Thermocouple Materials
Total Page:16
File Type:pdf, Size:1020Kb
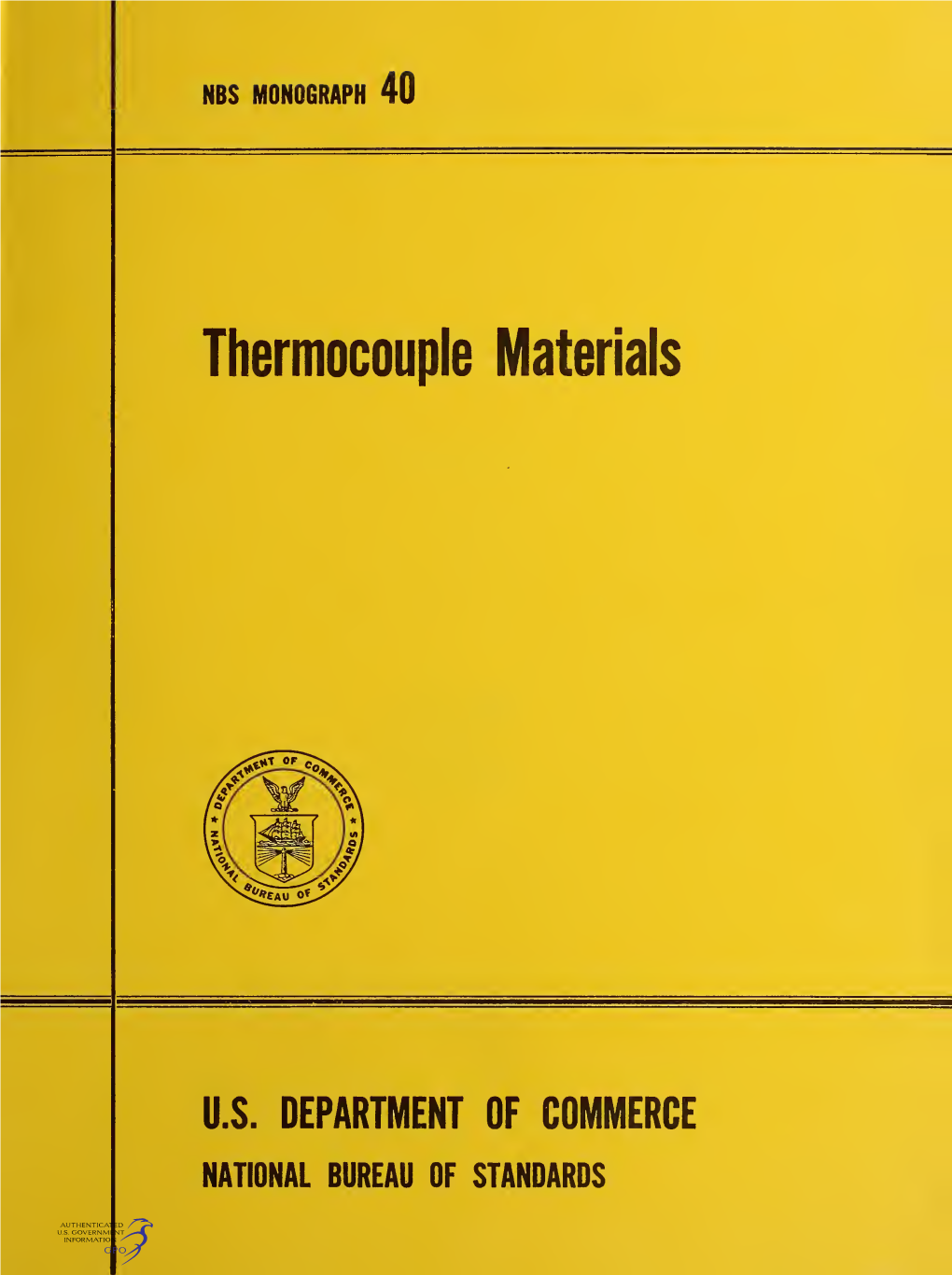
Load more
Recommended publications
-
Sensor Connectors
Sensor Connectors Thermocouple Connector - Two Pole Assembly Termination Code: 2 • Glass filled thermoplastic body provides high strength at temperatures up to 425°F 218°C) as well as low moisture absorption and good dielectric constant . • Heavy duty hollow pin construction prevents reverse mating of polarity.* • Body color coded to ISA and ANSI standards. 1” • Polarity indicated by symbols molded into body. • Contacts made of thermocouple materials which meet ISA and ANSI standards . • Jack spring loaded to insure firm grip to plug. • Accepts wire sizes to 14 awg. • Single screw cover cap for fast assembly. • Accepts crimp and tube adapter for product from .020 to .375. • Finger grips to permit ease of connection. 7/16” • Quick wiring hook up with large head screws and wire channel. Catalog Number Thermocouple Body Actual Alloy Plugs Jacks Type Color + In Connector - 1/2” LP-J L J-J Iron-Constantan® Black Iron Constantan® LP-K L J-K Chromel®-Alumel® Yellow Chromel® Alumel® 7/8” LP-E L J-E Chromel®-Constantan® Violet Chromel® Constantan® LP-T L J-T Copper-Constantan® Blue Copper Constantan® 1 3/8” LP-R/S L J-R/S Platinum/Rhodium- Green Copper #11 Alloy Platinum LP-CU L J-CU Uncompensated White Copper Copper Assembly Termination Code: 5 *Solid pin available on above construction. Add S to Part No. (i.e. LPS-J) Miniature Thermocouple Connector Assembly Termination Code: 3 • Thermoplastic body provides high strength at temperatures up to 425°F (218°C) as well as low moisture absorption and good dielectric constant . • Small, light weight and space saving. -
Seebeck and Peltier Effects V
Seebeck and Peltier Effects Introduction Thermal energy is usually a byproduct of other forms of energy such as chemical energy, mechanical energy, and electrical energy. The process in which electrical energy is transformed into thermal energy is called Joule heating. This is what causes wires to heat up when current runs through them, and is the basis for electric stoves, toasters, etc. Electron diffusion e e T2 e e e e e e T2<T1 e e e e e e e e cold hot I - + V Figure 1: Electrons diffuse from the hot to cold side of the metal (Thompson EMF) or semiconductor leaving holes on the cold side. I. Seebeck Effect (1821) When two ends of a conductor are held at different temperatures electrons at the hot junction at higher thermal velocities diffuse to the cold junction. Seebeck discovered that making one end of a metal bar hotter or colder than the other produced an EMF between the two ends. He experimented with junctions (simple mechanical connections) made between different conducting materials. He found that if he created a temperature difference between two electrically connected junctions (e.g., heating one of the junctions and cooling the other) the wire connecting the two junctions would cause a compass needle to deflect. He thought that he had discovered a way to transform thermal energy into a magnetic field. Later it was shown that a the electron diffusion current produced the magnetic field in the circuit a changing emf V ( Lenz’s Law). The magnitude of the emf V produced between the two junctions depends on the material and on the temperature ΔT12 through the linear relationship defining the Seebeck coefficient S for the material. -
Practical Temperature Measurements
Reference Temperatures We cannot build a temperature divider as we can a Metal A voltage divider, nor can we add temperatures as we + would add lengths to measure distance. We must rely eAB upon temperatures established by physical phenomena – which are easily observed and consistent in nature. The Metal B International Practical Temperature Scale (IPTS) is based on such phenomena. Revised in 1968, it eAB = SEEBECK VOLTAGE establishes eleven reference temperatures. Figure 3 eAB = Seebeck Voltage Since we have only these fixed temperatures to use All dissimilar metalFigures exhibit t3his effect. The most as a reference, we must use instruments to interpolate common combinations of two metals are listed in between them. But accurately interpolating between Appendix B of this application note, along with their these temperatures can require some fairly exotic important characteristics. For small changes in transducers, many of which are too complicated or temperature the Seebeck voltage is linearly proportional expensive to use in a practical situation. We shall limit to temperature: our discussion to the four most common temperature transducers: thermocouples, resistance-temperature ∆eAB = α∆T detector’s (RTD’s), thermistors, and integrated Where α, the Seebeck coefficient, is the constant of circuit sensors. proportionality. Measuring Thermocouple Voltage - We can’t measure the Seebeck voltage directly because we must IPTS-68 REFERENCE TEMPERATURES first connect a voltmeter to the thermocouple, and the 0 EQUILIBRIUM POINT K C voltmeter leads themselves create a new Triple Point of Hydrogen 13.81 -259.34 thermoelectric circuit. Liquid/Vapor Phase of Hydrogen 17.042 -256.108 at 25/76 Std. -
Type T Thermocouple Copper-Constantan Temperature Vs Millivolt Table Degree C
Technical Information Data Bulletin Type T Thermocouple CopperConstantan T Extension Grade Temperature vs Millivolt Table Thermocouple Grade E + Copper Reference Junction 32°F + Copper M Temperature Range Maximum Thermocouple Grade Maximum Useful Temperature Range: Temperature Range P Thermocouple Grade: 328 to 662°F –454 to 752°F Consrantan 200 to 350°C –270 to 400°C Consrantan E Extension Grade: 76 to 212°F Accuracy: Standard: 1.0°C or 0.75% 60 to 100°C Special: 0.5°C or 0.4% R Recommended Applications: A Mild Oxidizing,Reducing Vacuum or Inert Environments. Good Where Moisture Is Present. Low Temperature Applications. T Temp0123456789 U 450 6.2544 6.2553 6.2562 6.2569 6.2575 440 6.2399 6.2417 6.2434 6.2451 6.2467 6.2482 6.2496 6.2509 6.2522 6.2533 R 430 6.2174 6.2199 6.2225 6.2249 6.2273 6.2296 6.2318 6.2339 6.2360 6.2380 420 6.1873 6.1907 6.1939 6.1971 6.2002 6.2033 6.2062 6.2091 6.2119 6.2147 E 410 6.1498 6.1539 6.1579 6.1619 6.1657 6.1695 6.1732 6.1769 6.1804 6.1839 400 6.1050 6.1098 6.1145 6.1192 6.1238 6.1283 6.1328 6.1372 6.1415 6.1457 390 6.0530 6.0585 6.0640 6.0693 6.0746 6.0799 6.0850 6.0901 6.0951 6.1001 & 380 5.9945 6.0006 6.0067 6.0127 6.0187 6.0245 6.0304 6.0361 6.0418 6.0475 370 5.9299 5.9366 5.9433 5.9499 5.9564 5.9629 5.9694 5.9757 5.9820 5.9883 360 5.8598 5.8671 5.8743 5.8814 5.8885 5.8955 5.9025 5.9094 5.9163 5.9231 P 350 5.7847 5.7924 5.8001 5.8077 5.8153 5.8228 5.8303 5.8378 5.8452 -
Introduction to Thermocouples and Thermocouple Assemblies
Introduction to Thermocouples and Thermocouple Assemblies What is a thermocouple? relatively rugged, they are very often thermocouple junction is detached from A thermocouple is a sensor for used in industry. The following criteria the probe wall. Response time is measuring temperature. It consists of are used in selecting a thermocouple: slower than the grounded style, but the two dissimilar metals, joined together at • Temperature range ungrounded offers electrical isolation of one end, which produce a small unique • Chemical resistance of the 1 GΩ at 500 Vdc for diameters voltage at a given temperature. This thermocouple or sheath material ≥ 0.15 mm and 500 MΩ at 50 Vdc for voltage is measured and interpreted by • Abrasion and vibration resistance < 0.15 mm diameters. The a thermocouple thermometer. • Installation requirements (may thermocouple in the exposed junction need to be compatible with existing style protrudes out of the tip of the What are the different equipment; existing holes may sheath and is exposed to the thermocouple types? determine probe diameter). surrounding environment. This type Thermocouples are available in different offers the best response time, but is combinations of metals or ‘calibrations.’ How do I know which junction type limited in use to dry, noncorrosive and The four most common calibrations are to choose? (also see diagrams) nonpressurized applications. J, K, T and E. There are high temperature Sheathed thermocouple probes are calibrations R, S, C and GB. Each available with one of three junction What is ‘response time’? calibration has a different temperature types: grounded, ungrounded or A time constant has been defined range and environment, although the exposed. -
Thermocouple Standards Platinum / Platinum Rhodium
Thermocouple Standards 0 to 1600°C Platinum / Platinum Rhodium Type R & S Standard Thermocouple, Model 1600, Premium grade wire, gas tight assembly, g Type R and Type S No intermediate junctions. g Gas Tight Assembly g Premium Grade Wire The Isothermal range of Thermocouple Standards are the result of many years development. The type R and S standards will cover the range from 0°C to 1600°C. The measuring assembly comprises a 7mm x 300mm or 600mm gas tight 99.7% recrystallized alumina sheath inside which is a 2.5mm diameter twin bore tube holding the thermocouple. The inner 2.5mm assembly is removable since some calibration laboratories will only accept fine bore tubed thermocouples and some applications require fine bore tubing. The covered noble metal thermocouple wire connects the Also available without the physical cold junction - Specify No Cold Junction (NCJ). measuring sheath to the reference sheath which is a 4.5mm x 250mm stainless steel sheath suitable for Model 1600 referencing in a 0°C reference system. Two thermo electrically free multistrand copper wires (teflon coated) Hot Sheath connect the thermocouple to the voltage measuring device. Temperature Range 0°C to 1600°C (R or S) Emf Vs Temperature According to relevant document The thermocouple material is continuous from the hot or measuring junction to the cold, or referencing junction. Response Time 5 minutes Hot Junction see diagram Calibration Dimensions The 1600 is supplied with a certificate giving the error Connecting Cable see diagram between the ideal value and the actual emf of the thermo- couple at the gold point. -
Specifications Overview Compatible Thermocouple Sensors Connecting
HOBO® U12 J, K, S, T Thermocouple Data Logger (Part # U12-014) Inside this package: Thank you for purchasing a HOBO data logger. With proper care, it will give you years of accurate and reliable • HOBO U12 J, K, S, T measurements. Thermocouple Data Logger The HOBO U12 J, K, S, T Thermocouple data logger has a • Mounting kit with magnet, 12-bit resolution and can record up to 43,000 measurements hook-and-loop tape, tie- or events. The logger accepts J, K, S, and T type wrap mount, tie wrap, and thermocouple sensors, sold separately. The logger uses a two screws. direct USB interface for launching and data readout by a Doc # 13412-B, MAN-U12014 computer. Onset Computer Corporation An Onset software starter kit is required for logger operation. Visit www.onsetcomp.com for compatible software. Specifications Overview J type: 0 to 750 °C (32° to 1382°F) The U12 Thermocouple logger has two temperature channels. K type: 0 to 1250 °C (32° to 2282°F) Channel 1 is for a user-attached thermocouple. Channel 2 is the Measurement S type: -50 to 1760 °C (-58° to 3200°F) logger’s internal temperature, which is used for cold-junction range T type: -200 to 100 °C (-328° to 212°F) compensation of the thermocouple output. The logger can also Internal temperature: 0° to 50°C (32° to record the logger’s battery voltage (Channel 3) if selected. The 122°F) number of channels selected determines the maximum J type: ±2.5°C or 0.5% of reading, deployment time at a given sample interval. -
In-Situ Measurement and Numerical Simulation of Linear
IN-SITU MEASUREMENT AND NUMERICAL SIMULATION OF LINEAR FRICTION WELDING OF Ti-6Al-4V Dissertation Presented in Partial Fulfillment of the Requirements for the Degree Doctor of Philosophy in the Graduate School of The Ohio State University By Kaiwen Zhang Graduate Program in Welding Engineering The Ohio State University 2020 Dissertation Committee Dr. Wei Zhang, advisor Dr. David H. Phillips Dr. Avraham Benatar Dr. Vadim Utkin Copyrighted by Kaiwen Zhang 2020 1 Abstract Traditional fusion welding of advanced structural alloys typically involves several concerns associated with melting and solidification. For example, defects from molten metal solidification may act as crack initiation sites. Segregation of alloying elements during solidification may change weld metal’s local chemistry, making it prone to corrosion. Moreover, the high heat input required to generate the molten weld pool can introduce distortion on cooling. Linear friction welding (LFW) is a solid-state joining process which can produce high-integrity welds between either similar or dissimilar materials, while eliminating solidification defects and reducing distortion. Currently the linear friction welding process is most widely used in the aerospace industry for the fabrication of integrated compressor blades to disks (BLISKs) made of titanium alloys. In addition, there is an interest in applying LFW to manufacture low-cost titanium alloy hardware in other applications. In particular, LFW has been shown capable of producing net-shape titanium pre-forms, which could lead to significant cost reduction in machining and raw material usage. Applications of LFW beyond manufacturing of BLISKs are still limited as developing and quantifying robust processing parameters for high-quality joints can be costly and time consuming. -
Strain Gage Technical Data
STRAIN GAGE TECHNICAL DATA STRAIN GAGE MEASUREMENT The most universal measuring device for the electrical measurement of mechanical quantities is the strain gage. Several types of strain gages depend for their operation on the proportional variance of electrical resistance to strain: the piezoresistive or semi-conductor gage, the carbon resistive gage, the bonded metallic wire, and foil resistance gages. The bonded resistance strain gage is by far the most widely used in experimental stress analysis. This gage consists of a grid of very fine wire or foil bonded to a backing or carrier matrix. The electrical resistance of the grid varies linearly with strain. In use, the carrier matrix is bonded to the surface, force is applied, and the strain is found by measuring the change in resistance. The bonded resistance strain gage is low in cost, can be made with a short gage length, is only moderately affected by the bridge. This method assumes a wiring is located in a time-varying temperature changes, has small linear relationship between voltage magnetic field. out and strain, an initially balanced physical size and low mass, and Magnetic induction can be has fairly high sensitivity to strain. bridge, and a known VIN. In reality, the VOUT-strain relationship is controlled by using twisted lead In a strain gage application, the wires and forming minimum but carrier matrix and the adhesive nonlinear, but for strains up to a few thousand micro-strain, the error is equal loop areas in each side of must work together to transmit the the bridge. strain from the specimen to the grid. -
Apollo Space Suit
APOLLO SPACE S UIT 1962–1974 Frederica, Delaware A HISTORIC MECHANICAL ENGINEERING LANDMARK SEPTEMBER 20, 2013 DelMarVa Subsection Histor y of the Apollo Space Suit This model would be used on Apollo 7 through Apollo 14 including the first lunar mission of Neil Armstrong and Buzz International Latex Corporation (ILC) was founded in Aldrin on Apollo 11. Further design improvements were made to Dover, Delaware in 1937 by Abram Nathanial Spanel. Mr. Spanel improve mobility for astronauts on Apollo 15 through 17 who was an inventor who became proficient at dipping latex material needed to sit in the lunar rovers and perform more advanced to form bathing caps and other commercial products. He became mobility exercises on the lunar surface. This suit was known as famous for ladies apparel made under the brand name of Playtex the model A7LB. A slightly modified ILC Apollo suit would also go that today is known worldwide. Throughout WWII, Spanel drove on to support the Skylab program and finally the American-Soyuz the development and manufacture of military rubberized products Test Program (ASTP) which concluded in 1975. During the entire to help our troops. In 1947, Spanel used the small group known time the Apollo suit was produced, manufacturing was performed as the Metals Division to develop military products including at both the ILC plant on Pear Street in Dover, Delaware, as well as several popular pressure helmets for the U.S. Air Force. the ILC facility in Frederica, Delaware. In 1975, the Dover facility Based upon the success of the pressure helmets, the Metals was closed and all operations were moved to the Frederica plant. -
Pub Date Abstract
DOCUMENT RESUME ED 058 456 VT 014 597 TITLE Exploring in Aeronautics. An Introductionto Aeronautical Sciences. INSTITUTION National Aeronautics and SpaceAdministration, Cleveland, Ohio. Lewis Research Center. REPORT NO NASA-EP-89 PUB DATE 71 NOTE 398p. AVAILABLE FROMSuperintendent of Documents, U.S. GovernmettPrinting Office, Washington, D.C. 20402 (Stock No.3300-0395; NAS1.19;89, $3.50) EDRS PRICE MF-$0.65 HC-$13.16 DESCRIPTORS Aerospace Industry; *AerospaceTechnology; *Curriculum Guides; Illustrations;*Industrial Education; Instructional Materials;*Occupational Guidance; *Textbooks IDENTIFIERS *Aeronatics ABSTRACT This curriculum guide is based on a year oflectures and projects of a contemporary special-interestExplorer program intended to provide career guidance and motivationfor promising students interested in aerospace engineering and scientific professions. The adult-oriented program avoidstechnicality and rigorous mathematics and stresses real life involvementthrough project activity and teamwork. Teachers in high schoolsand colleges will find this a useful curriculum resource, w!th manytopics in various disciplines which can supplement regular courses.Curriculum committees, textbook writers and hobbyists will also findit relevant. The materials may be used at college level forintroductory courses, or modified for use withvocationally oriented high school student groups. Seventeen chapters are supplementedwith photographs, charts, and line drawings. A related document isavailable as VT 014 596. (CD) SCOPE OF INTEREST NOTICE The ERIC Facility has assigned this document for processing to tri In our judgement, thisdocument is also of interest to the clearing- houses noted to the right. Index- ing should reflect their special points of view. 4.* EXPLORING IN AERONAUTICS an introduction to Aeronautical Sciencesdeveloped at the NASA Lewis Research Center, Cleveland, Ohio. -
Temperature Measurement
mywbut.com 14 Temperature measurement 14.1 Principles of temperature measurement Temperature measurement is very important in all spheres of life and especially so in the process industries. However, it poses particular problems, since temperature measurement cannot be related to a fundamental standard of temperature in the same way that the measurement of other quantities can be related to the primary standards of mass, length and time. If two bodies of lengths l1 and l2 are connected together end to end, the result is a body of length l1 C l2.A similar relationship exists between separate masses and separate times. However, if two bodies at the same temperature are connected together, the joined body has the same temperature as each of the original bodies. This is a root cause of the fundamental difficulties that exist in establishing an absolute standard for temperature in the form of a relationship between it and other measurable quantities for which a primary standard unit exists. In the absence of such a relationship, it is necessary to establish fixed, reproducible reference points for temperature in the form of freezing and boiling points of substances where the transition between solid, liquid and gaseous states is sharply defined. The International Practical Temperature Scale (IPTS)Ł uses this philosophy and defines six primary fixed points for reference temperatures in terms of: ž the triple point of equilibrium hydrogen 259.34°C ž the boiling point of oxygen 182.962°C ž the boiling point of water 100.0°C ž the freezing point of zinc 419.58°C ž the freezing point of silver 961.93°C ž the freezing point of gold 1064.43°C (all at standard atmospheric pressure) The freezing points of certain other metals are also used as secondary fixed points to provide additional reference points during calibration procedures.