EXPERIMENTAL INVESTIGATION of WING-FUSELAGE INTEGRATION GEOMETRIES INCLUDING CFD ANALYSES Jirapat Su
Total Page:16
File Type:pdf, Size:1020Kb
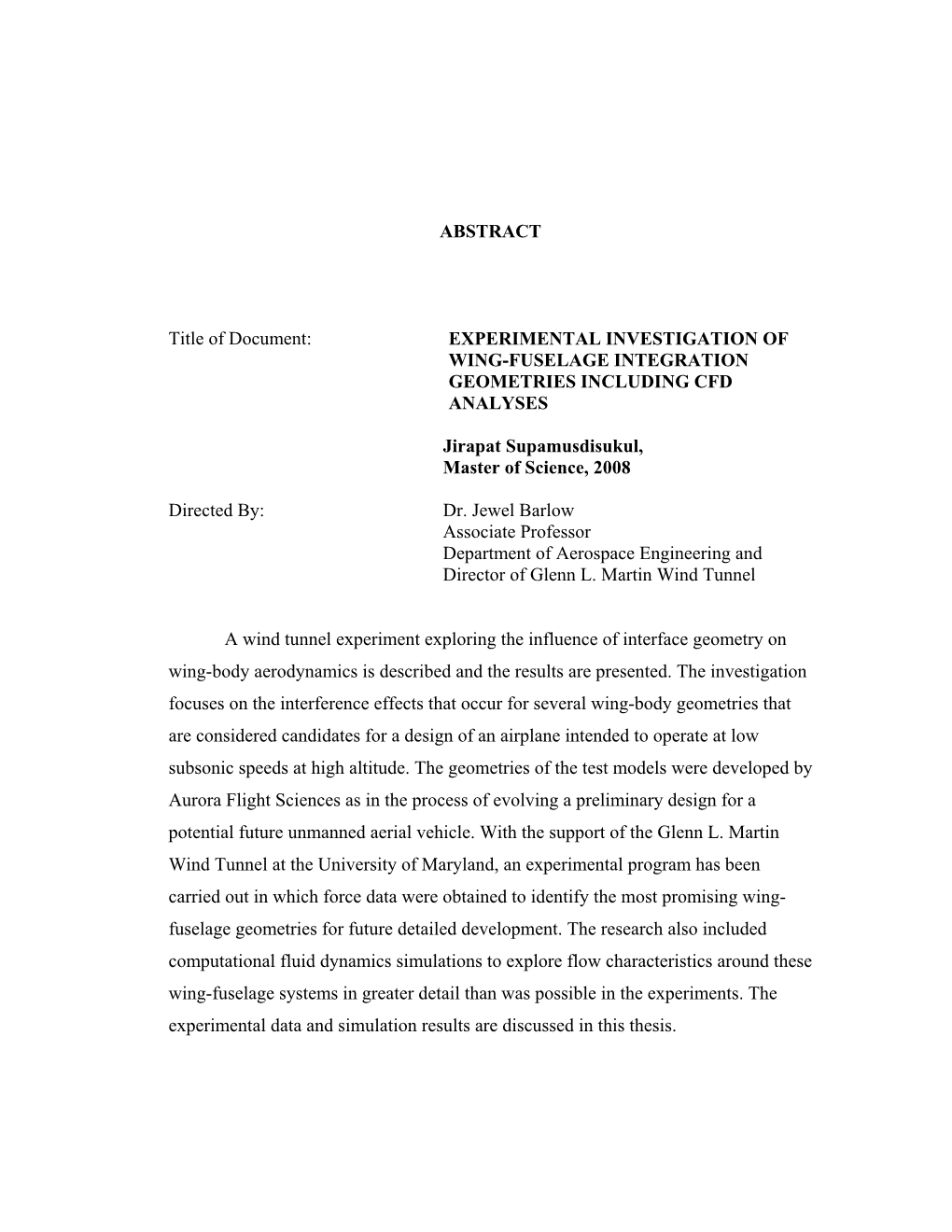
Load more
Recommended publications
-
Flying Wing Concept for Medium Size Airplane
ICAS 2002 CONGRESS FLYING WING CONCEPT FOR MEDIUM SIZE AIRPLANE Tjoetjoek Eko Pambagjo*, Kazuhiro Nakahashi†, Kisa Matsushima‡ Department of Aeronautics and Space Engineering Tohoku University, Japan Keywords: blended-wing-body, inverse design Abstract The flying wing is regarded as an alternate This paper describes a study on an alternate configuration to reduce drag and structural configuration for medium size airplane. weight. Since flying wing possesses no fuselage Blended-Wing-Body concept, which basically is it may have smaller wetted area than the a flying wing configuration, is applied to conventional airplane. In the conventional airplane for up to 224 passengers. airplane the primary function of the wing is to An aerodynamic design tools system is produce the lift force. In the flying wing proposed to realize such configuration. The configuration the wing has to carry the payload design tools comprise of Takanashi’s inverse and provides the necessary stability and control method, constrained target pressure as well as produce the lift. The fuselage has to specification method and RAPID method. The create lift without much penalty on the drag. At study shows that the combination of those three the same time the fuselage has to keep the cabin design methods works well. size comfortable for passengers. In the past years several flying wings have been designed and flown successfully. The 1 Introduction Horten, Northrop bombers and AVRO are The trend of airplane concept changes among of those examples. However the from time to time. Speed, size and range are application of the flying wing concepts were so among of the design parameters. -
CANARD.WING LIFT INTERFERENCE RELATED to MANEUVERING AIRCRAFT at SUBSONIC SPEEDS by Blair B
https://ntrs.nasa.gov/search.jsp?R=19740003706 2020-03-23T12:22:11+00:00Z NASA TECHNICAL NASA TM X-2897 MEMORANDUM CO CN| I X CANARD.WING LIFT INTERFERENCE RELATED TO MANEUVERING AIRCRAFT AT SUBSONIC SPEEDS by Blair B. Gloss and Linwood W. McKmney Langley Research Center Hampton, Va. 23665 NATIONAL AERONAUTICS AND SPACE ADMINISTRATION • WASHINGTON, D. C. • DECEMBER 1973 1.. Report No. 2. Government Accession No. 3. Recipient's Catalog No. NASA TM X-2897 4. Title and Subtitle 5. Report Date CANARD-WING LIFT INTERFERENCE RELATED TO December 1973 MANEUVERING AIRCRAFT AT SUBSONIC SPEEDS 6. Performing Organization Code 7. Author(s) 8. Performing Organization Report No. L-9096 Blair B. Gloss and Linwood W. McKinney 10. Work Unit No. 9. Performing Organization Name and Address • 760-67-01-01 NASA Langley Research Center 11. Contract or Grant No. Hampton, Va. 23665 13. Type of Report and Period Covered 12. Sponsoring Agency Name and Address Technical Memorandum National Aeronautics and Space Administration 14. Sponsoring Agency Code Washington , D . C . 20546 15. Supplementary Notes 16. Abstract An investigation was conducted at Mach numbers of 0.7 and 0.9 to determine the lift interference effect of canard location on wing planforms typical of maneuvering fighter con- figurations. The canard had an exposed area of 16.0 percent of the wing reference area and was located in the plane of the wing or in a position 18.5 percent of the wing mean geometric chord above the wing plane. In addition, the canard could be located at two longitudinal stations. -
Evolving the Oblique Wing
NASA AERONAUTICS BOOK SERIES A I 3 A 1 A 0 2 H D IS R T A O W RY T A Bruce I. Larrimer MANUSCRIP . Bruce I. Larrimer Library of Congress Cataloging-in-Publication Data Larrimer, Bruce I. Thinking obliquely : Robert T. Jones, the Oblique Wing, NASA's AD-1 Demonstrator, and its legacy / Bruce I. Larrimer. pages cm Includes bibliographical references. 1. Oblique wing airplanes--Research--United States--History--20th century. 2. Research aircraft--United States--History--20th century. 3. United States. National Aeronautics and Space Administration-- History--20th century. 4. Jones, Robert T. (Robert Thomas), 1910- 1999. I. Title. TL673.O23L37 2013 629.134'32--dc23 2013004084 Copyright © 2013 by the National Aeronautics and Space Administration. The opinions expressed in this volume are those of the authors and do not necessarily reflect the official positions of the United States Government or of the National Aeronautics and Space Administration. This publication is available as a free download at http://www.nasa.gov/ebooks. Introduction v Chapter 1: American Genius: R.T. Jones’s Path to the Oblique Wing .......... ....1 Chapter 2: Evolving the Oblique Wing ............................................................ 41 Chapter 3: Design and Fabrication of the AD-1 Research Aircraft ................75 Chapter 4: Flight Testing and Evaluation of the AD-1 ................................... 101 Chapter 5: Beyond the AD-1: The F-8 Oblique Wing Research Aircraft ....... 143 Chapter 6: Subsequent Oblique-Wing Plans and Proposals ....................... 183 Appendices Appendix 1: Physical Characteristics of the Ames-Dryden AD-1 OWRA 215 Appendix 2: Detailed Description of the Ames-Dryden AD-1 OWRA 217 Appendix 3: Flight Log Summary for the Ames-Dryden AD-1 OWRA 221 Acknowledgments 230 Selected Bibliography 231 About the Author 247 Index 249 iii This time-lapse photograph shows three of the various sweep positions that the AD-1's unique oblique wing could assume. -
Aircraft Design Final Design Review
Group 7 AIRCRAFT DESIGN FINAL DESIGN REVIEW March 20, 2013 Sagun Bajracharya Roger Francis Tim Tianhang Teng Guang Wei Yu Abstract This document summarizes the work that group 7 has done insofar regarding the design of a radio-controlled plane with respect to the requirements that were put forward by the course (AER406, 2013). This report follows the same format as the presentation where we inform the reader where the current design is, how the group progressed towards that design and how we started. This report also summarizes a number of the important parameters required for a conceptual design like the cargo type & amount,Wing aspect ratio, Optimum Airfoil lift(CL), Thrust to weight ratio & Takeoff distance. In addition, this report presents the plane's wing and tail design, stability analysis and a mass breakdown. The report finally ends with pictures of the current design. 2 Contents 1 Design Overview6 2 Required Parameters6 3 Trade Studies6 3.1 Wing Design....................................... 7 3.2 Wing Configuration................................... 8 3.3 Fuselage Design..................................... 8 3.4 Tail Design ....................................... 9 3.5 Overall Selection .................................... 10 3.6 Parameters from Reference Designs.......................... 11 4 Flight Score Optimization 11 4.1 Cargo Selection..................................... 11 4.2 Propeller Selection ................................... 12 4.3 Flight Parameter Selection............................... 13 5 Wing Design 16 5.1 -
Performance Enhancement by Wing Sweep for High-Speed Dynamic Soaring
aerospace Article Performance Enhancement by Wing Sweep for High-Speed Dynamic Soaring Gottfried Sachs *, Benedikt Grüter and Haichao Hong Department of Aerospace and Geodesy, Institute of Flight System Dynamics, Technical University of Munich, Boltzmannstraße 15, 85748 Munich, Germany; [email protected] (B.G.); [email protected] (H.H.) * Correspondence: [email protected] Abstract: Dynamic soaring is a flight mode that uniquely enables high speeds without an engine. This is possible in a horizontal shear wind that comprises a thin layer and a large wind speed. It is shown that the speeds reachable by modern gliders approach the upper subsonic Mach number region where compressibility effects become significant, with the result that the compressibility-related drag rise yields a limitation for the achievable maximum speed. To overcome this limitation, wing sweep is considered an appropriate means. The effect of wing sweep on the relevant aerodynamic characteristics for glider type wings is addressed. A 3-degrees-of-freedom dynamics model and an energy-based model of the vehicle are developed in order to solve the maximum-speed problem with regard to the effect of the compressibility-related drag rise. Analytic solutions are derived so that generally valid results are achieved concerning the effects of wing sweep on the speed performance. Thus, it is shown that the maximum speed achievable with swept wing configurations can be increased. The improvement is small for sweep angles up to around 15 deg and shows a progressive increase thereafter. As a result, wing sweep has potential for enhancing the maximum- speed performance in high-speed dynamic soaring. -
Conceptual Design of a Strut-Braced Wing Configuration
22 June2017 Aviation on Sustainable UTIAS NationalColloquium Bombardier Aerospace Engineering,Product Development Advanced Design Specialist Engineering Graham Potter Configuration Strut-Braceda Wing Conceptual Design of PRIVATE AND CONFIDENTIAL © Bombardier Inc. or its subsidiaries. All rights reserved. Environmentally Focused Aircraft Study Environmentally Focused 2 § § § Aircraft requirements: Technology assumption: Environmentally Focused Aircraft (EFA) study objective: § § § EIS Based on existing Bombardier products Consistent with EIS 2030-2035 by evaluating alternative long-rangeSignificantly business jet reduce and environmental commercial impact aircraft configurations (emissions, local air quality and community noise) Entry-Into-Service Business Jet Commercial Aircraft PRIVATE AND CONFIDENTIAL © Bombardier Inc. or its subsidiaries. All rights reserved. The History of the Strut-Braced Wing 3 Hurel-Dubois HD.31 Hurel-Dubois Shorts 360 Hurel-Dubois HD.31 Cessna Caravan PRIVATE AND CONFIDENTIAL © Bombardier Inc. or its subsidiaries. All rights reserved. Recent Research Efforts Research Recent 4 Boeing/NASA Boeing/NASA Virginia Tech Virginia ONERA PRIVATE AND CONFIDENTIAL © Bombardier Inc. or its subsidiaries. All rights reserved. WhyStrut-Braced a Configuration? 5 § § § § configuration equivalent conventional burn savings compared to Other studies suggest 5-10% fuel induced drag ratios with large reductionsin to Allows optimization higher aspect given aspect ratio allows reducedwingweightata Strut-braced configuration wing and drag compromiseweight between wing Optimum aspect ratio wing is a Wing Weight Aspect Ratio PRIVATE AND CONFIDENTIAL © Bombardier Inc. or its subsidiaries. All rights reserved. WhyStrut-Braced a Configuration? 6 § Start witha geometryconventional wing PRIVATE AND CONFIDENTIAL © Bombardier Inc. or its subsidiaries. All rights reserved. WhyStrut-Braced a Configuration? 7 § § Add astrut Start witha geometryconventional wing WING WEIGHT FUEL BURN PROFILE DRAG PRIVATE AND CONFIDENTIAL © Bombardier Inc. -
Research on Combination of Swing Wing with Canard and Tail Used in Fighter Aircraft
International Journal of Recent Technology and Engineering (IJRTE) ISSN: 2277-3878, Volume-8, Issue-2S3, July 2019 Research on Combination of Swing Wing with Canard and Tail used in Fighter Aircraft Praveen babu, Swathi P Shetty, Kavya G Achar, Steve JohnsonLobo, Lokesh K S, Jagadeesh Abstract: The present work discloses the new design of a To balance the aircraft, either fuel must be pumped to move fighter aircraft. Better performance of a fighter in the combat as the centre of gravity or the tail must provide a tremendous well in its ground activities is the main vision of our work. It is down load[1]. concentrating on the aircraft short distance take off and landing, Variable sweep aircraft typically exhibit a greater stalling controlling, as well as different maneuverings of the aircraft. Many fighter aircraft are having its own working rearward shift in aerodynamic center from subsonic to parameters and configurations. Every aircraft shown its own supersonic speed than fixed wing plane form. The first characteristics in flight like maneuverings, stalling etc.The major variable sweep design X-5 research vehicle minimized problem of them is prohibiting some of these characteristics in aerodynamic travel by employing a rail carriage system to some angle of attack. So to control we have implemented some provide forward translation to the wing at the swept back modifications. To achieve all these characteristics, we have position. The XF101-1 aircraft, the second variable sweep selected the combination of swing wing with canard and tail configuration. By using this technology we can increase the design, had a forward translation capability that was flight ability to its maximum. -
Airplane Design(Aerodynamic) Prof. EG Tulapurkara Chapter-1
Airplane design(Aerodynamic) Prof. E.G. Tulapurkara Chapter-1 Chapter 1 Lecture 2 Introduction - 2 Topics 1.5 Classification of airplanes according to configuration 1.5.1 Classification of airplanes based on wing configuration 1.5.2 Classification of airplanes based on fuselage 1.5.3 Classification of airplanes based on horizontal stabilizer 1.5.4 Classification of airplanes based on number of engines and their location 1.6 Factors affecting the configuration 1.6.1 Aerodynamic considerations – drag, lift and interference 1.6.2 Low structural weight 1.6.3 Layout peculiarities 1.6.4 Manufacturing processes 1.6.5 Cost and operational economics - Direct operating cost (DOC) and Indirect operating cost (IOC) 1.6.6 Interaction of various factors 1.7 Brief historical background 1.7.1 Early developments 1.5 Classification of airplanes according to configuration This classification is based on the following features of the configuration. a) Shape, number and position of wing. b) Type of fuselage. c) Location of horizontal tail. d) Location and number of engines. Dept. of Aerospace Engg., Indian Institute of Technology, Madras 1 Airplane design(Aerodynamic) Prof. E.G. Tulapurkara Chapter-1 The different types of configurations are shown in Fig.1.2. As an exercise the student is advised to study, at this stage, various types of airplanes from Jane's all the world aircraft (Ref.1.21). Fig.1.2 Types of airplanes(cont.) Dept. of Aerospace Engg., Indian Institute of Technology, Madras 2 Airplane design(Aerodynamic) Prof. E.G. Tulapurkara Chapter-1 Fig.1.2 Types of airplanes 1.5.1 Classification of airplanes based on wing configuration Early airplanes had two or more wings e.g. -
Its Advantages Included Clean Wing Airflow Without Disruption by Nacelles Or Pylons and Decreased Cabin Noise
Design of an innovative stall recovery device J.A. Stoop FO4873 Lund University Sweden, Delft University of Technology The Netherlands J.L. de Kroes Hilversum, The Netherlands John Stoop graduated in 1976 as an aerospace engineer at Delft University of Technology and did his PhD on the issue of 'Safety in the Design Process'. He is a part-time Associate Professor at the Faculty of Aerospace Engineering of the Delft University of Technology and is a guest professor at Lund University Sweden. Stoop has completed courses in accident investigation in the Netherlands, USA and Canada. Stoop is Affiliated Member of ISASI, and has been actively involved in accident investigations in the road and has played a role as safety analyst in maritime, railway and aviation accidents. Abstract Stall has been an inherent hazard since the beginning of flying. Despite a very successful stall mitigation strategy and a wide variety of solutions, stall as a phenomenon still exists. This contribution explores the nature and dynamics of stall as a loss of pitch control phenomenon and the remedies that have been developed over time. This contribution proposes the introduction of a stall shield device. A multi-actor collaborative approach is suggested for the development of such a device, including the technological, control and simulation and operational aspects of the design by involving designers, pilots and investigators in its development. The introduction of the stall shield concept may serve as an example of how serendipity through accident investigation may disclose critical systemic and knowledge deficiencies in aircraft stability and control, leading to systems resilience by innovative solutions. -
Box Wing Fundamentals – an Aircraft Design Perspective
Deutscher Luft- und Raumfahrtkongress 2011 DocumentID: 241353 BOX WING FUNDAMENTALS – AN AIRCRAFT DESIGN PERSPECTIVE D. Schiktanz, D. Scholz Hamburg University of Applied Sciences Aero – Aircraft Design and Systems Group Berliner Tor 9, 20099 Hamburg, Germany Abstract A systematic and general investigation about box wing aircraft is conducted, including aerodynamic and performance characteristics. The design of a promising medium range box wing aircraft based on the Airbus A320 taken as reference aircraft is performed. The design is taken through the general steps in aircraft preliminary design. The fuel consumption of the final aircraft is 9 % lower than that of the reference aircraft. The aircraft layout is well balanced regarding the position of the center of gravity and the travel of the center of gravity is minimized. This is necessary due to the aircraft’s particular characteristics concerning static longitudinal stability and controllability. The low wing tank capacity requires an additional fuselage tank. Because of its high span efficiency the aircraft has a glide ratio of 20,4. Its wing is about twice as heavy as the reference wing. This is partly compensated by a lighter fuselage. 1. INTRODUCTION This paper was conducted within the research project Airport 2030 [3]. The designed medium range box wing 1.1. Motivation aircraft is supposed to provide answers on how to reduce emissions in the airport environment and how to reduce costs for airlines with the help of an unconventional and A promising configuration for future aircraft is the box wing more efficient aircraft. configuration (see FIG. 1) which assures savings in fuel consumption compared to conventional aircraft. -
Progress in Inverted Joined Wing Scaled Demonstrator Programme
Progress in Inverted Joined Wing Scaled Demonstrator Programme Cezary Galinski Institute of Aviation Deputy Director for Science Al. Krakowska 110/114, 02-256 Warszawa, Poland, [email protected] Jarosław Hajduk (Airforce Institute of Technology), Adam Dziubinski (Institute of Aviation), Adam Sieradzki (Institute of Aviation), Mateusz Lis (Institute of Aviation), Grzegorz Krysztofiak (Institute of Aviation) ABSTRACT Efficiency is crucial for an airplane to reduce both costs of operations and emissions of air pollutants. There are several airplane concepts that potentially allow to increase the efficiency, which were not investigated thoroughly enough. Inverted join wing configuration, where upper wing is located in front of the lower one is an example of such a concept. Therefore, the project described in this paper is dedicated to fill this gap. CFD analyses, wind tunnel tests and flight tests of scaled demonstrator have been undertaken to perform this task. This paper presents a summary of results achieved so far with particular attention put on CFD and flight test results. 1 INTRODUCTION Joined wing configuration is considered as a candidate for future airplanes. It is an unconventional airplane configuration consisting of two lifting surfaces similar in terms of area and span. One of them is located at the top or above the fuselage, whereas the second is located at the bottom. Moreover one of lifting surfaces is attached in front of airplane Centre of Gravity, whereas the second is attached significantly behind it. Both lifting surfaces join each other either directly or with application of wing tip plates (box wing). For the first time it was proposed by Prandtl in [1]. -
Investigation and Design of a C-Wing Passenger Aircraft
Project Department of Automotive and Aeronautical Engineering Investigation and Design of a C-Wing Passenger Aircraft Author: Karan Bikkannavar Supervisor: Prof. Dr.-Ing. Dieter Scholz, MSME Delivery date: 02.03.2016 Abstract A novel nonplanar wing concept,‘C-Wing‘ design is studied and applied to a commercial aircraft to reduce induced drag which has a significant effect on fuel consumption. In-house preliminary sizing method which employs optimization algorithm is utilized and current Airbus A-320 aircraft is used as a reference to evaluate design parameters and to investigate C-Wing design potential beyond current wing tip designs. An increase in aspect ratio due to extended wing span (airport limit), reduction in mission fuel fraction and 7% mass savings were obtained for aircraft with C-Wing configuration. In the latter section, effect of variations of height to span ratio (h/b) of C-Wing on induced drag factor k, is formulated from a vortex lattice method and literature based equations. These equations primarily estimate Oswald factor e (span efficiency factor) for non planar configurations. The results from these equations were promising and in good proximity to the vortex based method. Finally costing methods used by Association of Auropean Airlines (AEA) is applied to the existing A320 aircraft and C-Wing configuration indicating difference of 6% reduction in Direct Operating Costs (DOC) for the novel concept. From overall outcomes, the C-Wing concept suggests interesting aerodynamic efficiency and stability benefits. © This work is protected by copyright The work is licensed under a Creative Commons Attribution-NonCommercial-ShareAlike 4.0 International License: CC BY-NC-SA http://creativecommons.org/licenses/by-nc-sa/4.0 Any further request may be directed to: Prof.