Analytical Approach for the Power Management of Blended-Mode
Total Page:16
File Type:pdf, Size:1020Kb
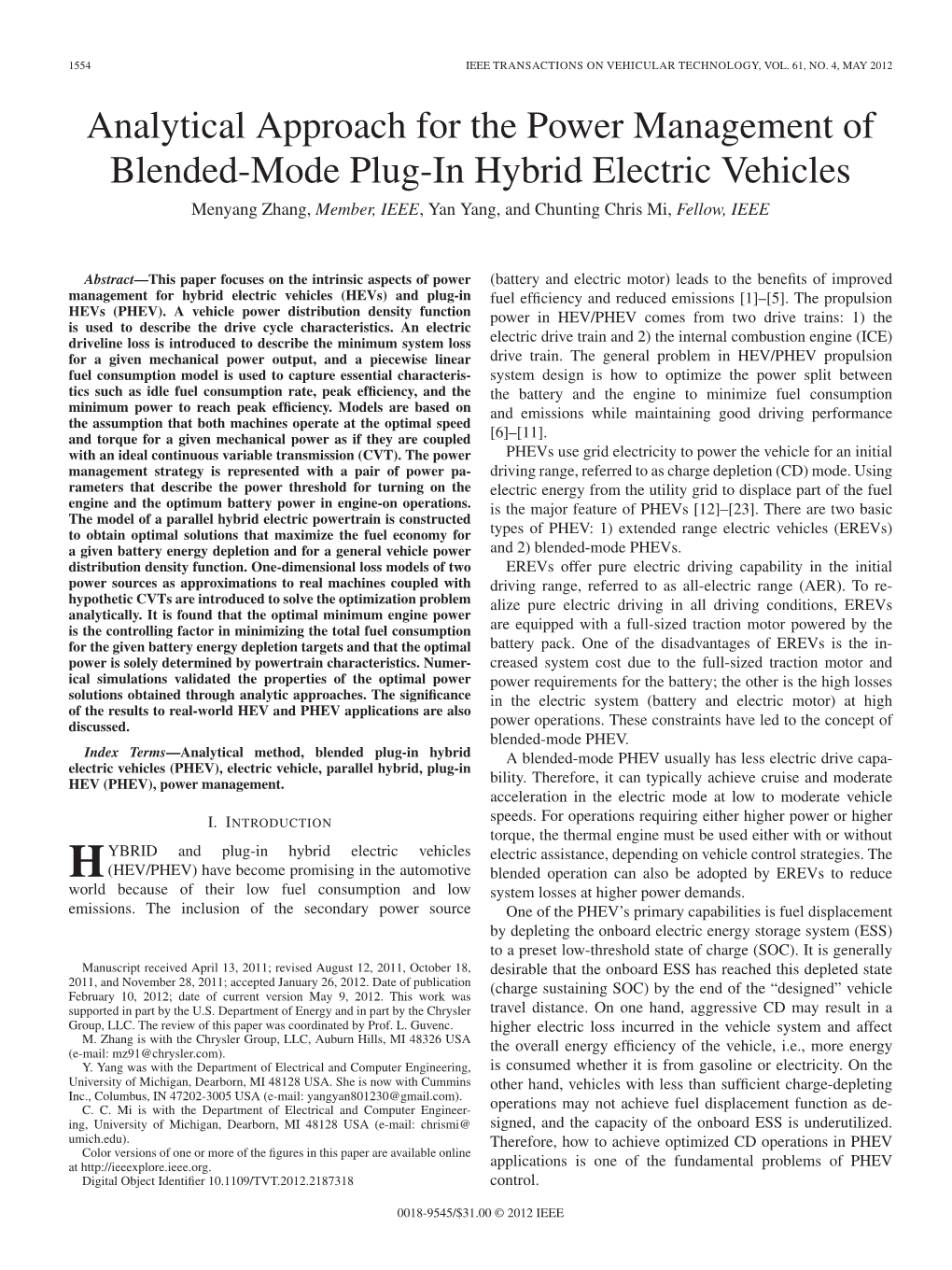
Load more
Recommended publications
-
Study on the Effects of Battery Capacity on the Performance of Hybrid Electric Vehicles
Missouri University of Science and Technology Scholars' Mine Electrical and Computer Engineering Faculty Research & Creative Works Electrical and Computer Engineering 01 Sep 2008 Study on the Effects of Battery Capacity on the Performance of Hybrid Electric Vehicles Deepak Somayajula Andrew Meintz Mehdi Ferdowsi Missouri University of Science and Technology, [email protected] Follow this and additional works at: https://scholarsmine.mst.edu/ele_comeng_facwork Part of the Electrical and Computer Engineering Commons Recommended Citation D. Somayajula et al., "Study on the Effects of Battery Capacity on the Performance of Hybrid Electric Vehicles," Proceedings of the IEEE Vehicle Power and Propulsion Conference (2008, Harbin, China), Institute of Electrical and Electronics Engineers (IEEE), Sep 2008. The definitive version is available at https://doi.org/10.1109/VPPC.2008.4677504 This Article - Conference proceedings is brought to you for free and open access by Scholars' Mine. It has been accepted for inclusion in Electrical and Computer Engineering Faculty Research & Creative Works by an authorized administrator of Scholars' Mine. This work is protected by U. S. Copyright Law. Unauthorized use including reproduction for redistribution requires the permission of the copyright holder. For more information, please contact [email protected]. IEEE Vehicle Power and Propulsion Conference (VPPC), September 3-5, 2008, Harbin, China Study on the Effects of Battery Capacity on the Performance of Hybrid Electric Vehicles Deepak Somayajula, Andrew Meintz, and Mehdi Ferdowsi, Member, IEEE Power Electronics and Motor Drives Laboratory Missouri University of Science and Technology Rolla, MO 65409, USA Email: [email protected], [email protected], and [email protected] Abstract—Hybrid electric vehicles are gaining a significant the drive cycle and the battery assists the engine. -
Fuel Economy of Plug-In Hybrid Electric and Hybrid Electric Vehicles: Effects of Vehicle Weight, Hybridization Ratio and Ambient Temperature
UC Riverside 2020 Publications Title Fuel Economy of Plug-In Hybrid Electric and Hybrid Electric Vehicles: Effects of Vehicle Weight, Hybridization Ratio and Ambient Temperature Permalink https://escholarship.org/uc/item/4z12798n Journal World Electric Vehicle Journal, 11(2) ISSN 2032-6653 Author Jung, Heejung Publication Date 2020-03-31 DOI 10.3390/wevj11020031 Peer reviewed eScholarship.org Powered by the California Digital Library University of California Article Fuel Economy of Plug-In Hybrid Electric and Hybrid Electric Vehicles: Effects of Vehicle Weight, Hybridization Ratio and Ambient Temperature Heejung Jung 1,2 1 Department of Mechanical Engineering, University of California Riverside, 900 University Ave, Riverside, CA 92521, USA; [email protected] 2 College of Engineering-Center for Environmental Research and Technology (CE-CERT), University of California Riverside, 1084 Columbia Ave, Riverside, CA 92507, USA Received: 10 December 2019; Accepted: 29 March 2020; Published: 31 March 2020 Abstract: Hybrid electric vehicles (HEVs) and plug-in hybrid electric vehicles (PHEVs) are evolving rapidly since the introduction of Toyota Prius into the market in 1997. As the world needs more fuel-efficient vehicles to mitigate climate change, the role of HEVs and PHEVs are becoming ever more important. While fuel economies of HEVs and PHEVs are superior to those of internal combustion engine (ICE) powered vehicles, they are partially powered by batteries and therefore they resemble characteristics of battery electric vehicles (BEVs) such as dependence of fuel economy on ambient temperatures. It is also important to understand how different extent of hybridization (a.k.a., hybridization ratio) affects fuel economy under various driving conditions. -
Autonomie Vehicle Validation Summary
Autonomie Vehicle Validation Summary Aymeric Rousseau, Neeraj Shidore, Dominik Karbowski, Phil Sharer Argonne National Laboratory This presentation does not contain any proprietary, confidential, or otherwise restricted information Outline . Validation Process . Component Model Development and Validation . Vehicle Validation Examples – Conventional Vehicles – Mild Hybrids – Full Hybrids – Plug-in Hybrids (Blended) – E-REV PHEV – BEV . Thermal Model Validation Overview 2 Generic Process to Validate Models Developed over the Past 15 Years Vehicle Instrumentation, Test Selection Test data analysis using ‘Import Test Data’ function in Autonomie - Evaluate individual sensors (QC) - Estimate additional signals for each component - Component performance data estimation - Find key parameter values and control scheme Calibration and validation of the vehicle model with test data Vehicle model development - Dynamic performance validation - Energy consumption validation - Develop models - Instantiate models To quickly and accurately predict or evaluate the energy - Develop low and high level control strategies consumption and dynamic performance of the vehicle under various driving conditions. 3 Advanced Vehicle Laboratory Capabilities 4 In-depth Approach to Vehicle Instrumentation . Significant instrumentation contributes to detailed vehicle/component understanding (120+ signals collected) Many Signal Sources . Torque sensors (axles) . Components Speeds . Coolant flow sensors . Coolant / Component temperatures . Exhaust temperatures, emissions -
Sizing and Fuel Consumption Evaluation Methodology for Hybrid Light Duty Vehicles
World Electric Vehicle Journal Vol. 4 - ISSN 2032-6653 - © 2010 WEVA Page000249 EVS25 Shenzhen, China, Nov 5-9, 2010 Sizing and fuel consumption evaluation methodology for hybrid light duty vehicles Nicolas Marc1,3, Eric Prada1, Antonio Sciarretta2, Shadab Anwer1, Franck Vangraefschepe2, François Badin1, Alain Charlet3, Pascal Higelin3 1 IFP Energies nouvelles, Rond-point de l'échangeur de Solaize, BP 3, 69360 Solaize, France ([email protected]) 2 IFP Energies nouvelles, 1 et 4 avenue de Bois-Préau, 92852 Rueil-Malmaison, France 3 PRISME/EPM, Université d'Orléans, 8 rue Léonard de Vinci, 45072 Orléans Cedex 2, France Abstract This paper presents a methodology dedicated to component sizing and fuel consumption evaluation of different degree of hybridization for light duty vehicles applications. The methodology will be described together with vehicle and components simulation and sizing principles. To ensure a systematic approach, with no bias for any of the cases considered, the energy management of the hybrid drivetrain will be carried out thanks to an optimization based on the Pontryagin's Minimum Principle. As hybrid fuel consumption is highly dependant on vehicle type of use, the hybrid vehicles will be evaluated on different actual use driving patterns as well as on missions representing the daily usage of the vehicle. The methodology and a panel of results are presented in the paper. Keywords: HEV, plug-in HEV, components sizing, energy consumption, simulation, optimized energy management 1 Introduction of map representations of the differently sized components (battery, electric HEVs are complex systems in which many machine, IC engine, etc.); parameters could impact the fuel economy potential and it appears that car and component 2. -
Battery Requirements for Plug-In Hybrid Electric Vehicles – Analysis and Rationale
Conference Paper Battery Requirements for Plug-In NREL/CP-540-42240 Hybrid Electric Vehicles – July 2009 Analysis and Rationale A.A. Pesaran and T. Markel National Renewable Energy Laboratory H.S. Tataria General Motors Corporation D. Howell U.S. Department of Energy Presented at the 23rd International Electric Vehicle Symposium (EVS-23) Anaheim, California December 2–5, 2007 NOTICE The submitted manuscript has been offered by an employee of the Alliance for Sustainable Energy, LLC (ASE), a contractor of the US Government under Contract No. DE-AC36-08-GO28308. Accordingly, the US Government and ASE retain a nonexclusive royalty-free license to publish or reproduce the published form of this contribution, or allow others to do so, for US Government purposes. This report was prepared as an account of work sponsored by an agency of the United States government. Neither the United States government nor any agency thereof, nor any of their employees, makes any warranty, express or implied, or assumes any legal liability or responsibility for the accuracy, completeness, or usefulness of any information, apparatus, product, or process disclosed, or represents that its use would not infringe privately owned rights. Reference herein to any specific commercial product, process, or service by trade name, trademark, manufacturer, or otherwise does not necessarily constitute or imply its endorsement, recommendation, or favoring by the United States government or any agency thereof. The views and opinions of authors expressed herein do not necessarily state or reflect those of the United States government or any agency thereof. Available electronically at http://www.osti.gov/bridge Available for a processing fee to U.S. -
Design and Evaluation of a Predictive Powertrain Control System
View metadata, citation and similar papers at core.ac.uk brought to you by CORE Taghavipour, A., Azad, N. L., & McPhee, J. Design and evaluation of a predictive powertrain control system for a plug-inprovided hybrid byelectric University vehicle of Waterloo's to improve Institutional the Repository fuel economy and the emissions. Proceedings of the Institution of Mechanical Engineers, Part D: Journal of Automobile Engineering, 229(5), 624–640. Copyright © 2014 SAGE. Reprinted by permission of SAGE Publications. https://dx.doi.org/10.1177/0954407014547925 Journal name 000(00):1–13 Design and Evaluation of a Predictive ©The Author(s) 2010 Reprints and permission: Powertrain Control System for a PHEV to sagepub.co.uk/journalsPermissions.nav DOI:doi number Improve Fuel Economy and Emissions http://mms.sagepub.com Amir Taghavipour,∗ Nasser L.Azad, and John McPhee Systems Design Engineering Department, University of Waterloo, Ontario, Canada Amir Taghavipour Amir Taghavipour received his BASc and MASc Degrees in Mechanical Engineering from Sharif University of Technology, Tehran, Iran, in 2007 and 2009. He is now a PhD student at the University of Waterloo, Department of Systems Design Engineering. His research interests are predictive automotive powertrain control, hybrid electric vehicles power management strategy design and optimization. Nasser Lashgarian Azad Nasser Lashgarian Azad is an Assistant Professor in Systems Design Engineering at the University of Waterloo. His primary research interests lie in modelling, estimation and control of complex dynamic mechanical and multi-domain physical systems, with special emphasis on advanced modelling and model reduction methods, sensitivity analysis techniques, non-linear and optimal control, with appli- cations to advanced vehicle systems, such as modern automotive powertrains and vehicle dynamics control systems. -
Background on Plug-In Electric Vehicles
The submitted manuscript has been created by Argonne National Laboratory, a U.S. Department of Energy laboratory managed by UChicago Argonne, LLC, under Contract No. DE-AC02-06CH11357. The U.S. Government retains for itself, and others acting on its behalf, a paid-up, nonexclusive, irrevocable worldwide license in said article to reproduce, prepare derivative works, distribute copies to the public, and perform publicly and display publicly, by or on behalf of the Government Background on Plug-in Electric Vehicles Danilo J. Santini Senior Economist Center for Transportation Research Argonne National Laboratory The American Lung Association Electric Vehicle Forum May 23rd Palos Hills IL Preparation of this presentation was sponsored by Clean Cities and the Vehicle Technologies Program, Energy Efficiency & Renewable Energy, U.S. Department of Energy. Topics of the Presentation . Historical context . Distinguishing among three major kinds of plug-in electric cars . Operations and infrastructure . What are the motivators for development and sales of plug-in electric vehicles? The first electric vehicles (EVs) . First crude electric made between 1832 & 1839 . More practical & successful vehicles made around 1842 . Better battery storage invented in 1865 with further improvements in 1881 Jay Leno’s Baker EV 1900s Markets Were: Where Garages Were for Personal Vehicles; Slow MPH Urban Delivery . (Midwestern) cities with lower density had higher EV car share – houses, more new construction . New York was the first city to lose all personal use EVs (multifamily, long commutes, hills) . New York City was the most successful location for truck fleet EVs by far (slow average speed, many customers, large fleets, long hours, used most available range or even more via battery swapping) . -
1 a Simulation-Based Assessment of Plug-In Hybrid Electric Vehicle
A Simulation-Based Assessment of Plug-in Hybrid Electric Vehicle Architectures by Daniel Sotingco B.S. Mechanical Engineering Franklin W. Olin College of Engineering, 2010 SUBMITTED TO THE DEPARTMENT OF MECHANICAL ENGINEERING IN PARTIAL FULLFILLMENT OF THE REQUIREMENTS FOR THE DEGREE OF MASTER OF SCIENCE IN MECHANICAL ENGINEERING AT THE MASSACHUSETTS INSTITUTE OF TECHNOLOGY June 2012 ©2012 Massachusetts Institute of Technology All rights reserved. Signature of author: ………………………………………………………………………………………………………………………………….. Department of Mechanical Engineering May 11, 2012 Certified by: ……………………………………………………………………………………………………………………………………………… Professor Jerome Milgram William I. Koch Professor of Ocean Engineering Thesis Advisor Accepted by: …………………………………………………………………………………………………………………………………………….. Professor David E. Hardt Ralph E. and Eloise F. Cross Professor of Mechanical Engineering Chair, Committee on Graduate Students 1 2 A Simulation-Based Assessment of Plug- in Hybrid Electric Vehicle Architectures By Daniel S. Sotingco Submitted to the Department of Mechanical Engineering on May 11, 2012 in Partial Fulfillment of the Requirements for the Degree of Master of Science in Mechanical Engineering Abstract Plug-in hybrid electric vehicles (PHEVs) are vehicles that utilize power from both an internal combustion engine and an electric battery that can be recharged from the grid. Simulations of series, parallel, and split-architecture PHEVs, as well as parallel and split PHEVs with ultracapacitors, were performed in Autonomie, the vehicle simulation package released by Argonne National Laboratory as the successor to the Powertrain System Analysis Toolkit (PSAT). The PHEV configurations were parameterized by battery capacity, motor peak power, engine peak power, and ultracapacitor capacity if applicable. Results were compared to EPA data for the Chevrolet Volt and Toyota Prius, showing close agreement on values for fuel consumption, charge-depleting range, and acceleration time. -
The Design of Control Strategy for Blended Series-Parallel Power-Split PHEV – a Simulation Study
International Journal of Transportation Systems Ning Ding, K. Prasad, T. T. Lie http://www.iaras.org/iaras/journals/ijts The Design of Control Strategy for Blended Series-Parallel Power-Split PHEV – a Simulation Study Ning Ding, K. Prasad and T.T. Lie Department of Electrical and Electronic Engineering Auckland University of Technology 34 St Paul Street, Auckland New Zealand [email protected] Abstract: - Electric Vehicles (EVs) have been extensively researched to reduce the fuel consumption and tailpipe emission. The series-parallel power-split Plug-in Electric Vehicle (PHEV) has been considered as one of the most suitable candidates. It contains both an internal combustion engine (ICE) and an electrical storage system (ESS) to achieve a better driving performance. The energy management system (EMS) is significant for a PHEV to improve the efficiency of the whole system. Electric vehicle mode (EV), charging depletion (CD) and charging sustaining (CS) modes will be discussed to build a control strategy in this study. This control strategy will be implemented with the state of charge (SoC) to show its impact through a simulation study. KeyWords: - Blended mode; Control strategy; Emission; Fuel economy; PHEV; Simulation; SoC 1 Introduction The PHEV inherits the features of HEV that includes The issues on Global Warming resulted from burning both Internal Combustion Engine (ICE) and Energy of fossil fuel has been discussed for decades. The Storage System (ESS). Fig.1 shows the connecting Electric Vehicle (EVs) as a potential candidate to status for PHEV [7]. The PHEV introduces the grid- reduce the air pollution from traffic section and to able battery technology to extend the energy density relieve the pressure from energy exhaustion have in a euphemistical way [8]. -
Plug-In Hybrid Electric Vehicles: How Does One Determine Their Potential for Reducing U.S
Page 0038 ISSN 2032-6653 The World Electric Vehicle Journal, Vol 2, September 2008 Plug-In Hybrid Electric Vehicles: How Does One Determine Their Potential for Reducing U.S. Oil Dependence? Anant Vyas*, Danilo Santiniº, Michael Duoba*, Mark Alexander† Estimation of the potential of plug-in hybrid electric vehicles’ (PHEV’s) ability to reduce U.S. gasoline use is difficult and complex. Although techniques have been proposed to estimate the vehicle kilometers of travel (VKT) that can be electrified, these methods may be inadequate and/or inappropriate for early market introduction circumstances. Factors that must be considered with respect to the PHEV itself include (1) kWh battery storage capability; (2) kWh/km depletion rate of the vehicle (3) liters/km use of gasoline (4) average daily kilometers driven (5) annual share of trips exceeding the battery depletion distance (6) driving cycle(s) (7) charger location [i.e. on-board or off-board] (8) charging rate. Each of these factors is actually a variable, and many interact. Off the vehicle, considerations include (a) primary overnight charging spot [garage, carport, parking garage or lot, on street], (b) availability of primary and secondary charging locations [i.e. dwellings, workplaces, stores, etc] (c) time of day electric rates (d) seasonal electric rates (e) types of streets and highways typically traversed during most probable trips depleting battery charge [i.e. city, suburban, rural and high vs. low density]; (f) cumulative trips per day from charger origin (g) top speeds and peak acceleration rates required to make usual trips. Taking into account PHEV design trade-off possibilities (kW vs. -
Design and Optimization of Hybrid Electric Vehicle Drivetrain and Control Strategy Parameters Using Evolutionary Algorithms
DESIGN AND OPTIMIZATION OF HYBRID ELECTRIC VEHICLE DRIVETRAIN AND CONTROL STRATEGY PARAMETERS USING EVOLUTIONARY ALGORITHMS Chirag Desai A Thesis in The Department of Electrical and Computer Engineering Presented in Partial Fulfillment of the Requirements for the Degree of Master of Applied Science (Electrical Engineering and Computer Science) at Concordia University Montréal, Québec, Canada December 2010 Chirag Desai, 2010 CONCORDIA UNIVERSITY SCHOOL OF GRADUATE STUDIES This is to certify that the thesis prepared By: Chirag Desai Entitled: “Design and Optimization of Hybrid Electric Vehicle Drivetrain and Control Strategy Parameters using Evolutionary Algorithms and submitted in partial fulfillment of the requirements for the degree of Master of Applied Science Complies with the regulations of this University and meets the accepted standards with respect to originality and quality. Signed by the final examining committee: ________________________________________________ Chair Dr. D. Qiu ________________________________________________ Examiner, External Dr. S. Rakheja, MIE To the Program ________________________________________________ Examiner Dr. P. Pillay ________________________________________________ Supervisor Dr. S. Williamson Approved by: ___________________________________________ Dr. W. E. Lynch, Chair Department of Electrical and Computer Engineering ____________20_____ ___________________________________ Dr. Robin A. L. Drew Dean, Faculty of Engineering and Computer Science ABSTRACT Design and Optimization of Hybrid Electric -
Design and Control Strategy of Powertrain in Hybrid Electric Vehicles Alexandre Ravey
Design and control strategy of powertrain in hybrid electric vehicles Alexandre Ravey To cite this version: Alexandre Ravey. Design and control strategy of powertrain in hybrid electric vehicles. Other [cond- mat.other]. Université de Technologie de Belfort-Montbeliard, 2012. English. NNT : 2012BELF0192. tel-00863541 HAL Id: tel-00863541 https://tel.archives-ouvertes.fr/tel-00863541 Submitted on 19 Sep 2013 HAL is a multi-disciplinary open access L’archive ouverte pluridisciplinaire HAL, est archive for the deposit and dissemination of sci- destinée au dépôt et à la diffusion de documents entific research documents, whether they are pub- scientifiques de niveau recherche, publiés ou non, lished or not. The documents may come from émanant des établissements d’enseignement et de teaching and research institutions in France or recherche français ou étrangers, des laboratoires abroad, or from public or private research centers. publics ou privés. University of Technology of BelfortMontbéliard Graduate school SPIM (Engineering sciences and microtechnology) THESIS Presented at The University of Technology of BelfortMontbéliard in order to obtain the title of Doctor of Philosoph by alexandre ravey Engineer at University of Technology of BelfortMontbéliard Electric Engineering and Control Systems Department CONCEPTIONETGESTIONDEL’ÉNERGIEDES ARCHITECTURESPOURVÉHICULESHYBRIDESÉLECTRIQUES Thesis committee : M. Mohamed EL Hachemi BENBOUZID Université de Brest M. Thierry-marie GUERRA Université de Valenciennes M. Mohamed GABSI Ecole Normale Supérieure de Cachan M. Pascal BROCHET Université Technologique de BelfortMontbéliard M. Abdellatif MIRAOUI Université de Cadi Ayyad M. Srdjan Miodrag LUKIC North Carolina State University M. David BOUQUAIN Université Technologique de BelfortMontbéliard Alexandre Ravey : Conception et gestion de l’énergie des architectures pour véhicules hybrides électriques , Phd Thesis.