| THERMOPLASTIC INDUSTRIAL PIPING SYSTEMS | PP UPP PE UPP ECTFE Pvdfchemprolinecpvc PE PFAPE PP-RCTPP-RCT
Total Page:16
File Type:pdf, Size:1020Kb
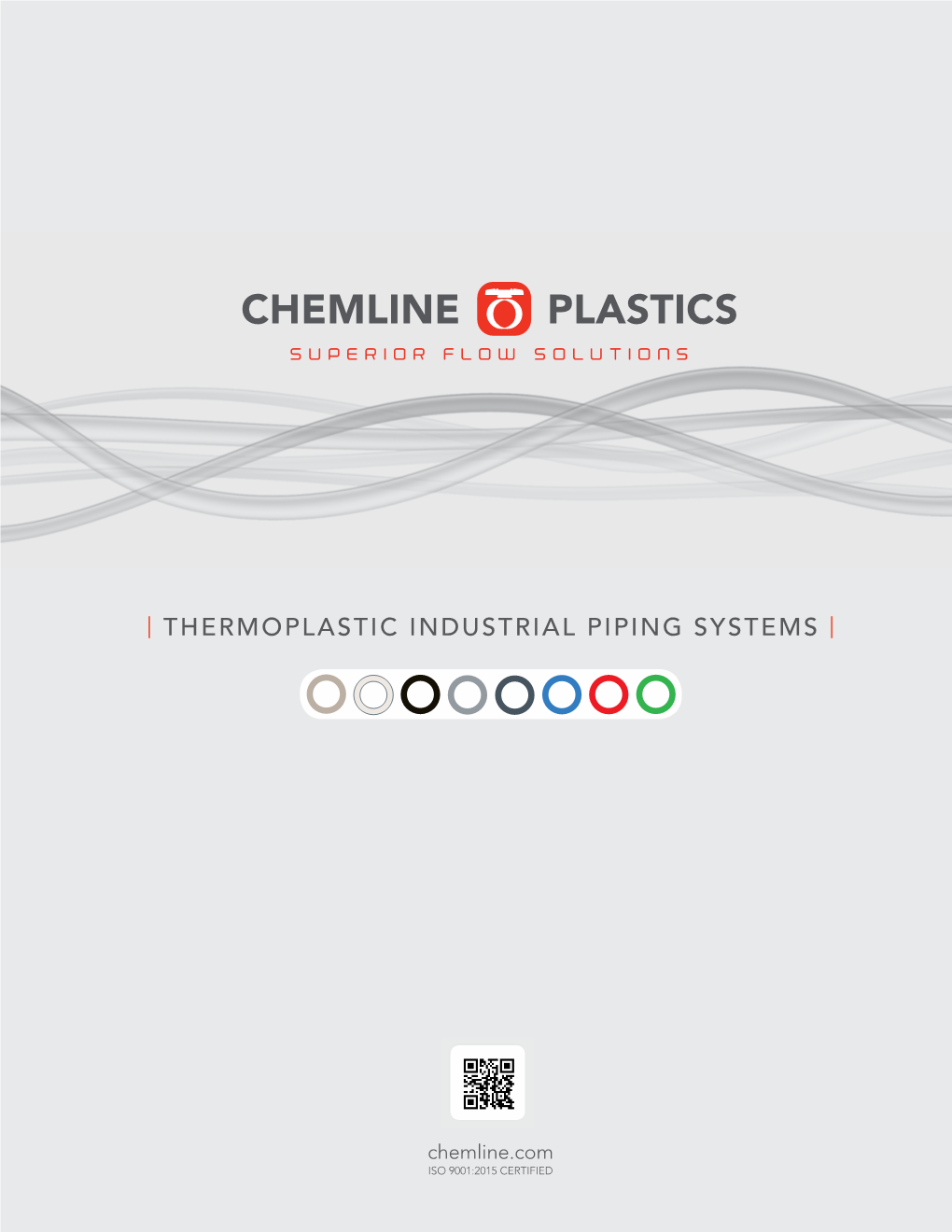
Load more
Recommended publications
-
Arium® Pro Ultrapure Water Systems Application-Orientated and Flexible to Meet the Highest Demands
arium® pro Ultrapure Water Systems Application-orientated and flexible to meet the highest demands Advantages – Modular – System selection specifically for your application – Flexible - Perfect integration into any laboratory – Easy to use – Display with touch function and intuitive menu – Fast – Favorites function with direct access for recurring volumes Product Description As a reliable source of ultrapure water, the arium® pro series offers a flexible and modular system which, compared to conventional devices, demonstrates excellent added value. All systems meet and exceed the ASTM Type 1 water quality standards and ensure the best reproducible results in their class. Up to 2 liters of consistently high-quality ultrapure water with a conductivity of 0.055 µS/cm (018,2 MO + cm) can be dispensed per minute. The ultrapure water is virtually microorganism-free when an arium® SterilePlus final filter is used. The patented Sartorius technology, the SD card slot, the long service life and low maintenance requirement distinguish the arium® pro systems as an easy-to-use, economical and reliable Type 1 ultrapure water system. Applications Modular – HPLC, GC-MS Various device configurations are specifically tailored to your – Biological applications, e.g. cell culture application. arium® pro provides any desired ultrapure water – Standard applications such as the production of solutions, quality for critical and standard applications. media, and reagents Water purification on a laboratory scale Flexible The space-saving installation of the device on, under, or above “Favorites” function your workstation integrates it perfectly into any laboratory. With the new favorites function it is possible to save recurring The positioning of the display and the water dispensing point volumes and retrieve them as required by direct access. -
GORE® Filters Water Applications
For Ultrapure GORE® Filters Water Applications Major Semiconductor Manufacturer Demonstrates GORE® Filters Perform Comparably to UF Module at Significantly Lower Cost Results The performance of the GORE® Filters was nearly equivalent to that of the ultrafiltration module: • UF: ~50 to 100 counts/liter at 0.05µm • GORE® HR Filters: ~50 to 200 counts/liter at 0.05µm • GORE® 0.02µm Filters: ~200 to 500 counts/liter at 0.05µm • Manufacturer now has data proving that GORE® Filters meet the requirements for ultrapure water applications that had previously required the more costly UF modules Water Quality Test Results Particles > 0.05 micron 1000 900 800 700 Situation 600 500 A major semiconductor manufacturer was seeking a lower-cost 400 300 alternative to ultrafiltration modules for an ultrapure water system. / Liter Counts 200 To compare filtration performance, parallel trials 100 ® 0 were run with GORE Filters and ultrafiltration (UF) modules. 0 5 10 15 20 25 30 35 40 45 50 55 60 65 70 75 Time (Hour) Trial Setup GORE® Filter 0.02µm Cartridge ® ® GORE Filter HR Cartridge • Single water source for GORE Filter and UF module UF Module • Single 10-inch GORE® Filter installed after pre-filter • Trial was run with GORE® 0.02µm Filters, then GORE® HR* Filters The manufacturer reported that in this • Water quality from UF module and GORE® Filters compared using ® UDI50 particle counter. application: “The GORE Filter provided *HR: High Retention filter. Testing demonstrates retention superior to typical 0.02µm filter the same particle removal function and efficiency as the UF.” — Senior UPW Engineer UPW loop Water Quality Test was performed post-UF Module and post-GORE® Filter Benefits Realized • GORE® Filters can meet the requirements for most of the GORE® manufacturer’s ultrapure water applications at significantly Filter Storage Tank lower cost than UF modules. -
ECTFE Data Sheet
ECTFE Fluoropolymer Extruded Films ETHYLENE-CHLOROTRIFLUOROETHYLENE FILM FOR USE IN HIGH-PERFORMANCE APPLICATIONS TCI’s ECTFE films are produced from HALAR® Ethylene-ChloroTrifluoroEthylene resins by a melt extrusion casting process. These films have the typical fluoropolymer traits of being resistant to harsh thermal, chemical, and ultraviolet environments. TCI’s ECTFE films offer excellent weatherability, chemical abrasion resistance, tear resistance, non-stick properties, and resistance to high-energy radiation. ECTFE films can be heat-sealed, thermoformed, and laminated to various substrates. TCI’s ECTFE films are utilized in a variety of industries: Chemical Processing TCI’s ECTFE Films Characteristics: Due to its superior chemical resistance to most acids and solvents over a broad temperature range Highest abrasion and tear resistance among all fluoropolymer films and low permeability to solvents and gases, ECTFE films applications include: chemical tank linings, pump Outstanding weatherability and resistance to diaphragms, chlorine cells, water treatment, spray UV radiation shielding applications for pipe joints, and semi- Chemically inert conductor processing environments. Excellent fire resistance, UL V-0 rating Outdoor Protection Superior anti-stick and low friction properties Excellent weatherability, non-stick properties, U-V Highest dielectric strength of all fluoropolymer stability, abrasion resistance, tear resistance, and high films light transmission make ECTFE film very effective for outdoor protective applications. Thermoformable and heat-sealable Continuous service temperature from Photovoltaic Panels -200°C (-328°F) up to 165°C (330°F) TCI’s ECTFE films offer excellent dielectric perfor- mance, superior water vapor barrier properties, fire resistance, and high solar transmittance. These films TCI’s ECTFE Films General Availability: are ideally suited for use in the back sheet and front Thickness range from 0.0005" to 0.010" sheet glazing of PV panels. -
Chemical Resistance
Materials - Chemical Resistance Please note: Substances All information in our catalogue is based on current technical knowledge, Substance Conc. PTFE PFA FEP ETFE ECTFE PVDF PP PA PS PMMA experience and manufacturers’ data. Users should check the suitability of at +20 °C in % parts and materials described in the catalogue before purchase. Accumulator acid 20 + + + + + + + – + – Acetaldehyde 100 + + + + + + ° –– ° BOLA does not accept any warranty claims as to suitability and fitness of Acetamide 100 + + + + + + + + + ° purpose of the materials and products described in this catalogue. Users Acetic acid 100 + + + + + + + – ° – should avoid making any assumptions on, or interpretation of, the data Acetic acid amide 100 + + + + + + + + + ° herein. Therefore we cannot provide warranty and cannot accept Acetic acid anhydride 100 + + + + + – ° ––– responsibility for any damage. Acetic acid butyl ester 100 + + + + + + ° + –– Acetic acid chloride 100 + + + + + + ° ° –– Acetic acid ethyl ester 100 + + + + + – ° + –– Acetic acid pentyl ester 100 + + + + + + + + – + Acetic anhydride 100 + + + + + – ° ––– Acetone 100 + + + + + – + + –– Acetonitrile 100 + + + + + ° + + –– Acetophenone 100 + + + + + + + ––– Acetyl benzene 100 + + + + + + + ––– Acetyl chloride 100 + + + + + + ° ° –– Acetylene tetrachloride 100 + + + –– + – + –– Acetylsalicylic acid 100 + + + + + + + + + – Acetone-2 100 + + + + + – + + –– Acrylic acid butyl ester 100 + + + + + ° ° + –– Acrylic acid ethylic ester 100 + + + + + ° ° + –– Acrylonitrile 100 + + + + + ° ° + –– Adipic acid -
Safety Data Sheet (SDS) Hydrogen Peroxide Solution, 30 - 32% W/W
Safety Data Sheet (SDS) Hydrogen Peroxide Solution, 30 - 32% w/w SECTION 1: Identification Product Identifier: BASELINE Hydrogen Peroxide Solution Master Product Number(s): S021001 EU Index Number: 008-003-00-9 Synonyms: Dihydrogen dioxide; Hydrogen dioxide; Hydroperoxide Chemical Names: DE Wasserstoffperoxid in Lösung; ES Peróxido de hidrógeno en disolución (Agua oxigenada); FR Peroxyde d'hydrogène en solution (Eau oxygénée); IT Perossido di idrogeno soluzione (Acqua ossigenata); NL Waterstofperoxide in oplossing Identified Uses: For laboratory use only. Not for drug, food, or household use. Manufacturer: SEASTAR CHEMICALS ULC 2061 Henry Avenue West, Sidney, BC V8L 5Z6 CANADA 1-250-655-5880 Emergency Number: CANUTEC (CAN): 1-613-996-6666 (24-hour) SECTION 2: Hazard identification GHS Classification in accordance with 29 CFR 1910 (OSHA HCS) / WHMIS HPR / Regulation (EC) No 1272/2008 For the full text of the H-Statement(s) and P-Statement(s) mentioned in this Section, see Section 16. Classification: Serious eye damage – Category 1 Acute toxicity, Oral – Category 4 Acute toxicity, Inhalation – Category 4 GHS Label Elements Pictograms: Signal Word: Danger Hazard H318: Causes serious eye damage. Statements: H302 + H332: Harmful if swallowed or if inhaled. Precautionary P261: Avoid breathing fume/gas/mist/vapours/spray. Statements: P280: Wear protective gloves/protective clothing/eye protection/face protection. P301 + P312: IF SWALLOWED: Call a POISON CENTER or doctor if you feel unwell. P304 + P340: IF INHALED: Remove person to fresh air and keep comfortable for breathing. P305 + P351 + P338: IF IN EYES: Rinse cautiously with water for several minutes. Remove contact lenses, if present and easy to do. -
"Determination of Total Organic Carbon and Specific UV
EPA Document #: EPA/600/R-05/055 METHOD 415.3 DETERMINATION OF TOTAL ORGANIC CARBON AND SPECIFIC UV ABSORBANCE AT 254 nm IN SOURCE WATER AND DRINKING WATER Revision 1.1 February, 2005 B. B. Potter, USEPA, Office of Research and Development, National Exposure Research Laboratory J. C. Wimsatt, The National Council On The Aging, Senior Environmental Employment Program NATIONAL EXPOSURE RESEARCH LABORATORY OFFICE OF RESEARCH AND DEVELOPMENT U.S. ENVIRONMENTAL PROTECTION AGENCY CINCINNATI, OHIO 45268 415.3 - 1 METHOD 415.3 DETERMINATION OF TOTAL ORGANIC CARBON AND SPECIFIC UV ABSORBANCE AT 254 nm IN SOURCE WATER AND DRINKING WATER 1.0 SCOPE AND APPLICATION 1.1 This method provides procedures for the determination of total organic carbon (TOC), dissolved organic carbon (DOC), and UV absorption at 254 nm (UVA) in source waters and drinking waters. The DOC and UVA determinations are used in the calculation of the Specific UV Absorbance (SUVA). For TOC and DOC analysis, the sample is acidified and the inorganic carbon (IC) is removed prior to analysis for organic carbon (OC) content using a TOC instrument system. The measurements of TOC and DOC are based on calibration with potassium hydrogen phthalate (KHP) standards. This method is not intended for use in the analysis of treated or untreated industrial wastewater discharges as those wastewater samples may damage or contaminate the instrument system(s). 1.2 The three (3) day, pooled organic carbon detection limit (OCDL) is based on the detection limit (DL) calculation.1 It is a statistical determination of precision, and may be below the level of quantitation. -
Semiconductor Industry
Semiconductor industry Heat transfer solutions for the semiconductor manufacturing industry In the microelectronics industry a the cleanroom, an area where the The following applications are all semiconductor fabrication plant environment is controlled to manufactured in a semicon fab: (commonly called a fab) is a factory eliminate all dust – even a single where devices such as integrated speck can ruin a microcircuit, which Microchips: Manufacturing of chips circuits are manufactured. A business has features much smaller than with integrated circuits. that operates a semiconductor fab for dust. The cleanroom must also be LED lighting: Manufacturing of LED the purpose of fabricating the designs dampened against vibration and lamps for lighting purposes. of other companies, such as fabless kept within narrow bands of PV industry: Manufacturing of solar semiconductor companies, is known temperature and humidity. cells, based on Si wafer technology or as a foundry. If a foundry does not also thin film technology. produce its own designs, it is known Controlling temperature and Flat panel displays: Manufacturing of as a pure-play semiconductor foundry. humidity is critical for minimizing flat panels for everything from mobile static electricity. phones and other handheld devices, Fabs require many expensive devices up to large size TV monitors. to function. The central part of a fab is Electronics: Manufacturing of printed circuit boards (PCB), computer and electronic components. Semiconductor plant Waste treatment The cleanroom Processing equipment Preparation of acids and chemicals Utility equipment Wafer preparation Water treatment PCW Water treatment UPW The principal layout and functions of would be the least complex, requiring capacities. Unique materials combined the fab are similar in all the industries. -
Products Evolved During Hot Gas Welding of Fluoropolymers
Health and Safety Executive Products evolved during hot gas welding of fluoropolymers Prepared by the Health and Safety Laboratory for the Health and Safety Executive 2007 RR539 Research Report Health and Safety Executive Products evolved during hot gas welding of fluoropolymers Chris Keen BSc CertOH Mike Troughton BSc PhD CPhys MInstP Derrick Wake BSc, Ian Pengelly BSc, Emma Scobbie BSc Health and Safety Laboratory Broad Lane Sheffield S3 7HQ This report details the findings of a research project which was performed as a collaboration between the Health and Safety Executive (HSE) and The Welding Institute (TWI). The project aim was to identify and measure the amounts of products evolved during the hot gas welding of common fluoropolymers, to attempt to identify the causative agents of polymer fume fever. Carbonyl fluoride and/or hydrogen fluoride were detected from certain fluoropolymers when these materials were heated to their maximum welding temperatures. Significant amounts of ultrafine particles were detected from all of the fluoropolymers investigated when they were hot gas welded. The report concludes that fluoropolymers should be hot gas welded at the lowest possible temperature to reduce the potential for causing polymer fume fever in operators. If temperature control is not sufficient to prevent episodes of polymer fume fever, a good standard of local exhaust ventilation (LEV) should also be employed. This report and the work it describes were funded by the Health and Safety Executive (HSE). Its contents, including any opinions and/or conclusions expressed, are those of the authors alone and do not necessarily reflect HSE policy. HSE Books © Crown copyright 2007 First published 2007 All rights reserved. -
PVDF: a Fluoropolymer for Chemical Challenges
Electronically reprinted from August 2018 PVDF: A Fluoropolymer for Chemical Challenges When it comes to selecting materials of construction, keep in mind the favorable properties of fluoropolymers for corrosive service Averie Palovcak and Jason ince its commercialization in the Pomante, mid-1960s, polyvinylidene fluoride Arkema Inc. (PVDF) has been used across a Svariety of chemical process indus- tries (CPI) sectors due to its versatility and IN BRIEF broad attributes. With flagship applications PVDF AND THE in architectural coatings and the CPI, the FLUOROPOLYMER FAMILY breadth of industries where PVDF is utilized today is expansive. PVDF components (Fig- COPOLYMERS CHANGE ures 1 and 2) are utilized and installed where FLEXURAL PROPERTIES engineers are looking to maximize longevity PVDF COMPONENTS and reliability of process parts in many CPI sectors, including semiconductor, pharma- FIGURE 1. A variety of fluoropolymer components are shown ceutical, food and beverage, petrochemi- here cal, wire and cable, and general chemicals. change the performance properties. Fluo- PVDF and the fluoropolymer family ropolymers are divided into two main cat- PVDF is a high-performance plastic that falls egories: perfluorinated and partially fluori- into the family of materials called fluoropoly- nated [1]. The partially fluorinated polymers mers. Known for robust chemical resistance, contain hydrogen or other elements, while fluoropolymers are often utilized in areas the perfluorinated (fully fluorinated) poly- where high-temperature corrosion barriers mers are derivatives or copolymers of the are crucial. In addition to being chemically tetrafluoroethylene (C2F4) monomer. Com- resistant and non-rusting, this family of poly- monly used commercial fluoropolymers mers is also considered to have high purity, include polytetrafluoroethylene (PTFE), non-stick surfaces, good flame and smoke perfluoroalkoxy polymer (PFA), fluorinated resistance, excellent weathering and ultra- ethylene propylene (FEP), polyvinylidene violet (UV) stability. -
Ultrapure Water
Ultrapure Water General Filter Requirements Achieving and maintaining ultrapure water (UPW) is extremely important in light of its widespread presence throughout the manufacture of semiconductor integrated circuits. The technology of the industry has advanced so rapidly over the past few years that it has redefined cleanliness requirements, specifically with regard to the need for quantitatively removing colloidal silica, particles, total organic carbon (TOC), bacteria, pyrogens (bacterial fragments) and metal ions. A well-designed UPW system with strategically placed filters, will ensure achievement of this goal, since the type of filter selected in each of the key areas will make a measurable difference in ultimate quality. To meet the demands of a high-purity deionized (DI) water system, filters must: • Not contribute organic, particulate or metal ion contamination to the effluent stream • Not unload trapped contaminants or shed filter material • Be integrity testable to verify removal ratings • Perform identically from lot to lot • Have a low-pressure drop for long life and maximum economy. DI Water Filter A well-maintained UPW system will have a number of carefully selected filters and purifiers placed in strategic positions. A schematic of a DI water system is depicted below. The locations of the filters are representative of those found in a typical water system. Reverse Osmosis (RO) Pretreatment Microza* UNA System Pretreatment is required to operate RO units effectively and economically. The pretreatment will vary depending on the source of the incoming feed water. With surface water as the feed, conventional pretreatment may include such unit operations as coagulation, flocculation, settling, granular media filtration, and cartridge filtration. -
Arium® Pro Ultrapure Water Systems Application-Orientated and Flexible to Meet the Highest Demands
arium® pro Ultrapure Water Systems Application-Orientated and Flexible to Meet the Highest Demands Modular – selection of five systems specially for your application Flexible – perfect fit to every laboratory environment Easy to use – glass touch display with intuitive menu Water Purification in Laboratories navigation arium® pro ultrapure water systems Description Modular The arium® pro series offers a flexible and The selection of five systems contains module modular system which, compared to conven- components specially tailored to your appli- tional devices, demonstrates excellent cost cation. arium® pro supplies the desired level efficiency. of ultrapure water quality for any critical and standard applications. All systems meet and exceed the ASTM Type 1 water quality standards and ensure the best Flexible reproducible results in their class. Up to The space-saving installation of the device 2 liter of consistently high-quality ultrapure on, under, or above your workstation water with a conductivity of 0.055 µS/cm integrates it perfectly into any laboratory. (0 18.2 MO + cm) can be dispensed each The display-dispense unit can be flexible minute. The ultrapure water is virtually positioned. microorganism-free when a Sartopore® 2 150 end filter is used. Display with touch-function Even the opening of the dispensing valve The patented Sartorius technology, SD card can be controlled by the unique display. slot, long service life, and low maintenance Simply navigate intuitively in the easy-to- requirement distinguish the arium® pro use and clear menu navigation by lightly systems as easy-to-use, efficient and reliable touching the display – even with gloves. Type 1 ultrapure water systems. -
2004/12/27-LES Prefiled Exhibit 135-M, Hydrogen Fluoride Industry
I IJ Materials of Construction Guideline for Anhydrous Hydrogen Fluoride UPDATED: 12/27/04 LAST REVISION: January 2000 EXPIRATION DATE: 12/31/05 Dn1C.KETED USNRC February 24, 2006 (4:12pm) OFFICE OF SECRETARY RULEMAKINGS AND ADJUDICATIONS STAFF HYDROGEN FLUORIDE INDUSTRY PRACTICES INSTITUTE Docket No. 70-3103-ML Materials of Construction Task Group Materials of Construction Guideline for Anhydrous Hydrogen Fluoride The Hydrogen Fluoride Industry Practices Institute (HFIPI) is a subsidiary of the American Chemistry Council (ACC). LES Exhibit 135-M rem n/ate -se V- oea6 Materials of Construction Guideline for Anhydrous Hydrogen Fluoride UPDATED: 12/27/04 L. LAST REVISION: January 2000 EXPIRATION DATE: 12/31/05 MATERIALS OF CONSTRUCTION GUIDELINE FOR ANHYDROUS HYDROGEN FLUORIDE This document has been prepared by the "Materials of Construction Task Group" of the Hydrogen Fluoride Industry Practices Institute (HFIPI). The members of this Task Group participating in preparation of this guideline were: M. Howells (Chairman) Honeywell H. Jennings DuPont G. Navar* LCI/Norfluor E. Urban* AlliedSignal P.Wyatt Arkema Inc. William Heineken BWXT Y-12 Mike Berg Solvay Fluorides, LLC * Former Task Group member ©2004 Hydrogen Fluoride Industry Practices Institute This document cannot be copied or distributed without the express written consent of the Hydrogen Fluoride Industry Practices Institute ("HFIPI"). Copies of this document are available from the HFIPI, c/o Collier Shannon Scott, 3050 K Street, NW, Suite 400, Washington, DC 20007-5108. Materials