A Holistic Approach on the Simulation of Rotary-Friction-Welding
Total Page:16
File Type:pdf, Size:1020Kb
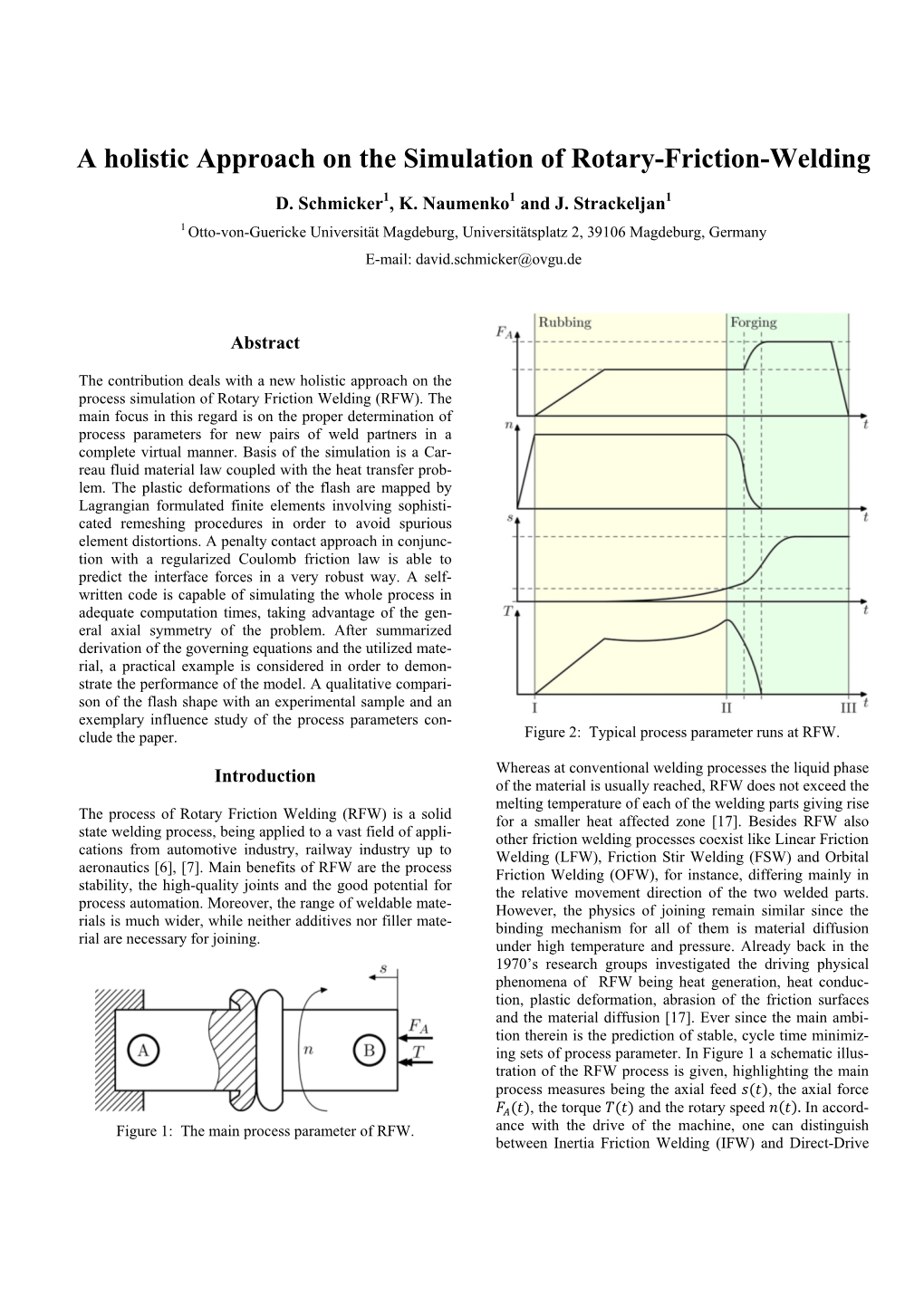
Load more
Recommended publications
-
MTI Friction Welding Technology Brochure
Friction Welding Manufacturing Technology, Inc. All of us at MTI… would like to extend our thanks for your interest in our company. Manufacturing Technology, Inc. has been a leading manufacturer of inertia, direct drive and hybrid friction welders since 1976. We hope that the following pages will further spark your interest by detailing a number of our products, services and capabilities. We at MTI share a common goal…to help you solve your manufacturing problems in the most Table of Contents efficient way possible. Combining friction welding Introduction to Friction Welding 2 with custom designed automation, we have Advantages of MTI’s Process 3 demonstrated dramatic savings in labor and Inertia Friction Welding 4 material with no sacrifice to quality. Contact us Direct Drive & Hybrid Friction Welding 5 today to find out what we can do for you. Machine Monitors & Controllers 6 Safety Features 7 Flash Removal 7 MTI Welding Services 8 Weldable Combinations 9 Applications Aircraft/Aerospace 10 Oil Field Pieces 14 Military 16 Bimetallic & Special 20 Agricultural & Trucking 22 Automotive 28 General 38 Special Welders & Automated Machines 46 Machine Models & Capabilities 48 Friction Welding 4 What It Is Friction welding is a solid-state joining process that produces coalescence in materials, using the heat developed between surfaces through a combination of mechanically induced rubbing motion and Information applied load. The resulting joint is of forged quality. Under normal conditions, the faying surfaces do not melt. Filler metal, flux and shielding gas are not required with this process. Dissimilar Materials Even metal combinations not normally considered compatible can be joined by friction welding, such as aluminum to steel, copper to aluminum, titanium to copper and nickel alloys to steel. -
The Influence of Rotational Speed and Pressure on the Properties of Rotary Friction Welded Titanium Alloy (Ti‐6Al‐4V)
View metadata, citation and similar papers at core.ac.uk brought to you by CORE provided by University of Johannesburg Institutional Repository The influence of rotational speed and pressure on the properties of rotary friction welded Titanium alloy (Ti‐6Al‐4V) MC Zulua and PM Mashininib aUniversity of Johannesburg, Depertment of Mechanical and Industrial Engineering Technology, Doornfontein campus, Johannesburg, 2028, South Africa bUniversity of Johannesburg, Depertment of Mechanical and Industrial Engineering Technology, Doornfontein campus, Johannesburg, 2028, South Africa email address : 215086813student.uj.ac.zaa, [email protected] Abstract This paper presents an investigation of rotary friction welding of 25.4 mm diameter Ti‐6Al‐4V rods. The weld process parameters used for this research were rotational speed, axial pressure and forging time. Only relative speed and axial pressure were the varied parameters while the forging time was kept constant. The mechanical properties of the weld joints were analysed and characterized. The results showed that the rotational speed and friction pressure have significant influence on the tensile strength, microstructure and weld integrity. As rotational speed increased heating time also increased in the weld, as a result, greater volume of material was affected by heat resulting in a wider width of the weld joint. Fine microstructure resulted due to an increased rotational speed and frictional pressure respectively. The oxidation and discolouration of welds were also discussed. Keywords: Rotary friction welding; process parameters; Ti‐6Al‐4V; microstructure; mechanical properties 1. Introduction Titanium alloys are non‐ferrous materials that can be welded by diverse types of welding techniques. Most of the welding processes that have been used in the past with success in joining of Titanium alloys were limited to conventional welding methods [1]. -
Friction Stir Welding of Aluminium Alloy AA5754 to Steel DX54
Aalto University School of Engineering Department of Engineering Design and Production Hao Wang Friction Stir Welding of Aluminium Al- loy AA5754 to Steel DX54: Lap Joints with Conventional and New Solu- tion Thesis submitted as a partial fulfilment of the requirements for the degree of Master of Science in Technology. Espoo, October 27, 2015 Supervisor: Prof. Pedro Vila¸ca Advisors: Tatiana Minav Ph.D. Aalto University School of Engineering ABSTRACT OF Department of Engineering Design and Production MASTER'S THESIS Author: Hao Wang Title: Friction Stir Welding of Aluminium Alloy AA5754 to Steel DX54: Lap Joints with Conventional and New Solution Date: October 27, 2015 Pages: 100 Major: Mechanical Engineering Code: IA3027 Supervisor: Professor Pedro Vila¸ca Advisors: Tatiana Minav Ph.D. The demand for joining of aluminum to steel is increasing in the automotive industry. There are solutions based on Friction Stir Welding (FSW) implemented to join these two dissimilar metals but these have not yet resulted in a reliable joint for the automotive industrial applications. The main reason is the brittle intermetallic compounds (IMCs) that are prone to form in the weld region. The objective of this thesis was to develop and test an innovative overlap joint concept, which may improve the quality of the FSW between aluminum alloy AA5754-H22 (2 mm) and steel DX54 (1.5 mm) for automotive applications. The innovative overlap joint concept consists of an interface with a wave shape produced on the steel side. The protrusion part of the shape will be directly processed by the tip of the probe with the intention of improving the mechanical resistance of the joint due to localized heat generation, extensive chemically active surfaces and extra mechanical interlocking. -
In-Situ Measurement and Numerical Simulation of Linear
IN-SITU MEASUREMENT AND NUMERICAL SIMULATION OF LINEAR FRICTION WELDING OF Ti-6Al-4V Dissertation Presented in Partial Fulfillment of the Requirements for the Degree Doctor of Philosophy in the Graduate School of The Ohio State University By Kaiwen Zhang Graduate Program in Welding Engineering The Ohio State University 2020 Dissertation Committee Dr. Wei Zhang, advisor Dr. David H. Phillips Dr. Avraham Benatar Dr. Vadim Utkin Copyrighted by Kaiwen Zhang 2020 1 Abstract Traditional fusion welding of advanced structural alloys typically involves several concerns associated with melting and solidification. For example, defects from molten metal solidification may act as crack initiation sites. Segregation of alloying elements during solidification may change weld metal’s local chemistry, making it prone to corrosion. Moreover, the high heat input required to generate the molten weld pool can introduce distortion on cooling. Linear friction welding (LFW) is a solid-state joining process which can produce high-integrity welds between either similar or dissimilar materials, while eliminating solidification defects and reducing distortion. Currently the linear friction welding process is most widely used in the aerospace industry for the fabrication of integrated compressor blades to disks (BLISKs) made of titanium alloys. In addition, there is an interest in applying LFW to manufacture low-cost titanium alloy hardware in other applications. In particular, LFW has been shown capable of producing net-shape titanium pre-forms, which could lead to significant cost reduction in machining and raw material usage. Applications of LFW beyond manufacturing of BLISKs are still limited as developing and quantifying robust processing parameters for high-quality joints can be costly and time consuming. -
Rotational Friction Welding Flyer
ROTATIONAL FRICTION WELDING MANUFACTURINGMANUFACTURING TECHNOLOGY,TECHNOLOGY, INC MTI is a world leader in designing and manufacturing friction welders, and offers a full line of all three TOP TEN ADVANTAGES: main types of Rotational Friction Welding machines — . 1 The machine-controlled process Inertia, Direct Drive, and Hybrid. eliminates human error—weld quality is independent of operator skill. 2 Dissimilar metals can be joined— even some considered incompatible WHAT IS ROTATIONAL FRICTION WELDING? or unweldable. Rotational Friction Welding is a solid-state joining process that produces coalescence . 3 Consumables are not required— in metals, or non-metals using the heat developed between two surfaces by a no flux, filler material, or shielding combination of mechanically-induced rotational rubbing motion and applied load. gases are needed. Under normal conditions, the fraying surfaces do not melt. 4 Only creates a narrow heat-affected zone, which results in more uniform There are three basic types of Rotational Friction Welding: Inertia Welding, Direct properties throughout the part, higher joint efficiencies, and stronger welds. Drive Welding, and Hybrid. Other variations include: Radial, Orbital, Linear or Reciprocating Welding and Friction Stir Welding. 5 The 100% bond of the contact area creates joints of forged quality. WHY ROTATIONAL FRICTION WELDING? . 6 Reduces raw material and machining costs when replacing forgings. Rotational Friction Welding does not compromise the integrity of the parent materials during welding – resulting in stronger welds, more uniform part properties, and . 7 Environmentally friendly, producing higher joint efficiencies. Even materials and geometries deemed unweldable are able to no smoke, fumes, or slag. be joined using Rotational Friction Welding. -
Study on the Effect of Energy-Input on the Joint Mechanical Properties of Rotary Friction-Welding
metals Article Study on the Effect of Energy-Input on the Joint Mechanical Properties of Rotary Friction-Welding Guilong Wang 1,2, Jinglong Li 1, Weilong Wang 1, Jiangtao Xiong 1 and Fusheng Zhang 1,* 1 Shaanxi Key Laboratory of Friction Welding Technologies, Northwestern Polytechnical University, Xi’an 710072, China; [email protected] (G.W.); [email protected] (J.L.); [email protected] (W.W.); [email protected] (J.X.) 2 State Key Laboratory of Solidification Processing, Northwestern Polytechnical University, Xi’an 710072, China * Correspondence: [email protected]; Tel.: +86-029-8849-1426 Received: 17 October 2018; Accepted: 3 November 2018; Published: 6 November 2018 Abstract: The objective of the present study is to investigate the effect of energy-input on the mechanical properties of a 304 stainless-steel joint welded by continuous-drive rotary friction-welding (RFW). RFW experiments were conducted over a wide range of welding parameters (welding pressure: 25–200 MPa, rotation speed: 500–2300 rpm, welding time: 4–20 s, and forging pressure: 100–200 MPa). The results show that the energy-input has a significant effect on the tensile strength of RFW joints. With the increase of energy-input, the tensile strength rapidly increases until reaching the maximum value and then slightly decreases. An empirical model for energy-input was established based on RFW experiments that cover a wide range of welding parameters. The accuracy of the model was verified by extra RFW experiments. In addition, the model for optimal energy-input of different forging pressures was obtained. To verify the accuracy of the model, the optimal energy-input of a 170 MPa forging pressure was calculated. -
The Use of Friction Welding for Corrosion Control in the Offshore Oil and Gas Industry Proserv UK To: Icorr, Aberdeen Branch 27.01.2015
The Use of Friction Welding for Corrosion Control in the Offshore Oil and Gas Industry Proserv UK To: Icorr, Aberdeen Branch 27.01.2015 Dave Gibson - Technical Authority, Friction Welding [email protected] Our Evolution What We Do: Life of Field Services Business Division What We Offer Solutions & Services • BOP Services Drilling Control Products and services • Drilling Control Systems Assurance & Performance Systems (DCS) focussed on operational • After-market & Lifecycle Management assurance Production Equipment Products and services • Flow Assurance & Sampling Solutions Systems (PES) focussed on production • Production Control & Safety Solutions optimisation • Asset Performance & Operational Integrity Products, services and • Subsea Marginal Field Development Subsea Production system design focused on • Subsea Brownfield Extension, Upgrade & Optimisation Systems (SPS) production enhancement • Obsolescence Management • Subsea Life of Field Services & Support • Subsea Infrastructure, Repair & Maintenance Products and services • Emergency Pipeline Repair Marine Technology focused on intervention and • Diverless Intervention Services (MTS) remediation to assure asset • Wellhead Abandonment & Decommissioning integrity • Friction Welding Summary 1. Why use Friction Welding Chosen for Corrosion Control ? 2. The Portable Friction Welding Process 3. Fatigue Strength of Friction Welds 4. Subsea Friction Welding Tooling 5. Subsea applications of Friction Welding for Cathodic Protection 6. Topside friction welding tooling 7. Topside applications of Friction welding for corrosion control 8. Corrosion Sensor Attachment Why is Friction Welding Chosen for Corrosion Control? Subsea • Welded, low electrical resistance, low maintenance connection • Suitable for large flat surfaces where clamps can’t be used (e.g. FPSO hulls, large diameter jacket legs and wind farm piles) • Better fatigue strength than arc welds in the “as welded” condition • When used with an ROV lower vessel costs and rapid installation. -
MSL Engineering Limited Platinum Blue House 1St Floor, 18 the Avenue Egham, Surrey, TW20 9AB
SMR Final Report 121404 Purpose of Issue Rev Date of Issue Author Agreed Approved Issued for information 0 Aug 2004 SM Issued for internal comment 1 November 2004 AFD DJM JB Issued as Final Report 2 December 2004 AFD DJM JB This Final report has been reviewed and approved by the Mineral Management Service. Approval does not signify that the contents necessarily reflect the views and policies of the Service, nor does mention of trade names or commercial products constitute endorsement or recommendation for use. This study was funded by the Mineral Management Service, U.S. Department of the Interior, Washington, D.C., under Contract Number 1435-01-04-CT-35320 ASSESSMENT OF REPAIR TECHNIQUES FOR AGEING OR DAMAGED STRUCTURES Project #502 DOC REF C357R001 Rev 1 NOV 2004 MSL Engineering Limited Platinum Blue House 1st Floor, 18 The Avenue Egham, Surrey, TW20 9AB Tel: +44 (0)1784 439194 Fax: +44 (0)1784 439198 E-mail: [email protected] C357R001Rev 2, December 2004 MMS Project #502 NUMBER DETAILS OF REVISION 0 Issued for information, August 2004 1 Issued for comment, November 2004. Extensive revisions throughout, including restructuring of report. 2 Issued as Final Report, December 2004. Conversion table added, Figure showing clamp details to avoid added, and general editorial revisions. C357R001Rev 2, December 2004 MMS Project #502 Assessment of Repair Techniques for Ageing or Damaged Structures By Dr. Adrian F Dier MSL Services Corporation Final Project Report: ASSESSMENT OF REPAIR TECHNIQUES FOR AGEING OR DAMAGED STRUCTURES MMS Project Number 502 November 2004 C357R001Rev 2, December 2004 i This Final report has been reviewed a nd approved by the Mineral Management Service. -
Friction Stir Processing of Aluminum Alloys
University of Kentucky UKnowledge University of Kentucky Master's Theses Graduate School 2004 FRICTION STIR PROCESSING OF ALUMINUM ALLOYS RAJESWARI R. ITHARAJU University of Kentucky, [email protected] Right click to open a feedback form in a new tab to let us know how this document benefits ou.y Recommended Citation ITHARAJU, RAJESWARI R., "FRICTION STIR PROCESSING OF ALUMINUM ALLOYS" (2004). University of Kentucky Master's Theses. 322. https://uknowledge.uky.edu/gradschool_theses/322 This Thesis is brought to you for free and open access by the Graduate School at UKnowledge. It has been accepted for inclusion in University of Kentucky Master's Theses by an authorized administrator of UKnowledge. For more information, please contact [email protected]. ABSTRACT OF THESIS FRICTION STIR PROCESSING OF ALUMINUM ALLOYS Friction stir processing (FSP) is one of the new and promising thermomechanical processing techniques that alters the microstructural and mechanical properties of the material in single pass to achieve maximum performance with low production cost in less time using a simple and inexpensive tool. Preliminary studies of different FS processed alloys report the processed zone to contain fine grained, homogeneous and equiaxed microstructure. Several studies have been conducted to optimize the process and relate various process parameters like rotational and translational speeds to resulting microstructure. But there is only a little data reported on the effect of the process parameters on the forces generated during processing, and the resulting microstructure of aluminum alloys especially AA5052 which is a potential superplastic alloy. In the present work, sheets of aluminum alloys were friction stir processed under various combinations of rotational and translational speeds. -
Effect of Speed on Hardness in Rotary Friction Welding Process
International Journal of Materials Science ISSN 0973-4589 Volume 12, Number 4 (2017), pp. 635-641 © Research India Publications http://www.ripublication.com Effect of Speed on Hardness in Rotary Friction Welding Process P. Koteswara Rao1, V. Mohan2, N.Surya3*, G. Sai Krishna Prasad4 1, 2, 3,4Assistant Professor, Department of Mechanical Engineering, TKRCET, Hyderabad, Telangana, India. Abstract Aim of this paper was to determine the hardness in rotary friction welding by varying speed. It is a solid state welding technology to join material by applying linear force to join the materials. The work was carried out on modified conventional lathe machine attached with two self chucks, one is in rotational and another one is fixed. The material diameter was used 10 & 14 mm in diameter rods of similar and dissimilar material with four combination of set (MS-MS, MS-Al, Cu-Brass, and Al-Al). It was observed that the value of hardness at HAZ is softer and harder away from the HAZ. Key Term: Lathe Machine; Rotary Friction; Speed; Hardness. INTRODUCTION Friction welding is a solid state joining technique by applying rotational speed and pressure at motion less work piece to join metal without any defect, porosity and no cracks propagation in the weld zone with fine grain structure etc due to thermo mechanical effect [1]. It has wide number of application such as automobile, aerospace, nuclear, electrical, chemical, cryogenic and marine etc [2]. The advantages like no material waste, production time is less and low energy expenditure in it [3]. The factor affecting the weld includes various rotational speeds, frictional load and weld duration [4]. -
Rotary Friction Welding of Inconel 718 to Inconel 600
metals Article Rotary Friction Welding of Inconel 718 to Inconel 600 Ateekh Ur Rehman * , Yusuf Usmani, Ali M. Al-Samhan and Saqib Anwar Department of Industrial Engineering, College of Engineering, King Saud University, Riyadh 11451, Saudi Arabia; [email protected] (Y.U.); [email protected] (A.M.A.-S.); [email protected] (S.A.) * Correspondence: [email protected]; Tel.: +966-1-1469-7177 Abstract: Nickel-based superalloys exhibit excellent high temperature strength, high temperature corrosion and oxidation resistance and creep resistance. They are widely used in high temperature applications in aerospace, power and petrochemical industries. The need for economical and efficient usage of materials often necessitates the joining of dissimilar metals. In this study, dissimilar welding between two different nickel-based superalloys, Inconel 718 and Inconel 600, was attempted using rotary friction welding. Sound metallurgical joints were produced without any unwanted Laves or delta phases at the weld region, which invariably appear in fusion welds. The weld thermal cycle was found to result in significant grain coarsening in the heat effected zone (HAZ) on either side of the dissimilar weld interface due to the prevailing thermal cycles during the welding. However, fine equiaxed grains were observed at the weld interface due to dynamic recrystallization caused by severe plastic deformation at high temperatures. In room temperature tensile tests, the joints were found to fail in the HAZ of Inconel 718 exhibiting good ultimate tensile strength (759 MPa) without a significant loss of tensile ductility (21%). A scanning electron microscopic examination of the fracture surfaces revealed fine dimpled rupture features, suggesting a fracture in a ductile mode. -
Manufacturing Services a Single-Source
MANUFACTURING SERVICES MTI offers an affordable, single-source turnkey solution to accommodate your applications by developing and producing your parts to save MTIwelding.com you time, money, and mitigate risk to your parts program. A SINGLE-SOURCE TURNKEY SOLUTION As one of the world’s largest, most experienced friction welding machine builders and integrators, MTI is positioned to be your single source turnkey solution to any Contract Friction Welding need. By providing you access to an array of in-house value-added services to accommodate your applications, we have the ability to process your parts using the latest in friction welding and part handling technology. We also maintain the widest range of friction welding equipment available. Only MTI offers all three types of rotary friction welding. With over 117,000 square feet of production space, we can produce friction-welded parts ranging anywhere in size. From small military aircraft rivets to 55-foot-long Friction Stir Welds, MTI is uniquely qualified to handle all your contract welding needs with the quality you expect. Take advantage of our in-house value-added services including custom design engineering, research and development resources, and pre- and post-weld processing. TECHNOLOGIES As the world leader in the design, manufacture and installation of Friction Welding machines, MTI is able to offer world-class Friction Welding contract services that include: Rotary Friction Linear Friction Friction Stir Plug Welding Welding Welding Welding QUALITY ASSURANCE We calibrate and maintain our machines to keep them at optimum performance so that your last welded part is of the same high quality as your first.