Offshore Wind Turbine Market Developments in the Netherlands
Total Page:16
File Type:pdf, Size:1020Kb
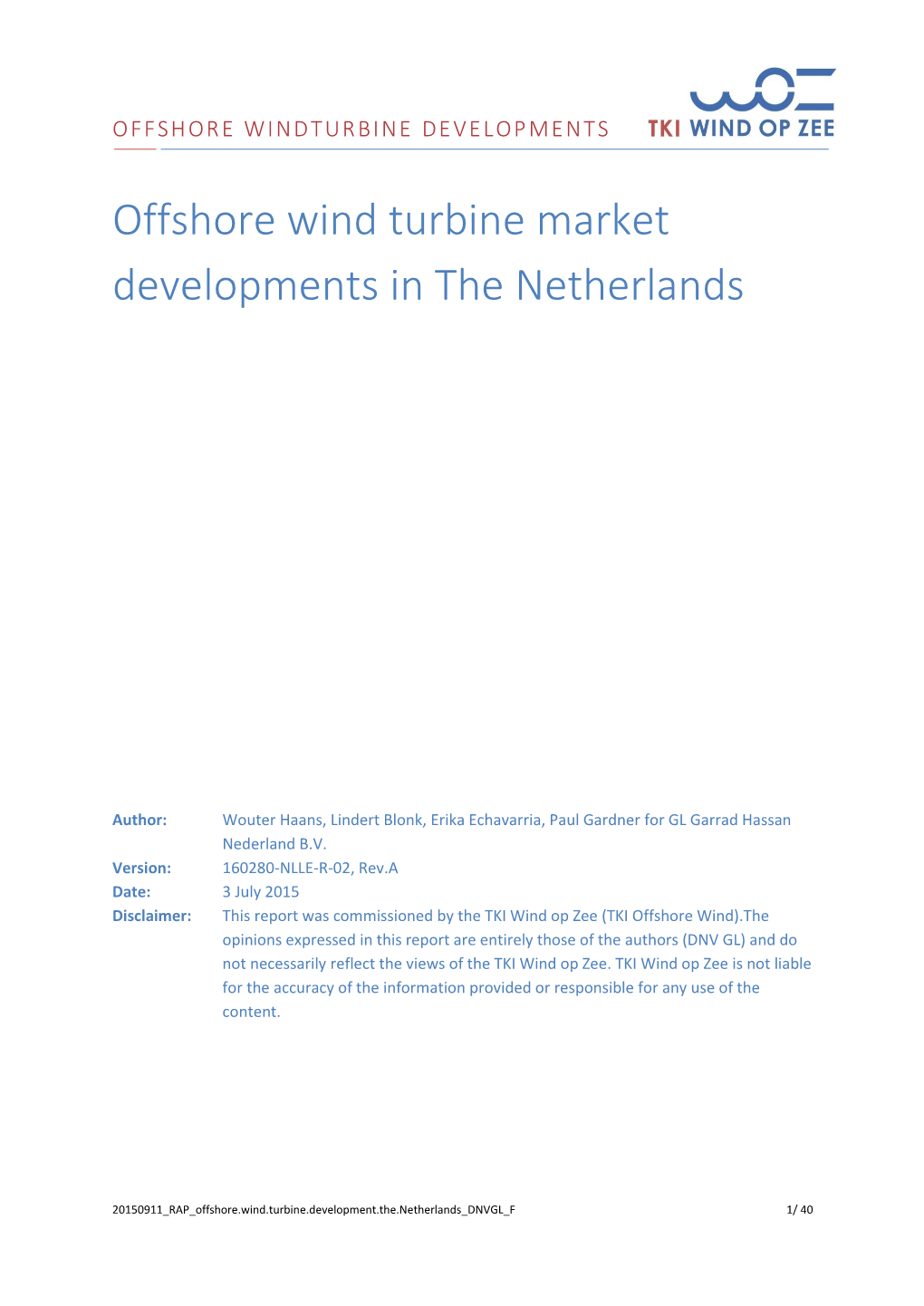
Load more
Recommended publications
-
Investigation of Innovative Structuers and Materials of the Towers Used in Wind Turbines
SCHOOL OF SCIENCE AND ENGINEERING INVESTIGATION OF INNOVATIVE STRUCTUERS AND MATERIALS OF THE TOWERS USED IN WIND TURBINES Rawane Abdaoui Suppurvised by : Abderrazzak El Boukili May 3rd / 2018 Table of Contents Table of Figures .......................................................................................................................... 3 Abstract ...................................................................................................................................... 7 Introduction ............................................................................................................................... 8 STEEPLE ANALYSIS .................................................................................................................... 11 Chapter 1: General Overview on Wind Turbines ...................................................................... 13 How is wind created?..................................................................................................................... 13 Types of Turbines based on the site .................................................................................................. 16 Offshore wind farms ...................................................................................................................... 16 Onshore wind farms ...................................................................................................................... 17 Types of Wind Turbines based on formalities .................................................................................. -
Theme 1 | Mini-Symposia WESC 2021
Theme 1 | Mini-Symposia Mini-Symposium: Advances in Lattice Boltzmann Methods in Wind Energy Stefan Ivanell, Henrik Asmuth (Uppsala University) Mini-Symposium: Advances in Lattice Boltzmann Methods in Wind Energy May 25 13:40 - 15:20 CEST Session Chairs: Stefan Ivanell (Uppsala University) (moderators) Henrik Asmuth (Uppsala University) Time Duration Speaker Affiliation Title 13:45 - 14:15 25 + 5 min Manfed Krafczyk TU Braunschweig GPGPU-accelerated Urban Scale Wind Simulations based on Lattice-Boltzmann methods Eastern Switzerland University Investigation of the influence of the inlet boundary conditions on the turbulent flow over 14:15 - 14:35 15 + 5 min Alain Schubiger of Applied Sciences a smooth 3-D hill 14:35 - 14:55 15 + 5 min Henrik Asmuth Uppsala University Lattice Boltzmann Large-eddy Simulation of Neutral Atmospheric Boundary Layers Friedrich-Alexander University A Holistic CPU/GPU Approach for the Actuator Line Model in Lattice Boltzmann 14:55 - 15:15 15 + 5 min Helen Schottenhamml Erlangen Simulations Session briefing: starting from 12:30 CEST (same virtual room) WESC 2021 Theme 1 | Mini-Symposia Mini-Symposium: Array-Array Interactions and Downstream Wake Effects Rebecca J. Barthelmie, Sara C. Pryor (Cornell University), Charlotte Hasager (DTU Wind Energy) Mini-Symposium: Array-Array Interactions and Downstream Wake Effects (I) May 25 15:30 - 17:10 CEST Session Chairs: Sara C. Pryor (Cornell University) (moderators) Charlotte Hasager (DTU Wind Energy) Time Duration Speaker Affiliation Title 15:30 - 15:50 15 + 5 min Jana -
SRI: Wind Power Generation Project Main Report
Environment Impact Assessment (Draft) May 2017 SRI: Wind Power Generation Project Main Report Prepared by Ceylon Electricity Board, Ministry of Power and Renewable Energy, Democratic Socialist Republic of Sri Lanka for the Asian Development Bank. CURRENCY EQUIVALENTS (as of 17 May 2017) Currency unit – Sri Lankan rupee/s(SLRe/SLRs) SLRe 1.00 = $0.00655 $1.00 = SLRs 152.70 ABBREVIATIONS ADB – Asian Development Bank CCD – Coast Conservation and Coastal Resource Management Department CEA – Central Environmental Authority CEB – Ceylon Electricity Board DoF – Department of Forest DS – District Secretary DSD – District Secretaries Division DWC – Department of Wildlife Conservation EA – executing agency EIA – environmental impact assessment EMoP – environmental monitoring plan EMP – environmental management plan EPC – engineering,procurement and construction GND – Grama Niladhari GoSL – Government of Sri Lanka GRM – grievance redress mechanism IA – implementing agency IEE – initial environmental examination LA – Local Authority LARC – Land Acquisition and Resettlement Committee MPRE – Ministry of Power and Renewable Energy MSL – mean sea level NARA – National Aquatic Resources Research & Development Agency NEA – National Environmental Act PIU – project implementation unit PRDA – Provincial Road Development Authority PUCSL – Public Utility Commission of Sri Lanka RDA – Road Development Authority RE – Rural Electrification RoW – right of way SLSEA – Sri Lanka Sustainable Energy Authority WT – wind turbine WEIGHTS AND MEASURES GWh – 1 gigawatt hour = 1,000 Megawatt hour 1 ha – 1 hectare=10,000 square meters km – 1 kilometre = 1,000 meters kV – 1 kilovolt =1,000 volts MW – 1 megawatt = 1,000 Kilowatt NOTE In this report, “$” refers to US dollars This environmental impact assessment is a document of the borrower. The views expressed herein do not necessarily represent those of ADB's Board of Directors, Management, or staff, and may be preliminary in nature. -
Kite Power Technologie
KITE POWER TECHNOLOGIE Het besturingssysteem hangt ongeveer 10 m onder de vlieger Roland Schmehl Associate Professor, Institute for Applied Sustainable Science, Engineering and Technology (ASSET), TU Delft De wind hoog boven de grond wordt gezien als een potentieel zeer grote bron van duurzame energie. Conventionele windturbines met hun starre toren zullen nooit in staat zijn deze bron ten volle te benutten. Eén van de mogelijke oplossingen om deze wind op grote hoogte te benutten, is het gebruik van kite power systemen. De kite power onderzoeksgroep van het ASSET instituut aan de TU Delft is bezig met de ontwikkeling van een kite power systeem gebaseerd op pompende cycli. Het 20 kW test systeem maakt gebruik van een enkele kabel die de kite met de grond verbindt. De kite wordt bestuurd door middel van een besturingssyseem onder de kite. Systematische tests in 2010 hebben bevestigd dat het pompende concept geïmplementeerd kan worden met een relatief laag energieverlies veroorzaakt door de pompende beweging. Het concept is Alle afbeeldingen bij dit artikel: een aantrekkelijke optie voor het onttrekken van windenergie van grote Asset, TU Delft hoogte en heeft de potentie om significant goedkoper energie te produceren dan conventionele windturbines. 22 WIND NIEUWS - APRIL 2011 Figuur 1: Energie producerende fase (kabel uitrollen) en energie consumerende fase (kabel inrollen). High altitude wind power Het onttrekken van windenergie van grote hoogte brengt een aantal voordelen met zich mee. Ten eerste het feit dat de wind op hoogte harder en constanter is dan de wind waartoe conventionele windturbines toegang hebben. Hierdoor kunnen vliegende wind energie (Airborne Wind Energy, AWE) systemen, die boven de 150 m ingezet kunnen worden, een substantieel hogere capaci - teits factor hebben. -
LEANING INTO the WIND Building Sustainable Wind Power in China
LEANING INTO THE WIND Building Sustainable Wind Power in China Lauren Caldwell, Emily Chen, Felix Zhang May 9, 2014 This is one of a series of case studies prepared for the class Case Studies in Sustainable Development: Smart Cities and Urban Innovation. The information presented here is not intended to propose solutions or to make recommendations. Instead, it provides a framework for examining issues affecting urban centers globally through the lens of sustainable development. Leaning into the Wind Introduction South of the Gobi Desert, about 1,200 miles west of Beijing, are vast fields lined with more than 3,500 fiberglass wind turbines.1 Jiuquan prefecture, Gansu province, is located in northwestern China and home to one of China’s latest superlative endeavors. The Jiuquan Wind Power Base is one of several multi-gigawatt megaprojects planned by China’s National Energy Administration to reduce carbon emissions and expand the country’s renewable energy capacity. Upon its completion in 2015, the Jiuquan Wind Power Base will be the largest wind power collective in the world. Investment in renewable energy has become a priority for the Chinese government. Pollution levels in the country have reached an all-time high, prompting concern both domestically and internationally. In January 2013, a report concluded that severe air pollution had reduced average life expectancy by 5.5 years in northern China. The research attributed higher instances of heart disease, cancer, and strokes to toxic air.2 In 2011, about 69 percent of China’s energy consumption was supplied by coal, compared to the world average of about 40 percent. -
Exhibit 11R Drawings and Specifications of Gamesa Eolica
Exhibit 11R Drawings and Specifications of Gamesa Eolica Wind Turbines The Applicant plans to use Gamesa G90 Wind Turbines at the Marble River Wind Farm (see enclosure #1, press announcement of purchase of Gamesa turbines). Gamesa is a leading company in the design, manufacturing, installation, operation and maintenance of wind turbines. In 2004, Gamesa was ranked second worldwide in a ranking of the Top 10 wind turbine manufacturers by BTM Consult, with a market share of 18.1%. In Spain, Gamesa Eólica is the leading manufacturer and supplier of wind turbines, with a market share of 56.8% in 2004. One of the partners in the Marble River Wind Farm, Acciona, has had a significant and successful history with Gamesa turbines. Gamesa has used the experience gained in its home market to develop a robust, adaptable wind turbine suitable for most wind conditions in the USA. Gamesa Wind US will carry out a major portion of the manufacturing of the wind turbines planned for Marble River in the Mid-Atlantic region, where Gamesa is already active in development and construction of wind energy projects. Gamesa G90 The Gamesa G90 is a 2-MW, three-bladed, upwind pitch regulated and active yaw wind turbine. The G90 has a blade length of 44m which, when added to the diameter of the hub, gives a total diameter of 90m and a swept area of 6362m2. The turbine blades are bolted to a hub at the low speed end of a 1:120 ratio gear box. Enclosure #2, G90-2.0MW, contains a picture of the G90 with a summary of the technical data. -
Introduction to Airborne Wind Energy
Introduction to Airborne Wind Energy March 2020 Udo Zillmann Kristian Petrick Stefanie Thoms www.airbornewindeurope.org 1 § Introduction to Airborne Wind Energy Agenda § Airborne Wind Energy – principle and concepts § Advantages § Challenges § Airborne Wind Europe § Meeting with DG RTD www.airbornewindeurope.org 2 § AWE principle and concepts Overview § Principles § Ground generation § On-board generation § Different types § Soft wing § Rigid wing § Semi-rigid wing § Other forms www.airbornewindeurope.org 3 § AWE principle Ground generation (“ground gen”) or yo-yo principle Kite flies out in a spiral and creates a tractive pull force to the tether, the winch generates electricity as it is being reeled out. Kite Tether Winch Tether is retracted back as kite flies directly back to the starting point. Return phase consumes a few % of Generator power generated, requires < 10 % of total cycle time. www.airbornewindeurope.org 4 § AWE principle On-board generation (“fly-gen”) Kite flies constantly cross-wind, power is produced in the on-board generators and evacuated through the tether www.airbornewindeurope.org 5 § AWE principle The general idea: Emulating the movement of a blade tip but at higher altitudes Source: Erc Highwind https://www.youtube.com/watch?v=1UmN3MiR65E Makani www.airbornewindeurope.org 6 § AWE principle Fundamental idea of AWE systems • With a conventional wind turbine, the outer 20 % of the blades (the fastest moving part) generates about 60% of the power • AWE is the logical step to use only a fast flying device that emulates the blade tip. www.airbornewindeurope.org 7 § AWE concepts Concepts of our members – soft, semi-rigid and rigid wings www.airbornewindeurope.org 8 § AWE Concept Overview of technological concepts Aerostatic concepts are not in scope of this presentation Source: Ecorys 2018 www.airbornewindeurope.org 9 § AWE Concept Rigid kite with Vertical Take Off and Landing (VTOL) 1. -
IEA Wind Technology Collaboration Programme
IEA Wind Technology Collaboration Programme 2017 Annual Report A MESSAGE FROM THE CHAIR Wind energy continued its strong forward momentum during the past term, with many countries setting records in cost reduction, deployment, and grid integration. In 2017, new records were set for hourly, daily, and annual wind–generated electricity, as well as share of energy from wind. For example, Portugal covered 110% of national consumption with wind-generated electricity during three hours while China’s wind energy production increased 26% to 305.7 TWh. In Denmark, wind achieved a 43% share of the energy mix—the largest share of any IEA Wind TCP member countries. From 2010-2017, land-based wind energy auction prices dropped an average of 25%, and levelized cost of energy (LCOE) fell by 21%. In fact, the average, globally-weighted LCOE for land-based wind was 60 USD/ MWh in 2017, second only to hydropower among renewable generation sources. As a result, new countries are adopting wind energy. Offshore wind energy costs have also significantly decreased during the last few years. In Germany and the Netherlands, offshore bids were awarded at a zero premium, while a Contract for Differences auction round in the United Kingdom included two offshore wind farms with record strike prices as low as 76 USD/MWh. On top of the previous achievements, repowering and life extension of wind farms are creating new opportunities in mature markets. However, other challenges still need to be addressed. Wind energy continues to suffer from long permitting procedures, which may hinder deployment in many countries. The rate of wind energy deployment is also uncertain after 2020 due to lack of policies; for example, only eight out of the 28 EU member states have wind power policies in place beyond 2020. -
U.S. Offshore Wind Manufacturing and Supply Chain Development
U.S. Offshore Wind Manufacturing and Supply Chain Development Prepared for: U.S. Department of Energy Navigant Consulting, Inc. 77 Bedford Street Suite 400 Burlington, MA 01803-5154 781.270.8314 www.navigant.com February 22, 2013 U.S. Offshore Wind Manufacturing and Supply Chain Development Document Number DE-EE0005364 Prepared for: U.S. Department of Energy Michael Hahn Cash Fitzpatrick Gary Norton Prepared by: Navigant Consulting, Inc. Bruce Hamilton, Principal Investigator Lindsay Battenberg Mark Bielecki Charlie Bloch Terese Decker Lisa Frantzis Aris Karcanias Birger Madsen Jay Paidipati Andy Wickless Feng Zhao Navigant Consortium member organizations Key Contributors American Wind Energy Association Jeff Anthony and Chris Long Great Lakes Wind Collaborative John Hummer and Victoria Pebbles Green Giraffe Energy Bankers Marie DeGraaf, Jérôme Guillet, and Niels Jongste National Renewable Energy Laboratory David Keyser and Eric Lantz Ocean & Coastal Consultants (a COWI company) Brent D. Cooper, P.E., Joe Marrone, P.E., and Stanley M. White, P.E., D.PE, D.CE Tetra Tech EC, Inc. Michael D. Ernst, Esq. Notice and Disclaimer This report was prepared by Navigant Consulting, Inc. for the use of the U.S. Department of Energy – who supported this effort under Award Number DE-EE0005364. The work presented in this report represents our best efforts and judgments based on the information available at the time this report was prepared. Navigant Consulting, Inc. is not responsible for the reader’s use of, or reliance upon, the report, nor any decisions based on the report. NAVIGANT CONSULTING, INC. MAKES NO REPRESENTATIONS OR WARRANTIES, EXPRESSED OR IMPLIED. Readers of the report are advised that they assume all liabilities incurred by them, or third parties, as a result of their reliance on the report, or the data, information, findings and opinions contained in the report. -
Pdf (Accessed 14 Sept
View metadata, citation and similar papers at core.ac.uk brought to you by CORE provided by SOAS Research Online Zhou, X., Li, X., Lema, R., Urban, F., 2015. Comparing the knowledge bases of wind turbine firms in Asia and Europe: patent trajectories, networks, and globalization. Science and Public Policy, 1-16. doi: 10.1093/scipol/scv055 Comparing the knowledge bases of wind turbine firms in Asia and Europe: patent trajectories, networks, and globalisation Yuan Zhou1, Xin Li2, Rasmus Lema3, Frauke Urban4 1 School of Public Policy and Management, Tsinghua University, Beijing, China 2 School of Economics and Management, Beijing University of Technology, China 3 Department of Business and Management, Aalborg University, Denmark 4 School of Oriental and African Studies SOAS, University of London, UK Abstract This study uses patent analyses to compare the knowledge bases of leading wind turbine firms in Asia and Europe. It concentrates on the following aspects: (a) the trajectories of key technologies, (b) external knowledge networks, and (c) the globalisation of knowledge application. Our analyses suggest that the knowledge bases differ significantly between leading wind turbine firms in Europe and Asia. Europe’s leading firms have broader and deeper knowledge bases than their Asian counterparts. In contrast, Chinese lead firms, with their unidirectional knowledge networks, are highly domestic in orientation with respect to the application of new knowledge. The Indian lead firm Suzlon, however, exhibits a better knowledge position. While our quantitative analyses validate prior qualitative studies it also brings new insights. The study suggests that European firms are still leaders in this industry, and Asian lead firms are unlikely to create new pathways that will disrupt incumbents in the near future. -
Profit Effective Management of Renewable Energy
APPLICATION NOTE Renewable energy is gaining increased Among the parameters which considerably popularity and interest, expressed both in affect and reduce profitability and revenue are: government financing and in investments from 1. Inferior power quality introduced by the the private sector. Of the incentives driving this grid/utility (e.g. harmonics) interest, one emerges from financial needs, 2. Erroneous utility readings influenced by today's unstable prices of fossil 3. Failure of equipment fuel. This drives the public and private sectors 4. Failure to utilize systems at maximum in search of alternative, reliable and affordable capacity energy sources. The other being environmental With over 30 years' experience in power awareness, which slowly but surely has engineering in the different fields of energy become a cause for successful lobbying in metering and power quality SATEC has risen to government, politics and finance. the challenge of designing tailor-made Two of the prominent methods for generation solutions for renewable energy applications. of electricity in methods referred to as Implementing its advanced power meters and renewable energy are solar power and wind power quality analyzers, SATEC is a supplier of energy, harvested by wind turbines. solutions for renewable energy projects such The design of such systems, which are as the Siemens GAMESA (Spain) wind turbines ultimately geared towards the income made and the Sinovel (China) wind turbines and for off the energy generated and sold, often the Perovo solar park (the Ukraine), EDF neglects, or overlooks, important aspects (Electricity de France), IEC (Israel Electric which help determine the ROI and, more Corporation) and Suzlon. -
Power Limit for Crosswind Kite Systems
Preprints (www.preprints.org) | NOT PEER-REVIEWED | Posted: 5 February 2018 doi:10.20944/preprints201802.0035.v1 Power Limit for Crosswind Kite Systems Mojtaba Kheiri1,2, Frédéric Bourgault1, Vahid Saberi Nasrabad1 1New Leaf Management Ltd., Vancouver, British Columbia, Canada 2 Concordia University, Department of Mechanical, Industrial and Aerospace Engineering, Montréal, Québec, Canada ABSTRACT static kite which only harvests from a region of the sky corresponding to its projected cross-section (and/or the rotor area of the turbine(s) it This paper generalizes the actuator disc theory to the application of carries). crosswind kite power systems. For simplicity, it is assumed that the kite sweeps an annulus in the air, perpendicular to the wind direction (i.e. Simplistically, a crosswind system parallels a horizontal axis wind straight downwind configuration with tether parallel to the wind). It is turbine (HAWT), where the kite traces a similar trajectory as the further assumed that the wind flow has a uniform distribution. turbine blade tip (see Fig.1)1. For a HAWT, approximately half the Expressions for power harvested by the kite is obtained, where the power is generated by the last one third of the blade (Bazilevs, et al., effect of the kite on slowing down the wind (i.e. the induction factor) is 2011). To capture the same wind power, a kite does not require taken into account. It is shown that although the induction factor may HAWT's massive hub and nacelle, steel tower and reinforced concrete be small for a crosswind kite (of the order of a few percentage points), foundation.