Automation Pyramid As Constructor for a Complete Digital Twin, Case Study: a Didactic Manufacturing System
Total Page:16
File Type:pdf, Size:1020Kb
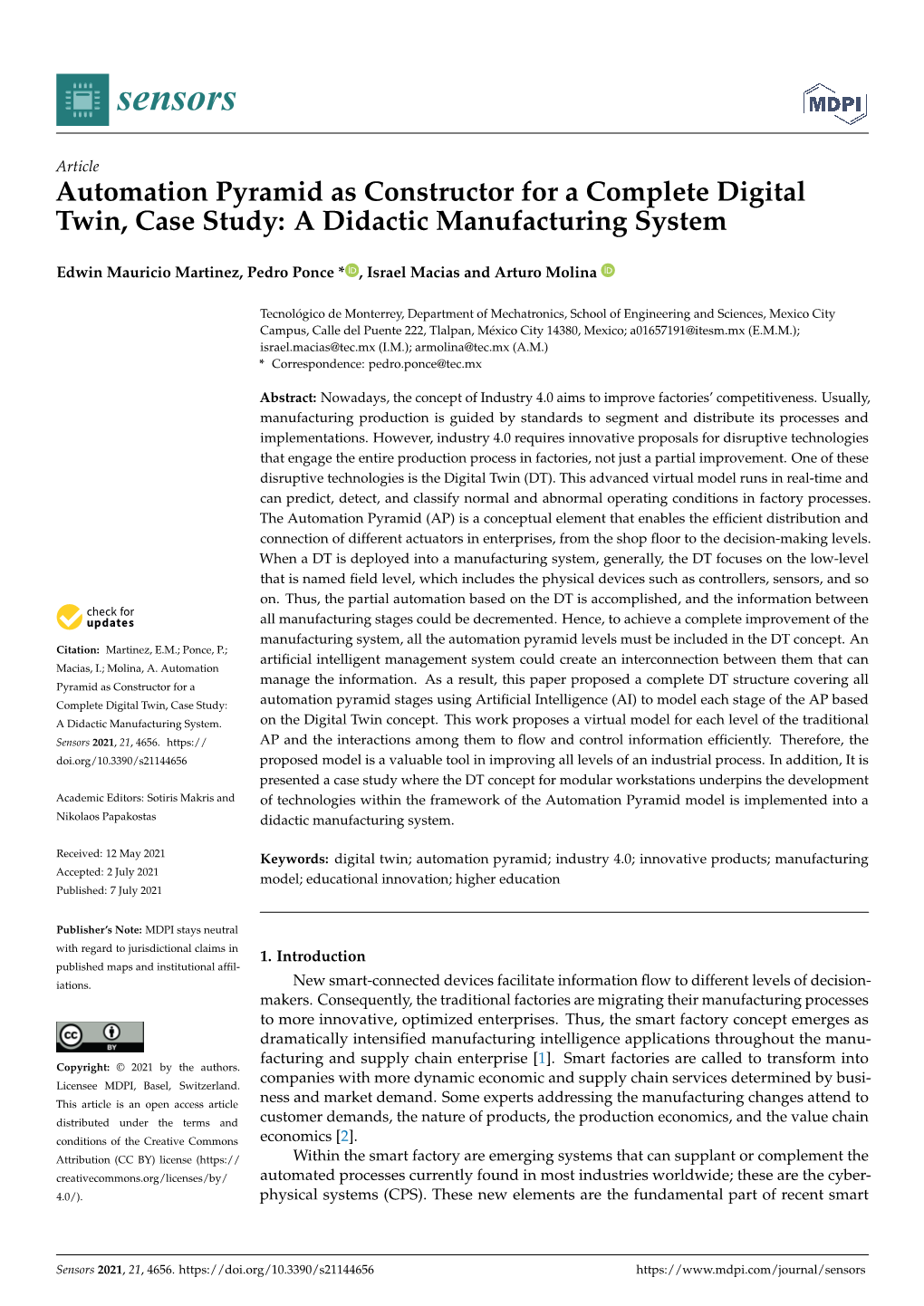
Load more
Recommended publications
-
Lean Manufacturing in a High Containment Environment
IPT 32 2009 11/3/10 15:48 Page 74 Manufacturing Lean Manufacturing in a High Containment Environment By Georg Bernhard A case study of how Pfizer’s Right First Time strategy helped overcome at Pfizer Global daunting capacity challenges at its new large-scale containment facility Manufacturing at Illertissen, Germany, while Six Sigma and Lean strategies enabled the site to achieve previously unknown levels of efficiency. In late 2006, Pfizer launched its smoking cessation film-coated tablets. All of the process stages (granulation, product varenicline, known as Chantix® in the US tableting and coating) are controlled and monitored from and Champix® across Europe. According to IMS a separate control room so that employees do not come benchmarks, Champix® was the fastest product launch in into contact with dust that might be generated during the the European pharmaceutical industry, with marketing tablet production run. Transport is handled by automated, in 16 European countries in a five-month period. As well and entirely robotic, laser-guided vehicles. Operators as creating rapid and unprecedented consumer demand, monitor and control all containment room activities from the product launch also brought capacity challenges for a separate control room. Pfizer Inc’s small-scale IllertissenCONtainment (ICON) facility in Illertissen, Germany. The facility’s innovative IT systems integration enabled an extraordinary 85 per cent level of automation (LoA), A strategic site in Pfizer’s global manufacturing network, outstripping even the ICON facility’s extremely high 76 per Illertissen is focused on oral solid dosage forms and is a cent LoA. Thus, in NEWCON, all process sequences centre of excellence in containment production. -
Automationml 2.0 (CAEX 2.15)
Application Recommendation Provisioning for MES and ERP – Support for IEC 62264 and B2MML Release Date: November 7, 2018 ID: AR-MES-ERP Version: 1.1.0 Compatibility: AutomationML 2.0 (CAEX 2.15) Provisioning for MES and ERP Author: Bernhard Wally [email protected] Business Informatics Group, CDL-MINT, TU Wien AR-MES-ERP 1.1.0 2 Provisioning for MES and ERP Table of Content Table of Content .............................................................................................................................................. 3 List of Figures .................................................................................................................................................. 6 List of Tables .................................................................................................................................................... 7 List of Code Listings ..................................................................................................................................... 11 Provided Libraries .................................................................................................................. 12 I.1 Role Class Libraries ............................................................................................................................ 12 I.2 Interface Class Libraries ..................................................................................................................... 12 Referenced Libraries ............................................................................................................. -
Understanding and Minimizing Your HMI/SCADA System Security Gaps
GE Digital Understanding and Minimizing Your HMI/SCADA System Security Gaps INTRODUCTION With HMI/SCADA systems advancing SCADA security in context technologically and implementations The International Society of Automation (ISA) production Being at the heart of an operation’s data becoming increasingly complex, some model demonstrates the layered structure of a typical visualization, control and reporting for industry standards have emerged with the operation, and shows that HMI/SCADA security is only one operational improvements, HMI/SCADA goal of improving security. However, part of part of an effective cyber-security strategy. These layers systems have received a great deal the challenge is knowing where to start in of automated solution suites share data, and wherever of attention, especially due to various data is shared between devices, there is a possibility for securing the entire system. unauthorized access and manipulation of that data. This cyber threats and other media-fueled The purpose of this paper is to explain where white paper concentrates on the HMI/SCADA layer, but vulnerabilities. The focus on HMI/SCADA vulnerabilities within a HMI/SCADA system unless other potential weaknesses at other levels are security has grown exponentially, and as a may lie, describe how the inherent security of covered, the operation as a whole remains vulnerable. result, users of HMI/SCADA systems across system designs minimize some risks, outline the globe are increasingly taking steps to some proactive steps businesses can take, protect this key element of their operations. and highlight several software capabilities The HMI/SCADA market has been that companies can leverage to further evolving with functionality, scalability and enhance their security. -
Integration of Sensor and Actuator Networks and the SCADA System to Promote the Migration of the Legacy Flexible Manufacturing System Towards the Industry 4.0 Concept
Journal of Sensor and Actuator Networks Article Integration of Sensor and Actuator Networks and the SCADA System to Promote the Migration of the Legacy Flexible Manufacturing System towards the Industry 4.0 Concept Antonio José Calderón Godoy ID and Isaías González Pérez * ID Department of Electrical Engineering, Electronics and Automation, University of Extremadura, Avenida de Elvas, s/n, 06006 Badajoz, Spain; [email protected] * Correspondence: [email protected]; Tel.: +34-924-289-600 Received: 16 April 2018; Accepted: 17 May 2018; Published: 21 May 2018 Abstract: Networks of sensors and actuators in automated manufacturing processes are implemented using industrial fieldbuses, where automation units and supervisory systems are also connected to exchange operational information. In the context of the incoming fourth industrial revolution, called Industry 4.0, the management of legacy facilities is a paramount issue to deal with. This paper presents a solution to enhance the connectivity of a legacy Flexible Manufacturing System, which constitutes the first step in the adoption of the Industry 4.0 concept. Such a system includes the fieldbus PROcess FIeld BUS (PROFIBUS) around which sensors, actuators, and controllers are interconnected. In order to establish effective communication between the sensors and actuators network and a supervisory system, a hardware and software approach including Ethernet connectivity is implemented. This work is envisioned to contribute to the migration of legacy systems towards the challenging Industry 4.0 framework. The experimental results prove the proper operation of the FMS and the feasibility of the proposal. Keywords: sensor and actuator network; fieldbuses; industrial communications; Ethernet; flexible manufacturing system; programmable logic controllers (PLC); supervisory control and data acquisition (SCADA); Industry 4.0; Industrial Internet of Things (IIoT) 1. -
Implementation of Lean Six Sigma Methodology on a Wine Bottling Line
MASTER THESIS The implementation of Lean Six Sigma methodology in the wine sector: an analysis of a wine bottling line in Trentino Master Thesis in Industrial Engineering by Sergio De Gracia Directed by Prof. Roberta Raffaelli Academic Year 2013-2014 Table of Contents Abstract ......................................................................................................................................... 9 Acknowledgements ..................................................................................................................... 10 Introduction ................................................................................................................................ 11 Lean Manufacturing .................................................................................................................... 14 1. Lean Manufacturing ................................................................................................................ 14 1.1. TPS in Lean Manufacturing.......................................................................................... 15 1.2. Types of waste and value added ................................................................................. 16 1.2.1. Value Stream Mapping (VSM) ................................................................................... 18 1.3. Continual Improvement process and KAIZEN ............................................................. 19 1.4. Lean Thinking ............................................................................................................. -
Manufacturing Execution Systems (MES)
Manufacturing Execution Systems (MES) Industry specific Requirements and Solutions ZVEI - German Electrical and Electronic Manufactures‘ Association Automation Division Lyoner Strasse 9 60528 Frankfurt am Main Germany Phone: + 49 (0)69 6302-292 Fax: + 49 (0)69 6302-319 E-mail: [email protected] www.zvei.org ISBN: 978-3-939265-23-8 CONTENTS Introduction and objectives IIIIIIIIIIIIIIIIIIIIIIIIIIIIIIIIIIIIIIIIIIIIIIIIIIIIIIIIIIIIIIIII5 1. Market requirements and reasons for using MES IIIIIIIIIIIIIIIIIIIIIIIIIIIIIIIIIIIIII6 2. MES and normative standards (VDI 5600 / IEC 62264) IIIIIIIIIIIIIIIIIIIIIIIIIIIIIIIII8 3. Classification of the process model according to IEC 62264 IIIIIIIIIIIIIIIIIIIIIIIIII 12 3.1 Resource Management IIIIIIIIIIIIIIIIIIIIIIIIIIIIIIIIIIIIIIIIIIIIIIIIIIIIIIIIIIIIIII13 3.2 Definition Management IIIIIIIIIIIIIIIIIIIIIIIIIIIIIIIIIIIIIIIIIIIIIIIIIIIIIIIIIIIIII14 3.3 Detailed Scheduling IIIIIIIIIIIIIIIIIIIIIIIIIIIIIIIIIIIIIIIIIIIIIIIIIIIIIIIIIIIIIIIII14 3.4 Dispatching IIIIIIIIIIIIIIIIIIIIIIIIIIIIIIIIIIIIIIIIIIIIIIIIIIIIIIIIIIIIIIIIIIIIIIIII15 3.5 Execution Management IIIIIIIIIIIIIIIIIIIIIIIIIIIIIIIIIIIIIIIIIIIIIIIIIIIIIIIIIIIIII15 3.6 Data Collection IIIIIIIIIIIIIIIIIIIIIIIIIIIIIIIIIIIIIIIIIIIIIIIIIIIIIIIIIIIIIIIIIIIIII16 IMPRINT 3.7 Tracking IIIIIIIIIIIIIIIIIIIIIIIIIIIIIIIIIIIIIIIIIIIIIIIIIIIIIIIIIIIIIIIIIIIIIIIIIIII16 3.8 Analysis IIIIIIIIIIIIIIIIIIIIIIIIIIIIIIIIIIIIIIIIIIIIIIIIIIIIIIIIIIIIIIIIIIIIIIIIIIIII17 Manufacturing Execution Systems (MES) 4. Typical MES modules and related terms IIIIIIIIIIIIIIIIIIIIIIIIIIIIIIIIIIIIIIIIIIIIIIIIII18 -
JANNE HARJU PLANT INFORMATION MODELS for OPC UA: CASE COPPER REFINERY Master of Science Thesis
JANNE HARJU PLANT INFORMATION MODELS FOR OPC UA: CASE COPPER REFINERY Master of Science Thesis Examiner: Hannu Koivisto Examiner and topic approved in the Council meeting of Depart of Auto- mation Science and Engineering on 5.11.2014 i i TIIVISTELMÄ TAMPEREEN TEKNILLINEN YLIOPISTO Automaatiotekniikan koulutusohjelma HARJU, JANNE: PLANT INFORMATION MODELS FOR OPC UA: CASE COPPER REFINERY Diplomityö, 59 sivua Tammikuu 2015 Pääaine: Automaatio- ja informaatioverkot Tarkastaja: Professori Hannu Koivisto Avainsanat: OPC, UA, ISA-95, CAEX, mallinnus, ADI Isojen laitosten informaation rakenne on usein hankala ihmisen hahmottaa silloin, kun kaikki tieto on yhdessä listassa. Jotta laitoksen informaatiosta saadaan parempi koko- naiskuva, tarvitsee se mallintaa jollakin tekniikalla. Kun laitoksen mallintaa hierarkki- sesti, pystyy sen rakenteen hahmottamaan helpommin. Lisäksi, kun malliin saadaan tuotua mittaussignaaleja ja muuta mittauksiin ja muihin arvoihin liittyvää dataa, saadaan se tehokkaaseen käyttöön. Nykyään paljon käytetty klassinen OPC tuo datan käytettäväksi ylemmille lai- toksen tasoille. OPC tuo mittaukset pelkkänä listana, eikä se tuo mittausten välille mi- tään metatietoa. Tässä työssä on tarkoitus tutkia, miten mallintaa esimerkki laitokset käyttäen klassisen OPC:n seuraajaa OPC UA:ta. Työn tavoitteena on tutkia eri OPC UA:n mallinnustyökaluja, menetelmiä ja itse mallinnusta. Työssä tutustutaan OPC UA:n lisäksi ISA-95:n ja sen OPC UA- malliin ja miten tätä mallia pystyy käyttämään oikean laitoksen mallinnuksessa hyödyksi. ISA-95 lisäksi tutustutaan toiseen malliin nimeltä CAEX. CAEX on alun perin suunniteltu suunnitteludatan tallentamiseen stan- dardoidulla tavalla. CAEX:sta on olemassa myös tutkimuksia OPC UA:n kanssa käytet- täväksi ja tässä työssä tutustutaan, onko mallinnettavien tehtaiden kanssa mahdollista käyttää CAEX:ia hyödyksi. Virallista OPC UA CAEX- mallia ei ole vielä tosin julkais- tu. -
INDUSTRY4.0 TECHNOLOGY BATTLES in MANUFACTURING OPERATIONS MANAGEMENT Non-Technical Dominance Factors for Iiot & MES
INDUSTRY4.0 TECHNOLOGY BATTLES IN MANUFACTURING OPERATIONS MANAGEMENT non-technical dominance factors for IIoT & MES Master thesis submitted to Delft University of Technology in partial fulfilment of the requirements for the degree of MASTER OF SCIENCE in Management of Technology Faculty of Technology, Policy and Management by ing. Aksel de Vries #1293087 To be defended in public on 09 February 2021. Graduation committee: Chair & First Supervisor: Prof.dr.ir. M.F.W.H.A. Janssen, ICT Second Supervisor: Dr. G. (Geerten) van de Kaa, ET&I Equinoxia Industrial Automation Impressum The cover photo shows the Djoser step pyramid. It was once high-tech and replaced old-school pyramid technology; the ruin in the front. The analogy is to the once high-tech Automation Pyramid: Figure 1: Automation Pyramid as advocated by MESA.org and ISA.org since 1986 A.D. About the author Aksel de Vries (1973) is a Chemical Process Engineer and has been work- ing in the field of Manufacturing Operations Management since 1998. At AspenTech Europe, Aksel delivered training and consultancy during the transition from Computer Integrated Manufacturing (CIM/21, Batch/21, SetCIM, etc.) to Industry4.0 on corporate vertical and horizontal inte- gration, fully leveraging ISA-88 and ISA-95. Aksel works as independent consultant www.equinoxia.eu since 2006 mainly in Biotech Pharma4.0 for System Integrators like Zenith Tech- nologies (now Cognizant) and blue-chip corporations such as DSM, GSK, BioNTech, Kite Pharma / Gilead Sciences, Amgen, Lonza, etc. Copyright © 2021 Equinoxia Industrial Automation, The Netherlands Aksel de Vries EXECUTIVE SUMMARY In 2011, the fourth industrial revolution was announced at the German Hannover Messe. -
The Role of Manufacturing Execution Systems (Mes) in Erp Selection
IFS EXECUTIVE SUMMARY THE ROLE OF MANUFACTURING EXECUTION SYSTEMS (MES) IN ERP SELECTION Enterprise resource planning (ERP) software is well-understood by most mid-level and senior managers. Fewer understand at a high level manufacturing execution systems (MES). MES is hard to define to begin with because it is an intermediary technology between process automation equipment on the plant floor and ERP software. So let’s define some terms and drive clarity on what MES is, who needs it and how IFS meets the needs of companies who want ERP software with the functional benefits of MES. Common definitions of MES suggest that it: • Tracks and documents the transformation of raw materials into finished goods • Provides information to help business decision-makers understand real-time conditions in their plant to support optimization of operations • Enables control of inputs, personnel, machines and support services APICS, the association for operations management, defines MES as involving: • Direct and supervisory control of equipment • Graphical displays showing what is going on in the plant currently • Gathering quality information, material transactions and traceability information through integration with the production equipment used Most of these needs are satisfied by IFS Applications™. IFS functionality for ERP will provide deep traceability for inputs through inventory and non-inventory quality management tools. Personnel are managed through human resources functionality, and support services from outside the organization are handled through embedded contract management tools. Documents having to do with these various disciplines are handled by native document management functionality that enables any document—be it a material test report or a personnel training record—to be attached to work orders, shop orders, customer orders, recipes; in fact, virtually to any object across the application. -
(SCADA) Systems
NCS TIB 04-1 NATIONAL COMMUNICATIONS SYSTEM TECHNICAL INFORMATION BULLETIN 04-1 Supervisory Control and Data Acquisition (SCADA) Systems October 2004 OFFICE OF THE MANAGER NATIONAL COMMUNICATIONS SYSTEM P.O. Box 4052 Arlington, VA 22204-4052 Office of the Manager National Communications System October 2004 By Communication Technologies, Inc. 14151 Newbrook Drive, Suite 400 Chantilly, Virginia 20151 703-961-9088 (Voice) 703-961-1330 (Fax) www.comtechnologies.com Supervisory Control and Data Acquisition (SCADA) Systems Abstract The goal of this Technical Information Bulletin (TIB) is to examine Supervisory Control and Data Acquisition (SCADA) systems and how they may be used by the National Communications System (NCS) in support of National Security and Emergency Preparedness (NS/EP) communications and Critical Infrastructure Protection (CIP). An overview of SCADA is provided, and security concerns are addressed and examined with respect to NS/EP and CIP implementation. The current and future status of National, International, and Industry standards relating to SCADA systems is examined. Observations on future trends will be presented. Finally, recommendations on what the NCS should focus on with regards SCADA systems and their application in an NS/EP and CIP environment are presented. i ii Table of Contents Executive Summary.................................................................................................................. ES-1 1.0 Introduction........................................................................................................................... -
Total Quality Management Course Code: POM-324 Author: Dr
Subject: Total Quality Management Course Code: POM-324 Author: Dr. Vijender Pal Saini Lesson No.: 1 Vetter: Dr. Sanjay Tiwari Concepts of Quality, Total Quality and Total Quality Management Structure 1.0 Objectives 1.1 Introduction 1.2 Concept of Quality 1.3 Dimensions of Quality 1.4 Application / Usage of Quality for General Public / Consumers 1.5 Application of Quality for Producers or Manufacturers 1.6 Factors affecting Quality 1.7 Quality Management 1.8 Total Quality Management 1.9 Characteristics / Nature of TQM 1.10 The TQM Practices Followed by Multinational Companies 1.11 Summary 1.12 Keywords 1.13 Self Assessment Questions 1.14 References / Suggested Readings 1 1.0 Objectives After going through this lesson, you will be able to: Understand the concept of Quality in day-to-day life and business. Differentiate between Quality and Quality Management Elaborate the concept of Total Quality Management 1.1 Introduction Quality is a buzz word in our lives. When the customer is in market, he or she is knowingly or unknowingly very cautious about the quality of product or service. Imagine the last buying of any product or service, e.g., mobile purchased last time. You must have enquired about various features like RAM, Operating System, Processor, Size, Body Colour, Cover, etc. If any of the features is not available, you might have suddenly changed the brand or have decided not to purchase it. Remember, how our mothers buy fruits, vegetables or grocery items. They are buying fresh and look-wise firm fruits, vegetable and groceries. Simultaneously, they are very conscious about the price of the fruits, vegetable and groceries. -
The MES Software Solution for Continuous Productivity Efficiency
The MES software solution for continuous Productivity Efficiency improvement The software solution for collecting and analyzing production data in real-time, to know and anticipate the production system’s weak points and to act on effective decision making to increase productivity and efficiency. 2 MES software technology for open and flexibe architectures Progea offers Pro.Lean© as a MES software solution that interconnects plant floor levels with managerial levels to provide KPI and OEE data, calculate machine downtimes, track and schedule production runs. Every modern company operating in the Industry 4.0 the Overall Equipment Effectiveness (OEE) values to age needs simple and efficient tools to ensure discover the effective connectivity, data collection, aggregation and analysis, efficiency of your production plant. Knowing the with minimum and rapid return of investment (ROI). data makes it easier to imagine how a more efficient The reality of productivity in today’s increasingly production can mean a significant increase in business competitive world, demands efficiency, quality and for any company by investing little. Even a small continuously improving processes according to the increase in performances and loss reductions will earn “Lean Manufacturing” philosophy and Industry 4.0 the company big financial gains. guidelines. Automation systems that manage In addition, data management and interconnections to manufacturing production can only be optimized by managerial systems, within a Industry 4.0 framework, having adequate real-time data. The permit you to digitalize production processes, reduce Movicon.NExT™ errors and machine downtimes. Other functions such as Pro.Lean© module offers maximum efficiency and uses production Traceability, Scheduling and Maintenance, Progea’s vast experience in the industrial automation make the Pro.Lean solution open and adaptable to any software sector.