A Numerical Study on the Effect of Explosive Reactive Armour on a Lightweight Armoured Vehicle's Hull
Total Page:16
File Type:pdf, Size:1020Kb
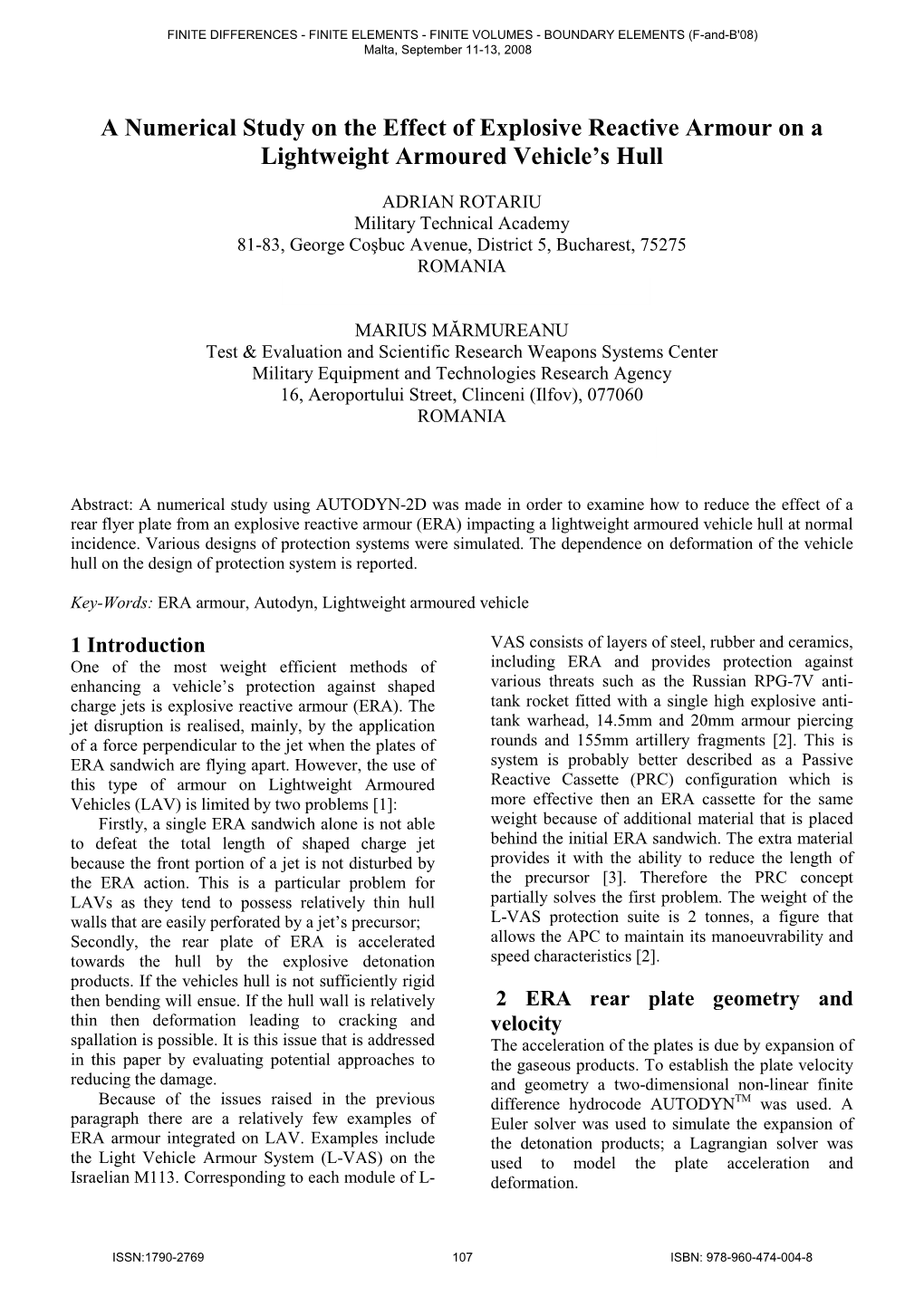
Load more
Recommended publications
-
Codex Astartes: the Space Marines (Version 1.4) Introduction
Codex Astartes: The Space Marines (version 1.4) Table of Contents Introduction - Why Space Marines? - What is in this Sourcebook? 1. Character Generation Stage One: Homeworld Stage Two: Generating Characteristics Stage Three: Determine Career Path Stage Four: Spending Experience Points, Buy Equipment 2. Space Marine Career Path 3. New Skills 4. New Talents 5. New Psychic Powers 6. Astartes Chapter Armoury New Craftsmanship New Weapon Special Qualities Ranged Weapons Melee Weapons Weapon Upgrades Ammo Armour Armour Upgrades Gear Cybernetics 7. Vehicles Ground Vehicles Air/Space Vehicles Special Vehicles Vehicle Upgrades 8. The Chapters The First Founding The Second Founding Subsequent Foundings Feature: The Red Hunters Chapter 9. Life in the Chapter Life in & out of combat (i.e. character downtime) Roleplaying aspects Inquisition, Ecclesiarchy, IG, Planetary Govt 10. Aliens, Heretics & Traitors xenos traitor marines Introduction Designer’s Note: This is a conversion of information from the years of Space Marine literature printed by Games Workshop into the DH system. This is the Space Marines as the superhuman protectors of the Imperium and is not balanced against the 8 established careers in the DH core rulebook. Although there is a suggestion for allowing a Space Marine in an acolyte group (see Game Master’s Notes), these rules are recommend for an all Space Marine campaign which would proceed from characters being recruited together and proceeding all the way up to company leadership or Deathwatch membership. Chapter I: Character Creation Stage One: Homeworld See DH core rulebook page 13 for details. Stage Two: Generating Characteristics (Modified for Space Marine Recruitment) Game Master’s Note: Before generating characteristics, determine how your Space Marine characters will be part of your campaign. -
Stab Resistant Body Armour
IAN HORSFALL STAB RESISTANT BODY ARMOUR COLLEGE OF DEFENCE TECHNOLOGY SUBMITTED FOR THE AWARD OF PhD CRANFIELD UNIVERSITY ENGINEERING SYSTEMS DEPARTMENT SUBMITTED FOR THE AWARD OF PhD 1999-2000 IAN HORSFALL STAB RESISTANT BODY ARMOUR SUPERVISOR DR M. R. EDWARDS MARCH 2000 ©Cranfield University, 2000. All rights reserved. No part of this publication may be reproduced without the written permission of the copyright holder. ABSTRACT There is now a widely accepted need for stab resistant body armour for the police in the UK. However, very little research has been done on knife resistant systems and the penetration mechanics of sharp projectiles are poorly understood. This thesis explores the general background to knife attack and defence with a particular emphasis on the penetration mechanics of edged weapons. The energy and velocity that can be achieved in stabbing actions has been determined for a number of sample populations. The energy dissipated against the target was shown to be primarily the combined kinetic energy of the knife and the arm of the attacker. The compliance between the hand and the knife was shown to significantly affect the pattern of energy delivery. Flexibility and the resulting compliance of the armour was shown to have a significant effect upon the absorption of this kinetic energy. The ability of a knife to penetrate a variety of targets was studied using an instrumented drop tower. It was found that the penetration process consisted of three stages, indentation, perforation and further penetration as the knife slides through the target. Analysis of the indentation process shows that for slimmer indenters, as represented by knives, frictional forces dominate, and indentation depth becomes dependent upon the coefficient of friction between indenter and sample. -
Denv S090015 Military Vehicle Protection.Qxd
Defence TNO | Knowledge for business Military vehicle protection Finding the best armour solutions circuit armour. All these current and future armours require constant and rigorous testing under fully controlled conditions. The Laboratory for Ballistic Research is a state of the art research facility of TNO and able to provide these conditions. New threats In today's scenarios, the threat to a military vehicle may come from any direction, including above and below. The crew of a military vehicle not only has to deal with more or less 'standard' fire from the enemy in front, but - more often than not - also with asymmetric threats like rocket-propelled grenades, explosively formed projectiles, mines and improvised explosive devices. The RPG7, for instance, is able to cut through 250 mm of armour steel. Falling prey to any of these threats, also known as a 'cheap kill', Developments in vehicle armour never stop. It's not just the nature of the is something that has to be avoided at all threat that is continually changing, but we also have to deal with new times. TNO uses its highly advanced resources and decades of expertise in armour trends in warfare, like lightweight armoured vehicles. For survival, today's research to help governments and and tomorrow's military vehicles will not only have to rely on armour, but manufacturers achieve their aim: the optimal e.g. also on mobility and manoeuvrability. TNO supports its clients - protection of military vehicles against the governments and manufacturers - in finding the best armour solutions for widest possible range of ballistic threats. -
The Evolution of Armour Steel
May 26, 2021 Clad in Steel: The Evolution of Armour Steel A little over a century ago, the armed forces of the British Empire received a new type of land-based military vehicle. The British Admiralty led the vehicle’s development in the utmost secrecy. To justify the connection with the Royal Navy, the invention was called a “landship” in official documents. As the Admiralty also managed oil production and processing, it decided to codename this vehicle the “tank” to mislead adversaries. This name is still used for self-propelled tracked armoured combat vehicles. Nowadays, armed forces around the world have hundreds of different types of tanks and other self-propelled vehicles. A key feature that they share is an armoured hull made of specialty grade steel . This protects the crew and critical parts from bullets, shells and other devastating effects. Over the past 100 years, one of the main challenges for designers has been to reduce the weight of armoured vehicles while increasing the level of protection that they provide. Aside from products for military use, civilian applications for armoured vehicles have also been developed. At the beginning of the 20th century, steel plates were used to reinforce the carriages of royalty and high-ranking officials. Today, armoured vehicles are used by heads of state, businesspeople, sport stars and entertainers. They are also used by government agencies and security services, as well as by banks for cash collection and transportation. Below, we discuss what armour is, how these steels evolved, as well as the role that Ukraine played in these developments. -
Contemporary Personal Ballistic Protection (PBP)
Chapter 8 Contemporary Personal Ballistic Protection (PBP) Izabela Luiza Ciesielska-Wróbel Additional information is available at the end of the chapter http://dx.doi.org/10.5772/intechopen.69085 Abstract The review concerns existing contemporary protective equipment and their compo- nents serving against ballistic and non-ballistic threats of different sorts. The main focus, however, is on the personal ballistic protection (PBP) based on textile components and their role in the protective elements. Soft ballistic protections are crucial Soft ballistic protections are crucial elements of PBP, forexample in military and law enforcements. Although the subject of PBP was limited in this chapter to soft ballistic protection, other elements, e.g. hard ballistic protection, stab-resistant vests, dual threat, so-called in-con- junction protective elements, modern helmets, were also mentioned in this chapter to demonstrate positioning of the soft ballistic protection and other elements in the global personal protection approach. Apart from it, the chapter contains selected information concerning high-performance polymers and fibres as well as a brief notes about their application in protective panels being basic elements of any protective element. The final remarks concern the most up-to-date approach in relation to ballistic protection, which is immersing high-performance fibres into non-Newtonian liquid substances having the ability of ordering their chemical particles and changing into a high concentration and high segregation lattice under the influence of kinetic energy impact. Keywords: personal ballistic protection, soft body armour, hard body armour, dual threat, stab-resistant vests, bullet-resistant vests, protective panels, high-performance fibres 1. Introduction This chapter provides selected and the most up-to-date information concerning personal ballistic protection (PBP). -
PDF Download Armour Pdf Free Download
ARMOUR PDF, EPUB, EBOOK Catriona Clarke,Terry McKenna | 32 pages | 26 Jan 2007 | Usborne Publishing Ltd | 9780746074749 | English | London, United Kingdom Armour Thyroid (thyroid tablets, USP) Home Page Keep using this medicine as directed, even if you feel well. You may need to take thyroid medication for the rest of your life. Call your doctor if you notice any signs of thyroid toxicity, such as chest pain, fast or pounding heartbeats, feeling hot or nervous, or sweating more than usual. If you need surgery, tell the surgeon ahead of time that you are using desiccated thyroid. You may need to stop using the medicine for a short time. Take the missed dose as soon as you remember. Skip the missed dose if it is almost time for your next scheduled dose. Do not take extra medicine to make up the missed dose. If you also take cholestyramine Prevalite , Questran or colestipol Colestid , avoid taking these medications within 4 hours before or after you take desiccated thyroid. Avoid taking an antacid within 4 hours before or after you take desiccated thyroid. Some antacids can make it harder for your body to absorb desiccated thyroid. Get emergency medical help if you have signs of an allergic reaction: hives ; difficult breathing; swelling of your face, lips, tongue, or throat. Common side effects may include temporary hair loss especially in children. This is not a complete list of side effects and others may occur. Call your doctor for medical advice about side effects. Armour Thyroid side effects in more detail. Tell your doctor about all medicines you use, and those you start or stop using during your treatment with desiccated thyroid, especially:. -
Aravain. ‘Very Well, but I Have Told You What I Sense
The Primarchs LION EL’JONSON: LORD OF THE FIRST KONRAD CURZE: THE NIGHT HAUNTER ANGRON: SLAVE OF NUCERIA CORAX: LORD OF SHADOWS VULKAN: LORD OF DRAKES JAGHATAI KHAN: WARHAWK OF CHOGORIS FERRUS MANUS: GORGON OF MEDUSA FULGRIM: THE PALATINE PHOENIX LORGAR: BEARER OF THE WORD PERTURABO: THE HAMMER OF OLYMPIA MAGNUS THE RED: MASTER OF PROSPERO LEMAN RUSS: THE GREAT WOLF ROBOUTE GUILLIMAN: LORD OF ULTRAMAR Also available KONRAD CURZE: A LESSON IN DARKNESS Ian St. Martin (audio drama) SONS OF THE EMPEROR Various authors CONTENTS Cover Backlist Title Page The Horus Heresy One Two Three Four Five Six Seven Eight Nine Ten Eleven About the Author An Extract from ‘Scions of the Emperor’ A Black Library Publication eBook license THE HORUS HERESY It is a time of legend. Mighty heroes battle for the right to rule the galaxy. The vast armies of the Emperor of Mankind conquer the stars in a Great Crusade – the myriad alien races are to be smashed by his elite warriors and wiped from the face of history. The dawn of a new age of supremacy for humanity beckons. Gleaming citadels of marble and gold celebrate the many victories of the Emperor, as system after system is brought back under his control. Triumphs are raised on a million worlds to record the epic deeds of his most powerful champions. First and foremost amongst these are the primarchs, superhuman beings who have led the Space Marine Legions in campaign after campaign. They are unstoppable and magnificent, the pinnacle of the Emperor’s genetic experimentation, while the Space Marines themselves are the mightiest human warriors the galaxy has ever known, each capable of besting a hundred normal men or more in combat. -
CAMAC Brochure
www.npaerospace.com CAMAC Platform Armour Complete Composite Platform Armour Systems We Have Delivered: At Up To Half the Weight of Steel Alternatives NP Aerospace combines core competencies in materials technology, manufacturing processes and integration to deliver world-leading CAMAC® composite armour systems for vehicles, ships and aircraft. Engineered using a unique combination of advanced ceramic and structural composite materials, our high performance multi-hit CAMAC® armour weighs up to 50% less than equivalent steel products. Our armour systems are tailored to the requirements of the threat, the individual The full armour package for SAIC’s ACV 1.1, Spall liner and full armour integration for the Mastiff family of vehicles, including Mastiff, platform and its operational duties. Our capabilities include: including applique armour, spall liners and lightweight composite floatation boxes. Ridgback, Wolfhound and Buffalo. • CAMAC® Spall liners for enhanced crew protection • CAMAC® Appliqué armour systems for vehicle and other platforms • CAMAC® Ultra-light semi-structural armour systems for protected weapon stations and other applications • CAMAC® Composite survivability pods for light patrol vehicles An integrated survivability capsule for TATA Motors, Shaped spall liner for the BAE Systems saving over 1 tonne of weight against steel alternatives. Terrier combat engineering vehicle. Lightweight collapsible protected Covert vehicle armour for a weapons stations for Navistar. variety of base platforms. 2 3 CAMAC Platform Armour CAMAC® Appliqué Armour CAMAC® Semi-Structural Armour CAMAC® Appliqué armour provides lightweight, multi-hit protection for new and existing CAMAC® ultra-light semi-structural armour provides platforms against a wide range of threats including small or medium calibre weapons, effective multi-hit protection for vehicle-mounted weapon improvised explosive devices (IEDs) or rocket propelled grenades (RPGs). -
1 Introduction
1 INTRODUCTION It will not be surprising to the reader that over the last century it has been increasingly necessary to apply thicker armour plates to armoured fighting vehicles to provide protection against new gun and projectile designs. Consequently, the design of a modern armoured fighting vehicle has evolved so that it will typically have 40–50% of its weight accounted for by protection. But as the weight of the armour increases, maintaining mobility and stealth, and deploying these vehicles over large strategic distances becomes increasingly problematic. Furthermore, armed forces would prefer to deploy armoured fighting vehicles to the battlefield by air—simply because of speed. This factor alone has led to a number of design constraints that have been placed on future armoured fighting vehicles intended to reduce their bulk and weight. At the same time, we are finding that weapons that are used to attack armoured vehicles have developed to the extent that: • some of the more advanced shaped-charge warheads can penetrate well over a metre of rolled homogeneous armour (RHA); • kinetic-energy long-rod penetrators are getting longer and faster and as a consequence are able to penetrate ever-greater depths of RHA; and • explosively formed projectiles and shaped-charge jet warheads are being delivered to their target in a variety of ways to exploit zones on an armoured vehicle that have traditionally been less well protected—such as the roof. Therefore it is desirable to ensure that universal protection is provided against all of these threats all around the vehicle—this adds weight! There was little improvement in the performance of armour materials between and during the two world wars and just after WWII when armoured vehicles used steel as the main armour material. -
Electric Armour for Armoured Vehicles (ELAV) - Executive Summary
A part of BMT in Defence COMMERCIAL - IN - CONFIDENCE REQUEST FOR INGORMATION EXPLOSIVE LINE CHARGE SYSTEMS Electric Armour for Armoured Vehicles (ELAV) - Executive Summary EDA Reference: 09-R&T-005 BMT Reference: 36745/R4563 Date: 4th May 2010 UNCLASSIFIED [bmt contract no/report no] [MMMMM YYYY] [issue] [CLASSIFICATION - DESCRIPTOR] UNCLASSIFIED ELECTRIC ARMOUR FOR ARMOURED VEHICLES 1 STUDY OVERVIEW 1.1.1 Under contract number 09-R&T-005, BMT Defence Services Limited (BMT) conducted a pan-European study into previous, current and planned research in Electric Armour (EA). The aim of this study was to coordinate and focus Research & Technology (R&T) effort at the European level and achieve a commensurate increase in efficiency, cross-pollination, innovation and exploitation of Key Technologies throughout the participating Member States (pMS). This study was carried out in the framework of EDA CapTech GEM3 “Ground Systems and their Environment”. It was conducted from November 2009 until June 2010. 1.1.2 The potential benefits stemming from the introduction of EA into Armoured Vehicles include: a. Increased protection to personnel and equipment; b. Increased strategic air-transportability; c. Increased tactical mobility. 1.1.3 However, the integration of these systems in a safe, practical and cost effective manner is not without difficulty. Several areas are critical, including: a. The requirement for high density and very rapid response power generation, storage, control and distribution systems; b. The safe integration of Mega-Ampere Pulsed Power systems into confined spaces alongside sensitive equipment and crew; c. Electromagnetic Compatibility and protection of equipment in a high power electrical discharge environment; d. -
(AVF0005) 1 Written Evidence Submitted by Brigadier
(AVF0005) Written evidence submitted by Brigadier (Retired) BW Barry OBE Senior Fellow Land Warfare International Institute for Strategic Studies (IISS) INQUIRY INTO BRITISH ARMOURED VEHICLE CAPABILITY HCDC is conducting an inquiry that “will focus on the procurement and use of Armoured Fighting Vehicles (AFVs) and ask whether more must be done to ensure the Army’s ability to deploy an armoured division.”i This submission provides analysis to assist in answering this question and subordinate questions including: - “Whether the Army is currently on track to be able to field the Strike Brigades and armoured division in line with the recommendations of the 2015 SDSR”. - “Whether the Army will be able to match the potential threat posed by peer adversaries by 2025” - The 13 more detailed questions listed at the Call for evidence.ii It is based on IISS analysis of global armoured warfare capabilities published in the annual IISS Military Balance and data held in the Military Balance+ database, as well as a strong body of analysis of recent, current, and future wars and the roles of AFVs in conflict. It does not look beyond 2030. EXECUTIVE SUMMARY Armoured warfare is a capability of great relevance, both currently and in the future. Based on data held by the Military Balance+ database, some 250,000 AFVs are in service globally. Most current British Army AFVs are either obsolete or approaching obsolescence. Together with the introduction of the Ajax and Boxer AFVs, the Army’s plans to upgrade Challenger and Warrior have the potential for a transformational enhancement to British armoured warfare capabilities. -
Eldar Character Guide
Eldar Character Guide The Path of the Outcast Table of Contents Chapter 1: An Ancient and Powerful Race 3 Chapter 6: Eldar Presence in the Expanse 63 An Ancient History 4 Craftworld Kelor 63 Eldar Physiology 5 Survivors of Strike 64 Eldar Clans and Craftworlds 6 Methods of War 64 Dead Gods 7 The Children of the Thorns 65 Paths of the Eldar 7 The Twlight Swords 65 Spirit Stones 8 The Crow Spirits 67 The Webway 8 Chapter 7: Eldar Starships 69 Eldar Technology 9 Eldar Vessel Special Rules 71 Chapter 2: Eldar Warriors 11 Eldar Weapon Special Rules 72 Guardians 12 Traversing the Webway 72 Corsairs 12 Creating Eldar Starships 73 Dark Reaper 13 Eldar Starship Hulls 74 Fire Dragon 14 Corsair Ship Hulls 75 Howling Banshee 15 Craftworld Ship Hulls 77 Shadow Spectre 16 Eldar Starship Components 79 Striking Scorpion 17 Chapter 8: Alternate Career Ranks 80 Swooping Hawk 17 Bonesinger 82 Warp Spider 19 Corsair Prince 84 Autarch 20 Harlequin 86 Wraithguard 22 Wraithlord 23 A Note from the Author 88 Chapter 3: Eldar Explorers 24 Paths of Ages Past 25 The Path of the Outcast 27 The Path of the Seer 34 New Skills 41 New Talents 42 New Traits 45 Chapter 4: Eldar Armory 46 Weapons 46 Armor 51 Gear 52 Armory Tables 54 Chapter 5: Eldar Psychic Powers 55 Farseer 56 Void Dreamer 59 Warlock 61 2 Chapter 1: An Ancient and Powerful Race The Eldar are an ancient and enigmatic species Clans such as the Crow Spirits and the Twilight which dominated the galaxy millions of years Swords are a plague upon Imperial shipping, their before the rise of the Imperium.