Vacuum Deposition Processes
Total Page:16
File Type:pdf, Size:1020Kb
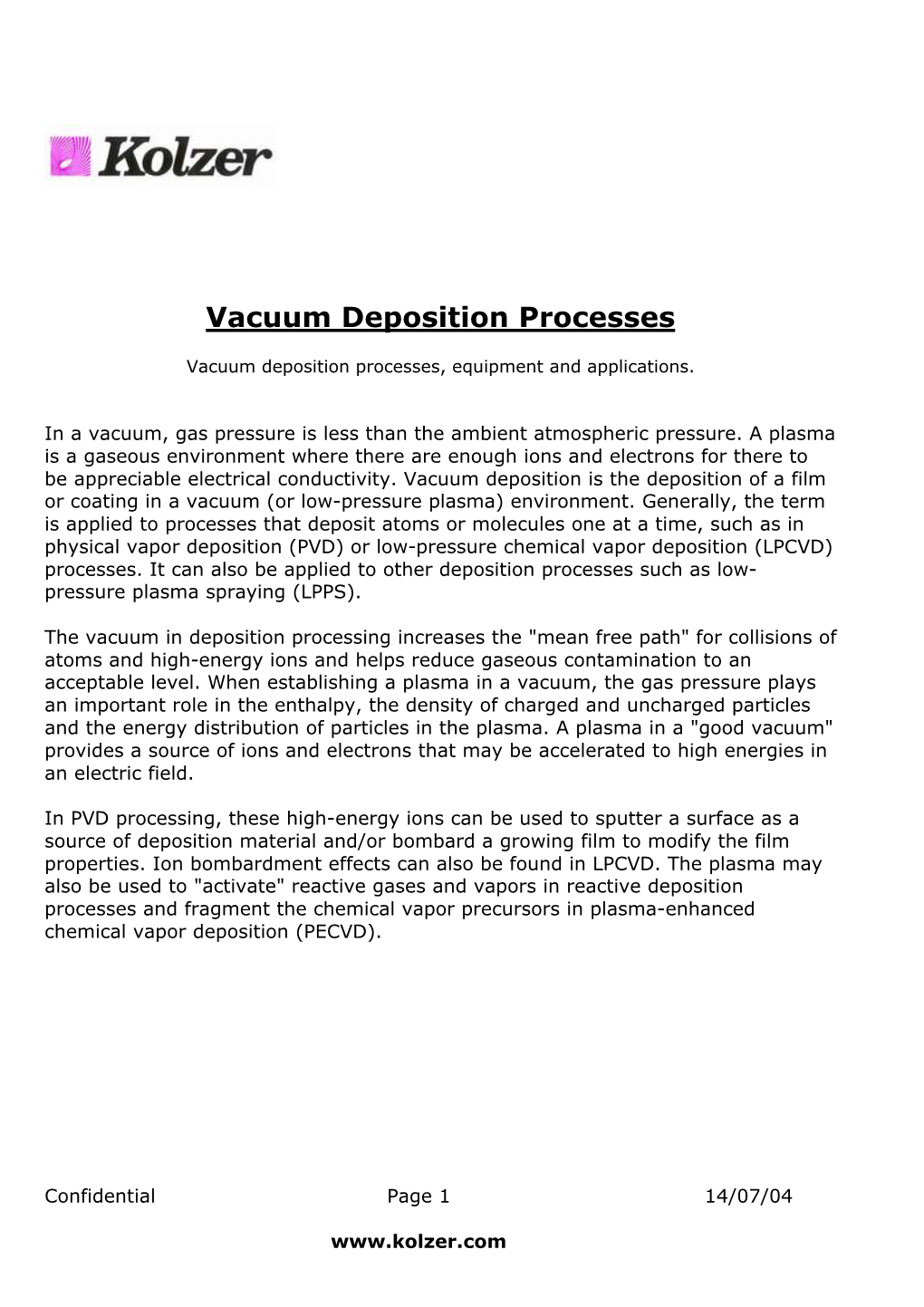
Load more
Recommended publications
-
History Corner a Short History: Vacuum Chambers for PVD
qM qMqM Previous Page | Contents |Zoom in | Zoom out | Front Cover | Search Issue | Next Page qMqM Qmags THE WORLD’S NEWSSTAND® History Corner A Short History: Vacuum Chambers for PVD Donald M. Mattox, Management Plus, Inc., Albuquerque, NM Contributed Original Article Introduction (e.g. European Southern Observatory (ESO) which uses magnetron here are many articles and books on vacuum coating [1,2], basic sputter deposition to recoat each of four 8 meter mirrors every 2 vacuum technology [3,4], and materials for vacuum applications years with aluminum [12]). An interesting astronomical mirror but there seems to be little published on the evolution of single and coating system was developed for the MMT (Fred Lawrence multi-chamber vacuum chambers for vacuum coating. he single Whipple Observatory, Tucson, AZ) to coat its 6.5-meter primary chamber system may be as large as a small room (“walk-in”) and the mirror without removing it from the telescope [13]. multi-chamber processing systems may be as long as a football (US) ield (i.e. 100 meters). Some systems may require special design consideration when some chambers are under continuous process gas/vapor low conditions [5] such as used in reactive deposition or low pressure/plasma enhanced chemical vapor deposition processes (LPCVD/PECVD). Single Chamber Batch Systems In a simple single-chamber “batch” PVD coating system the processing chamber is opened to the ambient ater every deposition. Early vacuum chambers were of glass. Edison’s interest in vacuum technology began in 1878 as it related to his development of the light bulb and its mass production [6]. -
Kalcor University PVD and Vacuum Metallization
Kalcor University PVD and Vacuum Metallization The Look of Bright Metal Call it Bling! Customers love the bright, shiny, metallic look of chrome. From bathroom faucets to car bumpers bright metal finishes are everywhere. Traditionally these parts were Chrome plated. Chrome plating is a technique of electroplating where a thin layer of chromium is electrically deposited onto a metal or plastic object’s outer surface. Typically, a cleaned part is placed into a large chrome plating vat, where it is allowed to warm to solution temperature and then, using application of electrical current the part is electroplated. THE DEMISE OF CHROME PLATING But, from a health standpoint, hexavalent chromium is the most toxic form of chromium. In the US it is now heavily regulated by the Environmental Protection Agency (EPA). The EPA lists it as a hazardous air pollutant because it is a human carcinogen, a "priority pollutant" under the Clean Water Act, and a "hazardous constituent" under the Resource Conservation and Recovery Act. Due to the low efficiency and high solution viscosity a mist of water and hexavalent chromium is released from the bath, which is toxic. So dangerous is hex chrome that the US automakers have prohibited its use on car parts. Several alternatives to the highly toxic process of Chrome plating have emerged, such as chrome- looking paints and the use of trivalent chrome; neither of which provides comparable appearance to Chrome plating. But for many decorative purposes, a process known as Physical Vapor Deposition, or PVD also frequently referred to as Vacuum Metalizing, is now quite common and can achieve a the look of Chrome plating. -
Perovskite Solar Cells Via Vapour Deposition Processes
Perovskite Solar Cells via Vapour Deposition Processes by Qingshan Ma A THESIS IN FULFILMENT OF THE REQUIREMENTS FOR THE DEGREE OF Doctor of Philosophy School of Photovoltaic and Renewable Energy Engineering Faculty of Engineering The University of New South Wales November 2017 Acknowledgment I would love to thank all the people who provided help and supports during my PhD adventure. I would like to acknowledge the School of Photovoltaic and renewable energy engineering for supporting my PhD studies. Without them, this thesis wouldn’t be possible. First and foremost, I would like to express my sincere thanks to my supervisors Dr. Shujuan Huang, Dr. Anita Ho-Baillie and Prof. Martin Green for their guidance and supports in the past 3.5 years. I would like to thank all my perovskite group members, Dr. Sanghun Woo, Dr. Rui Sheng, Arman Mahboubi Soufiani, Dr. Jae Yun, Dr. Yajie Jiang, Sheng Chen, Jincheol Kim, Cho Fai Jonathan Lau, Xiaofan Deng, Adrian Shi, Dr. Meng Zhang, Jianghui Zheng, Jueming Bing, Yongyoon Cho, Da Seul Lee and Benjamin Wilkinson, for their help in my research and the great time we had together. I also would like to thank Dr. Xiaoming Wen for the photoluminescence characterization and Dr. Trevor Young for the proof reading of my thesis. I thank my friend Zewen Zhang, who inspired me and always has been there with me during my time in Australia. I thank my friends Aobo Pu and Dr. Wenkai Cao for making my PhD life so enjoyable. Particularly, I will always remember the countless lunch that I have had with Aobo in the last a few years, which made me not feel so alone. -
Fabricating Reflective Coatings in the Vacuum of Space
Fabricating Reflective Coatings in the Vacuum of Space Elliot Carol, CEO Lunar Resources, Inc. Houston, TX © 2018 Lunar Resources, Inc., - Confidential and Proprietary Information - Do not copy or distribute without express written consent Wake Shield Facility Program Demonstrate Fabrication in Space Vacuum of Critical Building Blocks for Advanced Semiconductor Development and Production STS – 60, 69, 80 Free-flying platform for Thin Film Growth in Space Ultra-Vacuum -7 ~10 Torr ~10-14 Torr Flight Path Vacuum Wake Formation –Redirect Atmospheric and Other Particles Around Spacecraft © 2018 Lunar Resources, Inc., - Confidential and Proprietary Information - Do not copy or distribute without express written consent Wake Shield Facility Program Top-hat Source Cell Assembly Wake Side Flight Direction Kernco Flux (TPG K2) Chassis Chassis Carousel Outer Shield Side view (mid-line section) Side view (mid-line section) © 2018 Lunar Resources, Inc., - Confidential and Proprietary Information - Do not copy or distribute without express written consent Wake Shield Facility Program Designed and Built at University of Houston Assembly and Launched at KSC © 2018 Lunar Resources, Inc., - Confidential and Proprietary Information - Do not copy or distribute without express written consent Wake Shield Facility Program 190 Nm circular orbit Unberth WSF from Payload Bay Ram AO cleaning © 2018 Lunar Resources, Inc., - Confidential and Proprietary Information - Do not copy or distribute without express written consent Wake Shield Facility Program Deploy from -
Thin Film Deposition
Thin Film Deposition Thin Film Deposition can be achieved through two methods: Physical Vapour Deposition (PVD) or Chemical Vapour Deposition (CVD) Physical Vapor Deposition (PVD) comprises a group of surface coating technologies used for decorative coating, tool coating, and other equipment coating applications. It is fundamentally a vaporization coating process in which the basic mechanism is an atom by atom transfer of material from the solid phase to the vapor phase and back to the solid phase, gradually building a film on the surface to be coated. In the case of reactive deposition, the depositing material reacts with a gaseous environment of co-deposited material to form a film of compound material, such as a nitride, oxide, carbide or carbonitride. Physical evaporation is one of the oldest methods of depositing metal films. Aluminum, gold and other metals are heated to the point of vaporization, and then evaporate to form to a thin film covering the surface of the substrate. All film deposition takes place under vacuum or very carefully controlled atmosphere. The degrees of vacuum and units is shown below: Rough vacuum 1 bar to 1 mbar High vacuum 10-3 to 10-6 mbar Very high vacuum 10-6 to 10-9 mbar Ultra-high vacuum < 10-9 mbar = vacuum in space 1 atm = 760 mm = 760 torr = 760 mm Hg = 1000 mbar= 14.7 p.s.i 1 torr = 1,33 mbar Pressure (mbar) Mean free path Number Impingement Monolayer (: cm) Rate (: s-1 cm-2) impingement rate (s-1) 10-1 0,5 3 10 18 4000 10-4 50 3 10 16 40 10-5 500 3 10 15 4 10-7 5 104 3 10 13 4 10-2 10-9 5 106 3 10 11 4 10-4 the mean free path: = kT/(√2)πpd2 d is the diameter of the gas molecule The rate of formation of a surface layer is determined by the impinging molecules: = P/(2 mkT)1/2 (molecules/cm2 sec) where m is the mass of the molecule 1 VACUUM THERMAL EVAPORATION Vacuum evaporation is also known as vacuum deposition and this is the process where the material used for coating is thermally vaporized and then proceeds by potential differences to the substrate with little or no collisions with gas molecules. -
A Concise History of Vacuum Coating Technnology SVC Topics
SVCSVC TopicsTopics Donald M. Mattox, Technical Director • Society of Vacuum Coaters 71 Pinon Hill Place N.E. • Albuquerque, NM 87122 505/856-7188 • FAX: 505/856-6716 • www.svc.org A Concise History Of Vacuum Coating Technnology Part I: Prior to WWII (1940) Before the mid-1930s, many tech- niques for vaporizing material and depositing coatings in vacuum had been demonstrated; however, they remained mostly laboratory curiosi- ties. This was mainly because of the lack of good vacuum materials and systems. In the mid-1930s, improve- ments in materials, techniques and equipment led to the development of commercial applications of vacuum deposition for zinc-metallized paper for paper capacitors for the electron- ics industry, reflector coatings for mirrors and lighting and antireflection coatings for optics. The advent of World War II led to a dramatic increase in the use of vacuum coat- Apparatus for the production of mirrors by (a) Apparatus for the production of mirrors by (b) cathode sputtering. “This method for the evaporation of metal. “This method of deposition ings. preparation of reflecting surfaces is particularly has not been widely tested, and its possibilities The deposition of coatings in a useful as a process for half-silvering and for are, therefore, little known, but it would seem to vacuum environment was known for a depositing metals other than silver. ... For joint be especially valuable for small work where films long time before the process was used grease, a special solution of crude rubber and of any volatile substance are required. ... The commercially. Vacuum deposition of lard was made. -
Coating Methods for Use with the Platinum Metals a REVIEW of the AVAILABLE TECHNIQUES
Coating Methods for Use with the Platinum Metals A REVIEW OF THE AVAILABLE TECHNIQUES By Christopher Hood Group Research Centre, Johnson Matthey & Co Limited Th.e economic use of platinum group metal coatings requires that the most appropriate coating method should be used jor any particular applica- tion. This article reviews the techniques available for various substrate materials and outlines some of the more important properties obtained with different types of deposit. There is now a wide variety of methods which can be carried out by two techniques : that can be employed to form coatings of the vacuum evaporation and sputtering. These platinum group metals. The choice of methods are used for the large-scale produc- materials and methods to be used can best tion of micro-electronic components where be made after the manufacturer and the user platinum provides the required properties of of the product have considered the required good electrical conductivity and complete properties and related factors such as the freedom from atmospheric corrosion (I, 2). thickness and physical properties of the coat- Vacuum evaporation is carried out at a ing, the properties of suitable substrates, and pressure of IO-~Torr or below. The metal the cost of alternative processes. This review from which the coating is to be formed is describes processes which can be used to heated to a sufficiently high temperature to deposit a coating of a platinum group metal cause it to volatilise at the extremely low on to a substrate. The properties of the pressure of the chamber, the substrate being coating and the type of substrate to which arranged to condense this vaporised metal. -
Optimization of Thickness Uniformity Distribution on a Large-Aperture Concave Reflective Mirror and Shadow Mask Design in a Planetary Rotation System
coatings Article Optimization of Thickness Uniformity Distribution on a Large-Aperture Concave Reflective Mirror and Shadow Mask Design in a Planetary Rotation System Gang Wang 1,* , Yunli Bai 1, Jing Zhao 1, Li Wang 1, Jiyou Zhang 2 and Yuming Zhou 2 1 Beijing Institute of Space Mechanics & Electricity, 104 Youyi Road, Beijing 100094, China; [email protected] (Y.B.); [email protected] (J.Z.); [email protected] (L.W.) 2 Optical Ultraprecise Processing Technology Innovation Center for Science and Technology Industry of National Defense (Advanced Manufacture), 104 Youyi Road, Beijing 100094, China; [email protected] (J.Z.); [email protected] (Y.Z.) * Correspondence: [email protected] Abstract: Improving the spatial resolution of remote sensing satellites has long been a challenge in the field of optical designing. Although the use of large-aperture reflective mirrors significantly improves the resolution of optical systems, controlling the film thickness uniformity remains an issue. The planetary rotation system (PRS) has received significant attention owing to the excellent uniformity of the coating applied to the large-aperture reflective mirror. However, the development of the PRS remains hindered by a lack of research on its properties and the design method of the shadow mask. To address this, we performed a theoretical analysis of the distribution of film thickness and uniformity in the PRS, which is impacted by parameters of geometric configuration in the vacuum chamber. We present a film thickness expression based on Knudsen’s law and the Citation: Wang, G.; Bai, Y.; Zhao, J.; geometric configuration of the vacuum chamber that incorporates an additional shading function. -
Chapter 14: Thin Film Deposition Processes
Las Positas College Vacuum Technology 60A & 60B Chapter 14: Thin Film Deposition Processes Up to this point in the course almost all of the emphasis has been placed on the techniques involved with certain activities related to achieving and characterizing a vacuum environment. Now we will turn our attention to the reasons for working so hard to achieve a vacuum: the processes that are conducted in this environment. The deposition of thin films has made a tremendous impact on the level of technology we utilize in our daily lives. Thin film coatings provide enhanced optical performance on items ranging from camera lenses to sunglasses. Architectural glass is often coated to reduce the heat load in large office buildings, and provide significant cost savings by reducing air conditioning requirements. Microelectronics as we know them today would not be possible without vacuum technology. Microcircuits fabricated in multi-step vacuum processes are used in devices ranging from wrist watches to microwave ovens to automobile ignition and monitoring systems. The computer industry would not exist if it were not for vacuum technology. In 1990 the world market for integrated circuits was $50 billion; and for the electronic devices which rely on these microcircuits, $0.9 trillion. Decorative coatings applied to jewelry and plumbing fixtures is another large industry based upon vacuum technology. Many of the components of plumbing fixtures are manufactured by depositing thin films of chromium onto injection molded plastic parts. The useful life of tool bits has also been increased by the application of thin films that are chemical compounds. Tool steel cutting tools used in lathes and mills are often coated with the chemical compound titanium nitride to reduce wear of the cutting edges. -
A Review of Perovskite Photovoltaic Materials' Synthesis And
materials Review A Review of Perovskite Photovoltaic Materials’ Synthesis and Applications via Chemical Vapor Deposition Method Xia Liu 1,2,3, Lianzhen Cao 1,2,3,*, Zhen Guo 2,4,5,*, Yingde Li 1, Weibo Gao 3,* and Lianqun Zhou 2,* 1 Department of Physics and Optoelectronic Engineering, Weifang University, Weifang 261061, Shandong, China; [email protected] (X.L.); [email protected] (Y.L.) 2 Chinese Academy of Sciences Key Lab of Bio-Medical Diagnostics, Suzhou Institute of Biomedical Engineering and Technology, Chinese Academy of Sciences, Suzhou 215163, Jiangsu, China 3 Division of Physics and Applied Physics School of Physical and Mathematical Sciences Nanyang Technological University, Singapore 637371, Singapore 4 Shandong Guo Ke Medical Technology Development Co., Ltd., Jinan 250001, Shandong, China 5 Zhongke Mass Spectrometry (Tianjin) Medical Technology Co., Ltd., Tianjin 300399, China * Correspondence: [email protected] (L.C.); [email protected] (Z.G.); [email protected] (W.G.); [email protected] (L.Z.) Received: 31 August 2019; Accepted: 8 October 2019; Published: 11 October 2019 Abstract: Perovskite photovoltaic materials (PPMs) have emerged as one of superstar object for applications in photovoltaics due to their excellent properties—such as band-gap tunability, high carrier mobility, high optical gain, astrong nonlinear response—as well as simplicity of their integration with other types of optical and electronic structures. Meanwhile, PPMS and their constructed devices still present many challenges, such as stability, repeatability, and large area fabrication methods and so on. The key issue is: how can PPMs be prepared using an effective way which most of the readers care about. -
Glossary of Terms and Acronyms for Vacuum Coating Technology
Society of Vacuum Coaters Glossary of Terms and Acronyms for Vacuum Coating Technology Abridged with permission from The Foundations of Vacuum Coating Technology by Donald M. Mattox Noyes Publications/William Andrew Publishing (2003) ISBN 0-8155-1495-6 2 Society of Vacuum Coaters Glossary of Terms A Applied bias (PVD technology) An electrical potential applied from an external source. See Bias. Abnormal glow discharge (plasma) The DC glow discharge where Arc A high-current, low-voltage electrical discharge between two the cathode spot covers the whole cathode and an increase in the electrodes or between areas at different potentials. See Arc source. voltage increases the cathode current density. This is the type of Arc, gaseous An arc formed in a chamber containing enough gas- glow discharge used in most plasma processing. See Normal glow eous species to aid in establishing and maintaining an electrical discharge. arc. See Arc, vacuum. Abrasion test (characterization) Testing film adhesion and abrasion Arc, vacuum An arc formed in a vacuum such that all of the ionized resistance by rubbing, impacting or sliding in contact with another species originate from the arc electrodes. See Arc, gaseous. surface or surfaces. Examples: Tumble test, Tabor test, Eraser test. Arc suppression Techniques for quenching an arc before it becomes too destructive. These include: shutting-off the power or introduc- Abrasive cleaning The removal of surface material (gross clean- ing a voltage pulse with an opposite polarity. ing), including contamination, by an abrasive action. Arc vapor deposition (Physical vapor deposition, vacuum deposition Abrupt-type interface (film formation) The interface that is formed processes) Film deposition process where the source of vapor is between two materials (A and B) when there is no diffusion or chemi- from arc vaporization. -
The Foundations of Vacuum Coating Technology
The Foundations of Vacuum Coating Technology The Foundations of Vacuum Coating Technology Donald M. Mattox Management Plus, Inc. Albuquerque, New Mexico NOYES PUBLICATIONS WILLIAM ANDREW PUBLISHING Norwich, New York, U.S.A. i Copyright © 2003, Noyes Publications / William Andrew Publishing. All rights reserved. No part of this book may be reproduced or utilized in any form or by any means, electronic or mechanical, including photocopying, recording, or by any information storage and retrieval system, without permission in writing from the Publisher. Cover Art © 2003 by Brent Beckley / William Andrew Publishing Library of Congress Catalog Card Number: 2003004260 ISBN: 0-8155-1495-6 Published in the United States of America by Noyes / William Andrew Publishing 13 Eaton Avenue Norwich, NY 13815 1-800-932-7045 www.williamandrew.com www.knovel.com 10 9 8 7 6 5 4 3 2 1 This book may be purchased in quantity at discounts for education, business, or sales promotional use by contacting the Publisher. Plastics Design Library and its logo are trademarks of William Andrew Inc. Notice: To the best of our knowledge the information in this publication is accurate; however the Publisher does not assume any responsibility or liability for the accuracy or completeness of, or consequences arising from, such information. This book is intended for informational purposes only. Mention of trade names or commercial products does not constitute endorsement or recommendation for use by the Publisher. Final determination of the suitability of any information or product for any use, and the manner of that use, is the sole responsibility of the user.