Rail Accident Report
Total Page:16
File Type:pdf, Size:1020Kb
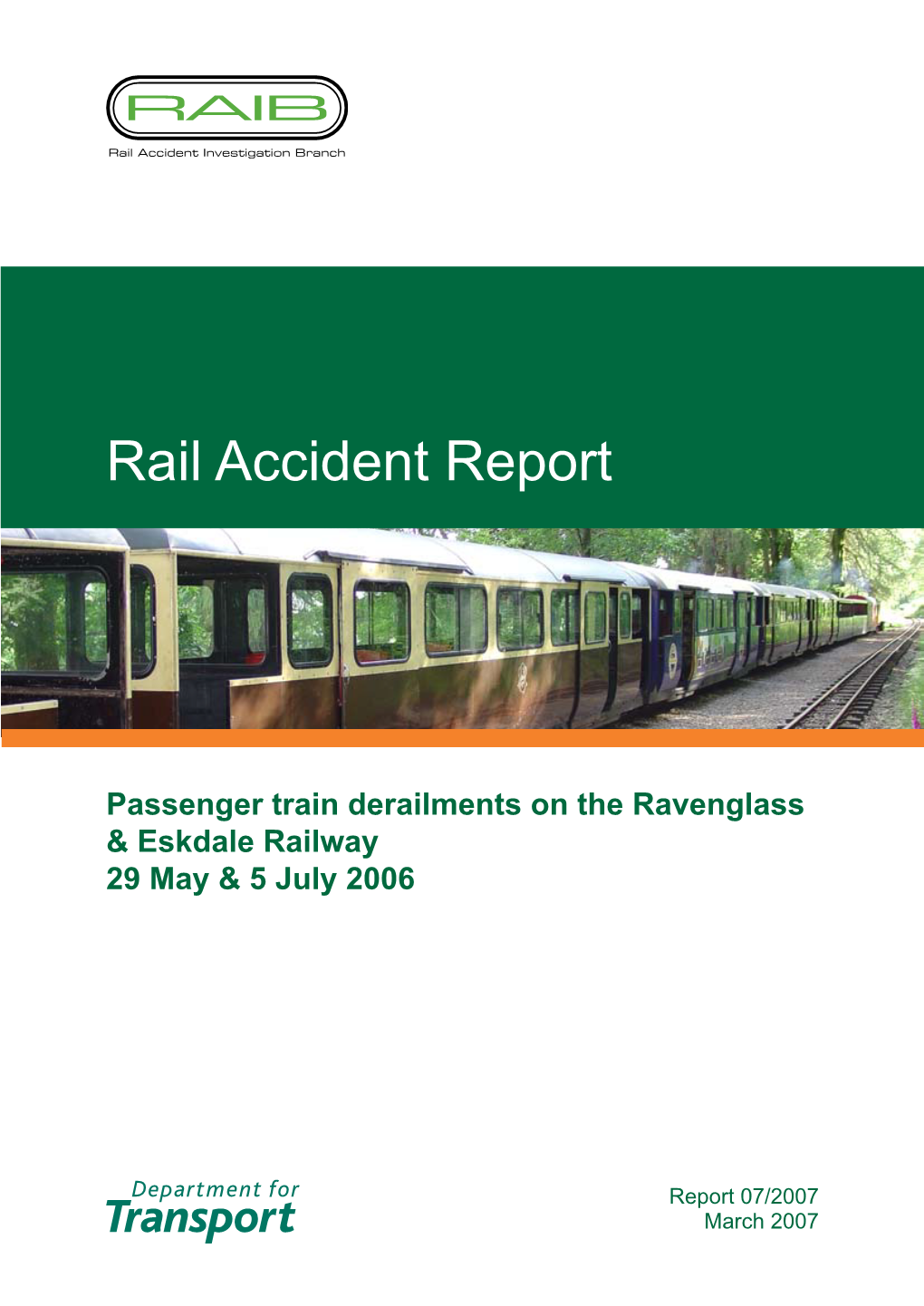
Load more
Recommended publications
-
Derailment of a Passenger Train Near Clogwyn Y Gwin South Foot Crossing, Welsh Highland Railway, 10 June 2018 Important Safety Message
Derailment of a passenger train near Clogwyn y Gwin South foot crossing, Welsh Highland Railway, 10 June 2018 Important Safety Message This derailment demonstrates the importance of heritage railways ensuring that specific and appropriate inspections and checks are built into the vehicle maintenance and overhaul regimes to monitor the integrity of all safety critical components which could cause derailment in the event of failure, and also to ensure that such components are reassembled correctly after overhaul. This is of particular importance on narrow gauge lines and railways that operate in mountainous areas. Summary of the accident At approximately 12:15 hrs on 10 June 2018, a passenger train, travelling from Porthmadog to Caernarfon on the Welsh Highland Railway, became derailed close to Clogwyn y Gwin South footpath crossing. The crossing is approximately 0.75 miles (1.2 km) north of Rhyd Ddu station. The train was travelling at around the maximum permitted speed at this location of 10 mph (16 km/h). The leading wheelset of the locomotive derailed on a right-hand curve. The driver immediately applied the train’s brake and the train came to a stop in a distance of about 30 metres. The train was hauled by a ‘Garratt’ steam locomotive, number 143, and comprised nine coaches. There were 74 passengers and 7 members of staff on board the train. Rail Accident Investigation Branch Safety digest 06/2018: Clogwyn y Gwin Locomotive 143 at Rhyd Ddu station travelling in same direction (right to left of photograph) as at the time of derailment No injuries were reported amongst the passengers or crew. -
Rigging Terms
Appendices 209 Appendix (i) Personal safety equipment and first aid Riggers often have to wear helmets, gloves, eye protection, face masks and respirators and steel capped boots to protect themselves from injury. It is the responsibility of your employer to provide the necessary protective equipment. It is the responsibility of riggers to wear and use the equipment properly and where and when necessary. Safety helmets Safety helmets with chin straps must be worn wherever there is a risk of objects falling from above and on any work site where the hard hat sign is displayed. Helmets should comply with AS 1801 Industrial safety helmets. Gloves Riggers should wear close fitting pigskin gloves to protect hands from: • heat and abrasion • molten metal • sharp edges. Special purpose gloves may be required for protection against chemicals including acids, alkalis, solvents, fats and oils. Eye protection Wear eye protection that conforms to AS 1337 Eye protectors for industrial applications if you are likely to be exposed to: • physical damage caused by – flying particles, dust, molten metal • chemical damage caused by – toxic liquids, gases and vapours dusts • radiation damage caused by – sunlight, visible light, infra red, laser. Respiratory protection Riggers should wear a face mask that conforms to AS 1716 Respiratory protective devices if you are likely to be exposed to: • toxic gases and vapours • irritating dusts, such as silica. Inhalation of some chemical vapours and gases can cause death or a wide range of unpleasant symptoms including narcosis and headaches. Common dusts such as silica can cause lung disease later in life and is found wherever there is excavation, ie building sites, road works, tunnelling and mining. -
Narrow Cab/Splashers) LOCOMOTIVE KIT
Brassmasters Scale Models www.brassmasters.co.uk L&SWR/SOUTHERN RAILWAY DRUMMOND T9 4-4-0 (narrow cab/splashers) LOCOMOTIVE KIT Designed by Martin Finney 4MM SCALE OO - EM - P4 INSTRUCTIONS AND PROTOTYPE NOTES PO Box 1137 Sutton Coldfield B76 1FU Copyright Brassmasters 2017 SECTION 1: BRIEF HISTORICAL DETAILS The locomotives which form the subject of this kit are the original ‘narrow’ series of Dugald Drummond’s celebrated T9 4-4-0s for the LSWR. A total of 51 locomotives were built by Dubs & Co. and at Nine Elms Works under five Order Numbers as follows: Numbers Date Built Maker Works/ Order Number Firebox Water Tubes 702 - 719 2/1899 - 6/1899 Dubs & Co. 3746-3763 Yes 721 - 732 6/1899 - 1/1900 Dubs & Co. 3764-3775 Yes 773# 12/1901 Dubs & Co. 4038 Yes 113 - 122 6/1899 - 9/1899 Nine Elms G9 No 280 - 284 10/1899 - 11/1899 Nine Elms K9 No 285 - 289 1/1900 - 2/1900 Nine Elms O9 No # renumbered 733 12/1924 For a detailed history of this class I suggest you refer to the following definitive books by the late D.L.Bradley: Part two of 'The Locomotives of the L.S.W.R.’ published by the R.C.T.S. LSWR Locomotives - The Drummond Classes published by Wild Swan. Other valuable sources of information and photographs are: The Drummond Greyhounds of the LSWR - D.L.Bradley - David & Charles A Pictorial Record of Southern Locomotives - J.H.Russell - OPC Drummond Locomotives - Brian Haresnape & Peter Rowledge - Ian Allan Locomotives Illustrated No. 44 - The Drummond 4-4-0s and Double singles of the LSWR - Ian Allan Southern Steam Locomotive Survey - The Drummond Classes - Bradford Barton www.rail-online.co.uk – lots of prototype photographs Variations/Modifications incorporated into the kit Starting with numbers 702,709 & 724 in May 1923 the locomotives were extensively rebuilt involving new: Smokeboxes: new, larger, smokeboxes were fitted incorporating the ‘Eastleigh’ superheater. -
Rigging: Guide 1995
RIGGING GUIDE 1995 WorkCover. Watching out for you. New South Wales Government A guide to rigging Edited by David West Expert advice from Des Highfield, Ivan Bignold, Phil Court, Chris Turner, Barry Haines, Roy Cullen and Jack Campbell 1. Rigging 2. Certification 3. Occupational health and safety Second edition 1997 Disclaimer This publication may contain occupational health and safety and workers compensation information. It may include some of your obligations under the various legislations that WorkCover NSW administers. To ensure you comply with your legal obligations you must refer to the appropriate legislation. Information on the latest laws can be checked by visiting the NSW legislation website (www.legislation.nsw.gov.au) or by contacting the free hotline service on 02 9321 3333. This publication does not represent a comprehensive statement of the law as it applies to particular problems or to individuals or as a substitute for legal advice. You should seek independent legal advice if you need assistance on the application of the law to your situation. © WorkCover NSW Foreword This competency guide has been developed jointly by the WorkCover Authority of NSW and the Victorian WorkCover Authority. It is a major revision of the old and widely respected NSW publication, A guide for riggers. It has been structured to reflect the nationally uniform certificate classes for rigging and conform to the standards for rigging set out in the National OHS Certification Standard for Users and Operators of Industrial Equipment. The text is also consistent with the nationally uniform assessment instruments used by certificate assessors and a range of Australian Standards which cover equipment and work involved with rigging. -
The Investigation of Derailments.Pmd
THE INVESTIGATION OF DERAILMENTS AUGUST 2014 INDIAN RAILWAYS INSTITUTE OF CIVIL ENGINEERING, Pune 411001 i ii FOREWORD TO THE FOURTH EDITION It has been an endeavour of IRICEN to publish books containing the latest information on subjects useful for the railway engineers. This book ‘The Investigation of Derailments’ published by IRICEN has served the objective for more than three decades. Railway men of various disciplines have immensely benefited from the contents of this book. Third edition of the book was published in 2007. Since then, some new type of rolling stock have been introduced. Also, there have been changes in maintenance practices for rolling stock and track.IRICEN is bringing out this Fourth Edition of the book, incorporating these changes. I hope that the railway men would find this revised edition a useful source of the required information for a scientific investigation of derailments. Pune, Vishwesh Chaube August, 2014 Director IRICEN, PUNE iii PREFACE TO THE FOURTH EDITION The first edition of the book ‘The Investigation of Derailments’ was published in May, 1981 by Indian Railways Institute of Advance Track Technology (Presently known as Indian Railways Institute of Civil Engineering), Pune. Second edition of the book was published in May, 1995, in which a new chapter, incorporating case studies was added. Third edition of the book was published in March, 2007. In this edition, information related to CASNUB bogies, Fiat Bogies and new types of locomotives was incorporated. Subsequent to the publication of the 3rd edition of the book, significant developments have taken place relating to rolling stock running on the Indian Railways network .Some new type of rolling stock have been introduced. -
Patriot 4-6-0
Brassmasters Scale Models PO Box 1137 Sutton Coldfield West Midlands B76 1FU www.brassmasters.co.uk LMS Unrebuilt Patriot 4-6-0 Prototype notes and instructions Copyright Brassmasters 1996 FOREWORD The Patriot marks our first departure from the “pure” Stanier locomotive with its parallel boiler and simple Belpaire firebox. In some ways it brings together our LNWR and LMS kits because its origins are partly LNWR, as a final development of the Claughton line, combined with the emerging LMS school via the Royal Scot. The later examples of the class included some of the soon to be standard Stanier features. A true hybrid, and therein perhaps lies the attraction of the class. Whilst nominally a standard LMS type, the Patriot was so different in appearance from the legions of Stanier locomotives which followed it that its “old fashioned”, to some even ugly, looks provide its charm. It is almost 35 years since the last Patriot was withdrawn and none were preserved. It is no exaggeration to state that this has been by far the most difficult of our kits to research. We searched for over four years for an official drawing of the complete locomotive to ensure the correct relationship between the main components. We had very large scale drawings for the dome and chimney but nothing on the frames and boiler. The artwork for the chassis was virtually complete when Geoff Hurley unearthed side and end Pipe and Rod drawings. The good news was that it confirmed our educated guesswork to be essentially correct; the bad news was that the frames, brake gear and bogie had to be redrawn. -
ESR 0540 Version of the Document Asinusebyrailcorp
Engineering Standard Rolling Stock ESR 0540 OVERHAUL OF 48 CLASS LOCOMOTIVE BOGIES Version 1.0 Issued June 2010 Owner: Chief Engineer Rolling Stock Approved Stephen White, Authorised Michael Uhlig, by: Technical Specialist Rolling by: Manager, Stock Performance Standards, Rolling Stock Access Integrity Rolling Stock Access Integrity Engineering Standard Disclaimer This document was prepared for use on the RailCorp Network only. RailCorp makes no warranties, express or implied, that compliance with the contents of this document shall be sufficient to ensure safe systems or work or operation. It is the document user’s sole responsibility to ensure that the copy of the document it is viewing is the current version of the document as in use by RailCorp. RailCorp accepts no liability whatsoever in relation to the use of this document by any party, and RailCorp excludes any liability which arises in any manner by the use of this document. Copyright The information in this document is protected by Copyright and no part of this document may be reproduced, altered, stored or transmitted by any person without the prior consent of RailCorp. UNCONTROLLED WHEN PRINTED Page 1 of 21 RailCorp Engineering Standard — Rolling Stock Overhaul of 48 class locomotive bogies ESR 0540 Document control Revision Date Summary of change (RSS 0540) 1.0 August 2007 Based on TRS 1082 (RSS 0540) 1.1 Mar 2008 References to some RSS standards amended (ESR 0540 1.0 June 2010 Reformatted and renumbered ESR 0540 Summary of changes from previous version Summary of change Section NOTE – If the final document is small enough for the ‘Contents’ and ‘Document control’ to fit on one page remove the page break between the existing pages 2 and 3. -
G.275/Wssr-071718/2017-18 Work Study to Review the Staff Strength at Boiler Shop-Goc
1 G.275/WSSR-071718/2017-18 WORK STUDY TO REVIEW THE STAFF STRENGTH AT BOILER SHOP-GOC 2 SOUTHERN RAILWAY PLANNING BRANCH G.275/WSSR-071718/2017-18 WORK STUDY TO REVIEW THE STAFF STRENGTH AT BOILER SHOP -GOC STUDIED BY WORK STUDY TEAM OF G.275/WSSR-121617/2016-17 PLANNING BRANCH AUGUST - 2017 . 3 I N D E X SERIAL CONTENTS PAGE NUMBER NUMBER (i) ACKNOWLEDGEMENT 1 (ii) TERMS OF REFERENCE (iii) METHODOLOGY (iv) SUMMARY OF RECOMMENDATIONS 2 CHAPTERS I INTRODUCTION 3-8 II PRESENT SCENARIO 9-17 III CRITICAL ANALYSIS 18-22 IV PLANNING BRANCH REMARKS ON CO-ORDINATING 23 OFFICER’S VIEWS V FINANCIAL SAVINGS 24 ANNEXURES I BOILER SHOP DETAILS 25-34 II TRAINING DETAILS 35 III IR CODE FOR MECH WORKSHOPS 36-37 IV CO-ORDINATING OFFICER’S VIEWS 38 . 1 (i) ACKNOWLEDGEMENT The work study team acknowledges the valuable guidance given by Dy.CME/GOC,PE/GOC,APE/GOC, SSE/Planning, SSE/Boiler Shop and the staff of Shop which was very helpful in completing the study in time. (ii) AUTHORITY Annual programme of work studies for the year 2017-18 (iii) TERMS OF REFERENCE Work study to review the staff strength at Boiler Shop/GOC (iv) METHODOLOGY The work study team has applied the following techniques in conducting the work study. (1) Collection and compilation of Data. (2) Observation of present system of working. (3) Interaction with Dy.CME/GOC,PE/GOC,APE/GOC, SSE/Planning, SSE/Boiler Shop and the staff of Shop (4) Discussion with Officers and Supervisors (5) Provision as per AT/TT/yardstick/requirement as deemed fit. -
Download the Instructions
Brassmasters Scale Models www.brassmasters.co.uk L&SWR/SOUTHERN RAILWAY ADAMS T3 4-4-0 LOCOMOTIVE KIT Designed by Martin Finney 4MM SCALE OO - EM - P4 INSTRUCTIONS AND PROTOTYPE NOTES PO Box 1137 Sutton Coldfield B76 1FU Copyright Brassmasters 2017 SECTION 1: BRIEF HISTORICAL DETAILS The twenty locomotives, which form the subject of this kit, were to the design of William Adams for the LSWR. Numbered 557-76 they were built at Nine Elms from December 1892 to November 1893. They were attached to Adams 3300 gallon tenders. Most were withdrawn between October 1930 and August 1933 but two, 563 and 571, survived into the 1940s, No. 563 being the last to stop working in August 1945. No. 563 is preserved and largely restored to its original condition in the Adams livery. It can be seen at The National Railway Museum at York. For a detailed history of this class I suggest you refer to the following definitive books by the late D.L.Bradley: Part two of 'The Locomotives of the L.S.W.R’. published by the R.C.T.S. LSWR Locomotives - The Adams Classes published by Wild Swan. Other valuable sources of information and photographs are: Locomotives Illustrated No. 124 – Adams LSWR 4-4-0s – RAS Publishing A Pictorial Record of Southern Locomotives - J.H.Russell - OPC Southern Steam Locomotive Survey - The Adams Classes - Bradford Barton The LSWR at Nine Elms: Vol. 1. – Barry Curl – KRB Publications With a life of fifty years, many detail modifications to the locomotives took place. Many of these I have attempted to cover by including alternative components in the kit, however it is essential to have a photograph of the individual locomotive you propose to construct to enable an authentic model to be built. -
08 OCT 2015 RUN DATE Page 1
SOUTHERN RAILWAY RUN DATE 08 OCT 2015 Page 1 LIST OF PURCHASE ORDER VALUED LESS THAN Rs.20 Lakhs RELEASED BETWEEN 01-SEP-15 AND 15-SEP-15 PO NO PO BASIC CAL PO Date TENDER NO SNo SR NO CONSIGNEE QTY RATE DD PLNO-DESCRIPTION TAXES MODE Firm Details OPENED ON %/RS AMOUNT 1 28150113103149 28150113 001 SMM/DSL/ED 2.00 NOS. 5100.00 30-04-2016 12200359-REVERSE CURRENT DIODE PANEL ED % 12.5 1275 01-SEP-15 10-AUG-15 TO DLW PART NO-1238 6017 AND DLW DRG ST- % 5 573.75 NO. EL/PT/0657 FIRM'S OFFER: FIRM'S TYPE Central SIRVEEN CONTROL SYSTEMS PVT. LTD NO:SRCD-25 PLOT NO A-7/1,GROUND &FIRST FLOOR, 002 AMM/DSD/GOC 8.00 NOS. 5100.00 30-04-2016 12200359-REVERSE CURRENT DIODE PANEL ED % 12.5 5100 ELECTRONIC COMPLEX TO DLW PART NO-1238 6017 AND DLW DRG KUSHAIGUDA ST- % 5 2295 NO. EL/PT/0657 FIRM'S OFFER: FIRM'S TYPE Central HYDERABAD NO:SRCD-25 PO VALUE:162658 003 SMM/DSSD/GOC 6.00 NOS. 5100.00 30-04-2016 12200359-REVERSE CURRENT DIODE PANEL ED % 12.5 3825 TO DLW PART NO-1238 6017 AND DLW DRG ST- % 5 1721.25 NO. EL/PT/0657 FIRM'S OFFER: FIRM'S TYPE Central NO:SRCD-25 004 AMM/DSD/ERS 4.00 NOS. 5100.00 30-04-2016 12200359-REVERSE CURRENT DIODE PANEL ED % 12.5 2550 TO DLW PART NO-1238 6017 AND DLW DRG ST- % 5 1147.5 NO. -
Flexichas Or a Way to Build a Fully Compensated Chassis Pdf Free
FLEXICHAS OR A WAY TO BUILD A FULLY COMPENSATED CHASSIS PDF, EPUB, EBOOK M. Sharman | 36 pages | 31 Dec 1997 | Stenlake Publishing | 9780860930723 | English | Catrine, United Kingdom Flexichas or a Way to Build a Fully Compensated Chassis PDF Book How it works Knowing that the centre of gravity of the complete loco lies between axles 1 and 2, axle 3 could in theory be dispensed with and the loco would balance on axles 1 and 2 alone, like an off-centre Got out the rivet punch once all sides were properly shaped. Spectacles on the windows were created from thin cuts of 6mm brass tube filed and sanded until smooth and thin. It is not possible to cover every possible variation of suspension arrangements for every possible wheel arrangement, but it is hoped that the following sections, which contain examples of both good and less good practice, will provide enough material on which sensible judgements can be made and sensible solutions achieved. Used, Mike french models Mike french models. Another convenient way of viewing how three-point suspension works is by inverting the stool, i. Very well done! The lower the centre of gravity of the loco, the less any transverse shift of the effective centre of gravity line will be. If all is running freely and the loco isn't suffering wheelspin, it shouldn't occur, but nude certain conditions e. Figure 6 illustrates this principle. Equations concerning such deflections are beyond the scope of this Digest sheet — see annex 9. Colin R Posted August 7. Best way to do projects, all together! I think I'm lost with it!! A springy equalising beam need not be subject to the limit of 'only three points' of rigid beam three-point suspension. -
Common Maintenance Schedule of 140T Crane (Gottwald & Cowans
qKfr {fFbR - td qildq Government of India-Ministry of Railways wguun ofi6w sik qrfi dTr{ Research Designs & Standards Organisation qIGFI\F - 226011 Lucknow -226011 EPBX (0522)2451200 otD (0522)2450115 Fax (0522) 2458500 DrD (0522) 2465310 No. SD.CRMG Date: 04.07.2018 The Chief Motive Power Engineer/Dsl, 1. Central Railway, CST Mumbai - 400 001. 2. Eastern Railway, Fairlie place, Kolkata - 700 OO1. g44101 3. East Central Railway, Hajipu r - . 4. East coast Railway, Rail Vihar, B-2, Bhubaneshwar - Ts1 017 5. Northern Railway, Baroda House, New Delhi - 110 001. 6. North Central Railway, Allahabad - 211 OO1. 7. North Eastern Railway, Gorakhpur - 273 OO1. 8. Northeast Frontier Railway, Maligaon, Guwahat -791 011. 9. North Western Railway, Jaipur - 302 006. 10. southern Railway Park rown, chennai - 600 003. 11. south central Railway, Rail Nilayam, secunderabad - 500 or1 . 12. south Eastern Railway, Garden Reach, Kolkata - Too 043. 13. South East Central Railway, Bilaspur - 495 004. 14. South Western Railway, Hubli - 580 023. 15. Western Railway, Churchgate, Mumbai - 400 001. 16. West Central Railway, Jabalpur - 492 OO1 17.Dy. CME/JMP (Crane), Locomotive Ws Eastern Railway, Jamalpur - 811 214. 18. Dy. CME/PR (Diesel), Locomotive Ws Parel Central naituay, Mumbai - 40OOO1. Sub: Common Maintenance Schedule for 14OT diesel hydraulic breakdown cranes (Gottwald & Cowans Sheldon design). Ref: Railway Board's letter no.2011lM (M&P)t17it3inn dated 04.0g.2017. With reference to above, as per directives of Railway Board, a common Maintenance Schedule no. MP.MI-37 (Rev.-00) June'2018 for 14Ot diesel hydraulic breakdown cranes (Gottwald & Cowans Sheldon design) has been finaliied by incorporating the recommendations of SAG & JAG committe"s, suggestions-tie & inputs from Jamalpur Wshop, Parel Wshop & user Railways.