Thesis Title
Total Page:16
File Type:pdf, Size:1020Kb
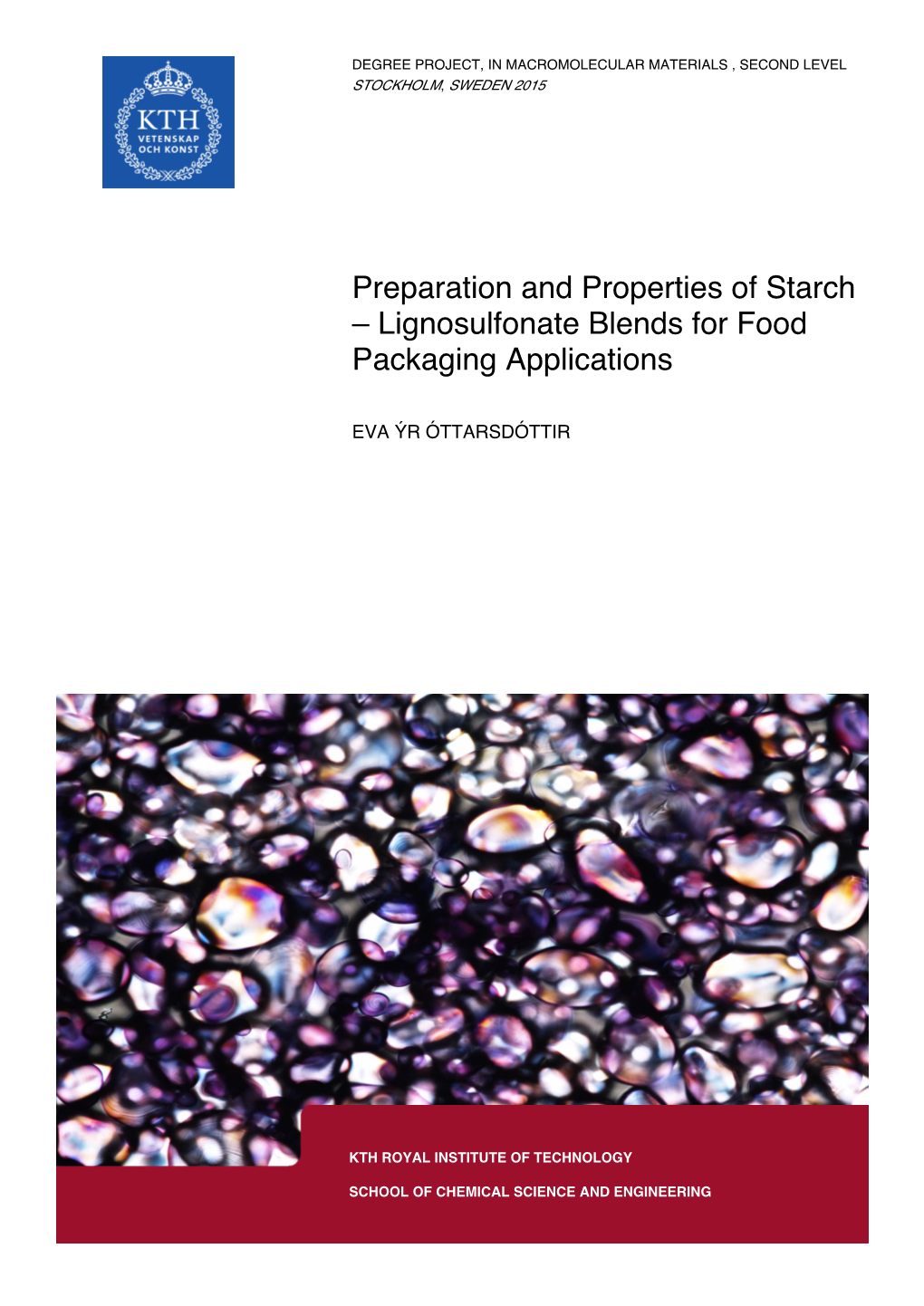
Load more
Recommended publications
-
TOPS®Pro Package Design and Pallet Software
TOPSPro Package Design and Pallet Software User’s Guide Version 6.8 July 2017 Print Version TOPS Software Corporation Copyright © 1996-2017 TOPS® Software Corporation. All rights reserved. The software described in this document is furnished under a license agreement. The software may be used or copied only in accordance with the terms of the agreement. No part of this document may be reproduced or transmitted in any form or by any means, electronic or mechanical, including photocopying and recording, for any purpose without the express written permission of TOPS® Software Corporation. Information in this document is subject to change without notice and does not represent product specification or commitment on the part of TOPS® Software Corporation. Windows is a trademark of Microsoft Corporation. Microsoft Word™ is a trademark of Microsoft Corporation. Microsoft Excel™ is a trademark of Microsoft Corporation. Microsoft Power Point™ is a trademark of Microsoft Corporation. TOPS® is a registered trademark of TOPS Software Corporation. MAXLOAD® is a registered trademark of TOPS® Software Corporation. MIXLOAD® is a registered trademark of TOPS Software Corporation. Adobe Acrobat© is a registered trademark of Adobe Systems Incorporated. TOPS® Software Corporation 1301 Central Expy South, Suite 200 Allen, Texas 75013 USA Telephone: (972) 739-8677 Facsimile: (972) 739-9478 Information: [email protected] Technical Support: [email protected] Sales: [email protected] MVP [email protected] Web Site: www.topseng.com Table of Contents Preface .........................................................................................................................ii -
Packaging, Labeling, and Shipping Requirements
0 Rev 1 Packaging, Labeling, and Shipping Requirements Commercial Lighting Packaging, Labeling, and Shipping Requirements September 2019 Racine, Wisconsin, USA LSC016 1 Rev 1 Packaging, Labeling, and Shipping Requirements Contents 1.0 Introduction ................................................................................................................................. 3 1.1 Compliance .................................................................................................................................... 3 1.2 AIAG Guidelines ............................................................................................................................. 3 2.0 Primary Container Requirements ................................................................................................. 4 2.1 Selection of a Primary Container .................................................................................................... 4 2.1.1 Container Size ......................................................................................................................... 5 2.1.2 Container Sealing .................................................................................................................... 5 3.0 Internal Part Protection Required ...................................................................................................... 5 4.0 Pallet Requirements .......................................................................................................................... 5 5.0 Unitization and Palletization -
Introduction to Corrugated Boxes
Introduction to Corrugated Boxes LASZLO HORVATH, PH.D., CPLP APRIL 23, 2020 ! Design Steps for Stacking Strength… "#$%&#%$'()*( "#$%&#%$'()*(( !"#$%&"' "+,-.'(/,+# /,+#(0)12 3 History of Corrugated Boards ! 1871 Albert Jones patented the first idea of a fluted paper ! 1874 Oliver Long suggested the creation of the single face board ! Late 1870, Machinery was developed to make corrugated board ! 1890 Another liner was added which resulted the first single wall corrugated board 4 Corrugated Board Basics 0+,'$5)1$2 Components: ! Linerboard ! Corrugating Medium ! Adhesive ! Linerboard and medium are characterized using Basis Weight 6)$$%-1#+,-(7'2+%8 Grades 92:';+<' ! Basis Weight: Weight of the board in lbs per 1000 sq. ft. = Corrugated Board Basics ! Most common medium is the 26 lbs / 1000 sq./ft. ! Basis weight grade specified board is characterized by weight and Mullen burst strength. Linerboard Grades (lbs. /1000ft2) Corrugating Medium Grades (lbs. /1000ft2) Basis Weight Burst Strength Grades (Psi) 23 26 70 26 (most common) 33 85 30 38 92 33 42 100 36 69 135 40 90 160 > Corrugated Board Basics ! Corrugated Board Types ! Corrugated Flute Types 4?!@(+,A !"#$%"&&"! !?B +,A >?43(+,A !?!@(+,A !?43(+,A @ Corrugated Board Basics Characteristics A-flute C-flute B-flute E-flute Stack Strength Best Good Fair Poor Printing Poor Fair Good Best Die Cutting Poor Fair Good Best Puncture Good Best Fair Poor Storage Space Most Fair Good Least Score/Bend Poor Fair Good Best Cushioning Best Good Fair Poor Flat Crush Poor Fair Good Good C Corrugated Board Basics ! Double wall corrugated ! Provides extra strength to the box ! Allows the utilization of the advantages of multiple board types ! BC or AB-flute board: ! B-flute side prints better ! A or C-flute side strengthens B Corrugated Board Basics ! The Corrugated Board Grade identifies the liner and medium combination. -
North American Packaging Standards and Identification Requirements for Production Parts
NORTH AMERICAN PACKAGING STANDARDS AND IDENTIFICATION REQUIREMENTS FOR PRODUCTION PARTS Control Number: 101-9999-P010 Document Date: 11-16-2017 Revision: C.11162017 Table of Contents 1. INTRODUCTION ..................................................................................................................................................................................................................................... 6 2. GENERAL REQUIREMENTS ...................................................................................................................................................................................................................... 6 2.1. ACCEPTABLE SHIPPING CONTAINERS ............................................................................................................................................................................................ 6 2.2. EFFICIENT PACKAGING ................................................................................................................................................................................................................ 6 2.3. HAZARDOUS MATERIALS TRANSPORTATION REGULATIONS ............................................................................................................................................................ 6 2.4. EXPENDABLE PACKAGING ........................................................................................................................................................................................................... -
Supplier Packaging Manual North America
Supplier Packaging Manual North America This publication applies to all AGCO suppliers (domestic or international) who ship to AGCO sites located in North America UPDATED: September 2019 Table of Contents 1 General..............................................................................................................................................................3 1.1 Packaging Manual purpose……..............................................................................................................3 2 Package Type...................................................................................................................................................3 2.1 Selection of Package Type......................................................................................................................3 2.2 Package Type for Manufacturing “Production Parts”...............................................................................3 2.3 Package Type for “Service Parts”............................................................................................................3 3 General Packaging Requirements..................................................................................................................4 3.1 Basic Protection Requirements.................................................................................................................4 3.1.1 Shock & Vibration.............................................................................................................................4 3.1.2 -
Unitizing Goods on Pallets and Slipsheets
United States Department of Agriculture Unitizing Goods on Forest Service Forest Pallets and Products Laboratory General Slipsheets Technical Report FPL-GTR-52 Abstract Acknowledgments Packaging, handling, and shipping methods and facilities The figures in this manual are adapted from a variety of have changed drastically since World War II. Today, most sources. They are as follows: products are individually packaged and then combined into unitized loads for more efficient handling, storage, and Figure shipping. The purpose of this manual is to promote the most number Based on information provided by: effective use of wood and wood fiber in current packaging 1 Forest Products Laboratory and shipping practices by providing a basic understanding of 2 A-B-C Packaging Machine Corporation the many factors involved in selecting an optimal method of 3-7 Material Handling Engineering Magazine unitizing goods on pallets and slipsheets. The manual also 8 Signode Corporation provides a valuable place of reference for the numerous 9 Mobile Chemical Company standards and specifications relating to unitizing loads. 10 Lantech Incorporated 11 CTX Products Company Keywords: Unitizing, palletizing, pallets, slipsheets, 12-13 Gloucester Engineering Company strapping, shrinkwrap, stretchwrap, netwrap, adhesives, hot 14-15 Radiant Engineering Company melts, material handling, packaging. 16-17 CTX Products Company 18 Malow Corporation and Trident Manufacturing Company 19 Presto Products Incorporated 20 MIMA Corporation 21 Lantech Corporation 22 Aktron Corporation 23-24 Bemis Company and Conwed Company 25-34 National Wood Pallet & Container Association, Virginia Polytechnic Institute and State University, and Forest Products Laboratory 35 Inca Presswood Pallets Limited 36 Elberta Crate & Box Co. 37 Menasha Corporation 38 St. -
Guide to Packaging Freight Shipments Iopp Transport Packaging Committee
Guide to Packaging Freight Shipments IoPP Transport Packaging Committee 1 Guide to Packaging Freight Shipments (IoPP Transport Packaging Committee Final — 11/27/07 (updated 8/4/14)) Scope These guidelines are voluntary and intended to assist in designing packages and other shipping units weighing 1 51 pounds or greater, that will perform satisfactorily as single entities in a domestic or international freight carrier environment. These guidelines are not to be considered approved carrier packaging specifications. Following part or all of these guidelines will not guarantee the automatic approval of a damage claim by any carrier. Terminology The following terms are specific to this guide: Performance-based: Design criteria focused on achieving a satisfactory performance to specified elements, such as degree of hazard. Shipping Unit: The complete unit that will be subjected to the distribution environment, for example a crate, box, bag, pallet, or bundle capable of movement by mechanical handling equipment. Single Package: A single shipping container, including any interior protective packaging, which provides a means of protecting and handling a product. Freight Carriers: Distribution carriers that utilize air, ocean or land to transport shipments weighing over 1 50 pounds or shipments that are unitized or palletized. Freight Shipment: A shipment tendered to a freight carrier Oversize Shipment: A shipping unit exceeding the carrier's size or weight requirements. Transport Package: A shipping unit that provides containment and protection to goods during handling, storage, and transportation. The term includes all industrial packaging and the shipping containers for consumer products. Significance and Use This guide addresses the transportation environment, which includes manual handling and the use of mechanical handling equipment. -
TMNA Packaging Workshop
Packaging Workshop February 4, 2020 / TMMTX Property of ORBIS Corporation | www.orbiscorporation.com Packaging Overview • Packaging Overview – Container selection factors – QPC optimization within target container – Parts that require custom dunnage BC 2 Property of ORBIS Corporation | www.orbiscorporation.com StakPak® System • 4 Generations in the family of StakPak® containers • 27 models / sizes • Weight capacity up to 40lbs. • Smooth internal walls for ORBIShield dunnage installation • Containers cube out standard AIAG pallets • Material: HDPE – ESD / FR / Micro Fine Cell • Manufacturing locations • Urbana, OH • Silao, Mexico • Osage City, KS 3 Property of ORBIS Corporation | www.orbiscorporation.com StakPak Systems 4 Property of ORBIS Corporation | www.orbiscorporation.com Benefits of StakPak Containers • Ergonomics/Safety • Eliminates corrugated – Sprains, strains, lacerations packaging costs • Legislation on recycling and – corrugated setup costs recyclable materials – disposal of corrugated or expendables – reduces logistics costs – packaging quality 5 Property of ORBIS Corporation | www.orbiscorporation.com StakPak Features • Drain holes in bumper and handles – prevent water from collecting in pocket areas and in bumper – allows container to dry faster after washing – saves water in washers that recycle the water • Continuous bumper – keeps dust and dirt from contaminating product inside – acts as lid for container below 6 Property of ORBIS Corporation | www.orbiscorporation.com StakPak Features (cont.) • Detached Lids • Attached -
IMO/ILO/UNECE CTU Code
IMO/ILO/UNECE Code of Practice for Packing of Cargo Transport Units (CTU Code) 2014 Table of contents Chapter 1. Introduction ..................................................................................................................... 2 Chapter 2. Definitions ....................................................................................................................... 5 Chapter 3. Key requirements ............................................................................................................ 9 Chapter 4. Chains of responsibility and information .......................................................................11 Chapter 5. General transport conditions .........................................................................................15 Chapter 6. CTU properties ..............................................................................................................17 Chapter 7. CTU suitability ...............................................................................................................22 Chapter 8. Arrival, checking and positioning of CTUs ....................................................................25 Chapter 9. Packing cargo into CTUs ..............................................................................................30 Chapter 10. Additional advice on the packing of dangerous goods .................................................32 Chapter 11. On completion of packing .............................................................................................35 -
Irvin Supplier Transport Label (STL) Templates Used on Unit Loads
Supplier Transport Label IRVIN PRODUCTS SUPPLIER TRANSPORT LABEL TEMPLATE SPECIFICATION REVISION 1, OCTOBER 22, 2019 Supplier Transport Label INTRODUCTION This standard describes the requirements for two common Irvin Supplier Transport Label (STL) templates used on unit loads. This standard does not supersede or replace any applicable safety or regulatory marking or labeling requirements. This standard is to be applied in addition to any other mandated labeling requirements. The following have been identified as the label types in use at Irvin Automotive: ● Individual container ● Master Load container Note: Mixed pallets are also allowed and require proper individual container labeling. In other words, mixed parts will require a master label for each part number on the pallets (resulting in multiple master labels). Keep like parts together. It is the responsibility of the supplier to provide bar code marked labels that meet the specifications outlined in this standard. Non-compliance with these requirements will be recorded and an Incident Report will be generated by Irvin. All associated costs for extra handling and relabeling will be supplier’s responsibility. Maximum weight (gross) of a container shall not exceed 40 lbs. (18Kg) for any returnable or non-returnable container. Maximum weight (gross) of a load unit (pallet) to be handled with a forklift or pallet jack shall not exceed 2400 lbs. (1089Kg). Container to be handled manually must fit within a standard 45” x 48” pallet. Containers must be suitable for KANBAN racks. Any specific details regarding packaging refer to standard PES-004 (Ref. IRV-SQ-ST-009). In this document, the word “shall” indicate a requirement and the word “should” indicates a recommendation. -
Vibrational Loading Mechanism of Unitized Corrugated Containers With
Bulletin 54 (Part 3 of 3 Parts) Reprinted From THE SHOCK AND VIBRATION BULLIETIN Part 3 Structural Dynamics, Machinery Dynamics and Vibration Problems JUNE 1984 A Publication of THE SHOCK AND VIBRATION INFORMATION CENTER Naval Research Laboratory, Washington, D.C. Office of The Under Secretary of Defense for Research and Engineering Approved for public release; distribution unlimited. VIBRATIONAL LOADING MECHANISM OF UNITIZED CORRUGATED CONTAINERS WITH CUSHIONS AND NON-LOAD-BEARING CONTENTS Thomas J. Urbanik, Research General Engineer Forest Products Laboratory,* Forest Service U.S. Department, of Agriculture The use of hardwood and recycled fiber will no doubt increase as specifications for corrugated fiberboard containers change from material to performance standards. This report shows another way to accelerate this use by reducing the strength requirements of containers shipped in unitized loads. The rate of container deformation with top loading and the compliance of internal packing material or cushions are newly identi fied variables governing the compression of bottom containers. Unitized containers need strength beyond the warehouse stacking requirements to support dynamic loads during shipping. The spring rates of top-loaded containers and internal cushions amplify the weight force of a unitized load during transportation. The progressive deformation with top-loading of corrugated Containers causes increasingly higher spring rates with a subsequent effect on dynamic loads. Cushions or internal packing provide a natural ability to absorb vibrations to adegree, depending on their spring rates relative to the containers'. Over-the-road shipping vibrations encompass the natural frequencies of most unitized loads and dynamically load the bottom containers. A worst case assessment calculates the maximum load on the bottom tier, expected during truck transportation. -
DUPONT™ TYVEK® AIR CARGO COVERS We Keep Your Air Freight Cool
DUPONT™ TYVEK® AIR CARGO COVERS We keep your air freight cool DuPontTM Tyvek® air cargo covers - advanced temperature protection for your pharmaceuticals, perishables and heat-sensitive products Temperature is one of the most important extraneous factors that can affect pharmaceutical and food products during transportation. Temperature excursions, often the result of long transit times, flight delay and extended time on the airport tarmac, are the nuisance of many pharmaceutical and fresh food logistics providers that do not have the correct products and procedures in place. It has been estimated that up to 5% of all transport events involve a temperature deviation from plan and, according to IATA, 57% of temperature excursions occur during these ‘uncontrolled’ air-cargo stages of the distribution process. Tyvek® covers significantly curtail the risk of temperature excursions and provide a high level of passive thermal protection from solar radiation and extreme ambient temperatures during supply chain and airport loading and unloading procedures.. We don’t take chances with your products Even the most rigorously pre–qualified shipping routes and regimes do not always perform as expected and with the introduction of mandatory temperature monitoring in many countries, it is vital that suitable precautions are in place to address all forseeable eventualities. Even the best coolchain programme can be subject to unforseen and unavoidable temperature exposures and pharma and food products are often exposed unintentionally to intense sunshine conditions for several hours. Flight delays and changes, apron congestion, human errors, ambient temperature spikes, security inspections, handling mode changes, capacity overloads, inadequate packaging, industrial action and equipment breakdowns and malfunctions can all result in temperature-sensitive merchandise being exposed for longer than is acceptable.