A First-Principle Power and Energy Model for Evtol Vehicles
Total Page:16
File Type:pdf, Size:1020Kb
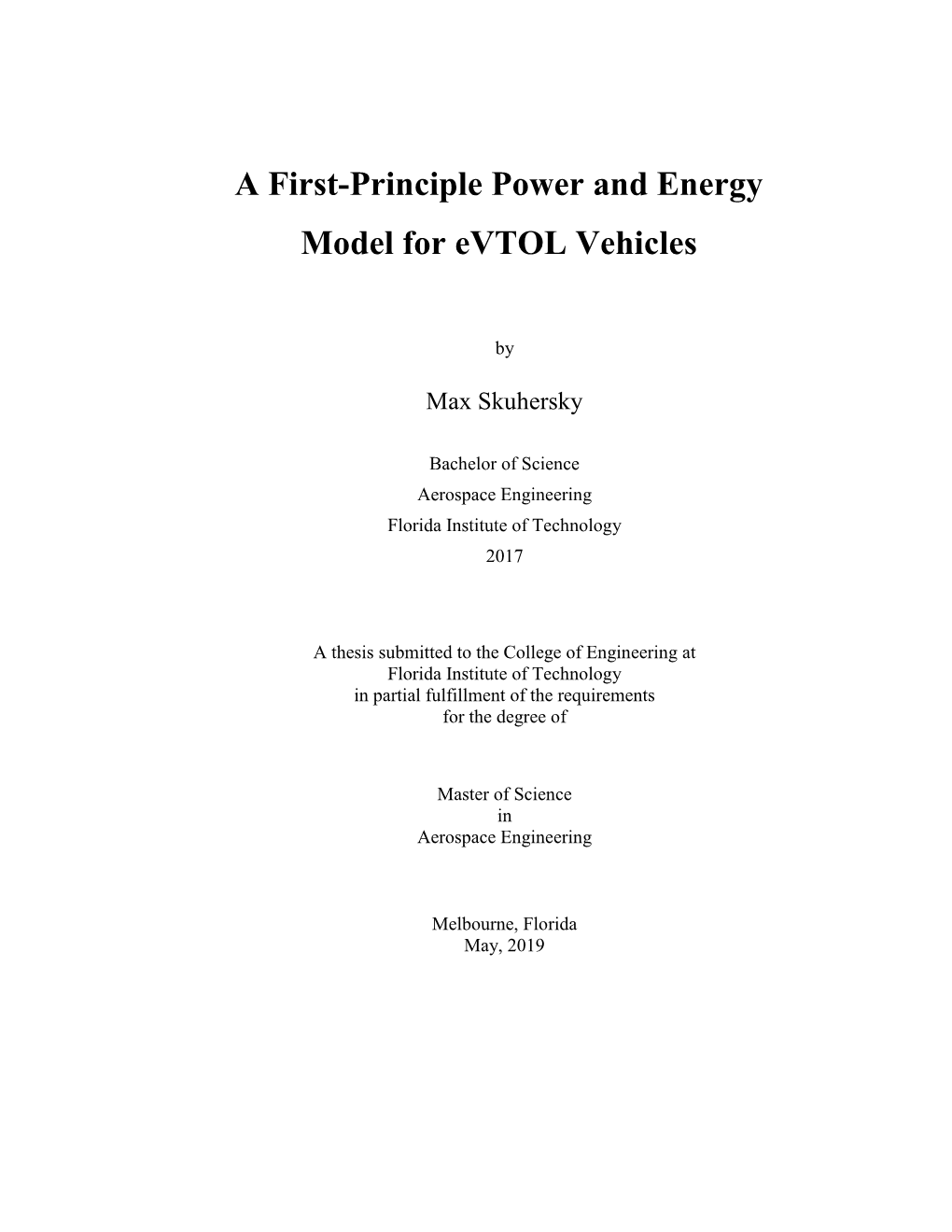
Load more
Recommended publications
-
THE ROADMAP to Scalable Urban Air Mobility
THE ROADMAP to scalable urban air mobility White paper 2.0 We bring urban air mobility to life. FOREWORD BY THE CEO MAKING HISTORY When I joined Volocopter in 2015, an amazing team of innovators had already made aviation history. With a dream, a yoga ball,1 and a new configuration of distributed electric vertical takeoff and landing (eVTOL) technology, Volocopter pioneered the way for electric passenger flights as early as 2011. Since then, Volocopter has relentlessly pursued its dream and continued to make great strides. I have witnessed the idea of electric flight grow into a fully-fledged initiative to bring seamless urban air mobility to cities. It’s true, we developed a revolutionary aircraft. But in fact, we launched the creation of an entire industry. The yoga ball evolved into the first certified multicopter, and Volocopter evolved to become the world’s first and only electric multicopter company with Design Organisation Approval (DOA) from the European Union Aviation Safety Agency (EASA). Five years, six very public flights, and two city commitments later, Volocopter continues to lead the pack as the “Pioneer of Urban Air Mobility” both in certification and in robust partnerships. We have set the stage for the next transformative industry. BRINGING URBAN AIR MOBILITY TO LIFE As the category-defining company, we are investing in multidimensional mobility. And as a team, we are engineering it. Volocopter has combined cutting-edge eVTOL technology with a holistic partnership approach as we build the world’s first fully electric, scalable UAM business for affordable air taxi services in cities. -
General Aviation Aircraft Propulsion: Power and Energy Requirements
UNCLASSIFIED General Aviation Aircraft Propulsion: Power and Energy Requirements • Tim Watkins • BEng MRAeS MSFTE • Instructor and Flight Test Engineer • QinetiQ – Empire Test Pilots’ School • Boscombe Down QINETIQ/EMEA/EO/CP191341 RAeS Light Aircraft Design Conference | 18 Nov 2019 | © QinetiQ UNCLASSIFIED UNCLASSIFIED Contents • Benefits of electrifying GA aircraft propulsion • A review of the underlying physics • GA Aircraft power requirements • A brief look at electrifying different GA aircraft types • Relationship between battery specific energy and range • Conclusions 2 RAeS Light Aircraft Design Conference | 18 Nov 2019 | © QinetiQ UNCLASSIFIED UNCLASSIFIED Benefits of electrifying GA aircraft propulsion • Environmental: – Greatly reduced aircraft emissions at the point of use – Reduced use of fossil fuels – Reduced noise • Cost: – Electric aircraft are forecast to be much cheaper to operate – Even with increased acquisition cost (due to batteries), whole-life cost will be reduced dramatically – Large reduction in light aircraft operating costs (e.g. for pilot training) – Potential to re-invigorate the GA sector • Opportunities: – Makes highly distributed propulsion possible – Makes hybrid propulsion possible – Key to new designs for emerging urban air mobility and eVTOL sectors 3 RAeS Light Aircraft Design Conference | 18 Nov 2019 | © QinetiQ UNCLASSIFIED UNCLASSIFIED Energy conversion efficiency Brushless electric motor and controller: • Conversion efficiency ~ 95% for motor, ~ 90% for controller • Variable pitch propeller efficiency -
Urban Air Mobility | USD 90 Billion of Potential: How to Capture a Share of the Passenger Drone Market
Urban Air Mobility | USD 90 billion of potential: How to capture a share of the passenger drone market The Roland Berger Center for Smart Mobility MANAGEMENT SUMMARY Urban Air Mobility / USD 90 billion of potential: How to capture a share of the passenger drone market Our updated market analysis and Global Urban Air Mobility Radar show that the passenger Urban Air Mobility (UAM) market is set to soar. The number of UAM projects continues to rise, barriers to progress – such as regulation and public acceptance – are increasingly being overcome and the coronavirus crisis shows no sign of causing serious delays. By 2050, we estimate that the passenger UAM industry will generate revenues of almost USD 90 billion a year, with 160,000 commercial passenger drones plying the skies. This potential is driving the emergence of an integrated ecosystem in the nascent UAM industry, consisting of five major building blocks: eVTOL vehicles; maintenance, repair and overhaul services; flight operations; physical infrastructure; and digital infrastructure. First collaborations are forming across this ecosystem. Yet among the many disparate market players, no dominant passenger UAM player or business model has emerged yet. Instead, companies are tending towards four business model archetypes: system providers, who are involved across the value chain, and service providers, hardware providers and ticket brokers, who focus on distinct areas. Most players are currently positioning themselves as system providers to gain as much industry knowledge as possible, and we believe this trend will continue. A shake out and consolidation are likely in the coming years. Despite the lack of a proven business model, investors are strongly backing the passenger UAM industry. -
DEVELOPMENT TRENDS and PROSPECTS for Evtol
Mitsui & Co. Global Strategic Studies Institute Monthly Report June 2018 DEVELOPMENT TRENDS AND PROSPECTS FOR eVTOL: A NEW MODE OF AIR MOBILITY Hideki Kinjo Industry Innovation Dept., Technology & Innovation Studies Div. Mitsui & Co. Global Strategic Studies Institute SUMMARY Development activities are gaining momentum for “electric vertical takeoff and landing aircraft” (eVTOL), which is designed to transport several passengers over short distances by air. Technology advancements, such as batteries and motors in the automotive industry and autopilot navigation in the drone industry are the backgrounds. Many startups, as well as major aircraft manufacturers, are now entering into eVTOL aircraft development. Among the services envisioned, the US company Uber aims to launch an air taxi service in the first half of the 2020s. Challenges with respect to aircraft development have mainly to do with batteries, while on the services front, ensuring safety and securing profitability are the issues. As for eVTOL initial spread in the market, it may possibly be for first aid and other emergency response services and in emerging economies where flight regulations are less stringent. The development of electric vertical takeoff and landing aircraft (eVTOL) is gaining momentum. Three- dimensional mobility in the sky is expected to provide passengers with much shorter travel times and greater convenience. This report discusses the unique features of eVTOL, trends in aircraft development, moves in the area of services, challenges to make eVTOL travel a reality, and future prospects. eVTOL REPRESENTS A NEW MODE OF MOBILITY MADE POSSIBLE BY TRANSFERRING TECHNOLOGIES FROM OTHER INDUSTRIES The eVTOL can be described as a vehicle that fits somewhere in between a drone and a conventional airplane. -
AHS -- Future of Vertical Flight
2017 April April graphic Mike Hirschberg, Executive Director Uber AHS International The Vertical Flight Technical Society www.vtol.org 1 . Electric Vertical Take Off and Landing aircraft, aka – Transformative Vertical Flight (TVF) aircraft – Urban Air Mobility – On Demand Mobility – Urban Air Taxi graphic Nov. Nov. 2017 graphic – Not a “flying car”! Uber . Includes hybrid/electric aircraft with a combustion engine to generate electricity for long range/endurance . Creates new design freedoms by allowing power distribution through electrical cables instead of driveshafts (“power by wire” like “fly by wire”) 2 NASA Puffin Single-Seat Electric VTOL Study Volocopter VC1 Demonstrator (2010) (2010) Photo courtesy of NASA Photo courtesy of Volocopter GmbH 3 NASA GL-10 Greased Lightning Volocopter VC200 (2014 tethered, 2015 transition) (2013 tethered - 2016 manned) Photo courtesy of NASA Photo courtesy of Volocopter GmbH 4 Photos courtesy of Volocopter GmbH www.eVTOL.news Click icon for movie link Karlsruhe, Germany 5 Original 2-seat Joby S2 Current 4-seat Joby S4 12 lift/cruise propellers + 4 cruise propellers 6 lift/cruise propellers All electric All electric Graphics courtesy of Joby Aviation Santa Cruz, California, USA www.eVTOL.news Click icon for movie link 6 2-seat “Eagle” LiliumJet prototype 640 kg, all electric New 5-seat LiliumJet concept 2-seat “Eagle” LiliumJet prototype • 36 electric fans – 24 on wings – 12 on canards • 160 kt (300 km/h) • “Eagle” first flight April 2017 Graphics courtesy of Lilium Aviation Garching, Germany www.eVTOL.news Click icon for movie link 7 Single-seat 8-propeller 23%-scale flight tests tandem tiltwing completed this summer Two full-scale single-seat aircraft under construction www.eVTOL.news Graphics courtesy of A3 8 Single-seat full-scale “octo-copter” conducting extensive manned and unmanned flight testing www.eVTOL.news Graphics courtesy of EHang 9 2/3-scale technology demonstrator under construction to fly in 2019 Planned top speed is 340 kt and a range of 1,000 nm www.eVTOL.news 10 . -
Cost Analysis of Evtol Configuration Design for an Air Ambulances System in Japan
Purdue University Purdue e-Pubs CESUN Conference Cost Analysis of eVTOL Configuration Design for an Air Ambulances System in Japan Yusuke Mihara Keio University Payuhavorakulchai Pawnlada Keio University Aki Nakamoto Keio University Tsubasa Nakamura Keio University Masaru Nakano Keio University Follow this and additional works at: https://docs.lib.purdue.edu/cesun Mihara, Yusuke; Pawnlada, Payuhavorakulchai; Nakamoto, Aki; Nakamura, Tsubasa; and Nakano, Masaru, "Cost Analysis of eVTOL Configuration Design for an Air Ambulances System in Japan" (2021). CESUN Conference. 3. https://docs.lib.purdue.edu/cesun/cesun2020/papers/3 This document has been made available through Purdue e-Pubs, a service of the Purdue University Libraries. Please contact [email protected] for additional information. Cost Analysis of eVTOL Configuration Design for an Air Ambulance System in Japan Yusuke Mihara Payuhavorakulchai Pawnlanda Aki Nakamoto Dept. of System Design and Dept. of System Design and Dept. of System Design and Management Management Management Keio University Keio University Keio University Yokohama, Japan Yokohama, Japan Yokohama, Japan [email protected] [email protected] [email protected] Tsubasa Nakamura Masaru Nakano Dept. of System Design and Dept. of System Design and Management Management Keio University Keio University Yokohama, Japan Yokohama, Japan [email protected] [email protected] Abstract—Electric-vertical-takeoff-and-landing (eVTOL) cost per seat mile by 26% compared to helicopters [3]. The aircraft, known as urban air mobility or flying cars, are being safety of air EMS (Emergent Medical Services)will also be considered for widespread use as air taxis, emergency medical further increased by the development of flight controls, sense- transportation, sightseeing vehicles, and rural transportation, and-avoid technologies, and fully autonomous aircraft, owing to their reduced-size, low-cost, and low-noise consequently reducing the current problem of a high crash rate characteristics. -
EMERGING TECHNOLOGIES in BUSINESS and GENERAL AVIATION Commercial Airliners ≈ 19,000
EMERGING TECHNOLOGIES IN BUSINESS AND GENERAL AVIATION Commercial Airliners ≈ 19,000 Business Jets ≈ 17,000 2018: +3.8% Piston Planes ≈ 265,000 Turboprops ≈ 12,500 2018: +5.0% 2018: +5.2% Rotorcraft ≈ 20,500 2018: +5.4% *Registered UAS ≈ 1,200,000 Source: Jetnet LLC, Flight Global, IAOPA World Assembly, FAA Europe = 26% North America = 60% Asia = 2% Africa = 3% South America = 5% Oceana = 4% MAGNI-X BEAVER ON FLOATS – HARBOUR AIR ZEROAVIA Hydrogen Fuel-cell Powertrain HYBRID ELECTRIC PANTHERA There is a Rotax 912 combined with an electric motor on the prop shaft AMPAIRE We are transforming existing passenger planes to electric. Our first twin-engine plane has a combustion engine in the nose and an electric engine in the tail, providing redundancy and improved levels of safety. PIPISTREL ALPHA ELECTRO BYE AEROSPACE EFLYER • Conventional airplane w/ electric engine • Conventional airplane with electric engine • Flying Siemens production ready • Certified in EU engine/controller in existing LSA airframe • Trying to get approval for training in CA • Picture of airframe in development • Deposits coming in from flight schools BYE AEROSPACE EFLYER NASA X-57 DISTRIBUTED ELECTRIC PROPULSION DEMONSTRATOR • Wingtip engines provide propulsion • LE engines provide high lift • Pilot has no direct control of propulsion system DAHER, AIRBUS, SAFRAN - ECOPULSE SVO EQUIPPED AIRPLANE Eviation Alice • No direct thrust control • Gnd control on TKO and LND • 9 pax / 240 kts / 540 NM range • Regional air service – think Cape Air JOBY AIR TAXI – JAN. 2020 CITYAIRBUS -
Study on the Societal Acceptance of Urban Air Mobility in Europe
Study on the societal acceptance of Urban Air Mobility in Europe May 19, 2021 Confidential and proprietary. Any use of this material without specific permission of EASA is strictly prohibited. 8A0846_Report_Spreads_210518_Langversion.indd 1 19.05.2021 12:55:16 Further information and the full survey insights are available at easa.europa.eu/UAM This study has been carried out for EASA by McKinsey & Company upon award of a specific contract implementing a running multiple framework contract for the provision of consultancy services. Consequently, it does not necessarily express the views of EASA itself, nor should it be relied upon as a statement, as any form of warranty, representation, undertaking, contractual, or other binding commitment upon EASA. Ownership of all copyright and other IPR in this material including any documentation, data and technical information, remains vested to EASA. All logo, copyrights, trademarks, that may be contained within, are the property of their respective owners. Reproduction of this study, in whole or in part, is permitted under the condition that this Disclaimer remains clearly and visibly affixed in full at all times with such reproduced part. This study has measured the attitude of the EU society towards UAM early 2021, well in advance of future deployment in EU cities foreseen around 2024-2025. The results have been generated with best effort at this point in time, however public perception may change over time once citizens are exposed to actual UAM operations. 8A0846_Report_Spreads_210518_Langversion.indd 2 19.05.2021 12:55:16 Executive Summary New technologies such as the enhancement of battery technologies and electric propulsion as well as major investments made into start-ups are enabling the development of new vertical take-off and landing Urban Air Mobility (UAM) aircraft. -
Urban Air Mobility (UAM) Offers a New Way for Us to Commute to Work and Transport Goods Using Electric Vertical Take-Off and Landing Aircraft (Evtols)
EN-ROUTE TO URBAN EN-ROUTE AIR MOBILITY TOON URBAN THE FAST TRACK AIR TO MOBILITYVIABLE AND SAFEON ON-DEMANDTHE FAST TRACK AIR TO SERVICES VIABLE ON-DEMAND AIR SERVICES TABLE OF CONTENT 05 ... A sustainable radius of life 09 ... Moving around in more than one mode 10 ... Flying packages before people 12 ... What's an eVTOL? 13 ... Three key eVTOL configurations 14 ... Six factors to drive success 1. A sustainable energy source 2. Mobile networks for low-altitude connectivity 3. Urban air traffic management 4. Critical safety and certifications 5. Competitive service-based pricing 6. Social acceptance 20 ... A peek into the future: The air ambulance 21 ... The path to commercial air taxis 26 ... Collaboration is the linchpin 29 ... A collaboration timeline 30 ... All paths lead to the sky 30 ... Welcome to the vertiport 32 ... You will travel in a flying car 2025The year eVTOLs could become a commercially viable option as air taxis – Altran “By 2050, with the urban population “Cities... consume close to 2/3 of more than doubling its current size, the world’s energy and account nearly 7 of 10 people in the world will for more than 70% of global live in cities.” 1 greenhouse gas emissions.” 2 40%Estimate of percent of US airline The50% amount of public space in the passengers that have some level of average city dedicated to roads. 4 anxiety about flying. 3 -9 The$5.73 estimated price per mile of The10 failure classification of one one passenger seat on an air taxi catastrophic incident for every one that Uber has announced it plans to billion hours of flying time, which launch in 2023. -
White Paper on Urban Air Mobility Systems
Table of Content Abstract.................................................................................................................1 Chapter 1 The UAM Concept................................................................... 2 Proposed Basic UAM Structure.....................................................................................3 Key components:........................................................................................................... 3 Command-and-Control Platform............................................................................... 9 Navigation and Positioning System.........................................................................10 Base Points.................................................................................................................... 10 Interface......................................................................................................................... 11 Key UAM Characteristics...............................................................................................12 What makes UAM a viable new transportation mode?..........................................13 Key differences between UAM and the current airline model.........................13 Key differences between AAVs and UAVs............................................................14 Key differences between AAVs and helicopters................................................. 14 Key advantages of UAM vs. existing ridesharing................................................15 Competition -
The Evtol Battery Balancing Act Umlaut Whitepaper
umlaut — White — päper. Certification and Time-to-Market: The eVTOL Battery Balancing Act umlaut Whitepaper Content Urban Air Mobility — an Overview 04 Urban Air Mobility Requirements for Batteries 06 Development 08 Market Trends 14 Design 16 Further Consideration 24 eVTOL Vehicle Companies 26 Future of eVTOL 28 References 30 3 umlaut Whitepaper umlaut Whitepaper Urban Air Mobility — an Overview Urban Air Mobility is the aerial passenger or cargo Last mile services will typically include delivery Apart from regular transport services, special appli- transport over short- to-medium distances. In of smaller packages currently transported by the cations are also planned. The German ADAC, which addition to numerous companies building smaller delivery companies (FedEx, UPS, etc.) to end cus- is similar to the AAA in the US, has announced plans unmanned air systems, more than one hundred tomers. Both Air Metro as well as Air Taxi services to work with Volocopter, a German eVTOL startup, companies are focused on the development and will transport passengers. Air Metro is doing that to evaluate eVTOLs for their medical transport mis- production of larger eVTOL (electrical vertical take- on a fixed and regular route e.g., from John F. sions currently conducted through a combination of off and landing) vehicles. Kennedy International Airport in New York City to helicopter and ground-based ambulance vehicles.1 lower Manhattan for example -- Air Taxi services There are three main use cases envisioned for the are intended to operate on demand like a taxi or near future: ridesharing operator today, although restricted to • Last mile delivery of goods take-off and landing infrastructure. -
Choose Paris Region, Groupe ADP and RATP Group Announce The
January 2021, 18th PRESS RELEASE Choose Paris Region, Groupe ADP and RATP Group announce the winners of the worldwide call for expressions of interest regarding the setup of an Urban Air Mobility industry branch In order to bring together an ecosystem around urban air mobility in the Paris region, the RATP Group, Groupe ADP and Choose Paris Region launched an international call for expressions of interest on October 1st, with the support of Paris Region. This initiative, the scope of which is unprecedented in Europe, brought together 150 applications from 25 countries. Some 30 winners were selected, with a view to conducting experiments from June 2021 in the test area at the Pontoise-Cormeilles-en-Vexin airfield, which was inaugurated on September 30th, 2020. To meet the challenges posed by this new form of mobility in terms of use cases, public acceptance, technologies and industrialization, the call for expressions of interest was structured around the following five categories: Vehicle development: for manufacturers and equipment suppliers (batteries, avionics, etc.); Urban infrastructure: for energy companies or vertiport designers; Operations: for suppliers of intermodal solutions, maintenance, or digital platforms; Airspace integration: for suppliers of unmanned traffic management (UTM) or communication/ navigation systems; Acceptability: for laboratories or research institutes dealing with social and environmental issues. One of the key selection criteria defined beforehand was the maturity of the solution. Working groups and start of experiments at summer 2021 Thus, from June 2021, in close cooperation with the French civil aviation authority (DGA) and with the support of the European Union Aviation Safety Agency (EASA) and Eurocontrol, tests will be carried out in a real aeronautical environment at Pontoise, with respect to parking, takeoff and landing operations, as well as operations around the vehicle, whether for maintenance or electrical recharging.