Mechanical and Functional Properties of Invar Alloy for Μ-MIM J
Total Page:16
File Type:pdf, Size:1020Kb
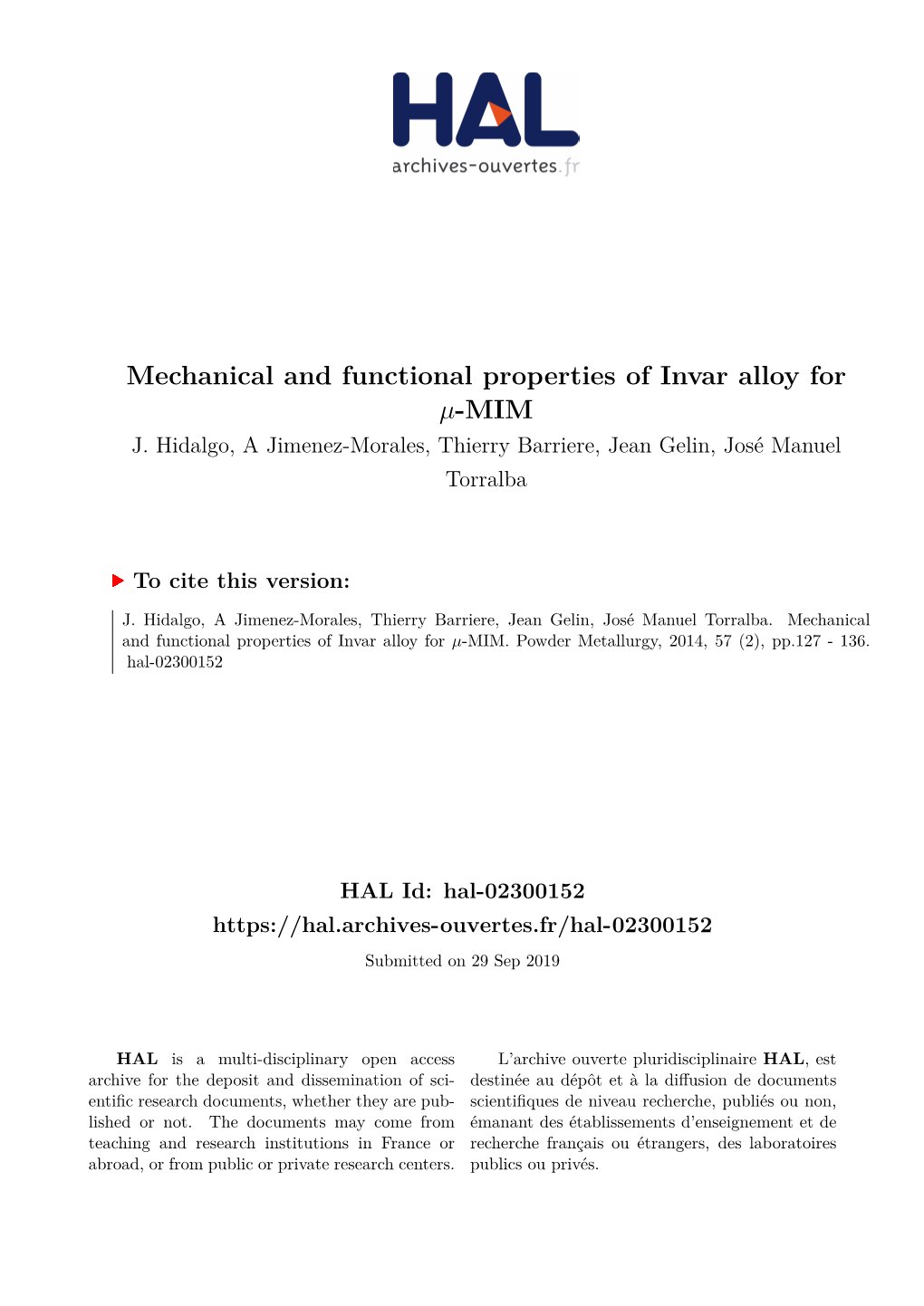
Load more
Recommended publications
-
Invar, Established a New Standard in the Way Precise Surveying Measurements Were Made, Both in Reliability and Accuracy
I N VA R The Breakthrough for a Low Expansion Alloy he discovery of the low expansion alloy, Invar, established a new standard in the way precise surveying measurements were made, both in reliability and accuracy. It became the first successful attempt to produce a metal alloy exhibiting a nearly zero coefficient of thermal expansion. In 1889, James Riley of Glasgow, Scotland, brought before the Iron and Steel Institute his investigations into the making of an alloy through a series of tests which combined up to 49 percent nickel with iron. Seven years later, in 1896, Charles Edouard Guillaume, a Swiss-born metallurgist and employee with the International Bureau of Weights and Measures near Paris, began looking specifically for an alloy to be used for surveyors’ wires that would not noticeably change when exposed to temperature variations. While experimenting with nickel contents between 30 and 60 percent, Guillaume discovered the coefficient of expansion at room temperature was lowest when mixing a nickel content of 36 percent with 64 percent iron. Since his new alloy exhibited the least amount of thermal expansion, and because Guillaume considered it invariable, it quickly became known as “Invar”. In 1920, Guillaume was awarded the Nobel Prize in Physics for his discovery of Invar >> By Jerry Penry, PS Displayed with permission • The American Surveyor • Vol. 9 No. 10 • Copyright 2012 Cheves Media • www.Amerisurv.com The Sokkia BIS30 3-meter Invar bar code leveling staff in use during a high precision survey. Image courtesy of Sokkia Corporation. Displayed with permission • The American Surveyor • Vol. 9 No. -
National Advisory Committee for Aeronautics
https://ntrs.nasa.gov/search.jsp?R=19930083526 2020-06-17T20:21:50+00:00Z GOVT. DOC. 1JlJf;, tEcH NFSS NICA,1. ~NO lil? , oor---------------------------------------------------~~~------~ L{) r N NATIONAL ADVISORY COMMITTEE FOR AERONAUTICS TECHNICAL NOTE 2758 / WEAR AND SLIDING F RICTION PROPERTIES OF NICKEL ALLOYS SUITED FOR CAGES OF HIGH-TEMPERATURE R OLLING- CONTACT BEARINGS I - ALLOYS RETAIN ING MECHANICAL PROPER TIES TO 600 0 F By R obert L. Johnson, Max A. Swikert and Edmond E. Bisson Lewis Flight Propulsion Laboratory Cleveland, Ohio Washington August 1952 lY NATIONAL ADVISORY COMMITTEE FOR AERONAUTICS TECHNICAL NOTE 2758 WEAR AND SLIDING FRICTION PROPERTIES OF NICKEL ALLOYS SUITED FOR CAGES OF HIGH-TEMPERATURE ROLLING-CONTACT BEARINGS I - ALLOYS REI'AINING MECHANICAL PROPERTIES TO 6000 F \. By Robert L. Johnson, Max A. SWikert, and Edmond E. Bisson SUMMARY Wear and sliding friction properties of a number of nickel alloys operating against hardened SAE 52100 steel were stUdied. These alloys include "L" nickel, wrought monel, cast monel, cast modified "H" monel, cast "s" monel, Invar, Ni-Resist 3, and Nichrome V. Some of the alloys studied may be useful as possible cage materials for high-temperature, high-speed bearings for aircraft turbines or for bearings to operate in corrosive media . Desirable operating properties of all the materials could be associated with the development on the rider surface of a naturally formed film of nickel oxide . On the basis of wear and friction proper ties, Ni-Resist 3, modified "H" monel, and Invar were the best materials studied in this investigation although they did not perform as well as nod!.llar iron. -
Special-Purpose Nickel Alloys
© 2000 ASM International. All Rights Reserved. www.asminternational.org ASM Specialty Handbook: Nickel, Cobalt, and Their Alloys (#06178G) Special-Purpose Nickel Alloys NICKEL-BASE ALLOYS have a number of meet special needs. The grades considered in ganese, and copper, a 0.005% limit on iron, and unique properties, or combinations of proper- this section include the following: a 0.02% limit on carbon. This high purity re- ties, that allow them to be used in a variety of sults in lower coefficient of expansion, electri- specialized applications. For example, the high • Nickel 200 (99.6% Ni, 0.04% C) cal resistivity, Curie temperature, and greater resistivity (resistance to flow of electricity) and • Nickel 201 (99.6% Ni, 0.02% C maximum) ductility than those of other grades of nickel heat resistance of nickel-chromium alloys lead • Nickel 205 (99.6% Ni, 0.04% C, 0.04% Mg) and makes Nickel 270 especially useful for to their use as electric resistance heating ele- • Nickel 233 (see composition in table that fol- some electronics applications such as compo- ments. The soft magnetic properties of lows) nents of hydrogen thyratrons and as a substrate nickel-iron alloys are employed in electronic • Nickel 270 (99.97% Ni) for precious metal cladding. devices and for electromagnetic shielding of computers and communication equipment. Iron- Composition limits and property data on sev- eral of these grades can be found in the article nickel alloys have low expansion characteris- Resistance Heating Alloys tics as a result of a balance between thermal ex- “Wrought Corrosion-Resistant Nickels and pansion and magnetostrictive changes with Nickel Alloys” in this Handbook. -
A Simple Theory of the Invar Effect in Iron-Nickel Alloys
1 A simple theory of the Invar effect in iron-nickel alloys François Liot1 & Christopher A. Hooley2 1Department of Physics, Chemistry, and Biology (IFM), Linköping University, SE-581 83 Linköping, Sweden; 2Scottish Universities Physics Alliance (SUPA), School of Physics and Astronomy, University of St Andrews, North Haugh, St Andrews, Fife KY16 9SS, U.K. Certain alloys of iron and nickel (so-called ‘Invar’ alloys) exhibit almost no thermal expansion over a wide range of temperature1–3. It is clear that this is the result of an anomalous contraction upon heating which counteracts the normal thermal expansion arising from the anharmonicity of lattice vibrations. This anomalous contraction seems to be related to the alloys’ magnetic properties, since the effect vanishes at a temperature close to the Curie temperature. However, despite many years of intensive research, a widely accepted microscopic theory of the Invar effect in face-centered-cubic Fe-Ni alloys is still lacking. Here we present a simple theory of the Invar effect in these alloys based on Ising magnetism, ab initio total energy calculations, and the Debye-Grüneisen model4. We show that this theory accurately reproduces several well known properties of these materials, including Guillaume’s famous plot1 of the thermal expansion coefficient as a function of the concentration of nickel. Within the same framework, we are able to account in a straightforward way for experimentally observed deviations from Vegard’s law2, 3, 5, 6. Our approach supports the idea that the lattice constant is governed by a few parameters, including the fraction of iron-iron nearest-neighbour pairs. -
Michelson's Nobel Lecture
NOBEL LECTURES IN PHYSICS 1901-1921 NOBEL LECTURES INCLUDING PRESENTATION SPEECHES AND LAUREATES BIOGRAPHIES PHYSICS CHEMISTRY PHYSIOLOGY OR MEDICINE LITERATURE PEACE ECONOMIC SCIENCES NOBEL LECTURES INCLUDING PRESENTATION SPEECHES AND LAUREATES' BIOGRAPHIES PHYSICS 1901-1921 b World Scientific b Singapore lNew Jersey · London lHong Kong Published for the Nobel Foundation in 1998 by World Scientific Publishing Co. Pte. Ltd. P 0 Box 128, Farrer Road, Singapore 912805 USA office: Suite lB, 1060 Main Street, River Edge, NJ 07661 UK office: 57 Shelton Street, Covent Garden, London WC2H 9HE NOBEL LECTURES IN PHYSICS (1901-1921) All rights reserved. ISBN 981-02-3401-5 Printed in Singapore. Foreword Since 1901 the Nobel Foundation has published annually , Les Prix Nobel with reports from the Nobel award ceremonies in Stockholm and Oslo as well as the biographies and Nobel lectures of the Laureates. In order to make the lectures available to people with special interests in the different prize fields the Foundation gave Elsevier Publishing Company the right to publish in English the lectures for 1901-1970, which were published in 1964-1972 through the following volumes: Physics 1901-1970 4 vols. Chemistry 1901-1970 4 vols. Physiology or Medicine 1901-1970 4 vols. Literature 1901-1967 1 vol. Peace 1901-1970 3 vols. Since the Elsevier series has been out of print for many years the Nobel Foundation has given World Scientific Publishing Company the right to publish these Nobel lectures, biographies and presentation speeches. The Nobel Foundation is very pleased that the intellectual and spiritual message to the world laid down in the laureates’ lectures will, thanks to the efforts of World Scientific, reach new readers all over the world. -
Stability of Materials for Use in Space-Based Interferometric Missions
STABILITY OF MATERIALS FOR USE IN SPACE-BASED INTERFEROMETRIC MISSIONS By ALIX PRESTON A DISSERTATION PRESENTED TO THE GRADUATE SCHOOL OF THE UNIVERSITY OF FLORIDA IN PARTIAL FULFILLMENT OF THE REQUIREMENTS FOR THE DEGREE OF DOCTOR OF PHILOSOPHY UNIVERSITY OF FLORIDA 2010 1 °c 2010 Alix Preston 2 This is dedicated to all who were told they would fail, only to prove them wrong 3 ACKNOWLEDGMENTS Much of this work would not have been made possible if it were not for the help of many graduate and undergraduate students, faculty, and sta®. I would like to thank Ira Thorpe, Rachel Cruz, Vinzenz Vand, and Josep Sanjuan for their help and thoughtful discussions that were instrumental in understanding the nuances of my research. I would also like to thank Gabriel Boothe, Aaron Spector, Benjamin Balaban, Darsa Donelon, Kendall Ackley, and Scott Rager for their dedication and persistence to getting the job done. A special thanks is due for the physics machine shop, especially Marc Link and Bill Malphurs, who spent many hours on the countless projects I needed. Lastly, I would like to thank my advisor, Dr. Guido Mueller, who put up with me, guided me, and supported me in my research. 4 TABLE OF CONTENTS page ACKNOWLEDGMENTS ................................. 4 LIST OF TABLES ..................................... 9 LIST OF FIGURES .................................... 10 KEY TO ABBREVIATIONS ............................... 17 KEY TO SYMBOLS .................................... 19 ABSTRACT ........................................ 20 CHAPTER 1 INTRODUCTION .................................. 22 1.1 Space-Based Missions .............................. 23 1.2 GRACE ..................................... 23 1.3 GRACE Follow-On ............................... 25 1.4 LISA ....................................... 26 1.4.1 Introduction ............................... 26 1.4.2 Sources .................................. 27 1.4.2.1 Cosmological background sources ............. -
The Cambridge Pendulum Apparatus
The Cambridge Pendulum Apparatus J. E. Jackson “A golden bud set on a leafless stem leads to my result”-E. Bramah, Kai Lung Unrolls his Mat. Summary Downloaded from https://academic.oup.com/gji/article/4/Supplement_1/375/650518 by guest on 24 September 2021 The three-pendulum method, developed and used by Lenox- Conyngham, was superseded in 1930, on the arrival of a new vacuum box for swinging two pendulums. With three invar pendulums taken over from the earlier apparatus and three new ones acquired in 1931, this box is the centrepiece of the apparatus which has been in use up to the present day, for geophysical investigations and for establishing gravity reference stations in many parts of the world. This article describes briefly the apparatus and the various modifications of pro- cedure and changes of auxiliary gear that have taken place in the past 30 years. A list of the work done with the apparatus is given. I. Introduction For two and a half centuries, geodesists have been studying the Figure of the Earth. Methods of investigation in this field are divisible into two classes, the geometrical and the physical. In the nineteenth century, surveyors with their triangulation and astronomical observations, helped by the utility of their work as a contribution to map-making, got away to a good geometrical start and produced a great many “Figures of the Earth”, each one of them closely fitting a small part of the geoid surface. Geodesy, in the modern sense of the word, stems from Newton’s law of gravitation. -
Charles-É. Guillaume
C HARLES - É . G UILLAUME Invar and elinvar Nobel Lecture, December 11, 1920 The anomaly of nickel steels Discovery of the anomaly - In 1889 the General Conference on Weights and Measures met at Sèvres, the seat of the International Bureau. It performed the first great deed dictated by the motto inscribed in the pediment of the splendid edifice that is the metric system : "A tous les temps, a tous les peuples" (For all times, to all peoples); and this deed consisted in the approval and distribution, among the governments of the states supporting the Metre Con- vention, of prototype standards of hitherto unknown precision intended to propagate the metric unit throughout the whole world. These prototypes were indeed noteworthy. They were made of a plati- num-iridium alloy developed by Henri Sainte-Claire-Deville which com- bined all the qualities of hardness, permanence, and resistance to chemical agents which rendered it suitable for making into standards required to last for centuries. Yet their high price excluded them from the ordinary field of science; at that time a single metre actually cost 7,000 crowns - and how much more today! A less costly answer had to be sought since between these precious proto- types and standards affording only uncertain guarantees there was a gap which nothing could fill. I first examined this problem in 1891 and soon discovered the really ex- cellent properties of pure nickel and still today this is the metal used to make a non-oxidizable standard, unaffected by the passage of time, rigid and of average expansibility. -
36% NICKEL-IRON ALLOY for Low Temperature Service
36% NICKEL-IRON ALLOY A PRACTICAL GUIDE TO THE USE OF NICKEL-CONTAINING ALLOYS NO 410 Distributed by Produced by NICKEL INCO INSTITUTE 36% NICKEL-IRON ALLOY A PRACTICAL GUIDE TO THE USE OF NICKEL-CONTAINING ALLOYS NO 410 Originally, this handbook was published in 1976 by INCO, The International Nickel Company, Inc. Today this company is part of Vale S.A. The Nickel Institute republished the handbook in 2020. Despite the age of this publication the information herein is considered to be generally valid. Material presented in the handbook has been prepared for the general information of the reader and should not be used or relied on for specific applications without first securing competent advice. The Nickel Institute, the American Iron and Steel Institute, their members, staff and consultants do not represent or warrant its suitability for any general or specific use and assume no liability or responsibility of any kind in connection with the information herein. Nickel Institute [email protected] www.nickelinstitute.org 36% NICKEL-IRON ALLOY For Low Temperature Service Introduction Tensile Requirements 36 per cent nickel-iron alloy possesses a useful The following tensile properties are specified in combination of low thermal expansion, moder- the ASTM standard: ately high strength and good toughness at tem- Tensile Strength .................... 65,000-80,000 psi peratures down to that of liquid helium, -452 ºF .................... 448-552 N/mm2 (-269 ºC). These properties coupled with good Yield Strength weldability and desirable physical properties (0.2% Offset), min ............ 35,000 psi make this alloy attractive for many cryogenic ............ 241 N/ mm2 applications. -
NATURE Obituary Notices
No. 3590, AUGUST 20, 1938 NATURE 321 Obituary Notices Dr. A. E. H. Tutton, F.R.S. magnificent crystals with six molecules of water. In LFRED EDWIN HOWARD TUTTON, who all, ninety-one salts were studied, and the results A died on July 14, was born on August 22, communicated in about fifty papers from 1890 until 1864, at Cheadle Moseley, now the Edgeley district 1929. As a result of this painstaking and accurate of the borough of Stockport. He attended science work, it was established that the crystallographic classes at the Stockport Mechanics Institute and properties vary regularly with the atomic weights also the evening courses in chemistry of Prof. of the interchangeable elements. The same result Roscoe at Owens College, Manchester. In 1883 was established for the perchlorates and double he went to the Normal School of Science (later the chroma.tes of the alkalis. This work could be brought Royal College of Science) and Royal School of into relation with the structures as revealed by the Mines, South Kensington, with an exhibition, which X-rays when this new method became available. In he took in preference to a scholarship which he had carrying out his crystallographic investigations gained for Owens College. During his period as a Tutton showed the greatest ingenuity in devising student, Huxley was professor of biology, Frankland and perfecting the measuring instruments, so that his of chemistry, Guthrie of physics, Judd of geology methods became well known as representing the and Lockyer of astronomy, and a fellow-student highest standard of crystallographic research. was H. -
The Legacy of Charles-Édouard Guillaume Swiss Perspective
The legacy of Charles-Édouard Guillaume Swiss perspective Philippe RICHARD Federal institute of metrology METAS Director Guillaume and Switzerland – Charles-Édouard Guillaume was born in Fleurier in Val de Travers on 15 February 1861. The city of Fleurier has two Nobel laureates! – From a watchmaking family, he focused part of his research on precision watchmaking and collaborated all his life with the watchmaking circles in his birth region. – Even after 53 years devoted to the International Bureau of Weights and Measures, Charles-Édouard Guillaume Guillaume’s family home in Fleurier remained deeply attached to Switzerland. © Fondation C.-E. Guillaume, Fleurier 2 Guillaume and Switzerland – In Switzerland, the memory of Charles-Édouard Guillaume, who became famous for his Nobel prize, is strongly associated with his work on precision horology. On the opening of one of the conferences he gave at La Chaux de Fonds, he declared: « Quand on parcourt les montagnes neuchâteloises, on est frappé par l’importance de l’horlogerie. » [When you walk in the mountains of the Neuchâtel region you are stunned by the importance of horology.] – In 1815, Charles-Frédéric Guillaume, Charles-Édouard Guillaume’s grandfather, sought refuge in England where he married a descendant of Revocation refugees who came from the Neuchâtel region. – They started a family and had three boys and established a horology activity. Charles-Édouard Guillaume’s father, who grew up in London before going back to Switzerland, became in turn a horologist. He is also highly educated and passed on to Charles-Édouard the taste for knowledge and horology. 3 Precision horology − The discovery of invar was an opportunity to return to the family tradition. -
EXEO-S10 (Low Thermal Expansion Alloy)
EXEO-S10 Low Thermal Expansion Alloy EXEO-S10 NACHI developed the EXEO series alloys in company-wide combined and connected engineering system by first analyzing and determining necessary characteristics and then applying Nachi original alloy design and special melting technologies. EXEO-S10 has superior low thermal expansion characteristics, it is clean with few impurities, and the best suitable for precision parts. L Alloy composition is accurately controlled by using special melting technology. L Nachi original technologies make it with very low level impurities and non-metallic inclusions. L It is used as parts of ultra-precision machinery, optical equipment, semiconductor manufacturing machine and electronic devices. Properties Expansion characteristics 60 Sample length 15 mm Thermal expansion curve 50 m) M 40 SUS420J2 30 20 10 EXEO-S10 Amount of expansion ( 0 −10 0 100 200 300 Temperature (°C) Physical properties Coefficient of Hardness Proof stress Tensile strength Elongation Reduction of area Density Item thermal expansion (HRB) (MPa) (MPa) (%) (%) (g/cm3) ((30-100°C)/°C) Annealed material 71 310 440 45 87 8.15 ≦1×10-6 Applications L Spindles for ultra-precision machinery L Parts for satellites L Parts for laser beam machine L Parts for magnetic chuck L Parts for precision measuring equipment L Material for glass sealing L Parts for optical communications equipment L Parts for electromagnetic filters L Parts for electromagnetic relays L Various supports and parts EXEO-S10_English.indd 1 2009/01/07 19:05:33 -S10 EXEO Low Thermal Expansion Alloy Production range Shape Range of dimensions (mm) Forged round bar F40 – 200 × L1000 - 3000 Rolled round bar F13 – 100 × L2000 - 5000 Forged flat bar Contact us for details (30 - 200) Rolled flat bar Contact us for details ( t 3 – 40) Hot drawn steel plate t 4 - 18, w 400 - 600, L 1000 - 2000 Cold drawn steel plate t 0.5 - 12, w 500 - 600, L 1000 - 2000 L Available either finished or semi-finished.