Requirements for Building Information Modeling Based Lean Production
Total Page:16
File Type:pdf, Size:1020Kb
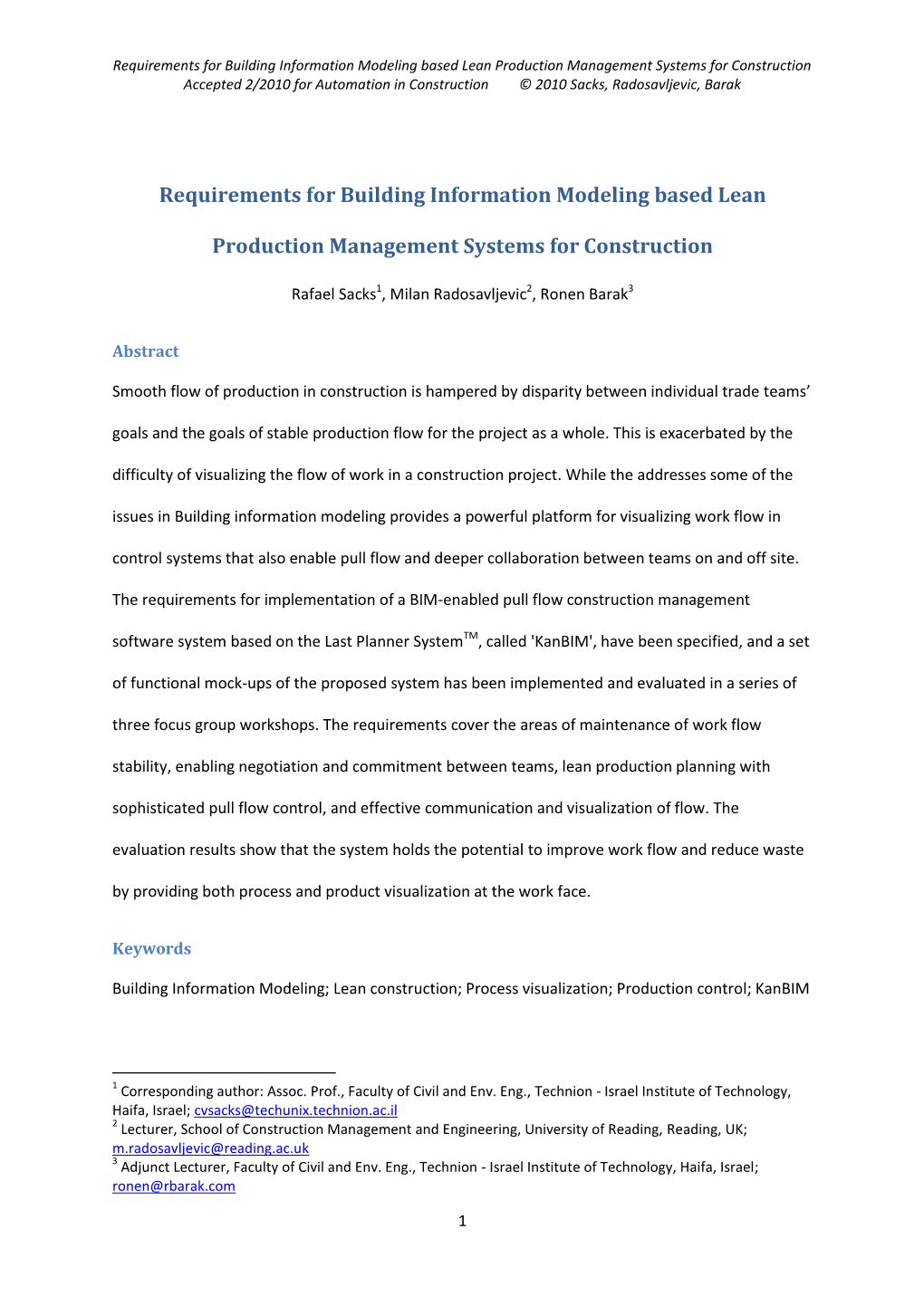
Load more
Recommended publications
-
Mcgraw Hill Construction
SmartMarket Report Lean Construction Leveraging Collaboration and Advanced Practices to Increase Project Efficiency Premier Partner: ■ Design and Construction Intelligence SmartMarket Report McGraw Hill Construction Lean Construction: Leveraging Collaboration and Advanced President Practices to Increase Project Keith Fox EfficiencySmartMarket Report About McGraw Hill Vice President, Product Development Executive Editor Kathryn E. Cassino Harvey M. Bernstein, F.ASCE, LEED AP Construction McGraw Hill Construction’s data, Editorial Advisor and Contributor McGraw Hill Construction analytics, and media businesses— Research & Analytics/ Stephen A. Jones Industry Insights & Alliances Dodge, Sweets, Architectural Record, Editorial Director GreenSource, and Engineering Vice President, Industry Michele A. Russo, LEED AP News-Record— create opportunities Insights & Alliances Harvey M. Bernstein, F.ASCE, LEED AP Managing Editor for owners, architects, engineers, Donna Laquidara-Carr, LEED AP contractors, building product Senior Director, Research & Analytics manufacturers, and distributors to Burleigh Morton Senior Director, Head of Marketing strengthen their market position, size Director, Green Content & William Taylor their markets, prioritize prospects, Research Communications and target and build relationships Michele A. Russo, LEED AP Manager, Content Operations Juan Ramos that will win more business. McGraw Hill Construction serves more than Reproduction or dissemination Art Directors one million customers through its of any information contained -
Moving-On — Beyond Lean Thinking
Moving-on — beyond lean thinking Lauri Koskela1 Abstract Lean Thinking is currently often positioned as the underlying theory of lean production among practitioners and academics, although its originators, Womack and Jones, seem not to have presented it as a theory. This paper endeavours to analyze whether Lean Thinking can be viewed as a theory of lean production. For this purpose, a critical assessment of Lean Thinking is carried out. Lean Thinking is argued to lack an adequate conceptualization of production, which has led to imprecise concepts, such as the term “value”. The five principles of Lean Thinking do not systematically cover value generation, and they do not always encapsulate the core topics in their respective areas. The failure to trace the origin of lean concepts and principles reduces the opportunity to justify and explain them. Despite claims for generality, the application area of the five lean principles is limited to the transformation of mass production, with, for instance, one-of-a-kind production and construction being largely out of scope. It is concluded that it is opportune to move on beyond Lean Thinking, towards a generic theory of production, for acquiring a solid foundation for designing, operating and improving production systems. Keywords: Lean thinking, theory, production Introduction “Lean production is ‘lean’ because it uses less of everything compared with mass production: half the human effort in the factory, half the manufacturing space, half the investments in tools, half the engineering hours to develop a new product in half the time.” This characterization of lean production, as presented in the book The machine that changed the world by Womack, Jones and Roos (1990), captured the attention of production practitioners and researchers worldwide. -
Mistakeproofing the Design of Construction Processes Using Inventive Problem Solving (TRIZ)
www.cpwr.com • www.elcosh.org Mistakeproofing The Design of Construction Processes Using Inventive Problem Solving (TRIZ) Iris D. Tommelein Sevilay Demirkesen University of California, Berkeley February 2018 8484 Georgia Avenue Suite 1000 Silver Spring, MD 20910 phone: 301.578.8500 fax: 301.578.8572 ©2018, CPWR-The Center for Construction Research and Training. All rights reserved. CPWR is the research and training arm of NABTU. Production of this document was supported by cooperative agreement OH 009762 from the National Institute for Occupational Safety and Health (NIOSH). The contents are solely the responsibility of the authors and do not necessarily represent the official views of NIOSH. MISTAKEPROOFING THE DESIGN OF CONSTRUCTION PROCESSES USING INVENTIVE PROBLEM SOLVING (TRIZ) Iris D. Tommelein and Sevilay Demirkesen University of California, Berkeley February 2018 CPWR Small Study Final Report 8484 Georgia Avenue, Suite 1000 Silver Spring, MD 20910 www. cpwr.com • www.elcosh.org TEL: 301.578.8500 © 2018, CPWR – The Center for Construction Research and Training. CPWR, the research and training arm of the Building and Construction Trades Department, AFL-CIO, is uniquely situated to serve construction workers, contractors, practitioners, and the scientific community. This report was prepared by the authors noted. Funding for this research study was made possible by a cooperative agreement (U60 OH009762, CFDA #93.262) with the National Institute for Occupational Safety and Health (NIOSH). The contents are solely the responsibility of the authors and do not necessarily represent the official views of NIOSH or CPWR. i ABOUT THE PROJECT PRODUCTION SYSTEMS LABORATORY (P2SL) AT UC BERKELEY The Project Production Systems Laboratory (P2SL) at UC Berkeley is a research institute dedicated to developing and deploying knowledge and tools for project management. -
A Simulation of Lean Construction Principles
Pollesch, P., Rovinsky, A., Alvarado III, R., and Alves, T.C.L. (2017). “House of Cards – a Simulation of Lean Construction Principles” In: LC3 2017 Volume II – Proceedings of the 25th Annual Conference of the International Group for Lean Construction (IGLC), Walsh, K., Sacks, R., Brilakis, I. (eds.), Heraklion, Greece, pp. 373–380. DOI: https://doi.org/10.24928/2017/0212 HOUSE OF CARDS – A SIMULATION OF LEAN CONSTRUCTION PRINCIPLES Paul Pollesch1, Alexander Rovinsky2, Raul Alvarado III3, and Thais da C. L. Alves4 Abstract: The "House of Cards" simulation was developed to stimulate discussion and improve the application of lean production concepts (5S, flow, waste, kaizen, transparency, and collaboration) to construction engineering and management. It is a simple, scalable, hands-on exercise that enables a facilitator to lead teams to intuitively grasp lean concepts and their benefits to construction processes. The simulation requires minimal resources for each team: 3-4 players, a deck of playing cards, a timer, and a playing surface. “House of Cards” presents six phases of gameplay, and progresses from a worst-case scenario to an optimized ideal. The objective is to play the cards as quickly as possible to construct a 13-story building. As in construction, there is a logical sequence of work required. Lower floors must be built before upper floors, structural work must precede mechanical, and mechanical must precede finish work. This simulation was developed with a construction project context, but can easily be adapted to other industries. The analogies can be tailored to meet other industrial processes, and the floors can be changed to different parts of assembly or production lines. -
LCM® Takt Planning in Building Construction
LCM® Takt Planning in Building Construction September 26 -27, 2017, UC Berkeley Clark Kerr Campus Patrick Theis Agenda – LCM® Takt Planning in Building Construction LCM® Simulation – Day 1 Time Subject Expert 9:00 – 9:15 am Welcome and Introduction Iris & Samir Challenges in projects and the potential of Lean Construction with emphasis on 9:15 – 9:45 am Samir, Iris, Patrick Takt planning 9:45 – 10:00 am Coffee Break 10:00 – 12:00 am Simulation Round 1 - The traditional project approach Group activity 12:00 – 1:00 pm Lunchbreak 1:00 – 1:30 pm Takt planning Introduction Patrick Production Planning Step 1 – Overall Process Analysis Presentation and 1:30 – 2:30 pm Patrick Workshop 2:30 – 2:45 pm Coffee & Dessert Break Simulation Round 2 - Optimized construction sequence with elimination of 2:45 – 3:45 pm Group Activity waste and adapted process sequence played in the LCM Simulation 3:45 – 4:30 pm Production Planning Step 2: The Process and Takt Planning Presentation Patrick 4:30 – 5:00 pm Wrap up of the day and discussion Samir, Patrick 2 September, 26 - 27 , 2017, LCM Simulation, Patrick Theis Agenda – LCM® Takt Planning in Building Construction LCM® Simulation – Day 2 Time Subject Expert 9:00 – 9:15 am Summary of Day 1 Samir, Patrick Production Planning Step 2: The process and takt planning presentation and 9:15 – 10:30 am Patrick workshop 10:30 – 10:45 am Coffee Break Production Planning Step 3: The Detailed Takt Planning Board on site 10:45 – 12:00 am Group activity Presentation and Workshop 12:00 – 12:45 pm Lunchbreak 12:45 – 1:15 pm -
A Comparison of Takt Time and LBMS Planning Methods
A Comparison of Takt Time and LBMS Planning Methods A COMPARISON OF TAKT TIME AND LBMS PLANNING METHODS Olli Seppänen1 ABSTRACT Takt time and LBMS are getting increased attention from practitioners of Lean Construction. The takt time approach focusses on designing work locations with similar quantities and plans on the same duration for each task without any buffers. To achieve level resource utilization takt time projects require substantial work backlog tasks or locations to absorb periods of low production demand. The LBMS approach plans on using consistent resources through all the locations. Buffers are added to absorb the risk of deviations and durations are allowed to vary based on quantity of work. This results in significantly longer schedules but decreases the need for workable backlog areas and the risk of demobilizations. To compare these two methods, three schedules planned with LBMS methodology were reformed into takt time schedules by forcing each task to have the same duration in each location. This was achieved by changing the crew size in each location to achieve a duration shorter than or equal to the takt time. The resulting schedules were compared in terms of total project duration, total project manhours and the risk of duration and manhours evaluated using Monte Carlo simulation. The results indicate that takt time achieves substantially shorter schedules but the manhours required in work backlog areas are much higher than in LBMS approach. In projects where quantities are similar between locations, takt time performs well if the resources are not demobilized when they run out of work. If the resources demobilize, the risk of return delays makes takt time a risky strategy. -
BIM) and Digital Twinning for Sustainable Construction
sustainability Review Lean Practices Using Building Information Modeling (BIM) and Digital Twinning for Sustainable Construction Samad M. E. Sepasgozar 1,* , Felix Kin Peng Hui 2 , Sara Shirowzhan 1 , Mona Foroozanfar 3, Liming Yang 1 and Lu Aye 4 1 Faculty of Built Environment, The University of New South Wales, Sydney, NSW 2052, Australia; [email protected] (S.S.); [email protected] (L.Y.) 2 Engineering Management Group, Department of Infrastructure Engineering, Faculty of Engineering and Information Technology, The University of Melbourne, Victoria, VIC 3010, Australia; [email protected] 3 Faculty of Architecture and Art, University of Tehran, Tehran 14174, Iran; [email protected] 4 Renewable Energy and Energy Efficiency Group, Department of Infrastructure Engineering, Faculty of Engineering and Information Technology, The University of Melbourne, Victoria, VIC 3010, Australia; [email protected] * Correspondence: [email protected]; Tel.: +61-(02)-4696-28400 Abstract: There is a need to apply lean approaches in construction projects. Both BIM and IoT are increasingly being used in the construction industry. However, using BIM in conjunction with IoT for sustainability purposes has not received enough attention in construction. In particular, the capability created from the combination of both technologies has not been exploited. There is a growing consensus that the future of construction operation tends to be smart and intelligent, which would be possible by a combination of both information systems and sensors. This investigation aims to find out the recent efforts of utilizing BIM for lean purposes in the last decade by critically reviewing the published literature and identifying dominant clusters of research topics. -
Lean Construction: an Effective Approach for Project Management
VOL. 11, NO. 3, FEBRUARY 2016 ISSN 1819-6608 ARPN Journal of Engineering and Applied Sciences ©2006-2016 Asian Research Publishing Network (ARPN). All rights reserved. www.arpnjournals.com LEAN CONSTRUCTION: AN EFFECTIVE APPROACH FOR PROJECT MANAGEMENT Richard Hannis Ansah, Shahryar Sorooshian and Shariman Bin Mustafa Faculty of Industrial Management, Universiti Malaysia Pahang (UMP), Lebuhraya Tun Razak, Kuantan, Pahang, Malaysia E-Mail: [email protected] ABSTRACT Projects have been considered as temporary based production systems which need to be designed, produced and delivered within a specified time. It has been asserted by a number of researchers that fast, complex and uncertain projects cannot be managed through the conventional ways and that fast track projects with long, complicated supply chains involving many players and subject to multiple, extensive process design changes have complex flow management that have failed miserably. The conceptual models of construction management and the tools it utilizes (work breakdown structure, critical path method, and earned value management) have been criticized to be deficient in handling the present unique challenges of projects. As a result, the industry is characterized by a number of wastes including: overproduction, lead time, transportation, inappropriate processing, inventories, unnecessary movements, rework and making do wastes. There is therefore the need for practical and robust models and techniques that will help projects teams deal with the issues of wastes in projects. This can only be achieved through the adoption of lean production systems in the construction industry, thus, Lean Construction (LC). In this paper, LC approach and the importance for its implementation has been discussed as the robust approach for project management. -
Introduction to Construction Management Introduction
A ROUTLEDGE FREEBOOK Introduction to Construction Management Introduction 01: Construction Economics By Danny Myers Chapter: An Introduction to the Basic Concepts 02: Management of Construction Projects By John E. Schaufelberger, Len Holm Chapter: Introduction 03: Quantity Surveyor's Pocket Book By Duncan Cartlidge Chapter: The quantity surveyor and the construction industry 04: Estimating and Tendering for Construction By Martin Brook Chapter: Introduction 05: Building Measurement By Andrew D. Packer Chapter: Introduction 06: Total Construction Management By John S. Oakland, Marton Marosszeky Chapter: Understanding lean construction You can discover more of our key construction property titles on our website here: https:/ / www.routledge.com/ products/ SCBU20 Introduction Introduction to Construction Management is a FreeBook brought to you by Routledge, containing a collection of selected chapters from six key titles published in the last twelve months. The chapters presented here cover introductions to key topics like project management, economics, measurement and tendering, all essential for aspiring construction students and professionals currently studying for their related qualifications. We have a wide range of textbooks, references, monographs, and practical guidebooks to serve the needs of students, instructors, and established professionals and the contents here represents only a very small sample of that offering. Courses in construction, quantity surveying and building surveying will find resources that will be useful as required texts and supplementary reading. Here is a selection of representative chapters from just six of our recent publications to give you an idea of the quality and variety of subject matter addressed in our portfolio. So, please enjoy this sample from available and new textbooks, and consider recommending them to your students, colleagues, and library. -
Is Building Construction Approaching the Threshold of Becoming
Is Building Construction Approaching the Threshold of Becoming Unsustainable? A System Theoretic Exploration towards a Post- Forrester Model for Taming Unsustainable Exponentialoids A Dissertation Presented to The Academic Faculty By José L. Fernández-Solís In partial fulfilment of the Requirements for a Degree Doctor in Philosophy in the College of Architecture Georgia Institute of Technology December 2006 © 2006 Copyright by José L. Fernández-Solís i Is Building Construction Approaching the Threshold of Becoming Unsustainable? A System Theoretic Exploration towards a Post- Forrester Model for Taming Unsustainable Exponentialoids Approved by: Dr. Linda Thomas Mobley Professor Godfried Augenbroe College of Architecture College of Architecture Georgia Institute of Technology Georgia Institute of Technology Dr. Thomas L. Galloway Dr. Lauri Koskela College of Architecture Built and Human Environment Georgia Institute of Technology University of Salford, UK Mr. Brian Bowen Executive in Residence College of Architecture Georgia Institute of Technology Date Approved: ii Human beings become builders by building.” Aristotle, “Nicomachean Ethics,” 2.1.1103a35 Technology is a neutral means or human activity – a kind of truth revealing – that sets up and challenges nature to yield (release and transform) a kind of energy that can, at will, be independently stored, and transmitted (distributed).” “The essence of modern technology starts human beings upon the way of THAT revealing through which reality everywhere, more or less distinctly, becomes resource.” Adapted from M. Heidegger, 1954, “The Question Concerning Technology and Other Essays,” “The bet or wager of the century is not some unqualified conquest of nature but the replacement of the natural milieu with the technical milieu. The modern gamble is whether this new milieu in contrast with the natural milieu will be better or even possible.” J. -
Lean Construction for Productivity Enhancement and Waste Minimization‖
International Journal of Engineering and Applied Sciences (IJEAS) ISSN: 2394-3661, Volume-2, Issue-11, November 2015 ―Advances in Construction: Lean Construction for Productivity enhancement and waste minimization‖ Aakanksha Ingle, Prof Ashish P Waghmare system, etc., in converting inputs into useful outputs. Abstract- The objective of this paper is to highlight the cost Productivity is the measure of utilization of input by the and benefits of the potential contribution of lean construction system. What is Lean construction? It is a collective term to the achievement of productivity enhancement and waste for changes in the design and delivery process. Among the minimization in construction industry. It is critical review of various construction processes, it is the one which can best literature. Researcher has used exploratory method for support a focus on sustainability through ―increasing value investigating the benefits of lean construction system by while reducing waste.‖ exploring, and understating the available literature and some case studies. There is need for waste minimization and Since the inception of Lean Manufacturing Concepts as far enhancement of productivity in construction activity. back as the 1900s, lean construction has been discussed and Productivity is critical determinant of cost efficiency. The debated by many researchers worldwide. According to conventional system of construction is not sustainable. In one Abdullah et al. (2009), Lean Construction is a concept that of the research it is estimated that current system of needs to be introduced within the construction industry, construction had around 50% of non value added efforts or specifically to increase the sector‘s productivity level waste. The meaning of lean construction is that it is the through the elimination of activities and actions deemed to application of lean thinking to the construction industry. -
An Assessment of Lean Design Management Practices in Construction Projects
sustainability Article An Assessment of Lean Design Management Practices in Construction Projects Rodrigo F. Herrera 1,* , Claudio Mourgues 2, Luis Fernando Alarcón 2 and Eugenio Pellicer 3 1 School of Civil Engineering, Pontificia Universidad Católica de Valparaíso, Pontificia Universidad Católica de Chile & Universitat Politècnica de València, Av. Brasil 2147, Valparaíso 2340000, Chile 2 School of Engineering, Pontificia Universidad Católica de Chile, Vicuña Mackenna 4860, Casilla 306 Correo 22 Santiago, Chile; [email protected] (C.M.); [email protected] (L.F.A.) 3 School of Civil Engineering, Universitat Politècnica de València, Camino de Vera s/n, 46022 Valencia, Spain; [email protected] * Correspondence: [email protected]; Tel.: +56-32-227-3882 Received: 30 October 2019; Accepted: 16 December 2019; Published: 18 December 2019 Abstract: Evidence exists for the application of lean management practices in the design process. However, there is no systematic review of this type of practice that links the design management practices to the lean construction principles. There is no tool to assess the level of use of lean design management practices in construction projects either. Therefore, this paper aims to assess the lean management practices that are performed at the design phase of construction projects. The research was divided into a literature review of design management practices; a validation of lean design management practices with a practice–principle relationship, based on an expert survey; the devolvement of a tool (questionnaire) to evaluate the lean design management practices; and an assessment in 64 construction projects (coherence, reliability, correlation, and descriptive analysis). It is concluded that evidence exists for the implementation of 19 lean design management practices.