Abstract Post-Shuttle EVA Operations On
Total Page:16
File Type:pdf, Size:1020Kb
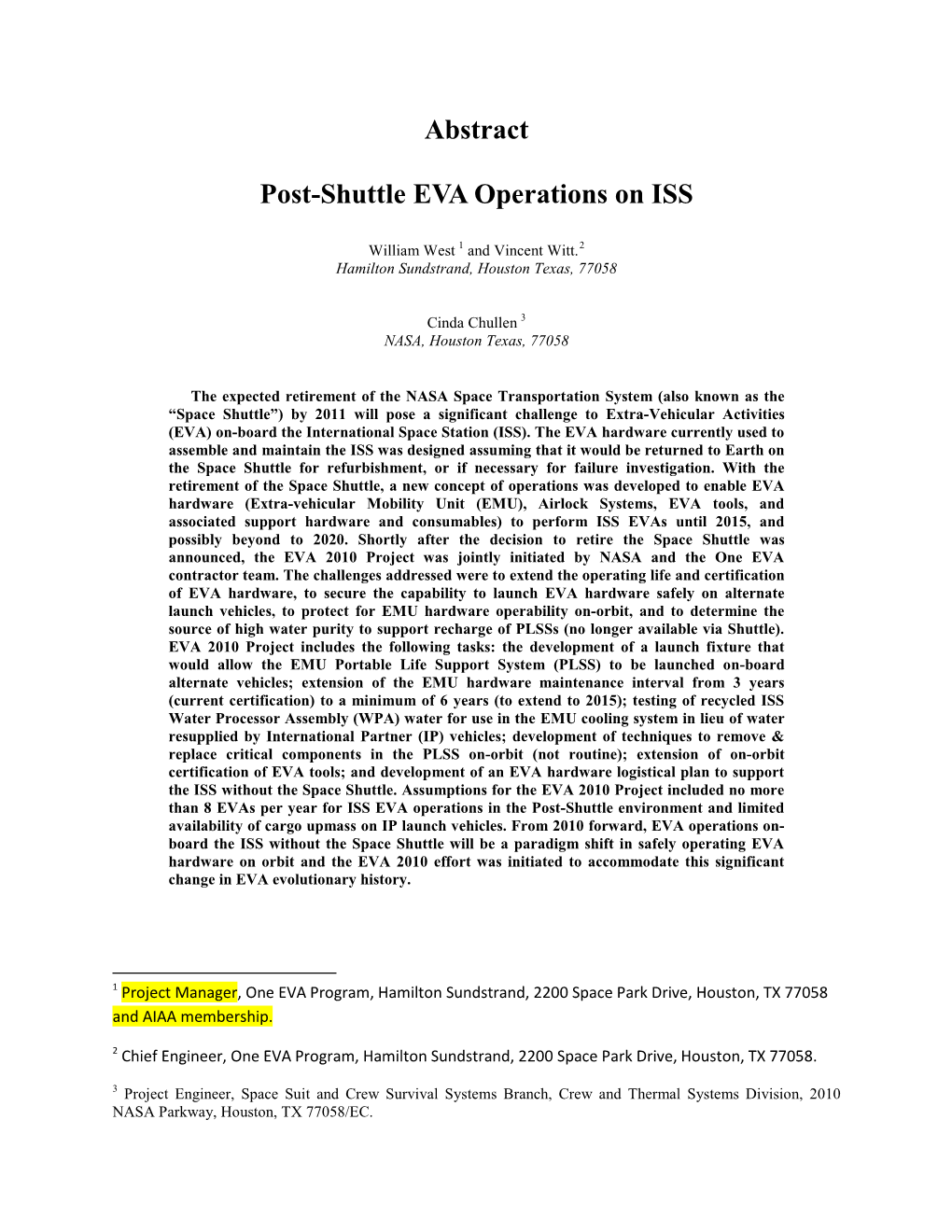
Load more
Recommended publications
-
GAO-07-595T NASA: Issues Surrounding the Transition from The
United States Government Accountability Office Testimony before the Subcommittee on GAO Space, Aeronautics, and Related Sciences, Committee on Commerce, Science and Transportation, U.S. Senate For Release on Delivery Expected at 2:30 p.m. EDT Wednesday, March 28, 2007 NASA Issues Surrounding the Transition from the Space Shuttle to the Next Generation of Human Space Flight Systems Statement of Allen Li, Director Acquisition and Sourcing Management GAO-07-595T March 28, 2007 NASA Accountability Integrity Reliability Highlights Issues Surrounding the Transition from Highlights of GAO-07-595T, a testimony the Space Shuttle to the Next Generation before the Subcommittee on Space, Aeronautics, and Related Sciences, of Human Space Flight Systems Committee on Commerce, Science and Transportation, U. S. Senate Why GAO Did This Study What GAO Found On January 14, 2004, the President NASA is in the midst of a transition effort of a magnitude not seen since the announced a new Vision for space end of the Apollo program and the start of the Space Shuttle Program more exploration that directs the than 3 decades ago. This transition will include a massive transfer of people, National Aeronautics and Space hardware, and infrastructure. Based on ongoing and work completed to- Administration (NASA) to focus its date, we have identified a number of issues that pose unique challenges to efforts on returning humans to the moon by 2020 in preparation for NASA as it transitions from the shuttle to the next generation of human future, more ambitions missions. space flight systems while at the same time seeking to minimize the time the United States will be without its own means to put humans in space. -
The Role and Training of NASA Astronauts In
Co-chairs: Joe Rothenberg, Fred Gregory Briefing: October 18-19, 2011 Statement of Task An ad hoc committee will conduct a study and prepare a report on the activities of NASA’s human spaceflight crew office. In writing its report the committee will address the following questions: • How should the role and size of the activities managed by the Johnson Space Center Flight Crew Operations Directorate change after space shuttle retirement and completion of the assembly of the International Space Station (ISS)? • What are the requirements of crew-related ground-based facilities after the space shuttle program ends? • Is the fleet of aircraft used for the training the Astronaut Corps a cost-effective means of preparing astronauts to meet the requirements of NASA’s human spaceflight program? Are there more cost-effective means of meeting these training requirements? The NRC was not asked to consider whether or not the United States should continue human spaceflight, or whether there were better alternatives to achieving the nation’s goals without launching humans into space. Rather, the NRC’s charge was to assume that U.S. human spaceflight would continue. 2 Committee on Human Spaceflight Crew Operations • FREDERICK GREGORY, Lohfeld Consulting Group, Inc., Co-Chair • JOSEPH H. ROTHENBERG, Swedish Space Corporation, Co-Chair • MICHAEL J. CASSUTT, University of Southern California • RICHARD O. COVEY, United Space Alliance, LLC (retired) • DUANE DEAL, Stinger Ghaffarian Technologies, Inc. • BONNIE J. DUNBAR, President and CEO, Dunbar International, LLC • WILLIAM W. HOOVER, Independent Consultant • THOMAS D. JONES, Florida Institute of Human and Machine Cognition • FRANKLIN D. MARTIN, Martin Consulting, Inc. -
GAO-05-230 Space Shuttle: Actions Needed to Better Position
United States Government Accountability Office Report to Congressional Requesters GAO March 2005 SPACE SHUTTLE Actions Needed to Better Position NASA to Sustain Its Workforce through Retirement GAO-05-230 March 2005 SPACE SHUTTLE Accountability Integrity Reliability Highlights Actions Needed to Better Position NASA Highlights of GAO-05-230, a report to to Sustain Its Workforce through congressional requesters Retirement Why GAO Did This Study What GAO Found The President’s vision for space The Space Shuttle Program has made limited progress toward developing a exploration (Vision) directs the detailed long-term strategy for sustaining its workforce through the space National Aeronautics and Space shuttle’s retirement. The program has taken preliminary steps, including Administration (NASA) to retire the identifying the lessons learned from the retirement of programs comparable space shuttle following completion to the space shuttle, such as the Air Force Titan IV Rocket Program, to assist of the International Space Station, planned for the end of the decade. in its workforce planning efforts. Other efforts have been initiated or are The retirement process will last planned, such as enlisting the help of human capital experts and revising the several years and impact thousands acquisition strategy for updating the space shuttle’s propulsion system prime of critically skilled NASA civil contracts; however, actions taken thus far have been limited. NASA’s prime service and contractor employees contractor for space shuttle operations has also taken some preliminary that support the program. Key to steps to begin to prepare for the impact of the space shuttle’s retirement on implementing the Vision is NASA’s its workforce, such as working with a consulting firm to conduct a ability to sustain this workforce to comprehensive study of its workforce. -
1 Statement of Kathryn C. Thornton Professor and Associate Dean School of Engineering and Applied Science University of Virginia
Statement of Kathryn C. Thornton Professor and Associate Dean School of Engineering and Applied Science University of Virginia before the Committee on Science and Technology Subcommittee on Space and Aeronautics U.S. House of Representatives April 3, 2008 Chairman Udall, Ranking Member Feeney, and members of the subcommittee, thank you for inviting me to appear before you today. My name is Kathryn Thornton and I am a Professor and Associate Dean in the School of Engineering and Applied Science at the University of Virginia. I appear here this morning not in my faculty role but as an organizer and co-chair of an independent workshop entitled Examining the Vision: Balancing Exploration and Science held last February at Stanford University. The workshop was co-hosted by Stanford University Department of Aeronautics and Astronautics, and The Planetary Society. Other organizers were co-chair Professor G. Scott Hubbard from Stanford University, Dr. Louis Friedman of The Planetary Society, and Dr. Wesley T. Huntress, Jr., of the Carnegie Institution of Washington. The post- workshop joint communiqué and a partial list of participants are attached. The intent of the workshop was to critically examine the current implementation of the Vision for Space Exploration as announced by President Bush in January 2004, especially to help prepare for a new Administration’s consideration of its broad space program goals and plans. The Vision for Space Exploration in its original plan was a major redirection of the human space flight program with an accompanying emphasis on scientific exploration. Whatever changes might be made in its implementation in the next Administration, we wanted to identify, highlight and support the best parts of the current concept. -
A Review of Nasa's Exploration
A REVIEW OF NASA’S EXPLORATION PROGRAM IN TRANSITION: ISSUES FOR CONGRESS AND INDUSTRY HEARING BEFORE THE SUBCOMMITTEE ON SPACE AND AERONAUTICS COMMITTEE ON SCIENCE, SPACE, AND TECHNOLOGY HOUSE OF REPRESENTATIVES ONE HUNDRED TWELFTH CONGRESS FIRST SESSION MARCH 30, 2011 Serial No. 112–8 Printed for the use of the Committee on Science, Space, and Technology ( Available via the World Wide Web: http://science.house.gov U.S. GOVERNMENT PRINTING OFFICE 65–305PDF WASHINGTON : 2011 For sale by the Superintendent of Documents, U.S. Government Printing Office Internet: bookstore.gpo.gov Phone: toll free (866) 512–1800; DC area (202) 512–1800 Fax: (202) 512–2104 Mail: Stop IDCC, Washington, DC 20402–0001 COMMITTEE ON SCIENCE, SPACE, AND TECHNOLOGY HON. RALPH M. HALL, Texas, Chair F. JAMES SENSENBRENNER, JR., EDDIE BERNICE JOHNSON, Texas Wisconsin JERRY F. COSTELLO, Illinois LAMAR S. SMITH, Texas LYNN C. WOOLSEY, California DANA ROHRABACHER, California ZOE LOFGREN, California ROSCOE G. BARTLETT, Maryland DAVID WU, Oregon FRANK D. LUCAS, Oklahoma BRAD MILLER, North Carolina JUDY BIGGERT, Illinois DANIEL LIPINSKI, Illinois W. TODD AKIN, Missouri GABRIELLE GIFFORDS, Arizona RANDY NEUGEBAUER, Texas DONNA F. EDWARDS, Maryland MICHAEL T. MCCAUL, Texas MARCIA L. FUDGE, Ohio PAUL C. BROUN, Georgia BEN R. LUJA´ N, New Mexico SANDY ADAMS, Florida PAUL D. TONKO, New York BENJAMIN QUAYLE, Arizona JERRY MCNERNEY, California CHARLES J. ‘‘CHUCK’’ FLEISCHMANN, JOHN P. SARBANES, Maryland Tennessee TERRI A. SEWELL, Alabama E. SCOTT RIGELL, Virginia FREDERICA S. WILSON, Florida STEVEN M. PALAZZO, Mississippi HANSEN CLARKE, Michigan MO BROOKS, Alabama ANDY HARRIS, Maryland RANDY HULTGREN, Illinois CHIP CRAVAACK, Minnesota LARRY BUCSHON, Indiana DAN BENISHEK, Michigan VACANCY SUBCOMMITTEE ON SPACE AND AERONAUTICS HON. -
Happy Holidays!!!
December 2000 Cosmonotes Décembre 2000 The Newsletter of the Canadian Alumni of the International Space University Le Bulletin des Anciens Etudiants Canadiens de l’Université Internationale de l’Espace reminiscing on an Aerospace Medicine docked to the Station, three HAPPY Elective at KSC, and an article from the spacewalks will be conducted to busy, busy, busy MSS6. Another deliver, assemble, and activate the opinion piece is included in this issue, U.S. electrical power system on board HOLIDAYS!!! this time on The Dreams our Star Stuff the ISS. The electrical power system, Here is the December 2000 edition of is Made of – thank you to Eric Choi which is built into a 47-foot integrated your CAISU newsletter, Cosmonotes, (SSP 99) for polling the alumni and truss structure known as P6, consists again packed with many fascinating writing a delightful article from all of solar arrays, radiators for cooling, articles from alumni and friends. This responses received. batteries for solar energy storage, and electronics. P6 is the first section of a issue of Cosmonotes was slightly Thank you to all alumni who system that ultimately will deliver 60 delayed to include an article on the volunteered to write articles for times more power to the ISS research November 30th launch of STS-97 with Cosmonotes! It is thanks to the facilities than was possible on Mir. Canadian Astronaut Marc Garneau on constant willingness of alumni to board, a launch that many CAISU contribute that this newsletter keeps Mission Specialist Marc Garneau members were present in Florida to getting better (and thicker!) with each (Ph.D.) will attach P6 to the evolving view thanks to an invitation from the issue. -
Page 8373 TITLE 42—THE PUBLIC HEALTH and WELFARE § 18363
Page 8373 TITLE 42—THE PUBLIC HEALTH AND WELFARE § 18363 SUBCHAPTER V—SPACE SHUTTLE available for activities pursuant to this para- RETIREMENT AND TRANSITION graph. § 18361. Sense of Congress on the Space Shuttle (Pub. L. 111–267, title VI, § 602, Oct. 11, 2010, 124 program Stat. 2828.) (a) Findings REFERENCES IN TEXT Congress makes the following findings: Section 101(2)(B), referred to in subsec. (b)(2), is Pub. (1) The Space Shuttle program represents a L. 111–267, title I, § 101(2)(B), Oct. 11, 2010, 124 Stat. 2809, national asset consisting of critical skills and which is not classified to the Code. capabilities, including the ability to lift large § 18363. Disposition of orbiter vehicles payloads into space and return them to Earth. (2) The Space Shuttle has carried more than (a) In general 355 people from 16 nations into space. Upon the termination of the Space Shuttle (3) The Space Shuttle has projected the best program as provided in section 18362 of this of American values around the world, and title, the Administrator shall decommission any Space Shuttle crews have sparked the imagi- remaining Space Shuttle orbiter vehicles ac- nation and dreams of the world’s youth and cording to established safety and historic pres- young at heart. ervation procedures prior to their designation as (b) Sense of Congress surplus government property. The orbiter vehi- cles shall be made available and located for dis- It is the sense of Congress that— play and maintenance through a competitive (1) it is essential that the retirement of the procedure established pursuant to the disposi- Space Shuttle and the transition to new tion plan developed under section 613(a) of the human space flight capabilities be done in a National Aeronautics and Space Administration manner that builds upon the legacy of this na- Authorization Act of 2008 (42 U.S.C. -
Toward a History of the Space Shuttle an Annotated Bibliography
Toward a History of the Space Shuttle An Annotated Bibliography Part 2, 1992–2011 Monographs in Aerospace History, Number 49 TOWARD A HISTORY OF THE SPACE SHUTTLE AN ANNOTATED BIBLIOGRAPHY, PART 2 (1992–2011) Compiled by Malinda K. Goodrich Alice R. Buchalter Patrick M. Miller of the Federal Research Division, Library of Congress NASA History Program Office Office of Communications NASA Headquarters Washington, DC Monographs in Aerospace History Number 49 August 2012 NASA SP-2012-4549 Library of Congress – Federal Research Division Space Shuttle Annotated Bibliography PREFACE This annotated bibliography is a continuation of Toward a History of the Space Shuttle: An Annotated Bibliography, compiled by Roger D. Launius and Aaron K. Gillette, and published by NASA as Monographs in Aerospace History, Number 1 in December 1992 (available online at http://history.nasa.gov/Shuttlebib/contents.html). The Launius/Gillette volume contains those works published between the early days of the United States’ manned spaceflight program in the 1970s through 1991. The articles included in the first volume were judged to be most essential for researchers writing on the Space Shuttle’s history. The current (second) volume is intended as a follow-on to the first volume. It includes key articles, books, hearings, and U.S. government publications published on the Shuttle between 1992 and the end of the Shuttle program in 2011. The material is arranged according to theme, including: general works, precursors to the Shuttle, the decision to build the Space Shuttle, its design and development, operations, and management of the Space Shuttle program. Other topics covered include: the Challenger and Columbia accidents, as well as the use of the Space Shuttle in building and servicing the Hubble Space Telescope and the International Space Station; science on the Space Shuttle; commercial and military uses of the Space Shuttle; and the Space Shuttle’s role in international relations, including its use in connection with the Soviet Mir space station. -
An Update on Nasa Exploration Systems Development Hearing Committee on Science, Space, and Technology House of Representatives
AN UPDATE ON NASA EXPLORATION SYSTEMS DEVELOPMENT HEARING BEFORE THE SUBCOMMITTEE ON SPACE COMMITTEE ON SCIENCE, SPACE, AND TECHNOLOGY HOUSE OF REPRESENTATIVES ONE HUNDRED FIFTEENTH CONGRESS FIRST SESSION NOVEMBER 9, 2017 Serial No. 115–37 Printed for the use of the Committee on Science, Space, and Technology ( Available via the World Wide Web: http://science.house.gov U.S. GOVERNMENT PUBLISHING OFFICE 27–676PDF WASHINGTON : 2018 For sale by the Superintendent of Documents, U.S. Government Publishing Office Internet: bookstore.gpo.gov Phone: toll free (866) 512–1800; DC area (202) 512–1800 Fax: (202) 512–2104 Mail: Stop IDCC, Washington, DC 20402–0001 COMMITTEE ON SCIENCE, SPACE, AND TECHNOLOGY HON. LAMAR S. SMITH, Texas, Chair FRANK D. LUCAS, Oklahoma EDDIE BERNICE JOHNSON, Texas DANA ROHRABACHER, California ZOE LOFGREN, California MO BROOKS, Alabama DANIEL LIPINSKI, Illinois RANDY HULTGREN, Illinois SUZANNE BONAMICI, Oregon BILL POSEY, Florida ALAN GRAYSON, Florida THOMAS MASSIE, Kentucky AMI BERA, California JIM BRIDENSTINE, Oklahoma ELIZABETH H. ESTY, Connecticut RANDY K. WEBER, Texas MARC A. VEASEY, Texas STEPHEN KNIGHT, California DONALD S. BEYER, JR., Virginia BRIAN BABIN, Texas JACKY ROSEN, Nevada BARBARA COMSTOCK, Virginia JERRY MCNERNEY, California BARRY LOUDERMILK, Georgia ED PERLMUTTER, Colorado RALPH LEE ABRAHAM, Louisiana PAUL TONKO, New York DRAIN LAHOOD, Illinois BILL FOSTER, Illinois DANIEL WEBSTER, Florida MARK TAKANO, California JIM BANKS, Indiana COLLEEN HANABUSA, Hawaii ANDY BIGGS, Arizona CHARLIE CRIST, Florida ROGER W. MARSHALL, Kansas NEAL P. DUNN, Florida CLAY HIGGINS, Louisiana RALPH NORMAN, South Carolina SUBCOMMITTEE ON SPACE HON. BRIAN BABIN, Texas, Chair DANA ROHRABACHER, California AMI BERA, California, Ranking Member FRANK D. -
Shuttle Derived Heavy Lift Launch Vehicle Attributes
Shuttle-DerivedShuttle-Derived HeavyHeavy LiftLift LaunchLaunch VehicleVehicle SideSide MountMount vsvs In-LineIn-Line NASAWATCH.COM SPACE SHUTTLE PROGRAM NASA Johnson Space Center, Houston, Texas Presenter Shuttle Derived Heavy Lift Launch Mack Henderson Vehicle Attributes Date 6/11/10 Page 2 • A Shuttle derived heavy-lift launch vehicle (HLV) provides a logical next step to meet the forecasted Space needs, following the Space Shuttle retirement • Shuttle Side configuration makes maximum use of existing Shuttle assets and facilities without the Expense and Risks of using an Orbiter vehicle • It retains the contractor and civil servant technical skill-base. Ground and Mission operations, will be similar to the Space Shuttle Program • HLV provides a near term capability that can meet the evolving needs of NASA - Expansion and Upgrades for the International Space Station - Fly missions that demonstrate FTD and enabling technologies that will be needed to safely and efficiently go beyond Low Earth Orbit (LEO) • Side Mount can be flown simultaneously with a crewed or uncrewed Shuttle HLV PROVIDES A CAPABILITY SOON TO MEET NATIONAL NEEDS WHILE FUTURE VEHICLES ARE EVOLVING NASAWATCH.COM SPACE SHUTTLE PROGRAM NASA Johnson Space Center, Houston, Texas Presenter HLV Near Term Customers Mack Henderson Date 6/11/10 Page 3 • Space Based Solar Power- multi Centers/DOE/DoD • Technology demonstrations- Flagship technologies • Inflatable habitat - commercial • Satellite servicing- GSFC/DoD/commercial • ISS repair/upgrades- ISS Program • Propellant depot- -
1. Purpose and Need for Action
Final Constellation Programmatic Environmental Impact Statement 1. PURPOSE AND NEED FOR ACTION This Final Constellation Programmatic Environmental Impact Statement has been prepared by the National Aeronautics and Space Administration (NASA) to assist in the decision-making process as required by the National Environmental Policy Act of 1969, as amended (NEPA) (42 United States Code [U.S.C.] 4321 et seq.); Council on Environmental Quality regulations for implementing the procedural provisions of NEPA (40 Code of Federal Regulations [CFR] parts 1500-1508); NASA policies and procedures at 14 CFR subpart 1216.3; and Executive Order 12114, Environmental Effects Abroad of Major Federal Actions. 1.1 BACKGROUND The Constellation Program would provide the flight systems and Earth-based ground infrastructure for an expanded human presence in the Solar System. Building on the achievements of previous lunar exploration efforts and crewed missions to low Earth orbit and the many technological advancements made over the past five decades, the Constellation Program would enable the United States (U.S.) to continue to access the International Space Station, return humans to the Moon, and enable human exploration of Mars and beyond. 1.1.1 U.S. Human Space Exploration Programs Beginning in the late 1950s, the U.S. embarked upon the ongoing effort of human space exploration. The first human spaceflight initiative was Project Mercury, established in October 1958 with crewed spacecraft first launched from Cape Canaveral Air Force Station (CCAFS) in the early 1960s. NASA’s Launch Operations Center and the portions of CCAFS that were used by NASA were renamed the John F. Kennedy Space Center (KSC) in 1963. -
NASA) FOIA Case Logs, 2012-2015
Description of document: National Aeronautics and Space Administration (NASA) FOIA Case Logs, 2012-2015 Requested date: 19-February-2016 Released date: 24-February-2016 Posted date: 29-August-2016 Source of document: FOIA Request NASA Headquarters 300 E Street, SW Room 5Q16 Washington, DC 20546 Fax: (202) 358-4332 Email: [email protected] Online FOIA Form The governmentattic.org web site (“the site”) is noncommercial and free to the public. The site and materials made available on the site, such as this file, are for reference only. The governmentattic.org web site and its principals have made every effort to make this information as complete and as accurate as possible, however, there may be mistakes and omissions, both typographical and in content. The governmentattic.org web site and its principals shall have neither liability nor responsibility to any person or entity with respect to any loss or damage caused, or alleged to have been caused, directly or indirectly, by the information provided on the governmentattic.org web site or in this file. The public records published on the site were obtained from government agencies using proper legal channels. Each document is identified as to the source. Any concerns about the contents of the site should be directed to the agency originating the document in question. GovernmentAttic.org is not responsible for the contents of documents published on the website. National Aeronautics and Space Administration Headquarters Washington, DC 20546-0001 February 24, 2016 Reply to Attn of: Office of Communication FOIA: 16-HQ-F-00317 Thank you for your Freedom of Information Act (FOIA) request dated and received February 19, 2016, at the NASA Headquarters FOIA Office.