New Design of a CNG-H2-AIR Mixer for Internal Combustion Engines: an Experimental and Numerical Study
Total Page:16
File Type:pdf, Size:1020Kb
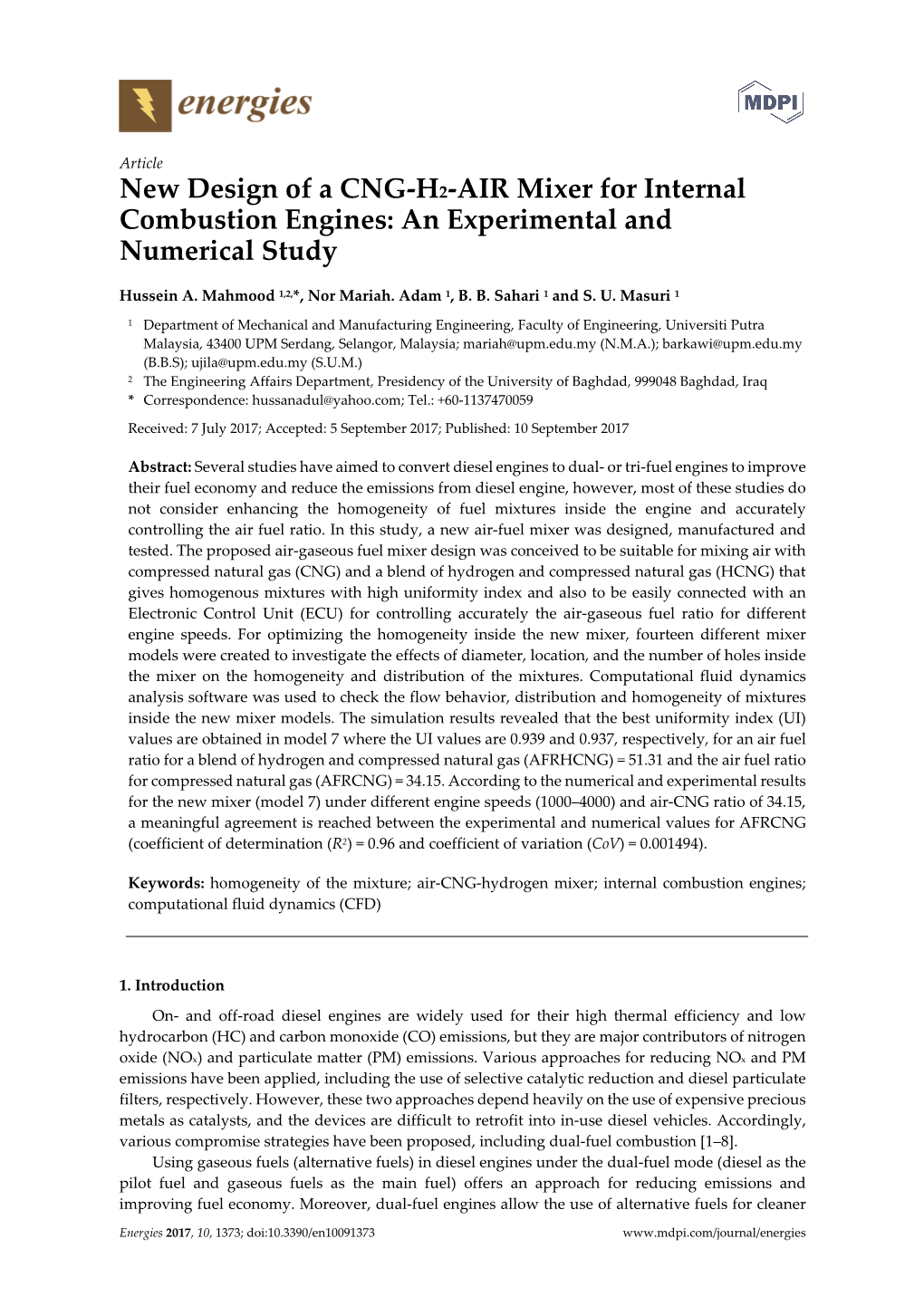
Load more
Recommended publications
-
Unconventional Gas and Oil in North America Page 1 of 24
Unconventional gas and oil in North America This publication aims to provide insight into the impacts of the North American 'shale revolution' on US energy markets and global energy flows. The main economic, environmental and climate impacts are highlighted. Although the North American experience can serve as a model for shale gas and tight oil development elsewhere, the document does not explicitly address the potential of other regions. Manuscript completed in June 2014. Disclaimer and copyright This publication does not necessarily represent the views of the author or the European Parliament. Reproduction and translation of this document for non-commercial purposes are authorised, provided the source is acknowledged and the publisher is given prior notice and sent a copy. © European Union, 2014. Photo credits: © Trueffelpix / Fotolia (cover page), © bilderzwerg / Fotolia (figure 2) [email protected] http://www.eprs.ep.parl.union.eu (intranet) http://www.europarl.europa.eu/thinktank (internet) http://epthinktank.eu (blog) Unconventional gas and oil in North America Page 1 of 24 EXECUTIVE SUMMARY The 'shale revolution' Over the past decade, the United States and Canada have experienced spectacular growth in the production of unconventional fossil fuels, notably shale gas and tight oil, thanks to technological innovations such as horizontal drilling and hydraulic fracturing (fracking). Economic impacts This new supply of energy has led to falling gas prices and a reduction of energy imports. Low gas prices have benefitted households and industry, especially steel production, fertilisers, plastics and basic petrochemicals. The production of tight oil is costly, so that a high oil price is required to make it economically viable. -
200 LNG-Powered Vessels Planned in Chongqing by 2020
Number #110 April 2016 2016, APRIL 1 Asian NGV Communications is a publication of AltFuels Communications Group. China: 200 LNG-powered vessels planned in Chongqing by 2020 India Emirates 15,000 vehicles MAN showcases converted to CNG natural gas buses in Delhi this year in Dubai 2 ASIAN NGV COMMUNICATIONS 2016, APRIL 3 Summary April 2016 #110 COPIES DISTRIBUTION We print and mail to 24 Asian countries around 4,000 hard copies addressed to conversion pag 04 China: 200 LNG-powered vessels planned in Chongqing by 2020 centres, Oil & Gas companies, OEM NGVs, governmental related offices, filling station 11. MAN showcases natural owners, equipment suppliers, gas buses in Dubai related associations and industries. In addition, the 12. New collaboration electronic version of the magazine is sent to more than boosts LNG use as 15,000 global NGV contacts in marine fuel in Middle 94 countries. East pag 06 New LNG terminal project begins commercial This e-version is also available 13. Pioneer dual fuel engine for free download to all visitors operations in Beihai of www.ngvjournal.com. demonstrated in Korea Below is the list of hard copy 14. Korean scientists develop receivers. Armenia, Australia, engine operating with Azerbaijan, Bangladesh, China, Egyp, India, Indonesia, Iran, hydrogen and CNG Israel, Japan, Kazakhstan, Korea, Malaysia, Myanmar (Burma), 15. Japan: first hydrogen New Zealand, Pakistan, The refuelling station will Philippines, Russia, Singapore, open in Tohoku Taiwan, Thailand, Turkey, United pag 08 India: 15,000 vehicles Arab Emirates, Vietnam, If your 16. New venture will NGV business is in Asia, the converted to CNG in Delhi Pacific, and the Middle East, promote hydrogen fuel since January advertise with us! cell technologies in Japan Asian NGV Communications 1400 - PMB 174, 300-5, Changchon –Ri, Namsan- 17. -
Hydrogen-Enriched Compressed Natural Gas (HCNG)
Year 2005 UCD—ITS—RR—05—29 Hydrogen Bus Technology Validation Program Andy Burke Zach McCaffrey Marshall Miller Institute of Transportation Studies, UC Davis Kirk Collier Neal Mulligan Collier Technologies, Inc. Institute of Transportation Studies ◊ University of California, Davis One Shields Avenue ◊ Davis, California 95616 PHONE: (530) 752-6548 ◊ FAX: (530) 752-6572 WEB: http://its.ucdavis.edu/ Hydrogen Bus Technology Validation Program Andy Burke, Zach McCaffrey, Marshall Miller Institute of Transportation Studies, UC Davis Kirk Collier, Neal Mulligan Collier Technologies, Inc. Technology Provider: Collier Technologies, Inc. Grant number: ICAT 01-7 Grantee: University of California, Davis Date: May 12, 2005 Conducted under a grant by the California Air Resources Board of the California Environmental Protection Agency The statements and conclusions in this Report are those of the grantee and not necessarily those of the California Air Resources Board. The mention of commercial products, their source, or their use in connection with material reported herein is not to be construed as actual or implied endorsement of such products 2 Acknowledgments Work on this program was funded by the Federal Transit Administration, the California Air Resources Board, and the Yolo-Solano Air Quality Management District. This Report was submitted under Innovative Clean Air Technologies grant number 01-7 from the California Air Resources Board. 3 Table of Contents Abstract………………………………………………………………………………...................6 Executive Summary…………………………………………………………………...................7 -
Improving Performance of Compressed Natural Gas Fueled Passenger Car Engine by Addition of Hydrogen
Journal of Scientific & Industrial Research Vol. 77, January 2018, pp. 61-65 Improving Performance of Compressed Natural Gas Fueled Passenger Car Engine by Addition of Hydrogen A K Sehgal1*, M Saxena2, S Pandey3 and R K Malhotra4 *1Indian Oil Corporation Ltd, Faridabad, India 2Univeristy of Technology and Management, Shillong, India 3University of Petroleum and Energy Studies, Dehradun, India 4Petroleum Federation of India, New Delhi, India Received 06 October 2016; revised 05 June 2017; accepted 07 October 2017 Hydrogen is a clean fuel that can be used as sole fuel or blends with compressed natural gas (CNG) in the spark ignition engines. Blending of hydrogen in CNG improves the burning velocity and calorific value of CNG. Engine tests were carried out using CNG and optimized fuel blend of 18%HCNG for comparing the engine performance and emissions behavior. Marginal improvement in engine performance (up to 2%) and significant reduction in emissions with18%HCNG compared to neat CNG. The brake specific fuel consumption was 5% lesser compared to CNG. Replacement of methane by hydrogen in the 18%HCNG blend reduced the HC emissions by ~20% and NOx emissions was increased by ~ 10-20% compared to CNG. 18% HCNG decreased the methane emissions up to 25% compared to CNG. The investigation showed that 18% HCNG has given better performance and emissions compared to CNG. Keywords: Hydrogen, Compressed Natural Gas, Emissions, Methane Emissions Introduction produce any major pollutants such as CO, HC, SOx, Natural gas is a naturally occurring form of fossil smoke and other toxic metals except NOx. Hydrogen energy. Utilization of natural gas as fuel for internal can be produced from renewable sources such as combustion engines was almost restricted to biomass and water as well as from non-renewable stationary applications prior to World War II. -
CLIMATE ACTION PLAN Websites
CLIMATE ACTION PLAN Websites Climate action cuts across all sectors of our economy and is being addressed in multiple ways. Information on government actions related to climate action are also found in the following: h LiveSmart BC http://www.livesmartbc.ca/ h The BC Energy Plan: A Vision for Clean Energy Leadership http://www.energyplan.gov.bc.ca/ h The BC Bioenergy Strategy http://www.energyplan.gov.bc.ca/bioenergy/ h The Agriculture Plan: Growing a Healthy Future for BC Farmers http://www.al.gov.bc.ca/Agriculture_Plan/ h The Mountain Pine Beetle Action Plan http://www.for.gov.bc.ca/hfp/mountain_pine_beetle/ h Living Water Smart: British Columbia's Water Plan http://www.livingwatersmart.ca./ h The BC Air Action Plan http://www.bcairsmart.ca/ h The BC Transit Plan http://www.th.gov.bc.ca/Transit_Plan/index.html h Energy Efficient Building Strategy http://www.energyplan.gov.bc.ca/efficiency/ h BC Green Building Code http://www.housing.gov.bc.ca/building/green/ h Pacific Institute for Climate Solutions http://www.pics.uvic.ca/ h Towns for Tomorrow http://www.townsfortomorrow.gov.bc.ca/ h Climate Action Secretariat http://www.climateactionsecretariat.gov.bc.ca/ BRITISH COLUMBIA’S Contents Message from the B.C. Government 1 Highlights 2 The Challenge 6 The Opportunity 10 The B.C. Climate Action Plan – Phase One 12 Section One: Setting the Course 13 Section Two: Acting in Every Sector 25 Acting in Every Sector: Transportation 26 Acting in Every Sector: Buildings 36 Acting in Every Sector: Waste 41 Acting in Every Sector: Agriculture 43 Acting -
Hydrogen Enriched Compressed Natural Gas (Hcng) – a Futuristic Fuel for Internal Combustion Engines
HYDROGEN ENRICHED COMPRESSED NATURAL GAS (HCNG) – A FUTURISTIC FUEL FOR INTERNAL COMBUSTION ENGINES by Kasianantham NANTHAGOPAL a*, Rayapati SUBBARAO b, Thangavelu ELANGO a, Ponnusamy BASKAR a and Kandasamy ANNAMALAI c a Automotive Research Centre, SMBS,VIT University, Vellore-14, Tamilnadu, India, e-mail: [email protected] b Department of Mechanical Engineering , Indian Institute of Technology Madras, Chennai-25, India. c Department of Automobile Engineering , MIT Campus, Anna University, Chennai-25, India Air pollution is fast becoming a serious global problem with increasing population and its subsequent demands. This has resulted in increased usage of hydrogen as fuel for internal combustion engines. Hydrogen resources are vast and it is considered as one of the most promising fuel for automotive sector. As the required hydrogen infrastructure and refueling stations are not meeting the demand, widespread introduction of hydrogen vehicles is not possible in the near future. One of the solutions for this hurdle is to blend hydrogen with methane. Such types of blends take benefit of the unique combustion properties of hydrogen and at the same time reduce the demand for pure hydrogen. Enriching natural gas with hydrogen could be a potential alternative to common hydrocarbon fuels for internal combustion engine applications. Many researchers are working on this for the last few years and work is now focused on how to use this kind of fuel to its maximum extent. This technical note is an assessment of HCNG usage in case of internal combustion engines. Several examples and their salient features have been discussed. Finally, overall effects of hydrogen addition on an engine fueled with HCNG under various conditions are illustrated. -
Hydrogen Energy Storage: Grid and Transportation Services Workshop
02 Hydrogen Energy Storage: Grid and Transportation Services February 2015 NREL is a national laboratory of the U.S. Department of Energy, Office of Energy EfficiencyWorkshop Structure and Renewable / 1 Energy, operated by the Alliance for Sustainable Energy, LLC. Hydrogen Energy Storage: Grid and Transportation Services February 2015 Hydrogen Energy Storage: Grid and Transportation Services Proceedings of an Expert Workshop Convened by the U.S. Department of Energy and Industry Canada, Hosted by the National Renewable Energy Laboratory and the California Air Resources Board Sacramento, California, May 14 –15, 2014 M. Melaina and J. Eichman National Renewable Energy Laboratory Prepared under Task No. HT12.2S10 Technical Report NREL/TP-5400-62518 February 2015 NREL is a national laboratory of the U.S. Department of Energy, Office of Energy Efficiency and Renewable Energy, operated by the Alliance for Sustainable Energy, LLC. This report is available at no cost from the National Renewable Energy Laboratory (NREL) at www.nrel.gov/publications National Renewable Energy Laboratory 15013 Denver West Parkway Golden, CO 80401 303-275-3000 www.nrel.gov NOTICE This report was prepared as an account of work sponsored by an agency of the United States government. Neither the United States government nor any agency thereof, nor any of their employees, makes any warranty, express or implied, or assumes any legal liability or responsibility for the accuracy, completeness, or usefulness of any information, apparatus, product, or process disclosed, or represents that its use would not infringe privately owned rights. Reference herein to any specific commercial product, process, or service by trade name, trademark, manufacturer, or otherwise does not necessarily constitute or imply its endorsement, recommendation, or favoring by the United States government or any agency thereof. -
Review on Opportunities and Difficulties with HCNG As a Future Fuel for Internal Combustion Engine
Advances in Aerospace Science and Applications. ISSN 2277-3223 Volume 4, Number 1 (2014), pp. 79-84 © Research India Publications http://www.ripublication.com/aasa.htm Review on Opportunities and Difficulties with HCNG as a Future Fuel for Internal Combustion Engine Priyanka Goyal1 and S.K. Sharma2 1Amity Institute of Aerospace Engineering, Amity University, Noida. 2Amity School of Engineering & Technology, Amity University, Noida. Abstract Air pollution is fast becoming a serious global problem with increasing population and its subsequent demands. This has resulted in increased usage of hydrogen as fuel for internal combustion engines. Hydrogen blended with natural gas (HCNG) is a viable alternative to pure fossil fuels because of the effective reduction in total pollutant emissions and the increased engine efficiency. This research note is an assessment of hydrogen enriched compressed natural gas usage in case of internal combustion engines. Several examples and their salient features have been discussed. Finally, overall effects of hydrogen addition on an engine fueled with hydrogen enriched com-pressed natural gas under various conditions are illustrated. In addition, the difficulties to deploy HCNG are clearly described. Keywords: CNG; HCNG; Hydrogen; Emissions. 1. Introduction In today’s modern world, where new technologies are being introduced, use of transportation energy is increasing rapidly. Fossil fuel, particularly petroleum fuel, isthe major contributor to energy production. Fossil fuel consumption is continuously rising as aresult of population growth in addition to improvements in the standard of living. Increased energy demand requires increased fuel production, thus draining current fossil fuel reserve levels at a faster rate. This has resulted in fluctuating oil prices and supply disruptions. -
US Shale Gas Development What Led to the Boom?
Date Issue Brief # I S S U E BRIEF US Shale Gas Development What Led to the Boom? Zhongmin Wang and Alan Krupnick May 2013 Issue Brief 13-04 Resources for the Future Resources for the Future is an independent, nonpartisan think tank that, through its social science research, enables policymakers and stakeholders to make better, more informed decisions about energy, environmental, and natural resource issues. Located in Washington, DC, its research scope comprises programs in nations around the world. 2 [AUTHORS] | RESOURCES FOR THE FUTURE US Shale Gas Development What Led to the Boom? Zhongmin Wang and Alan Krupnick1 Key Points The shale gas boom resulted from factors that 1. Introduction ultimately enabled firms to produce shale gas In this issue brief, we provide an overview of the economic, profitably, including policy, and technology history of shale gas development in technological innovation, the United States to ascertain what led to the shale gas government policy, private boom. For a much more detailed review, see our discussion entrepreneurship, private paper (Wang and Krupnick 2013). land and mineral rights ownership, high natural gas In the past decade, shale gas experienced an extraordinary prices in the 2000s, market boom in the United States, accounting for only 1.6 percent of structure, favorable total US natural gas production in 2000, 4.1 percent by 2005, geology, water availability, and an astonishing 23.1 percent by 2010. This remarkable and natural gas pipeline growth has spurred interest in exploring for shale gas infrastructure. resources elsewhere. A number of countries, including China, The key question for Mexico, Argentina, Poland, India, and Australia are beginning policymakers in countries to develop their own shale gas resources. -
Analysis of Fuel Consumption of HCNG Bus for US and European Test Codes
International Journal of Applied Engineering Research ISSN 0973-4562 Volume 12, Number 19 (2017) pp. 8232-8237 © Research India Publications. http://www.ripublication.com Analysis of Fuel Consumption of HCNG Bus for US and European Test Codes Jeongok Han1, Jungmin Chae2, Tongwon Lee3 and Kwangho Ko4* 1,2 Department of New Energy Technology, Research Institute of KOGAS, Suinro, Ansansi, Gyeonggi-do, Korea. 3,4 Department of Automotive engineering, AJOU Motor College, Boryeongsi, Chungnam, Korea. 4*corresponding author’s 1Orcid: 0000-0002-4261-6730, 2Orcid: 0000-0002-7142-7218, 3Orcid: 0000-0001-5075-9603 4Orcid: 0000-0001-9290-5269 & 4SCOPUS ID 55415346100) Abstract The US test code adopts carbon balance method also and fuel density at 20’C, one of the important coefficients in calculating This study examines the US and European test codes for fuel procedure should be specified. In EU, UNECE Regulation No. consumption calculation of natural gas fueled vehicles, and 101-Revision 3 presents the fuel economy test procedure for analyzes the suitability for the HCNG(Hydrogen added the natural gas fueled vehicles and the standard test fuel density Compressed Natural Gas) fueled vehicles. The fuel is fixed as 0.654kg/m3 which is the value at 15’C[4]. It uses consumption calculation formula is derived by the balancing average fuel density value in the calculation procedure and the relation of the carbon weight of the fuel with vehicle exhaust test code specifies different calculating coefficients for various gas. US code do not limit the composition of test gas fuel, but gas fuels like HCNG(Hydrogen added Compressed Natural European code specifies reference test fuel (G20, G23). -
Unconventional Gas
POSTNOTE Number 374 April 2011 Unconventional Gas Overview UK reserves of unconventional gas, principally shale gas and coalbed methane (CBM), may add an additional 50% to the UK‟s potentially recoverable gas resources. There is significant uncertainty, however, over the prospects for both gas sources. Several companies in the UK are looking to exploit them but there is currently no full- scale production. Gas may reduce greenhouse gas emissions Unconventional sources of gas have recently by displacing coal, but there are concerns gained much attention due to the significant that the gas might instead supplement coal contribution they are making to US gas and lead to an overall increase in emissions. production. This POSTnote examines the Several groups are also concerned about potential for unconventional gas exploitation in the local environmental impact of shale gas the UK, the regulatory regimes covering such extraction, though the industry disputes activity, and the issues surrounding the most of their claims. extraction and use of the gas. Large-scale production of either shale gas or CBM is unlikely in the next five years. Background There is also much discussion about the possibility of gas The principal component of natural gas and the main contributing to an even greater share of electricity constituent of both conventional and unconventional gas is generation to help the UK meet its greenhouse gas methane. The term unconventional refers to the source emission-reduction targets, as gas produces half the 2 rather than the nature of the gas itself (Box 1). In the last emissions of coal. decade, the USA has experienced a significant increase in unconventional gas production as a result of developments This situation has led to significant interest in the UK‟s own in extraction technology. -
Oil, Gas & Coal
Oil, Gas & Coal Marco Mazzotti CCS and the Industry of Carbon-Based Resources – FS2020 February 24th, 2020 | | CCS overview I. Fossil fuel resources and II. CO2 and III.CCS: the global energy system climate change the concept years millions of years seconds hours/days years millenia | 24/02/2020 | 2 Oil, Gas & Coal: uses and processing Fossil fuels – stratigraphic age distribution Legend: CAMBRIAN, ORDOVICIAN, SILURIAN, DEVONIAN, MISSISSIPPIAN, PENNSYLVANIAN, PERMIAN, TRIASSIC, JURASSIC, CRETACEOUS, TERTIARY, QUATERNARY. | 24/02/2020 | 3 Oil, Gas & Coal: uses and processing Fossil fuels – an overview Decay of biomass through bio-geochemical processes Not present in nature Coal Oil Natural gas Hydrogen solid liquid gas gas ~ 2C/1H ~ 1C/2H ~ 1C/4H H2 100% 100% Carbon Hydrogen Production 3,900,000,000 toe 4,200,000,000 toe 2,900,000,000 toe 200,000,000 toe (2012, world) Uses Heat & electricity Coke (Steel) Chemicals Transport Hydrogen ~12% ~15% ~53% | 24/02/2020 | 4 From last week | 24/02/2020 | 5 Readings . Daniel Yergin „The prize – The epic quest for oil, money & power“, 1991 . Daniel Yergin „The quest – Energy, security, and the remaking of the modern world“, 2011 . Vaclav Smil „Energy at the crossroads – Global perspectives and uncertainties“, 2003 (chapter 4) . Rachel Maddow „Blowout – Corrupted democracy, rogue state Russia, and the richest, most destructive industry on earth“, 2019 . William T. Vollmann „No immediate danger – Vol. 1 of carbon ideologies“, 2018 (nuclear) . William T. Vollmann „No good alternative – Vol. 2 of carbon ideologies“, 2018 (coal, natural gas and oil) | 24/02/2020 | 6 Today’s topics . Oil & Gas . Extraction technologies .