Compositions Providing Frost Appearance for Printing on Glass Or Ceramic Substrates and Methods for the Use Thereof
Total Page:16
File Type:pdf, Size:1020Kb
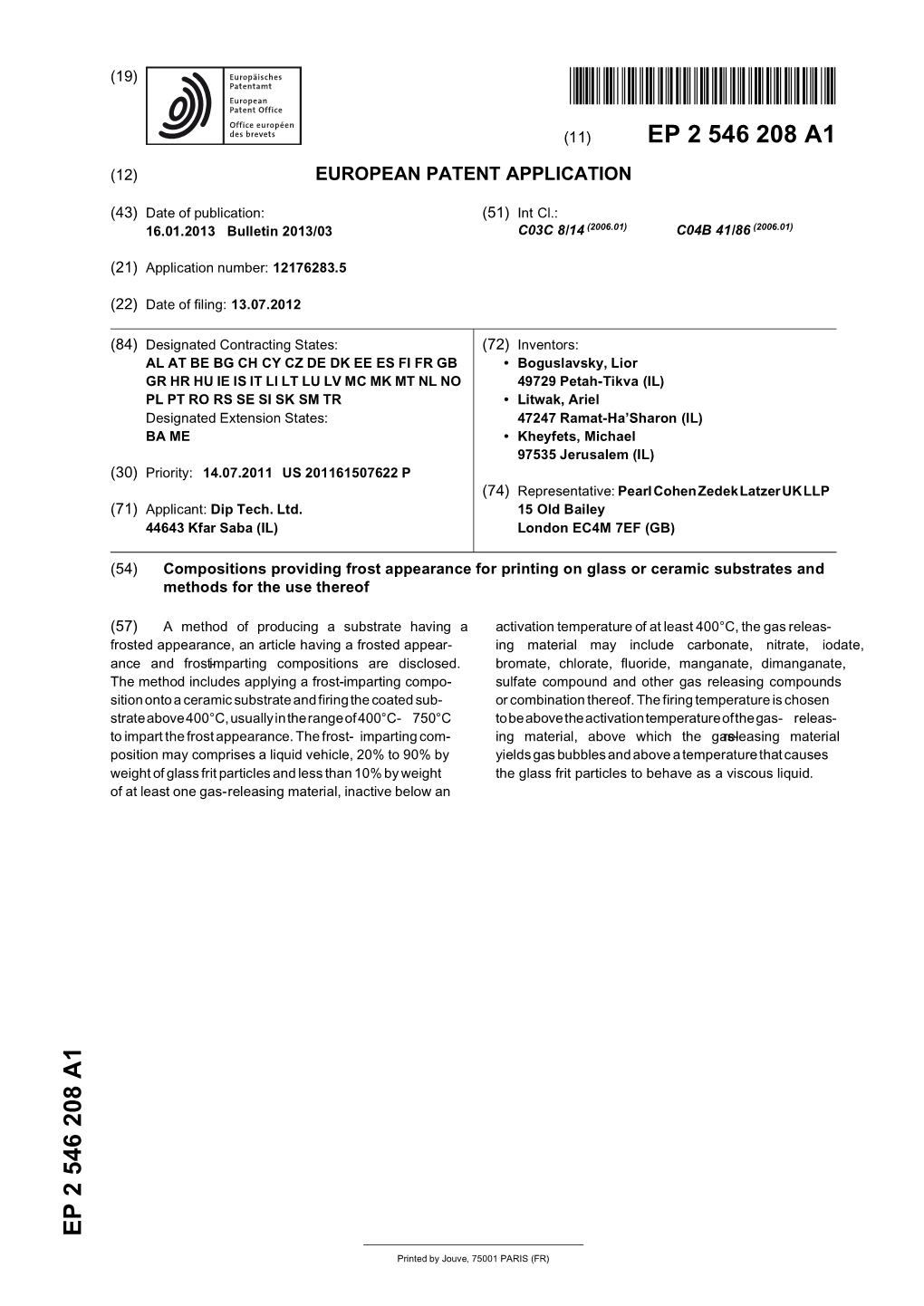
Load more
Recommended publications
-
Mineral Processing
Mineral Processing Foundations of theory and practice of minerallurgy 1st English edition JAN DRZYMALA, C. Eng., Ph.D., D.Sc. Member of the Polish Mineral Processing Society Wroclaw University of Technology 2007 Translation: J. Drzymala, A. Swatek Reviewer: A. Luszczkiewicz Published as supplied by the author ©Copyright by Jan Drzymala, Wroclaw 2007 Computer typesetting: Danuta Szyszka Cover design: Danuta Szyszka Cover photo: Sebastian Bożek Oficyna Wydawnicza Politechniki Wrocławskiej Wybrzeze Wyspianskiego 27 50-370 Wroclaw Any part of this publication can be used in any form by any means provided that the usage is acknowledged by the citation: Drzymala, J., Mineral Processing, Foundations of theory and practice of minerallurgy, Oficyna Wydawnicza PWr., 2007, www.ig.pwr.wroc.pl/minproc ISBN 978-83-7493-362-9 Contents Introduction ....................................................................................................................9 Part I Introduction to mineral processing .....................................................................13 1. From the Big Bang to mineral processing................................................................14 1.1. The formation of matter ...................................................................................14 1.2. Elementary particles.........................................................................................16 1.3. Molecules .........................................................................................................18 1.4. Solids................................................................................................................19 -
Supergene Mineralogy and Processes in the San Xavier Mine Area, Pima County, Arizona
Supergene mineralogy and processes in the San Xavier mine area, Pima County, Arizona Item Type text; Thesis-Reproduction (electronic) Authors Arnold, Leavitt Clark, 1940- Publisher The University of Arizona. Rights Copyright © is held by the author. Digital access to this material is made possible by the University Libraries, University of Arizona. Further transmission, reproduction or presentation (such as public display or performance) of protected items is prohibited except with permission of the author. Download date 28/09/2021 18:44:48 Link to Item http://hdl.handle.net/10150/551760 SUPERGENE MINERALOGY AND PROCESSES IN THE SAN XAVIER MINE AREA— PIMA COUNTY, ARIZONA by L. Clark Arnold A Thesis Submitted to the Faculty of the DEPARTMENT OF GEOLOGY In Partial Fulfillment of the Requirements For the Degree of MASTER OF SCIENCE In the Graduate College THE UNIVERSITY OF ARIZONA 1964 STATEMENT BY AUTHOR This thesis has been submitted in partial fulfillment of require ments for an advanced degree at The University of Arizona and is de posited in the University Library to be made available to borrowers under rules of the Library. Brief quotations from this thesis are allowable without special permission, provided that accurate acknowledgment of source is made. Requests for permission for extended quotation from or reproduction of this manuscript in whole or in part may be granted by the head of the major department or the Dean of the Graduate College when in his judg ment the proposed use of the material is in the interests of scholarship. In all other instances, however, permission must be obtained from the author. -
Nickel Minerals from Barberton, South Africa: I
American Mineralogist, Volume 58, pages 733-735, 1973 NickelMinerals from Barberton,South Africa: Vl. Liebenbergite,A NickelOlivine SvsneNoA. nn Wnar Nationnl Institute lor Metallurgy, I Yale Road.,Milner Park, I ohannesburg,South Alrica Lnwrs C. ClI.x Il. S. GeologicalSuruey, 345 Middlefield Road, Menlo Park, California 94025 Abstract Liebenbergite, a nickel olivine from the mineral assemblage trevorite-liebenbergite-nickel serpentine-nickel ludwigite-bunsenite-violarite-millerite-gaspeite-nimite, is described mineral- ogically.Ithasa-1.820,P-1.854,7-1.888,ZVa-88",specificgravity-4'60,Mohs hardness- 6 to 6.5, a - 4.727, b - 10.191,c = 5.955A, and Z - 4. X-ray powder data (48 lines) were indexed according to the space grottp Pbnm. The mean chemical composi- tion, calculated from electron microprobe analyses of eight separate liebenbergite grains, gives the mineral formula: (NL eMgoaCoo,sFeo o)Sio "nOn The name is for W. R. Liebenberg, Deputy Director-General of the National Institute for Metallurgy, South Africa. Introduction mission on New Minerals and Mineral Names (rMA). A re-investigationof the trevorite deposit at Bon Accord in the Barberton Mountain Land, South Experimental Methods Africa, led to the discovery of two peculiar but distinct nickel mineral assemblages.Minerals from The refractive indices were determined by the the assemblagewillemseite-nimite-feroan trevorite- conventional liquid immersion method using a reevesite-millerite-violarite-goethitehave been de- sodium lamp as light source.The optical and crystal scribed in earlier papers in this series (de Waal, morphologicalparameters were studiedwith the aid 1969, l97oa, 1970b;de Waal and Viljoen, I97L). of a universal stage. -
Gem Water Cover:Fa 17/5/09 23:06 Page 1 GEM WATER Adding Crystals to Water Is Both Visually Appealing and Healthy
Gem Water cover:fa 17/5/09 23:06 Page 1 GEM WATER Adding crystals to water is both visually appealing and healthy. The water becomes infused with crystalline energy. It is a known fact that water carries mineral information and Gem Water provides effective remedies, acting quickly on a physical level. It is similar and complementary to wear- ing crystals, but the effects are not necessarily the same. The introduction to the book tells you all you need to know about the correct way to prepare Gem Water and pro- vides important information on which crystals to use and which not to prepare as Gem Water. The concept may appear simple at first, but you need to apply it with care, and the book explains all the facts you need to know before getting started. The second part of the book features more than 100 Michael Joachim Goebel Gienger, Crystals and 34 special mixtures with their effects as Gem Water remedies. Gem Water How to prepare and use EARTHDANCER more than 130 crystal waters for therapeutic treatments A FINDHORN PRESS IMPRINT MichaelMichael GiengerGienger JoachimJoachim GoebelGoebel Gem Water 96:– 17/5/09 23:13 Page 1 Gem Water How to prepare and use more than 130 crystal waters for therapeutic treatments Michael Gienger Joachim Goebel EARTHDANCER A FINDHORN PRESS IMPRINT Gem Water 96:– 17/5/09 23:13 Page 2 Publishers’ Note The information in this book was produced according to our best knowledge and belief, and the healing effects of the gem waters described have been tried and tested many times. -
Barite (Barium)
Barite (Barium) Chapter D of Critical Mineral Resources of the United States—Economic and Environmental Geology and Prospects for Future Supply Professional Paper 1802–D U.S. Department of the Interior U.S. Geological Survey Periodic Table of Elements 1A 8A 1 2 hydrogen helium 1.008 2A 3A 4A 5A 6A 7A 4.003 3 4 5 6 7 8 9 10 lithium beryllium boron carbon nitrogen oxygen fluorine neon 6.94 9.012 10.81 12.01 14.01 16.00 19.00 20.18 11 12 13 14 15 16 17 18 sodium magnesium aluminum silicon phosphorus sulfur chlorine argon 22.99 24.31 3B 4B 5B 6B 7B 8B 11B 12B 26.98 28.09 30.97 32.06 35.45 39.95 19 20 21 22 23 24 25 26 27 28 29 30 31 32 33 34 35 36 potassium calcium scandium titanium vanadium chromium manganese iron cobalt nickel copper zinc gallium germanium arsenic selenium bromine krypton 39.10 40.08 44.96 47.88 50.94 52.00 54.94 55.85 58.93 58.69 63.55 65.39 69.72 72.64 74.92 78.96 79.90 83.79 37 38 39 40 41 42 43 44 45 46 47 48 49 50 51 52 53 54 rubidium strontium yttrium zirconium niobium molybdenum technetium ruthenium rhodium palladium silver cadmium indium tin antimony tellurium iodine xenon 85.47 87.62 88.91 91.22 92.91 95.96 (98) 101.1 102.9 106.4 107.9 112.4 114.8 118.7 121.8 127.6 126.9 131.3 55 56 72 73 74 75 76 77 78 79 80 81 82 83 84 85 86 cesium barium hafnium tantalum tungsten rhenium osmium iridium platinum gold mercury thallium lead bismuth polonium astatine radon 132.9 137.3 178.5 180.9 183.9 186.2 190.2 192.2 195.1 197.0 200.5 204.4 207.2 209.0 (209) (210)(222) 87 88 104 105 106 107 108 109 110 111 112 113 114 115 116 -
Aurichalcite (Zn, Cu)5(CO3)2(OH)6 C 2001-2005 Mineral Data Publishing, Version 1
Aurichalcite (Zn, Cu)5(CO3)2(OH)6 c 2001-2005 Mineral Data Publishing, version 1 Crystal Data: Monoclinic, pseudo-orthorhombic by twinning. Point Group: 2/m. As acicular to lathlike crystals with prominent {010}, commonly striated k [001], with wedgelike terminations, to 3 cm. Typically in tufted divergent sprays or spherical aggregates, may be in thick crusts; rarely columnar, laminated or granular. Twinning: Observed in X-ray patterns. Physical Properties: Cleavage: On {010} and {100}, perfect. Tenacity: “Fragile”. Hardness = 1–2 D(meas.) = 3.96 D(calc.) = 3.93–3.94 Optical Properties: Transparent to translucent. Color: Pale green, greenish blue, sky-blue; colorless to pale blue, pale green in transmitted light. Luster: Silky to pearly. Optical Class: Biaxial (–). Pleochroism: Weak; X = colorless; Y = Z = blue-green. Orientation: X = b; Y ' a; Z ' c. Dispersion: r< v; strong. α = 1.654–1.661 β = 1.740–1.749 γ = 1.743–1.756 2V(meas.) = Very small. Cell Data: Space Group: P 21/m. a = 13.82(2) b = 6.419(3) c = 5.29(3) β = 101.04(2)◦ Z=2 X-ray Powder Pattern: Mapim´ı,Mexico. 6.78 (10), 2.61 (8), 3.68 (7), 2.89 (4), 2.72 (4), 1.827 (4), 1.656 (4) Chemistry: (1) CO2 16.22 CuO 19.87 ZnO 54.01 CaO 0.36 H2O 9.93 Total 100.39 (1) Utah; corresponds to (Zn3.63Cu1.37)Σ=5.00(CO3)2(OH)6. Occurrence: In the oxidized zones of copper and zinc deposits. Association: Rosasite, smithsonite, hemimorphite, hydrozincite, malachite, azurite. -
Infrare D Transmission Spectra of Carbonate Minerals
Infrare d Transmission Spectra of Carbonate Mineral s THE NATURAL HISTORY MUSEUM Infrare d Transmission Spectra of Carbonate Mineral s G. C. Jones Department of Mineralogy The Natural History Museum London, UK and B. Jackson Department of Geology Royal Museum of Scotland Edinburgh, UK A collaborative project of The Natural History Museum and National Museums of Scotland E3 SPRINGER-SCIENCE+BUSINESS MEDIA, B.V. Firs t editio n 1 993 © 1993 Springer Science+Business Media Dordrecht Originally published by Chapman & Hall in 1993 Softcover reprint of the hardcover 1st edition 1993 Typese t at the Natura l Histor y Museu m ISBN 978-94-010-4940-5 ISBN 978-94-011-2120-0 (eBook) DOI 10.1007/978-94-011-2120-0 Apar t fro m any fair dealin g for the purpose s of researc h or privat e study , or criticis m or review , as permitte d unde r the UK Copyrigh t Design s and Patent s Act , 1988, thi s publicatio n may not be reproduced , stored , or transmitted , in any for m or by any means , withou t the prio r permissio n in writin g of the publishers , or in the case of reprographi c reproductio n onl y in accordanc e wit h the term s of the licence s issue d by the Copyrigh t Licensin g Agenc y in the UK, or in accordanc e wit h the term s of licence s issue d by the appropriat e Reproductio n Right s Organizatio n outsid e the UK. Enquirie s concernin g reproductio n outsid e the term s state d here shoul d be sent to the publisher s at the Londo n addres s printe d on thi s page. -
Thirty-Fourth List of New Mineral Names
MINERALOGICAL MAGAZINE, DECEMBER 1986, VOL. 50, PP. 741-61 Thirty-fourth list of new mineral names E. E. FEJER Department of Mineralogy, British Museum (Natural History), Cromwell Road, London SW7 5BD THE present list contains 181 entries. Of these 148 are Alacranite. V. I. Popova, V. A. Popov, A. Clark, valid species, most of which have been approved by the V. O. Polyakov, and S. E. Borisovskii, 1986. Zap. IMA Commission on New Minerals and Mineral Names, 115, 360. First found at Alacran, Pampa Larga, 17 are misspellings or erroneous transliterations, 9 are Chile by A. H. Clark in 1970 (rejected by IMA names published without IMA approval, 4 are variety because of insufficient data), then in 1980 at the names, 2 are spelling corrections, and one is a name applied to gem material. As in previous lists, contractions caldera of Uzon volcano, Kamchatka, USSR, as are used for the names of frequently cited journals and yellowish orange equant crystals up to 0.5 ram, other publications are abbreviated in italic. sometimes flattened on {100} with {100}, {111}, {ill}, and {110} faces, adamantine to greasy Abhurite. J. J. Matzko, H. T. Evans Jr., M. E. Mrose, lustre, poor {100} cleavage, brittle, H 1 Mono- and P. Aruscavage, 1985. C.M. 23, 233. At a clinic, P2/c, a 9.89(2), b 9.73(2), c 9.13(1) A, depth c.35 m, in an arm of the Red Sea, known as fl 101.84(5) ~ Z = 2; Dobs. 3.43(5), D~alr 3.43; Sharm Abhur, c.30 km north of Jiddah, Saudi reflectances and microhardness given. -
Daqingshanite-(Ce) (Sr, Ca, Ba)3(Ce, La)(PO4)(CO3)3−X(OH, F)X C 2001-2005 Mineral Data Publishing, Version 1
Daqingshanite-(Ce) (Sr, Ca, Ba)3(Ce, La)(PO4)(CO3)3−x(OH, F)x c 2001-2005 Mineral Data Publishing, version 1 Crystal Data: Hexagonal. Point Group: 3m (probable). As subhedral to rounded platy crystals, may be crudely rhombohedral, to 3 mm, in aggregates. Twinning: Complex polysynthetic twinning observed in some material. Physical Properties: Cleavage: Perfect on {1011}. Fracture: Conchoidal. Hardness = n.d. VHN = 335 (20 g load). D(meas.) = 3.81 D(calc.) = 3.71 Optical Properties: Semitransparent. Color: Pale yellow to nearly white; colorless in thin section. Streak: White. Luster: Vitreous to greasy. Optical Class: Uniaxial (–). ω = 1.708 = 1.609 Cell Data: Space Group: R3m, R3m, or R32. a = 10.058–10.073 c = 9.225–9.234 Z = 3 X-ray Powder Pattern: Bayan Obo deposit, China. 3.16 (10), 2.52 (7), 3.95 (6), 2.040 (6), 1.941 (6), 2.110 (5), 1.895 (4) Chemistry: (1) (2) (1) (2) (1) (2) P2O5 11.73 10.50 Fe2O3 0.21 K2O 0.03 CO2 16.19 n.d. MnO 0.02 F 0.80 0.29 ThO2 0.04 < 0.22 MgO 0.72 < 0.12 Cl 0.10 + Al2O3 0.18 < 0.12 CaO 6.17 0.94 H2O 0.68 n.d. La2O3 7.88 10.22 SrO 26.10 41.82 −O=F2 0.34 Ce2O3 10.16 12.24 BaO 15.98 4.57 Total [99.376] RE2O3 2.696 < 3.36 Na2O 0.13 < 0.16 (1) Bayan Obo deposit, China; CO2 and H2O by gas chromatography, original total given as 99.20%; RE2O3 =Pr6O11 0.70%, Nd2O3 1.59%, Sm2O3 0.106%, Eu2O3 0.02%, Gd2O3 0.12%, Tb4O7 0.05%, Dy2O3 0.03%, Ho2O3 0.03%, Er2O3 0.01%, Tm2O3 0.01%, Yb2O3 0.02%, Lu2O3 0.01%; corresponds to (Sr1.52Ca0.67Ba0.63Mg0.11Na0.03)Σ=2.96(Ce0.37La0.29RE0.10Al0.02 3+ Fe0.02)Σ=0.80(PO4)1.00(CO3)2.23[(OH)0.46F0.26]Σ=0.72. -
Carbon Mineral Ecology: Predicting the Undiscovered Minerals of Carbon
American Mineralogist, Volume 101, pages 889–906, 2016 Carbon mineral ecology: Predicting the undiscovered minerals of carbon ROBERT M. HAZEN1,*, DANIEL R. HUMMER1, GRETHE HYSTAD2, ROBERT T. DOWNS3, AND JOSHUA J. GOLDEN3 1Geophysical Laboratory, Carnegie Institution, 5251 Broad Branch Road NW, Washington, D.C. 20015, U.S.A. 2Department of Mathematics, Computer Science, and Statistics, Purdue University Calumet, Hammond, Indiana 46323, U.S.A. 3Department of Geosciences, University of Arizona, 1040 East 4th Street, Tucson, Arizona 85721-0077, U.S.A. ABSTRACT Studies in mineral ecology exploit mineralogical databases to document diversity-distribution rela- tionships of minerals—relationships that are integral to characterizing “Earth-like” planets. As carbon is the most crucial element to life on Earth, as well as one of the defining constituents of a planet’s near-surface mineralogy, we focus here on the diversity and distribution of carbon-bearing minerals. We applied a Large Number of Rare Events (LNRE) model to the 403 known minerals of carbon, using 82 922 mineral species/locality data tabulated in http://mindat.org (as of 1 January 2015). We find that all carbon-bearing minerals, as well as subsets containing C with O, H, Ca, or Na, conform to LNRE distributions. Our model predicts that at least 548 C minerals exist on Earth today, indicating that at least 145 carbon-bearing mineral species have yet to be discovered. Furthermore, by analyzing subsets of the most common additional elements in carbon-bearing minerals (i.e., 378 C + O species; 282 C + H species; 133 C + Ca species; and 100 C + Na species), we predict that approximately 129 of these missing carbon minerals contain oxygen, 118 contain hydrogen, 52 contain calcium, and more than 60 contain sodium. -
Thirty-Seventh List of New Mineral Names. Part 1" A-L
Thirty-seventh list of new mineral names. Part 1" A-L A. M. CLARK Department of Mineralogy, The Natural History Museum, Cromwell Road, London SW7 5BD, UK AND V. D. C. DALTRYt Department of Geology and Mineralogy, University of Natal, Private Bag XO1, Scottsville, Pietermaritzburg 3209, South Africa THE present list is divided into two sections; the pegmatites at Mount Alluaiv, Lovozero section M-Z will follow in the next issue. Those Complex, Kola Peninsula, Russia. names representing valid species, accredited by the Na19(Ca,Mn)6(Ti,Nb)3Si26074C1.H20. Trigonal, IMA Commission on New Minerals and Mineral space group R3m, a 14.046, c 60.60 A, Z = 6. Names, are shown in bold type. Dmeas' 2.76, Dc~ac. 2.78 g/cm3, co 1.618, ~ 1.626. Named for the locality. Abenakiite-(Ce). A.M. McDonald, G.Y. Chat and Altisite. A.P. Khomyakov, G.N. Nechelyustov, G. J.D. Grice. 1994. Can. Min. 32, 843. Poudrette Ferraris and G. Ivalgi, 1994. Zap. Vses. Min. Quarry, Mont Saint-Hilaire, Quebec, Canada. Obschch., 123, 82 [Russian]. Frpm peralkaline Na26REE(SiO3)6(P04)6(C03)6(S02)O. Trigonal, pegmatites at Oleny Stream, SE Khibina alkaline a 16.018, c 19.761 A, Z = 3. Named after the massif, Kola Peninsula, Russia. Monoclinic, a Abenaki Indian tribe. 10.37, b 16.32, c 9.16 ,~, l~ 105.6 ~ Z= 2. Named Abswurmbachite. T. Reinecke, E. Tillmanns and for the chemical elements A1, Ti and Si. H.-J. Bernhardt, 1991. Neues Jahrb. Min. Abh., Ankangite. M. Xiong, Z.-S. -
Sodium Permanganate Etch Baths and Their Use in Cleaning, Desmearing And/Or Etching Resinous Substrates
Europaisches Patentamt J European Patent Office Publication number: 0 207 586 Office europeen des brevets B1 EUROPEAN PATENT SPECIFICATION Date of publication of patent specification: 22.11.90 int. ci.5: C 23 C 18/22, H 05 K 3/42, C 09 K 13/02 Application number: 86302336.2 Date of filing: 27.03.86 Sodium permanganate etch baths and their use in cleaning, desmearing and/or etching resinous substrates. (§) Priority: 31.05.85 US 739726 Proprietor: MORTON INTERNATIONAL, INC. 110 North Wacker Drive Chicago Illinois 60606 (US) Date of publication of application: 07.01.87 Bulletin 87/02 Inventor: Krulik, Gerald 25142 Barents Street Publication of the grant of the patent- Laguna Hills California 92653 (US) 22.11.90 Bulletin 90/47 Representative: Bankes, Stephen Charles Digby Designated Contracting States- etal AT BE CH DE FR GB IT LI LU NL SE BARON & WARREN 18 South End Kensington London W8 5BU (GB) 1 References cited: US-A-3080323 US-A-3 095 380 US-A-3 528924 US-A-3 652 351 US-A-3 652 417 <0 00 IO N o CM o Note: Within nine months from the publication of the mention of the grant of the European patent, any person may give notice to the European Patent Office of opposition to the European patent granted. Notice of opposition shall Q. be filed in a written reasoned statement. It shall not be deemed to have been filed until the opposition fee has been Ill paid. (Art. 99(1 ) European patent convention). Courier Press, Leamington Spa, England.