Proceedings of the Indiana Academy of Science
Total Page:16
File Type:pdf, Size:1020Kb
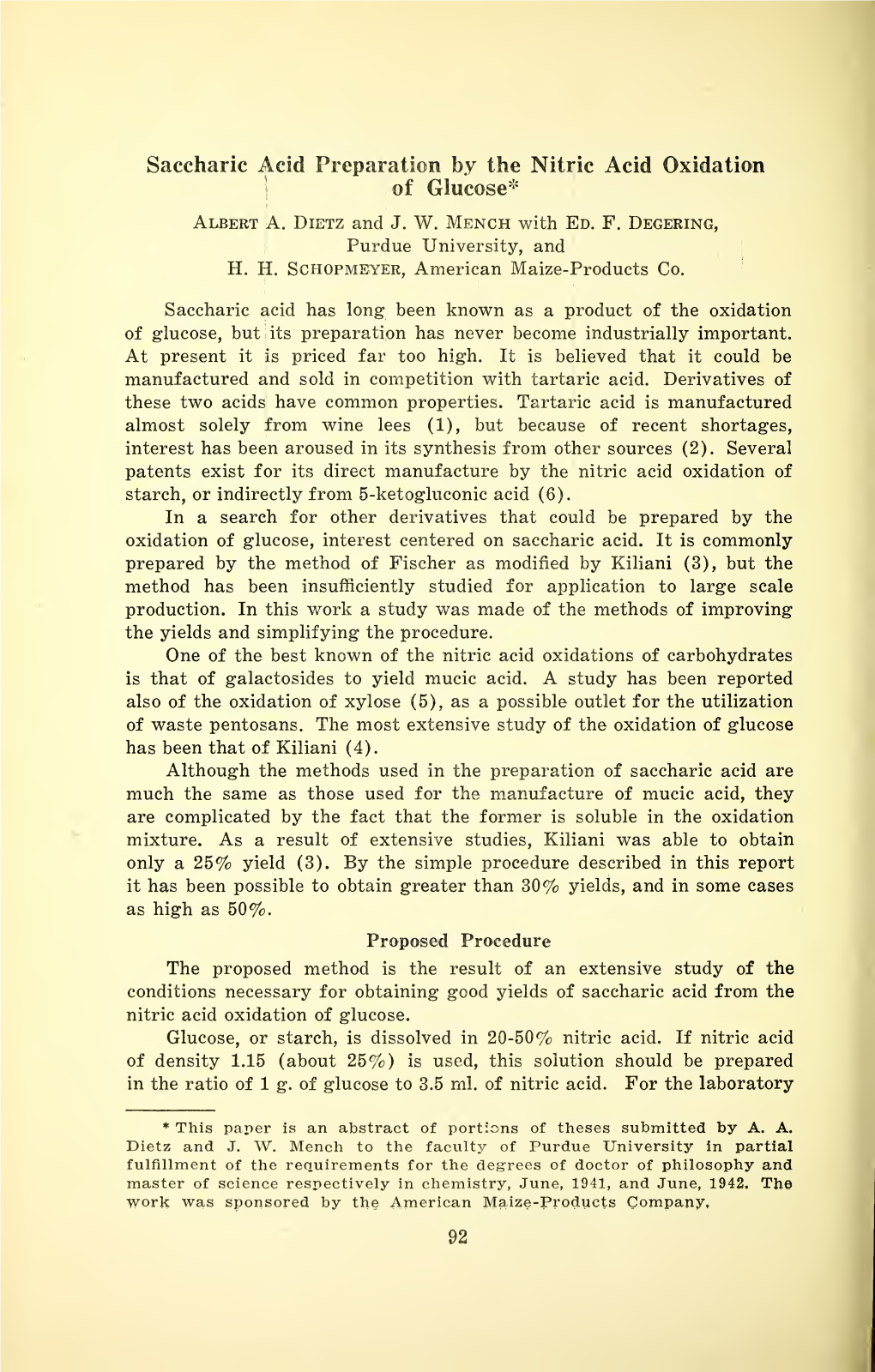
Load more
Recommended publications
-
Proceedings of the Indiana Academy of Science
The Nitrogen Dioxide Oxidation of Starch* J. W. Mench, with Ed F. Degering, Purdue University Although the literature contains over two hundred references to the oxidation of starch, little is known concerning the structures of the products because various oxidants may simultaneously attack one or more of the hydroxl groups to produce a complicated structure containing car- boxyl, aldehyde, and ketone groupings. An exception appears to result when periodic acid is used, since this oxidant seemingly exhibits a specificity towards parts of the carbohydrate molecule containing adja- 1 2 cent, secondary hydroxyl groupings. - The observations of Unruh, Yec- kel, and Kenyon,M that cellulose can be oxidized with nitrogen dioxide to a polyanhydroglucuronic acid, indicate that this reagent preferentially attacks the primary hydroxyl groups in certain glycosides. We have attempted to apply to starch both the static and cyclic method of oxidation reported by these men, in an effort to produce the alpha-linked polyanhydroglucuronic acids. However, the tendency of the powdered carbohydrate to pack made these procedures unsatisfactory, since the reactions were difficult to control and at least partial hydrolysis of the starch frequently occurred. We have found, however, that under suitable conditions, starch may be oxidized by nitrogen dioxide to produce a new type of oxidized starch containing, predominately, uronic acid residues. This point was con- firmed, qualitatively, by a positive beta-naphthol test,5 which indicated the presence of glucuronic acid, although attempts to hydrolyze the prod- ucts to glucuronic acid, and to prepare the cinchonine salt or oxime of this compound were without success. The procedure and diluent utilized in this work was suggested by the work of Maurer and Drefahl,6 who oxidized galactose, methyl gluco- side, and methyl galactoside with nitrogen dioxide in carbon tetrachloride or chloroform—obtaining mucic acid and the corresponding substituted uronic acids, respectively. -
Elimination of Galactaric Acid Catabolism by Using RNA Sequencing and CRISPR/Cas9 Joosu Kuivanen*†, Y.‑M
Kuivanen et al. Microb Cell Fact (2016) 15:210 DOI 10.1186/s12934-016-0613-5 Microbial Cell Factories RESEARCH Open Access Engineering Aspergillus niger for galactaric acid production: elimination of galactaric acid catabolism by using RNA sequencing and CRISPR/Cas9 Joosu Kuivanen*†, Y.‑M. Jasmin Wang† and Peter Richard Abstract Background: meso-Galactaric acid is a dicarboxylic acid that can be produced by the oxidation of D-galacturonic acid, the main constituent of pectin. Mould strains can be engineered to perform this oxidation by expressing the bacterial enzyme uronate dehydrogenase. In addition, the endogenous pathway for D-galacturonic acid catabolism has to be inactivated. The filamentous fungus Aspergillus niger would be a suitable strain for galactaric acid produc‑ tion since it is efficient in pectin hydrolysis, however, it is catabolizing the resulting galactaric acid via an unknown catabolic pathway. Results: In this study, a transcriptomics approach was used to identify genes involved in galactaric acid catabolism. Several genes were deleted using CRISPR/Cas9 together with in vitro synthesized sgRNA. As a result, galactaric acid catabolism was disrupted. An engineered A. niger strain combining the disrupted galactaric and D-galacturonic acid catabolism with an expression of a heterologous uronate dehydrogenase produced galactaric acid from D-galactu‑ ronic acid. The resulting strain was also converting pectin-rich biomass to galactaric acid in a consolidated bioprocess. Conclusions: In the present study, we demonstrated the use of CRISPR/Cas9 mediated gene deletion technology in A. niger in an metabolic engineering application. As a result, a strain for the efficient production of galactaric acid from D-galacturonic acid was generated. -
Trichoderma Reesei Toni Paasikallio, Anne Huuskonen and Marilyn G
Paasikallio et al. Microb Cell Fact (2017) 16:119 DOI 10.1186/s12934-017-0736-3 Microbial Cell Factories RESEARCH Open Access Scaling up and scaling down the production of galactaric acid from pectin using Trichoderma reesei Toni Paasikallio, Anne Huuskonen and Marilyn G. Wiebe* Abstract Background: Bioconversion of D-galacturonic acid to galactaric (mucic) acid has previously been carried out in small scale (50–1000 mL) cultures, which produce tens of grams of galactaric acid. To obtain larger amounts of biologically produced galactaric acid, the process needed to be scaled up using a readily available technical substrate. Food grade pectin was selected as a readily available source of D-galacturonic acid for conversion to galactaric acid. Results: We demonstrated that the process using Trichoderma reesei QM6a Δgar1 udh can be scaled up from 1 L to 1 10 and 250 L, replacing pure D-galacturonic acid with commercially available pectin. T. reesei produced 18 g L− galac- 1 1 taric acid from food-grade pectin (yield 1.00 g [g D-galacturonate consumed]− ) when grown at 1 L scale, 21 g L− 1 1 galactaric acid (yield 1.11 g [g D-galacturonate consumed]− ) when grown at 10 L scale and 14 g L− galactaric acid 1 (yield 0.77 g [g D-galacturonate consumed]− ) when grown at 250 L scale. Initial production rates were similar to those observed in 500 mL cultures with pure D-galacturonate as substrate. Approximately 2.8 kg galactaric acid was precipitated from the 250 L culture, representing a recovery of 77% of the galactaric acid in the supernatant. -
Sigma Sugars and Carbohydrates
Sigma Sugars and Carbohydrates Library Listing – 614 spectra This library represents a material-specific subset of the larger Sigma Biochemical Condensed Phase Library relating to sugars and carbohydrates found in the Sigma Biochemicals and Reagents catalog. Spectra acquired by Sigma-Aldrich Co. which were examined and processed at Thermo Fisher Scientific. The spectra include compound name, molecular formula, CAS (Chemical Abstract Service) registry number, and Sigma catalog number. Sigma Sugars and Carbohydrates Index Compound Name Index Compound Name 255 (+/-)-Epi-inosose-2 475 2,3,4,6-Tetra-O-methyl-D-glucopyranose 468 1,2,3,4-Tetra-O-acetyl-6- 487 2,3,5-Tri-O-benzoyl-1-O-p-nitrobenzoyl diphenylphosphoryl-b-D-manopyranose D-ribofuranoside 471 1,2,3,4-Tetra-O-acetyl-b-D- 490 2,3,5-Tri-O-benzyl-1-O-p-nitrobenzoyl- glucopyranose D-arabinofuranoside 472 1,2,3,5-Tetra-O-acetyl-b-D-ribofuranose 488 2,3,5-Tri-O-benzyl-b-D-arabinofuranose 473 1,2,3,5-Tetra-O-benzoyl-a-D- 489 2,3,5-Tri-O-benzyl-b-L-arabinofuranose xylofuranose 107 2,3-Dehydro-2-deoxy-N- 258 1,2-O-Isopropylidene-3-O-benzyl-rac- acetylneuraminic acid glycerol 142 2,3-Diphospho-D-glyceric acid, 261 1,2-O-Isopropylidene-5-O-p-tosyl-a-D- penta(CHA) salt xylofuranose 143 2,3-Diphospho-D-glyceric acid, 259 1,2-O-Isopropylidene-D-glucofuranose pentasodium salt 262 1,2-O-Isopropylidene-D-xylofuranose 144 2,3-Diphospho-D-glyceric acid, tris salt 135 1,2:3,4-Di-O-isopropylidene-D- 260 2,3-O-Isopropylidene-b-D- galactopyranose ribofuranosylamine, tosylate salt 141 1,2:3,5-Di-O-isopropylidene-D- -
Experiment 20 Identification of Some Carbohydrates
Experiment 20 Identification of Some Carbohydrates Carbohydrates are the direct product of the photosynthetic combination of carbon dioxide and water. By weight, they are the most common organic compounds on earth. Since most have the empirical formula CnH2nOn = Cn(H2O)n it was initially believed that they were hydrates of carbon. Hence the name. In actuality they are polyhydroxylaldehydes and ketones and exist as cyclic hemi- and full acetals. The cyclic forms may be five-membered rings (furanose) or six-membered rings (pyranose). They are classified as mono-, di-, and polysaccharides. The term sugar applies to mono-, di-, and oligosaccharides, which are all soluble in water and thereby distinguished from polysaccharides, which are not soluble in water. The most commonly encountered carbohydrates are starch, glycogen, inulin, cellulose, sucrose, fructose, arabinose, mannose, glucose, maltose, galactose, and lactose. The method of analysis used in this experiment is one of elimination. The assumption is made that the compound is a single carbohydrate and tests are applied sequentially until a positive result is obtained. The carbohydrate giving the positive test is thus identified. The sugars that we will identify are shown below. Figure 20.1 Monosaccharides Aldohexoses O H C O H CH OH 2 O H C OH C HO OH HO C H HO HO C H OH H C OH HOCH OH HO C H 2 O H C OH D-glucose H C OH HO OH HO H C OH CH2OH D-mannose CH2OH O H C OH H C OH CH2OH CH2OH ketohexose O O C OH HO C H HO HOCH2 O OH HO C H HO C H HO D-galactose H C OH HO H C OH CH2OH CH OH -
Food Waste Conversion to Galactaric Acid
Food waste conversion to Galactaric acid KT Consortium Maria do Carmo Cabral Sacadura, John Woodley, Rafiqul Gani Annual Meeting KT Consortium, Department of Chemical and Biochemical Engineering, Technical University of Denmark June 2017 Introduction Galactaric acid (GA), also known as mucic acid, is a symmetrical six carbon diacid. GA is used as a chelator and in skin care products and has the potential application in polymer synthesis as a platform chemical. Its market is limited to the pharmaceutical and cosmetic industry. Currently, GA is commercially produced by oxidation of galactose with nitric acid or from D-galacturonic acid (D-galUA) by electrolytic oxidation. An alternative source of D-galUA is pectin, an abundant component in non- woody plant biomass such as in fruit peels. Citrus Processing Waste (CPW) is mainly generated from the industry of juice production which generates 10 million tonnes of wet CPW. Thus, it represents an available and inexpensive source for production of GA. The present project suggests an alternative route for production of GA through extraction of pectin from dry citrus peel, and its hydrolysis releasing D-galUA which is later oxidized to GA. An innovative, sustainable and environment-friendly solution is sought and analyzed through an economical and environmental assessment based on calculations done with simple derived models. The aim is to produce 2000 tonnes per year of GA. Figure 1. Chemical structure of Galactaric acid. For the extraction of pectin from dry citrus peel (TK1), citric acid and water are used as solvents (TK2) and the operation runs for 60 min at the solution’s boiling point (around 100 Process flowsheet ºC) and pH 2.3. -
FAUSTINO JOVITA MALAGUTI Sugar, Substitution Theory, and Amides
Revista CENIC. Ciencias Químicas ISSN: 1015-8553 ISSN: 2221-2442 [email protected] Centro Nacional de Investigaciones Científicas Cuba FAUSTINO JOVITA MALAGUTI Sugar, substitution theory, and amides Wisniak, Jaime FAUSTINO JOVITA MALAGUTI Sugar, substitution theory, and amides Revista CENIC. Ciencias Químicas, vol. 50, no. 1, 2019 Centro Nacional de Investigaciones Científicas, Cuba Available in: https://www.redalyc.org/articulo.oa?id=181662291006 PDF generated from XML JATS4R by Redalyc Project academic non-profit, developed under the open access initiative Jaime Wisniak. FAUSTINO JOVITA MALAGUTI Sugar, substitution theory, and amides Reseñas FAUSTINO JOVITA MALAGUTI Sugar, substitution theory, and amides FAUSTINO JOVITA MALAGUTI Azúcar, teoría de sustitución y amidas. Jaime Wisniak * Redalyc: https://www.redalyc.org/articulo.oa? Ben-Gurion University of the Negev, Israel id=181662291006 [email protected] Received: 31 July 2019 Accepted: 20 September 2019 Abstract: Faustino Jovita Malaguti (1802-1878), an Italian-French pharmacist, proved that diluted, even very diluted acids, at temperatures below 95 .C, acted in an identical manner upon sugar and that the final result was a mixture of ulmic and formic acid or only ulmic acid, depending if the reaction was conducted in the presence or absence of atmospheric air. Malaguti studied the preparation of mucic and paramucic acid and their derivatives, ethyl citrate and the formula of citric acid, crystalline camphoric acid by the prolonged action of nitric acid on camphor, the preparation and properties of several derivatives of camphoric acid, studied the chlorination of a large number of ethers to prove that the assumption of the substitution theory that one atom of hydrogen could be replaced by one atom of chlorine. -
Hazardous Waste Management Plan
Effective Date: August 1998 Review Date: HAZARDOUS WASTE December 2013 MANAGEMENT PLAN This document is required as per Title 40 of the Federal Code of Regulations at part 262. It provides generalized rules and guidelines for The University of Alabama in Huntsville’s management of hazardous wastes. TABLE OF CONTENTS 1.0 HAZARDOUS WASTE POLICY STATEMENT 2.0 INTRODUCTION 3.0 UAH HAZARDOUS WASTE REGULATIONS 4.0 HAZARDOUS WASTE MANAGEMENT SYSTEM 5.0 RESPONSIBILITY FOR IDENTIFICATION AND DISPOSAL 6.0 HAZARDOUS WASTE DETERMINATION 6.1 Characteristic Wastes 6.1.1 Ignitable Waste 6.1.2 Corrosive Waste 6.1.3 Reactive Waste 6.1.4 Toxic Waste 6.2 Acutely Hazardous Waste 6.3 Solvents 7.0 WASTE MINIMIZATION 7.1 Minimizing Reactive Waste 7.2 Minimizing Quantities 7.3 Recycling 7.4 Substitution 7.5 Reduction of Scale 7.6 Donations of Chemicals to the University 7.7 Unknowns 8.0 HAZARDOUS WASTE COLLECTION PROCEDURES 8.1 Segregation 8.1.1 Hazardous Waste Accumulation Areas 8.2 Packaging and Containers 8.3 Labeling 8.4 Inspection 8.5 Initiating Waste Removal 9.0 EPA EMPTY DEFINITION AND DISPOSAL OF EMPTY CONTAINERS 10.0 MISCELLANEOUS WASTE RULES 11.0 EMERGENCY PROCEDURES 12.0 RESPONSIBILITY AND ENFORCEMENT APPENDIX A LISTED HAZARDOUS WASTES APPENDIX B COMMON NON-REGULATED CHEMICAL WASTES 1.0 HAZARDOUS WASTE POLICY STATEMENT The University of Alabama in Huntsville is committed to full compliance with federal, state, and local laws and regulations pertaining to the management of hazardous waste. The Office of Environmental Health & Safety has overall responsibility for policies and procedures for the management of hazardous waste on campus. -
An Improvement of the Method for the Determination of Galactan
Title An Improvement of the Method for the Determination of Galactan Author(s) MIYAKE, K. Citation The journal of the College of Agriculture, Tohoku Imperial University, Sapporo, Japan, 4(8), 337-345 Issue Date 1912-03-30 Doc URL http://hdl.handle.net/2115/12509 Type bulletin (article) File Information 4(8)_p337-345.pdf Instructions for use Hokkaido University Collection of Scholarly and Academic Papers : HUSCAP An Improvement of tbe Metbod for the Determination of Galactan. By K. Miyake. The presence of galactan (or substances containing a galactose group in the molecnle) in natural prodncts has been shown, in recent years, by numer ous i'nwstigators. Quantitative determination of galactan has therefore been deemed desir able and the following method!), the llnderlying principle of which had been worked out by Toll C 11 S and his associates,~) was provisionally adopted by the association of the official agricultural chemists, U. S. A., for its determi nation in foods and feeding stuf£~. "Extract a convenient quantity of the substance, representing from 2.5 to 3.0 grams of the dry material, on a hardened filter with five sllccessive portions of 10 cc. of ether, place the extracted residue in a beaker about 5.5 cm. in diameter and 7 em. deep, together with 60 cc. of nitric acid of 1.15 specific gravity, and evaporate the solution to exactly one-third its volume III a water bath at a temperature of 94°to 96°C. After standing twenty fOllr hours, add 10 cc. of water to thc precipitate, and allow it to stand 1) U. -
Highly Efficient Chemical Process to Convert Mucic Acid Into Adipic Acid
Angewandte Chemie DOI: 10.1002/anie.201310991 Sustainable Chemistry Highly Efficient Chemical Process To Convert Mucic Acid into Adipic Acid and DFT Studies of the Mechanism of the Rhenium-Catalyzed Deoxydehydration** Xiukai Li, Di Wu, Ting Lu, Guangshun Yi, Haibin Su,* and Yugen Zhang* Abstract: The production of bulk chemicals and fuels from Combined biocatalytic and chemocatalytic pathways have renewable bio-based feedstocks is of significant importance for been used to produce adipic acid from renewable precursors, the sustainability of human society. Adipic acid, as one of the with cis,cis-muconic acid as the key intermediate.[6] In the most-demanded drop-in chemicals from a bioresource, is used reported biocatalytic conversions of glucose into muconic primarily for the large-volume production of nylon-6,6 acid, the multiple-step fermentation processes invoke several polyamide. It is highly desirable to develop sustainable and different kinds of enzymes, but the product yield and the environmentally friendly processes for the production of adipic production efficiency are very low.[7, 8] In contrast, the acid from renewable feedstocks. However, currently there is no conversion of muconic acid into adipic acid is rather suitable bio-adipic acid synthesis process. Demonstrated herein straightforward by using a hydrogenation reaction.[9] Adipic is the highly efficient synthetic protocol for the conversion of acid preparations by chemocatalytic hydrogenations of furan- mucic acid into adipic acid through the oxorhenium-complex- 2,5-dicarboxylic acid (FDCA)[10] and glucaric acid[11] have catalyzed deoxydehydration (DODH) reaction and subse- been reported in patents. However, drastic reaction condi- quent Pt/C-catalyzed transfer hydrogenation. -
One-Pot FDCA Diester Synthesis from Mucic Acid and Their Solvent-Free Regioselective Polytransesterification for Production of Glycerol-Based Furanic Polyesters
molecules Article One-Pot FDCA Diester Synthesis from Mucic Acid and Their Solvent-Free Regioselective Polytransesterification for Production of Glycerol-Based Furanic Polyesters Deyang Zhao 1,2, Frederic Delbecq 3 and Christophe Len 1,2,* 1 Sorbonne Universités, Université de Technologie de Compiègne, Centre de Recherches de Royallieu, CS 60319, F-60203 Compiègne CEDEX, France; [email protected] 2 PSL Research University, Chimie ParisTech, CNRS, Institute of Chemistry for Life and Health Sciences, 11 rue Pierre et Marie Curie, F-75231 Paris CEDEX 05, France 3 Ecole Supérieure de Chimie Organique et Minérale, 1 allée du Réseau Jean-Marie Buckmaster, F-60200 Compiègne, France; [email protected] * Correspondence: [email protected]; Tel.: +33-(0)638-500-976; Fax: +33-(0)344-971-591 Received: 17 February 2019; Accepted: 8 March 2019; Published: 15 March 2019 Abstract: A one pot-two step procedure for the synthesis of diethyl furan-2,5-dicarboxylate (DEFDC) starting from mucic acid without isolation of the intermediate furan dicarboxylic acid (FDCA) was studied. Then, the production of three different kinds of furan-based polyesters— polyethylene-2,5-furan dicarboxylate (PEF), polyhydropropyl-2,5-furan dicarboxylate(PHPF) and polydiglycerol-2,5-furandicarboxylate (PDGF)—was realized through a Co(Ac)2·4H2O catalyzed polytransesterification performed at 160 ◦C between DEFDC and a defined diol furan-based prepolymer or pure diglycerol. In parallel to polymerization process, an unattended regioselective 1-OH acylation of glycerol by direct microwave-heated FDCA diester transesterification led to the formation of a symmetric prepolymer ready for further polymerization and clearly identified by 2D NMR sequences. -
Aqueous Dehydration, Hydrogenation and Hydrodeoxygenation Reactions of Bio-Based Mucic Acid Over Ni, Nimo, Pt, Rh, and Ru on Neutral Or Acidic Catalyst Supports
Article Aqueous Dehydration, Hydrogenation and Hydrodeoxygenation Reactions of Bio-Based Mucic Acid over Ni, NiMo, Pt, Rh, and Ru on Neutral or Acidic Catalyst Supports Brigita Hočevar, Miha Grilc * and Blaž Likozar Department of Catalysis and Chemical Reaction Engineering, National Institute of Chemistry, Hajdrihova 19, Ljubljana 1000, Slovenia; [email protected] (B.H.); [email protected] (B.L.) * Correspondence: [email protected]; Tel.: +386-1-4760540 Received: 11 January 2019; Accepted: 11 March 2019; Published: 20 March 2019 Abstract: Hydrotreatment of mucic acid (also known as galactaric acid, an glucaric acid enantiomer), one of the most promising bio-based platform chemicals, was systematically investigated in aqueous media over alumina, silica, or carbon-supported transition (nickel and nickel-molybdenum) or noble (platinum, ruthenium and rhodium) metals. Mucic acid was only converted into mucic-1,4-lactone under non-catalytic reaction conditions in N2 atmosphere, while the 5 MPa gaseous H2 addition triggers hydrogenation in the bulk phase, resulting in formation of galacturonic and galactonic acid. However, dehydroxylation, hydrogenation, decarbonylation, decarboxylation, and cyclization occurred during catalytic hydrotreatment, forming various partially and completely deoxygenated products with a chain length of 3–6 C atoms. Characterization results of tested catalysts were correlated with their activity and selectivity. Insufficient pore diameter of microporous supports completely hindered the mass transfer of reactants to the active sites, resulting in negligible conversion of mucic acid. A comprehensive reaction pathway network was proposed and several industrially interesting compounds were formed, including levulinic acid, furoic acid, and adipic acid. However, selectivity towards adipic acid, a bio-based nylon 6,6 precursor, was low (up to 5 mol%) in aqueous media and elevated temperatures.