Grinding and Other Abrasive Processes
Total Page:16
File Type:pdf, Size:1020Kb
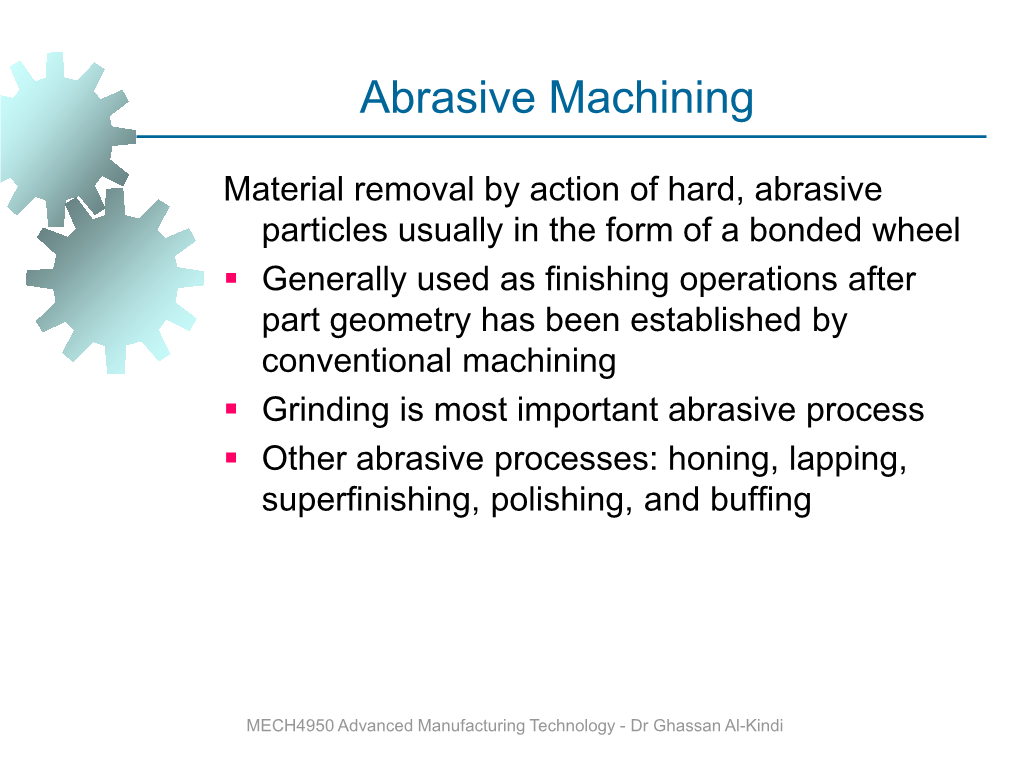
Load more
Recommended publications
-
Review of Superfinishing by the Magnetic Abrasive Finishing Process
High Speed Mach. 2017; 3:42–55 Review Article Open Access Lida Heng, Yon Jig Kim, and Sang Don Mun* Review of Superfinishing by the Magnetic Abrasive Finishing Process DOI 10.1515/hsm-2017-0004 In the conventional lapping process, loose abrasive Received May 2, 2017; accepted June 20, 2017 particles in the form of highly-concentrated slurry are of- ten used. The finishing mechanism then involves actions Abstract: Recent developments in the engineering indus- between the lapping plate, the abrasive, and the work- try have created a demand for advanced materials with su- piece, in which the abrasive particles roll freely, creating perior mechanical properties and high-quality surface fin- indentation cracks along the surface of the workpiece, ishes. Some of the conventional finishing methods such as which are then removed to finally achieve a smoother sur- lapping, grinding, honing, and polishing are now being re- face [1]. The lapping process typically is not used to change placed by non-conventional finishing processes. Magnetic the dimensional accuracy due to its very low material re- Abrasive Finishing (MAF) is a non-conventional superfin- moval rate. Grinding, on the other hand, is used to achieve ishing process in which magnetic abrasive particles inter- the surface finish and dimensional accuracy of the work- act with a magnetic field in the finishing zone to remove piece simultaneously [2]. In grinding, fixed abrasives are materials to achieve very high surface finishing and de- used by bonding them on paper or a plate for fast stock burring simultaneously. In this review paper, the working removal. -
Lapping Plate
Lapping Plate 05M20.20 Patent Pending Lapping is the process of rubbing two surfaces together with an abrasive and a lubricant to improve the quality of at least one of the surfaces. Although lapping can be used to create fl at surfaces, in the context of woodworking, lapping better serves to minimize the roughness of a surface – known as surface conditioning. By minimizing the roughness in the sole of a plane, there is reduced friction between the plane and the workpiece, which in turn reduces abrasion. For blades or chisels, the cutting edge can be made sharper if both intersecting surfaces are free of scratches, even if the back of the blade isn’t perfectly fl at. Straight cutting edge on a lapped blade. Jagged cutting edge on a ground blade. Figure 1: A ground blade versus a lapped blade. Lapping can remove only small amounts of material. If the sole of your plane or the back of your blade is twisted, wavy or bowed, it will be necessary to sand or grind off the high points prior to lapping. Lapping is always performed with an abrasive oil slurry, which not only allows the object to slide Small Abrasive about the lapping plate (called a lap), but also Particles provides a means to remove abraded particles and worn abrasive. Oil Object Abraded Metal Lap Groove in Lap Large Abrasive Particles Figure 2: Lapping mechanics. 2 Important Notes The lapping plate is made of soft iron and will wear over time. These instructions provide information on how to ensure the lap remains fl at for a lifetime. -
Grinding and Honing. Part 2 INFO 20M Information for Ship and Tool-Lovers
Foto: Henk Bos Grinding and honing. Part 2 INFO 20M Information for ship and tool-lovers Info 20M Number 66e Version 1.1 Mai - June 2012 INFO 20M Information paper great pleasure boats and toollovers The paper "great pleasure boats" is meant for owners, skippers and other interested parties of recreational vessels over 20 meters such as: - Former inland vessels - Former Marine vessels - Former fishing vessels - Former Navy ships - Former tugs and pushboats - Houseboats - Recreational vessels specifically built for that purpose. The magazine INFO-20M "great pleasure boats" provides this target group with information about nautical law and the (technical) equipment on board the ship. ISSN: 1872-7824 Initiative: Henk Bos Cover Photo: Henk Bos Design: Henk Bos Correctors: Ge Bos-Thoma, Henk Bos and Janneke Bos In this issue: Henk Bos (HB), Janneke Bos (JB), Rob, Piet, Oldengaerde and Neil Miller English translation: Ge Bos-Thoma. Production and Publishing: Henk en Janneke Bos (Expertisebureau Bos) (c) 2006-2012 Website: http://www.xs4all.nl/~bosq Hasebroekstraat 7, 1962 SV Heemskerk, Tel: 0251-230 050, e-mail: [email protected] Distribution: 20M info is distributed by email free of charge by the following organizations: - The National Association for the Preservation of the Historic Vessel (LVBHB) - Foundation for the preservation of Authentic Steam and Motor Vessels and Tugs (BASM) - Royal Dutch Motorboat Club (KNMC) - The Association Motor Tug (VDMS) and the Association of the Tugboat (VDS) - The Flemish Association for Water Sports (VVW) - Zeekadetkorps Netherlands (ZKK) - Scouting Netherlands (SN) Other organizations may contact the publisher. Info 20M can also be downloaded through the website. -
Hand-Forging and Wrought-Iron Ornamental Work
This is a digital copy of a book that was preserved for generations on library shelves before it was carefully scanned by Google as part of a project to make the world’s books discoverable online. It has survived long enough for the copyright to expire and the book to enter the public domain. A public domain book is one that was never subject to copyright or whose legal copyright term has expired. Whether a book is in the public domain may vary country to country. Public domain books are our gateways to the past, representing a wealth of history, culture and knowledge that’s often difficult to discover. Marks, notations and other marginalia present in the original volume will appear in this file - a reminder of this book’s long journey from the publisher to a library and finally to you. Usage guidelines Google is proud to partner with libraries to digitize public domain materials and make them widely accessible. Public domain books belong to the public and we are merely their custodians. Nevertheless, this work is expensive, so in order to keep providing this resource, we have taken steps to prevent abuse by commercial parties, including placing technical restrictions on automated querying. We also ask that you: + Make non-commercial use of the files We designed Google Book Search for use by individuals, and we request that you use these files for personal, non-commercial purposes. + Refrain from automated querying Do not send automated queries of any sort to Google’s system: If you are conducting research on machine translation, optical character recognition or other areas where access to a large amount of text is helpful, please contact us. -
The Art of Superfinishing
The Superfinishing Experts™ Corporate Headquarters Darmann Abrasive Products, Inc. 100 Sterling Street Clinton, MA 01510 Phone: 978-365-4544 Fax: 800-736-3839 Darmann Eastern Europe, LLC Przemyslowa 1 Street 41-300 Dabrowa Gorniza Poland Phone: +48 608 079 027 Darmann Abrasive Products, Inc. 1F, Building 36 458 North Fu Te Road Shanghai Waigaoqiao F.T.Z 200131 China Phone: +86 (21) 586 2809 www.darmann.com The Art of Superfinishing. About Us. The Superfinishing Process. Darmann Abrasive Products, Inc. has been designing and manu- Superfinishing, sometimes called micromachining or facturing fine grit, bonded abrasive products for superfinishing short-stroke honing, was invented in 1934 by Chrysler and precision grinding applications since 1983. Innovation, Corporation. However, it took about 40 years before gaining combined with superior engineering and unsurpassed customer widespread acceptance. service has made us a world-wide leader in the field. We have During grinding, extreme heat and aggressive stock developed a unique value proposition which we removal often alters micro structure and base metal hardness. call The Darmann Advantage. This creates slight dimensional and surface imperfections such as smeared peaks, waviness and chatter. The Darmann Advantage. Superfinishing, a low temperature, low stock removal • Darmann Is The Market Leader – process, improves part geometry and surface finish by removing No one sells more superfinishing tools than the amorphous layer formed during the grinding process. Darmann. We provide the broadest range This dramatically improves these imperfections, which can of conventional abrasive types, hardness, compromise part quality and performance. engineered structures, bond options, part geometries, packaging and printing. We’ve Superfinishing Benefits. -
MACHINISTGRINDER (Duration: Two Years)
GOVERNMENT OF INDIA MINISTRY OF SKILL DEVELOPMENT & ENTREPRENEURSHIP DIRECTORATE GENERAL OF TRAINING COMPETENCY BASED CURRICULUM MACHINISTGRINDER (Duration: Two years) CRAFTSMEN TRAINING SCHEME (CTS) NSQF LEVEL- 5 SECTOR –CAPITAL GOODS AND MANUFACTURING MACHINIST GRINDER (Engineering Trade) (Revised in 2019) Version: 1.2 CRAFTSMEN TRAINING SCHEME (CTS) NSQF LEVEL - 5 Developed By Ministry of Skill Development and Entrepreneurship Directorate General of Training CENTRAL STAFF TRAINING AND RESEARCH INSTITUTE EN-81, Sector-V, Salt Lake City, Kolkata – 700 091 www.cstaricalcutta.gov.in CONTENTS S No. Topics Page No. 1. Course Information 1 2. Training System 3 3. Job Role 7 4. General Information 10 5. Learning Outcome 13 6. Assessment Criteria 15 7. Trade Syllabus 23 Annexure I(List of Trade Tools & Equipment) 40 Annexure II (List of Trade experts) 46 Machinist Grinder 1. COURSE INFORMATION During the two-year duration, a candidate of Machinist Grindertrade is trained on subjects Professional Skill, Professional Knowledge, Engineering Drawing, Workshop Science & Calculation and Employability Skills related to job role. In addition to this, a candidate is entrusted to make/do project work and Extra Curricular Activities to build up confidence. The practical skills are imparted in simple to complex manner & simultaneously theory subject is taught in the same fashion to apply cognitive knowledge while executing task.The course covers the detail aspect of Machinist (Grinder). The broad components covered under Professional Skill subject are as below: FIRST YEAR: The practical part starts with basic fitting covering components like filing, sawing, drilling, tapping, chipping, grinding and different fits. The accuracy proposed is of ±0.2mm and angular accuracy of 1°. -
Lapping Kit Lappin
Lapping Kit 05M01.01Lapping Kit 05M01.01 Contents Contents Five 2-ounce containers of 90x, 180x, 280x, 400x and 600x silicon Five 2-ounce containers of 90x, 180x, 280x, 400x and 600x silicon carbide particles. carbide particles. Background Background Lapping is the process of rubbing two surfaces together with an abrasive Lapping is the process of rubbing two surfaces together with an abrasive and a lubricant to improve the quality of at least one of the surfaces. and a lubricant to improve the quality of at least one of the surfaces. Lapping can be used for fl attening (or truing) a surface, such as a worn Lapping can be used for fl attening (or truing) a surface, such as a worn sharpening stone. Lapping can also minimize the roughness of a surface sharpening stone. Lapping can also minimize the roughness of a surface (i.e., surface conditioning), such as a plane sole or blade. By minimizing (i.e., surface conditioning), such as a plane sole or blade. By minimizing the roughness in the sole of a plane, there is reduced friction between the the roughness in the sole of a plane, there is reduced friction between the plane and the workpiece, which in turn reduces abrasion. For blades or plane and the workpiece, which in turn reduces abrasion. For blades or chisels, the cutting edge can be made sharper if both intersecting surfaces chisels, the cutting edge can be made sharper if both intersecting surfaces are free of scratches. are free of scratches. Choosing an Abrasive Choosing an Abrasive Although any grit will provide adequate results for any application, each is Although any grit will provide adequate results for any application, each is best suited to a particular application. -
Super Finishing Strips.Pdf
DIAMOND STRIPS FINISHING / POLISHING Super finishing INDUSTRY Pulp, paper, printing, hot rolling mills, oil, gas, mining, drilling, water engineering, earthmoving equipment. MAIN APPLICATIONS The actual goal through the super finishing operation is to achieve a surface that is as smooth as possible, so that the following advantages can be achieved: wear resistance, frictional resistance, fouling resistance and fatigue resistance. Superfinishing systems are commonly used for optimising surfaces of rolls and other cylindrical parts. Long super-abrasive strips (with tails) are used for polishing and finishing hard brittle materials such as thermal sprayed coatings like HVOF sprayed carbides and ceramics. KGS flexible diamond tools are used on super-finishing machines for roll finishing of very hard materials like tungsten carbide, ceramics, thermal spray, epoxy and special alloys. This process in mainly used for precision engineering applications, ensuring improved operations and a longer product life. Your future benefits are: High tolerance of material, Less maintanance, Less replacement costs / investments. This system provides predictable, consistent (over the entire surface) and repeatable finishes. It improves the surface structure which can easily be compared to levels reached by honing or lapping. Another important advantage is the ability to achieve the desired surface texture. From a highly reflective finish and low Ra value, to a specific surface roughness for friction grip and/or ink, water or oil retention. During the constant use of these rolls, they tend to lose this surface roughness and become “polished” over time. In this way rolls can be refurbished many times before fully being stripped and recoated. Also, another advantage is the removal of chatter marks, feed marks and other imperfections left by (previous) grinding operations. -
Manufacture Engineers, Part B
CORE Metadata, citation and similar papers at core.ac.uk Provided by Cranfield CERES Proceedings of the Institution of Mechanical Engineers, Part B: Journal of Engineering Manufacture http://pib.sagepub.com/ Electrolytic In-Process Dressing Superfinishing of Spherical Bearings Using Metal−−Resin Bond Ultra-Fine CBN Wheels M H Raffles, D J Stephenson, P Shore and T Jin Proceedings of the Institution of Mechanical Engineers, Part B: Journal of Engineering Manufacture 2011 225: 112 DOI: 10.1243/09544054JEM2003 The online version of this article can be found at: http://pib.sagepub.com/content/225/1/112 Published by: http://www.sagepublications.com On behalf of: Institution of Mechanical Engineers Additional services and information for Proceedings of the Institution of Mechanical Engineers, Part B: Journal of Engineering Manufacture can be found at: Email Alerts: http://pib.sagepub.com/cgi/alerts Subscriptions: http://pib.sagepub.com/subscriptions Reprints: http://www.sagepub.com/journalsReprints.nav Permissions: http://www.sagepub.com/journalsPermissions.nav Citations: http://pib.sagepub.com/content/225/1/112.refs.html Downloaded from pib.sagepub.com at CRANFIELD UNIV INFO & LIB SVC on May 4, 2011 112 SPECIAL ISSUE PAPER Electrolytic in-process dressing superfinishing of spherical bearings using metal–resin bond ultra-fine CBN wheels M H Raffles, D J Stephenson*, P Shore, and T Jin Cranfield University, Cranfield, UK The manuscript was received on 28 January 2010 and was accepted after revision for publication on 19 July 2010. DOI: 10.1243/09544054JEM2003 Abstract: The use of electrolytic in-process dressing (ELID) superfinishing has been investi- gated with the aim of substantially improving surface finish on spherical bearing balls as well as reducing process times. -
Lesson 6 - GRINDING and OTHER ABRASIVE PROCESSES Abrasive Machining
Lesson 6 - GRINDING AND OTHER ABRASIVE PROCESSES Abrasive Machining Material removal by action of hard, abrasive particles usually in the form of a bonded wheel • Generally used as finishing operations after part geometry has been established by conventional machining • Grinding is most important abrasive process • Other abrasive processes: honing, lapping, superfinishing, polishing, and buffing 2002©John Wiley & Sons, Inc. M. P. Groover, “Fundamentals of Modern Manufacturing 2/e” Why Abrasive Processes are Important • Can be used on all types of materials • Some can produce extremely fine surface finishes, to 0.025µm (1 -in) • Some can hold dimensions to extremely close tolerances 휇 2002©John Wiley & Sons, Inc. M. P. Groover, “Fundamentals of Modern Manufacturing 2/e” Grinding Material removal process in which abrasive particles are contained in a bonded grinding wheel that operates at very high surface speeds Grinding wheel • Grinding wheel are usually disk-shaped and Rotation precisely balanced for high rotational speeds • Grinding process involves abrasives which remove small amounts of material from a surface Small chips through a cutting process that produces tiny chips Workpiece https://www.youtube.com/watch?v=nNDIm8eLrQ8 2002©John Wiley & Sons, Inc. M. P. Groover, “Fundamentals of Modern Manufacturing 2/e” Grinding • Grinding is a chip-removal process that uses an individual abrasive grain as the cutting tool Copyright © 2010 Pearson Education South Asia Pte Ltd Grinding • Grinding applications include: 1. Finishing of ceramics and glasses 2. Cutting off lengths of bars, structural shapes, masonry and concrete 3. Removing unwanted weld beads and spatter 4. Cleaning surfaces with jets of air or water containing abrasive particles. -
AGREEMENT Between
AGREEMENT between MILLWRIGHTS LOCAL UNION 1121 of the EASTERN MILLWRIGHT REGIONAL COUNCIL UNITED BROTHERHOOD OF CARPENTERS AND JOINERS OF AMERICA, and LABOR RELATIONS DIVISION OF THE ASSOCIATED GENERAL CONTRACTORS OF MASSACHUSETTS, INC. and BUILDING TRADES EMPLOYERS' ASSOCIATION OF BOSTON AND EASTERN MASSACHUSETTS, INC. and CONNECTICUT CONSTRUCTION INDUSTRIES ASSOCIATION, INC. and AGC/CCIA BUILDING CONTRACTORS LABOR DIVISION OF CONNECTICUT, INC. EFFECTIVE: OCTOBER 1, 2015 THROUGH SEPTEMBER 30,2019 Expires September 30, 2019 Eastern Millwright Regional Council UNITED BROTHERHOOD OF CARPENTERS AND JOINERS OF AMERICA, EASTERN MILLWRIGHT REGIONAL COUNCIL MILLWRIGHTS LOCAL UNION 1121 ROBERT LOUBIER, Executive Secretary Treasurer 1661 Worcester Road, Suite 302 Framingham, Massachusetts 01701-5402 Phone 617-254-1655 Fax 617-783-5554 LABOR RELATIONS DIVISION OF THE ASSOCIATED GENERAL CONTRACTORS OF MASSACHUSETTS, INC. BRIAN O'DONNELL, Director of Labor Relations 888 Worcester Street - #40 Wellesley, Massachusetts 02482-3793 Phone 781-235-2680 Fax 781-235-6020 BUILDING TRADES EMPLOYERS' ASSOCIATION OF BOSTON AND EASTERN MASSACHUSETTS, INC. THOMAS J GUNNING, Executive Director 150 Grossman Drive, Suite 313 Braintree, Massachusetts 02184 Phone 781-431-7440 Fax 781-235-6020 CONNECTICUT CONSTRUCTION INDUSTRIES ASSOCIATION, INC. DONALD SHUBERT, President 912 Silas Deane Highway Wethersfield, CT 06109 Phone 860-529-6855 Fax 860-563-0616 AGCICCIA BUILDING CONTRACTORS LABOR DIVISION OF CONNECTICUT, INC. DONALD SHUBERT, President 912 Silas Deane Highway -
Compoforging of Al-Si Metal Matrix Composites Reinforced with -Sic: an Alternative Technique
The Open Industrial & Manufacturing Engineering Journal, 2010, 3, 1-6 1 Open Access Compoforging of Al-Si Metal Matrix Composites Reinforced with -SiC: An Alternative Technique M. F. Valencia García1,*, H. V. Martínez2 and A. Morales Ortiz2 1Escuela de Ingeniería de Antioquia; Grupo Productividad hacia la Competitividad GPC – A.A. 7516 Medellín, Colombia 2Universidad Pontificia Bolivariana; Facultad de Ingeniería Mecánica. Grupo de Investigación sobre Nuevos Materiales GINUMA – A.A. 56006 Medellín, Colombia Abstract: This paper reports the -SiC particles surface modification by copper Electroless Plating (EP), as well as a morphological characterization of Al-Si reinforced composite obtained with such modified particles and consolidated by compoforging. The -SiC particles were obtained by thermal degradation of organic waste. The compoforging technique is a hybrid between the compocasting process and semi-solid forging. The properties of the obtained composite material derive from its globular structure, which is achieved by mixing the semi-solid alloy and the reinforcing particles. This method produced an almost perfect distribution of the reinforce particles. Furthermore, it is possible to achieve minimum defects (i.e. porosity) by applying pressures up to 60MPa. Keywords: Silicon carbide, electroless plating, superficial modification, mechanical mixing, compoforging. INTRODUCTION Table 1. Process Conditions for -SiC Synthesis About 35 years ago, semi-solid metallurgy, or semi-solid processing of alloys (SSM and SSP, respectively), was origi- Variable Value Unit nated. This technology combines the advantages of tradi- o tional forging and foundry processes. Nowadays such tech- Process temperature 1370 C nology and the development of Metal Matrix Composites Atmosphere process 1.5 L/min (MMC’s) have been strong, combining dispersion process to obtain Particulate reinforced Metal Matrix Composites Processing times 40 min (PRMCs).