FINAL 20130814 Dissertation
Total Page:16
File Type:pdf, Size:1020Kb
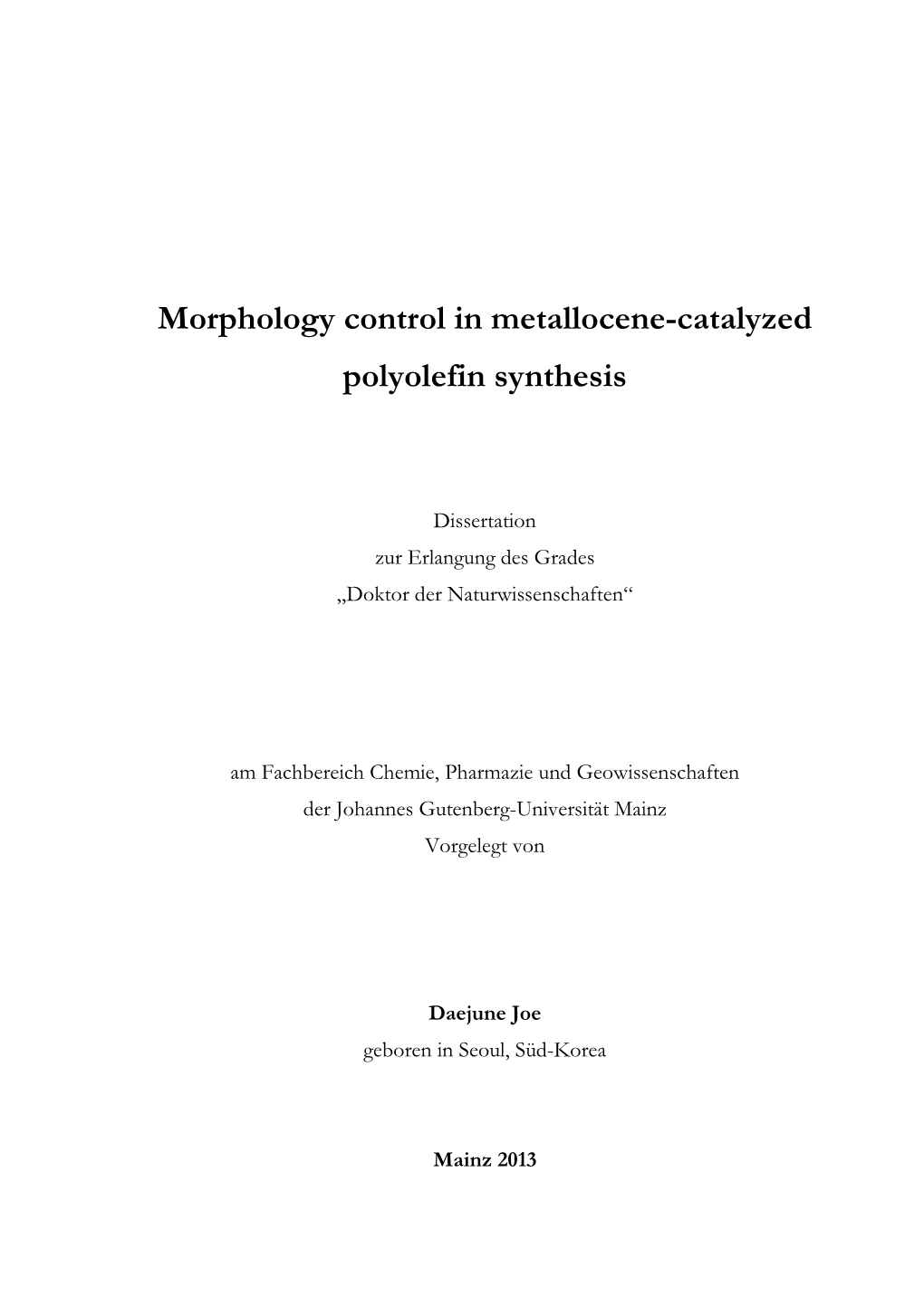
Load more
Recommended publications
-
Linear Alpha-Olefins (681.5030)
IHS Chemical Chemical Economics Handbook Linear alpha-Olefins (681.5030) by Elvira O. Camara Greiner with Yoshio Inoguchi Sample Report from 2010 November 2010 ihs.com/chemical November 2010 LINEAR ALPHA-OLEFINS Olefins 681.5030 B Page 2 The information provided in this publication has been obtained from a variety of sources which SRI Consulting believes to be reliable. SRI Consulting makes no warranties as to the accuracy completeness or correctness of the information in this publication. Consequently SRI Consulting will not be liable for any technical inaccuracies typographical errors or omissions contained in this publication. This publication is provided without warranties of any kind either express or implied including but not limited to implied warranties of merchantability fitness for a particular purpose or non-infringement. IN NO EVENT WILL SRI CONSULTING BE LIABLE FOR ANY INCIDENTAL CONSEQUENTIAL OR INDIRECT DAMAGES (INCLUDING BUT NOT LIMITED TO DAMAGES FOR LOSS OF PROFITS BUSINESS INTERRUPTION OR THE LIKE) ARISING OUT OF THE USE OF THIS PUBLICATION EVEN IF IT WAS NOTIFIED ABOUT THE POSSIBILITY OF SUCH DAMAGES. BECAUSE SOME STATES DO NOT ALLOW THE EXCLUSION OR LIMITATION OF LIABILITY FOR CONSEQUENTIAL OR INCIDENTAL DAMAGES THE ABOVE LIMITATION MAY NOT APPLY TO YOU. IN SUCH STATES SRI CONSULTING’S LIABILITY IS LIMITED TO THE MAXIMUM EXTENT PERMITTED BY SUCH LAW. Certain statements in this publication are projections or other forward-looking statements. Any such statements contained herein are based upon SRI Consulting’s current knowledge and assumptions about future events including without limitation anticipated levels of global demand and supply expected costs trade patterns and general economic political and marketing conditions. -
Recent Developments in Ziegler-Natta Catalysts for Olefin Polymerization and Their Processes
Indian Journal of Technology Vol. 26, February 1988, pp. 53-82 Recent Developments in Ziegler-Natta Catalysts for Olefin Polymerization and Their Processes V CHANDRASEKHAR, P R SRINIVASAN & S SIVARAM* Research Centre, Indian Petrochemicals Corporation Ltd, P.O. Petrochemicals, Baroda 391346, India The chemistry of Ziegler-Natta catalysts in olefin polymerization is reviewed. Factors determining catalyst activity are identified for the current generation of high activity - high selectivity catalysts. These include the nature of transition metal, its oxidation states and the ligands around it, the nature of alkylaluminium compounds, the physical state ofthe catalyst and its dependence on the method of preparation as well as activation of support and the role ofinternal and external donors. The effect of reaction parameters on catalyst performance as well as effect of nature of catalysts on polymer properties such as molecular weight, molecular weight distribution and stereoregularity are discussed. Current developments in soluble titanium! zirconium, vanadium and magnesium-titanium catalysts are reviewed. Different classes of industrial processes for production of polyethylene and polypropylene, namely slurry phase, gas phase and solution processes are discussed, The nature of contemporary catalysts is exemplified by selected patents from current literature, The various reactor types for polyolefins and salient reactor design aspects are discussed, The dependence of polymer properties on reactor design 11:1 well as kinetic modelling and simulation of polyolefin processes are briefly reviewed. I. Introduction made the dramatic discovery that not only propylene Polyolefins are a group of bulk commodity polymers could be polymerized to high molecular weight pol comprising of polyethylenes, polypropylene, poly ymers by Ziegler catalysts but the polymer so pro (butene-I) and various copolymers ofethylene, propy duced had a highly stereo regular structure (termed lene and higher alpha olefins. -
Surfactant Book 2007
Surfactants: Strategic Personal Care Ingredients Anthony J. O’Lenick, Jr. ISBN 978-1-932633-96-2 Copyright 2014, by Anthony J. O'Lenick, Jr. This book is out of print. The copyright has reverted back to the author. It is being made available free of charge in electronic version. Please feel free to use it, download it or cite it in other publications. Allured Publishing Corporation 362 South Schmale Road, Carol Stream, IL 60188-2787 USA Tel: 630/653-2155 Fax: 630/653-2192 e-mail: [email protected] Table of Contents Preface................................................................................................................... vii About the Author ................................................................................................. viii Acknowledgments .................................................................................................. ix Chapter 1: Raw Materials for Surfactant Preparation Background ............................................................................................................. 1 Triglycerides............................................................................................................ 4 Methyl Esters ........................................................................................................ 20 Fatty Acids ............................................................................................................ 20 Natural Acids .................................................................................................... 20 Guerbet -
United States Patent (19) 11 Patent Number: 5,807,502 Wollenweber Et Al
USOO5807502A United States Patent (19) 11 Patent Number: 5,807,502 Wollenweber et al. (45) Date of Patent: Sep. 15, 1998 54 AQUEOUS FATTY ALCOHOL DISPERSIONS 4,396,524 8/1983 Hempel et al. ......................... 252/321 4,549,002 10/1985 Hoefer et al. ... - - - - - 526/209 4,600,523 7/1986 Priorr et al. ............................ 252/321 75 Inventors: Horst-Werner Wollenweber, Duesseldorf, Rainer Hoefer, Neuss; 4,976,888 12/1990 De Clercq et al. ..................... 252/358 Heinz-Guenther Schulte, Muehlheim, 5,147,412 9/1992 Klinksiek et al. .................... 23/293 R all of Germany 5,346,973 9/1994 Feustel et al. .......................... 526/209 FOREIGN PATENT DOCUMENTS 73 Assignee: Henkel Kommanditgesellschaft Auf Aktien, Duesseldorf, Germany 1297 755 3/1992 Canada. 230 977 8/1987 European Pat. Off.. 21 Appl. No.: 765,752 399 266 11/1990 European Pat. Off.. 11 90 927 4/1965 Germany. 22 PCT Filed: Jun. 12, 1995 29 OO O30 7/1980 Germany. 30 39 393 4/1981 Germany. 86 PCT No.: PCT/EP95/02260 30 O1 387 7/1981 Germany. 36 01929 7/1987 Germany. S371 Date: Dec. 20, 1996 40 06 391 9/1991 Germany. S 102(e) Date: Dec. 20, 1996 OTHER PUBLICATIONS 87 PCT Pub. No.: WO95/35143 Database WPI, Week 8323 London: Derwent Publications Ltd., AN-83–55096K, Class A97, JP58–072000 A (Daiichi PCT Pub. Date: Dec. 28, 1995 Kogyo Seiyaku), abstract. 30 Foreign Application Priority Data Primary Examiner Richard D. Lovering Jun. 20, 1994 DE Germany .......................... 44 21 270.4 ASSistant Examiner-Daniel S. Metzmaier (51) Int. Cl. ............................................... B01D 19/04 Attorney, Agent, or Firm-Ernest G. -
JAIST Repository
JAIST Repository https://dspace.jaist.ac.jp/ エチレン重合における新規均一系シルセスシロキサン Title 担体型クロム触媒の設計と高効率活性化剤の検討 Author(s) Zeng, Yanning Citation Issue Date 2015-03 Type Thesis or Dissertation Text version ETD URL http://hdl.handle.net/10119/12770 Rights Supervisor:寺野 稔, マテリアルサイエンス研究科, Description 博士 Japan Advanced Institute of Science and Technology Design of novel homogeneous chromium-based catalyst system using silsequioxane support and high-efficiency activator for ethylene polymerization ZENG YANNING Japan Advanced Institute of Science and Technology Design of novel homogeneous chromium-based catalyst system using silsequioxane support and high-efficiency activator for ethylene polymerization by ZENG YANNING Submitted to Japan Advanced Institute of Science and Technology In partial fulfillment of the requirements For the degree of Doctor of Philosophy Supervisor: Professor Dr. Minoru Terano School of Materials Science Japan Advanced Institute of Science and Technology March 2015 2 Referee-in-chief: Professor Dr. Minoru Terano Japan Advanced Institute of Science and Technology Referees: Professor Dr. Masayuki Yamaguchi Japan Advanced Institute of Science and Technology Professor Dr. Kohki Ebitani Japan Advanced Institute of Science and Technology Associate Professor Dr. Toshiaki Taniike Japan Advanced Institute of Science and Technology Professor Dr. Kotohiro Nomura Tokyo Metropolitan University 3 Preface The present dissertation is the result of the studies under the direction of Professor Dr. Minoru Terano during 2012-2015. The purpose of this dissertation is to shed new light for precise control of polyethylene structure with designed Phillips-type catalysts. The first chapter is a general introduction according to the object of this research. Chapter 2 describes the design of novel homogeneous Phillips catalyst using the model of trivalent chromium site and support. -
Hydrogenation of Methyl Laurate to Produce Lauryl Alcohol Over Cu/Zno/Al O with Methanol As the Solvent and Hydrogen Source*
Pure Appl. Chem., Vol. 84, No. 3, pp. 779–788, 2012. http://dx.doi.org/10.1351/PAC-CON-11-06-09 © 2011 IUPAC, Publication date (Web): 5 November 2011 Hydrogenation of methyl laurate to produce lauryl alcohol over Cu/ZnO/Al2O3 with methanol as the solvent and hydrogen source* Shuguang Liang, Huizhen Liu, Jinli Liu, Weitao Wang, Tao Jiang‡, Zhaofu Zhang, and Buxing Han‡ Beijing National Laboratory for Molecular Sciences, Institute of Chemistry, Chinese Academy of Sciences, Beijing 100190, China Abstract: Hydrogenation of methyl laurate was conducted over a Cu/ZnO/Al2O3 catalyst, using methanol as the solvent and hydrogen source, to give lauryl alcohol. In this process, the solvent underwent partial decomposition in contact with the catalyst to generate hydrogen, which served as the hydrogenation agent. The effect of different factors on the reaction was examined, to optimize production of lauryl alcohol with high conversion efficiency and selec- tivity. Use of methanol as the solvent not only favored the reaction, but also suppressed a side reaction involving transesterification between methyl laurate and lauryl alcohol. Under opti- mal reaction conditions, 91.8 % conversion of methyl laurate and 88.8 % yield of lauryl alcohol could be achieved. Keywords: Cu/ZnO/Al2O3; heterogeneous catalysis; hydrogenation; lauryl alcohol; methanol; methyl laurate; supercritical fluids. INTRODUCTION Fatty alcohols derived from renewable resources, such as plant oils and animal oils, have found their numerous applications in industries, mostly used as raw materials for the synthesis of surfactants or plasticizers [1,2]. Especially, the fatty-alcohol-based surfactants have gained growing significance in the detergent market in the past few years, owing to their excellent washing properties and superior biodegradability compared to conventional detergents made from petrochemicals [3]. -
Investigations Into Alkene Hydration and Alkene Oxidation Catalysis
Louisiana State University LSU Digital Commons LSU Doctoral Dissertations Graduate School 2013 Investigations into alkene hydration and alkene oxidation catalysis William Schreiter Louisiana State University and Agricultural and Mechanical College, [email protected] Follow this and additional works at: https://digitalcommons.lsu.edu/gradschool_dissertations Part of the Chemistry Commons Recommended Citation Schreiter, William, "Investigations into alkene hydration and alkene oxidation catalysis" (2013). LSU Doctoral Dissertations. 473. https://digitalcommons.lsu.edu/gradschool_dissertations/473 This Dissertation is brought to you for free and open access by the Graduate School at LSU Digital Commons. It has been accepted for inclusion in LSU Doctoral Dissertations by an authorized graduate school editor of LSU Digital Commons. For more information, please [email protected]. INVESTIGATIONS INTO ALKENE HYDRATION AND ALKENE OXIDATION CATALYSIS A Dissertation Submitted to the Graduate Faculty of the Louisiana State University and Agricultural and Mechanical College in partial fulfillment of the requirements for the degree of Doctor of Philosophy In The Department of Chemistry by William James Schreiter B. A., Lawrence University, 2004 May 2013 TABLE OF CONTENTS ABSTRACT .......................................................................................................................................v CHAPTER 1. INTRODUCTION .....................................................................................................1 1.1 Alkene -
United States Patent Office Patented Apr
2,979,495 United States Patent Office Patented Apr. 11, 1961 1. 2 a method whereby the used solvent or catalyst suspending agent in the Ziegler process for the polymerization of 2,979,495 polymerizable hydrocarbons is recovered in a purified ETHYLENE POLYMERIZATION PROCESS IN state for recycling to the process. WHICH THE KEROSENE SUSPENDING ME. 5 Other objects and advantages of the invention will DUM ES RECOVERED become apparent from the following description and ap pended claims. James V. Cavender, Jr., Texas City, Tex., assignor to According to the invention, solvent or catalyst suspend Monsantoporation of Chemical Delaware Company, St. Louis, Mo., a cor ing agent suitable for recycle to the catalyst preparation O step in the Ziegler process is prepared by subjecting used No Drawing. Fied May 14, 1956, Ser. No. 584,874 solvent or catalyst suspending agent to washing or scrub 2 Claims. (C. 260-94.9) bing with concentrated sulfuric acid. The acid-washed solvent can then be separated from the acid, washed with alkali to remove any residual traces of acid, dried, and This invention relates to the polymerization of hydro 5 distilled, or handled in any other conventional manner carbons. More particularly, it relates to an improvement to yield a product containing essentially no contaminants the process for the production of Ziegler-type polymers, so that it performs in a manner comparable to the fresh relating specifically to a method for cleaning up the cata solvent when employed in the polymerization reaction. lyst Suspending agent employed to render it suitable for The following example is presented as illustrative of recycle purposes. -
(12) United States Patent (10) Patent No.: US 6,534,550 B1 Walterick, Jr
USOO653455OB1 (12) United States Patent (10) Patent No.: US 6,534,550 B1 Walterick, Jr. (45) Date of Patent: Mar. 18, 2003 (54) FOAM CONTROL COMPOSITION AND 5,700,351 A * 12/1997 Schuhmacher et al. ..... 516/126 METHOD FOR CONTROLLING FOAM IN 5,807,502 A 9/1998 Wollenweber et al. ........ 516/18 AQUEOUS SYSTEMS 5,866,041 A 2/1999 Svarz et al. .................. 516/11 5,874,017 A 2/1999 Palmer et al. ................ 516/13 (76) Inventor: Gerald C. Walterick, Jr., 24 FOREIGN PATENT DOCUMENTS Farmbrook Dr, Levittown, PA (US) 19055 DE 197 O2 846 A1 * 7/1998 WO 96/25215 * 8/1996 (*) Notice: Subject to any disclaimer, the term of this patent is extended or adjusted under 35 OTHER PUBLICATIONS U.S.C. 154(b) by 0 days. Hawley's Condensed Chemical Dictionary, Eleventh Edi tion, (Van Nostrand Reinhold Company, NY, NY, copyright (21) Appl. No.: 09/537,104 1987) pp. 300 and 1147, Oct. 1989.* WPI on EAST, week 199836, London: Derwent Publica (22) Filed: Mar. 29, 2000 tions, Ltd., AN 1998–415057, Class A25, DE 19702846 A1, (51) Int. Cl." .......................... B01D 19/04; D21H 23/00 (HENKEL KGAA) abstract, 1998.* (52) U.S. Cl. ......................... 516777; 516/126; 516/132; WPI on EAST, week 199918, London: Derwent Publica 516/133; 516/134; 162/158; 162/179 tions Ltd., AN 1996-393170, Class A25, WO9625215 A1, (58) Field of Search ................................. 516/126, 132, (HENKEL KGAA) abstract, 1999.* 516/77, 133, 134; 162/158, 179 * cited by examiner (56) References Cited Primary Examiner Daniel S. Metzmaier U.S. -
I Finai Summary
NASA CONTRACTOR NASA CR-1104 REPORT I Finai Summary , NATIONAL AERONAUTICS ,4ND SPACE ADMINISTRATION WASHINGTON, D. C. JULY 1968 NASA CR-1104 STUDY OF METHODS FOR CHEMICAL SYNTHESIS OF EDIBLE FATTY ACIDS AND LIPIDS Final Summary Edited by John W. Frankenfeld Distribution of this report is provided in the interest of information exchange. Responsibility for the contents resides in the author or organization that prepared it. Prepared under Contract No. NAS 2-3708 by ESSO RESEARCH AND ENGINEERING COMPANY Linden, N.J. for Ames Research Center NATIONAL AERONAUTICS AND SPACE ADMINISTRATION For sale by the Clearinghouse for Federal Scientific and Technical Information Springfield, Virginia 22151 - CFSTI price $3.00 PRECEDING PAGE BLANK NOT FILMED. I* The authors wish to express their appreciation for the assistance V PRECEDING PAGE BLANK NOT FILMED. CONTENTS Page LIST OF FIGURES ix LIST OF TABLES X SUMMARY 1 INTRODUCTION 2 Human Energy Requirements - Advantages of Fats 2 Statement of the Problem 3 Approach - Assumptions 4 TECHNICAL Di SCiiSSION 6 Historical - The German Process 6 REDUCTIVE POLYMERIZATION OF CARBON MONOXIDE 10 The Fischer-Tropsch Synthesis 10 Wax Cracking and Oxidative Dehydrogenation 19 The Ziegler Reaction 20 Telomerization of Ethylene and Acetylene 25 SYNTHESIS OF ETHnENE AND CONVERSION OF Cog TO CO 26 Ethylene y& Methane and Acetylene 26 Reduction of Carbon Dioxide to Carbon Monoxide 29 Conversion of Carbon Monoxide to Ethylene 31 CONVERSION OF HYDROCARBONS TO ACIDS 34 Oxidation of Paraffins 34 Oxidation of Olefins 34 Ozonolysis -
EU Biorefinery Outlook to 2030
EU Biorefinery Outlook to 2030 Studies to support R&I policy in the area of bio-based products and services FINAL PRESENTATION AND MEETING EU Biorefinery Outlook to 2030 Consortium partners Ausilio Bauen Rene van Ree Patrick Reumerman Philipp von Raffaella Moreschi Project Director WP 2 & 4 lead Bothmer Lesly Garcia Chavez Stakeholder Niccolò Bertuzzi Richard Platt WP 1 lead Kaisa Vikla Engagement lead WP 7 lead Project Manager Iris Vural Gursel Philipp von Alice De Ferrari Cecile Geier WP 3 lead Bothmer and Martin Behrens Ilaria Abbondanti Jo Howes Bert Annevelink WP 5 demand lead Sitta Yamini Valerie Sartorius Panchaksharam Lee Roberts EU Biorefinery Outlook to 2030 Contents 1. Introduction 2. Stakeholder engagement 3. EU policy context 4. Biorefinery classification and definition of pathways 5. Current deployment of biorefineries 6. Barriers to the deployment of biorefineries 7. Market prospects for biorefineries - demand 8. Deployment scenarios of EU biorefineries to 2030 9. Roadmaps 10.Outlook for deployment 11.Conclusions EU Biorefinery Outlook to 2030 3 Introduction Structure and objectives of the study EU Biorefinery Outlook to 2030 4 This project is part of three studies for The Directorate- General for Research and Innovation (DG RTD) The overall objective is to provide a range of new information and analysis that will help identify future policy directions, emerging technologies, societal demands, challenges and opportunities in the fields of the Bioeconomy related to bio-based products and the bio-based innovation. Hence, -
United States Patent Office Patented Nov
2,959,567 United States Patent Office Patented Nov. 8, 1960 2 include, among other compounds, a variety of alumi num trialkyls such as aluminum trimethyl, aluminum tri 2,959,567 ethyl, aluminum tripropyl, aluminum triisobutyl and POLYETHYLENE STABILIZED WITH TETRA higher aluminum trialkyls as well as dialkyl aluminum 5 halides, dialkyl aluminum hydrides and dialkyl alumi AS9, SUBSTITUTED ETHYLENE D num alkoxides. Salts of metals selected from the group Charles R. Pfeifer, Midland, Mich., assignor to The Dow consisting of titanium, zirconium, vanadium, uranium, Chemical Company, Midland, Mich., a corporation of thorium and chromium are preferably employed as the Delaware group IV-B, V-B and VI-B metallic compounds in the 10 catalyst, although salts of the remaining metals in these No Drawing. Filed Jan. 26, 1956, Ser. No. 561,685 sub-groups may also be employed. Compounds of these 4 Claims. (C. 260-45.9) metals including their halogenides, oxyhalogenides, com plex halogenides, freshly precipitated oxides and hydrox ides and such organic compounds as alcoholates, acetates, This invention relates to improved, non-corrosive com 5 benzoates, acetyl acetonates and the like may be used in positions comprised of select corrosion-inhibiting agents the catalyst. and polymerized olefinic and other ethylenically unsat A particularly active catalyst mixture for the Zeigler urated materials which have been prepared with certain process may be obtained by mixing a titanium or zir catalytic metal compounds. In particular it relates to conium compound, such as a tetrachloride, oxychloride compositions of this nature which are not promotive of 20 or acetyl acetonate with an aluminum trialkyl or a dialkyl oxidative corrosion of metals and other materials of con aluminum compound.