5 Foaming Behavior, Structure,.Hwp
Total Page:16
File Type:pdf, Size:1020Kb
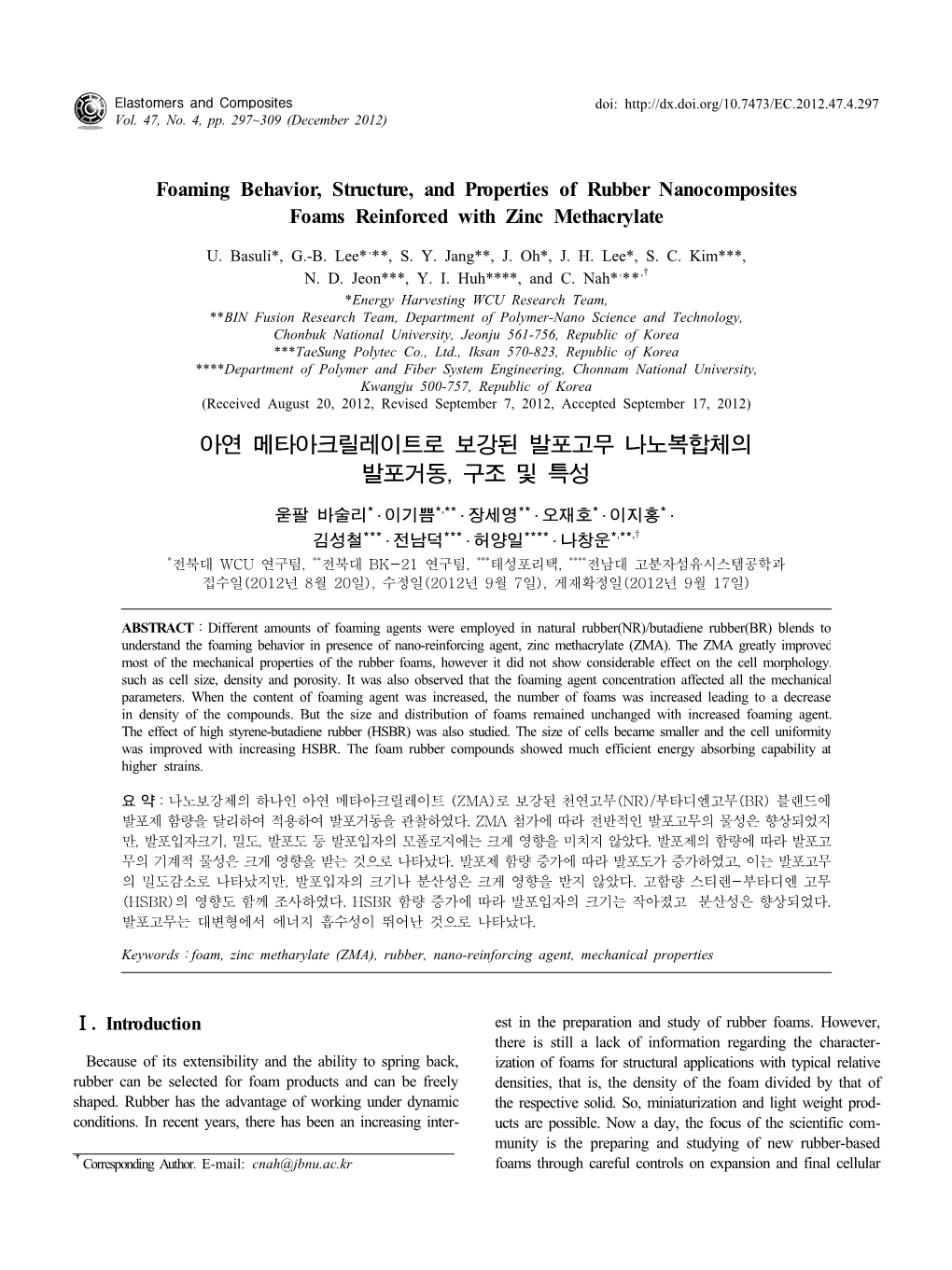
Load more
Recommended publications
-
The Ohio Motor Vehicle Industry
Policy Research and Strategic Planning Office A State Affiliate of the U.S. Census Bureau The Ohio Polymers Industry: Rubber and Plastic Resins and Products, and Related Machinery May 2010 Ted Strickland, Governor of Ohio Lee Fisher, Lt. Governor of Ohio Lisa Patt-McDaniel,Director, Ohio Department of Development THE OHIO POLYMERS INDUSTRY: Rubber and Plastic Resins and Products, and Related Machinery MAY 2010 B403 Don Larrick, Principal Analyst Policy Research and Strategic Planning, Ohio Department of Development P.O. Box 1001, Columbus, Oh. 43216-1001 Production Support: Steve Kelley, Editor; Robert Schmidley, GIS Specialist TABLE OF CONTENTS Page Executive Summary- - - - - - - - - - - - - - - - - - - - - - - - - - - - - - - - - - - - - - - - - 1 Description of Ohio’s Polymers Industry - - - - - - - - - - - - - - - - - - - - - - 4 Notable Polymers Industry Manufacturers- - - - - - - - - - - - - - - - - - - - - - - - - - - - - 6 Recent Expansion and Attraction Announcements- - - - - - - - - - - - - - - - - - - - - - - 12 The Composition of Ohio’s Polymers Industry: Value-Added- - - - - - - - - - - - - - - - 14 The Composition of Ohio’s Polymers Industry: Employment - - - - - - - - - - - - - - - - 16 Industry Pay - - - - - - - - - - - - - - - - - - - - - - - - - - - - - - - - - - - - - - - - - - - - - - - - - - 18 The Distribution of Industry Establishments in Ohio - - - - - - - - - - - - - - - - - - - - - - 20 The Distribution of Industry Employment in Ohio - - - - - - - - - - - - - - - - - - - - - - - - 22 Foreign Investment in Ohio -
Enhancing the Biodegradation of Waste Rubber a Novel Approach to Sustainable Management of Discarded Rubber Materials
INTERNATIONAL LATEX CONFERENCE 2015 Enhancing the Biodegradation of Waste Rubber A novel approach to sustainable management of discarded rubber materials Teresa Clark 8/12/2015 Rubber items are a critical part of modern society and a focus on the waste management of rubber is becoming more critical. Advancements have been made in recycling rubber waste, but a vast majority of rubber products are discarded into landfills. Sustainability efforts must include self-remediation through biodegradation of rubber (pre- consumer and post-consumer) in these waste sites. Current advancements provide insight into alternative methods of utilizing bio-mimicry to these return waste products to the natural carbon cycle, produce “green” energy and expand the scope of “Zero Waste”. Included are an assessment of the unique environment within landfills and the energy impact of utilizing these methods. Additionally, a brief update to the current progress in validating the biodegradation of rubber waste is included. Enhancing the Biodegradation of Waste Rubber International Latex Conference 2015 - Teresa Clark Contents Introduction .................................................................................................................................................. 2 Waste disposal of rubber materials .............................................................................................................. 2 Composting of Rubber ................................................................................................................................. -
Natural Rubber Value Chains: a Game Changer for Smallholders
Natural Rubber value chains: A game changer for smallholders A. Nosa Betty¹; A. A.i²; A. E.o² 1: RUBBER RESEARCH INSTITUTE OF NIGERIA, RESEARCH OUTREACH , Nigeria, 2: Rubber Research Institute of Nigeria,, Research outreach, Nigeria Corresponding author email: [email protected] Abstract: ABSTRACT The study analyzed the value chain of natural rubber in Nigeria. The study specifically mapped the natural rubber value chain and identify the functions performed by the respondents in the chain; identified the existing marketing channels and estimated the marketing margin at each value addition point. Data for the study were collected using a well-structured questionnaire administered to 425 respondents selected using a two–stage sampling process involving random and purposive sampling techniques. Data collected were analyzed using descriptive statistics, flow chat, marketing margins, marketing efficiency The findings showed a mean age of 53 years for farmers and 44 years for marketers, with males (97.86%) dominating. Most were married and majority had at least primary education. The main value chain agencies were input suppliers/nursery farmers, rubber farmers, marketers/collectors, processor and manufacturers, while the key product points along the chain were seeds, seedlings, budded stump, lump, latex concentrates, sheet, and crumbs. Marketing margin analysis showed crumb having the highest margin (N234.01) with processing cost having the major component. Value added by processing were N14.36k, N115.16, N136.14 and N124.38 per budded stump, latex concentrate, crumb and sheet respectively. The nursery was the most efficient and it was more profitable to process into crumb rubber. It was therefore recommendations that farmers may integrate backward to produce their own budded stumps and process their latex before selling for profit Acknowledegment: ACKNOWLEDGEMENTS The authors would like to acknowledge Prof. -
Preliminary Study on the Preparation of Latex Foam Rubber from Graft Copolymer of Deproteinised Natural Rubber and Methyl Methacrylate
Rubb. Res., 4(3), 141-152 REPRINT Preliminary Study on the Preparation of Latex Foam Rubber from Graft Copolymer of Deproteinised Natural Rubber and Methyl Methacrylate C. NAKASON*#. A. KAESAMAN,* N. YIMWAN* AND K. KETSARIN* Deproteinised natural rubber (DPNR) latex was prepared by incubation of fresh field natural rubber latex with a proteolytic enzyme in the presence of an emuisifier. The nitrogen content was decreased from 0.9% (in the fresh field natural rubber latex) to 0.07% (in the DPNR). A graft copolymer of the deproteinised natural rubber latex and poly(methyl methacrylate) (PMMA) was then synthesized using tert. butylhydroperoxide and tetraethylene pentamine as a redox initiator. The presence of grafted PMMA in the natural rubber molecules was confirmed using FTIR. Intense absorption peaks at 1732 cm~' (-C=O stretch) and 1140 cm~' (-C-O stretch) were observed. It was also found that the quantity of grafted PMMA increased with the increase in the level ofMMA used in the grafting reaction. The graft copolymer latex was later compounded and processed into a latex foam rubber. Results showed that the latex of graft copolymer blended with high ammonia concentrated latices provided high quality latex foam rubber. This included surface appearance and physical properties, such as hardness, compression set and density. It was also found that hardness, compression set and density of the latex foam rubber increased with the increase in the level of graft copolymer in compounding formulation. Furthermore, at the same blend ratio, the properties increased with the increase in the level of methyl methacrylate used in the grafting reaction. -
Effect of Fillers on the Recovery of Rubber Foam
polymers Article Effect of Fillers on the Recovery of Rubber Foam: From Theory to Applications Thridsawan Prasopdee 1 and Wirasak Smitthipong 1,2,3,* 1 Specialized Center of Rubber and Polymer Materials in Agriculture and Industry (RPM), Department of Materials Science, Faculty of Science, Kasetsart University, Chatuchak, Bangkok 10900, Thailand; [email protected] 2 Office of Research Integration on Target-Based Natural Rubber, National Research Council of Thailand (NRCT), Chatuchak, Bangkok 10900, Thailand 3 Office of Natural Rubber Research Program, Thailand Science Research and Innovation (TSRI), Chatuchak, Bangkok 10900, Thailand * Correspondence: [email protected] Received: 24 October 2020; Accepted: 17 November 2020; Published: 19 November 2020 Abstract: Natural rubber foam (NRF) can be prepared from concentrated natural latex, providing specific characteristics such as density, compression strength, compression set, and so on, suitable for making shape-memory products. However, many customers require NRF products with a low compression set. This study aims to develop and prepare NRF to investigate its recoverability and other related characteristics by the addition of charcoal and silica fillers. The results showed that increasing filler loading increases physical and mechanical properties. The recoverability of NRF improves as silica increases, contrary to charcoal loading, due to the higher specific surface area of silica. Thermodynamic aspects showed that increasing filler loading increases the compression force (F) as well as the proportion of internal energy to the compression force (Fu/F). The entropy (S) also increases with increasing filler loading, which is favorable for thermodynamic systems. The activation enthalpy (DHa) of the NRF with silica is higher than the control NRF, which is due to rubber–filler interactions created within the NRF. -
FAQ - Foam Rubber
FAQ - Foam Rubber More information on Foam Rubber https://en.wikipedia.org/wiki/Foam_rubber Foam rubber (also known as cellular, sponge, or expanded rubber) refers to rubber that has been manufactured with a foaming agent to create an air-filled matrix structure. Commercial foam rubbers are generally made of either polyurethane or natural latex. Latex foam rubber, used in mattresses, is well known for its endurance. Polyurethane is a thermosetting polymer that comes from combination of Methyl di-isocyanate and polyethylene and some other chemical additives.[1] What is foam rubber used for? Foam rubber is found in a wide range of applications, from cushioning in automobile seats and furniture to insulation in walls and appliances to soles and heels in footwear. Foams are made by forming gas bubbles in a plastic mixture, with the use of a blowing agent. How do they make foam rubber? How Foam Rubber Is Made. Foam rubber uses a blowing agent, typically a gas or a chemical that produces a gas, to create a mass of small bubbles in a liquid mixture. This mixture may contain polyols, polyisocyanates, water, and additives such as flame retardants, fillers, and colorants. When was foam rubber invented? In 1937 isocyanate based materials were first used for the formation of foam rubbers, after World War II styrene-butadiene rubber replaced many natural types of foam. Foam rubbers have been used commercially for a wide range of applications since around the 1940s. Is foam rubber flammable? A 'foam' is a solid or liquid substance formed with bubbles trapped inside it. -
Recycling Industry
Recycling Industry The Number 1 Solution in Mixing for the Recycling Industry! Date of Sale: 00/00/00 Explore 100’s of custom designed mixer Describe your location by applications for the Recycling Industry. landmark or area of town. 3575 3rd Ave PO Box 286 Marion, IA 52302 319-377-6371 www.marionmixers.com Rubber Mulch Coloring & Drying Case Study Marion Mixers, Inc. Mixing Recycled Tires Into Playground Mulch Mix Recycled Tires Into Playground Mulch A Midwestern tire recycling company chose Marion Mixers to design and build a batch mixer that would coat ground chunks of car tire with a latex colorant. After applying the colorant, the mixer must then dry the materials so the colorant can’t rub-off during the bagging process. The company’s goal was to turn 80,000 scrap car tires per year into upscale landscape mulch for use in playgrounds. The customer brought samples of both the ground rubber (<1¼”) and the colorant to our new test lab. Thoroughly coating the rubber chunks was relatively simple. Drying the rubber took a bit more resolve. The equipment now in operation today includes a mixer, a batch sequencing control panel, a liquid metering system, a forced air drying system and two bulk material conveyors. Chunks of ground rubber are loaded into the mixer from pre-weighed super- sacks. Undiluted, latex paint is volumetrically metered into the mixer. The mixer evenly coats the rubber. A variable speed controller slows the speed of the mixer shaft to avoid scrubbing the latex off the rubber chunks during the drying cycle. -
Acoustic Metasurface-Aided Broadband Noise Reduction in Automobile Induced by Tire-Pavement Interaction
materials Article Acoustic Metasurface-Aided Broadband Noise Reduction in Automobile Induced by Tire-Pavement Interaction Hyeonu Heo 1 , Mathew Sofield 1, Jaehyung Ju 2,* and Arup Neogi 1,* 1 Department of Physics, University of North Texas, P.O. Box 311427, Denton, TX 76203, USA; [email protected] (H.H.); mathewsofi[email protected] (M.S.) 2 UM-SJTU Joint Institute, Shanghai Jiao Tong University, 800 Dongchuan Road, Shanghai 200240, China * Correspondence: [email protected] (J.J.); [email protected] (A.N.) Abstract: The primary noise sources of the vehicle are the engine, exhaust, aeroacoustic noise, and tire–pavement interaction. Noise generated by the first three factors can be reduced by replacing the combustion engine with an electric motor and optimizing aerodynamic design. Currently, a dominant noise within automobiles occurs from the tire–pavement interaction over a speed of 70–80 km/h. Most noise suppression efforts aim to use sound absorbers and cavity resonators to narrow the bandwidth of acoustic frequencies using foams. We demonstrate a technique utilizing acoustic metasurfaces (AMSes) with high reflective characteristics using relatively lightweight materials for noise reduction without any change in mechanical strength or weight of the tire. A simple technique is demonstrated that utilizes acoustic metalayers with high reflective characteristics using relatively lightweight materials for noise reduction without any change in mechanical strength or weight of the tire. The proposed design can significantly reduce the noise arising from tire–pavement interaction over a broadband of acoustic frequencies under 1000 Hz and over a wide range of vehicle speeds using a negative effective dynamic mass density approach. -
Dear Customer
~ Table of Contents ~ ADHESIVES 38-40, 57 MESH TRUCK COVER 17 AUTOMOTIVE ITEMS 57-58 MONOFILAMENT THREAD 36 BOBBINS 34-36 NAILS 25-26 BOLSTERS (POLYFOAM) 11 NEEDLES 53-55 BONDED CUSHION WRAP 13 NO-SAG CLIPS 28 BUNGI / SHOCK CORD 59 NO-SAG SPRINGS 28 BURLAP 17 PANEL BOARDS 57 BUTTONS, DIES & CUTTERS 31-32 PILLOW INSERTS 14 BUTTON MACHINE 31 PLASTIC BAGS 5 BUTTON MOULDS 32 PLI-GRIP (FABRI-FAST) 21 BUTTON TUFTER 32, 50 POLYSCRIM 11 BUTTON TWINE 37 POLYFOAM 9-12 CAMBRIC & NON-WOVEN DUST CLOTH 16 RAZOR BLADES 59 CANE (CHAIR) 30 ROCKER BASES 27 CARPET PAD (AUTOMOTIVE) 14,58 ROCKER SPRINGS 27 CASTERS 42 RUBBER WEBBING 22 CHALK 23 SHEARS 48 CHURCH SEATING FOAM 12 SHOCK CORD / BUNGI 59 COIL SPRINGS 29 SILICONE SPRAY 39 COTTON FELT 13 SKIRT LINING 17 CUSHION FILLING 4, 5 SNAP FASTENERS 46 CUSHION UNITS 27 SPRING REPAIR BRACKET 28 CUSHION WRAP 13 SPRING TWINE 37 DACRON 13 SPRINGS (UPHOLSTERY) 28-29 DENIM (DECK CLOTH) 16 STAPLERS & STAPLES 43-45 DOWNY SOFT PILLOW FILLER 13 STEAMERS 47 DRY-FAST FOAM CUSHIONS 11 STITCHING TWINE 37 DUCK & CANVAS 17 SUPERFOAM 7-8, 12 EK CLIPS & EK NAILS 28 SWIVELS 27 EDGE WIRE & CLIPS 29 T-NUTS 41 EDGE ROLL 29 T-PINS 54 FABRI-FAST (PLI-GRIP) 21 TACKS 26 FOAM 7-12 TACKING STRIP 21 FOAM SAWS 6 THREAD 34-37 GENERAL PURPOSE CLIPS 57 TOOLS 49-52 GIMP SCROLL 20 TORSION SPRINGS 29 GLIDES 41 TUFTING NEEDLE 50 GLUE & CEMENT 38-40, 57 TWINE (BUTTON) 37 GLUE GUN 38 TWIST PINS 54 GROMMETS & DIES 33 UPHOLSTERY PINS 54 HAIRFLEX 14 UPHOLSTERY TEXT BOOK 49 HEADLINER & CLIPS 57 VELCRO TYPE HOOK AND LOOP 24 HOG RINGS (SEAT COVER TIES) 55 VENTILATORS 33 HOG RING PLIERS 56 WEBBING 22 HOOK & LOOP (VELCRO TYPE) 24 WELT CORD 23, 58 LACQUER SPRAY 15 WOVEN CANE 30 LEGS 41 ZIPPERS 18-19 ~ Page 1 ~ ~Company Policies ~ DEAR CUSTOMER: ALL PRICES IN THIS CATALOG ARE NET WHOLESALE. -
INSIDE // Speaker Interview // Conference Program // Product Showcase
Floor Plan // Exhibitor List // Event Information // Exhibitor Spotlight INSIDE // Speaker Interview // Conference Program // Product Showcase 2nd annual March 6 – 8, 2018 Novi, Michigan, USA show previewNorth America’s leading exhibition and conference for the technical foam manufacturing supply chain Exhibitor Spotlight Joe Rapp, President & CEO, Amcor Inc 18 FREE-TO -ATTEND EXHIBITION & Three-day, two-track manufacturing CONFERENCE and applications conference 20 Speaker Interview Dr Hamdy Khalil, Senior Global Director for Advanced Technologies and Innovation, Woodbridge Foam Corporation 26 organized by REGISTER FOR A FREE EXHIBITION AND CONFERENCE PASS WWW.FOAM-EXPO.COM Register for your free pass now | www.foam-expo.com/register 1 welcome contents Floor Plan 3 from the Exhibitor Listings 4 Reasons to Attend 5 event director Product Showcase 7 ello and welcome to Featured Innovation 9 Foam Expo 2018, Product News 15 H the second edition Exhibitor Spotlight 19 of the only exhibition, Conference @ Foam Expo 21 conference and Conference at a Glance – Day 1 23 networking event for the Conference at a Glance – Day 2 24 technical foams industry. Conference at a Glance – Day 3 25 Being held March 6-8 in Novi, MI, Speaker Interview 27 Foam Expo is a free-to-visit event. I invite you to networking meet colleagues from North America, Europe and Essential Contacts 29 Asia who share an interest in – and are leading Useful Information 35 the development and marketing of – the latest innovations in advanced and technical foam Sponsors & Supporters 36 materials and products. About Foam Expo Europe and Sustainable Materials for receptions Foam Expo offers you direct contact with the Transportation Expo 38 engineers and executives who produce materials and products used in automotive, aerospace, construction, medical, packaging, and sports advertisers index and leisure. -
OECD Emission Scenario Document Additives in the Rubber Industry IC 15
OECD Emission Scenario Document Additives in the Rubber Industry IC 15 (‘others’) Exposure Assessment of the environmental Releases of Chemicals in the Rubber Industry 1. version Institute for Environmental Research (INFU) University Dortmund September 1999 2. updated version Umweltbundesamt, comment of NL integrated January 2001 3. updated Version nomenclature adjusted to EUBEES-Document July 2001 4. updated and amended version incorporation of OECD comments 3 March 2003 Umweltbundesamt (Federal Environmental Agency), Berlin, Germany Contents 1 Introduction .......................................................................................................................1 2 Life Cycle Steps and Emission Pathways .........................................................................1 3 Main Processes.................................................................................................................2 3.1 Natural- and synthetic Rubber..................................................................................5 3.1.1 Mastication and creation of mixtures ....................................................................5 3.1.2 Shaping.................................................................................................................6 3.1.3 Vulcanisation / Curing...........................................................................................6 3.2 Latex.........................................................................................................................7 3.3 Rubber-Metal............................................................................................................7 -
MICHELIN TIRES ALLIANCE TIRES, CAMBRIDGE TIRE OFFERS the PROTECTION of a ROAD HAZARD CERTIFICATE at $1.50 PER TIRE
- rPpdCLg Nssqa s3 -Ilpls -- 4bd'cJP . I FRIDAY, DECEMBER 2. 1977 THE TECH PAGE 9 a (The Police Blotter is a report Larceny, it was determined that locked and unoccupied. A subse- rI written by the Campus Patrol on the suspect was already serving a quent search of the dorm under- crimes, incidents; and actions on sentence at the Deer Island House taken by several students turned the MIT canmpU each week.) of Correction. As part of a up the television, which had been prisoners' "pre-release" program secreted elsewhere in the building. * 3 Thief surrenders he had been serving his sentence Vehicles stolen Fast action by a resident of of late at a halfway house in S _ £ :ee Ashdown House resulted recently Boston. With his halfway house A 1972 Ford Torino was stolen in the capture and arrest of a privilege now revoked. he is cur- from its parking place in front of suspect allegedly involved in the rently back at the House of Cor- 18 Vassar Sreet on Tuesday. Also larceny of the student's Seiko rection. Trial, of the Grand taken Tuesday was a 1965 Buick watch valued at well over Sl00.' Larceny charge has been Skylark, taken from the Tang lot. When the student returned to scheduled for mid-December. Taken last Saturday from En- his room in the early evening. he dicott Street was a green 1968 Looking discovered a stranger rifling his Typewriter stolen Dodge Van. personal personal property. On A man previously sought by the seeing the student. the stranger Campus Police appeared Monday for an MBA Program? bolted from the room and ran at a Sloan School area building Headquarters down the hall, dropping the stu- where, by passing himself off dent's watch as he fled.