A Design of Coreless Permanent Magnet Axial Flux Generator for Low Speed Wind Turbine
Total Page:16
File Type:pdf, Size:1020Kb
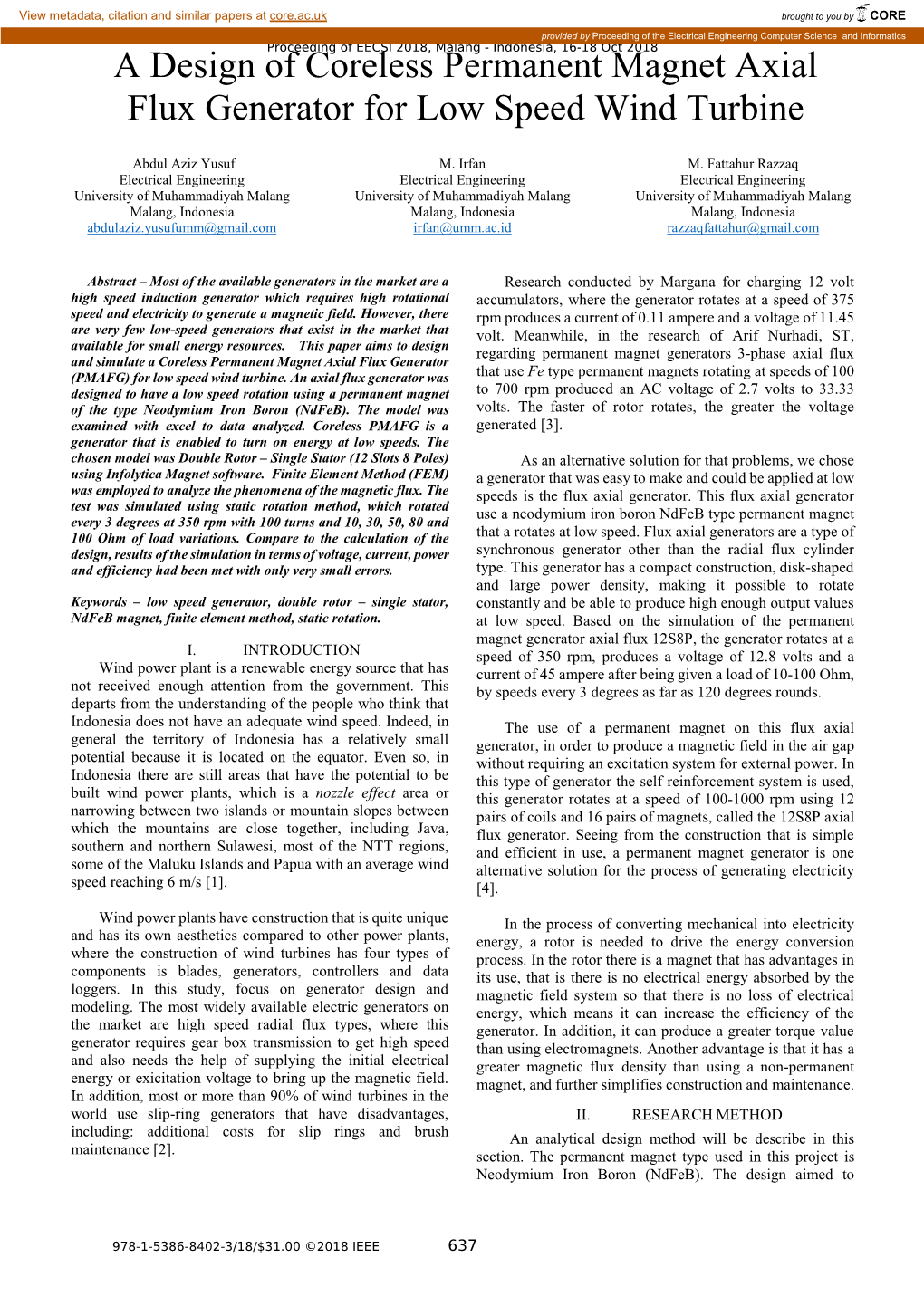
Load more
Recommended publications
-
Determination of Dy Substitution Site in Nd2-Xdyxfe14b by HAADF-STEM
www.nature.com/scientificreports OPEN Determination of Dy substitution site in Nd 2−xDyxFe14B by HAADF‑STEM and illustration of magnetic anisotropy of “g” and “f” sites, before and after substitution Syed Kamran Haider1,2,3,6, Min‑Chul Kang4,6, Jisang Hong5, Young Soo Kang3*, Cheol‑Woong Yang4* & Dongsoo Kim1,2* Nd2Fe14B and Nd2−xDyxFe14B (x = 0.25, 0.50) particles were prepared by the modifed co‑precipitation followed by reduction–difusion process. Bright feld scanning transmission electron microscope (BF‑STEM) image revealed the formation of Nd–Fe–B trigonal prisms in [− 101] viewing zone axis, confrming the formation of Nd2Fe14B/Nd2−xDyxFe14B. Accurate site for the Dy substitution in N d2Fe14B crystal structure was determined as “f” site by using high‑angle annular dark feld scanning transmission electron microscope (HAADF‑STEM). It was found that all the “g” sites are occupied by the Nd, meanwhile Dy occupied only the “f” site. Anti‑ferromagnetic coupling at “f” site decreased the magnetic moment values for Nd1.75Dy0.25Fe14B (23.48 μB) and Nd1.5Dy0.5Fe14B (21.03 μB) as compared to Nd2Fe14B (25.50 μB). Reduction of magnetic moment increased the squareness ratio, coercivity and energy product. Analysis of magnetic anisotropy at constant magnetic feld confrmed that “f” site substitution did not change the patterns of the anisotropy. Furthermore, magnetic moment of Nd2Fe14B, Nd2−xDyxFe14B, Nd (“f” site), Nd (“g” site) and Dy (“f” site) was recorded for all angles between 0° and 180°. Nd2Fe14B type magnets have the highest recorded maximum energy product (BH)max among permanent magnets1–5. -
The Curiosity Guide Subject: Magnetism Investigation: 01 Season 1 Ep
The Curiosity Guide Subject: Magnetism Investigation: 01 Season 1 Ep. 5 (#105) Slow Poke Magnet Description: Magnetism vs Gravity. Who wins? Materials: 3/4 inch copper pipe or tube of aluminum foil (24 inches long) 3 small neodymium magnets that fit just inside the copper pipe by diameter Cushion 3/4 inch PVC tube or plastic conduit (24 inches long) Stopwatch Aluminum cookie sheet Procedure: 1) Hold the magnet 24 inches above the cushion and predict what will happen when the magnet is released 2) Drop the magnet through the plastic tube and time how long it takes to fall through 3) Demonstrate that the magnet does not stick to the copper and discuss that copper is nonmagnetic 4) Drop the magnet through the copper tube and time its travel through the tube 5) Predict what could cause the delayed drop 6) Repeat by dropping both magnets at the same time through the different tubes and notice the differences My Results: Explanation: This phenomenon is known as Lenz’s Law. Moving a magnetic field beside a metal that is nonmagnetic causes the electrons in the metal to move in an attempt to eliminate the magnetic field. As the electrons rearrange it stimulates an electric field and a new magnetic field in the copper. The magnet is then attracted to the new field and begins to slow down gravity’s effect on it falling through the tube. Variation with Cookie Sheet: Place the magnet on the cookie sheet to demonstrate that it is not magnetic. Place the magnet on one side of the cookie sheet and lift it up so that it can slide down. -
Critical Rare Earths, National Security, and US-China Interactions
CHILDREN AND FAMILIES The RAND Corporation is a nonprofit institution that helps improve policy and EDUCATION AND THE ARTS decisionmaking through research and analysis. ENERGY AND ENVIRONMENT HEALTH AND HEALTH CARE This electronic document was made available from www.rand.org as a public service INFRASTRUCTURE AND of the RAND Corporation. TRANSPORTATION INTERNATIONAL AFFAIRS LAW AND BUSINESS Skip all front matter: Jump to Page 16 NATIONAL SECURITY POPULATION AND AGING PUBLIC SAFETY Support RAND SCIENCE AND TECHNOLOGY Browse Reports & Bookstore TERRORISM AND Make a charitable contribution HOMELAND SECURITY For More Information Visit RAND at www.rand.org Explore the Pardee RAND Graduate School View document details Limited Electronic Distribution Rights This document and trademark(s) contained herein are protected by law as indicated in a notice appearing later in this work. This electronic representation of RAND intellectual property is provided for non- commercial use only. Unauthorized posting of RAND electronic documents to a non-RAND website is prohibited. RAND electronic documents are protected under copyright law. Permission is required from RAND to reproduce, or reuse in another form, any of our research documents for commercial use. For information on reprint and linking permissions, please see RAND Permissions. This product is part of the Pardee RAND Graduate School (PRGS) dissertation series. PRGS dissertations are produced by graduate fellows of the Pardee RAND Graduate School, the world’s leading producer of Ph.D.’s in policy analysis. The dissertation has been supervised, reviewed, and approved by the graduate fellow’s faculty committee. Dissertation Critical Rare Earths, National Security, and U.S.-China Interactions A Portfolio Approach to Dysprosium Policy Design David L. -
Securing Critical Materials for Critical Sectors Policy Options for the Netherlands and the European Union
HCSS GEO-ECONOMICS Securing Critical Materials for Critical Sectors Policy options for the Netherlands and the European Union Irina Patrahau, Ankita Singhvi, Michel Rademaker, Hugo van Manen, René Kleijn and Lucia van Geuns HCSS helps governments, non-governmental organizations and the private sector to understand the fast-changing environment and seeks to anticipate the challenges of the future with practical policy solutions and advice. Securing Critical Materials for Critical Sectors Policy options for the Netherlands and the European Union HCSS Geo-Economics The Hague Centre for Strategic Studies ISBN/EAN: 9789492102805 Authors: HCSS: Irina Patrahau, Michel Rademaker (Project Leader), Hugo van Manen, and Lucia van Geuns Centrum voor Milieuwetenschappen: Ankita Singhvi and René Kleijn December 2020 The research for and production of this report have been conducted within the PROGRESS research framework agreement. Responsibility for the contents and for the opinions expressed, rests solely with the authors and does not constitute, nor should be construed as, an endorsement by the Netherlands Ministries of Foreign Affairs and Defense. This project has been completed on behalf of the China Knowledge Network of the Government of the Netherlands. © The Hague Centre for Strategic Studies. All rights reserved. No part of this report may be reproduced and/or published in any form by print, photo print, microfilm or any other means without prior written permission from HCSS. All images are subject to the licenses of their respective owners. Design: Mihai Eduard Coliban (layout) and Constantin Nimigean (typesetting). The Hague Centre for Strategic Studies [email protected] hcss.nl Lange Voorhout 1 2514EA The Hague The Netherlands HCSS GEO-Economics Securing Critical Materials for Critical Sectors Policy options for the Netherlands and the European Union Irina Patrahau, Ankita Singhvi, Michel Rademaker, Hugo van Manen, René Kleijn and Lucia van Geuns Table of Contents Management Samenvatting 7 Executive Summary (EN) 10 1. -
Role of Substitution in Mitigating the Supply Pressure of Rare Earths in Electric Road 2 Transport Applications
SUSMAT-00036; No of Pages 11 Sustainable Materials and Technologies xxx (2017) xxx–xxx Contents lists available at ScienceDirect Sustainable Materials and Technologies journal homepage: www.elsevier.com/locate/susmat 1 Role of substitution in mitigating the supply pressure of rare earths in electric road 2 transport applications 3Q1 Claudiu C. Pavel a,⁎, Christian Thiel b, Stefanie Degreif c,DarinaBlagoevaa,MatthiasBuchertc, 4 Doris Schüler c, Evangelos Tzimas a 5 a Energy, Transport and Climate Directorate, Joint Research Centre, European Commission, Westerduinweg 3, 1755 LE Petten, The Netherlands 6 b Energy, Transport and Climate Directorate, Joint Research Centre, European Commission, Enrico Fermi 2749, I - 21027 Ispra, (VA), Italy 7 c Oeko-Institut e.V., Rheinstrasse 95, 64295 Darmstadt, Germany 8 9 article info abstract 10 Article history: The development of new high-efficiency magnets and/or electric traction motors using a limited amount of 20 11 Received 7 September 2016 critical rare earths or none at all is crucial for the large-scale deployment of electric vehicles (EVs) and related 21 12 Received in revised form 6 December 2016 applications, such as hybrid electric vehicles (HEVs) and e-bikes. For these applications, we estimated the 22 13 Accepted 19 January 2017 23 14 short-term demand for high-performing NdFeB magnets and their constituent rare earths: neodymium, praseo- Available online xxxx 24 1516171819 dymium and dysprosium. In 2020, EV, HEV and e-bike applications combined could require double the amount used in 2015. To meet the global deployment target of 7.2 million EVs sales in 2020 proposed by the International 25 36 Keywords: – 26 37 Critical materials Energy Agency, the demand for NdFeB in the EV sector might increase by up to 14 times in only 5 years (2015 38 Rare earths 2020). -
Ferromagnetic Material for Strong Magnetic Shielding
Advanc of em al e rn n ts Akash, Int J Adv Technol 2016, 7:4 u o i J n l T a e DOI: 10.4172/0976-4860.1000166 n c o h International Journal of Advancements i t n a o n l r o e g t y n I in Technology ISSN: 0976-4860 Short Communication Open Access Ferromagnetic Material for Strong Magnetic Shielding Akash Yadav* Department of Mechanical Engineering, The ICFAI University Dehradun, India *Corresponding author: Akash Yadav, Department of Mechanical Engineering, The ICFAI University Dehradun, India; Tel: +919997655162; E-mail: [email protected] Received date: June 12, 2016; Accepted date: June 16, 2016; Published date: July 12, 2016 Copyright: © 2016 Yadav A. This is an open-access article distributed under the terms of the Creative Commons Attribution License, which permits unrestricted use, distribution, and reproduction in any medium, provided the original author and source are credited. Abstract Purpose of this research is to find out the effective way to shield the magnets by using two most common available materials that is iron and steel. The material that is available in market they shield less magnetic field and also are costly. If you want to shield the higher magnetic field you have to expense a lot. To shield the magnetic field you have to make the sheet and wrapped it around the magnet, but thickness of shielded plates varies with the type of magnet and the power of magnet. Finally here we have a better material that can shield your magnet and can save your 100s of equipment that you are using. -
Investigation of the Electrowinning of Neodymium Oxide in Room Temperature Ionic Liquid
INVESTIGATION OF THE ELECTROWINNING OF NEODYMIUM OXIDE IN ROOM TEMPERATURE IONIC LIQUID by Partaksh Sidhu A thesis submitted to the Faculty and the Board of Trustees of the Colorado School of Mines in partial fulfillment of the requirements for the degree of Master of Science (Metallurgical and Materials Engineering). Golden, Colorado Date Signed: ____________________________ Partaksh Sidhu Signed: ____________________________ Dr. Patrick Taylor Thesis Advisor Golden, Colorado Date ______________________________ Signed: ____________________________ Dr. Angus Rockett Professor and Department Head Department of Metallurgical and Materials Engineering ii ABSTRACT Neodymium has widespread applications in magnets, electronics, optical and laser materials. Currently, neodymium is produced using high-temperature molten salts processes that are very energy intensive and costly. There has been ongoing efforts to develop a technique for production of neodymium from neodymium oxide at low temperatures. Electrowinning technique for reduction of neodymium oxide in room temperature ionic liquid is designed, discussed and evaluated. The chemical process for synthesis of Nd(TFSI)3 from Nd2O3 and hydrogen-cation- based ionic liquid (HTFSI) is described. The electrochemical behavior and the electrodeposition of neodymium in hydrogen-cation-based ionic liquid are investigated. The cyclic voltammetric measurements are conducted and discussed to show one-step reduction of the trivalent neodymium ion in hydrogen-cation-based ionic liquid. The electrodeposition -
Strong Magnetic Shielding by Common Available Material
Advanc of em al e rn n u ts o i J n l T a e n c o h International Journal of Advancements i t n a o n l r o Akash, Int J Adv Technol 2016, 7:4 e g t y n I in Technology DOI: 10.4172/0976-4860.1000168 ISSN: 0976-4860 Short Communication Open Access Strong Magnetic Shielding by Common Available Material Akash Yadav* Department of Mechanical Engineering, The ICFAI University Dehradun, India *Corresponding author: Akash Yadav, Department of Mechanical Engineering, The ICFAI University Dehradun, India; Tel: +919997655162; E-mail: [email protected] Received date: June 12, 2016; Accepted date: June 16, 2016; Published date: July 12, 2016 Copyright: © 2016 Yadav A. This is an open-access article distributed under the terms of the Creative Commons Attribution License, which permits unrestricted use, distribution, and reproduction in any medium, provided the original author and source are credited. Abstract Purpose of this research paper is to find way to shield a very strong magnet that is of neodymium n50 grades or any other grade. There are several places where we require to shield the magnets completely or some sides/part of it. There are materials available in market for shielding but they are costly. The main aspect of this paper is to find a material by which we can shield very strong magnetic field and the cost can be reduced by significant amount. The method is to use many different common available material to shield it which are available commonly. The material that are being used are ferromagnetic, paramagnetic and diamagnetic. -
A COVID Curiosity: Transurethral Insertion of Neodymium Magnets in Pediatric Patients
Case Series Clinics in Surgery Published: 25 May, 2021 A COVID Curiosity: Transurethral Insertion of Neodymium Magnets in Pediatric Patients Shekarriz Arman1, Upadhyay Jyoti2* and Carr Michael2 1Duke University, Pratt School of Engineering, USA 2Children’s Hospital of the Kings Daughters and Eastern Virginia Medical School, USA Abstract Rare-earth metal magnets are a growing problem in the pediatric population with ingestion into the GI tract as the most prominent route. Neodymium magnet transurethral insertion has been reported in 6 pediatric patients in the literature. All of these, except one, have required an open surgical approach for removal. We provide three additional cases, all of whom have behavioral health concerns, with two patients presenting during the COVID-19 pandemic. We describe the use of a self-made magnetic device for successful retrieval of this unique foreign body from the bladder of a pediatric patient. Two patients presented in a timely manner whereas one patient presented during the pandemic but admitted to placing these magnets in his urethra a least one year prior. Clinicians should be aware of the signs and symptoms associated with this rare tendency of transurethral insertion of strong magnets in pediatric patients, the association with behavioral health diagnoses as well as environmental stressors due to the effects of COVID-19 pandemic, which may contribute to this occurrence. Key Points 1) COVID-19 pandemic and other environmental stressors increase the propensity for self- harm in patients with behavioral health disease. 2) Neodymium rare-earth magnets transurethral insertion is increasing in the pediatric population, which are difficult to treat endoscopically. -
Role of Substitution in Mitigating the Supply Pressure of Rare Earths in Electric Road Transport Applications
Sustainable Materials and Technologies 12 (2017) 62–72 Contents lists available at ScienceDirect Sustainable Materials and Technologies journal homepage: www.elsevier.com/locate/susmat Role of substitution in mitigating the supply pressure of rare earths in electric road transport applications Claudiu C. Pavel a,⁎, Christian Thiel b, Stefanie Degreif c,DarinaBlagoevaa, Matthias Buchert c, Doris Schüler c, Evangelos Tzimas a a Energy, Transport and Climate Directorate, Joint Research Centre, European Commission, Westerduinweg 3, 1755 LE Petten, The Netherlands b Energy, Transport and Climate Directorate, Joint Research Centre, European Commission, Enrico Fermi 2749, I - 21027 Ispra, (VA), Italy c Oeko-Institut e.V., Rheinstrasse 95, 64295 Darmstadt, Germany article info abstract Article history: The development of new high-efficiency magnets and/or electric traction motors using a limited amount of crit- Received 7 September 2016 ical rare earths or none at all is crucial for the large-scale deployment of electric vehicles (EVs) and related appli- Received in revised form 6 December 2016 cations, such as hybrid electric vehicles (HEVs) and e-bikes. For these applications, we estimated the short-term Accepted 19 January 2017 demand for high-performing NdFeB magnets and their constituent rare earths: neodymium, praseodymium and Available online 23 January 2017 dysprosium. In 2020, EV, HEV and e-bike applications combined could require double the amount used in 2015. To meet the global deployment target of 7.2 million EVs sales in 2020 proposed by the International Energy Agen- Keywords: – Critical materials cy, the demand for NdFeB in the EV sector might increase by up to 14 times in only 5 years (2015 2020). -
Making and Breaking Magnets
Making and Breaking Magnets Overview Can you turn a paper clip into a magnet? If you create a magnet, can you then take away the magnetic-ness? The answer to both questions is ‘yes’; let’s investigate how and why. Doing the activity Carefully unwrap the neodymium magnet (keep it away from credit Necessary materials: cards, cell phones, computers, other magnets, etc.); you have two • neodymium magnet* paper clips included in the bag with this magnet. If you just touch the • paper clips paper clips together, can you pick one up using the other? Now, tap *Be careful with this magnet! It’s the end of one of the paper clips against the neodymium magnet very strong, and can wipe credit about 10 times. Try picking up the other paperclip again — what cards, do bad things to cell phones, happens now? If you drop the paper clip you tapped against the break if it “jumps” to a surface, etc. magnet onto a hard surface, does anything change when you try to pick up the other paper clip? What’s happening The paper clips are made of steel, which is ferromagnetic because it contains iron. As we discussed in the Magnetic Surprises activity, ferromagnetic materials aren’t permanent magnets on their own, the way the neodymium magnet is, but they can be magnetized by a strong magnetic field. Ferromagnetic objects contain lots of little magnetic subunits called magnetic domains. When the object isn’t in a magnetic field, these domains aren’t organized in any particular way. The north and south poles of the domains all point in different directions, so overall, the material doesn’t act like a magnet (for more on magnetic poles, see the Refrigerator Magnets activity). -
US Department of Energy (2011) Critical Materials Strategy / Report
THIS PAGE INTENTIONALLY LEFT BLANK U.S. DEPARTMENT OF ENERGY CRITICAL MATERIALS STRATEGY DECEMBER 2011 i THIS PAGE INTENTIONALLY LEFT BLANK ii TABLE OF CONTENTS FOREWORD ........................................................................................................................................................... 1 ACKNOWLEDGEMENTS .......................................................................................................................................... 2 EXECUTIVE SUMMARY ........................................................................................................................................... 3 CHAPTER 1. INTRODUCTION .................................................................................................................................. 8 CHAPTER 2. USE OF KEY MATERIALS IN CLEAN ENERGY TECHNOLOGIES .............................................................. 14 CHAPTER 3. MARKET DYNAMICS AND CHARACTERIZATION ................................................................................ 37 CHAPTER 4. SUPPLY AND DEMAND PROJECTIONS ............................................................................................... 77 CHAPTER 5. CRITICALITY ASSESSMENT ............................................................................................................... 113 CHAPTER 6. PROGRAM DIRECTIONS .................................................................................................................. 120 APPENDIX A. CRITICALITY ASSESSMENTS BY ELEMENT .....................................................................................