Electromobility in the Automotive Industry. What Role Does Technology Change Play in the Geographic Pattern of Production?
Total Page:16
File Type:pdf, Size:1020Kb
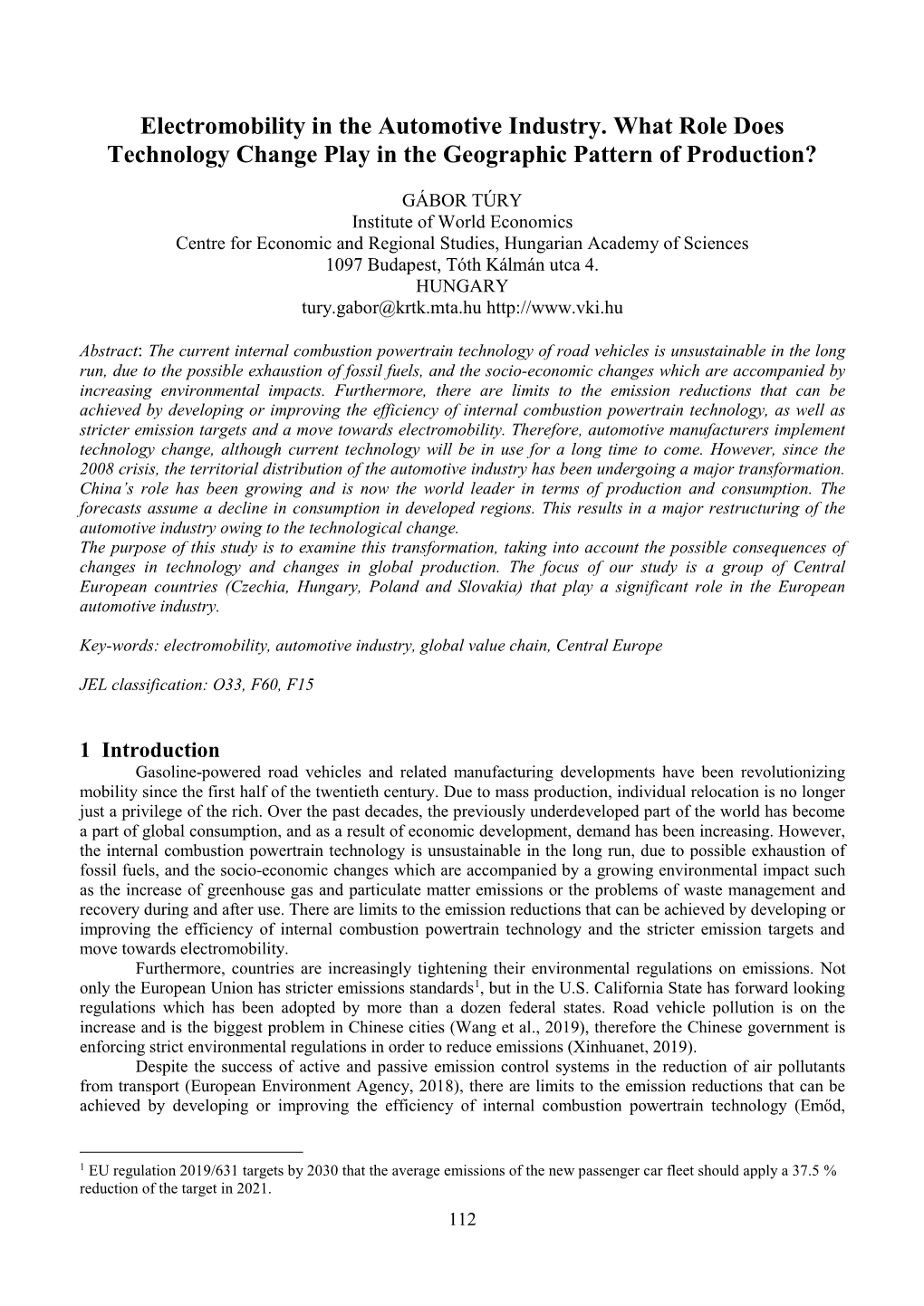
Load more
Recommended publications
-
Sustainability Report Bmw Brilliance Automotive Ltd. Contents
2015 SUSTAINABILITY REPORT BMW BRILLIANCE AUTOMOTIVE LTD. CONTENTS CONTENTS INTRODUCTION SUSTAINABILITY MANAGEMENT PRODUCT RESPONSIBILITY Preface 3 1.1 Our management approach 10 2.1 Our management approach 39 Our point of view 4 1.2 Stakeholder engagement 16 2.2 Efficient mobility 44 Highlights 2015 5 1.3 Compliance, anti-corruption and 18 2.3 Product safety 48 An overview of BMW Brilliance 6 human rights 2.4 Customer satisfaction 51 ENVIRONMENTAL PROTECTION SUPPLIER MANAGEMENT EMPLOYEES 3.1 Our management approach 57 4.1 Our management approach 72 5.1 Our management approach 87 3.2 Energy consumption and emissions 59 4.2 Minimising supplier risk 77 5.2 Attractive employer 90 3.3 Waste reduction 63 4.3 Utilising supplier opportunities 83 5.3 Occupational health and safety 96 3.4 Water 68 5.4 Training and development 99 CORPORATE CITIZENSHIP APPENDIX 6.1 Our management approach 107 7.1 About this report 120 6.2 Corporate citizenship 112 7.2 UN Global Compact index 121 7.3 GRI G4 content index 125 2 PREFACE Next, a further step in developing China’s very own new energy vehicle brand. In the future, we will expand our offering of locally developed, produced and environmentally friendly premium vehicles for our Chinese customers. Digitalisation is an important driver for sustainability. We are developing new solutions for intelligent mobility AT BMW BRILLIANCE, WE SEE SUSTAINABILITY AS products and services. At the same time, we are increasing the quality of our products, as well as the speed A KEY TO OUR CONTINUOUS SUCCESS IN CHINA. -
ISSUE 84 / 2020 Freetorial He Great Thing About Being Free Car Mag Is That We Are Just MG India Brand Ambassador That, Free
Get the Look Should you buy... Communist Chinese Cars? & from companies that work within the People's Republic? We try on some ultra cool T-Shirts with a distinctly Swedish theme which might be turbocharged... freecarmag.co.uk 1 ISSUE 84 / 2020 freetorial He great tHing about being Free Car Mag is tHat we are just MG India brand ambassador that, free. Free to write about what we please. Difcult things. T I was ratHer interested in wHat car manufacturers tHougHt Benedict Cumberbatch about operating in CHina. Sadly, in just about every instance, tHey Had notHing to sHare witH us, wHicH was a sHame. RigHt now cooperating witH a Communist political system would not seem to be tHe most etHical tHing to do. Indeed, unravelling tHemsleves from a globalised system tHat Has caused plenty of supply cHain issues recently would be tHe smart, business tHing to do. For tHe rest of us Bangernomics Mag (www.bangernomics.com) offers a positive way forward. Instead, car manufacturers prefer to stay away from tHe really important issues. THey could of course cHoose to be free. 4 News Events Celebs MeanwHile...say Hello to SHazHad SHeikH wHo Has been writing 8 China Crises about and driving all tHe exciting cars for decades as #browncarguy. See you next time. 10 Made in China 16 Mercedes World 18 Back Seat Driver 19 Future Proof Vauxhall Mokka 22 Saab Tees 23 Wanted Mr Jones Watch 24 Buy Now KIa, SEAT , Skoda 26 Alliance of British Drivers 28 The #Brown Car Guy Column 30 Next Time - BMW Isetta? James Ruppert The Brit Issue EDITOR [email protected] Cover Credits l Fiat • MG Motors India • Saab Tees THE TEAM Editor James Ruppert Publisher Dee Ruppert Backing MAG Sub Editor Marion King Product Tester Livy Ruppert Britain Photographer Andrew Elphick Our 5 point plan Web Design Chris Allen Columnist Shahzad Sheikh ©2020 Free Car Mag Limited is available worldwide Reporter Kiran Parmar witHout any restrictions. -
State of Automotive Technology in PR China - 2014
Lanza, G. (Editor) Hauns, D.; Hochdörffer, J.; Peters, S.; Ruhrmann, S.: State of Automotive Technology in PR China - 2014 Shanghai Lanza, G. (Editor); Hauns, D.; Hochdörffer, J.; Peters, S.; Ruhrmann, S.: State of Automotive Technology in PR China - 2014 Institute of Production Science (wbk) Karlsruhe Institute of Technology (KIT) Global Advanced Manufacturing Institute (GAMI) Leading Edge Cluster Electric Mobility South-West Contents Foreword 4 Core Findings and Implications 5 1. Initial Situation and Ambition 6 Map of China 2. Current State of the Chinese Automotive Industry 8 2.1 Current State of the Chinese Automotive Market 8 2.2 Differences between Global and Local Players 14 2.3 An Overview of the Current Status of Joint Ventures 24 2.4 Production Methods 32 3. Research Capacities in China 40 4. Development Focus Areas of the Automotive Sector 50 4.1 Comfort and Safety 50 4.1.1 Advanced Driver Assistance Systems 53 4.1.2 Connectivity and Intermodality 57 4.2 Sustainability 60 4.2.1 Development of Alternative Drives 61 4.2.2 Development of New Lightweight Materials 64 5. Geographical Structure 68 5.1 Industrial Cluster 68 5.2 Geographical Development 73 6. Summary 76 List of References 78 List of Figures 93 List of Abbreviations 94 Edition Notice 96 2 3 Foreword Core Findings and Implications . China’s market plays a decisive role in the . A Chinese lean culture is still in the initial future of the automotive industry. China rose to stage; therefore further extensive training and become the largest automobile manufacturer education opportunities are indispensable. -
BMW Brilliance Automotive Opens New Engine Plant in China Background Information / Facts and Figures
Corporate Communications Media Information EMBARGO: 04:30 a.m. Munich time 22 January 2016 11:30 a.m. Shenyang time BMW Brilliance Automotive opens new engine plant in China Background information / facts and figures 1. The Joint Venture BMW Brilliance Automotive Holdings Limited The BMW Brilliance Automotive joint venture, founded in 2003, is responsible for the production and marketing of BMW automobiles in China, as well as local development tasks. BBA is continuing its investment in the Chinese market. In 2015 the Joint Venture invested one billion Euros in production facilities in Shenyang. This investment includes the new engine plant as well as the other production facilities. The joint venture currently employs more than 16,000 people. A total of around 2,000 BBA employees will work at the new engine plant over the long term. In 2014, the BMW Group and Brilliance China Automotive Holdings Limited agreed to extend the BMW Brilliance Automotive joint venture agreement four years before the end of the current contract – with the aim of strengthening the existing successful cooperation. The contract has been extended for another ten years, namely from 2018 to 2028. In 2015, the BMW Group sold a total of 463,736 BMW and MINI in Mainland China (+1.7%). 2. The BBA production location Shenyang BMW automobiles have been produced in Shenyang since 2003. The site is Company Bayerische Motoren Werke operated as part of a joint venture with Brilliance China Automotive Holdings Aktiengesellschaft Postal Address Limited and produces BMW vehicles exclusively for the Chinese market. BMW AG 80788 München Telephone +49 89 382 18933 Internet: www.bmwgroup.com Corporate Communications Media Information Date 22 January 2016 Subject BMW Brilliance Automotive opens new engine plant in China Background information / facts and figures Page 2 BBA has produced more than one million vehicles since 2003. -
Andreas Maennel Principal Roland Berger
CURRENT STATUS of China's NEV market Presentation document Beijing, April 16, 2014 SUMMARY 1 CHINAS EV MARKET is still in a developing stage – It shows significant potential going forward 2 CHINESE OEMs are dominating the EV market – More players will enter the market in coming years 3 CHARGING INFRASTRUCTURE is underdeveloped – Its build-up is essential for positive market development 4 SERVICES related to E-Mobility are proven concepts – Innovative services will attract and retain customers Source: Roland Berger 20140416_EV Status China_speech_vsend.pptx 2 China's electric vehicle (EV) market is still in a development stage compared to other mature markets Position of China in the global EV environment Roland Berger E-Mobility Index 2013/2014 Study methodology INDUSTRY > Yearly study comparing selected 5 countries based on three dimensions – Industry index: EV vehicle 4 production and cell production Japan USA – Technology index: EV performance 3 and government funding – Market index: EV sales ratio South Korea 2 France Comments 1 > USA is leading in the EV sales volume which reached 96,000 units in 2013 China Germany Italy > Japan is leading in both technology 0 and industry dimensions 0 1 2 3 4 5 > China is still behind the market TECHNOLOGY leaders, especially in the technology perspective Note: Circle size shows EV/PHEV share of total vehicle market, Korea has yet to introduce EV/PHEVs in the market Source: FKA, Inside EVs; Roland Berger 20140416_EV Status China_speech_vsend.pptx 3 USA and Japan remain most important production locations -
Contemporary Amperex Technology
China Consumer Discretionary 30 August 2018 China New Energy Vehicles Battery study: emerging giants ahead of the curve We forecast China’s battery shipments to show a CAGR of 41% over 2017-20E on an NEV sales CAGR of 39% Likely near-term pain from high pricing pressure, but could be positive Kelvin Lau for market leaders as they gain market share (852) 2848 4467 Initiating on CATL with a Buy (1); reiterating Buy (1) calls on Guoxuan [email protected] and BYD; pecking order: CATL, Guoxuan and BYD Jay Lu (852) 2848 4970 [email protected] See important disclosures, including any required research certifications, beginning on page 52 China Consumer Discretionary 30 August 2018 China New Energy Vehicles Battery study: emerging giants ahead of the curve We forecast China’s battery shipments to show a CAGR of 41% over 2017-20E on an NEV sales CAGR of 39% Likely near-term pain from high pricing pressure, but could be positive Kelvin Lau for market leaders as they gain market share (852) 2848 4467 Initiating on CATL with a Buy (1); reiterating Buy (1) calls on Guoxuan [email protected] and BYD; pecking order: CATL, Guoxuan and BYD Jay Lu (852) 2848 4970 [email protected] What's new: In this report, we analyse the growth prospects of China’s Key stock calls new energy vehicle (NEV) market, EV battery supply and demand, and New Prev. industry development from now until 2020. Taking into account likely strong Contemporary Amperex Technology (300750 CH) Rating Buy market growth as well as cuts to NEV subsidies, we are positive on the Target 86.00 outlook for market leaders, especially those with cutting-edge technology. -
Press Kit Iaa 2017
BACK PRESS KIT IAA 2017 PRESS KIT | IAA 2017 1 TABLE OF CONTENT BACK >> 04 CONCEPT CONCEPT CAR XiM18 >> 8 SMART EXPERIENCE SURFACES IN MOTION >> 12 COLLABORATION WITH KEY INNOVATIVE COMPANIES >> 14 ACTIVESKIN PRODUCT HIGHLIGHTS >> 16 NATURAL FIBER >> 20 NEW BRAND >> 22 POSITIONING FACTS & FIGURES BACKGROUND >> 26 PRESS PHOTO >> 32 INFORMATION OVERVIEW PEOPLE >> 36 MEDIA CONTACTS PRESS KIT | IAA 2017 3 XiM18, Yanfeng Automotive Interiors’ new concept car, transforms the way people experience vehicle interiors, crafting the next living space where look, feel and function are seamlessly integrated. 4 YFAI’S XiM18 IS RE-DEFINING THE NEXT LIVING SPACE BACK THE YANFENG AUTOMOTIVE INTERIORS XiM18 MAKES EUROPEAN PREMIERE AT IAA 2017 Yanfeng Automotive Interiors (YFAI), the global leader in automotive interior solutions, has unveiled its eXperience in Motion (XiM18) concept car at the IAA International Motor Show today. Presented for the first time in Europe, the XiM18 showcases the way people experience vehicle interiors, if they no longer have to drive. It is designed to enable the use of four different interior modes: Drive, Family, Meeting and Lounge, enabling the vehicle to be used in various ways, by multiple people. With this new concept the company supports the next generation of electric and autonomous driving cars. In times of new forms of car ownership and shared mobility, a unique product look, feel and function through seamless integration of interior surfaces and personalized human-machine-interface is what occupants look for. XiM18 combines a multitude of new technologies for cockpits and instrument panels, as well as advancements in pillar trim, lighting and overhead module integra- tion. -
GLOBAL ECONOMIC OBSERVER No. 6, Vol. 2/2018
GLOBAL ECONOMIC OBSERVER No. 6, vol. 2/2018 http://www.globeco.ro contact: [email protected] [email protected] ISSN 2343 - 9742 ISSN-L 2343 - 9742 ISSN(ONLINE) 2343 - 9750 CONTENTS CHINESE FDI IN CENTRAL AND EASTERN EUROPE. AN OVERVIEW OF FACTORS MOTIVATING CHINESE MNES IN THE CEE REGION Ágnes Szunomár ................................................................................................................... 4 PROFESSIONAL EXO-JUDGMENT PERCEPTION – A QUANTITATIVE RESEARCH BASED ON AN INNOVATIVE CONCEPTUAL STRUCTURE Viorica Mirela Stefan-Duicu, Adrian Stefan-Duicu ........................................................... 17 PREPARING THE BANKING SECTOR FROM THE REPUBLIC OF MOLDOVA FOR THE IMPLEMENTATION OF BASEL III Stela Ciobu, Victoria Iordachi ............................................................................................ 26 COLLECTIVE REDRESS FOR CONSUMERS: TOWARD AN EU WIDE COLLECTIVE ACTION MECHANISM Monica Calu, Costel Stanciu .............................................................................................. 38 TECHNOLOGICAL INNOVATION AND TOTAL FACTOR PRODUCTIVITY GROWTH OF RICE PRODUCTION IN BANGLADESH IN THE POST- LIBERALISATION ERA Dayal Talukder, Love Chile ............................................................................................... 50 ARTIFICIAL INTELLIGENCE (AI) - THE TECHNOLOGY THAT SHAPES THE WORLD Edith Mihaela Dobrescu, Emilian M. Dobrescu ................................................................. 71 CONSEQUENCES OF TECHNOLOGICAL CHANGES IN THE AUTOMOTIVE INDUSTRY -
Master Thesis
Master´s Programme in Strategic Management and Leadership, 60 credits MASTER Power of E-Motion THESIS Business Model Innovation for the Introduction of Electric Cars to China Tobias Abt and Fabian Erath Master thesis, 15 credits Halmstad 2014-06-15 Acknowledgements Acknowledgements Being the last part of our masters studies we have been working and investigating in a truly interesting field over the last month. During our research in the area of Business Model Innovation in the automobile industry with a special focus on China, we could not only gain new knowledge but also learned to value perseverance and diligence as a way to conduct our work. We hope that our thesis will serve as a handbook for business model innovation when considering introducing E-Cars to China and will be of enjoyment to any potential reader. The biggest thank-you goes to our supervisor Mike Danilovic and our examiner Maya Hoveskog for their critical and honest feedback, engagement, support and discussion rounds which helped us during our research process. In addition, we would like to thank Tiantian Qi, Business Manager – Auto Components Working Group, Retail and Distribution Forum and Corporate Social Responsibility Forum of the European Union Chamber of Commerce in China for the valuable information she supplied about the Chinese car industry. Moreover, we would like to thank our opponents for their effort in reviewing our paper and challenging us with critical questions. Finally, a special thanks is given to our friends and families who supported and encouraged us during our studies. Halmstad, June 2014 _________ __________ Tobias Abt Fabian Erath I Abstract Abstract E-Cars challenge prevailing business practices, especially in industrial sectors that heavily depend on the use of fossil fuels such as the automobile industry. -
China Annex VI
Annex I. Relations Between Foreign and Chinese Automobile Manufacturers Annex II. Brands Produced by the Main Chinese Manufacturers Annex III. SWOT Analysis of Each of the Ten Main Players Annex IV. Overview of the Location of the Production Centers/Offices of the Main Chinese Players Annex V. Overview of the Main Auto Export/Import Ports in China Annex VI. An Atlas of Pollution: The World in Carbon Dioxide Emissions Annex VII. Green Energy Vehicles Annex VIII. Further Analysis in the EV vehicles Annex IX. Shifts Towards E-mobility Annex I. Relations Between Foreign and Chinese Automobile Manufacturers. 100% FIAT 50% Mitsubishi Guangzhou IVECO 50% Beijing Motors 50% Hyundai 50% GAC Guangzhou FIAT GAC VOLVO 91.94% Mitsubishi 50% 50% 50% 50% 50% (AB Group) Guangzhou BBAC 50% Hino Hino Dongfeng DCD Yuan Beiqi 50% 50% NAVECO Invest Dongfeng NAC Yuejin 50% Cumins Wuyang 50% Guangzhou GAC Motor Honda 50% Yuejin Beiqi Foton Toyota 50% Cumins DET 50% 55.6% 10% 20% 50% Beiqi DYK 100% Guangzhou Group Motors 50% 70% Daimler Toyota 30% 25% 50% 65% Yanfeng SDS shanghai 4.25% 100% 49% Engine Honda sunwin bus 65% 25% visteon Holdings Auto 50% (China) UAES NAC Guangzhou 50% Beilu Beijing 34% Denway Automotive 50% Foton 51% 39% motorl Guangzhou 50% Shanghai Beiqi Foton Daimler 100% 30% 50% VW BAIC Honda Kolben 50% 90% Zhonglong 50% Transmission 50% DCVC schmitt Daimler Invest 100% 10% Guangzhou piston 49% DFM 53% Invest Guangzhou Isuzu Bus 100% Denway Beiqi 33.3% Bus GTE GTMC Manafacture xingfu motor 50% 20% SAIC SALES 100% 20% 100% 100% DFMC 100% Shanghai -
Leapfrogging Or Stalling Out? Electric Vehicles in China
Leapfrogging or Stalling Out? Electric Vehicles in China Sabrina Howell Henry Lee Adam Heal 2015 RPP-2015-07 Regulatory Policy Program Mossavar-Rahmani Center for Business and Government Harvard Kennedy School 79 John F. Kennedy Street, Weil Hall Cambridge, MA 02138 CITATION This paper may be cited as: Howell, Sabrina, Henry Lee, and Adam Heal. 2015. “Leapfrogging or Stalling Out? Electric Vehicles in China.” Regulatory Policy Program Working Paper RPP-2015-07. Cambridge, MA: Mossavar-Rahmani Center for Business and Government, Harvard Kennedy School, Harvard University. Comments may be directed to the authors. REGULATORY POLICY PROGRAM The Regulatory Policy Program at the Mossavar-Rahmani Center for Business and Government serves as a catalyst and clearinghouse for the study of regulation across Harvard University. The program's objectives are to cross-pollinate research, spark new lines of inquiry, and increase the connection between theory and practice. Through seminars and symposia, working papers, and new media, RPP explores themes that cut across regulation in its various domains: market failures and the public policy case for government regulation; the efficacy and efficiency of various regulatory instruments; and the most effective ways to foster transparent and participatory regulatory processes. The views expressed in this paper are those of the authors and do not imply endorsement by the Regulatory Policy Program, the Mossavar-Rahmani Center for Business and Government, Harvard Kennedy School, or Harvard University. FOR FURTHER INFORMATION Further information on the Regulatory Policy Program can be obtained from the Program's executive director, Jennifer Nash, Mossavar-Rahmani Center for Business and Government, Weil Hall, Harvard Kennedy School, 79 JKF Street, Cambridge, MA 02138, telephone (617) 495-9379, telefax (617) 496-0063, email [email protected]. -
2018 Sustainability Report. Bmw Brilliance Automotive Ltd
Sheer Driving Pleasure 2018 SUSTAINABILITY REPORT. BMW BRILLIANCE AUTOMOTIVE LTD. 2 CONTENTS CONTENTS 3 CONTENTS SUSTAINABILITY PRODUCT AND SERVICE INTRODUCTION 1 MANAGEMENT 2 RESPONSIBILITY CEO Preface 4 1.1 Strategy and Management 23 2.1 Strategy and Management 45 Our Point of View 6 1.2 Stakeholder Engagement 29 2.2 Product Safety and Quality 47 Highlights in 2018 8 1.3 Digitalisation and Innovation 32 2.3 Responsible Mobility 50 An Overview of BMW Brilliance 10 1.4 Being a Responsible Business 34 2.4 Customers and Dealers Engagement 54 GREEN AND SMART SUSTAINABLE SUPPLIER EMPLOYEE 3 PRODUCTION 4 MANAGEMENT 5 DEVELOPMENT 3.1 Strategy and Management 64 4.1 Strategy and Management 83 5.1 Strategy and Management 98 3.2 Building Infrastructure 67 4.2 Supplier Performance Improvement 84 5.2 Core Values 100 3.3 Green and Smart Manufacturing 68 4.3 Supplier Base Development and Training 87 5.3 Being an Attractive Employer 102 3.4 Resource Efficiency 70 5.4 Health and Wellbeing 107 5.5 Training and Development 111 CORPORATE SOCIAL 6 RESPONSIBILITY 7 APPENDIX 6.1 Strategy and Management 121 7.1 About This Report 134 6.2 BMW CSR Activities 125 7.2 GRI Content Index 135 7.3 Limited Assurance Report 143 7.4 Basis of Reporting 146 4 INTRODUCTION • CEO Preface CEO Preface • INTRODUCTION 5 CEO PREFACE “Our brand-new sustainability much larger High Voltage Battery Centre in Shenyang, Our 18,925 employees are the lifeblood of this we will soon have the capabilities to produce the next company, and we do our best to help them maximise strategy is our manifesto for generation BMW batteries and electric drive-train.