The Measurement of the Adhesion of Glaze Ice
Total Page:16
File Type:pdf, Size:1020Kb
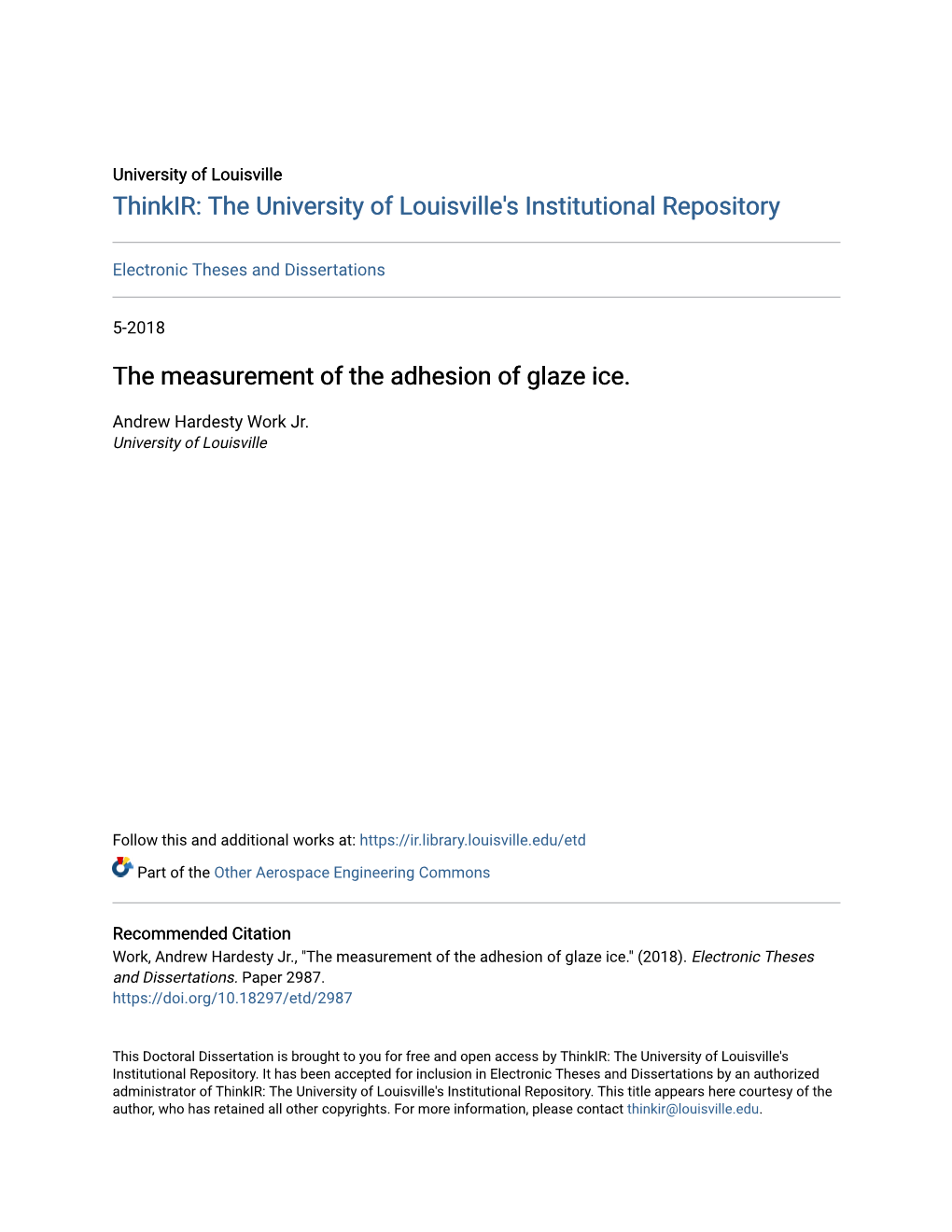
Load more
Recommended publications
-
Winter Storm Preparedness and Response
Winter Storm Preparedness and Response SAFETY AT HOME AND WHILE TRAVELING BE AWARE OF THE FORECAST Winter weather advisory. Formerly called a “Travelers’ Advisory,” this Winter storms are worth * serious consideration In alert may be issued by the National Weather Service for a variety of Illinois. Blizzards, heavy severe conditions. Weather advisories may be announced for snow, snow, freezing rain and blowing and drifting snow, freezing drizzle, freezing rain (when less sub-zero temperatures hit hard than ice storm conditions are expected), or a combination of weather and frequently across the events. state. Even if you think you are safe and warm at home, a * Winter storm watch. Severe winter weather conditions may affect your winter storm can become area (freezing rain, sleet or heavy snow may occur either separately or dangerous If the power is cut in combination). off. With a little planning, you can protect yourself and your * Winter storm warning. Severe winter weather conditions are imminent. family from the many hazards of winter weather, both at Freezing rain or freezing drizzle. Rain or drizzle is likely to freeze upon home and on the road. * impact, resulting in a coating of ice glaze on roads and all other exposed objects. * Sleet. Small particles of ice, usually mixed with rain. If enough sleet accumulates on the ground, it makes travel hazardous. * Blizzard warning. Sustained wind speeds of at least 35 miles per hour are accompanied by considerable failing and/or blowing snow. This is the most perilous winter storm, with visibility dangerously restricted. * Wind chill. A strong wind combined with a temperature slightly below freezing can have the same chilling effect as a temperature nearly 50 degrees lower in a calm atmosphere. -
ESSENTIALS of METEOROLOGY (7Th Ed.) GLOSSARY
ESSENTIALS OF METEOROLOGY (7th ed.) GLOSSARY Chapter 1 Aerosols Tiny suspended solid particles (dust, smoke, etc.) or liquid droplets that enter the atmosphere from either natural or human (anthropogenic) sources, such as the burning of fossil fuels. Sulfur-containing fossil fuels, such as coal, produce sulfate aerosols. Air density The ratio of the mass of a substance to the volume occupied by it. Air density is usually expressed as g/cm3 or kg/m3. Also See Density. Air pressure The pressure exerted by the mass of air above a given point, usually expressed in millibars (mb), inches of (atmospheric mercury (Hg) or in hectopascals (hPa). pressure) Atmosphere The envelope of gases that surround a planet and are held to it by the planet's gravitational attraction. The earth's atmosphere is mainly nitrogen and oxygen. Carbon dioxide (CO2) A colorless, odorless gas whose concentration is about 0.039 percent (390 ppm) in a volume of air near sea level. It is a selective absorber of infrared radiation and, consequently, it is important in the earth's atmospheric greenhouse effect. Solid CO2 is called dry ice. Climate The accumulation of daily and seasonal weather events over a long period of time. Front The transition zone between two distinct air masses. Hurricane A tropical cyclone having winds in excess of 64 knots (74 mi/hr). Ionosphere An electrified region of the upper atmosphere where fairly large concentrations of ions and free electrons exist. Lapse rate The rate at which an atmospheric variable (usually temperature) decreases with height. (See Environmental lapse rate.) Mesosphere The atmospheric layer between the stratosphere and the thermosphere. -
Detection of Glaze Icing Load and Temperature of Composite Insulators Using Fiber Bragg Grating
sensors Article Detection of Glaze Icing Load and Temperature of Composite Insulators Using Fiber Bragg Grating Jie Wei 1, Yanpeng Hao 1, Yuan Fu 1, Lin Yang 1,*, Jiulin Gan 2 and Zhongmin Yang 2 1 School of Electric Power, South China University of Technology, Guangzhou 510640, China; [email protected] (J.W.); [email protected] (Y.H.); [email protected] (Y.F.) 2 State Key Laboratory of Luminescent Materials and Devices, South China University of Technology, Guangzhou 510640, China; [email protected] (J.G.); [email protected] (Z.Y.) * Correspondence: [email protected]; Tel.: +86-159-8918-4979 Received: 2 January 2019; Accepted: 13 March 2019; Published: 16 March 2019 Abstract: Conventional methods for the online monitoring of icing conditions of composite insulators suffer from difficulties. To solve this issue, a novel method is first proposed to detect glaze icing load via embedding three optical fibers with fiber Bragg gratings (FBGs) into a 10 kV composite insulator. Specifically, FBG temperature compensation sensors were packaged in ceramic tubes to solve strain and temperature cross-sensitivity. Temperature effect experiments and simulated glaze icing load experiments were performed to verify the feasibility of the proposed method. The results show that temperature sensitivities of all FBGs are identical (i.e., 10.68 pm/◦C), which achieves a simultaneous measurement of temperature and strain. In addition, the proposed method can detect glaze icing load of the composite insulator above 0.5 N (i.e., 15% of icicle bridged degree) in the laboratory. Keywords: glaze icing detection; fiber Bragg grating (FBG); composite insulator with embedded FBG; simultaneous measurement of temperature and strain 1. -
Differential Responses of Tree Species to a Severe Ice Storm and Their
Forest Ecology and Management 468 (2020) 118177 Contents lists available at ScienceDirect Forest Ecology and Management journal homepage: www.elsevier.com/locate/foreco Differential responses of tree species to a severe ice storm andtheir T implications to forest composition in the southeast United States ⁎ Deliang Lua,b,c, Lauren S. Piled, Dapao Yub, Jiaojun Zhub,c, Don C. Bragge, G. Geoff Wanga, a Department of Forestry and Environmental Conservation, Clemson University, Clemson, SC 29634, USA b CAS Key Laboratory of Forest Ecology and Management, Institute of Applied Ecology, Shenyang 110016, China c Qingyuan Forest CERN, Chinese Academy of Sciences, Shenyang 110016, China d USDA Forest Service, Northern Research Station, Columbia, MO 65211, USA e USDA Forest Service, Southern Research Station, Monticello, AR 71656, USA ARTICLE INFO ABSTRACT Keywords: The unique terrain, geography, and climate patterns of the eastern United States encourage periodic occurrences Glaze event of catastrophic ice storms capable of large-scale damage or destruction of forests. However, the pervasive and Natural disturbance persistent effects of these glaze events on regional forest distribution and composition have rarely beenstudied. Lifeform group In the southeastern US, ice storm frequency and intensity increase with increasing latitude and along the Tree damage complex gradients from the coast (low, flat, sediment controlled and temperature moderated near the ocean) to Species distribution the interior (high, rugged, bedrock controlled, distant from warming ocean). To investigate the potential in- fluence of this disturbance gradient on regional forest composition, we studied the differential responses oftrees (canopy position, lifeform group, and species group) to a particularly severe ice storm. -
UNIVERSITY of CALIFORNIA, SAN DIEGO Temperature Reconstruction
UNIVERSITY OF CALIFORNIA, SAN DIEGO Temperature reconstruction at the West Antarctic Ice Sheet Divide, for the last millennium, from the combination of borehole temperature and inert gas isotope measurements. A dissertation submitted in partial satisfaction of the requirements for the degree Doctor of Philosophy in Oceanography by Anais J. Orsi Committee in charge: Jeffrey P. Severinghaus, Chair Bruce D. Cornuelle Helen Fricker Dan Lubin Lynne D. Talley William Trogler 2013 Copyright Anais J. Orsi, 2013 All rights reserved. The dissertation of Anais J. Orsi is approved, and it is ac- ceptable in quality and form for publication on microfilm and electronically: Chair University of California, San Diego 2013 iii EPIGRAPH Fortitudine Vincimus By endurance we conquer - Ernest Shackelton iv TABLE OF CONTENTS Signature Page................................... iii Epigraph....................................... iv Table of Contents..................................v List of Figures.................................... xii List of Tables.................................... xv Acknowledgements................................. xvi Vita, Publications, and Fields of Study....................... xix Abstract of the Dissertation............................. xxi Chapter 1 Introduction.............................1 Chapter 2 Magnitude and Temporal Evolution of DO 8 Abrupt Temperature Change Inferred From Nitrogen and Argon Isotopes in Greenland Ice Using a New Least-Squares Inversion.............4 2.1 Introduction..........................5 2.1.1 Reconstructing polar surface temperature......5 2.1.2 Abrupt climate changes................6 2.1.3 Noble gas isotopes..................8 2.1.4 Temperature reconstruction.............9 2.2 Methods............................9 2.2.1 Laboratory measurements..............9 2.2.2 Timescale....................... 10 2.2.3 Isolation of the thermal signal............ 12 2.2.3.1 Gas loss correction............. 13 2.2.3.2 Using two pairs of isotopes........ 14 2.2.3.3 Using a densification model....... -
Roofing Glossary Formatted
A Absorption the ability of a material to accept within itsbody quantities of gases or liquid, such as moisture. Accelerated Weathering:the process in which materials are exposed to a controlled environment where various exposures such as heat, water, condensation, or light are altered to magnify their effects, thereby accelerating the weathering process. The material's physical properties are measured after this process and compared to the original properties of the unexposed material, or to the properties of the material that has been exposed to natural weathering. Adhere: to cause two surfaces to be held together by adhesion, typically with asphalt or roofing cements in built-up roofing and with contact cements in some single-ply membranes. Aggregate: rock, stone, crushed stone, crushed slag, water-worn gravel or marble chips used for surfacing and/or ballasting a roof system. Aging: the effect on materials that are exposed to an environment for an interval of time. Alligatoring: the cracking of the surfacing bitumen on a built-up roof, producing a pattern of cracks similar to an alligator's hide; the cracks may or may not extend through the surfacing bitumen. Aluminum: a non-rusting metal sometimes used for metal roofing and flashing. Ambient Temperature: the temperature of the air; air temperature. Application Rate: the quantity (mass, volume, or thickness) of material applied per unit area. Apron Flashing: a term used for a flashing located at the juncture of the top of the sloped roof and a vertical wall or steeper- sloped roof. Architectural Shingle: shingle that provides a dimensional appearance. Asphalt:a dark brown or black substance found in a natural state or, more commonly, left as a residue after evaporating or otherwise processing crude oil or petroleum. -
Preliminary Assessment of System an Ice Accretion
Preliminary Assessment of an Ice Accretion System Paul Tattelman, Air Force Geophysics Laboratory, Hanscom Air Force Base, Massachusetts Climatic chamber tests of an off-the-shelf ice northwesternunited States. Two shortcomings of this detection system manufactured by Rosemount instrumentation that preclude its use at most observing Engineering Company were conducted at the sites are its size and its Orientation which results in Armament Development and Test Center, Eglin AFB, ice amounts being a function of the wind direction. Florida. The purpose of the tests was to Due to the importance of ice accretion design determine the feasibility of taking objective criteria for exposed AF systems, the Air Force observations of ice accretion near the earth's Geophysics Laboratory funded research to test the surface. Data was collected for a variety of feasibility of taking objective observations of ice wind, temperature, and precipitation conditions accretion using a sophisticated ice detection system which simulate natural icing. This paper marketed by Rosemount Engineering Company. presents the preliminary results of the tests. The'Rosemount'Ice Detection System Ice accretion can be a major destructive force The Rosemount Engineering Company, Minneapolis, to structures, such as towers, radar, elevated Minnesota markets a line of ice detectors which are cables, etc. Concurrent, or more probably subsequent used primarily to detect ice formation in the intake strong winds may be the critical factor in damaging portion of turbomachinery. They are aerodynamically equipment loaded with ice. Despite this, routine designed for use on aircraft, but they have been used objective observations of ice accretion at the earth's to detect icizig on towers. -
1. Walking and Working in Cold, Snow &
In this issue of the Environmental Health and Safety (EHS) Listserv, November 8, 2018 1. Walking and Working in Cold, Snow & Ice 2. Reduce Your Lab’s Energy Footprint 3. Hidden Stormwater Control 4. Near Misses Matter! 5. Near Misses to Ponder ---------------------------------------------------------- 1. Walking and Working in Cold, Snow & Ice Walking and working in snowy/icy/cold conditions are the focus of this article. Let’s begin by reviewing suggestions for “walking.” Walking around campus or from your vehicle/bus to your workplace during the winter can be hazardous. Every winter, slip/trip/fall injuries at UNL attributed to snow and ice account for approximately 3% of the overall number of injuries in a given year. That may not sound like much…until YOU are one of the injured. Winter Walking. Just like winter driving, winter walking requires anticipation. Think "defensive walking.” Follow these guidelines to help avoid injury: Use appropriate footwear for the surface/conditions. Avoid slick-soled shoes. Wear boots/shoes/overshoes with grip soles such as rubber or neoprene composite. Plan ahead to give yourself sufficient time to reach your destination. Plan your route and watch where you walk. Avoid routes that have not been cleared or appear glazed over. Avoid carrying large/heavy/awkwardly-shaped objects that can obstruct your view or affect your balance or center of gravity. Consider a backpack instead. Use special care in parking lots. Try to park in areas free of ice. When entering/exiting your vehicle, use your vehicle for support. Think about the walking surface whenever you move about campus, especially on days that are sunny. -
All Installed Roofing Systems Must Meet the Code and Regulatory Requirements and Recommendations of the Most Current Edition Of: 1
August 2013 State Wide Roof Asset Mgmt Program DCAM #14039(2) 14040(4) 14041(5) PERFORMANCE SPECIFICATIONS 1.0 SCOPE OF WORK/SUPPLEMENTARY CONDITIONS Pursuant to the provisions of O.S. 61 and Title 580 Department of Central Services, Chapter 20 Construction and Properties Division Rules, et seq.,: All installed roofing systems must meet the Code and Regulatory Requirements and Recommendations of the most current edition of: 1. The International Code Council (all Codes) including the International Building Code and its References, for example ANSI-SPRI ES-1 certification requirements. 2. All adopted Codes of the Oklahoma State Fire Marshall 3. All recommendations of the National Roofing Contractors Association, (NRCA) 4. Sheet Metal and Air Conditioning Contractor’s National Association, (SMACNA) 5. All requirements of the State of Oklahoma Roofing Program and the State of Oklahoma Roof Warranty, Roofing System Manufacturer’s Warranty, (RSMW) 6. All applicable American Society for Testing and Materials, (ASTM) Standards, (partial list below) 7. The requirements of U.L. 790 and U.L. 580 8. FM Global Approval Standards 4450, 4470, 4471, 4435, 4451, and 4454 9. All applicable FM Loss Prevention Data Sheets, including FM Data Sheets 1-34, 1-28, 1-29, and 1-49 10. The State Of Oklahoma Has Adopted the International Building Codes of 2009 with revisions. These apply. Excerpted from the: May 2007 — Factory Mutual Approval Guide All installed roofing systems provided as roofing renovations through the use of this Roofing Maintenance Contract must be FM Approved Roof Constructions. Continued approval is based upon production or availability of the product as FM Approved, the continued use of acceptable quality control procedures, satisfactory field experience, and compliance with the terms stipulated in the Approval Agreement. -
Study Guide for How to Perform Roof Inspections Course
Study Guide for How to Perform Roof Inspections Course This study guide can help you: • take notes; • read and study offline; • organize information; and • prepare for assignments and assessments. As a member of InterNACHI, you may check your education folder, transcript, and course completions by logging into your Members-Only Account at www.nachi.org/account. To purchase textbooks (printed and electronic), visit InterNACHI’s ecommerce partner Inspector Outlet at www.inspectoroutlet.com. Copyright © 2007-2015 International Association of Certified Home Inspectors, Inc. Page 1 of 106 Page 2 of 106 Student Verification & Interactivity Student Verification By enrolling in this course, the student hereby attests that s/he is the person completing all coursework. S/he understands that having another person complete the coursework for him or her is fraudulent and will result in being denied course completion and corresponding credit hours. The course provider reserves the right to make contact as necessary to verify the integrity of any information submitted or communicated by the student. The student agrees not to duplicate or distribute any part of this copyrighted work or provide other parties with the answers or copies of the assessments that are part of this course. If plagiarism or copyright infringement is proven, the student will be notified of such and barred from the course and/or have his/her credit hours and/or certification revoked. Communication on the message board or forum shall be of the person completing all coursework. Page 3 of 106 Introduction to Course Introduction to Roof Inspections An inspection of the roof system is both one of the most crucial areas of home inspection and one of the biggest concerns on the prospective home buyer's mind. -
WINTER STORMS: HOW WINTER STORMS FORM There Are Many Ways for Winter Storms to Form; However, All Have Three Key Components
Keeping Minnesota Ready MINNESOTA WINTER HAZARD AWARENESS WEEK Winter is the signature season of Minnesota. It’s normally a long season of cold temperatures and snow and ice that can last from November through April. Yet winter doesn’t slow Minnesotans down – in fact Minnesotans are just as mobile, social and active during winter as they are during the summer months – both indoors and especially outdoors. But in order to ensure a safe and enjoyable winter, it is critical to be informed and aware of the potential risks and hazards associated with winter weather and how to avoid them. The topics below describe some of the more common features of winter weather, including warnings and alerts and resources for more information. Keeping Minnesota Ready MONDAY – WINTER WEATHER WINTER STORMS: HOW WINTER STORMS FORM There are many ways for winter storms to form; however, all have three key components. COLD AIR: For snow and ice to form, the temperature must be below freezing in the clouds and near the ground. MOISTURE: Water evaporating from bodies of water, such as a large lake or the ocean, is an excellent source of moisture. LIFT: Lift causes moisture to rise and form clouds and precipitation. An example of lift is warm air colliding with cold air and being forced to rise. Another example of lift is air flowing up a mountain side. Warm Front Cold Front Lake Effect Mountain Effect Arctic Keeping Minnesota Ready WARNINGS AND ALERTS: KEEPING AHEAD OF THE STORM By listening to NOAA Weather Radio, commercial radio and television for the latest winter storm warnings, watches and advisories. -
Snow and Ice
NHP Science Note: 2013 Working together Snow and Ice This Note is one of a series of short guides covering a range of natural hazards. These guides aim to provide non-experts with a brief introduction to each hazard and to highlight key aspects that may need to be taken into account in decision- making during an emergency involving this hazard. They are not intended to be fully comprehensive, detailed analyses or to indicate what will happen on any particular occasion. Instead they will signpost issues that are likely to be important and provide links to sources of more detailed information. Each Note will be updated on an annual basis in line with the review of the National Risk Assessment. What are snow and ice? Most precipitation in the UK starts its life high in the atmosphere as ice or snow, but mostly it will melt before reaching the ground. If the atmosphere is colder than normal (or at high altitudes) melting does not occur and the precipitation reaches the ground in its frozen state. There are many forms of frozen precipitation, the main ones being snow and hail of varying size and water content. The ground temperature may be different from that of the air. Thus snow or hail may melt when it reaches the ground, but conversely, rain (or fog) may freeze, depositing black ice or glaze on the ground. Wet snow and freezing rain or fog can also accumulate in cold weather on trees, masts and cables, increasing their weight until they break or collapse. Freezing rain is liquid water falling into a layer of sub-zero air temperature where it freezes instantaneously on contact with surfaces – although rare in the UK it can cause severe black or glazed ice conditions in a very short period of time.