Urn S. Department of Energy
Total Page:16
File Type:pdf, Size:1020Kb
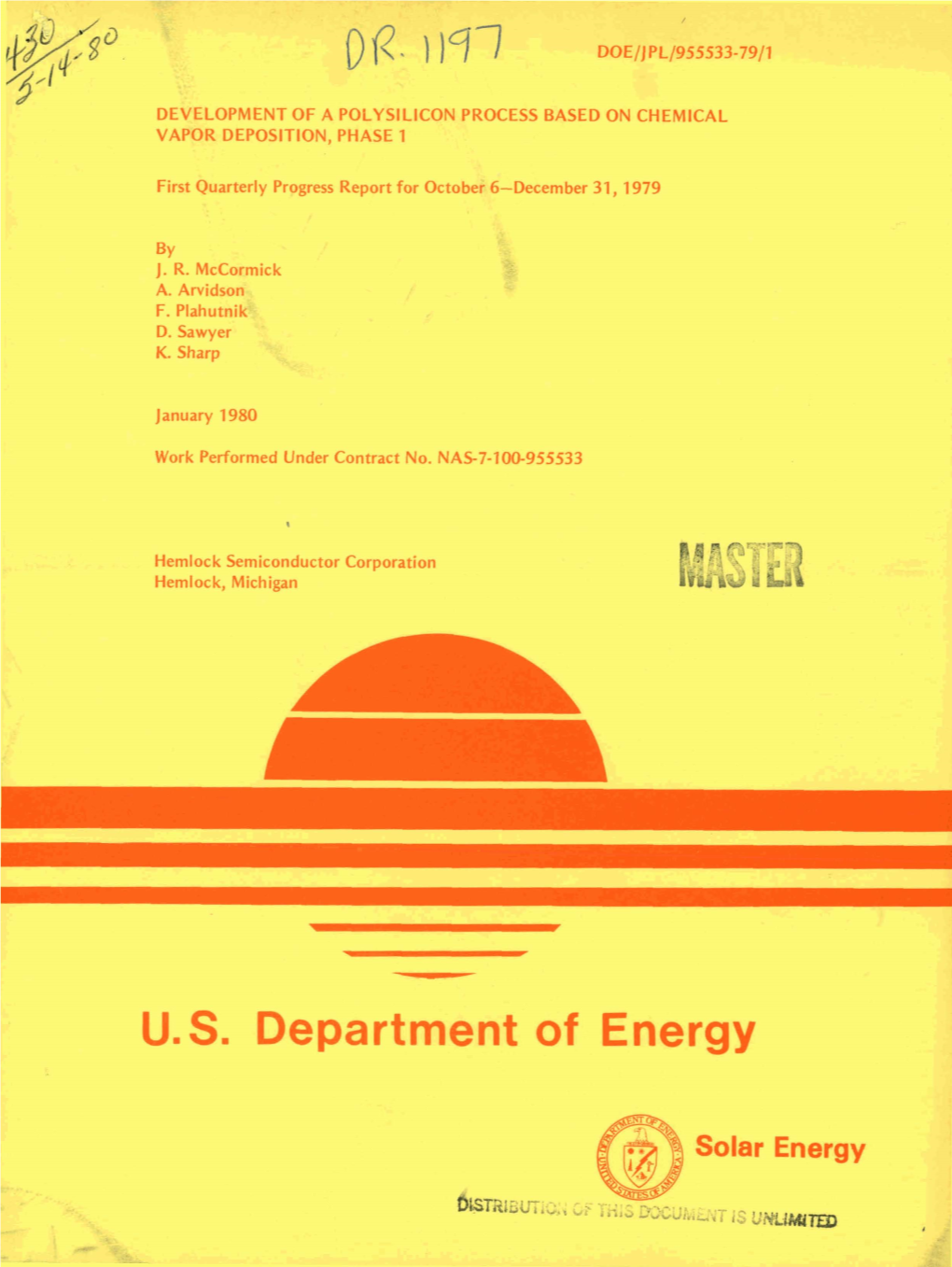
Load more
Recommended publications
-
Influence of Silicon on High-Temperature
Solar Energy Materials & Solar Cells 160 (2017) 410–417 Contents lists available at ScienceDirect Solar Energy Materials & Solar Cells journal homepage: www.elsevier.com/locate/solmat Influence of silicon on high-temperature (600 °C) chlorosilane interactions with iron crossmark ⁎ Josh Allera, , Nolan Swainb, Michael Babera, Greg Tatarb, Nathan Jacobsonc, Paul Gannonb a Mechanical and Industrial Engineering, Montana State University, Bozeman, MT 59717, USA b Chemical and Biological Engineering, Montana State University, Bozeman, MT 59717, USA c NASA Glenn Research Center, Cleveland, OH 44135, USA ARTICLE INFO ABSTRACT Keywords: High-temperature ( > 500 °C) chlorosilane gas streams are prevalent in the manufacture of polycrystalline Iron silicon, the feedstock for silicon-based solar panels and electronics. This study investigated the influence of Chlorosilane metallurgical grade silicon on the corrosion behavior of pure iron in these types of environments. The Silicon experiment included exposing pure iron samples at 600 °C to a silicon tetrachloride/hydrogen input gas mixture Silicon tetrachloride with and without embedding the samples in silicon. The samples in a packed bed of silicon had significantly Iron silicide higher mass gains compared to samples not in a packed bed. Comparison to diffusion studies suggest that the Corrosion increase in mass gain of embedded samples is due to a higher silicon activity from the gas phase reaction with silicon. The experimental results were supported by chemical equilibrium calculations which showed that more- active trichlorosilane and dichlorosilane species are formed from silicon tetrachloride in silicon packed bed conditions. 1. Introduction most common material added to a chlorosilane gas stream is silicon. Silicon may be present in a fluidized bed reactor used to convert silicon Chlorosilane species are used at high temperatures in the refine- tetrachloride to trichlorosilane or deposition equipment used to deposit ment, manufacture, and deposition of silicon and silicon-containing silicon on a wafer. -
Dichlorosilane Safety Data Sheet
Dichlorosilane Safety Data Sheet P-4587 This SDS conforms to U.S. Code of Federal Regulations 29 CFR 1910.1200, Hazard Communication. Issue date: 01/01/1980 Revision date: 01/27/2021 Supersedes: 03/09/2017 Version: 1.0 SECTION: 1. Product and company identification 1.1. Product identifier Product form : Substance Substance name : Dichlorosilane Chemical name : Dichlorosilane CAS-No. : 4109-96-0 Formula : SiH2Cl2 Other means of identification : Chlorosilane A-199, DCS 1.2. Relevant identified uses of the substance or mixture and uses advised against Use of the substance/mixture : Industrial use; Use as directed. 1.3. Details of the supplier of the safety data sheet Praxair, Inc. 10 Riverview Drive Danbury, CT 06810-6268 - USA T 1-800-772-9247 (1-800-PRAXAIR) - F 1-716-879-2146 www.praxair.com 1.4. Emergency telephone number Emergency number : Onsite Emergency: 1-800-645-4633 CHEMTREC, 24hr/day 7days/week — Within USA: 1-800-424-9300, Outside USA: 001-703-527-3887 (collect calls accepted, Contract 17729) SECTION 2: Hazard identification 2.1. Classification of the substance or mixture GHS US classification Flam. Gas 1 H220 Press. Gas (Liq.) H280 Acute Tox. 2 (Inhalation: gas) H330 Skin Corr. 1B H314 Eye Dam. 1 H318 STOT SE 3 H335 2.2. Label elements GHS US labeling Hazard pictograms (GHS US) : GHS02 GHS04 GHS05 GHS06 Signal word (GHS US) : Danger Hazard statements (GHS US) : H220 - EXTREMELY FLAMMABLE GAS H280 - CONTAINS GAS UNDER PRESSURE; MAY EXPLODE IF HEATED H314 - CAUSES SEVERE SKIN BURNS AND EYE DAMAGE H330 - FATAL IF INHALED CGA-HG22 - CORROSIVE TO THE RESPIRATORY TRACT CGA-HG11 - SYMPTOMS MAY BE DELAYED CGA-HG01 - MAY CAUSE FROSTBITE. -
Interagency Committee on Chemical Management
DECEMBER 14, 2018 INTERAGENCY COMMITTEE ON CHEMICAL MANAGEMENT EXECUTIVE ORDER NO. 13-17 REPORT TO THE GOVERNOR WALKE, PETER Table of Contents Executive Summary ...................................................................................................................... 2 I. Introduction .......................................................................................................................... 3 II. Recommended Statutory Amendments or Regulatory Changes to Existing Recordkeeping and Reporting Requirements that are Required to Facilitate Assessment of Risks to Human Health and the Environment Posed by Chemical Use in the State ............................................................................................................................ 5 III. Summary of Chemical Use in the State Based on Reported Chemical Inventories....... 8 IV. Summary of Identified Risks to Human Health and the Environment from Reported Chemical Inventories ........................................................................................................... 9 V. Summary of any change under Federal Statute or Rule affecting the Regulation of Chemicals in the State ....................................................................................................... 12 VI. Recommended Legislative or Regulatory Action to Reduce Risks to Human Health and the Environment from Regulated and Unregulated Chemicals of Emerging Concern .............................................................................................................................. -
Praxair Material Safety Data Sheet
Product: Dichlorosilane P- 4587-G Date: July 2007 Praxair Material Safety Data Sheet 1. Chemical Product and Company Identification Product Name: Dichlorosilane (MSDS No. P-4587-G) Trade Names: Praxair® Chlorosilane A-199, Dichlorosilane Chemical Name: Dichlorosilane Synonyms: DCS Chemical Family: Silicon halide Product Grades: 2.0-, 2.7-semiconductor process gas Telephone: Emergencies: 1-800-645-4633* Company Name: Praxair, Inc. CHEMTREC: 1-800-424-9300* 39 Old Ridgebury Road Routine: 1-800-PRAXAIR Danbury, CT 06810-5113 * Call emergency numbers 24 hours a day only for spills, leaks, fire, exposure, or accidents involving this product. For routine information, contact your supplier, Praxair sales representative, or call 1-800-PRAXAIR (1-800-772-9247). 2. Hazards Identification EMERGENCY OVERVIEW DANGER! Poisonous, flammable, corrosive liquid and gas under pressure. May be fatal if inhaled. Can cause eye, skin, and respiratory tract burns. Can form explosive mixtures with air. Water can cause violent reaction. Contact with water or moist air liberates irritating gas. May ignite on contact with air or water. Self-contained breathing apparatus and protective clothing must be worn by rescue workers. Under ambient conditions, this is a colorless gas with an irritating, choking odor. OSHA REGULATORY STATUS: This material is considered hazardous by the OSHA Hazard Communications Standard (29 CFR 1910.1200). POTENTIAL HEALTH EFFECTS: Effects of a Single (Acute) Overexposure Inhalation. Low vapor concentrations will irritate the nose, throat, and chest, causing discomfort or pain with coughing, excess sputum, runny nose, and difficulty with breathing. Higher concentrations may result in the inhalation of harmful and possibly lethal, amounts of material. -
United States Patent (19) 11 Patent Number: 4,980,143 Ruff (45) Date of Patent: Dec
United States Patent (19) 11 Patent Number: 4,980,143 Ruff (45) Date of Patent: Dec. 25, 1990 54 PROCESS FOR INCREASING THE 56 References Cited PERCENTAGE OF SILICON U.S. PATENT DOCUMENTS TETRACHLORIDE 4,044,109 8/1977 Kotzsch et al. ..................... 423/341 75 Inventor: Klaus Ruff, Troisdorf, Fed. Rep. of FOREIGN PATENT DOCUMENTS Germany 0156318 9/1982 Japan ................................... 423/341 73 Assignee: Huels Aktiengesellschaft, Marl, Fed. OTHER PUBLICATIONS Rep. of Germany Kojundo Silicon KK, JP-005691, 7/22/82 Abstract. Primary Examiner-Gary P. Straub 21 Appl. No.: 364,246 Assistant Examiner-Lori F. Cuomo Attorney, Agent, or Firm-Felfe & Lynch 22 Filed: Jun. 9, 1989 57 ABSTRACT A process is described for increasing the percentage of 30 Foreign Application Priority Data silicon tetrachloride during the reaction of hydrogen chloride or a mixture of hydrogen chloride and chlorine Aug. 20, 1988 DE Fed. Rep. of Germany ....... 3828344 with substances containing metallic silicon. In this pro cess the chlorosilanes are exposed to a temperature 51) Int. Cl. .............................................. C01B33/08 ranging between 300° C. and 1400° C. 52 U.S. C. ................ ... 423/341; 423/342 58 Field of Search ................................ 423/341, 342 2 Claims, 1 Drawing Sheet 7 O NORCELOROSLANE ADDED 8 O 50 a 40 IOWOL. Of TRICLCROSANE ADDED 3.O 2O - O 460 48O 5OO 52O 540 560 58O TEMPERATURENC U.S. Patent Dec. 25, 1990 4,980,143 NO TRICHLOROSILANE ADDED 6O - 5 O | 4.O O WOL-9 OF TRICHLOROSLANE ADDED 3O w IO O-- - - - - 46O 48O 5OO 52O 54O 56O 58O TEMPERATURE NC 4,980,143 1. -
A Survey of the Preparation, Purity, and Availability of Silanes a Subcontract Report
SERI/STR-211-2092 UC Category: 63 DE84000090 A Survey of the Preparation, Purity, and Availability of Silanes A Subcontract Report James H. Lorenz December 1983 Prepared under Subcontract No. CL-3-00321-01 Draft Prepared under Task No. 1479.10 WPA No. 425 SERI Technical Monitor: Amir Mikhail Solar Energy Research Institute 1617 Cole Boulevard Golden, Colorado 80401 Prepared for the U.S. Department of Energy Contract No. DE-AC02-83CH10093 STR-2092 .; ��: 5=-��� -�•. ------------------------------------------------------- -----���� PREFACE This report was prepared by James H. Lorenz under Consultant Agreement No. CL-3-00321-01, Prime Contract No . EG-77-G-01-4042 , for the Solar Energy Research Institute. The objective of this work was to provide researchers in the field of amorphous silicon wit h up-t o-dat e informat ion on silane and disilane. Users of silanes in general should find this report of in terest for it s surveys of the preparation and purification procedures of silanes and for the summaries of the in dust rial aspect s of processes used commercially in the United St at es and Japan. Comments on the purit y of available silanes and it s impact on phot ovolt aic device performance are presented. Informat ion supplied by silane producers as well as the purity analysis data supplied by Dr. Reed Corderman of Brookhaven National Laboratory is gratefully acknowledged. The const ruct ive reviews by Dr. Corderman and Dr. Ralph Lutwack of the Jet Propulsion Laboratory were very helpful. Amir Mikhail Project Manager Approved for SOLAR ENERGY RESEARCH INSTITUTE ( --- - 1\ (·. " I \! .. '--- . ----- .. ·-·· .....-c.-- � :> Thomas'.,_;'J\;_j\i}lV_)� Surek, Manager Photovoltaic Program Office Stone, Deputy Manager Solar Elect ric Conversion Research Division � C> /J-7! � . -
ADEQ Technical Support Document DRAFT(Public)
DRAFT TECHNICAL SUPPORT DOCUMENT TECHNICAL REVIEW AND EVALUATION OF APPLICATION FOR AIR QUALITY PERMIT NO. 70386 Praxair, Inc. I. INTRODUCTION This Class II, synthetic minor source air quality control operating permit is issued to Praxair, Inc, the Permittee, for the continued operation of a chemical synthesis and repackaging facility near Kingman in Mohave County, Arizona. This permit is a renewal of Air Quality Permit Number 56187. A. Company Information 1. Facility Name: Praxair, Inc. 2. Facility Location: Lat 35º 1’ 40”, Long 114º 8’ 36” Intersection of I-40 and Griffith Road 3. Mailing Address: PO Box 6157 Kingman, Arizona 86401 4. Attainment Classification: This facility is located in an area that is attainment or unclassified for all criteria pollutants. II. PROCESS DESCRIPTION A. Process This source is a chemical synthesis and repackaging facility located near Kingman, Arizona. This facility manufactures arsine and phosphine; fills, processes, tests, and warehouses gaseous products which are used by the semiconductor industry and other industries; and stores in bulk argon, liquid helium, hydrogen, nitrogen, nitrous oxide, and nitrogen trifluoride. Gaseous products include arsine, diborane, disilane, diethyltelluride, phosphine, silane, dichlorosilane, dichloromethane, fluoromethane, methyl bromide, methyl iodide, nitrogen dioxide, trichlorosilane, hexafluoroethane, octafluorocyclobutane, octafluorotetrahydrofuran, perfluoropropane, trifluoromethane, sulfur hexafluoride, silicon tetrafluoride, geranium tetrafluoride, silicon tetrachloride, enriched boron-11 trifluoride, boron trifluoride, mixtures of diborane and either boron trifluoride or enriched boron-11 trifluoride, and mixtures of disilane and silicon tetrafluoride. Fluorine and inert gases are stored on site and are used to mix with other gases to create unique mixture concentrations as specified by the customer. Arsine production: arsine is synthesized by the reaction of mixing zinc arsenide with sulfuric acid to produce zinc sulfate and pure arsine gas. -
Safety Data Sheet Dichlorosilane
SAFETY DATA SHEET DICHLOROSILANE Section 1. Identification GHS product identifier : DICHLOROSILANE Product code : Not available. Chemical name : Dichlorosilane Other means of : DCS identification Product type : Gas. Relevant identified uses of the substance or mixture and uses advised against Product use : Not available. Manufacturer : REC Silicon Inc. 119140 Rick Jones Way Silver Bow, Montana 59750 United State of America 406-496-9877 3322 Road N Northeast Moses Lake, Washington 98837 United State of America 509-766-9299 e-mail address of person : [email protected] responsible for this SDS Emergency telephone : CHEMTREC, U.S. : 1-800-424-9300 International: +1-703-527-3887 number (with hours of operation) Section 2. Hazards identification Classification of the : FLAMMABLE GASES - Category 1 substance or mixture GASES UNDER PRESSURE - Compressed gas SUBSTANCES AND MIXTURES, WHICH IN CONTACT WITH WATER, EMIT FLAMMABLE GASES - Category 3 ACUTE TOXICITY: INHALATION - Category 2 SKIN CORROSION/IRRITATION - Category 1 SERIOUS EYE DAMAGE/ EYE IRRITATION - Category 1 GHS label elements Hazard pictograms : Signal word : Danger Hazard statements : Extremely flammable gas. Contains gas under pressure; may explode if heated. In contact with water releases flammable gases. Fatal if inhaled. Causes severe skin burns and eye damage. Precautionary statements Prevention : Wear protective gloves. Wear eye or face protection. Keep away from heat, sparks, open flames and hot surfaces. - No smoking. Do not breathe gas. Version : 1 Date of issue/Date of revision : 05/31/2011. Singapore/English (GB) DICHLOROSILANE Page: 2/10 Section 2. Hazards identification Response : IF INHALED: Remove victim to fresh air and keep at rest in a position comfortable for breathing. -
Closed Loop Process for Producing Polycrystalline Silicon and Fumed Silica
^ ^ H ^ I H ^ H ^ H ^ II ^ ^ ^ II ^ II ^ H ^ ^ ^ ^ ^ ^ ^ I ^ European Patent Office Office europeen des brevets EP 0 921 098 A1 EUROPEAN PATENT APPLICATION (43) Date of publication: (51) |nt CI * C01 B 33/029, C01 B 33/035, 09.06.1999 Bulletin 1999/23 C0-| B 33/1 8 CQ1 B 33/04, P01 R 33/1 07 (21) Application number: 98309027.5 (22) Date of filing: 04.11.1998 (84) Designated Contracting States: (72) Inventor: The designation of the inventor has not AT BE CH CY DE DK ES Fl FR GB GR IE IT LI LU yet been filed MC NL PT SE Designated Extension States: (74) Representative: Eyles, Christopher Thomas ALLTLVMKROSI W.P. THOMPSON & CO. Celcon House (30) Priority: 10.11.1997 US 966798 289-293 High Holborn London WC1V7HU (GB) (71) Applicant: MEMC Electronic Materials, Inc. St. Peters, Missouri 63376 (US) (54) Closed loop process for producing polycrystalline silicon and fumed silica (57) A closed loop process for producing electronic monochlorosilane; b) converting the trichlorosilane to grade polycrystalline silicon from silane and fumed silica silicon tetrachloride and silane; c) converting the silane from silicon tetrachloride involves the steps of a) sub- to polycrystalline silicon and hydrogen; d) reacting the jecting impure silicon to hydrochlorination with hydrogen silicon tetrachloride from steps a) and b) with hydrogen chloride to produce trichlorosilane and silicon tetrachlo- and oxygen to produce fumed silica and hydrogen chlo- ride together with minor amounts of dichlorosilane and ride; and e) recycling the hydrogen chloride from step d) for use in step a). -
Dupont™ Kalrez® Chemical Resistance and Fluid Compatability, Including All Chemicals Under the Clean Air
DuPont™ Kalrez® Chemical Resistance and Fluid Compatibility, Including All Chemicals Under the Clean Air Act Technical Information—Rev. 4, July 2010 DuPont™ Kalrez® perfluoroelastomer parts combine the elastomeric properties of fluoroelastomers with the chemical resistance of DuPont™ Teflon® fluoropolymer resins. Due to its unique properties, Kalrez® parts should be considered for service in all applications and environments where dependable, long-term service is desired, as well as in hot or aggressive environments that are beyond the service ability of common elastomers. This guide is intended to provide assistance in determining the suitability of seven commercially available elastomers—nitrile (NBR), ethylene propylene (EPDM), silicone (VMQ), fluorosilicone (FVMQ), vinylidene fluoride-based fluoroelastomer (FKM), polysulfides (T), and Kalrez® perfluoroelastomer parts—for service in over 1,600 chemicals and fluids. The criteria used for these ratings included volume swell resistance based on laboratory immersion testing, laboratory aging tests, actual field experience, and informed judgments based on experience in similar chemical groups. The ratings for the six common elastomers are based on published literature and are offered for general comparative purposes only—we cannot guarantee their accuracy nor assume responsibility for their use. Thermal Stability The ratings for these six common elastomers may be overly optimistic for elevated temperature and/or high concentration applications because many are based on ambient temperature testing. Suitability of these elastomers for service at elevated temperatures rapidly diminishes because higher temperatures increase the effects of chemicals on the base polymer as well as the cross-link systems. Serviceability is further limited by the upper service temperature limit of each polymer. -
Section 2. Hazards Identification OSHA/HCS Status : This Material Is Considered Hazardous by the OSHA Hazard Communication Standard (29 CFR 1910.1200)
SAFETY DATA SHEET Nonflammable Gas Mixture: Dichlorosilane / Helium / Hydrogen / Hydrogen Chloride / Nitrogen / Silane / Trichlorosilane Section 1. Identification GHS product identifier : Nonflammable Gas Mixture: Dichlorosilane / Helium / Hydrogen / Hydrogen Chloride / Nitrogen / Silane / Trichlorosilane Other means of : Not available. identification Product use : Synthetic/Analytical chemistry. SDS # : 018592 Supplier's details : Airgas USA, LLC and its affiliates 259 North Radnor-Chester Road Suite 100 Radnor, PA 19087-5283 1-610-687-5253 24-hour telephone : 1-866-734-3438 Section 2. Hazards identification OSHA/HCS status : This material is considered hazardous by the OSHA Hazard Communication Standard (29 CFR 1910.1200). Classification of the : GASES UNDER PRESSURE - Compressed gas substance or mixture GHS label elements Hazard pictograms : Signal word : Warning Hazard statements : Contains gas under pressure; may explode if heated. May displace oxygen and cause rapid suffocation. Precautionary statements General : Read and follow all Safety Data Sheets (SDS’S) before use. Read label before use. Keep out of reach of children. If medical advice is needed, have product container or label at hand. Close valve after each use and when empty. Use equipment rated for cylinder pressure. Do not open valve until connected to equipment prepared for use. Use a back flow preventative device in the piping. Use only equipment of compatible materials of construction. Prevention : Not applicable. Response : Not applicable. Storage : Protect from sunlight when ambient temperature exceeds 52°C/125°F. Store in a well- ventilated place. Disposal : Not applicable. Hazards not otherwise : In addition to any other important health or physical hazards, this product may displace classified oxygen and cause rapid suffocation. -
Chlorosilane Disproportionation Catalyst and Method for Producing a Silane Compound by Means of the Catalyst
turopaiscnes patentamt European Patent Office © Publication number: 0 213 215 Office europeen des brevets A1 EUROPEAN PATENT APPLICATION Application number: 85110110.5 C01B © Int. CI.4: 33/107 , C01 B 33/04 , ~ B01J 31/02 © Date of filing: 12.0&85 © Date of publication of application: © Applicant: DENKI KAGAKU KOGYO KABUSHIKI 11.03.87 Bulletin 87/11 KAISHA 4-1, Yuraku-cho 1-chome © Designated Contracting States: Chiyoda-ku Tokyo(JP) BE CH GB IT LI NL © Inventor: Yamada, Mitsunori 55-1, Oaza-Suzawa Oml-machi Nishi-Kubiki-gun Niigata-ken(JP) Inventor: Ishii, Masaji 4- 33-4-302, Tsurumaki Setagaya-ku Tokyo(JP) inventor: Miyai, Akira 1964-5, Yamazaki-machi Mashida-shi Tokyo(JP) Inventor: Nakajima, Yukihlko 5- 33-18, Asahi-machl Atsugishi Kanagawa-ken(JP) Inventor: Sato, Shinsei 3-5-22, Mlnami-Rlnkan Yamato-shi Kanagawa-ken(JP) © Representative: Wgchtersh&user, GUnter, Dr. Tal29 D-8000 Munchen 2(DE) *) Chlorosilane disproportionation catalyst and method for producing a silane compound by means of the catalyst (57/ A chlorosilane disproportionation catalyst com- prising a tertiary amine of the formula: 5 R^ » N-R (A) R N £2 where each R represents an aliphatic hydrocarbon N group and the sum of carbon atoms in the three aliphatic hydrocarbon groups as R is 12 or more, and a tertiary amine hydrochloride of the formula: EL LU arox uopy centre 0 213 215 R\ + - N-RH CI (B) where R is as defined above. 2 U 213 215 2 CHLOROSILANE DISPROPORTIONATION CATALYST AND METHOD FOR PRODUCING A SILANE COM- POUND BY MEANS OF THE CATALYST as taught in U.S.