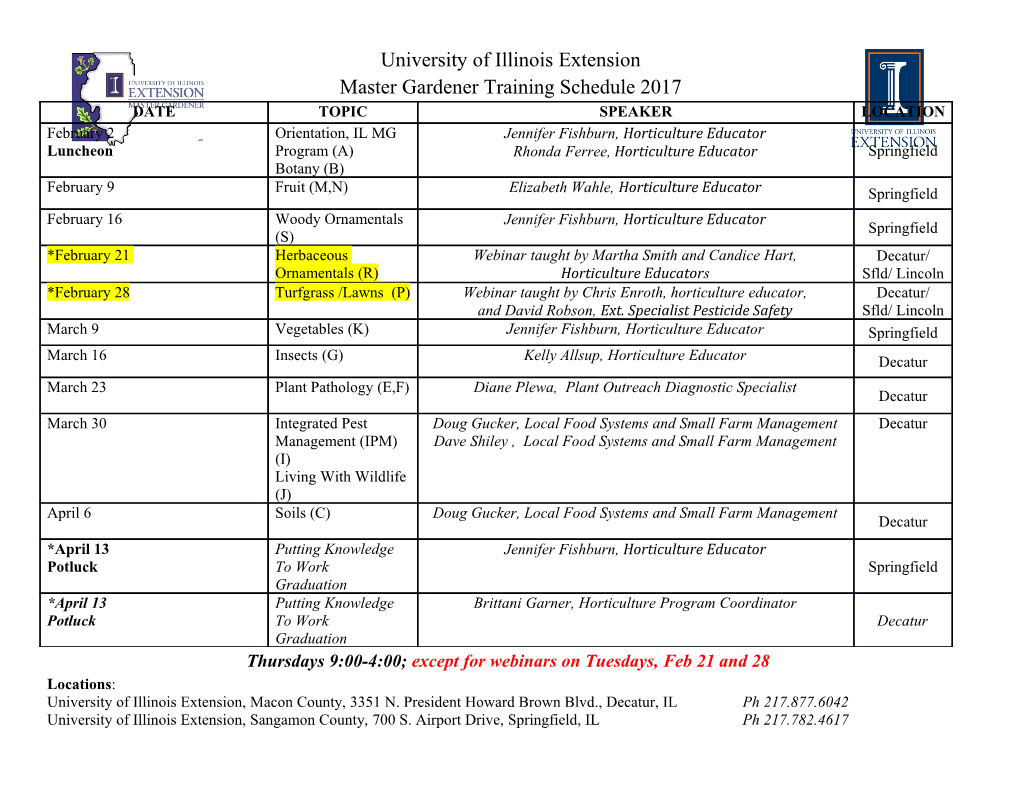
DE~ELQPMENTOF A POLYSILICON PROCESS BASED ON CHEMICAL VAmR DEPOSITION, PHASE 1 First ~uarterlyPrpgress Report fw 0ctobd6-December 31,1979 January 1980 Work Performed Under Contract No. NAS-7-100.955533 Hemlock Semiconductor Corporation Hemlock, Michigan UrnS. Department of Energy DISCLAIMER This report was prepared as an account of work sponsored by an agency of the United States Government. Neither the United States Government nor any agency Thereof, nor any of their employees, makes any warranty, express or implied, or assumes any legal liability or responsibility for the accuracy, completeness, or usefulness of any information, apparatus, product, or process disclosed, or represents that its use would not infringe privately owned rights. Reference herein to any specific commercial product, process, or service by trade name, trademark, manufacturer, or otherwise does not necessarily constitute or imply its endorsement, recommendation, or favoring by the United States Government or any agency thereof. The views and opinions of authors expressed herein do not necessarily state or reflect those of the United States Government or any agency thereof. DISCLAIMER Portions of this document may be illegible in electronic image products. Images are produced from the best available original document. Thisk was prepared as an accaunt of woxk spnmd by an agency of the United States Gow~nmntNeither the U&ed States Co'v~rnnwntnor my agency thereof. nor any of their cmpb~,n&w my mrranty, express or impUed, or wsum any legal llPbility a r-nsfbility far &e ~wuriir~r,mmpktenm, qr umkrsa1 rrf r*q InlLrrrprtien, ygudtrs, ptoBud, or proms dbdanrd, ~r ~eprosmt1&at its wuulrl not InWmga pmtely owned rights. Reference hcrdn to aay spacific oommercinl product, process, or ae~teby trade name, trodemark, mauufactmer, ar atherwke, does not gscesserily wnaitute or its e~o~~,swxr~tfoa,or 6- by the tlnited State6 Gsrmmcnt tx nay *BEY Ud.Pht rmd sgIni&1~of authors expressed herein do net mystate or reflect thw of the Uaitad Stuta Covwnnrcnt or my aguney thereaf." This report has bssn reproduced directly fr~mahe best available sapye DOE/JPL/955533-7911 Distribution Category UC-63b .. DRL NO 125 DRD SE-2 FIRST QUARTERLY .PROGRESS REPORT 6 October to 31 December 1979 on DEVELOPMENT OF A POLYSILICON PROCESS BASED ON CHEMICAL VAPOR DEPOSITION (PHASE 1) prepared by J. R. McCormick, Principal Investigator and A. Arvidson, F. Plahutnik, D. Sawyer and K. Sharp January 1980 JPL Contract 955533 "The JPL Low-Cost Silicon Solar Array Project is sponsored by the U.S. Depqrtment of Energy and forms part of the Solar Photovoltaic Conversion Program to initiate a major effort toward the development of low-cost solar arrays. This work was performed for the Jet Propulsion Laboratory, California Insitute of Technology by agreement between NASA and DOE." ,13+ 99 HEMLOCK SEMICONDUCTOR CORPORATION a wholly owned subsidiary of Dow Corning Corporation 12334 Geddes Rd., Hemlock, Michigan 48626 ABSTRACT The goal of this program is to demonstrate that. a dichlorosilane based reductive chemical vapor deposition (CVD) process is capable of producing, at low cost, high quality polycrystalline silicon. Physical form and purity of this material will be consistent with LSA material requirements for use in the manufacture of high efficiency solar cells. Chemical processes involved in achieving the above objective are reviewed with emphasis placed on advantages of this process when compared with existing polycrystalline silicon production technology. Installation of a CVD reactor with associated analytical instrumentation is described. Preliminary reactor data has been favorable demonstrating the anticipated increased deposition rate and conversion efficiency when dichloro- silane decomposition is compared with trichlorosilane decomp- osition. No serious problems have been encountered which might limit dichlorosilane use as a reactor feed material. Design considerations for a process development unit (PDU) for dichlorosilane synthesis are reviewed. A design which effectiveiy suppresses monochlorosilane during the redistribution of trichlorosilane was decided upon and its implementation is described. The PDU will be used to collect data on optimization of the redistribution proce'ss as well as to determine product quality. Based on experimental data collected during the first quarter along with already available data on the redistri- bution and hydrogenation processes, a preliminary mass balance is established. TABLE OF CONTENTS PAGE Abstract i Table of Contents i i List of Figures iii List of Tables iv 1.0 Summary 1 2.0 Introduction 3 2.1 Program Objectives 3 2.2 Program Approach 4 2.3 Process Description 6 2.3.1 Relevant Chemistry 6 2.3.2 Proccss Implcmcntation 11 3.0 Technical Status 13 3.1 CVD Reactor Feasibility 13 3.1.1 General 13 3.1.2 Experimcntal CVD Reactor and Support System 14 3.1.3 Experimental Results i 7 3.2 Intermediate Dichlorosilane Reactor Development 2 2 3.2.1 General 2 2 3.3 Dichlorosilane Proccss/Product Evaluation 22 3.3.1 General '?k i- 3.3.2 PDU Support 2 3 3.3.3 Froccss Dcvclopmcnt Unit Design 2 8 3.4 Preliminary EPSDU Design 30 3.4.1 General 3 (1 3.4.2 Status 31 4.0 Conclusions and Recommendations 3 2 5.0 Program Schedule/Plans 3 2 6.0 New ~echnolo~~ 33 7.0 References 33 8.0 Acknowledgements 34 Appendicies A - Tables 1 through 5 Appendicies B - Figures 1 through 19 LIST OF FIGURES Page Figure 1 - Schedule of Effort by Phases 40 Figure 2 - schematic of Current .Trichlorosilane Based CVD Process 41 Figure 3 - Schematic of HSC Dichlorosilane Based CVD Process 4 2 Equilibrium Relationships for Silicon Gener ation from Chlorosilane at 1050°C 43 Figure 5 - Silicon Deposition Efficiency 44 Figure 6 - Vent Composition - Relationships for Silicon Production from SiH2C12 45 Figure 7 - Schematic of HSC Low Cost Dichlorosilane Based Polycrystalline Silicon Process 46 Figure 8 - Program Plan Milestone Schedule 47-48 Figure 9 - Schematic of Reactor Feed and Vent Piping 4 9 Figure 10 - Schematic of Rearranger Piping 50 Figure 11 - Schematic of Dichlorosilane Cylinder Piping 51 Figure 12 - Schematic of Bendix Gas Chromatograph Connection to Reactor 394 and Data Process- ing System 52 Figure 13 - Chromatographic Data from Dichlorosilane-to- Silicon Run #394-044 53 Figure 14 - Chromatographic Data from Dichlorosilane-to- Silicon Run #394-052-2 54 Figure 15 - Schematic of Laboratory Trichlorosilane Rearranger Unit 5 5 Figure 16 - Schematic of Dichlorosilane Preparation Unit with Monochlorosilane Suppression 56 Figure 17 - Schematic of Dichlorosilane Preparation Unit with Monochlorosilane Removal 5 7 Figure 18 - Schematic of Dichlorosilane Mini-Plant 58 Figure 19 - Preliminary Molar Material Balance for HSC Dichlorosilane Process 59 LIST OF TABLES Page Table 1 - Summary of Experimental Reactor Performance using Trichlorosilane Feed Table 2 - Summary of Experimentai Reactor Performance 36 using Dichlorosilane feed Table 3 - Effectiveness of Various Drying Methods for 37 Dowex MWA-1 Table 4 - Thermal Decomposition Products of Dowex MWA-1 38 Table 5 - Thermal Decomposition Characteristics of 39 Dowex FWA-I .1.O Summary This report describes a process for the low-cost production of polycrystalline sil.icon from dichlorosilane via reductive chemical vapor deposition (CVD) with hydrogen. The dichlorosilane is generated from the catalyzed redistri- bution of trichlorosiiane. The by-product silicon tetra- chloride may, if desirable, be recycled to trichlorosilane via hydrogenation. Objectives of Phase 1 (the current contract) are to demonstrate the feasibility of using dichlorosilane as a CVD reactor feed material and to utilize a base catalyzed redistribution of trichlorosialne to pro- duce high purity dichlorosilane. Phases 2 and 3 of the program will demonstrate the technology readiness of the process at the EPSDU level. The chemistry relevant to this process is reviewed and advantages of this process over the existing Siemens po1.y- crystalline silicon production process are discussed. An experimental CVD reactor system designed for use with dichlorosilane feed and associated analytical instru- mentation was pla.ced in operation. In the limited number of CVD runs completed in the first quarter results, have beec encouraging. Silicon deposition rates obtained using dichloro- silane feed are significantly greater than those observed using trichlorosilane under comparable reactor operating conditions. No problems unique to the use of dichlorosilane as a reactor feed material have been encountered. With the exception of some unreacted dichlorosilane present in the decomposition byproduct stream, vent gas compsition contains those chlorosilane species observed in trichlorosilane decomposition. A PDU (mini-plant) was designed to provide sufficient dichlorosilane for extended reactor operation and evaluate the quality of dichlorosilane produced via the redistri- bution of trichlorosilane. A mixed feed (HSiC13-SiC14) redistribution process coupled with a single distillation step is described. This process was determined to be the most cost effective aproach to pure dichlorosilane prepar- ation. Laboratory equipment was installed to support PDU efforts. Evaluation of Dowex Resin MWA-1 as a redistri- bution catalyst was initiated. Dowex Resin MVA-1 decompo- sition characteristics including loss of functional amine is under investigation. A preliminary material balance is presented encompass- ing hydrogenation, redistribution and reductive chemical vapor deposition. Expcrimental data obtained
Details
-
File Typepdf
-
Upload Time-
-
Content LanguagesEnglish
-
Upload UserAnonymous/Not logged-in
-
File Pages68 Page
-
File Size-