Assessment. Educational qualification: M Sc (Chemistry) 1989 Agra University, Agra (India) B Ed 1990 Dayalbagh Educational Institute, Agra (India) Ph D (Chemistry) 1994 Dayalbagh Educational Institute, Agra (India) Post Doc 1994-98 National Physical Laboratory, New Delhi Dept. of Meteorology, Stockholm University, Sweden Previous jobs: Scientist CSIR-Indian Institute of Chemical Technology, Hyderabad, INDIA. (various positions) Publications: Research papers and Reviews: 86 General Science articles: 14 Books: 05 Book Chapters: 12 Technical reports: 02 Citations/h-index: 2431/25 Awards and honors: Fellow, Indian Geophysical Union (IGU). International START Young Scientist Award 2000 by IGBP-START (System for Analysis, Research and Training for global change) Washington DC, USA. 1 Thomas Kuhn Honour Pin Award 2002 by The International Union of Air Pollution Prevention & Environmental Protection Associations (IUAPPA) and the International Academy of Sciences. CSIR Young Scientist Award 2004 by Council of Scientific and Industrial Research, New Delhi. M S Krishnan Gold Medal 2004 by Indian Geophysical Union (IGU). -
Ministry of Civil Aviation Goes All Guns Blazing in Fight Against COVID-19 WHO Recommendations Were Issued
Issue 12 • Jan.-Mar., 2020 (Q4) Ministry of Civil Aviation goes all guns blazing in fight against COVID-19 WHO recommendations were issued. It list of the sectors most directly exposed as a included regular meetings of Secy, MoCA vector in spreading the disease. with all airlines, airport operators, DGCA Close maneuvering and advance planning and BCAS for enhancing universal screening through online meetings and virtual war room of arriving passengers & disinfecting of were carried out by MoCA to optimally utilise aircraft and airport premises ensuring safety demand and supply. Under the Lifeline UDAN of ground staff and security personnel. initiative of MoCA, 403 flights covering over Civil Aviation secretary and AAI chairman 3,97,632 kms of aerial distance transported also held review meetings with regard to around 748 tons of medical and essential Soon after several positive cases of COVID-19 quarantine of passengers coming from seven cargo across India over one month since the were reported all over the country with the nations – China, Italy, Iran, Republic of lockdown started. Daily updates on Lifeline onset of March, most of which were linked Korea, France, Spain & Germany in mid- UDAN portal enabled stakeholders to plan and to people with a travel history to affected March and conducted video conferences with track domestic essential air cargo movement. countries, a high-level meeting of Union all Airport Directors to work closely with Ministry of Civil Aviation on March 3, 2020 state governments, including relevant district The MoCA deployed all its required strength reviewed the preparedness to prevent the in the battle against the deadly pandemic administration officials to rapidly implement which has created an insurmountable growth spread of coronavirus. -
DPIIT on the Move
February 2021 | Vol 2 Issue 2 DPIIT On The Move Newsletter from Department for Promotion of Industry and Internal Trade DPIIT successfully concludes Udyog Manthan – series of CURATOR’s NOTE 46 webinars on quality & productivity Wishing all our readers a Happy New Year! It is a pleasure to bring to you the first issue of Volume 2 of DPIIT On The Move! Like always we are eager to share some key developments that we witnessed here at DPIIT in the past month. DPIIT successfully organized ‘Udyog Manthan’ – a marathon of 46 sector-specific webinars - With the aim of promoting quality and productivity in the Indian industry, DPIIT seen as the harbinger of quality organized Udyog Manthan - a marathon of 46 sector-specific webinars between and productivity in Indian January 4, 2021 to March 2, 2021. Udyog Manthan was organised in association industrial landscape. with Quality Council of India, National Productivity Council and industry bodies. The first India-EU High Level The webinar series focused on covering various sectors of manufacturing and Dialogue on Trade and services including toys, leather, furniture, chemicals, tourism, pharma etc. and Investment was held this witnessed over 400 speakers and experts, more than 3500 participants and month. Hon’ble CIM, Shri 18,000 digital audiences over a period of 8 weeks. The sectors covered in Udyog Piyush Goyal met UK Secretary Manthan contribute up to 70% of the country’s GDP. of State to discuss India-UK trade and investment Each webinar comprised a two-hour session involving discussions led by sectoral relationship. and industry experts of a particular sector. -
Vcstchps Brochure
CHHATTISGARH CERTIFICATION SOCIETY, INDIA FOR FORESTRY & AGRICULTURE (CGCERT) Certification of Traditional Community Health Practitioners under Voluntary Certification Scheme for Traditional Community Health Practitioners (VCSTCHPs) 1. Introduction of CGCERT: Chhattisgarh Certification Society, India for Forestry & agriculture (CGCERT) is an autonomous organization and it is running in State Forest Research & Training Institute, Vidhan Sabha, Zero Point, Baloda Bazar, Raipur (C.G). The Chhattisgarh Certification Society, INDIA (for Forestry & Agriculture) for certification was registered (Registration no. 405) on 18th of September 2003 as an autonomous and independent society under the Chhattisgarh Society Registration Act, 1973 (serial no. 44 of year 1973). Chhattisgarh Certification Society (for Forestry & Agriculture) is financially supported & working under administrative control of Forest Department, Govt. of Chhattisgarh. CGCERT provides the services for various Forestry & agricultural produce including the Organic Certification as per the National Standards for Organic Production (NSOP). Recently, CGCERT has been provisionally approved for Voluntary Certification Scheme for Traditional Community Health Practitioners (VCSTCHPs) & Voluntary Certification Scheme for Medicinal Plant Products (VCSMPPs) by Quality Control of India, New Delhi. 2. VCSTCHPs background: Herbal Medicinal Plant Based Traditional Community Health Practitioners (TCHPs) play a vital role in meeting the health care needs, especially of the far flung, unreached -
Certifying Certification
TRAFFIC Online Report Series No. 9 Certifying certification: can certification secure a sustainable future for medicinal plants, harvesters and consumers in India? Pushp Jain TRAFFIC International August 2004 TRAFFIC This report was published with the kind support of Published by TRAFFIC International, Cambridge, UK. © 2004 TRAFFIC International All rights reserved. All material appearing in this publication is copyrighted and may be reproduced with permission. Any reproduction in full or in part of this publication must credit TRAFFIC International as the copyright owner. The views of the author expressed in this publication do not necessarily reflect those of TRAFFIC, WWF or IUCN. The designations of geographical entities in this publication, and the presentation of the material, do not imply the expression of any opinion whatsoever on the part of TRAFFIC or its supporting organizations concerning the legal status of any country, territory, or area, or of its authorities, or concerning the delimitation of its frontiers or boundaries. The TRAFFIC symbol copyright and Registered Trademark ownership is held by WWF. TRAFFIC is a joint programme of WWF and IUCN. Suggested citation: Jain, P., 2004. Certifying Certification: Can certification secure a sustainable future for medicinal plants, harvesters and consumers in India? TRAFFIC International, Cambridge, UK. ISBN 1 85850 206 3 Front cover photograph: Medicinal plants in an ayurvedic hospital herb garden. Photograph credit: © WWF-Canon/Mauri Rautkari. CERTIFYING CERTIFICATION: CAN CERTIFICATION SECURE A SUSTAINABLE FUTURE FOR MEDICINAL PLANTS, HARVESTERS AND CONSUMERS IN INDIA? Pushp Jain April 2004 : © WWF-Canon/Mauri Rautkari Credit Kunbi tribe member using a medicament made from madar, or swallow-wort, Calotropis sp., India. -
October 2018 Issue - 10
INDIA CONSULATE GENERAL OF INDIA PERTH BULLETIN OCTOBER 2018 ISSUE - 10 Indian Economy: Vision of a USD 5 Trillion Indian Economy India Moves 23 Positions Higher on World Bank's Ease of Doing Business Ranking The Working Group tasked to develop a roadmap towards achieving a 5 trillion-dollar Indian economy by 2025 has India recorded a jump of 23 positions in the World Bank's prepared its report and it is being circulated to the annual ranking of ease of doing business, the government stakeholders for further suggestions. The Working Group said in a statement on Wednesday. India now ranks 77th in was constituted by the Department of Industrial Policy and the annual list, as against 100 last year. The commerce Promotion in the Ministry of Commerce and Industry with ministry said that the improvement of 23 positions in the participation from government and industry. India is one of Ease of Doing Business ranking is significant. It said that last the fastest growing major economies and is currently year, the country had registered a jump of 30 places, "a rare ranked as the world’s sixth largest economy. Projections of feat for any large and diverse country of the size of India". growth, over the medium term, remain encouraging and optimistic for India. The underlying strengths are indicative Read More: of the potential of India to achieve a USD 5 trillion economy by 2025. https://www.ndtv.com/business/india-jumps-23-positions- on-world-bank-s-ease-of-doing-business-ranking- Read More: 1940801 http://www.currentriggers.com/business/market/vision- usd-5-trillion-indian-economy/ India ranked 58th most competitive economy in World India attracted USD 22 bn of FDI flows in first half of Economic Forum's index, jumps 5 places from 2017 2018: UN report India has been ranked as the 58th most competitive economy on the World Economic Forum's global India attracted USD 22 billion of FDI flows in the first half of competitiveness index for 2018, which was topped by the 2018, according to a UN report which states that the global US. -
22-Kusum Nair.Vp
Progressive Research – An International Journal Society for Scientific Development Volume 13 (3) : 271-272, (2018) in Agriculture and Technology Print ISSN : 0973-6417, Online ISSN : 2454-6003 Meerut (U.P.) INDIA SAN I TA TION AND CLEAN LI NESS IN IN DIA : A SO CIO LOG I CAL STUDY Kusum Nair De part ment of So ci ol ogy, D.B.S. Col lege, Kanpur E-mail : [email protected] There are many casualties of not having sanitation and adjudged the cleanest city in the country, according to the proper cleanliness. People suffer from various diseases survey released. such as diarrhea, malnutrition, dengue, malaria and many Swachh Survekshan–a survey conducted to rank more. It also suffers children’s development. The major cities on various sanitation and cleanliness parameters – reason behind this is the carelessness and laziness of was launched in 2016. It was conducted among 73 top people themselves. The people themselves create the cities of India. problem of dirt and unhealthy environment. It was followed by Swachh Survekshan 2017 that People think of their own only and do not think of covered 434 cities. The third round of Swachh others. People do not mind to throw garbage in open Survekshan was conducted, covering all 4041 statutory areas which may negatively affect the environment. towns in India (2). People have to start to make their area clean and stay healthy. People should make a proper area for sanitation Sanitation coverage in rural India so that public health will not suffer. Mass awareness Sanitation coverage in rural India has increased programmes are already initiated by different institutions, substantially from 39 percent in 2014 to 76 percent in organisations and government bodies to save human January 2018, the Economic Survey 2017-18 has said. -
UDYOG MANTHAN a Marathon of Focused Webinars on Promoting Quality and Productivity in Indian Industry
16 20 22 Swachh Survekshan “MSME Sustainable (ZED) Virtual Learning - Acquiring Knowledge 2021 Certification” Scheme in a State of Stagnation www.udyogmanthan.qcin.org UDYOG MANTHAN A Marathon of Focused Webinars on Promoting Quality and Productivity in Indian Industry 4th January - 2nd March 2021 QUALITY INDIA A QCI PUBLICATION | January - March 2021 EDITOR’S NOTE Bodies (ULBs) in monitoring service level progress and their performance against targets. Total number of ULBs covered was 4,320. Dear Friends To be able to reach out to the masses in every corner of the country, ensuring maximum citizen To take forward Hon’ble PM’s vision of Aatmanirbhar participation, the Citizen Feedback was put live across Bharat, DPIIT organized a two-month long webinar various media – Swachhata App, Swachh Survekshan series in association with QCI and NPC called ‘Udyog website, MyGov portal. Other ways to participate Manthan’ from 4th Jan 2021 to 2nd March 2021 to in the process were the helpline number installed foster a mindset of Quality inspired productivity by the Ministry – 1969 and QCI’s Vote For Your City across Indian industry. This collaborative exercise App, through which citizens also participated in the was conducted with active support of DoC, BIS, TIC feedback process in huge numbers, making the spirit Council, CII, ASSOCHAM and other industry chambers of a true ‘Jan Andolan’ come alive. The social media and various sectorial Ministries. This inspiring campaigns for Swachh Survekshan focused on the Dr. Ravi P. Singh exercise has culminated into some extremely useful aspect through hashtags like #मेरा शहर मेरी िजम्मेेदारी insights and recommendations, which will soon be Secretary General and #MyCityMyResponsibility. -
[CAREERS] Jobs in Central Government (Quasi-Establishments)
AFTER INTERMEDIATE WHAT [CAREERS] Jobs in Central Government (Quasi-Establishments) ………………………………………………………………………………………………..… Central Government –Quasi –Establishments are also called Semi- Central Government Establishments. These are autonomous organizations owned, controlled and governed by the Central Government. a. A government-owned corporation, state-owned company, state-owned entity, state enterprise, publicly owned corporation, government business enterprise, commercial government agency, public sector undertaking or para-statal is a legal entity created by a government to undertake commercial activities on behalf of an owner government. Their legal status varies from being a part of government to stock companies with a state as a regular stockholder. There is no standard definition of a government-owned corporation (GOC) or state-owned enterprise (SOE), although the two terms can be used interchangeably. The defining characteristics are that they have a distinct legal form and they are established to operate in commercial affairs. While they may also have public policy objectives, GOCs should be differentiated from other forms of government agencies or state entities established to pursue purely non-financial objectives. Some of the prominent CG’Q’ establishments under Government of India are: 1. Employees State Insurance Corporation. 2. Central Board for Workers’ Education. 3. 4 National Council of Safety in Mines, Dhanbad, 4. National Labour Institute. Council of Scientific and Industrial Research. Central Social Welfare Board. 5. Indian Council of Agricultural Research. 6. Sports Authority of India. 7. National Council for Hotel Management and Catering Technology, New Delhi. 8. Institute of Hotel Management, Catering and Nutrition, New-Delhi and several other places. Registration Act, 1860 under the Registered under Societies.