Shear-Thinning Fluid Flow in Variable- Aperture Channels
Total Page:16
File Type:pdf, Size:1020Kb
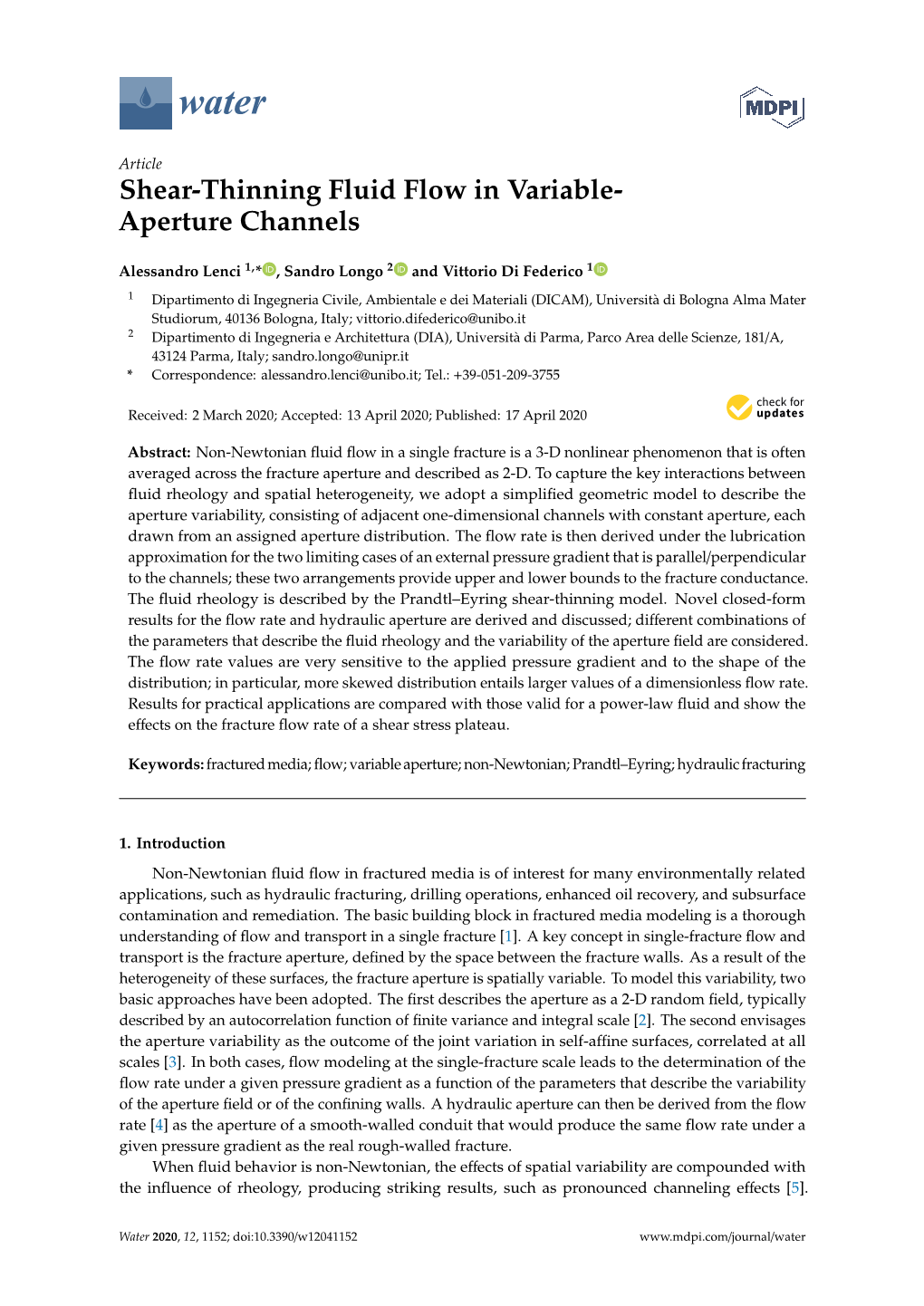
Load more
Recommended publications
-
Shear Thickening in Concentrated Suspensions: Phenomenology
Shear thickening in concentrated suspensions: phenomenology, mechanisms, and relations to jamming Eric Brown School of Natural Sciences, University of California, Merced, CA 95343 Heinrich M. Jaeger James Franck Institute, The University of Chicago, Chicago, IL 60637 (Dated: July 22, 2013) Shear thickening is a type of non-Newtonian behavior in which the stress required to shear a fluid increases faster than linearly with shear rate. Many concentrated suspensions of particles exhibit an especially dramatic version, known as Discontinuous Shear Thickening (DST), in which the stress suddenly jumps with increasing shear rate and produces solid-like behavior. The best known example of such counter-intuitive response to applied stresses occurs in mixtures of cornstarch in water. Over the last several years, this shear-induced solid-like behavior together with a variety of other unusual fluid phenomena has generated considerable interest in the physics of densely packed suspensions. In this review, we discuss the common physical properties of systems exhibiting shear thickening, and different mechanisms and models proposed to describe it. We then suggest how these mechanisms may be related and generalized, and propose a general phase diagram for shear thickening systems. We also discuss how recent work has related the physics of shear thickening to that of granular materials and jammed systems. Since DST is described by models that require only simple generic interactions between particles, we outline the broader context of other concentrated many-particle systems such as foams and emulsions, and explain why DST is restricted to the parameter regime of hard-particle suspensions. Finally, we discuss some of the outstanding problems and emerging opportunities. -
Impact of Thixotropy on Flow Patterns Induced in a Stirred Tank
CORE Metadata, citation and similar papers at core.ac.uk Provided by Open Archive Toulouse Archive Ouverte Impact of thixotropy on flow patterns induced in a stirred tank: Numerical and experimental studies G. Couerbe a, D.F. Fletcher b, C. Xuereb a, M. Poux a,∗ a Universit e´ de Toulouse, Laboratoire de G enie´ Chimique, CNRS/INP/UPS, 5 rue Paulin Talabot, BP 1301, 31106 Toulouse Cedex, France b School of Chemical and Biomolecular Engineering, The University of Sydney, NSW 2006, Australia abstract Agitation of a thixotropic shear•thinning fluid exhibiting a yield stress is investigated both experimentally and via simulations. Steady•state experiments are conducted at three 1 impeller rotation rates (1, 2 and 8 s − ) for a tank stirred with an axial•impeller and flow•field measurements are made using particle image velocimetry (PIV) measurements. Three• dimensional numerical simulations are also performed using the commercial CFD code Keywords: ANSYS CFX10.0. The viscosity of the suspension is determined experimentally and is mod• Thixotropy elled using two shear•dependant laws, one of which takes into account the flow instabilities CFD of such fluids at low shear rates. At the highest impeller speed, the flow exhibits the famil• PIV iar outward pumping action associated with axial•flow impellers. However, as the impeller Stirred tank speed decreases, a cavern is formed around the impeller, the flow generated in the vicin• Impeller ity of the agitator reorganizes and its pumping capacity vanishes. An unusual flow pattern, Mixing where the radial velocity dominates, is observed experimentally at the lowest stirring speed. It is found to result from wall slip effects. -
Non-Newtonian Fluid Math Dean Wheeler Brigham Young University May 2019
Non-Newtonian Fluid Math Dean Wheeler Brigham Young University May 2019 This document summarizes equations for computing pressure drop of a power-law fluid through a pipe. This is important to determine required pumping power for many fluids of practical importance, such as crude oil, melted plastics, and particle/liquid slurries. To simplify the analysis, I will assume the use of smooth and relatively long pipes (i.e. neglect pipe roughness and entrance effects). I further assume the reader has had exposure to principles taught in a college-level fluid mechanics course. Types of Fluids To begin, one must understand the difference between Newtonian and non-Newtonian fluids. There are many types of non-Newtonian fluids and this is a vast topic, which is studied under a branch of physics known as rheology. Rheology concerns itself with how materials (principally liquids, but also soft solids) flow under applied forces. Some non-Newtonian fluids exhibit time-dependent or viscoelastic behavior. This means their flow behavior depends on the history of what forces were applied to the fluid. Such fluids include thixotropic (shear-thinning over time) and rheopectic (shear-thickening over time) types. Viscoelastic fluids exhibit elastic or solid-like behavior when forces are first applied, and then transition to viscous flow under continuing force. These include egg whites, mucous, shampoo, and silly putty. We will not be analyzing any of these time-dependent fluids in this discussion. Time-independent or inelastic fluids flow with a constant rate when constant forces are applied to them. They are the focus of this discussion. -
Characteristics of Stratified Flows of Newtonian/Non-Newtonian Shear- Thinning Fluids
Characteristics of stratified flows of Newtonian/non-Newtonian shear- thinning fluids Davide Picchia*, Pietro Poesiob, Amos Ullmanna and Neima Braunera a Tel-Aviv University, Faculty of Engineering, School of Mechanical Engineering Ramat Aviv, Tel-Aviv, 69978, Israel b Università degli Studi di Brescia, Dipartimento di Ingegneria Meccanica ed Industriale, Via Branze 38, 25123,Brescia, Italy [email protected] , [email protected], [email protected], [email protected] Abstract Exact solutions for laminar stratified flows of Newtonian/non-Newtonian shear-thinning fluids in horizontal and inclined channels are presented. An iterative algorithm is proposed to compute the laminar solution for the general case of a Carreau non- Newtonian fluid. The exact solution is used to study the effect of the rheology of the shear-thinning liquid on two-phase flow characteristics considering both gas/liquid and liquid/liquid systems. Concurrent and counter-current inclined systems are investigated, including the mapping of multiple solution boundaries. Aspects relevant to practical applications are discussed, such as the insitu hold-up, or lubrication effects achieved by adding a less viscous phase. A characteristic of this family of systems is that, even if the liquid has a complex rheology (Carreau fluid), the two-phase stratified flow can behave like the liquid is Newtonian for a wide range of operational conditions. The capability of the two-fluid model to yield satisfactory predictions in the presence of shear-thinning liquids is tested, and an algorithm is proposed to a priori predict if the Newtonian (zero shear rate viscosity) behaviour arises for a given operational conditions in order to avoid large errors in the predictions of flow characteristics when the power-law is considered for modelling the shear-thinning behaviour. -
Magnetorheological Fluid, Apparent Viscosity, Yield Stress
American Journal of Polymer Science 2012, 2(4): 50-55 DOI: 10.5923/j.ajps.20120204.01 Magneto Mechanical Properties of Iron Based MR Fluids S. Elizabeth Premalatha1,2, R. Chokkalingam1, M. Mahendran1,* 1Smart Materials Lab, Department Physics, Thiagarajar College of Engineering, Madurai, 625015, India 2Department of Physics, Sri S. Ramasamy Naidu Memorial College, Sattur, 626203, India Abstract The main aim of this article is to prepare MR fluids, composed of iron particles and analyse their flow behaviour in terms of the internal structure, stability and magneto rheological properties. MR fluids are prepared using silicone oil (OKs) mixed with iron powder. To reduce sedimentation, grease is added as stabilizers. The size of the particles is observed by Optical microscope and flow properties are examined by rheometer. Sedimentation is measured by simple observation of changes in boundary position between clear and turbid part of MR fluid placed into glass tube. The various additive percentages can also influence the MR fluid’s performances. Keywords Magnetorheological Fluid, Apparent Viscosity, Yield Stress When the field is cut off, the MR fluid comes to original 1. Introduction state.MR fluid behave like Newton fluid in zero magnetic field. When certain amount of magnet field is applied, the Using some standard materials, science and technology magnetic particles form chain cluster due to dipole-dipole have made amazing development in the design of electronics interaction between particles[7-12]. The important and machinery. Such materials have the ability to change characteristics of the magnetically active dispersed phase are their shape or size by adding a little bit of heat or to change particle size, shape, density, particle size distribution, from the liquid to a solid when this material is near to a saturation magnetization and coercive field [13] Other than magnet. -
A Basic Introduction to Rheology
WHITEPAPER A Basic Introduction to Rheology RHEOLOGY AND Introduction VISCOSITY Rheometry refers to the experimental technique used to determine the rheological properties of materials; rheology being defined as the study of the flow and deformation of matter which describes the interrelation between force, deformation and time. The term rheology originates from the Greek words ‘rheo’ translating as ‘flow’ and ‘logia’ meaning ‘the study of’, although as from the definition above, rheology is as much about the deformation of solid-like materials as it is about the flow of liquid-like materials and in particular deals with the behavior of complex viscoelastic materials that show properties of both solids and liquids in response to force, deformation and time. There are a number of rheometric tests that can be performed on a rheometer to determine flow properties and viscoelastic properties of a material and it is often useful to deal with them separately. Hence for the first part of this introduction the focus will be on flow and viscosity and the tests that can be used to measure and describe the flow behavior of both simple and complex fluids. In the second part deformation and viscoelasticity will be discussed. Viscosity There are two basic types of flow, these being shear flow and extensional flow. In shear flow fluid components shear past one another while in extensional flow fluid component flowing away or towards from one other. The most common flow behavior and one that is most easily measured on a rotational rheometer or viscometer is shear flow and this viscosity introduction will focus on this behavior and how to measure it. -
Numerical Simulation of the Flow of a Power Law Fluid in An
View metadata, citation and similar papers at core.ac.uk brought to you by CORE provided by Texas A&M University NUMERICAL SIMULATION OF THE FLOW OF A POWER LAW FLUID IN AN ELBOW BEND A Thesis by KARTHIK KANAKAMEDALA Submitted to the Office of Graduate Studies of Texas A&M University in partial fulfillment of the requirements for the degree of MASTER OF SCIENCE December 2009 Major Subject: Mechanical Engineering NUMERICAL SIMULATION OF THE FLOW OF A POWER LAW FLUID IN AN ELBOW BEND A Thesis by KARTHIK KANAKAMEDALA Submitted to the Office of Graduate Studies of Texas A&M University in partial fulfillment of the requirements for the degree of MASTER OF SCIENCE Approved by: Chair of Committee, K. R. Rajagopal Committee Members, N. K. Anand Hamn-Ching Chen Head of Department, Dennis O‟Neal December 2009 Major Subject: Mechanical Engineering iii ABSTRACT Numerical Simulation of the Flow of a Power Law Fluid in an Elbow Bend. (December 2009) Karthik Kanakamedala, B. Tech, National Institute of Technology Karnataka Chair of Advisory Committee: Dr. K. R. Rajagopal A numerical study of flow of power law fluid in an elbow bend has been carried out. The motivation behind this study is to analyze the velocity profiles, especially the pattern of the secondary flow of power law fluid in a bend as there are several important technological applications to which such a problem has relevance. This problem especially finds applications in the polymer processing industries and food industries where the fluid needs to be pumped through bent pipes. Hence, it is very important to study the secondary flow to determine the amount of power required to pump the fluid. -
Numerical Simulations of Planar Extrusion and Fused Filament Fabrication of Non-Newtonian Fluids
ANNUAL TRANSACTIONS OF THE NORDIC RHEOLOGY SOCIETY, VOL. 25, 2017 Numerical Simulations of Planar Extrusion and Fused Filament Fabrication of Non-Newtonian Fluids Raphaël Comminal, Jesper H. Hattel, and Jon Spangenberg Department of Mechanical Engineering, Technical University of Denmark, Kgs. Lyngby, Denmark ABSTRACT optimization algorithms and sensitivity In this study, the planar extrudate analysis built on numerical simulations have swelling of power-law and Oldroyd-B fluids successfully been applied to develop are investigated. Our numerical predictions computer-aided design strategies for are in good agreement with the other results extrusion dies1,2,3. available in the literature. In addition, a Generally, non-Newtonian fluids are simplified two-dimensional model of fused either characterized by a non-constant filament fabrication that provides details of viscosity that depends on the flow the flow in the gap between the printing conditions (shear-thinning and pseudo- head and the substrate is presented. The plastic liquids), or by a time-dependent numerical simulations use the stress response that includes an elastic stress streamfunction/log-conformation and the component representing the recoverable volume-of-fluid methods. deformations coming from the stretching of polymer chains (viscoelastic liquids). INTRODUCTION Extrudate swelling is a typical phenomenon The simulation of non-Newtonian free- influenced by shear-thinning and surface flows is an important topic of viscoelasticity. computational rheology. The free-surface This conference paper presents flow simulations of non-Newtonian fluids numerical results of two-dimensional have several applications in polymer simulations of the extrudate swelling and the processing. Extrusion and fused filament fused filament fabrication of non-Newtonian fabrications are two examples of these fluids. -
Understanding Shear Thinning Using Brownian Dynamics Simulation
University of Tennessee at Chattanooga UTC Scholar Student Research, Creative Works, and Honors Theses Publications 5-2021 Understanding shear thinning using Brownian dynamics simulation Mackenzie Nicole Wall University of Tennessee at Chattanooga, [email protected] Follow this and additional works at: https://scholar.utc.edu/honors-theses Part of the Physical Chemistry Commons Recommended Citation Wall, Mackenzie Nicole, "Understanding shear thinning using Brownian dynamics simulation" (2021). Honors Theses. This Theses is brought to you for free and open access by the Student Research, Creative Works, and Publications at UTC Scholar. It has been accepted for inclusion in Honors Theses by an authorized administrator of UTC Scholar. For more information, please contact [email protected]. 1 Understanding Shear Thinning Using Brownian Dynamics Simulation Mackenzie Nicole Wall Departmental Honors Thesis University of Tennessee at Chattanooga Department of Chemistry and Physics Examination Date: 23 March 2021 Dr. Luis Sanchez-Diaz Dr. John Lee Lecturer of Physics Associate Professor of Chemistry Project Director Department Examiner 2 Abstract: In this work, we study the changes in structure during the shear thinning regime using Brownian Dynamics with a simple steady-state shear flow of binary charged colloidal suspension. Previous research has analyzed the viscosity, radial distribution, elasticity and plasticity of materials with rheo-SANS experimentation; however, less research has been conducted to replicate the experiment through computer simulations. With Brownian Dynamic Simulation, this study was able to reproduce the results obtained in a recent rheo-SANS experiment and it also explored the viscosity, radial distribution, elastic and plastic behavior of a system under different parameters. The comparison of simulated data with experimental data revealed the computer simulation to successfully generate results indicative of shear thinning behavior in both the viscosity versus shear data as well as the radial distribution data. -
Thixotropy of Systems with Shear Thinning and Plastic Flow Behavior
Journal of Materials Science and Engineering B 9 (3-4) (2019) 56-65 doi: 10.17265/2161-6221/2019.3-4.003 D DAVID PUBLISHING Thixotropy of Systems with Shear Thinning and Plastic Flow Behavior Dimiter Hadjistamov DECE GmbH, Helvetierstr. 15, Riehen 4125, Schweiz Abstract: The definition of the thixotropy is a decrease in viscosity with time in shear and a subsequent recovery of viscosity after the shear deformation is removed. We used therefore start-up experiments with constant shear rates and can speak consequently of shear stress instead of viscosity. The shear stress increases sharply at the beginning of the stress growth experiment, passes an overshoot and begins to decrease up to the steady state shear stress. We can assume that a stress growth curve with an overshoot points out to thixotropic behavior. After the steady state shear stress is reached, the shear deformation is stopped, and the stress relaxation begins. It is to be expected that the shear stress will recover after the stress relaxation. Systems with shear thinning and plastic flow behavior were examined. The thixotropy is discussed in relation to the flow behavior. Stress growth experiments were performed with shear rates from the first Newtonian region and from the shear thinning region of the systems with shear thinning flow behavior. Stress start-up experiments were carrying out with shear rates from the first and second yield stress regions and from the transition section of a system with plastic flow behavior. Key words: Thixotropy, rheopexy, systems with shear thinning flow behavior, systems with plastic flow behavior, time related flow behaviour. -
High Shear Rate Viscometry
Noname manuscript No. (will be inserted by the editor) C. J. Pipe · T. S. Majmudar · G. H. McKinley High Shear Rate Viscometry the date of receipt and acceptance should be inserted later Abstract We investigate the use of two distinct and complementary approaches to measuring the vis- cometric properties of low viscosity complex fluids at high shear rates up to 80,000 s−1. Firstly we adapt commercial controlled-stress and controlled-rate rheometers to access elevated shear rates by using par- allel plate fixtures with very small gap settings (down to 30 µm). The resulting apparent viscosities are gap-dependent and systematically in error but the data can be corrected - at least for Newtonian fluids - via a simple linear gap correction originally presented by Connelly & Greener (1985). Secondly we use a microfabricated rheometer-on-a-chip to measure the steady flow curve in rectangular microchannels. The Weissenberg-Rabinowitsch-Mooney analysis is used to convert measurements of the pressure-drop/flow- rate relationship into the true wall-shear rate and the corresponding shear-rate-dependent viscosity. Mi- crochannel measurements are presented for a range of Newtonian calibration oils, a weakly shear-thinning dilute solution of poly(ethylene oxide), a strongly shear-thinning, concentrated solution of xanthan gum and a wormlike micelle solution that exhibits shear-banding at a critical stress. Excellent agreement between the two approaches is obtained for the Newtonian calibration oils, and the relative benefits of each technique are compared andPreprint contrasted by considering the physical processes and instrumental limitations that bound the operating spaces for each device. -
Incompressible Non-Newtonian Fluid Flows
3 Incompressible Non-Newtonian Fluid Flows Quoc-Hung Nguyen and Ngoc-Diep Nguyen Mechanical Faculty, Ho Chi Minh University of Industry, Vietnam 1. Introduction A non-Newtonian fluid is a fluid whose flow properties differ in many ways from those of Newtonian fluids. Most commonly the viscosity of non-Newtonian fluids is not independent of shear rate or shear rate history. In practice, many fluid materials exhibits non-Newtonian fluid behavior such as: salt solutions, molten, ketchup, custard, toothpaste, starch suspensions, paint, blood, and shampoo etc. In a Newtonian fluid, the relation between the shear stress and the shear rate is linear, passing through the origin, the constant of proportionality being the coefficient of viscosity. In a non-Newtonian fluid, the relation between the shear stress and the shear rate is different, and can even be time-dependent. Therefore a constant coefficient of viscosity cannot be defined. In the previous parts of this book, the mechanics of Newtonian fluid have been mentioned. In this chapter, the common rheological models of non-Newtonian fluids are introduced and several approaches concerned with non-Newtonian fluid flows are considered. In addition, the solution of common non-Newtonian fluid flows in a circular pipe, annular and rectangular duct are presented. 2. Classification of non-Newtonian fluid As above mentioned, a non-Newtonian fluid is one whose flow curve (shear stress versus shear rate) is nonlinear or does not pass through the origin, i.e. where the apparent viscosity, shear stress divided by shear rate, is not constant at a given temperature and pressure but is dependent on flow conditions such as flow geometry, shear rate, etc.