Cold Forging – Case Studies
Total Page:16
File Type:pdf, Size:1020Kb
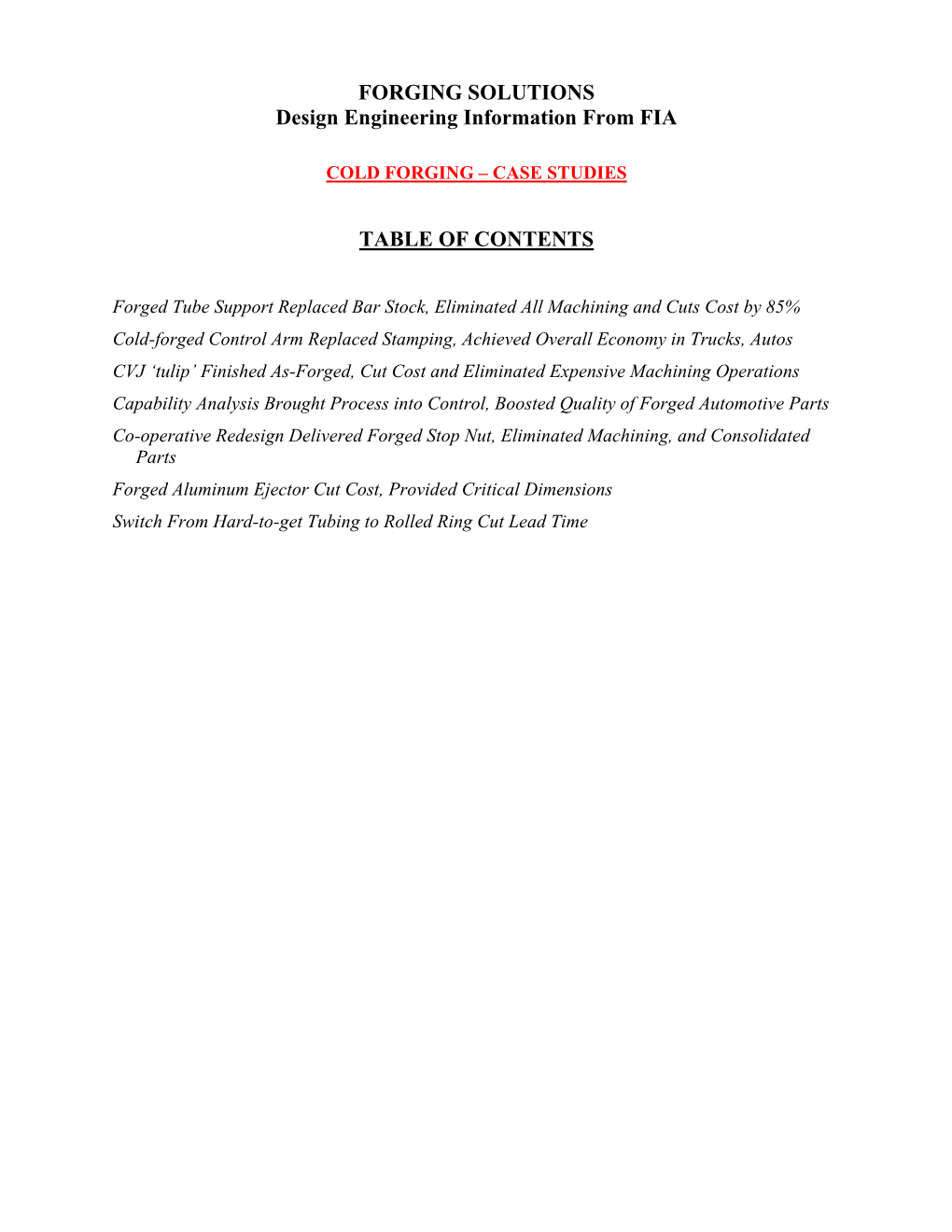
Load more
Recommended publications
-
Integrating Cold Forging and Progressive Stamping for Cost
Precision Cold Forging Progressive Stamping Enables Cost Effective Production of Complex Parts Overview Both Cold Forging and Precision Stamping are proven technologies used in the fabrication of parts for a wide range of industries. Many of our previous Tech Bulletins have detailed the benefits of each technology, and in several cases, these processes are thought of as an either- or choice. This Tech Bulletin provides insights into how combining these technologies in a process known as Precision Cold Forging Progressive Stamping can provide significant synergies and additional benefits for the cost-effective production of complex parts that cannot easily be created by either technique alone. What is Cold Forging? As detailed in other Interplex Tech Bulletins, Cold Forging is essentially an impact forming process in which billets of raw material are compressed and reformed into a part’s desired shape. Cold Forging offers the key benefits of lower costs, rapid high-volume throughput, high part strength, and very efficient material utilization. This, in comparison to processes like machining that remove Figure 1 – Cold Forged significant amounts of raw material rather than simply reforming all the Automotive Seat Belt Gear material into the desired shape. What is Precision Stamping? Precision Stamping is another proven technology that uses a press and die to form sheet metal, blanks or coil material into desired shapes. Variations of the stamping process can effectively yield several different output results including bending, embossing, flanging, coining, etc. Like Cold Forging, Precision Stamping typically offers high material utilization with minimal waste and can also deliver high-volume production results. -
1 Modeling and Optimization in Manufacturing by Hydroforming and Stamping
13 1 Modeling and Optimization in Manufacturing by Hydroforming and Stamping Hakim Naceur1 and Waseem Arif2 1Université Polytechnique Hauts-de-France, CNRS, INSA Hauts-de-France, UMR 8201-LAMIH, F-59313 Valenciennes, France 2University of Gujrat, Mechanical Engineering Department, Gujrat, Pakistan 1.1 Introduction Due to the strict environmental policies and shortage of energy, the manufacturing industries are pressurized to cut down the raw material cost and to save energy. This is particularly true in the automotive industry, where manufacturers are obliged to develop advanced techniques to reduce the pollution by reducing the fuel con- sumption without significant increase in the cost. Among all the manufacturing techniques, the stamping and hydroforming methods hold a top position among the cold sheet metal forming processes due to the versatility of components that can be produced and high production rates [1]. Stamping and hydroforming processes are intensively used in various industrial sectors such as transportation, car body in white (Figure 1.1), household appliances, metal packaging, etc. The use of fluid pressure has been remarkably increased in sheet metal form- ing processes since it allows a superior final surface quality of the workpiece than standard deep drawing process [2–4]. In particular, sheet hydroforming process has great potential to manufacture body-in-white parts with consistently extreme level of ultimate tensile strength, reduced weight, geometrical accuracy, and minimum tol- erances. It has certain advantages, e.g. more uniform thickness distribution of the final workpiece component, lower tooling cost, and versatility to produce partswith different geometries using the same setup [5]. The worldwide acknowledgment of these two sheet metal forming processes is largely due to the external pressure from the government legislators to develop lightweight products. -
Problem- Solving Guide
Common Stamping Problems Problem- Manufacturers know that punching can be the most cost-effective process for making Dayton Progress Corporation holes in strip or sheet metal. However, as the part material increases in hardness to 500 Progress Road Solving accommodate longer or more demanding runs, greater force is placed on the punch P.O. Box 39 Dayton, OH 45449-0039 USA and the die button, resulting in sudden shock, excessive wear, high compressive loading, and fatigue-related failures. Dayton Progress Detroit Guide 34488 Doreka Dr. The results of some of these Fraser, MI 48026 problems are shown in the Dayton Progress Portland photos on this page. 1314 Meridian St. Portland, IN 47371 USA Dayton Progress Canada, Ltd. 861 Rowntree Dairy Road Woodbridge, Ontario L4L 5W3 Punch Chipping & Point Breakage Dayton Progress Mexico, S. de R.L. de C.V. Access II Number 5, Warehouse 9 Chips and breaks can be caused by Benito Juarez Industrial Park press deflection, improper punch Querétaro, Qro. Mexico 76130 materials, excessive stripping force, Dayton Progress, Ltd. and inadequate heat treatment. G1 Holly Farm Business Park Honiley, Kenilworth Slug Jamming Warwickshire CV8 1NP UK Slug jamming is often the result Dayton Progress Corporation of Japan of improper die design, worn-out 2-7-35 Hashimotodai, Midori-Ku die parts, or obstruction in the slug Sagamihara-Shi, Kanagawa-Ken relief hole. 252-0132 Japan Slug Pulling Dayton Progress GmbH Adenauerallee 2 Slug pulling occurs when the slug 61440 Oberursel/TS, Germany sticks to the punch face upon withdrawal and comes out of the Dayton Progress Perfuradores Lda Zona Industrial de Casal da Areia Lote 17 lower die button. -
Methods Used for the Compaction and Molding of Ceramic Matrix Composites Reinforced with Carbon Nanotubes
processes Review Methods Used for the Compaction and Molding of Ceramic Matrix Composites Reinforced with Carbon Nanotubes Valerii P. Meshalkin and Alexey V. Belyakov * Mendeleev University of Chemical Technology of Russia (MUCTR), 9 Miusskaya Square, 125047 Moscow, Russia; [email protected] * Correspondence: [email protected]; Tel.: +7-495-4953866 Received: 2 August 2020; Accepted: 11 August 2020; Published: 18 August 2020 Abstract: Ceramic matrix composites reinforced with carbon nanotubes are becoming increasingly popular in industry due to their astonishing mechanical properties and taking into account the fact that advanced production technologies make carbon nanotubes increasingly affordable. In the present paper, the most convenient contemporary methods used for the compaction of molding masses composed of either technical ceramics or ceramic matrix composites reinforced with carbon nanotubes are surveyed. This stage that precedes debinding and sintering plays the key role in getting pore-free equal-density ceramics at the scale of mass production. The methods include: compaction in sealed and collector molds, cold isostatic and quasi-isostatic compaction; dynamic compaction methods, such as magnetic pulse, vibration, and ultrasonic compaction; extrusion, stamping, and injection; casting from aqueous and non-aqueous slips; tape and gel casting. Capabilities of mold-free approaches to produce precisely shaped ceramic bodies are also critically analyzed, including green ceramic machining and additive manufacturing technologies. Keywords: carbon nanotubes; ceramic matrix composites; compaction; molding; casting; powder mixtures; green bodies; plastic molding powders; slips; polymerizable monomers; solid freeform fabrication; machinery 1. Introduction Compaction molding is an important technological stage in the mass production of technical ceramics and ceramic matrix composites (hereinafter, CMCs). -
The Simulation of Cold Volumetric Stamping by the Method of Transverse Extrusion
MATEC Web of Conferences 224, 01105 (2018) https://doi.org/10.1051/matecconf/201822401105 ICMTMTE 2018 The simulation of cold volumetric stamping by the method of transverse extrusion Anatoly K. Belan1, Vladimir A. Nekit1,*, and Olga A. Belan1 1Nosov Magnitogorsk State Technical University, Lenin Street, 38, Magnitogorsk city, Chelyabinsk Region, Russian Federation, 455000 Abstract. The article is devoted to the theoretical study and development of the production process of manufacturing rod products with larger heads by transverse extrusion. For carrying out researches the elastic-plastic finite- element model based on the variation principle was chosen. This model, due to the development of a complex of boundary and initial conditions, has been adapted to the scheme of volume stamping of the fasteners and implemented in the form of a software package in the system DEFORM 3D.The paper presents the results of computer simulation of the technology of manufacturing the mortgage bolt 1 Introduction With the development of mechanical engineering, automotive and construction, there is a growing need for sophisticated modern fasteners which allows you to create strong, high- performance, reliable and durable connections. These fasteners contain: flanged fasteners, self-drilling and self-tapping screws, their use greatly simplifies and speed up installation work [1]. Fig. 1. Items with long cone and an enlarged head. To reduce terms of development and introduction of new types of fasteners the systems of the automated design and modelling allowing to model several options of the technology * Corresponding author: [email protected] © The Authors, published by EDP Sciences. This is an open access article distributed under the terms of the Creative Commons Attribution License 4.0 (http://creativecommons.org/licenses/by/4.0/). -
The Dynisco Extrusion Processors Handbook 2Nd Edition
The Dynisco Extrusion Processors Handbook 2nd edition Written by: John Goff and Tony Whelan Edited by: Don DeLaney Acknowledgements We would like to thank the following people for their contributions to this latest edition of the DYNISCO Extrusion Processors Handbook. First of all, we would like to thank John Goff and Tony Whelan who have contributed new material that has been included in this new addition of their original book. In addition, we would like to thank John Herrmann, Jim Reilly, and Joan DeCoste of the DYNISCO Companies and Christine Ronaghan and Gabor Nagy of Davis-Standard for their assistance in editing and publication. For the fig- ures included in this edition, we would like to acknowledge the contributions of Davis- Standard, Inc., Krupp Werner and Pfleiderer, Inc., The DYNISCO Companies, Dr. Harold Giles and Eileen Reilly. CONTENTS SECTION 1: INTRODUCTION TO EXTRUSION Single-Screw Extrusion . .1 Twin-Screw Extrusion . .3 Extrusion Processes . .6 Safety . .11 SECTION 2: MATERIALS AND THEIR FLOW PROPERTIES Polymers and Plastics . .15 Thermoplastic Materials . .19 Viscosity and Viscosity Terms . .25 Flow Properties Measurement . .28 Elastic Effects in Polymer Melts . .30 Die Swell . .30 Melt Fracture . .32 Sharkskin . .34 Frozen-In Orientation . .35 Draw Down . .36 SECTION 3: TESTING Testing and Standards . .37 Material Inspection . .40 Density and Dimensions . .42 Tensile Strength . .44 Flexural Properties . .46 Impact Strength . .47 Hardness and Softness . .48 Thermal Properties . .49 Flammability Testing . .57 Melt Flow Rate . .59 Melt Viscosity . .62 Measurement of Elastic Effects . .64 Chemical Resistance . .66 Electrical Properties . .66 Optical Properties . .68 Material Identification . .70 SECTION 4: THE SCREW AND BARREL SYSTEM Materials Handling . -
Rotary Swaging What Is Rotary Swaging?
Rotary Swaging What is Rotary Swaging? Net-Shape-Forming Rotary swaging is a process for precision forming of tubes, bars or wires. lt belongs to the group of net-shape-forming processes, of which one of the characteristics is that the finished shape of the formed workpieces is obtained without, or with only a minimum amount of further final processing by machining. The forming dies of the swaging machine are arranged concentric around the workpiece. The swaging dies perform high frequency radial movements with short strokes. The stroke frequencies are ranging from 1,500 to 10,000 per minute depending on the machine size, with total stroke lengths of 0.2 to 5 mm. The radial movements of the dies are for most applications simultaneous. Usually one die set consists of four die segments. Depending on the application and on the size of the machine, alternatively sets of two, three, six or in special cases up to eight dies can be used. To prevent the formation of longitudinal burrs at the gaps between the dies, there is a relative rotational movement between dies and the workpiece. The swaging dies rotate around the workpiece, or alternatively the workpiece rotates Operation principle between the dies. For production of non-circular forms the dies and the workpiece are stationary without rotational movement. Rotary swaging is an incremental forming process where the oscillating forming takes place in many small processing steps. One of the advantages of the incremental forming process compared to the continuous processes is the homogenous material forming. Rotary swaging achieves very high forming ratios in only one processing step as the deformability of the material is uniformly distributed over the cross-section. -
Process Analysis and Design in Stamping and Sheet
PROCESS ANALYSIS AND DESIGN IN STAMPING AND SHEET HYDROFORMING DISSERTATION Presented in Partial Fulfillment of the Requirements for the Degree Doctor of Philosophy in the Graduate School of The Ohio State University By Ajay D. Yadav, M.S. * * * * * The Ohio State University 2008 Dissertation Committee: Approved by: Professor Taylan Altan, Adviser Associate Professor Jerald Brevick -------------------------------------------------- Professor Gary L. Kinzel Adviser Industrial and Systems Engineering Graduate Program ABSTRACT This thesis presents initial attempts to simulate the sheet hydroforming process using Finite Element (FE) methods. Sheet hydroforming with punch (SHF-P) process offers great potential for low and medium volume production, especially for forming (a) lightweight materials such as Al- and Mg- alloys and (b) thin gage high strength steels (HSS). Sheet hydroforming has found limited applications and is thus still a relatively new forming process. Therefore, there is very little experience-based knowledge of process parameters (namely forming pressure, blank holder tonnage) and tool design in sheet hydroforming. For wide application of this technology, a design methodology to implement a robust SHF-P process needs to be developed. There is a need for a fundamental understanding of the influence of process and tool design variables on hydroformed part quality. This thesis addresses issues unique to sheet hydroforming technology, namely, (a) selection of forming (pot) pressure, (b) excessive sheet bulging and tearing at large forming pressures, and (c) methods to avoid leaking of pressurizing medium during forming. Through process simulation and collaborative efforts with an industrial sponsor, the influence of process and tool design variables on part quality in SHF-P of axisymmetric punch shapes (cylindrical and conical punch) is investigated. -
Aluminum Stamping Solutions
Select the Coating that Matches Commitment to Quality & Customer Satisfaction Aluminum Your Speci c Needs Dayton Lamina is a leading manufacturer of tool, die and mold components for the metal-working and plastics industries. As a customer-focused, world-class supplier of choice, we provide Stamping Abrasive Wear Adhesive Wear the brands, product breadth, distribution network and technical Regardless of the end product(s) your Common Abrasion, pitting, cavitation, striation, Galling, pick-up, sticking, welding, company manufactures, you can Names etc. etc. support for all your metal forming needs. Solutions improve the length of run time, reduce Processes Hard sheet material—jagged edges Soft sheet material Piercing, shearing, etc. Drawing, extruding, etc. Our goal is to give our customers the most innovative and value- changeover time, improve uptime, Sliding wear—along direction of Perpendicular to direction of forming added products and services. and get more for your stamping dollar forming by selecting the type of coating that Process temperature may be too high Process temperature may be too matches your individual operational or low high Clearances may be too tight Clearances may be tight capabilities. Solutions Increase surface hardness Increase lubrication The chart on the right describes the Increase clearances Choose lower coefficient coating causes, e ects, and solutions for abrasive Choose high thermal resistance Choose high thermal resistance coating coating wear and adhesive wear. The slider Increase clearances graph following shows the relative suitability for each type of treatment/ Abrasive Wear Adhesive Wear coating in both of those categories. The bubble chart shows the relationship be- tween service temperature, coe cient Uncoated XNP XCN CRN XNT Tool XNM XCD XCDP of friction, and hardness of the coating. -
Metal Stamping Design Guidelines
Larson Tool & Stamping Company Metal Stamping Design Guidelines 90 Olive St., Attleboro, MA 02703-3802 Phone: (508) 222-0897 www.larsontool.com Design Guide by Neil Fonger Metal Stamping Design Guidelines Metal Stamping is an economical way of producing quantities of parts that can have many qualities including strength, durability; wear resistance, good conductive properties and stability. We would like to share some ideas that could help you design a part that optimizes all the features that the metal stamping process offers. Material Selection There are many sheet and strip materials to choose from that respond well to metal stamping and forming. However, price and availability can vary greatly and affect the cost and delivery of production metal stampings. There are factors that should be considered when selecting an alloy and specifying physical characteristics of that material. Tolerancing Most common steel grades are offered in standard gage thicknesses and tolerances. These sizes are usually readily available as stock items and are generally the best choice when cost and delivery are a major factor. Rolling mills work from master coils, and so usually have minimum order quantities, somewhere in the truckload range. If the material required to produce a metal stamping order is much less than this quantity, a steel warehouse can search its inventory to find material that might happen to fall within the specified tolerance, but this makes availability a variable from order to order. Custom material can be purchased from companies that specialize in re-rolling smaller quantities, but the cost can increase exponentially. Chemistry Over-specifying an alloy is one of the biggest factors in driving up the cost of a metal stamping. -
Sheet Metal Fabrication Guide
CUSTOM MECHANICAL SOLUTIONS TENERE.COM A STARTER GUIDE TO SHEET METAL FABRICATION An introduction to basic sheet metal fabrication terms and definitions INTRODUCTION Whether you’re liking a photo on social media or making the switch to a solar powered home, sheet metal is everywhere. And because its uses are so varied - from the servers that run social media platforms to in-home intelligent energy storage systems - we’ve put together a guide to help you understand the ins and outs of sheet metal fabrication. Sheet Metal Fabrication Defined nearly any shape or size. Sheet metal fabrication is the process of Depending on the process and the engineering transforming sheet metal into specific shapes, required, sheet metal fabrication often involves usually by bending, punching, or cutting. Metal varying levels of human interaction, but all involve sheets of various gauges can be manipulated into some form of heavy machinery and equipment. LASER CUTTING - an extremely precise method SET-UP TIME - the amount of time it takes to set METAL FORMING AND STAMPING of cutting that uses a concentrated beam of light. up the proper dies and punches for a job. This Also used by evil geniuses. time varies depending on the complexity of the Press Brakes Turrets and Lasers part and machine. MACHINING/MILLING - the controlled removal A press brake squeezes a single sheet of metal When it comes to cutting sheet metal, turret of material using a cutting tool or lathe. SHEARING - a form of cutting in which downward between two plates or dies to bend the metal to punches and laser cutters are common options. -
Prediction and Reduction of Defects in Sheet Metal Forming Dissertation
PREDICTION AND REDUCTION OF DEFECTS IN SHEET METAL FORMING DISSERTATION Presented in Partial Fulfillment of the Requirements for the Degree Doctor of Philosophy in the Graduate School of The Ohio State University Ali Fallahiarezoodar M. S. Graduate Program in Industrial and Systems Engineering The Ohio State University 2018 Dissertation Committee: Taylan Altan, Advisor Farhang Pourboghrat Jerald Brevick Copyright by Ali Fallahiarezoodar 2018 ABSTRACT Sheet metal forming as process of forming a metal blank into a useful part is a major metal forming process. The overall objective of the sheet metal forming process is to form the part within the required tolerances without any defects. Defects in sheet metal forming appeared as tearing, necking, wrinkling, and springback. In the last decade, the advanced high strength steels (AHSS) and high strength aluminum alloys are increasingly used in automotive industry to satisfy the demands for improved safety, fuel efficiency and low-emission of greenhouse gas. However, in general, in high strength materials, low formability and high springback are observed. Therefore, forming of these materials is more challenging than normal mild steels. Several parameters affect the quality of the final part. Blank and tool material, friction and lubrication, and process parameters such as forming speed and temperature can significantly affect the result. Determination of material properties and formability is necessary for tooling and process design. The common methods for determination of material properties required for designing and simulating the sheet metal forming process are reviewed. Also, forming limit diagram as an indication of material formability is studied. The limitations of the forming limit diagram are presented and a practical method for developing the forming limit diagram is presented.