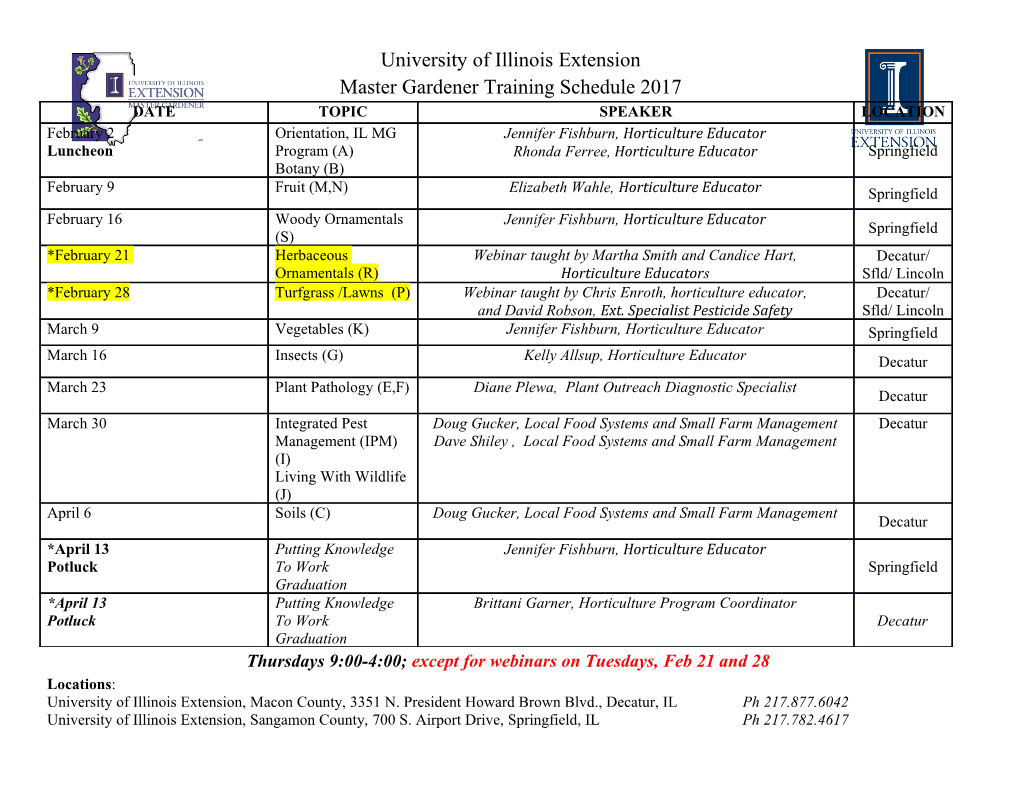
sensors Article Automation Pyramid as Constructor for a Complete Digital Twin, Case Study: A Didactic Manufacturing System Edwin Mauricio Martinez, Pedro Ponce * , Israel Macias and Arturo Molina Tecnológico de Monterrey, Department of Mechatronics, School of Engineering and Sciences, Mexico City Campus, Calle del Puente 222, Tlalpan, México City 14380, Mexico; [email protected] (E.M.M.); [email protected] (I.M.); [email protected] (A.M.) * Correspondence: [email protected] Abstract: Nowadays, the concept of Industry 4.0 aims to improve factories’ competitiveness. Usually, manufacturing production is guided by standards to segment and distribute its processes and implementations. However, industry 4.0 requires innovative proposals for disruptive technologies that engage the entire production process in factories, not just a partial improvement. One of these disruptive technologies is the Digital Twin (DT). This advanced virtual model runs in real-time and can predict, detect, and classify normal and abnormal operating conditions in factory processes. The Automation Pyramid (AP) is a conceptual element that enables the efficient distribution and connection of different actuators in enterprises, from the shop floor to the decision-making levels. When a DT is deployed into a manufacturing system, generally, the DT focuses on the low-level that is named field level, which includes the physical devices such as controllers, sensors, and so on. Thus, the partial automation based on the DT is accomplished, and the information between all manufacturing stages could be decremented. Hence, to achieve a complete improvement of the manufacturing system, all the automation pyramid levels must be included in the DT concept. An Citation: Martinez, E.M.; Ponce, P.; artificial intelligent management system could create an interconnection between them that can Macias, I.; Molina, A. Automation manage the information. As a result, this paper proposed a complete DT structure covering all Pyramid as Constructor for a Complete Digital Twin, Case Study: automation pyramid stages using Artificial Intelligence (AI) to model each stage of the AP based A Didactic Manufacturing System. on the Digital Twin concept. This work proposes a virtual model for each level of the traditional Sensors 2021, 21, 4656. https:// AP and the interactions among them to flow and control information efficiently. Therefore, the doi.org/10.3390/s21144656 proposed model is a valuable tool in improving all levels of an industrial process. In addition, It is presented a case study where the DT concept for modular workstations underpins the development Academic Editors: Sotiris Makris and of technologies within the framework of the Automation Pyramid model is implemented into a Nikolaos Papakostas didactic manufacturing system. Received: 12 May 2021 Keywords: digital twin; automation pyramid; industry 4.0; innovative products; manufacturing Accepted: 2 July 2021 model; educational innovation; higher education Published: 7 July 2021 Publisher’s Note: MDPI stays neutral with regard to jurisdictional claims in 1. Introduction published maps and institutional affil- iations. New smart-connected devices facilitate information flow to different levels of decision- makers. Consequently, the traditional factories are migrating their manufacturing processes to more innovative, optimized enterprises. Thus, the smart factory concept emerges as dramatically intensified manufacturing intelligence applications throughout the manu- facturing and supply chain enterprise [1]. Smart factories are called to transform into Copyright: © 2021 by the authors. Licensee MDPI, Basel, Switzerland. companies with more dynamic economic and supply chain services determined by busi- This article is an open access article ness and market demand. Some experts addressing the manufacturing changes attend to distributed under the terms and customer demands, the nature of products, the production economics, and the value chain conditions of the Creative Commons economics [2]. Attribution (CC BY) license (https:// Within the smart factory are emerging systems that can supplant or complement the creativecommons.org/licenses/by/ automated processes currently found in most industries worldwide; these are the cyber- 4.0/). physical systems (CPS). These new elements are the fundamental part of recent smart Sensors 2021, 21, 4656. https://doi.org/10.3390/s21144656 https://www.mdpi.com/journal/sensors Sensors 2021, 21, x FOR PEER REVIEW 2 of 29 Sensors 2021, 21, 4656 2 of 29 physical systems (CPS). These new elements are the fundamental part of recent smart en- terprises.enterprises. CPS CPS are collaborating, are collaborating, computational computational entities entities which which connect connect with the with real the phys- real iphysicalcal world world;; the CPS the get CPS online get online information information and process and process datadata using using Internet Internet services services [3]. As [3]. systemsAs systems comprising comprising various various technological technological elements elements,, CPSCPS requires requires knowledge knowledge of many of many dis- ciplinesdisciplines such such as assoftware software engineering, engineering, communica communicationtion protocols, protocols, control control theory, theory, design design strategies,strategies, and knowledgeknowledge ofof novel novel areas areas such such as as edge edge computing computing [4]. [4]. The The literature literature reports re- portsseveral several methodologies, methodologies, frameworks, frameworks and, implementationsand implementations of CPS. of CPS. For For instance, instance, in [5in], [5],a cyber-application a cyber-application framework framework was was proposed, proposed, advocating advocating several several patterns patterns for partiallyfor par- tiallyhandling handling ordered ordered knowledge knowledge to build to build pervasive pervasive applications. applications. TheThe CPS CPS is is comprised comprised of of assorted assorted technological technological elements elements with with different different purposes purposes ac- cordingaccording to the to the task task assigned. assigned. In [6], In [the6], authors the authors classified classified the elements the elements of CPS of CPSfrom froma pro- a ductionproduction perspective: perspective: smart smart objects, objects, CPS CPS objects, objects, and and digital digital-twinning-twinning processes. processes. Then, Then, theythey proposed aa systematicsystematic framework framework for for the the CPS, CPS which, which includes includes two two primary primary states: states the: theinterconnection interconnection of three of three physical physical segments segments and and the communicationthe communication of real of real physical physical and andvirtual virtual devices. devices. RegardingRegarding the the third third element element above, above, the the Digital Digital Twin Twin (DT) is one of the fundamental partsparts of of CPS. CPS. In In recent recent years, years, DT DThas hasacquired acquired relevance relevance due to due its tousefulness its usefulness in the indus- in the try.industry. Several Several authors authors have also have discussed also discussed the definition the definition of this technological of this technological entity. The entity. first definitionThe first definition is attributed is attributed to [6,7], which to [6, 7defined], which the defined DT generally the DT generallyas nonphysical as nonphysical elements describedelements describedby digital model by digitals to represent models to physical represent elements physical’ behaviors elements’ in behaviors real-world in envi- real- ronmentsworld environments [8]. With the [8 experience]. With the and experience the effort and of theapplying effort ofthis applying conceptual this technology, conceptual sometechnology, authors some added authors characteristics added characteristics to the first definition. to the first In [9], definition. the authors In [ 9discussed], the authors that discussed that DT must comprise five segments: the physical, virtual, connection, data, and DT must comprise five segments: the physical, virtual, connection, data, and service seg- service segment. This model was initially proposed by [10], whose authors argued that the ment. This model was initially proposed by [10], whose authors argued that the five ele- five elements must have the same importance in developing any DT. The real-world device ments must have the same importance in developing any DT. The real-world device is the is the base for building the virtual segment; the virtual one allows to run the simulations, base for building the virtual segment; the virtual one allows to run the simulations, deci- decision-making, and control of the physical device. The core of DT is the data form since sion-making, and control of the physical device. The core of DT is the data form since it it can allow generating new knowledge (Figure1). Besides, DT can increment the complete can allow generating new knowledge (Figure 1). Besides, DT can increment the complete performance of manufacturing systems. performance of manufacturing systems. Figure 1. Digital Twin General Scheme. Figure 1. Digital Twin General Scheme. Through innovative and effective tools such as DTs, developing new manufacturing processesThrough and innovative functions and that effective collaborate tools to such incorporate as DTs, developing the newly new emerging manufacturing CPS into processescompanies and in theirfunctions current that
Details
-
File Typepdf
-
Upload Time-
-
Content LanguagesEnglish
-
Upload UserAnonymous/Not logged-in
-
File Pages29 Page
-
File Size-