Executive Summary English
Total Page:16
File Type:pdf, Size:1020Kb
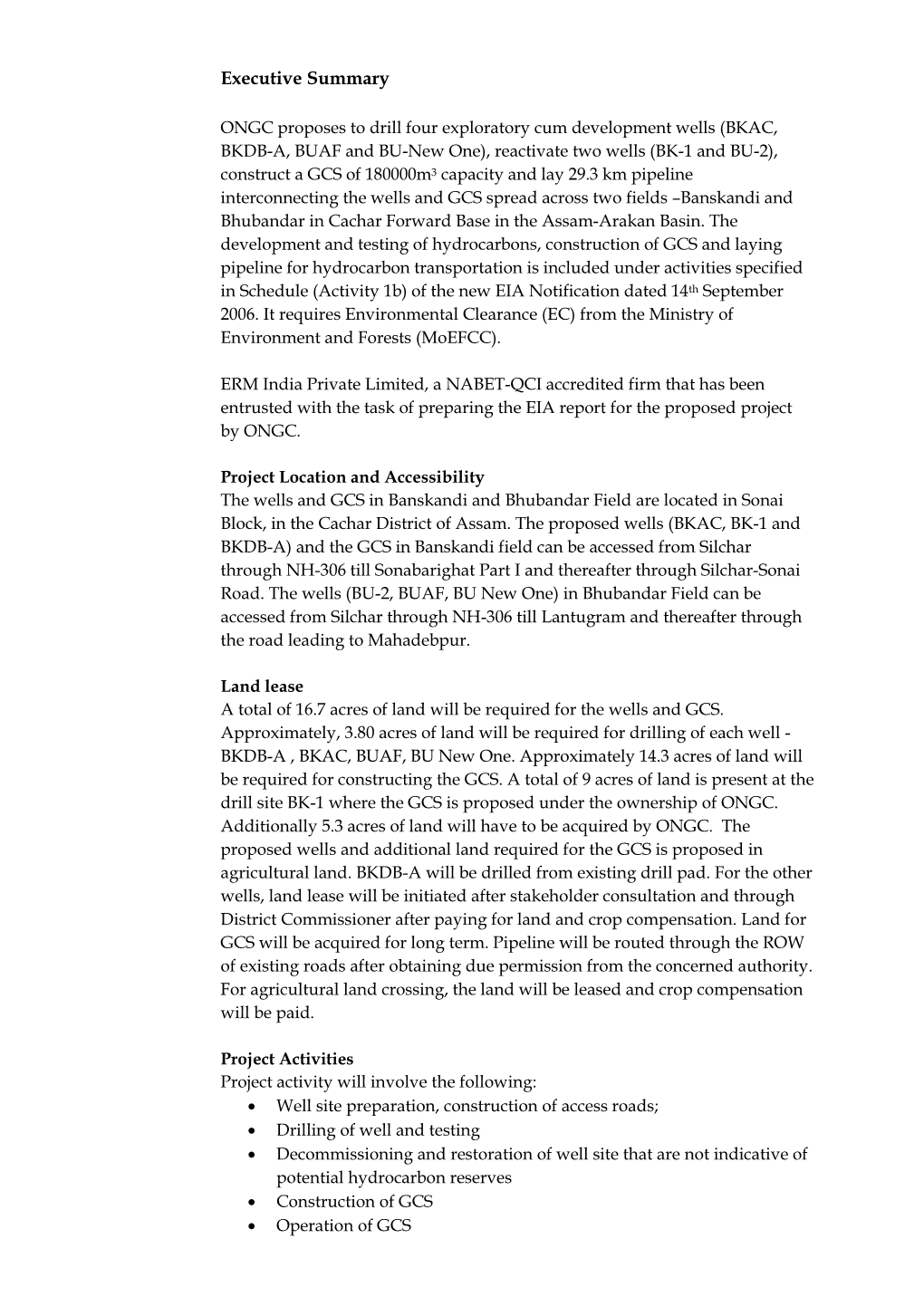
Load more
Recommended publications
-
Office of the District & Sessions Judge
OFFICE OF THE DISTRICT & SESSIONS JUDGE List of candidates for the first phase of preliminary Screening (Oral ) Test for ensuing selection of Grade - IV staff to be held w.e.f. 07.07.2019 to 21.07.2019 Date of Screening (Oral ) Test Roll No of candidates Remarks 07.07.2019 0001 to 0600 Except rejected candidates 10.07.2019 0601 to 0760 Except rejected candidates 11.07.2019 0761 to 0920 Except rejected candidates 12.07.2019 0921 to 1080 Except rejected candidates 14.07.2019 1081 to 1880 Except rejected candidates 16.07.2019 1881 to 2040 Except rejected candidates 17.07.2019 2041 to 2200 Except rejected candidates 18.07.2019 2201 to 2360 Except rejected candidates 19.07.2019 2361 to 2520 Except rejected candidates 21.07.2019 2521 to 3320 Except rejected candidates Date of ROLL Reporting Name of Applicant Father name & Address D.O.B Caste Sex Screening NO Time test(oral) LT. KUNJA RAM DAS NATUNPATTY, 0001 SURAJIT DAS HOUSE NO. 25 P.O-SILCHAR DIST- 10/31/83 GENERAL MALE 7th July 2019 09:00 A.M CACHAR PIN-788001 LATE PROBASH RANJAN BARMAN , GUNOMOYEE ROAD BY LANE 1 , 0002 PREMJIT BARMAN 12/31/87 ST ( P ) MALE 7th July 2019 09:00 A.M P.O. - TARAPUR , DIST -CACHAR , PIN – 788003 AOULAD HUSSAIN BARBHUIYA , ABDUL ALIM VILL – DUDPATIL , P.O. - 0003 02/28/97 GENERAL MALE 7th July 2019 09:00 A.M BARBHUIYA MASUGHAT , DIST – CACHAR , PIN – 788008 SANJIT ROY, ARUN CHANDRA 0004 SUMU ROY ROAD, HOSPITAL ROAD, HOUSE NO 12/07/93 GENERAL MALE 7th July 2019 09:00 A.M 31 DIST-CACHAR , PIN-788005 0005 INELIGIBLE LT. -
SUHRID Scheme Beneficiary List
LIST OF BENEFICIARIES FOR FINANCIAL ASSISTANCE IN RESPECT OF EDUCATIONAL BENEFIT UNDER BORKHOLA MLA AREA DEVELOPMENT FUND (SUHRID) FOR THE YEAR 2017-18 Sl. NAME OF NAME OF NAME OF NAME OF NAME OF NAME OF G.P. NAME OF BANK A/C NO. IFSC CODE AMOUNT No. DISTRICT LAC BLOCK VILLAGE/TOWN BENEFICIARIES CHOTO DUDHPATIL G.P. SHASTRINAGAR SURANJIT DAS Allahabad Bank, Dudpatil 59044740662 ALLA0211328 5000 1 Branch --DO-- SHASTRINAGAR AMIT DEB Allahabad Bank, Dudpatil 50277775606 ALLA0211328 5000 2 Branch 3 HATICHERA G.P. SHIRISTAL POMPI DAS UBI, Doloo Branch 1099010379663 UTBI0DLUG70 5000 4 --DO--. PUTICHERRA HRIDOY DAS SBI, Leburbond 35934533744 5000 5 --DO-- GUTIBARI GOBINDA DAS SBI, Rongpur Branch 20347072449 SBIN0017401 5000 CHOTO DUDHPATIL G.P. SHASTRINAGAR SARASWATI BALA DAS Allahabad Bank, Dudpatil 50186434513 ALLA0211328 5000 6 Branch 7 --DO-- SHASTRINAGAR RUMI DEY CBI, Silchar Branch. 3574426885 CBIN0281352 5000 --DO-- NETAJI NAGAR SHIPRA DAS Allahabad Bank, Dudpatil ALLA0211328 5000 BORKHOLA 50212503025 8 Branch DEV. BLOCK 9 MASUGHAT G.P. MASUGHAT JAYASHEE SINHA CBI, Hospital Road. 3568996172 CBIN0283235 5000 CHOTO DUDHPATIL G.P. CHOTODUDHPATIL RINKI RANI DAS Allahabad Bank, Dudpatil 50424899480 ALLA0211328 5000 10 Branch --DO-- NATHPARA CHIRANJIT DEBNATH Allahabad Bank, Dudpatil 5017502953 ALLA0211328 5000 11 CHOTODUDHPATIL Branch CACHAR BORKHOLA 12 BADARPUR MASIMPUR G.P. MASIMPUR PT-II SIBAM GOALA UBI, Shib bari Road. 1709010176996 UTBI0SIIH74 5000 CHOTO DUDHPATIL G.P. NETAJINAGAR SUMAN DAS Allahabad Bank, Dudpatil 59044699978 ALLA0211328 5000 13 Branch --DO-- SHASTRINAGAR PINKI DEY Allahabad Bank, Dudpatil 50377885673 ALLA0211328 5000 14 Branch --DO-- SHASTRINAGAR SUSHMITA DAS Allahabad Bank, Dudpatil 50436632411 ALLA0211328 5000 15 Branch KUMARPARA NIZJOYNAGAR KUMARPARA LITON DAS Bandhan Bank, 50160009786887 BDBL0001528 5000 16 SALCHAPRA G.P. -
Twenty Fifth Annual Report Annual Report 2017-18
TWENTY FFIFTHIFTH ANNUAL REPORT 20172017----18181818 ASSAM UNIVERSITY Silchar Accredited by NAAC with B grade with a CGPS OF 2.92 TWENTY-FIFTH ANNUAL REPORT 2017-18 REPORT 2017-18 ANNUAL TWENTY-FIFTH ANNUAL REPORT 2017-18 PUBLISHED BY INTERNAL QUALITY ASSURANCE CELL, ASSAM UNIVERSITY, SILCHAR Annual Report 2017-18 ASSAM UNIVERSITY th 25 ANNUAL REPORT (2017-18) Report on the working of the University st st (1 April, 2017 to 31 March, 2018) Assam University Silchar – 788011 www.aus.ac.in Compiled and Edited by: Internal Quality Assurance Cell Assam University, Silchar | i Annual Report 2017-18 STATUTORY POSITIONS OF THE UNIVERSITY (As on 31.3.2018) Visitor : Shri Pranab Mukherjee His Excellency President of India Chief Rector : Shri Jagdish Mukhi His Excellency Governor of Assam Chancellor : Shri Gulzar Eminent Lyricist and Poet Vice-Chancellor : Prof Dilip Chandra Nath Deans of Schools: (As on 31.3.2018) Prof. G.P. Pandey : Abanindranath Tagore School of Creative Arts & Communication Studies Prof. Asoke Kr. Sen : Albert Einstein School of Physical Sciences Prof. Nangendra Pandey : Aryabhatta School of Earth Sciences Prof. Geetika Bagchi : Ashutosh Mukhopadhyay School of Education Prof. Sumanush Dutta : Deshabandhu Chittaranjan School of Legal Studies Prof. Dulal Chandra Roy : E. P Odum School of Environmental Sciences Prof. Supriyo Chakraborty : Hargobind Khurana School of Life Sciences Prof. Debasish Bhattacharjee : Jadunath Sarkar School of Social Sciences Prof. Apurbananda Mazumdar : Jawarharlal Nehru School of Management Prof. Niranjan Roy : Mahatma Gandhi School of Economics and Commerce Prof. W. Raghumani Singh : Rabindranath Tagore School of Indian Languages and Cultural Studies Prof. Subhra Nag : Sarvepalli Radhakrishnan School of Philosophical Studies Prof. -
Executive Summary English
Environmental Impact Assessment Report for the proposed Exploration, Development and production in 5 onshore PML blocks in Assam Arakan Fold Belt (AAFB), Assam & Assam Arakan (A & AA) Basin, Cachar District and Karimganj District, Assam Executive Summary 1.0 INTRODUCTION Oil & Natural Gas Corporation Limited (ONGC) is the largest crude oil and natural gas producer in India, contributing around seventy five percent to Indian domestic production. Crude oil is the raw material used by downstream companies like IOC, BPCL, and HPCL (subsidiary of ONGC) to produce petroleum products like Petrol, Diesel, Kerosene, Naphtha, and Cooking Gas-LPG. ONGC has proposed exploration, development and production activities in the envisaged prospects for hydrocarbon falling in 5 PML blocks identified through seismic surveys. The PML blocks lie within the “Assam Arakan Fold Belt” (AAFB) falls in the Assam-Arakan Basin, Cachar and Karimganj Districts, Assam. The area covered in PML blocks identified as project area is presented below: Block Name Area (Sq. Average Depth (meter) Km) Banskandi PML 15.0 2500-4000 During exploration stage Bhubandar PML 6.0 & 2,500 m for development wells. Sector VC PML 497.0 Adamtila PML 4.0 Adamtila Extension PML 148.0 1.1 Project Location Study area of the project is divided into two separate units based on the relative distance between and nearness of PML blocks as well as nearest IMD meteorological stations. While, Banskandi PML, Bhubandar PML and Sector VC PML are covered in one unit (Study Area-I) (covered in Cachar District); Adamtila and Adamtila Extension PML are covered in another unit (Study Area-II) (covered in Karimganj District). -
World Bank Document
Public Disclosure Authorized Public Disclosure Authorized Public Disclosure Authorized Public Disclosure Authorized COMPILED FOR ALL BYPCU LINE DEPARTMENTS w.e.f. March 15, 2012 till end of2012 w.e.f.15, Project March Final (Version-3) Final IDA Cr. 5062IDA Cr. 31-Jan-2015 Final Assam Agricultural Competitiveness Project (AACP): Additional Financing IDA CR 5062 PROCUREMENT PLAN (10 December 2013) I. General 1 Project information: a.Country: India b. Borrower: Government of India for Government of Assam. c. Project Name: Assam Agricultural Competitiveness Project (AACP)- Additional Financing d. Credit No.: IDA CR 4013.5062 e. Project Implementing Agencies: AACP is a multisectoral project. The project is monitored & coordinated by the State level Project Coordination Unit (PCU) and implemented by 8-line departments/ agencies. These are departments of Agriculture, Animal Husbandry & Veterinary, Dairy Development, Fisheries, Public Works, Forest and Sericulture with their Project Implementation Units (PIU) at Guwahati and Agencies like Assam Agriculture University with its HQ at Jorhat, Assam Livestock Development Agency, and also by 11 ATMA Societies in the districts of Kamrup, Nagaon, Barpeta, Sonitpur, Jorhat , Hailakandi , Dhubri, Dibrugarh, Dhemaji, Nalbari and Karbi Anglong . 2 Bank’s approval Date of the procurement Plan: [Original: 27th Jan. 2012.; Revision 1: proposed now] 3 Date of General Procurement Notice: June 12, 2004 (Same as for the Original Project) 4 Period covered by this procurement plan: From March 15, 2012 till end of the Project 5 Goods, Works & non-consulting services shall be procured in accordance with the provisions in the "Guidelines for Procurement under IBRD Loans and IDA Credits" published by the Bank in January 2011 6 Services of Consultants shall be procured in accordance with the provisions in the "Guidelines for the Use of Consultants by World Bank Borrowers and by the World Bank as Executing Agency " published by the Bank in January 2011. -
Office of the District & Sessions Judge, Cachar
OFFICE OF THE DISTRICT & SESSIONS JUDGE, CACHAR, SILCHAR Memo No.JCD.III/GR.IV/2020/ 4082 Dated:- 21-11-2020 The following candidates are found eligible for the Screening Test(Oral) in connection with recruitment of 07 (seven) numbers of Office Peon of this establishment. The date of the Screening Test(Oral) will be notified in the official website of this establishment. District & Sessions Judge, Cachar, Silchar Roll No. Name Sex Father Name/Guardian Name Address Date of Birth Qualification Caste C/O. Lt. Dhiraj Purkayastha, Ward No. 2, Malugram, 0001 DHRUBA PURKAYASTHA MALE LATE DHIRAJ PURKAYASTHA Shibbari Road, Near E & D Bandh, Silchar, Cachar, Assam - 06.06.1986 H.S.L.C Gen 788002 0002 DIPANKAR DAS MALE DILIP KUMAR DAS Vill & P.O- Masughat, Dist- Cachar, Assam 31.08.1988 H.S.L.C S.C 0003 JIKU DEB FEMALE DILIP DAS Mabadeb Tilla, Haflong, District- N.C. Hills 28.01.1987 H.S Gen 0004 SIDDHARTHA KAR MALE PIJUSH KAR 196 C, Alok Bhawan, Hospital Road, Silchar, Cachar, Assam 18.06.1990 H.S. Gen 0005 UTTAM NUNIA MALE RAGHUNATH NUNIA Vill- Kashipur Pt-I, P.O Kashipur, P.S- Silchar-788009 23.09.2000 H.S Gen Vill- Rongpur Pt-VI,P.S- Lala, P.O- Rongpur south, Dist- 0006 ARSHADUR RAHMAN MAZUMDER MALE FAKHAR UDDIN MAZUMDER 11.02.1999 H.S Gen Hailakandi Vill.- Gobindakupa, P.O. Digorkhal, P.S. Katigorah, PIN - 0007 MOUSMITA PAUL FEMALE RAMENDRA MOHAN PAUL 20.04.1994 H.S. Gen 788815, Dist. Cachar, Assam Roll No. Name Sex Father Name/Guardian Name Address Date of Birth Qualification Caste Vill- Rongpur Pt-VI,P.S- Lala, P.O- Rongpur south, Dist- 0008 SHAIDUR RAHMAN MAZUMDER MALE FAKHAR UDDIN MAZUMDER 06.10.2000 H.S Gen Hailakandi 0009 SHIBOM SANKAR MALAKAR MALE SHIBU MALAKAR Vill- Nayabari, P.O- Tillabazar, Dist- Karimganj, Pin-788709 19.08.1994 H.S S.C Vill.- Jarailtala, P.O. -
District Flood Contingency Plan Cachar Year:2020-21
DISTRICT FLOOD CONTINGENCY PLAN CACHAR YEAR:2020-21 DISTRICT ADMINISTRATION CACHAR Prepared by- DDMA, Cachar 1 INDEX SL. NO. CONTENTS PAGE NO. 1 Cachar-District Profile 3-4 2 Silchar Sadar Revenue Circle, Silchar 5-9 3 Udharbond Revenue Circle, Udharbond 10-14 4 Sonai Revenue Circle 15-23 5 Katigorah Revenue Circle, Katigorah 24-32 6 Lakhipur Revenue Circle 33-37 7 Inland Water Transport Division 38-40 8 Fishery Department, Cachar 41-42 9 Health & Family Welfare Department, Cachar 43-51 10 Irrigation Department, Cachar 52-55 11 Elementary Education, SSA, Cachar 56-59 12 Silchar Development Authority 60-61 13 PWD Department (Silchar Building Division) 62-78 14 PWD (NH Division) 79-83 15 Soil Conservation Department 84-95 16 Agricultural Department 96-102 17 P.H.E. Div.-I, Silchar 103-104 18 P.H.E. Div.-II, Silchar 105-110 19 A.H. & Vety. Department, Cachar 111-119 20 Water Resources Department, Mechanical Division 120-121 21 District Social Welfare Department 122-129 22 Food & Civil Supply 130-131 23 Annexure-I: Contact Details 132-138 2 CACHAR DISTRICT PROFILE BACKGROUND : Cachar district is located on the southern part of the State of Assam in the north-east of India. The peculiar position of Cachar district which is land locked and is dependent on surface communication through Meghalaya for its connectivity with rest of the country frequently faces the flood which snaps the surface communication. Cachar district has prepared Action Plan to face any situation in the event of flood which mostly becomes a seasonal phenomenon or any other calamities in this district. -
City Disaster Management Plan Silchar
CITY DISASTER MANAGEMENT PLAN SILCHAR OFFICE OF THE DEPUTY COMMISSIONER, CACHAR ASSAM (Updated on 12th October’2012) Part - I District Disaster Management Authority, Cachar, Silchar. Government of Assam. A. SILCHAR CITY DISASTER MANAGEMENT PLAN The Silchar Town of cachar district is vulnerable to the natural disaster like floods, cyclones, earth- quakes, Hail storm etc.The Silchar city is the gate way of three districts of Barak valley as well as Tripura, Mizoram and Manipur. Considering the high Social and economic importance of Silchar town it is evident that any disaster here will have implications not only on the District and State but on the region as well. Hence to improve upon our capabilities with respect to Mitigation, Preparedness, Response and Recovery of any disaster situation it is important to have a City Disaster Management Plan (CDMP) in place. The TDMP is so planned that it can be pressed into action in case of any emergency, be it – natural or human induced. Since this City Disaster Management Plan (CDMP) is concerned with the many hazards to which the district and the citizens may be exposed before, during and after a disaster occurs, responsible authorities operate in accordance with the five phases of disaster management: 1. Prevention – Preventive actions are taken to avoid an incident or to intervene to stop an incident from occurring. Such actions are primarily applicable to terrorist incidents. They may include the application of intelligence and other information to a range of activities that may include deterrence, heightened security for potential targets, investigations to determine the nature and source of the threat, public health surveillance and testing, disrupting illegal activities etc. -
Office of the District & Sessions Judge,Cachar
OFFICE OF THE DISTRICT & SESSIONS JUDGE,CACHAR, SILCHAR Memo No.JCD.III/GR.IV/2020/4083 Dated: 21.11.2020 The following candidates are found ineligible for the reason shown against their respective names in connection with recruitment of 07 (seven) numbers of Office Peon of this establishment. District & Sessions Judge, Cachar, Silchar Sl. No Name Sex Father Name/Guardian Name Address Date of Birth Qualification Caste Cause of rejected application 1. Documents not Self Attested Vill.-Kukubari, P.O. Chincoorie, Dist.-Dist. 001 Raju Rabi Das Male Lt. Dubraj Rabidas 31.10.1993 H.S.L.C SC 2. One Copy Photograph submitted. Cachar, Assam 3. no phone number. Sreema Road, Tikorbasti, Silchar-7, Dist.- 1. no standard form. 002 Taniya Chakroborty Female Kalyan Chakroborty 20.08.2002 H.S.L.C General Cachar, Assam 2. Under Age Vill.-Saibag, P.O.-Lathigram, P.S- 003 Bijayendra Shekhar Chakraborty Male Bijon Behari Chakraborty Udharbond, Dist.- Cachar, Assam, PIN- 16.08.1992 H.S.L.C General 1. BCA qualified as per exchange card submitted 788030 Vill.-Talkargrant,(Chatirbond) P.O.-Digor 004 Mintu Nath Male Himendu Nath 15.09.1996 H.S.L.C OBC 1. Documents not Self Attested Khal, Dist.-Cachar, Assam Vill.-Rongpur Part-IV, P.O. Rongpur, Dist- 1. Documents not self attested 005 Ajit Dey Male Haripada Dey 09.08.1994 HS. OBC Cachar, Assam, PIN-788009 2. Mobile No. not furnished B.C. Gupta Road, Malugram, Silchar, PIN- 006 Priya Singh Female Surendar Singh 31.05.2001 HS. OBC 1. Documents not self attested 788002, Dist.Cachar, Assam Bagha Jatin Lane, Chengkuri Road, Silchar, 007 Swarnakshi Nath Female Manik Chandra Nath 17.02.1989 Bachelor of Visual Arts OBC 1. -
DETAILS of the Phd SCHOLARS (Under 2009 and 2017 Regulations)
ASSAM UNIVERSITY, SILCHAR DETAILS OF THE PhD SCHOLARS (Under 2009 and 2017 Regulations) Dept: Agricultural Engineering Sl. School Department Name & Address of Name of the Mode of Registration / Research Topic Tentative date Availing Funding Agency No. the PhD Scholar Supervisor & pursuing Enrolment of completion of Fellowship & of Fellowship with e-mail ID and Co-Supervisor PhD (Full Number & PhD Course Name (Yes/No) Contact No. & (if any) Time/Part Date of Adhaar No/ Time Registration / Voter Card No./ Admission Driving Licence No./Passport No. 1. Triguna Sen Agricultural Rishi Kumar, Dr. Laxmi Part Time Ph.D./2269/13 Microbial removal of heavy 2019 No - School of Engineering e-mail Narayan Sethi Dt: 26.02.13 metals from aquatic Technology ID:rishisingh131@ Dr. Sudipto environment using gmail.com, Phone Saqrkar bioreactors. No.: 9717346600 Aadhaar No.- 583732874806 2. Triguna Sen Agricultural Kamakshi Prasad Dr. Laxmi Part Time Ph.D./2362/13 Integrating water 2019 No - School of Engineering Padhy, S/o: Sri Narayan Sethi Dt: 12.09.13 harvesting and hydraulic Technology Raghunath Prasad ram fed micro-irrigation Padhy, AT/P O: system for crop planning in Medical Bank hilly terrain Colony-II, Berhampur, Distt.: Ganjam, Odisha, PIN: 760004, e- mail ID: kamakshipadhy@y ahoo.com, kppadhy77@gmail. com, Phone No.: 09438055369 3. Triguna Sen Agricultural Gajendra Prasad, Dr. Sudipto Part Time PhD/SOT/10/1 Design and development of No - School of Engineering Department of Sarkar 6 solar biomass hybrid drying Technology Agricultural Dr. Laxmi Dtd. system for fruits and Engineering, Narayan Sethi 13/04/2016 vegetables Triguna Sen School of Technology, Assam University, Silchar-788011, e-mail ID: iitkgp.gajendra@g mail.com, Phone No.: 8811083834 Adhaar No.- 848895343201, 7488218615 4. -
High Schools @ Cachar.Xlsx
Sl Educational Name of the school Location & Address Name of the Head of the Institution Contact No. No. Block 1 A.C.MEMORIAL HIGH SCHOOL P.O. Joyngar, Pin - 788025. SALCHAPRA SURAJIT NATH 9577552301 2 ADHARCHAND H. S. SCHOOL AMBICAPATTY,SILCHAR,ASSAM, PIN-788004 SILCHAR PRASANTA KUMAR NATH 9854618186 3 AMBIKACHARAN HIGH SCHOOL P.O. Katirail, Pin - 788804. KATIGORAH HIMANGSHU SEKHAR CHAKRAVARTY 7635803972 VILL.-KUMARPARA, P.O.-ARUNACHAL, DIST.-CACHAR, 4 ARUNACHAL GIRLS HIGH SCHOOL SALCHAPRA ARCHANA DAS 9401048211 ASSAM. PIN-788025 5 B.N.M.P. H.S SCHOOL P.O. Dholai, Pin - 788018 NARSINGPUR IS, CDC, SILCHAR (i/c) 9707931424 6 BADRI PAR HINDI HIGH SCHOOL P.O. Badripar, Pin- 788009. RAJA BAZAR HARILAL YADAB 8638978238 7 BAGPUR HIGH SCHOOL P.O. Bagpur, Pin - 788101. LAKHIPUR ABDUL SUKKUR LASKAR 7002929599 8 BALARAM HIGH SCHOOL P.O. Pallorbond, Pin - 788101 LAKHIPUR Y. CHURAMONI SINGHA 9435708707 9 BALESWAR HIGHER SECONDARY SCHOOL P.O. Jalalpur, Pin - 788816. KATIGORAH MOFUR UDDIN 9854112353 10 BAM BIDYAPITH HIGH SCHOOL P.O. Bhaga Bazar, Pin - 788120 NARSINGPUR SAMSUL HAQUE BARBHUIYA 9435373553 11 BAM SENIOR MADRASSA NARSINGPURAHMED HUSSAIN MAZUMDER 9707092584 12 BAM NABA KUMAR MEMORIAL HIGH SCHOOL P.O. Dholai Bazar - 788018 NARSINGPUR BANDANA DAS 9957625711 13 BANSKANDI HIGH SCHOOL RANIPUR P.O. Ranipur, Pin - 788101. RAJA BAZAR BRINDA SINGH 9101832236 14 BANSKANDI NENA MEAH HIGHER SECONDARY SCHOOL P.O. Banskandi, Pin - 788101. LAKHIPUR NAZRUL ISLAM BARBHUIYA 9101916074 15 BANTARAPUR HIGH SCHOOL P.O. Sundari, Pin - 788099. SONAI M. GUNABATI SINGHA 9435927210 16 BARKHOLA MANIPURI HIGH SCHOOL P.O. Borkhola, Pin -788110. SALCHAPRA RANJIT KUMAR SINGHA 9957504762 VILL GANIRGRAM-2,P.O. -
Performance Grant 2017-18 GP Wise Allocation
Statement for distribution of Performance Grant under 14th Finance Commission for the year 2017-2018 to Gaon Panchayats Sno District Block Gaon Panchayt Amount (Rs) 1 BARPETA BAJALI BAGHMARA 590370 2 BARPETA BAJALI BAMUNKUCHI 696029 3 BARPETA BAJALI BANDHA SIDHANI 708706 4 BARPETA BAJALI BARBANG 652685 5 BARPETA BAJALI DUBI 624340 6 BARPETA BAJALI MARIPUR ANANDAPUR 688039 7 BARPETA BAJALI NITYANANDA PANBARI 611172 8 BARPETA BAJALI PATACHARKUCHI 536849 9 BARPETA BAJALI SADERI 717321 10 BARPETA BAJALI SATHISAMUKA MAJARKHAT 530242 11 BARPETA BAJALI TIHU-DEKHATA 616796 12 BARPETA BARPETA BHELLA 964885 13 BARPETA BARPETA NAGAON 731115 14 BARPETA BARPETA RADHAKUCHI 855477 15 BARPETA BARPETA SUNDARIDIA 563275 16 BARPETA BARPETA UTTAR PUB PAKA 721874 17 BARPETA BHABANIPUR BAHMURA 1156160 18 BARPETA BHABANIPUR CHAULIABARI 771334 19 BARPETA BHABANIPUR DABALIAPARA 1011086 20 BARPETA BHABANIPUR GALIA 809142 21 BARPETA BHABANIPUR GERUAPARA 830033 22 BARPETA BHABANIPUR HAZIPARA 1191157 23 BARPETA BHABANIPUR KALBARI 648757 24 BARPETA BHABANIPUR MAJGAON 829854 25 BARPETA BHABANIPUR SARUPETA 694467 26 BARPETA BHABANIPUR SINGIMARI 687949 27 BARPETA BHABANIPUR SUKMANATH 827935 28 BARPETA CHENGA BAHARI 835211 29 BARPETA CHENGA BATGAON 791510 30 BARPETA CHENGA DAKHIN GODHANI 868109 31 BARPETA CHENGA HARIPUR 929264 32 BARPETA CHENGA NIZ CHENGA 587112 33 BARPETA GOBARDHANA BAGARIGURI 901365 34 BARPETA GOMAPHULBARI AZAD 996534 35 BARPETA GOMAPHULBARI BARBILA 712143 36 BARPETA GOMAPHULBARI GUMA 814142 37 BARPETA GOMAPHULBARI PAZARBHANGA 764459 38 BARPETA MANDIA