Soil-Structure Interaction Scoping Phase 1
Total Page:16
File Type:pdf, Size:1020Kb
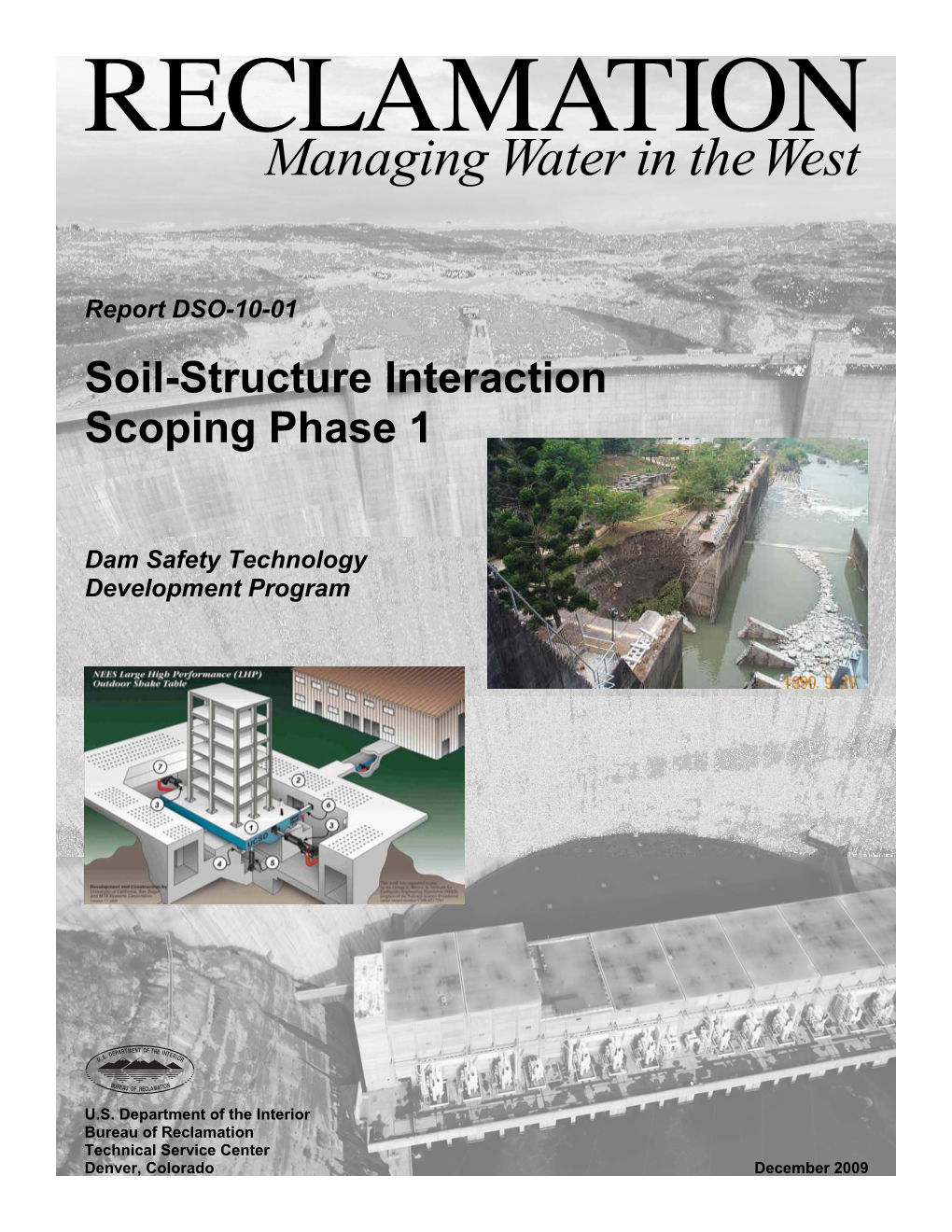
Load more
Recommended publications
-
Determination of Earth Pressure Distributions for Large-Scale Retention Structures
DETERMINATION OF EARTH PRESSURE DISTRIBUTIONS FOR LARGE-SCALE RETENTION STRUCTURES J. David Rogers, Ph.D., P.E., R.G. Geological Engineering University of Missouri-Rolla DETERMINATION OF EARTH PRESSURE DISTRIBUTIONS FOR LARGE-SCALE RETENTION STRUCTURES 1.0 Introduction Various earth pressure theories assume that soils are homogeneous, isotropic and horizontally inclined. These assumptions lead to hydrostatic or triangular pressure distributions when calculating the lateral earth pressures being exerted against a vertical plane. Field measurements on deep retained excavations have shown that the average earth pressure load is approximately uniform with depth with small reductions at the top and bottom of the excavation. This type of distribution was first suggested by Terzaghi (1943) on the basis of empirical data collected on the Berlin Subway and Chicago Subway projects between 1936-42. Since that time, it has been shown that this uniform distribution only occurs when the following conditions are met: 1. The upper portions of the vertical side walls of the excavation are supported in stages as the excavation is deepened; 2. The walls of the excavation are pervious enough so that water pressure does not build up behind them; and 3. The lateral movements of the walls are kept below 1% to 2% of the depth of the excavation. With the passage of time, the approximately uniform pressure distribution evidenced during construction has been observed to transition toward the more traditional triangular distribution. In addition, it has been found that the tie-back force in anchored bulkhead walls generally increases with time. The actual load imposed on a semi-vertical retaining wall is dependent on eight aspects of its construction: 1. -
Chapter (8) Retaining Walls
Chapter (8) Retaining Walls Foundation Engineering Retaining Walls Introduction Retaining walls must be designed for lateral earth pressure. The procedures of calculating lateral earth pressure was discussed previously in Chapter7. Different types of retaining walls are used to retain soil in different places. Three main types of retaining walls: 1. Gravity retaining wall (depends on its weight for resisting lateral earth force because it have a large weigh) 2. Semi-Gravity retaining wall (reduce the dimensions of the gravity retaining wall by using some reinforcement). 3. Cantilever retaining wall (reinforced concrete wall with small dimensions and it is the most economical type and the most common) Note: Structural design of cantilever retaining wall is depend on separating each part of wall and design it as a cantilever, so it’s called cantilever R.W. The following figure shows theses different types of retaining walls: There are another type of retaining wall called “counterfort RW” and is a special type of cantilever RW used when the height of RW became larger than 6m, the moment applied on the wall will be large so we use spaced counterforts every a specified distance to reduce the moment RW. Page (177) Ahmed S. Al-Agha Foundation Engineering Retaining Walls Where we use Retaining Walls Retaining walls are used in many places, such as retaining a soil of high elevation (if we want to construct a building in lowest elevation) or retaining a soil to save a highways from soil collapse and for several applications. The following figure explain the function of retaining walls: Page (178) Ahmed S. -
Title of Paper
Raw earth construction: is there a role for unsaturated soil mechanics ? D. Gallipoli, A.W. Bruno & C. Perlot Université de Pau et des Pays de l'Adour, Laboratoire SIAME, Anglet, France N. Salmon Nobatek, Anglet, France ABSTRACT: “Raw earth” (“terre crue” in French) is an ancient building material consisting of a mixture of moist clay and sand which is compacted to a more or less high density depending on the chosen building tech- nique. A raw earth structure could in fact be described as a “soil fill in the shape of a building”. Despite the very nature of this material, which makes it particularly suitable to a geotechnical analysis, raw earth construc- tion has so far been the almost exclusive domain of structural engineers and still remains a niche market in current building practice. A multitude of manufacturing techniques have already been developed over the cen- turies but, recently, this construction method has attracted fresh interest due to its eco-friendly characteristics and the potential savings of embodied, operational and end-of-life energy that it can offer during the life cycle of a structure. This paper starts by introducing the advantages of raw earth over other conventional building materials followed by a description of modern earthen construction techniques. The largest part of the manu- script is devoted to the presentation of recent studies about the hydro-mechanical properties of earthen materi- als and their dependency on suction, water content, particle size distribution and relative humidity. A raw earth structure therefore consists of com- pacted moist soil and may be described in geotech- 1 DEFINITION OF EARTHEN nical terms as a “soil fill in the shape of a building”. -
Chapter 3. the Crust and Upper Mantle
Theory of the Earth Don L. Anderson Chapter 3. The Crust and Upper Mantle Boston: Blackwell Scientific Publications, c1989 Copyright transferred to the author September 2, 1998. You are granted permission for individual, educational, research and noncommercial reproduction, distribution, display and performance of this work in any format. Recommended citation: Anderson, Don L. Theory of the Earth. Boston: Blackwell Scientific Publications, 1989. http://resolver.caltech.edu/CaltechBOOK:1989.001 A scanned image of the entire book may be found at the following persistent URL: http://resolver.caltech.edu/CaltechBook:1989.001 Abstract: T he structure of the Earth's interior is fairly well known from seismology, and knowledge of the fine structure is improving continuously. Seismology not only provides the structure, it also provides information about the composition, crystal structure or mineralogy and physical state. In subsequent chapters I will discuss how to combine seismic with other kinds of data to constrain these properties. A recent seismological model of the Earth is shown in Figure 3-1. Earth is conventionally divided into crust, mantle and core, but each of these has subdivisions that are almost as fundamental (Table 3-1). The lower mantle is the largest subdivision, and therefore it dominates any attempt to perform major- element mass balance calculations. The crust is the smallest solid subdivision, but it has an importance far in excess of its relative size because we live on it and extract our resources from it, and, as we shall see, it contains a large fraction of the terrestrial inventory of many elements. In this and the next chapter I discuss each of the major subdivisions, starting with the crust and ending with the inner core. -
Italy and China Sharing Best Practices on the Sustainable Development of Small Underground Settlements
heritage Article Italy and China Sharing Best Practices on the Sustainable Development of Small Underground Settlements Laura Genovese 1,†, Roberta Varriale 2,†, Loredana Luvidi 3,*,† and Fabio Fratini 4,† 1 CNR—Institute for the Conservation and the Valorization of Cultural Heritage, 20125 Milan, Italy; [email protected] 2 CNR—Institute of Studies on Mediterranean Societies, 80134 Naples, Italy; [email protected] 3 CNR—Institute for the Conservation and the Valorization of Cultural Heritage, 00015 Monterotondo St., Italy 4 CNR—Institute for the Conservation and the Valorization of Cultural Heritage, 50019 Sesto Fiorentino, Italy; [email protected] * Correspondence: [email protected]; Tel.: +39-06-90672887 † These authors contributed equally to this work. Received: 28 December 2018; Accepted: 5 March 2019; Published: 8 March 2019 Abstract: Both Southern Italy and Central China feature historic rural settlements characterized by underground constructions with residential and service functions. Many of these areas are currently tackling economic, social and environmental problems, resulting in unemployment, disengagement, depopulation, marginalization or loss of cultural and biological diversity. Both in Europe and in China, policies for rural development address three core areas of intervention: agricultural competitiveness, environmental protection and the promotion of rural amenities through strengthening and diversifying the economic base of rural communities. The challenge is to create innovative pathways for regeneration based on raising awareness to inspire local rural communities to develop alternative actions to reduce poverty while preserving the unique aspects of their local environment and culture. In this view, cultural heritage can be a catalyst for the sustainable growth of the rural community. -
Earth's Structure and Processes 8-3 the Student Will Demonstrate An
Earth’s Structure and Processes 8-3 The student will demonstrate an understanding of materials that determine the structure of Earth and the processes that have altered this structure. (Earth Science) 8-3.1 Summarize the three layers of Earth – crust, mantle, and core – on the basis of relative position, density, and composition. Taxonomy level: 2.4-B Understand Conceptual Knowledge Previous/future knowledge: Students in 3rd grade (3-3.5, 3-3.6) focused on Earth’s surface features, water, and land. In 5th grade (5-3.2), students illustrated Earth’s ocean floor. The physical property of density was introduced in 7th grade (7-5.9). Students have not been introduced to areas of Earth below the surface. Further study into Earth’s internal structure based on internal heat and gravitational energy is part of the content of high school Earth Science (ES-3.2). It is essential for students to know that Earth has layers that have specific conditions and composition. Layer Relative Position Density Composition Crust Outermost layer; thinnest Least dense layer overall; Solid rock – mostly under the ocean, thickest Oceanic crust (basalt) is silicon and oxygen under continents; crust & more dense than Oceanic crust - basalt; top of mantle called the continental crust (granite) Continental crust - granite lithosphere Mantle Middle layer, thickest Density increases with Hot softened rock; layer; top portion called depth because of contains iron and the asthenosphere increasing pressure magnesium Core Inner layer; consists of Heaviest material; most Mostly iron and nickel; two parts – outer core and dense layer outer core – slow flowing inner core liquid, inner core - solid It is not essential for students to know specific depths or temperatures of the layers. -
Earth Layers Rocks
Released SOL Test Questions 4. Which of these best describes the relationship between Sorted by Topic Earth’s layers? Compiled by SOLpass – www.solpass.org (2007-12) a. The hottest layers are closest to the core. SOL 5.7 Earth’s Constantly b. The more liquid layers are closest to the crust. Changing Surface c. The lightest layers are closest to the core. The student will investigate and understand how Earth’s d. The more metallic layers are closest to the crust. surface is constantly changing. Key concepts include 5. What layer of Earth is located just below the crust? a) identification of rock types (2007-26) b) the rock cycle and how transformations between rocks a. Inner core occur b. Mantle c) Earth history and fossil evidence c. Continental shelf d) the basic structure of Earth’s interior d. Outer core e) changes in Earth’s crust due to plate tectonics 6. Which of these Earth layers is the thinnest? f) weathering, erosion, and deposition; and (2003-24) g) human impact a. The inner core b. The outer core EARTH LAYERS c. The mantle 1. Which layer of Earth is the thinnest? d. The crust (2011-34) a. Inner core ROCKS b. Crust 7. Pumice is formed when lava from a volcano cools. Which c. Outer core rock type is pumice? d. Mantle (2011-26) a. Gaseous rock 2. Earth is composed of four layers. Many scientists believe that as Earth cooled, the denser materials sank to the b. Igneous rock center and the less dense materials rose to the top. -
Risk Assessment and Spatial Variability in Geotechnical Stability
RISK ASSESSMENT AND SPATIAL VARIABILITY IN GEOTECHNICAL STABILITY PROBLEMS by Pooya Allahverdizadeh Sheykhloo Copy rights by Pooya Allahverdizadeh Sheykhloo 2015 All Rights Reserved A thesis submitted to the Faculty and the Board of Trustees of the Colorado School of Mines in partial fulfillment of the requirements for the degree of Doctor of Philosophy (Civil and Environmental Engineering). Golden, Colorado Date ________________ Signed: _____________________________ Pooya Allahverdizadeh Sheykhloo Signed: _____________________________ Dr. D. V. Griffiths Thesis Advisor Golden, Colorado Date ________________ Signed: ______________________ Dr. John E. McCray Professor and Head Department of Civil and Environmental Engineering ii ABSTRACT Reliability analysis has gained considerable popularity in practice and academe as a way of quantifying and managing geotechnical risk in the face of uncertain input parameters. The purpose of this study is to investigate the influence of soil spatial variability on the probability of failure of different geotechnical engineering problems, including block compression, bearing capacity of strip footings, passive and active earth pressure and slope stability problems. The primary methodology will be the Random Finite Element Method (RFEM) which combines finite element analysis with random field theory and Monte-Carlo simulation. The influence of the spatial correlation length of soil properties on design outcomes has been assessed in detail through parametric studies. Results from traditional Factor of Safety approaches have been compared with those from probabilistic analysis. In addition, the influence of the coefficient of variation of the input random variables and two different input random variable distribution functions on the probability of failure have been studied. The concept of a “worst case” spatial correlation length has been examined in detail, and was observed in all the geotechnical problems considered in this thesis. -
Evaluation of Seismic Performance in Mechanically Stabilized Earth Structures
Evaluation of seismic performance in Mechanically Stabilized Earth structures J.E. Sankey The Reinforced Earth Company, Vienna, Virginia – USA P. Segrestin Freyssinet International, Velizy, France ABSTRACT: Recent earthquake events have brought about renewed interest in the response of a variety of structures to seismic loads. In the case of mechanically stabilized earth structures, such as Reinforced Earth®, current seismic design codes do not appear to fully incorporate their inherent flexibility. A brief catalogue of major earthquakes and corresponding descriptions regarding the condition of local Reinforced Earth structures is provided to demonstrate the realistic flexibility of the structures. A call for better consideration of the ductile response of Reinforced Earth is recommended based on its flexible composition of discrete steel reinforcements and select soil matrix. 1 BACKGROUND subjected to seismic events in the Northridge, Kobe and Izmit Earthquakes. The actual physical In the last decade there have been major earthquake condition will then be compared to the criteria used events in the United States (Northridge, California, in design for the walls. Even in cases where the 1994, 6.7 Richter magnitude), Japan (Great Hanshin, seismic accelerations exceeded the design Kobe, 1995, 7.2 Richter magnitude), and Turkey accelerations, it will be shown that little if any (North Anatolian, Izmit, 1999, 7.4 Richter distress resulted. The rationale shall be presented magnitude). The Northridge Earthquake was that the ductility of the Reinforced Earth may allow responsible for 57 deaths, 11,000 injuries and $20 minor permanent deflections to occur without billion US in damages. The Kobe Earthquake was a distress that would affect service life. -
Lecture Liquefaction of Soils During Earthquakes I.M
LECTURE LIQUEFACTION OF SOILS DURING EARTHQUAKES I.M. Idriss Woodward-Clyde Consultants San Francisco, California, U.S.A. DEFINITION OF TERMS The following definitions perta1n1ng to cyclic loading conditions are based on slight modifications of those originally proposed by Lee and Seed (1967). FAILURE: When the induced cyclic: strains become excessive. COMPLETE LIQUEFACTION: When a soil exhibits no resistance to de formation over a wide strain range. PARTIAL LIQUEFACTION: When a soil exhibits no resistance to de formation over a strain range less than that considered to cons titute failure. INITIAL LIQUEFACTION: When a soil first exhibits any degree of partial liquefaction during cyclic loading. Ordinarily, the fir@t condition reached is INITIAL LIQUEFACTION, followed by PARTIAL, and COMPLETE liquefaction, with FAILURE being reached at some stage during the partial or complete liquefaction stages. The following definitions are given by Seed, Arango and Chan (1975) : INITIAL LIQUEFACTION: Denotes a condition where ,during the course of cyclic stress applications, the residual pore water pressure on completion of any full stress cycle becomes equal to the applied 507 J. B. MlUtins (ed.), Numerical Methods in GeomechanicB, 507-530. Copyright e 1982 by D. Reidel Publishing Company. 508 1. M.IDRISS confining pressure; the development of initial liquefaction has no implications concerning the magnitude of the deformations which the soil might subsequently undergo; however,it defines a condition which is a useful basis for assessing various possible forms of subsequent soil behavior. INITIAL LIQUEFACTION WITH LIMITED STRAIN POTENTIAL OR CYCLIC MOBI LITY: Denotes a condition in which cyclic stress applications develop a condition of initial liquefaction and subsequent cyclic stress applications cause limited strains to develop either be cause of the remaining resistance of the soil to deformation or because the soil dilates, the pore pressure drops, and the soil stabilizes under the applied loads. -
Reinforced Earth: Principles and Applications in Engineering Construction
International Journal of Advanced Academic Research | Sciences, Technology & Engineering | ISSN: 2488-9849 Vol. 2, Issue 6 (June 2016) REINFORCED EARTH: PRINCIPLES AND APPLICATIONS IN ENGINEERING CONSTRUCTION Okechukwu, S.I; Okeke, O. C; Akaolisa, C. C. Z; Jack, L. And Akinola, A. O. Department of Geology, Federal University of Technology, Owerri, Imo State, Nigeria Abstract Reinforced earth is a material formed by combining earth and reinforcement material. The reinforced soil is obtained by placing extensible or inextensible materials such as metallic strips or polymeric reinforcement within the soil to obtain the requisite properties. The reinforcement enables the soil mass to resist tension in a way which the earth alone could not. The source of this resistance to tension is the internal friction of soil, because the stresses that are created within the mass are transferred from soil to the reinforcement strips by friction. Reinforcement of soil is practiced to improve the mechanical properties of the soil being reinforced by the inclusion of structural elements. The reinforcement improves the earth by increasing the bearing capacity of the soil. It also reduces the liquefaction behavior of the soil. Reinforced earth is not complex to achieve. The components of reinforced earth are soil, skin and reinforcing material. The reinforcing material may include steel, concrete, glass, planks etc. Reinforced earth has so many applications in construction work. Some of the applications include its use in stabilization of soil, construction of retaining walls, bridge abutments for highways, industrial and mining structures. Keywords: Reinforcement, Reinforced earth. 1.0 Introduction An internally stabilized system such as reinforced earth involves reinforcements installed within and extending beyond the potential failure mass. -
Framework for Estimation of the Lateral Earth Pressure on Retaining Structures with Expansive and Non-Expansive Soils As Backfil
FRAMEWORK FOR ESTIMATION OF THE LATERAL EARTH PRESSURE ON RETAINING STRUCTURES WITH EXPANSIVE AND NON-EXPANSIVE SOILS AS BACKFILL MATERIAL CONSIDERING THE INFLUENCE OF ENVIRONMENTAL FACTORS by Jiaying Guo Thesis submitted to the Faculty of Graduate and Postdoctoral Studies in partial fulfillment of the requirements for the degree of Master of Applied Science in Civil Engineering Department of Civil Engineering Faculty of Engineering, University of Ottawa Ottawa, Ontario, Canada © Jiaying Guo, Ottawa, Canada, 2016 DEDICATION I dedicate this thesis to my beloved parents ii ACKNOWLEDGEMENT The completion of this thesis could not have been possible without the help of Prof. Sai K. Vanapalli, my beloved supervisor. His expertise, patience, consistent guidance and unconditional supports have helped me bring this thesis into reality. I would like to thank my colleagues at the University of Ottawa: Zhong Han, Hongyu Tu, Shunchao Qi, Yunlong Liu, Ping Li, Penghai Yin, and Junping Ren. These graduate students are extremely hardworking individuals and passionate with their research in the area of unsaturated soils. It has been a great pleasure jointly working with this talented group of students. I have immensely benefited from their friendship, encouragement and continuous support. I would also like to take this opportunity to thank my parents. Without their support, encouragement and understanding, it would not have been possible for me to achieve my goals of higher education. iii ABSTRACT Lateral earth pressures (LEP) that arise due to backfill on retaining structures are typically determined by extending the principles of saturated soil mechanics. However, there is evidence in the literature to highlight the LEP on retaining structures due to the influence of soil backfill in saturated and unsaturated conditions are significantly different.