The Celtic Knot in Woodworking
Total Page:16
File Type:pdf, Size:1020Kb
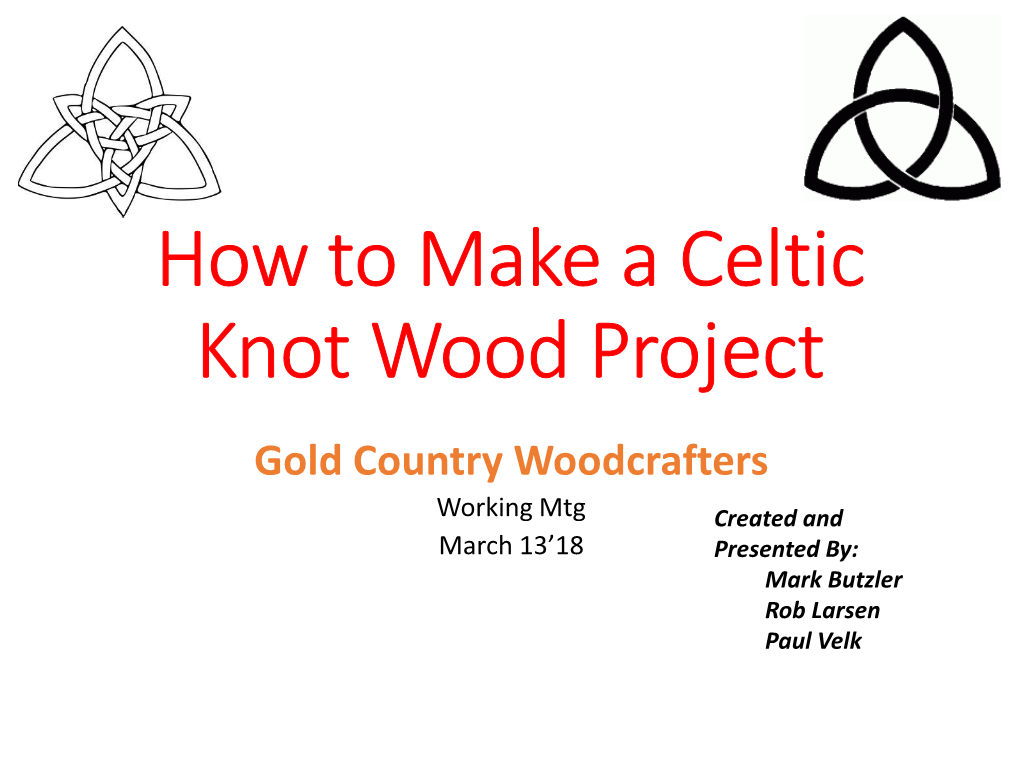
Load more
Recommended publications
-
The Caledonii Grande Tradition Greetings from the Editorial Staff
amildanachamildanach Journal of Celtic Studies ◊ Caledonii Grande Tradition SS http://www.angelfire.com/sc/Caledonii/ Premiere Edition ◊ Five dollars Greetings from the Editorial Staff It has been several years since the We are striving to present articles Sabbats, Gods and Goddesses of publication of the original Samildanach of worth to those of you who wish the Celts and customs relating to was released. Now, with new to be enriched in your study of them. We invite you to submit your computers and a full Staff comprised Celtic life ways. We’ll also carry articles to our Editorial Staff at least of hard working Caledonii members, sections announcing upcoming six weeks before the release date we hope to bring you this magazine Gatherings around the South East, for each issue. Issues of the zine will of Celtic Studies. You’ll find a lot in and notable Gathers throughout number four a year to correspond this issue which we hope will be of the States; as well as, articles on the to the great Fire Festivals. interest to you. – Continued on page 2 The Caledonii Grande Tradition A Little Background Grande Tradition known as the Wiccans and Mystic Christians can Fellowship of Caledon. In its come together and affirm their By Lord Ariel Morgan meetings, the Druidh, the Elders interconnectedness as Creators Ard Druidh Chosen Chief of the Order and Third Degree, and the Episcopacy, children and as brothers and sisters Wisdom Keeper of the Tradition sit together and create the policies of the Caledonii family. Within the which govern the Caledonii. -
On the Topology of Celtic Knot Designs
On the Topology of Celtic Knot Designs Gwen Fisher Mathematics Department California Polytechnic State University San Luis Obispo, CA 93407 [email protected] Blake Mellor Mathematics Department Loyola Marymount University Los Angeles, CA 90045-2659 [email protected] Abstract We derive formulas for counting the number of strands in a variety of knotwork designs inspired by traditional Celtic designs, including rectangular panels, circular borders, rectangular borders, and half frames. We include graphic examples for each of these types of designs. 1. Introduction There is a long tradition of abstract geometric designs in the art of the Celtic peoples of ancient Britain, Scotland and Ireland, including spirals, key patterns and, in the Christian era, knots and interlacings [1]. Complex knotwork patterns were used profusely in the Celtic illuminated manuscripts, such as in the Books of Durrow (early 5th to early 6th century), Kells (middle 6th to early 8th century), Lindesfarne (late 7th century), and Grimbald of St. Bertin (early 11th century). In these manuscripts, interlacing designs (both purely geometric, as in Figure 1, and incorporating animal figures) fill areas and are used as borders for text and illustrations. Françoise Henry called these designs a “sacred riddle” [7], and their symbolic meaning is a fascinating and unresolved issue in Celtic art history. James Trilling [10] has theorized that knotwork designs were, like the crosses that they commonly accompanied, protections against evil: the complex designs would trap and confuse the “evil eye”. Figure 1: A knotwork design, from [5] Whatever their meaning, the complexity of Celtic knotwork designs is evidence of substantial mathematical sophistication [4], and their design and analysis lead to many mathematical questions. -
General Introduction the Evergreen: a Northern Seasonal (1895- 1896/97)
GENERAL INTRODUCTION THE EVERGREEN: A NORTHERN SEASONAL (1895- 1896/97) “Four seasons fill the measure of the year; There are four seasons in the mind of man.” Epigraph to The Evergreen, from John Keats’s “The Human Seasons” Evergreen flyleaf ornament. Published as a semi-annual by Patrick Geddes & Colleagues in the Lawnmarket of Edinburgh and by T. Fisher Unwin in London, The Evergreen: A Northern Seasonal was produced out of interlacing connections as complex as those of the Celtic knot work it showcased. These include arts and crafts, Scottish Renascence, Pan-Celticism, and an urban renewal enhanced with what we would today call an ecological concern with nature and green space in the modern world. With local roots and international aspirations, The Evergreen sought to express a message of social regeneration by uniting art and science in the architecture of the page and the built environment. Expressed in Geddes’s triad of “sympathy, synergy, and synthesis,” this vision was embodied in the emblem of three flying black birds, each carrying a leaf in its beak, which decorated the openings of The Evergreen’s four volumes (Burbridge 73). As Regina Hewitt observes, Geddes conceptualized The Evergreen “as a resource for—and 1 perhaps even a manifesto of—cultural evolution” (“Patrick Geddes”). Although The Evergreen’s print run lasted less than two years, this innovative, interdisciplinary magazine had far-reaching impact. In his review for Pall Mall Magazine, Israel Zangwill highlighted the importance of the local and the social to this illustrated periodical. “’Till I went to Edinburgh,” he wrote, “I did not know what the ‘Evergreen’ was. -
Celtic Patterns to Colour Pdf, Epub, Ebook
CELTIC PATTERNS TO COLOUR PDF, EPUB, EBOOK Struan Reid,David Thelwell | 32 pages | 01 Jul 2014 | Usborne Publishing Ltd | 9781409574651 | English | London, United Kingdom Celtic Patterns to Colour PDF Book You can learn more about how we plus approved third parties use cookies and how to change your settings by visiting the Cookies notice. There were Celts through most of Europe and even Asia, so these coloring sheets are Celtic favorites all over! Celtic Dogs Design. Knotted Celtic Art Design. Celtic Dublin. Triquetra Knot. Celtic Art Coloring Pages to Print. Cross Shape. Print all of our Celtic Coloring pages for free. Follow the lines. Patrick Celtic Coloring. Coloring pages. It can seem like a tangled maze, so some pre-thinking is in order for many of these coloring pages! Quad Celtic Knot. Copyright Disclaimer Disclosure Privacy Terms. Christmas Patterns to Colour Emily Bone. Also, get your favorite crayons, coloring pencils, and watercolors ready for my relaxing adult coloring pages! Trinity Celtic Triangle. Round Pattern. Accept all Manage Cookies. Celtic Heraldry. That's why there were so many intertwined animals, knots, vines, leaves and other decorations behind the main artwork. Celtic Knot Pattern. Swan Celtic Animals. Easy Celtic Bird. Designs are taken from stone carvings, pottery and jewellery and include the intricate knotwork patterns for which the Celts were famous. Vine Motif. Celtic Style Shamrock. Abigail Wheatley. Printable Celtic Symbol Coloring Pages. Beautiful Celtic Coloring Pages. Celtic Owl Design. Small Celtic Knots. They shared common languages, religious beliefs, traditions and of course artwork. Celtic Leaves. Celtic Triquetra Circle Interlaced. Dispatched from the UK in 1 business day When will my order arrive? Celtic Design. -
Thesis&Preparation&Appr
THESIS&PREPARATION&APPROVAL&FORM& & Title&of&Thesis:& Scottish&Fiddling&in&the&United&States:&Reviving&a&Tradition&and&Maintaining&a&Community& & & I. To&be&completed&by&the&Student:& & I&certify&that&this&document&meets&the&preparation&guidelines&as&presented&in&the& Style&Guide&and&Instructions&for&Preparing&Theses&and&Dissertations.&& & & _________________________________& &_______________& (Signature&of&Student)&& & (Date)& & & II. To&be&completed&by&thesis&advisor:& & I&certify&that&this&document&is&suitable&for&submission.& & & _________________________________&& _______________& (Signature&of&Advisor)&& & (Date)& & III. To&be&completed&by&School&Director:& & I&certify,&to&the&best&of&my&knowledge,&that&the&required&procedures&have&been& followed&and&the&preparation&criteria&have&been&met&for&this&thesis/dissertation.&& & & _________________________________& &_______________& (Signature&of&Director)&& & (Date)& & & xc:&Graduate&Coordinator& SCOTTISH FIDDLING IN THE UNITED STATES: REVIVING A TRADITION AND MAINTAINING A COMMUNITY A thesis submitted to the College of the Arts of Kent State University in partial fulfillment of the requirements for the degree of Master of Arts By Deanna T. Nebel May, 2015 Thesis written by Deanna T. Nebel B.M., Westminster College, 2013 M.A., Kent State University, 2015 Approved by ____________________________________________________ Jennifer Johnstone, Ph.D., Advisor ____________________________________________________ Ralph Lorenz, Ph.D., Acting Director, School of Music ____________________________________________________ -
Icons of the Iron Age: the Celts in History and Archaeology Course Guide
ICONS OF THE IRON AGE: THE CELTS IN HISTORY AND ARCHAEOLOGY COURSE GUIDE Professor Susan A. Johnston GEORGE WASHINGTON UNIVERSITY Icons of the Iron Age: The Celts in History and Archaeology Professor Susan A. Johnston George Washington University Recorded Books™ is a trademark of Recorded Books, LLC. All rights reserved. Icons of the Iron Age: The Celts in History and Archaeology Professor Susan A. Johnston Executive Producer John J. Alexander Executive Editor Donna F. Carnahan RECORDING Producer - David Markowitz Director - Matthew Cavnar COURSE GUIDE Editor - James Gallagher Design - Edward White Lecture content ©2008 by Susan A. Johnston Course guide ©2008 by Recorded Books, LLC 72008 by Recorded Books, LLC Cover image: Celtic knot design on a stone cross, Ballyroebuck, Ireland © Tom O’Brien/shutterstock.com #UT129 ISBN: 978-1-4361-5001-9 All beliefs and opinions expressed in this audio/video program and accompanying course guide are those of the author and not of Recorded Books, LLC, or its employees. Course Syllabus Icons of the Iron Age: The Celts in History and Archaeology About Your Professor...................................................................................................4 Introduction...................................................................................................................5 Lecture 1 The Creation of the Celts ......................................................................6 Lecture 2 The Documentary Sources..................................................................10 Lecture -
Celebrating the Celtic Imagination Midsummer 2008
Celebrating the Celtic Imagination Midsummer 2008 52 NEW Items! welcome to gaelsong Midsummer 2008 Midsummer night has always been a night for love magic…as the heat of the sun gives way to the cool of the evening, lovers meet in the enchanted air and make merry in song and dance all the night long. It is a time to envision the future and revel in the present. A walk through the dew on midsummer morn brings Colleen Connell, magical rewards, as we delight in the beauty of Founder the new day. At GaelSong, we hope to add beauty and magic to your life. We present beautiful gifts in the Celtic style, made all over the world. Many items we offer are hand-crafted by artisans devoted actual size to keeping traditional Celtic handiwork and design alive. Whether you seek wisdom by reflecting on the past or seek beauty and inspiration in the present, we hope our products will warm and enchant you. NEW! TRINITY KN O T BLOSSOM FAIRY HOUSES … A trinity knot and sparkling gem form an ever-flowering EV E RY W H ERE ! silver blossom on a delicate tendril of silver vine. Discover a world of Framed in sunny 14k gold or moonlight Sterling silver. whimsical habitats constructed from J1037 Trinity Knot Blossom Earrings, sterling $48 natural materials. J2055 Trinity Knot Blossom Pendant, sterling $48 Building diminutive J1042 Trinity Knot Blossom Earrings, houses from found 14k gold and sterling $248 materials (twigs, J2056 Trinity Knot Blossom Pendant, shells, pinecones and 14k gold and sterling $248 such) is a delightful pastime—and a sweet way to invite FLOWER FAIRIES the fairies. -
Who Were the Celts?
Who Were the Celts? The Celts were groups of people who lived in Europe during the Iron Age (800 BC-AD). The Iron Age was the period of time when iron replaced bronze in the making of tools and weapons. It was discovered that iron could be produced from iron ore in a process called smelting. Iron was harder than bronze so made better objects. Who Were the Celts? There were three main Celtic groups; the Gauls (in Northern mainland Europe), the Britons (in England) and the Gaels (in Ireland). Iron Age Celts lived in Britain and Ireland from 750 BC. Celts lived in tribes, each with their own king or queen. Celtic tribes, in what is now Britain, included the Iceni, the Cornovii and the Ordovices. The Celts ruled Britain until the Romans invaded in AD 43. Celtic Art Because the Celtic people lived all over Europe, Celtic art is varied. Some of it came in the form of stone carvings, jewellery, pottery, tools and other objects. “The Guard” by Patrimonio Nacional Galegois licensed under CC BY 2.0 “Image from page 379 of "The arts in early England" (1903)” “Celticy widdly-woo” by gajtalbot licensed under CC BY 2.0 “Glasnevin Cemetery” by William Murphy is licensed under CC BY 2.0 by Internet Archive Book Images is licensed under CC BY 2.0 How Do We Know About Celtic Art? There are only very limited records from the Celtic period so our knowledge of Celtic art comes from archaeology. This is the study of history through excavating sites and studying “Newgrange” by Sean MacEntee licensed under CC BY 2.0 artefacts and other remains. -
Lughnasadh 2013 © July 2013 No Portion of This Publication May Be Used Without the Author Or Artist’S Permission
Pooka’s Page for Grownups We listen to you! A parent and teacher wrote to me that one of things she enjoyed most about the magazine were that the Pooka stories explained the sabbats so well to her children and students. However, she was disappointed with past Lughnasadh tales. She said they were very enjoyable, but that they didn’t go far enough in explaining about the holiday. Perhaps others of you have felt the same? She had a good point and so, with this story, I’ve tried to do better. If any of you have similar concerns, or if there’s something you particularly like and want to see more of, if you have a question or idea or even just want to say “Hi”, pop over to our Pooka Pages Team Facebook page and leave a comment . (And by the way, this is the best place to stay current on Pooka Pages news including the fastest way to learn when a new issue is posted. We announce it there first!) facebook.com/PookaPagesTeam In the last issue, we began a couple of on-going projects and lessons for kids including Nathalie Dussault’s Wheel of the Year Plaque and Christine’s Rune Lessons. Beginning with this issue, Laura Cordelia will be teaching children about magical symbols. If you’re new to Pooka Pages or have missed one of these projects for some reason, they will eventually be posted on the Pooka Pages website. In the meanwhile, you can write to me at: [email protected] and I’ll e-mail them to you. -
Oak & Acorn Necklet Page 49
PRSRT STD U.S. Postage P.O. Box 15388 Seattle, WA 98115 PAID www.gaelsong.com GaelSong customer number Celebrating the Celtic Imagination Winter Solstice 2010 key code 88 NEW Items! Printed in USA on recycled paper (minimum post-consumer 10% waste); certified by Forest Stewardship Council. NEW! UNDer THe misTleToe Bring the tradition of mistletoe to your holidays! This festive ornament captures the look without ever losing leaves. Hang it on a tree, or hang it from the ceiling and wait to steal a kiss. Solid pewter; hand-enameled. 2 ½" wide. Handcrafted in USA. D92011 Mistletoe Ornament $21 actual size EXCLUSIVE! Oak & Acorn Necklet page 49 Heroic Gems In centuries past, explorers sailed the world, seeking gems and precious metals NEW! JULIET WORE VELVeT fit for royalty. Celebrate the age of heroes with this garnet and silver set. The Spend your day in a reverie of romance. Flowing empire-waist velvet Hand-patinaed bronze oak leaves uncommonly large, spectacular deep-red garnet gemstone, surrounded by tunic suggests a storied past, with look that goes anywhere. The deep silver knotwork, adds a noble touch to any ensemble. Sterling silver; pendant on color shimmers with each movement. Luxurious silk velvet drapes with hand-formed glass acorns 18" chain. beautifully—and is machine washable and dryable! Sizes XS-XXL. J13570 Heroic Earrings $40 | J20020 Heroic Pendant $76 82% rayon/18% silk. Made in USA. In Cranberry (above), Bronze, SAVE $20! Buy both for $96 Deep Teal and Black (see page 8). A60018 Velvet Juliet Tunic $96 actual size NEW! celTic santas The spirit of giving is universal, and Santa comes in many different guises. -
A Call for the Study of Irish Rhetoric
Georgia State University ScholarWorks @ Georgia State University English Theses Department of English 12-2021 A Call for the Study of Irish Rhetoric Rachel E. Woods Georgia State University Follow this and additional works at: https://scholarworks.gsu.edu/english_theses Recommended Citation Woods, Rachel E., "A Call for the Study of Irish Rhetoric." Thesis, Georgia State University, 2021. https://scholarworks.gsu.edu/english_theses/267 This Thesis is brought to you for free and open access by the Department of English at ScholarWorks @ Georgia State University. It has been accepted for inclusion in English Theses by an authorized administrator of ScholarWorks @ Georgia State University. For more information, please contact [email protected]. A Call for the Study of Irish Rhetoric by Rachel Elena Woods Under the Direction of Michael Harker, PhD A Thesis Submitted in Partial Fulfillment of the Requirements for the Degree of Master of Arts in the College of Arts and Sciences Georgia State University 2021 ABSTRACT This thesis examines the existing scholarship in Irish rhetoric and the narrative that has been built thus far. Current knowledge of Irish rhetoric examines minute periods in the literature and communication rather than a coherent overview of its rhetorical development. This thesis identifies and analyzes three periods of rhetorical significance using the stipulative characterization of Irish rhetoric being narrative based relying on recursive elements from Irish history. It then posits a new perspective and language to typify Irish rhetoric using the metaphor of a Celtic braid. Through the composition of a braid, I classify three strands of rhetoric and trace them through the identified rhetorical periods to demonstrate the continuous nature of Irish rhetoric. -
The Ordinary of the Adrian Empire from the Archiver's Office Compiled
The Ordinary of the Adrian Empire From the Archiver’s Office Compiled by Herald Griffin Haldane Updated by Dragon KoA Organized by Heraldic Charge Device [Type-Registrant-Kingdom] As of July 31, 2005 A Acorn [Fieldless] an acorn slipped and leaved Or. [B-House Solstice ALHA] [Fieldless] An acorn argent. [B-Duchy of Kildare KILD] [Fieldless] An acorn sable. [B-Duchy of Kildare KILD] [Fieldless] An acorn slipped and leaved sable. [B-Duchy of Kildare KILD] [Fieldless] An acorn slipped and leaved argent. [B-Duchy of Kildare KILD] Azure, a squirrel sejant erect argent, and on a chief sable three acorns argent. [D-Miranda Snowden TERR] Azure, on a bend sinister sable between two squirrels sejant erect contourny argent three acorns argent. [D-Miranda Snowden TERR] Or, a chevron between two acorns inverted slipped and leaved vert and a squirrel sejant erect contourny sable. [D-Nathaniel of Cedar Stream CAER] Per bend argent and vert, an oak leaf and an acorn slipped and leaved, all counterchanged. [D-James the Red, UMBR] Per bend engrailed vert and sable, a wolf’s head erased and three acorns inverted argent. [D-William Ce’Wolf, TERR] Per bend vert and azure, in bend sinister a sun and an acorn argent. [D-Kitara Kell deGour deLey, TRDF] Per chevron azure and vert, two acorns and a mushroom argent. [E-Barony of MoDuinne, YORK] Per pale gules and sable, an acorn in chief slipped and leaved of three oak leaves Or. [B-Killian Oakesblood, YORK] Sable, an acorn inverted and slipped and leaved within a bordure wavy Or.