Propulsion Systems Definition for a Liquid Fly-Back Booster
Total Page:16
File Type:pdf, Size:1020Kb
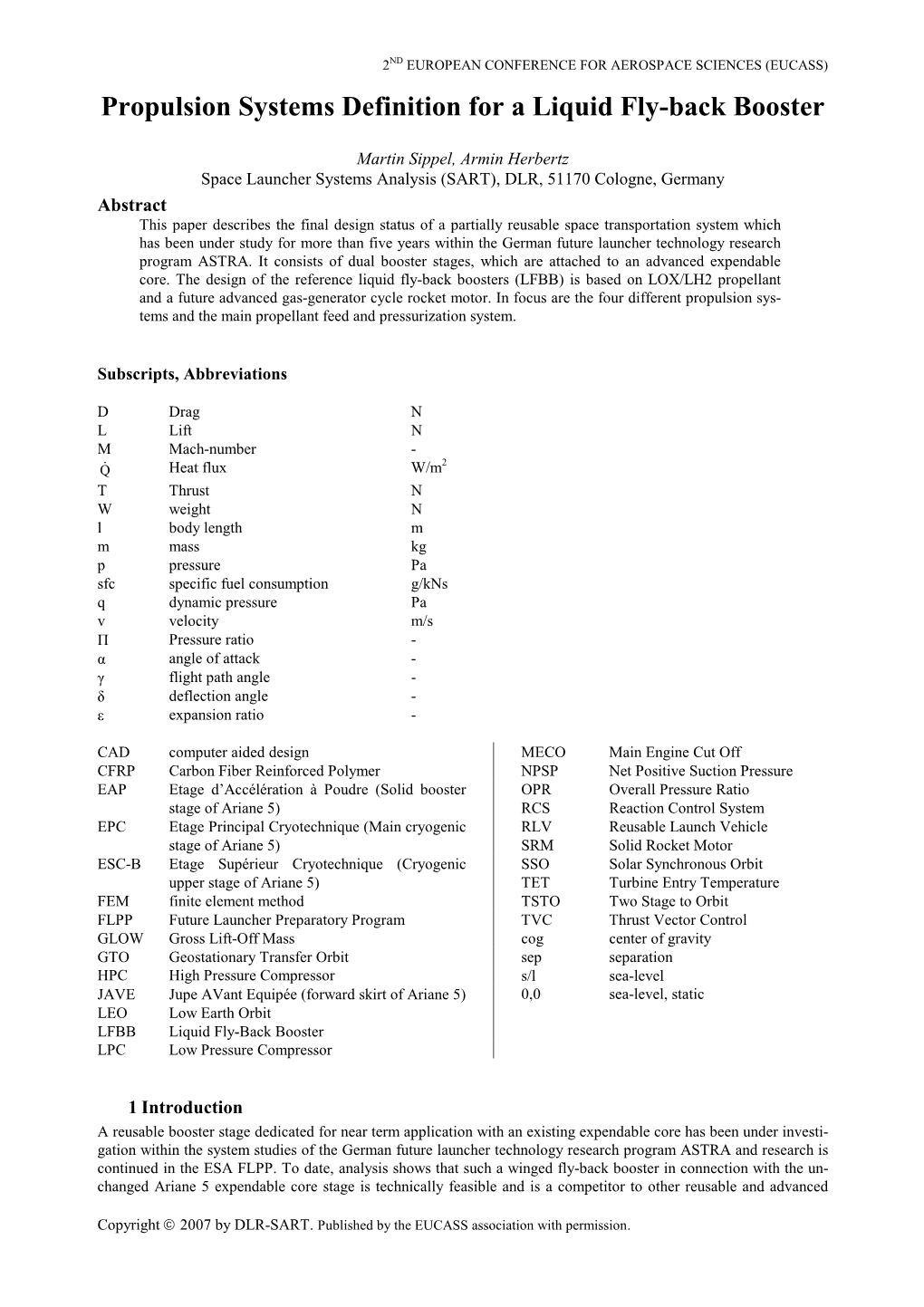
Load more
Recommended publications
-
Cubesat Mission: from Design to Operation
applied sciences Article CubeSat Mission: From Design to Operation Cristóbal Nieto-Peroy 1 and M. Reza Emami 1,2,* 1 Onboard Space Systems Group, Department of Computer Science, Electrical and Space Engineering, Luleå University of Technology, Space Campus, 981 92 Kiruna, Sweden 2 Aerospace Mechatronics Group, University of Toronto Institute for Aerospace Studies, Toronto, ON M3H 5T6, Canada * Correspondence: [email protected]; Tel.: +1-416-946-3357 Received: 30 June 2019; Accepted: 29 July 2019; Published: 1 August 2019 Featured Application: Design, fabrication, testing, launch and operation of a particular CubeSat are detailed, as a reference for prospective developers of CubeSat missions. Abstract: The current success rate of CubeSat missions, particularly for first-time developers, may discourage non-profit organizations to start new projects. CubeSat development teams may not be able to dedicate the resources that are necessary to maintain Quality Assurance as it is performed for the reliable conventional satellite projects. This paper discusses the structured life-cycle of a CubeSat project, using as a reference the authors’ recent experience of developing and operating a 2U CubeSat, called qbee50-LTU-OC, as part of the QB50 mission. This paper also provides a critique of some of the current poor practices and methodologies while carrying out CubeSat projects. Keywords: CubeSat; miniaturized satellite; nanosatellite; small satellite development 1. Introduction There have been nearly 1000 CubeSats launched to the orbit since the inception of the concept in 2000 [1]. An up-to-date statistics of CubeSat missions can be found in Reference [2]. A summary of CubeSat missions up to 2016 can also be found in Reference [3]. -
Increasing Launch Rate and Payload Capabilities
Aerial Launch Vehicles: Increasing Launch Rate and Payload Capabilities Yves Tscheuschner1 and Alec B. Devereaux2 University of Colorado, Boulder, Colorado Two of man's greatest achievements have been the first flight at Kitty Hawk and pushing into the final frontier that is space. Air launch systems aim to combine these great achievements into a revolutionary way to deliver satellites, cargo and eventually people into space. Launching from an aircraft has many advantages, including the ability to launch at any inclination and from above bad weather, which could delay ground launches. While many concepts for launching rockets from an airplane have been developed, very few have made it past the drawing board. Only the Pegasus and, to a lesser extent, SpaceShipOne have truly shown the feasibility of such a system. However, a recent push for rapid, small payload to orbit launches by the military and a general need for cheaper, heavy lift options are leading to an increasing interest in air launch methods. In order for the efficiency and flexibility of the system to be realized, however, additional funding and research are necessary. Nomenclature ALASA = airborne launch assist space access ALS = air launch system DARPA = defense advanced research project agency LEO = low Earth orbit LOX = liquid oxygen RP-1 = rocket propellant 1 MAKS = Russian air launch system MECO = main engine cutoff SS1 = space ship one SS2 = space ship two I. Introduction W hat typically comes to mind when considering launching people or satellites to space are the towering rocket poised on the launch pad. These images are engraved in the minds of both the public and scientists alike. -
Paper Session II-B-National Launch System Payload Accommodations
The Space Congress® Proceedings 1992 (29th) Space - Quest For New Fontiers Apr 22nd, 2:00 PM Paper Session II-B - National Launch System Payload Accommodations Capt James M. Knauf National Launch System Requirements Officer HQ Airor F ce Space Command Follow this and additional works at: https://commons.erau.edu/space-congress-proceedings Scholarly Commons Citation Knauf, Capt James M., "Paper Session II-B - National Launch System Payload Accommodations" (1992). The Space Congress® Proceedings. 15. https://commons.erau.edu/space-congress-proceedings/proceedings-1992-29th/april-22-1992/15 This Event is brought to you for free and open access by the Conferences at Scholarly Commons. It has been accepted for inclusion in The Space Congress® Proceedings by an authorized administrator of Scholarly Commons. For more information, please contact [email protected]. NATIONAL LAUNCH SYSTEM PAYLOAD ACCOMMODATIONS Capt James M. Knauf National Launch System Requirements Officer HQ Air Force Space Command - Peterson AFB, CO ABSTRACT Early definition, documentation, acceptance, and continuing implementation of a standard system of payload accommodations for space launch systems is essential. Attempts to provide truly standard payload accommodations have not met with significant success in increasing responsiveness or reducing operations costs. The operational philosophy of the National Launch System (NLS) is based on standardization and includes standardized payload accommodations. These must be incorporated into NLS design concepts early in the development phase to ensure the NLS goal of increased responsiveness and reduced operating cost. At the same time, sufficient flexibility will be maintained to accommodate the rare unique payload requirement which cannot meet the standard due to specific mission requirements, safety concerns, or other reasons. -
Integrated Spacecraft/Payload Element Fact Sheet
National Aeronautics and Space Administration Space Launch System Integrated Spacecraft/ Payload Element NASA’s Space Launch System (SLS) will pro- vide the agency with super heavy-lift capability to return astronauts to the Moon and launch payloads to the Moon or deeper into the solar system. The integrated spacecraft/payload element for the initial SLS configuration, called Block 1, consists of the upper stage and payload section facts of the rocket, above the core stage, including adapters and separation systems. In the SLS Block 1 crew configuration, the inte- grated spacecraft/payload element connects the core stage to the Orion crew vehicle. In the Block 1 cargo variant, the integrated spacecraft/ payload element sits at the top of the vehicle, above the core stage, and includes a 5 meter- diameter payload fairing that encapsulates the payload. NASA is building the super heavy-lift SLS rocket to send astronauts in Orion to the Moon and NASA to launch cargo and scientific payloads to the Moon or deep into the solar system. Block 1 is the initial launcher, with progressively more powerful vehicles planned for the future to SLS Block 1 will be used for NASA’s first Artemis enable NASA to establish a sustainable pres- missions. The initial flight, Artemis I, is a test of ence at the Moon before sending humans to the new system – including Orion and ground sys- Mars. tems at Kennedy Space Center – and will include deployment of 13 CubeSats. The integrated spacecraft/payload element on the Block 1 crew vehicle is comprised of the In- The next flight, Artemis II, is a lunar flyby mission terim Cryogenic Propulsion Stage (ICPS), which that will make astronauts in Orion the record- provides in-space propulsion, the Launch Ve- holders for farthest distance humans have trav- hicle Stage Adapter (LVSA), and the Orion Stage eled from Earth. -
Analysis of a Heavy Lift Launch Vehicle Design Using Small Liquid
Analysis of a Heavy Lift Launch Vehicle Design Using Small Liquid Rocket Engines by DAVID PHILLIP RUSS S.B., Massachusetts Institute of Technology 1987 SUBMITTED IN PARTIAL FULFILLMENT OF THE REQUIREMENTS FOR THE DEGREE OF MASTER OF SCIENCE IN AERONAUTICS AND ASTRONAUTICS at the MASSACHUSETTS INSTITUTE OF TECHNOLOGY May 1988 ® David P. Russ 1988 The author hereby grants M.I.T. and Hughes Aircraft Company permission to reproduce and to distribute copies of this thesis document in whole or in part. Signature of Author Department of Aeronautics and Astronautics December 18, 1987 Reviewed by C. P. Rubin Hughes Aircraft Company Certified by Professor Walter M. Hollister Thesis Supervjsor, Departmer of Aeronautics and Astronautics .. Accepted by , .AU Professor Harold Y. Wachman Chairman, Depart'rmental Graduate Committee Department of Aeronautics and Astronautics MAY i od ;WITHDRAWfIN i M.I.1W.i..: P. I LBRARt S UBAer 7:Ir_ Aero Analysis of a Heavy Lift Launch Vehicle Design Using Small Liquid Rocket Engines by David P. Russ Submitted to the Department of Aeronautics and Astronautics in partial fulfillment of the requirements for the degree of Master of Science in Aeronautics and Astronautics May, 1988 Abstract The trend in launch vehicle design has been to increase performance by using en- gines of greater and greater complexity, which has a negative effect on cost and reliability. However, a design making use of over 300 small, simple rocket engines can deliver over 340,000 lbs to low Earth orbit. This design, derived by using the rocket equations to size the major components, features a 42 ft. -
GAO-15-706, Federal Aviation Administration: Commercial Space
United States Government Accountability Office Report to the Chairman, Committee on Science, Space and Technology, House of Representatives August 2015 FEDERAL AVIATION ADMINISTRATION Commercial Space Launch Industry Developments Present Multiple Challenges GAO-15-706 August 2015 FEDERAL AVIATION ADMINISTRATION Commercial Space Launch Industry Developments Present Multiple Challenges Highlights of GAO-15-706, a report to the Chairman, Committee on Science, Space and Technology, House of Representatives Why GAO Did This Study What GAO Found The U.S. commercial space launch During the last decade, U.S. companies conducted fewer orbital launches in total industry has changed considerably than companies in Russia or Europe, which are among their main foreign since the enactment of the Commercial competitors. However, the U.S. commercial space launch industry has expanded Space Launch Amendments Act of recently. In 2014, U.S. companies conducted 11 orbital launches, compared with 2004. FAA is required to license or none in 2011. In addition, in 2014, U.S. companies conducted more orbital permit commercial space launches, but launches than companies in Russia, which conducted four, or Europe, which to allow the space tourism industry to conducted six. develop, the act prohibited FAA from regulating crew and spaceflight The Federal Aviation Administration (FAA)—which is responsible for protecting participant safety before 2012—a the public with respect to commercial space launches, including licensing and moratorium that was later extended but permitting launches—faces multiple challenges in addressing industry will now expire on September 30, developments. If Congress does not extend the regulatory moratorium beyond 2015. Since October 2014, there have September 2015, FAA will need to determine whether and when to regulate the been three mishaps involving FAA safety of crew and spaceflight participants. -
Payload Developers and Principal Investigators Payload Planning, Integration and Operations Primer International Space Station P
OZ-10-056 BASELINE Payload Developers and Principal Investigators Payload Planning, Integration and Operations Primer International Space Station Program ISS National Laboratory Office June 2010 BASELINE National Aeronautics and Space Administration International Space Station Program Johnson Space Center Houston, Texas i OZ-10-056 REVISION A JUNE 2010 INTERNATIONAL SPACE STATION PROGRAM PAYLOAD DEVELOPERS AND PRINCIPAL INVESTIGATORS PAYLOAD PLANNING, INTEGRATION AND OPERATIONS PRIMER CONCURRENCE JUNE 2010 REVISION A PREPARED BY: K. Jules OZ111 Book Manager ORGN SIGNATURE DATE CONCURRED BY: M. Edeen OZ111 ISS National Laboratory Office Manager ORGN SIGNATURE DATE ii OZ-10-056 REVISION A JUNE 2010 Contents List of Tables and Figures............................................................................................................ viii 1 Introduction ............................................................................................................................. 9 1.1 Objective ......................................................................................................................... 9 1.2 Layout ............................................................................................................................. 9 2 Background ........................................................................................................................... 10 2.1 Payload Integration Templates Definitions .................................................................. 10 2.1.1 Standard Payload Integration -
Evolution of Communications Payload Technologies for Satellites
09_EvolutionOfComms_FA.FH11 24/4/08 3:09 pm Page 1 C M Y CM MY CY CMY K Evolution of Communications Payload Technologies for Satellites Composite 09_EvolutionOfComms_FA.FH11 24/4/08 3:09 pm Page 2 C M Y CM MY CY CMY K ABSTRACT Space is the military’s loftiest “high ground”. Historically, whoever held high ground had a significant advantage over its adversaries. This age-old principle is still true in today’s wireless communications planning and siting of a base station or relay point, where a high point will ensure the best coverage and clear line of sight conditions to the end communicator. However, with the wide availability and use of satellites in all sectors of society, there is now a growing trend for satellite communications to be more than just relay or “bent-pipe”. With some intelligent design and processing capabilities incorporated on board, satellites are able to meet the growing complexities of info-communications. Liew Hui Ming Koh Wee Sain Lee Yuen Sin Ter Yin Wei Composite 09_EvolutionOfComms_FA.FH11 24/4/08 3:09 pm Page 3 C M Y CM MY CY CMY K Evolution of Communications Payload Technologies 104 for Satellites satellite systems are designed, implemented INTRODUCTION and operated. This article will focus on the key technology advancements in Satellite Satellites have traditionally been bent-pipe Communications (SATCOM) payloads used for devices for relaying information over large telecommunications services. geographical areas in a single transmission, under the same coverage beam. The bent-pipe To set the context of the various types of payloads used in most of today’s networks satellite payloads that were designed, a brief perform purely frequency translation and description on the different types of orbits for signal amplification functions before the satellites and an outline on the international re-transmission of data to the ground. -
STARSHIP USERS GUIDE Revision 1.0 | March 2020
STARSHIP USERS GUIDE Revision 1.0 | March 2020 COPYRIGHT Subject to the existing rights of third parties, Space Exploration Technologies Corp. (SpaceX) is the owner of the copyright in this work, and no portion hereof is to be copied, reproduced, or disseminated without the prior written consent of SpaceX. © Space Exploration Technologies Corp. All rights reserved. STARSHIP PAYLOAD GUIDE COMPANY DESCRIPTION SpaceX was founded in 2002 to revolutionize access to space and enable a multi-planetary society. Today, SpaceX performs routine missions to space with its Falcon 9 and Falcon Heavy launch vehicles for a diverse set of customers, including the National Aeronautics and Space Administration (NASA), the Department of Defense, international governments, and leading commercial companies. SpaceX provides further support to NASA with the Dragon spacecraft by conducting cargo resupply and return missions to and from the International Space Station (ISS). Soon, SpaceX will begin transporting crew to the ISS as well. To offer competitive launch and resupply services, SpaceX has incorporated reusability into the Falcon and Dragon systems, which improves vehicle reliability while reducing cost. The Starship Program now leverages SpaceX’s experience to introduce a next- generation, super heavy-lift space transportation system capable of rapid and reliable reuse. STARSHIP PROGRAM OVERVIEW SpaceX’s Starship system represents a fully reusable transportation system designed to service Earth orbit needs as well as missions to the Moon and Mars. This two-stage vehicle—composed of the Super Heavy rocket (booster) and Starship (spacecraft) as shown in Figure 1—is powered by sub-cooled methane and oxygen. Starship is designed to evolve rapidly to meet near term and future customer needs while maintaining the highest level of reliability. -
Financial Operational Losses in Space Launch
UNIVERSITY OF OKLAHOMA GRADUATE COLLEGE FINANCIAL OPERATIONAL LOSSES IN SPACE LAUNCH A DISSERTATION SUBMITTED TO THE GRADUATE FACULTY in partial fulfillment of the requirements for the Degree of DOCTOR OF PHILOSOPHY By TOM ROBERT BOONE, IV Norman, Oklahoma 2017 FINANCIAL OPERATIONAL LOSSES IN SPACE LAUNCH A DISSERTATION APPROVED FOR THE SCHOOL OF AEROSPACE AND MECHANICAL ENGINEERING BY Dr. David Miller, Chair Dr. Alfred Striz Dr. Peter Attar Dr. Zahed Siddique Dr. Mukremin Kilic c Copyright by TOM ROBERT BOONE, IV 2017 All rights reserved. \For which of you, intending to build a tower, sitteth not down first, and counteth the cost, whether he have sufficient to finish it?" Luke 14:28, KJV Contents 1 Introduction1 1.1 Overview of Operational Losses...................2 1.2 Structure of Dissertation.......................4 2 Literature Review9 3 Payload Trends 17 4 Launch Vehicle Trends 28 5 Capability of Launch Vehicles 40 6 Wastage of Launch Vehicle Capacity 49 7 Optimal Usage of Launch Vehicles 59 8 Optimal Arrangement of Payloads 75 9 Risk of Multiple Payload Launches 95 10 Conclusions 101 10.1 Review of Dissertation........................ 101 10.2 Future Work.............................. 106 Bibliography 108 A Payload Database 114 B Launch Vehicle Database 157 iv List of Figures 3.1 Payloads By Orbit, 2000-2013.................... 20 3.2 Payload Mass By Orbit, 2000-2013................. 21 3.3 Number of Payloads of Mass, 2000-2013.............. 21 3.4 Total Mass of Payloads in kg by Individual Mass, 2000-2013... 22 3.5 Number of LEO Payloads of Mass, 2000-2013........... 22 3.6 Number of GEO Payloads of Mass, 2000-2013.......... -
April 1998 Volume 3, Issue 2
A publication of Technical Editor Robert C. Reynolds NASA Johnson Space Center Managing Editor Houston, Texas 77058 Cindi A. Karpiuk April 1998 Volume 3, Issue 2. NEWS Three Upper Stage Breakups in One Week Top February Debris Activity Observations by the U.S. Space Surveillance determined; sixty-three of these debris had of the vehicle at the time of the breakup was 435 Network (SSN) have confirmed a trio of upper been officially cataloged by early March. The km by 35,875 km with an inclination of 7.3 stage breakups during the week of 15 February 1360 kg upper stage was in an orbit of degrees. The first indication of an event came involving former Soviet, European, and approximately 940 km by 960 km with an when Millstone radar personnel, using data from Japanese vehicles, two of which had been in inclination of 82.6 degrees. The debris were the Eglin radar, linked four new objects with the orbit for about a decade. February also thrown into orbits spanning an altitude regime Ariane vehicle. Specialists at Naval Space witnessed two fragmentations associated with of 300 km by 1200 km. Naval Space Command were then able to establish an vehicles catastrophically decaying from highly Command analysts calculated ejection approximate time of the event. Early indications elliptical orbits (see special article in this issue). velocities ranging from 15 m/s to more than were that the separation velocities were very During the quarter U.S. Naval Space Command 250 m/s. This was the second Tsyklon third low. Ariane 4 third stages on GTO missions personnel further discovered evidence for stage to breakup violently. -
89 Part 1214—Space Flight
National Aeronautics and Space Admin. Pt. 1214 § 1213.109 News releases concerning 1214.203 Optional reflight guarantee. international activities. 1214.204 Patent and data rights. 1214.205 Revisit and/or retrieval services. (a) Releases of information involving 1214.206 Damage to payload. NASA activities, views, programs, or 1214.207 Responsibilities. projects involving another country or APPENDIX A TO SUBPART 1214.2—COSTS FOR an international organization require WHICH NASA SHALL BE REIMBURSED prior coordination and approval by the APPENDIX B TO SUBPART 1214.2—OCCUPANCY Headquarters offices of External Rela- FEE SCHEDULE tions and Public Affairs. (b) NASA Centers and Headquarters Subpart 1214.3—Payload Specialists for offices will report all visits proposed by Space Transportation System (STS) Missions representatives of foreign news media 1214.300 Scope. to the Public Affairs Officer of the Of- 1214.301 Definitions. fice of External Relations for appro- 1214.302 Background. priate handling consistent with all 1214.303 Policy. NASA policies and procedures. 1214.304 Process. 1214.305 Payload specialist responsibilities. 1214.306 Payload specialist relationship with PART 1214—SPACE FLIGHT sponsoring institutions. Subpart 1214.1—General Provisions Re- Subpart 1214.4—International Space garding Space Shuttle Flights of Pay- Station Crew loads for Non-U.S. Government, Reim- 1214.400 Scope. bursable Customers 1214.401 Applicability. Sec. 1214.402 International Space Station crew- 1214.100 Scope. member responsibilities. 1214.101 Eligibility for flight of a non-U.S. 1214.403 Code of Conduct for the Inter- government reimbursable payload on the national Space Station Crew. Space Shuttle. 1214.404 Violations. 1214.102 Definitions.