22. Cathodic Protection
Total Page:16
File Type:pdf, Size:1020Kb
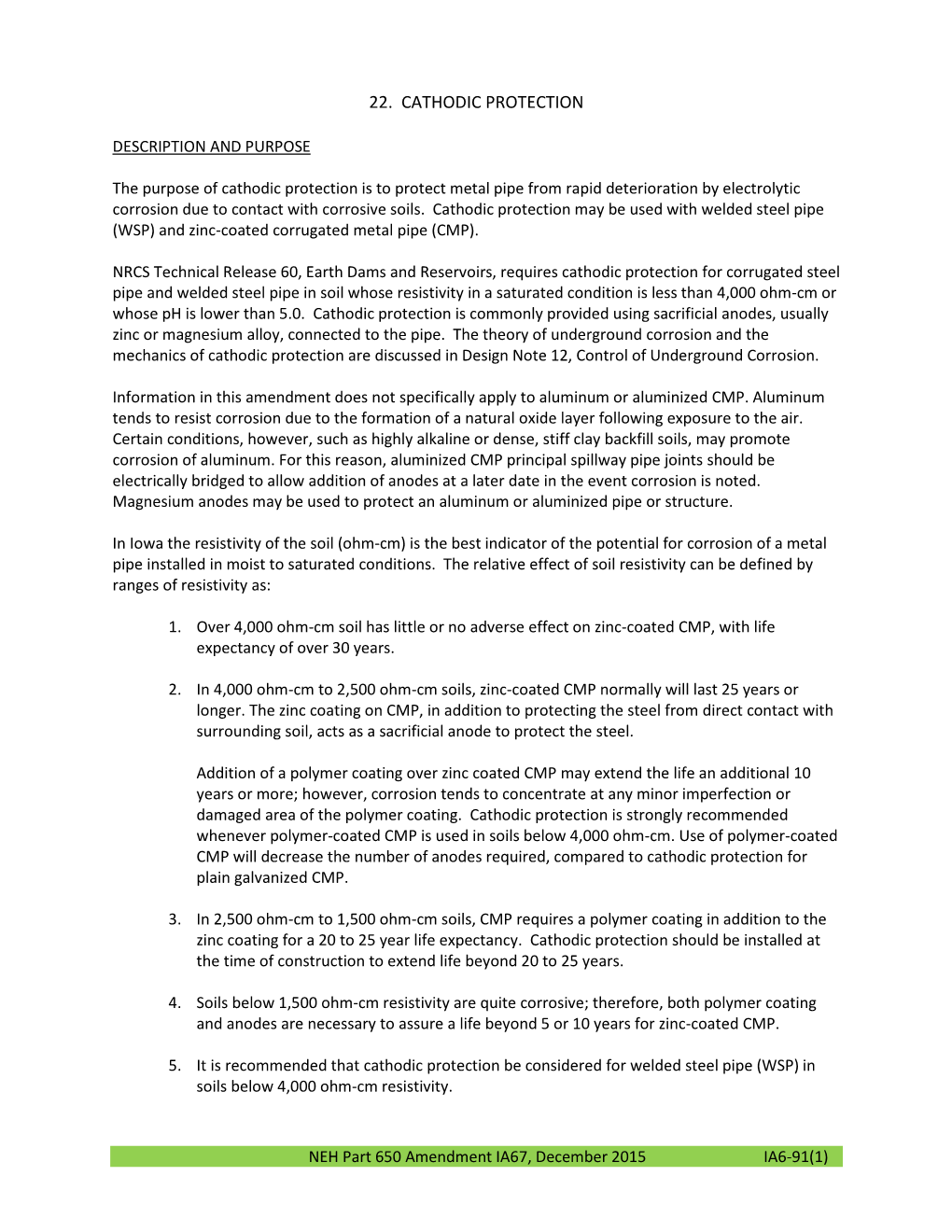
Load more
Recommended publications
-
Cathodic Protection of Concrete Bridges: a Manual of Practice
SHRP-S-372 Cathodic Protection of Concrete Bridges: A Manual of Practice J. E. Bennett John J. Bartholomew ELTECH Research Corporation Fairport Harbor, Ohio James B. Bushman Bushman & Associates Medina, Ohio Kenneth C. Clear K. C. Clear, Inc. Boston, Virginia Robert N. Kamp Consulting Engineer Albany, New York Wayne J. Swiat Corrpro Companies, Inc. Medina, Ohio Strategic Highway Research Program National Research Council Washington, DC 1993 SHRP-S-372 ISBN 0-309-05750-7 Contract C-102D Product No. 2034 Program Manager: Don M. Harriott Project Manager: It. Martin (Marty) Laylor Consultant: John P. Broomfield Production Editor: Cara J. Tate Program Area Secretary: Carina S. Hreib December 1993 key words: bridges bridge maintenance bridge rehabilitation cathodic protection chlorides corrosion corrosion prevention corrosion rate CP electrochemical methods reinforced concrete Strategic Highway Research Program National Academy of Sciences 2101 Constitution Avenue N.W. Washington, DC 20418 (202) 334-3774 The publication of this report does not necessarily indicate approval or endorsement of the findings, opinions, conclusions, or recommendations either inferred or specifically expressed herein by the National Academy of Sciences, the United States Government, or the American Association of State Highway and Transportation Officials or its member states. © 1993 National A_zademy of Sciences I.SM/NAP/1293 Acknowledgments The research described herein was supported by the Strategic Highway Research Program (SHRP). SHRP is a unit of the National Research Council that was authorized by section 128 of the Surface Transportation and Uniform Relocation Assistance Act of 1987. This report is a compilation of work by ELTECH Research Corporation, Corrpro Companies, Inc., and Kenneth C. -
Analysis of Alternatives
ANALYSIS OF ALTERNATIVES Legal name of applicants: Henkel AG & Co. KGaA; Henkel Global Supply Chain B.V. Submitted by: Henkel AG & Co. KGaA. Substance: Dichromium tris(chromate), EC No: 246-356-2, CAS No: 24613-89-6 Use title: Use of Dichromium tris(chromate) for surface treatment of metals such as aluminium, steel, zinc, magnesium, titanium, alloys, composites, sealings of anodic films Use number: 2 Use number: 2 Copy right protected - Property of Members of the CCST Consortium - No copying / use allowed. ANALYSIS OF ALTERNATIVES Disclaimer This document shall not be construed as expressly or implicitly granting a license or any rights to use related to any content or information contained therein. In no event shall applicant be liable in this respect for any damage arising out or in connection with access, use of any content or information contained therein despite the lack of approval to do so. ii Use number: 2 Copy right protected - Property of Members of the CCST Consortium - No copying / use allowed. ANALYSIS OF ALTERNATIVES CONTENTS DECLARATION .......................................................................................................................................................... XV 1. SUMMARY 1 2. INTRODUCTION .................................................................................................................................................. 8 2.1. Substances ........................................................................................................................................ 8 2.2. -
Galvanic Corrosion
10 GALVANIC CORROSION X. G. ZHANG Teck Metals Ltd., Mississauga, Ontario, Canada A. Introduction graphite, are dispersed in a metal, or on a ship, where the B. Definition various components immersed in water are made of different C. Factors in galvanic corrosion metal alloys. In many cases, galvanic corrosion may result in D. Material factors quick deterioration of the metals but, in other cases, the D1. Effects of coupled materials galvanic corrosion of one metal may result in the corrosion D2. Effect of area protection of an attached metal, which is the basis of cathodic D3. Effect of surface condition protection by sacrificial anodes. E. Environmental factors Galvanic corrosion is an extensively investigated subject, E1. Effects of solution as shown in Table 10.1, and is qualitatively well understood E2. Atmospheric environments but, due to its highly complex nature, it has been difficult to E3. Natural waters deal with in a quantitative way until recently. The widespread F. Polarity reversal use of computers and the development of software have made G. Preventive measures great advances in understanding and predicting galvanic H. Beneficial effects of galvanic corrosion corrosion. I. Fundamental considerations I1. Electrode potential and Kirchhoff’s law I2. Analysis B. DEFINITION I3. Polarization and resistance I4. Potential and current distributions When two dissimilar conducting materials in electrical con- References tact with each other are exposed to an electrolyte, a current, called the galvanic current, flows from one to the other. Galvanic corrosion is that part of the corrosion that occurs at the anodic member of such a couple and is directly related to the galvanic current by Faraday’s law. -
Introduction Engineering 360.826.4570 Nwcorrosion.Com Jeremy Hailey, P.E
Jeremy Hailey Northwest Corrosion Introduction Engineering 360.826.4570 nwcorrosion.com Jeremy Hailey, P.E. • Corrosion Engineer with 16 years experience • Started NW Corrosion Engineering 10 years ago • Focus on corrosion control system designs, troubleshooting, and some installation work • Conduct training seminars and classes for Steel Tank Institute, National Association of Corrosion Engineers, and the American Water Works Ass’n. • NACE Certified Corrosion Specialist, Cathodic Protection Specialist, and Certified Coating Inspector Jeremy Hailey Northwest Corrosion Topics of Discussion Engineering 360.826.4570 nwcorrosion.com 1. Corrosion Theory 2. Methods of Corrosion Control 3. Corrosion Protection Criteria 4. Considerations for Design of Corrosion Control Systems Jeremy Hailey Northwest Corrosion Corrosion Theory Engineering 360.826.4570 nwcorrosion.com All materials have various physical properties – Color, hardness, ductility, shear strength, ability to conduct heat, melting point, electrical potential….. Corrosion in metal occurs because of an electrical imbalance, or electrical potential difference. Much like when two beakers of water, each at a different temperature, are poured together the resulting temperature will be somewhere between the two starting temperatures. Jeremy Hailey Northwest Corrosion Requirements of a Corrosion Cell Engineering 360.826.4570 nwcorrosion.com For corrosion to occur, four individual items must be present: 1. Anode – The place where corrosion occurs; the more electronegative site 2. Cathode -
State of the Art Cathodic Protection Practices and Equipment State of the Art
State of the Art Cathodic Protection Practices and Equipment State of the Art Definition: The level of development (as of a device, procedure, process, technique, or science) reached at any particular time usually as a result of modern methods Cathodic Protection 9 Type 9 Materials 9 Installation 9 Monitor / Survey Techniques Types of Cathodic Protection Sacrificial Anode ¾Small Current Requirement • Well Coated Structures • Isolated Structures ¾Low to Medium Soil Resistivity Types of Cathodic Protection Impressed Current ¾ Large Current Requirement • Poorly Coated Structures • Shorted Structures ¾ High Soil Resistivity Sacrificial Anodes Magnesium & Zinc Typical Sacrificial Anode Zinc Ribbon TYPICAL SACRIFICIAL ANODE INSTALLATION SINGLE ANODE MULTIPLE ANODE GRADE GRADE PIPE PIPE AT PIPE DEPTH TO 5' TYPICAL ANODE ANODE ANODE ANODE 10'-15' MIN 5' TO 15' ANODE FOR MAGNESIUM TYPICAL 5' MIN FOR ZINC 5' MIN Typical Sacrificial Anode Installation Typical Sacrificial Anode Installation Typical Sacrificial Anode Installation Ribbon Anode Impressed Current Rectifier ¾ Constant Voltage ¾ Constant Current ¾ Auto Potential ¾ Pulse ¾ Alternative Power ¾Solar ¾ Thermo Electric ¾ Wind ¾ Hydro Impressed Current Anode Graphite Impressed Current Anode High Silicon Cast Iron Impressed Current Anode Mixed Metal Oxide TYPICAL IMPRESSED CURRENT ANODE INSTALLATION DISTRUBUTED PIPE PIPE - RECTIFIER + ANODE ANODE ANODE ANODE ANODE ANODE TYPICAL IMPRESSED CURRENT ANODE INSTALLATION REMOTE RECTIFIER ANODES - + PIPE 200' TO 500' TYPICAL TYPICAL IMPRESSED CURR 50' -
Cathodic Protection
December 6, 2016 Bridge Preservation in Corrosive Environments Using Cathodic Protection Transportation Research Board Webinar Presenters: Atiq H. Alvi, PE T.Y. Lin International Ivan Lasa Florida Department of Transportation Ali Akbar Sohangpurwala Concorr, Inc. Statistics Cost of Corrosion Corrosion Comprehensive Study 2002 Corrosion Costs and Preventive Strategies in the United States” PUBLICATION NO. FHWA-RD-01-156 Corrosion Total Direct Cost of Corrosion in the U.S. $276 billion per year = 3.1% of GDP Corrosion Costs and Preventive Strategies in the United States” PUBLICATION NO. FHWA-RD-01-156 Corrosion • 587,964 Bridges • Average Age = 40 years • 40% are ate least 40 years or older • 14% Structurally Deficient w/ Corrosion as Primary Cause • Cost to maintain $5.8 billion per year • Cost to improve $10.6 billion • Cost of corrosion to bridges $8.29 billion (not including cost to traveling public) Corrosion Costs and Preventive Strategies in the United States” PUBLICATION NO. FHWA-RD-01-156 Overview of the Corrosion Process Corrosion Process Four Components Needed for Corrosion Process • Electrolyte • Anodic Reaction • Cathodic Reaction • Electrical Path Corrosion Process Metals Return to Nature • Natural Ores Combined with Oxygen, Sulfur, etc. • Smelting Process • Extracted Metallic Materials • Eventually Return to Natural Condition - Corrosion Corrosion Process Ores in Natural State Corrosion Process Smelting Process Corrosion Process Extracted Metallic Materials Corrosion Process Eventual Return to Natural Condition Corrosion -
CORROSION PROTECTION PROVIDED by TRIVALENT CHROMIUM PROCESS CONVERSION COATINGS on ALUMINUM ALLOYS By
CORROSION PROTECTION PROVIDED BY TRIVALENT CHROMIUM PROCESS CONVERSION COATINGS ON ALUMINUM ALLOYS By Liangliang Li A DISSERTATION Submitted to Michigan State University in partial fulfillment of the requirements for the degree of Chemical Engineering – Doctor of Philosophy 2013 ABSTRACT CORROSION PROTECTION PROVIDED BY TRIVALENT CHROMIUM PROCESS CONVERSION COATINGS ON ALUMINUM ALLOYS By Liangliang Li High strength aluminum alloys are widely used in aviation and aerospace industries because of their desirable strength/weight ratio that results from the alloy addition ( e.g. , Cu, Fe etc ). However, this alloy addition causes pitting corrosion of the aluminum surrounding those intermetallic inclusions. One efficient way to inhibit the corrosion is through the protective coating system that contains the topcoat, primer, and conversion coating. The conversion coating is in direct contact with the alloy surface and is expected to provide both good corrosion protection and adhesion. The chromate conversion coating (CCC) has been widely used in aviation/aerospace industry and provides excellent active corrosion protection and adhesion to aluminum alloys. Unfortunately, the Cr(VI) is toxic and chromate is a carcinogen. Therefore, a trivalent chromium process (TCP) coating was developed as a drop-in replacement of CCC. This dissertation focuses on a fundamental understanding of the formation mechanism, chemical structure, and basic electrochemical properties of the TCP coating on three high strength aluminum alloys: AA2024-T3, AA6061-T6, and AA7075- T6. The formation of the TCP coating is driven by an increase in the interfacial pH. The coating is about 50-100 nm thick and has a biphasic structure consisting of a 3- ZrO 2/Cr(OH) 3 top layer and an AlF 6 /Al(OH) 3 interfacial layer. -
Underground Storage Tank Management Division Galvanic (Sacrificial Anode) Cathodic Protection System Evaluation
Underground Storage Tank Management Division Galvanic (Sacrificial Anode) Cathodic Protection System Evaluation This form must be utilized to evaluate underground storage tank (UST) cathodic protection systems in South Carolina. Access to the soil directly over the cathodically protected structure that is being evaluated must be provided. A site drawing depicting the UST cathodic protection system and all reference electrode placements must be completed. I. UST OWNER II. UST FACILITY Name: Name: ID#: Address: Address: City: State: City: County: III. CP TESTER IV. CP TESTER’S QUALIFICATIONS Tester’s Name: NACE International Certification#: Company Name: Certification Date: Type of Certification: Address: Source of Certification: City: State: Other (Explain): V. REASON SURVEY WAS CONDUCTED (mark only one) o Routine-3 year o Routine-within 6 months of installation o 60-day re-survey after fail o Re-survey after repair/modification Date next cathodic protection survey must be conducted by _____________(required within 6 months of installation/repair & every 3 years thereafter) VI. CATHODIC PROTECTION TESTER’S EVALUATION (mark only one) o PASS All protected structures at this facility pass the cathodic protection survey and it is judged that adequate cathodic protection has been provided to the UST system (indicate all criteria applicable by completion of Section VIII). o FAIL One or more protected structures at this facility fail the cathodic protection survey and it is judged that adequate cathodic protection has not been provided to the UST system (complete Section IX). o INCONCLUSIVE If the remote and the local do not both indicate the same test result on all protected structures (both pass or both fail), inconclusive is indicated and the survey must be evaluated and/or conducted by a corrosion expert (complete Section VII). -
Guidelines for Field Installation of Corrosion Monitoring and Cathodic Protection Systems
Technical Memorandum No. MERL-2012-40 Guidelines for Field Installation of Corrosion Monitoring and Cathodic Protection Systems U.S. Department of the Interior Bureau of Reclamation December 2012 Mission Statements The U.S. Department of the Interior protects America’s natural resources and heritage, honors our cultures and tribal communities, and supplies the energy to power our future. The mission of the Bureau of Reclamation is to manage, develop, and protect water and related resources in an environmentally and economically sound manner in the interest of the American public. Technical Memorandum No. MERL-2012-40 Guidelines for Field Installation of Corrosion Monitoring and Cathodic Protection Systems U.S. Department of the Interior Bureau of Reclamation December 2012 BUREAU OF RECLAMATION Technical Service Center, Denver, Colorado Materials Engineering and Research Lab Group, 86-68180 Technical Memorandum No. MERL-2012-40 Guidelines for Field Installation of Corrosion Monitoring and Cathodic Protection Systems 8/2 --------Mfed:r Daryl A. Little Date "Materials Engineer, Materials Engineering and Research Lab Group, 86-68180 Z- Che1648: Jessica D. Tor� Date Materials Engineer, Mats Engineering and Research Lab Group, 86-68180 � Editorial Approval: Teri Manross Date Technical Writer-E 'tor, Client Support and Technical Presentations Office, 86-68010 ( Technic�oval: Lee E. Sears� Date Material ngineer, Materials Engineering and Research Lab Group, 86-68180 ///7 �- Peer Review: William F. Kepler, P.E. Date Civil Engineer, Materials Engineering and Research Lab Group, 86-68180 REVISIONS l l d Date Description d e ica va ke ar c ro iew hn c he Rev Prep Peer C Te App Contents Page Chapter I: Introduction........................................................................................1 Corrosion Monitoring and Cathodic Protection Systems ................................ -
INTEGRATED CORROSION ENGINEERING Eight Decades of Innovation
INTEGRATED CORROSION ENGINEERING Eight Decades of Innovation Integrated Corrosion Engineering (ICE) is SERVICES PROVIDED comprised of licensed and experienced • FEED Studies and detailed engineering & professionals for the cathodic protection design industry. ICE is a full turnkey division of • Bid Submittal assistance to general contractors & operating companies ICC for all cathodic protection services. • Bill of materials and procurement coordination & recommendations • Capabilites of expiditing long lead CP materials through BK Corrosion & JA Electronics • Field Engineers & Technicians for assembly in the field • Final testing for commissioning followed by a detailed report that meets NACE Standards & Requirements • Annual Survey Compliance & Maintenance COMMON APPLICATIONS • Carbon Steel & Ductile Iron Pipelines • Well Castings • New & Existing Storage Tanks • Rail Transit Systems • Soil Resistivity Testing • Plant & Facility Piping • Marine Vessels • Bridges An Integrated Corrosion Company WHY INTEGRATED CORROSION ENGINEERING? Integrated Corrosion Engineering (ICE) is a leading storage tanks; industrial plants; oil and natural provider of cathodic protection and corrosion gas facilities, piping, vessels and storage tanks; engineering services. With decades of practical and government infrastructure such as dams and professional experience, our company has been able bridges; reinforced concrete structures; marine to refine our expertise, sophistication and capabilities facilities; piping and offshore structures. to economically support -
Understanding Cathodic Protection and Its Applications
Jeff Schramuk NACE CP Specialist 5/25/2017 #7695 IEEE‐IAS/IES Dinner Presentation: 5/24/2017 Understanding Cathodic Protection and Its Applications Jeff Schramuk NACE CP Specialist #7695 630‐235‐1559 www.cpsolutionsinc.net 1 Topics to be Covered 1. Corrosion Problems Facing Water Utilities 2. Asset Management 3. Corrosion Chemistry with Specific Examples 4. Pipe Materials and Coatings 5. Basic Cathodic Protection 6. CP for Existing WMs using an Anode Retrofit Program 7. Cathodic Protection for New Water Mains 8. Cathodic Protection Performance Verification 9. Stray DC Current Interference 2 www.cpsolutionsinc.net 1 Jeff Schramuk NACE CP Specialist 5/25/2017 #7695 Section 1 Corrosion Problems Facing Water Utilities 3 What’s the Rest of the (Unexcavated) Pipe Look Like? 4 www.cpsolutionsinc.net 2 Jeff Schramuk NACE CP Specialist 5/25/2017 #7695 State of the Water Industry Report – Year 2016 The Top 3 Issues Facing the Water Industry by All Respondents 1. Renewal & replacement of aging water and wastewater infrastructure. 2. Financing for capital improvements. 3. Public understanding of the value of water systems and services. Source: “2016 State of the Water Industry: The Cornerstone Needs Support”, Journal AWWA, 108:7, Jul-2016, pp. 63-73. 5 What is the leading cause of many water main breaks? Corrosion! 6 www.cpsolutionsinc.net 3 Jeff Schramuk NACE CP Specialist 5/25/2017 #7695 What Are the Consequences of Pipeline Failures? Energy Pipeline “Incidents” Water Main Breaks 7 Section 2 Asset Management 8 www.cpsolutionsinc.net 4 Jeff Schramuk NACE CP Specialist 5/25/2017 #7695 Asset Management: A Real‐World Definition “A water utility’s asset management plan is an optimization process that attempts to meet the competing objectives of cost minimization and reliability maximization.” Source: Rubin, S.J., A Call for Reliability Standards, Journal AWWA, (Jan-2011) 9 Evaluating Failure Risk: Probability vs. -
Cathodic Protection NOD, Phase I Uniform National Discharge
This document is part of Appendix A, Cathodic Protection: Nature of Discharge for the “Phase I Final Rule and Technical Development Document of Uniform National Discharge Standards (UNDS),” published in April 1999. The reference number is EPA-842-R-99-001. Phase I Final Rule and Technical Development Document of Uniform National Discharge Standards (UNDS) Appendix A Cathodic Protection: Nature of Discharge April 1999 NATURE OF DISCHARGE REPORT Cathodic Protection 1.0 INTRODUCTION The National Defense Authorization Act of 1996 amended Section 312 of the Federal Water Pollution Control Act (also known as the Clean Water Act (CWA)) to require that the Secretary of Defense and the Administrator of the Environmental Protection Agency (EPA) develop uniform national discharge standards (UNDS) for vessels of the Armed Forces for “...discharges, other than sewage, incidental to normal operation of a vessel of the Armed Forces, ...” [Section 312(n)(1)]. UNDS is being developed in three phases. The first phase (which this report supports), will determine which discharges will be required to be controlled by marine pollution control devices (MPCDs)—either equipment or management practices. The second phase will develop MPCD performance standards. The final phase will determine the design, construction, installation, and use of MPCDs. A nature of discharge (NOD) report has been prepared for each of the discharges that has been identified as a candidate for regulation under UNDS. The NOD reports were developed based on information obtained from the technical community within the Navy and other branches of the Armed Forces with vessels potentially subject to UNDS, from information available in existing technical reports and documentation, and, when required, from data obtained from discharge samples that were collected under the UNDS program.