Thermal Contact Conductance in a Vacuum'' and Related Parameter Study 2
Total Page:16
File Type:pdf, Size:1020Kb
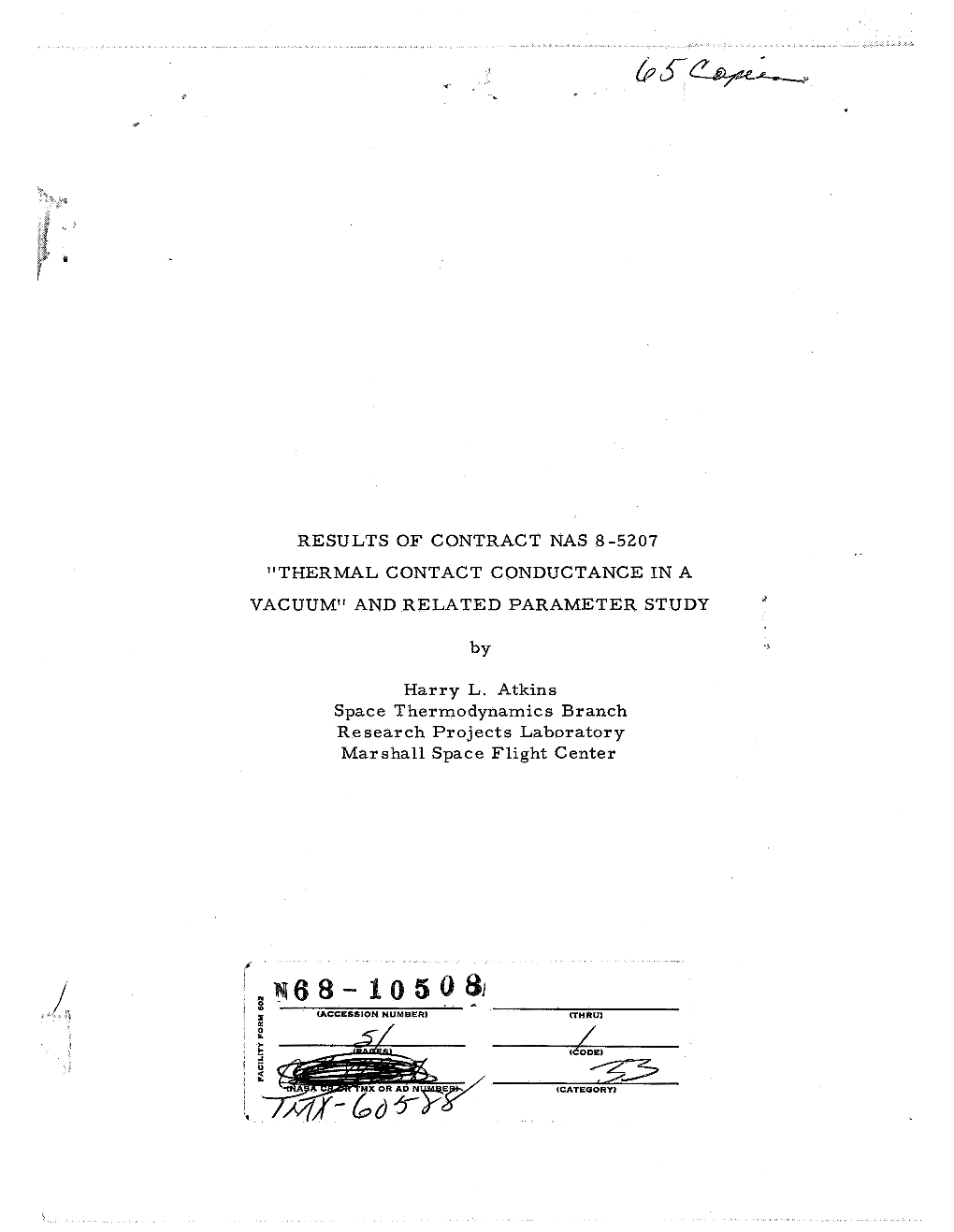
Load more
Recommended publications
-
A Study Into the Localized Corrosion of Magnesium Alloy Magnox Al-80
A Study into the Localized Corrosion of Magnesium Alloy Magnox Al-80 Ronald N. Clark‡*, James Humpage**, Robert Burrows*, Hugh Godfrey***, Mustufa Sagir****, Geraint Williams** ‡Corresponding author. E-mail: [email protected]. *National Nuclear Laboratory, Unit 102B, Sperry Way, National Nuclear Laboratory, Stonehouse, GL10 3UT, UK **Swansea University, Materials Research Centre, Bay Campus, Fabian Way, Crymlyn Burrows, Swansea, SA1 8EN, Wales, UK ***National Nuclear Laboratory, Workington Laboratory, Havelock Road, Derwent Howe, Workington, Cumbria, CA14 3YQ, UK ****Sellafield Limited, Hinton House, Birchwood Park Avenue, Risley, Warrington, Cheshire, WA3 6 GR, UK [email protected] [email protected] [email protected] [email protected] [email protected] ABSTRACT Magnesium (Mg) non-oxidizing alloy, known as Magnox, was historically used as a fuel cladding material for the first-generation of carbon dioxide (CO2) gas-cooled nuclear reactors in the UK. Waste Magnox is currently stored in cooling ponds, pending final disposal. The corrosion resistance of Mg and its alloys is relatively poor, compared to modern cladding materials such as zirconium (Zr) alloys, so it is important to have a knowledge of the chloride concentration/pH dependence on breakdown and localized corrosion characteristics prior to waste retrievals taking place. Our results show that Magnox exhibits passivity in high pH solutions, with charge transfer resistance and passive film thicknesses showing an increase with immersion time. When chloride is added to the system the higher pH maintains Magnox passivity, as shown through a combination of potentiodynamic and time-lapse/post corrosion imaging experiments. Potentiodynamic polarization of Magnox reveals a -229 mV-decade linear dependence of breakdown potential with chloride ion concentration. -
WATTS 04-2013 P1 PARC Management Team / Bestuurspan Aug
04-2013 WATTS Year 83 + 4m Monthly newsletter of the Pretoria Amateur Radio Club Maandelikse nuusbrief van die Pretoria Amateur Radio Klub. PARC, PO Box 73696, Lynnwood Ridge 0040, RSA web http://www.parc.org.za mail: [email protected] Bulletins: 145,725 MHz 08:45 Sundays/Sondae Relays: 1.840, 3.700, 7.066, 10.135, 14.235, 51.400, 438.825, 1297 MHz ZR6FD logo Activated frequencies are announced prior to bulletins Papier / Paper Drukwerk ZS6RH Swapshop: 2m and 7.066 MHz Live on-air after bulletins ZS6RH Bulletin repeats Mondays | herhalings : Maandae 2m 19:45 Another glimpse of the extensive facility operated by Iain-ZS5IE (more photos on QRZ.com) In this issue In hierdie uitgawe Next club events Fleamarkets at PMC Member news and activities Lede-nuus en Aktiwiteite Wed 1 May (public holiday) Sat 10 Aug Sat 7 Dec Technical Rig reviews Tegnies Club social at U.P. G7FEK limited space antenna Thursday 4 Apr 7pm Aluminium alloys Club committee meeting ● Page eight -- Bladsy agt Thursday 18 Apr 7pm WATTS 04-2013 p1 PARC Management team / Bestuurspan Aug. 2012 – Aug. 2013 Committee members Chairman, Contests Pierre Holtzhausen ZS6PJH [email protected] 012-655-0726 082-575-5799 Vice Chairman, SARL liason Fritz Sutherland ZS6SF [email protected] 012-811-3875 083-304-0028 Secretary, Clubs, Strategy Jean de Villiers ZS6ARA [email protected] 012-663-6554 083-627-2506 Treasurer, SARS Andre van Tonder ZS6BRC [email protected] 361-3292 082-467-0287 Rallies, Social Johan de Bruyn ZS6JHB [email protected] 012-803-7385 079-333-4107 Webmaster Graham Reid ZR6GJR [email protected] 083-701-0511 RAE, Bulletin co-ordinator Vincent Harrison ZS6BTY [email protected] 012-998-8165 083-754-0115 Repeaters, Technical Craig Symington ZS6RH [email protected] 081-334-6817 Technical, Kits. -
Maec.19 70 (University of London) London
COMPLEX & INCREMENTAL STRESS CREEP OF A HIGH STRENGTH ALUMINIUM ALLOY AT ELEVATED TEMPERATURES (ALLOY: HIDUMINIUM RR58 SPECIFICATION DTD 731) by SURINDAR BAHADUR MATHUR Thesis presented in the Department of Mechanical Engineering for the Award of the Doctor of Philosphy in Mechanical Engineering of the University of London. Mechanical Engineering Department Imperial College of Science and Technology mAec.19 70 (University of London) London. ABSTRACT A theory for creep rates under complex and incremental stresses is deduced from experimental data concerning complex creep at elevated temperatures for the test material HIDUMINIUM RR 58 - Specification DID 731. The most important results are for tubular specimens tested at 150°C and 250°C under incremental loads. The analysis of results relates to steady state creep only. Modified relationships in stress equivalence and strain equivalence are proposed to account for thermal softening, polygonization, recrystallization and the resulting exaggerated flow in the direction of the applied shear. (The original equations are based on the hypothesis of Von Mises). A further relationship is suggested between the immediate total energy of distortion and the subsequent creep work rate. Results of the static tests and the results of the tests for creep behaviour under complex loading are presented and compared with the results of static torsion and simple incremental torsion creep tests on the basis of the proposed equations. An appendix describes the complex creep testing machine, furnace, extensometers -
Microstructual Characteristics of Magnesium Metal Matrix Composites
University of Central Florida STARS Electronic Theses and Dissertations, 2004-2019 2012 Microstructual Characteristics Of Magnesium Metal Matrix Composites Dongho Shin University of Central Florida Part of the Materials Science and Engineering Commons Find similar works at: https://stars.library.ucf.edu/etd University of Central Florida Libraries http://library.ucf.edu This Masters Thesis (Open Access) is brought to you for free and open access by STARS. It has been accepted for inclusion in Electronic Theses and Dissertations, 2004-2019 by an authorized administrator of STARS. For more information, please contact [email protected]. STARS Citation Shin, Dongho, "Microstructual Characteristics Of Magnesium Metal Matrix Composites" (2012). Electronic Theses and Dissertations, 2004-2019. 2244. https://stars.library.ucf.edu/etd/2244 MICROSTRUCTUAL CHARACTERISTICS OF MAGNESIUM METAL MATRIX COMPOSITES by DONGHO SHIN B.S. Korea Military Academy, 2006 A thesis submitted in partial fulfillment of the requirements for the degree of Master of Science in the Department of Mechanical, Materials and Aerospace Engineering in the College of Engineering and Computer Science at the University of Central Florida Orlando, Florida Summer Term 2012 Major Professor: Yongho Sohn 1 © 2012 Dongho Shin ii ABSTRACT Magnesium (Mg) Metal matrix composites (MMCs) reinforced by ceramic reinforcements are being developed for a variety of applications in automotive and aerospace because of their strength-to-weight ratio. Reinforcement being considered includes SiC, Al2O3, Carbon fiber and B4C in order to improve the mechanical properties of MMCs. Microstructural and interfacial characteristics of MMCs can play a critical role in controlling the MMCs’ mechanical properties. This study was carried out to understand the microstructural and interfacial development between Mg-9wt.Al-1wt.Zn (AZ91) alloy matrix and several reinforcements including SiC, Al2O3, Carbon fibers and B4C. -
Aluminium Alloys Chemical Composition Pdf
Aluminium alloys chemical composition pdf Continue Alloy in which aluminum is the predominant lye frame of aluminum welded aluminium alloy, manufactured in 1990. Aluminum alloys (or aluminium alloys; see spelling differences) are alloys in which aluminium (Al) is the predominant metal. Typical alloy elements are copper, magnesium, manganese, silicon, tin and zinc. There are two main classifications, namely casting alloys and forged alloys, both further subdivided into heat-treatable and heat-free categories. Approximately 85% of aluminium is used for forged products, e.g. laminated plates, foils and extrusions. Aluminum cast alloys produce cost-effective products due to their low melting point, although they generally have lower tensile strength than forged alloys. The most important cast aluminium alloy system is Al–Si, where high silicon levels (4.0–13%) contributes to giving good casting features. Aluminum alloys are widely used in engineering structures and components where a low weight or corrosion resistance is required. [1] Alloys composed mostly of aluminium have been very important in aerospace production since the introduction of metal leather aircraft. Aluminum-magnesium alloys are both lighter than other aluminium alloys and much less flammable than other alloys containing a very high percentage of magnesium. [2] Aluminum alloy surfaces will develop a white layer, protective of aluminum oxide, if not protected by proper anodization and/or dyeing procedures. In a wet environment, galvanic corrosion can occur when an aluminum alloy is placed in electrical contact with other metals with a more positive corrosion potential than aluminum, and an electrolyte is present that allows the exchange of ions. -
Magnox Corrosion
Department Of Materials Science & Engineering From Magnox to Chernobyl: A report on clearing-up problematic nuclear wastes Sean T. Barlow BSc (Hons) AMInstP Department of Materials Science & Engineering, The University of Sheffield, Sheffield S1 3JD, UK IOP Nuclear Industry Group, September 28 | Warrington, Cheshire, UK Department Of Materials Science & Engineering About me… 2010-2013: Graduated from University of Salford - BSc Physics (Hons) Department Of Materials Science & Engineering About me… 2013-2018: Started on Nuclear Fission Research Science and Technology (FiRST) at the University of Sheffield Member of the Immobilisation Science Laboratory (ISL) group • Wasteforms cement, glass & ceramic • Characterisation of materials (Trinitite/Chernobylite) • Corrosion science (steels) Department Of Materials Science & Engineering Department Of Materials Science & Engineering Fully funded project based PhD with possibility to go on secondment • 3-4 month taught course at Manchester • 2 mini-projects in Sheffield • 3 years for PhD + 1 year write up • Funding available for conferences and training • Lots of outreach work • Site visits to Sellafield reprocessing facility, Heysham nuclear power station & Atomic Weapons Authority Department Of Materials Science & Engineering Fully funded project based PhD with possibility to go on secondment • 3-4 month taught course at Manchester • 2 mini-projects in Sheffield • 3 years for PhD + 1 year write up • Funding available for conferences and training • Lots of outreach work • Site visits to Sellafield reprocessing facility, Heysham nuclear power station & Atomic Weapons Authority Department Of Materials Science & Engineering Department Of Materials Science & Engineering 2017: Junior Project Manager at DavyMarkham Department Of Materials Science & Engineering PhD projects… 4 main projects 1. Magnox waste immobilisation in glass 2. -
The Effect of Yttrium on Wear, Corrosion and Corrosive Wear Of
The Effect of Yttrium on Wear, Corrosion and Corrosive Wear of Mg-Al Alloys by Meisam Nouri A thesis submitted in partial fulfillment of the requirements for the degree of Doctor of Philosophy in Materials Engineering Department of Chemical and Materials Engineering University of Alberta c Meisam Nouri, 2017 Abstract Magnesium remarkably deserves considerable interest from industry especially trans- portation sector because of its high strength to weight ratio. However, poor wear resistance and low corrosion resistance of magnesium are barriers to extend use of its alloys. Yttrium is one of rare-earth elements which has been demonstrated effectiveness in improving the corrosion resistance and tribological properties of some metallic alloys. In this work, the effects of yttrium on wear, corrosion and corrosive wear of as-cast Mg-3 wt% Al and AZ31 alloys were investigated. It was shown that the added yttrium increased the dry wear resistance of the alloys through the formation of a harder second phases. The corrosion resistance of the alloys was evaluated in tap water and salt solution. A small amount of added Y improved the corrosion resistance but such benefit de- creased at higher yttrium contents. Corrosive wear tests were performed in the same environment for the alloys. The improvement in corrosive wear resistance mainly came from the reduction of corrosion-wear synergy caused by the added yttrium, which in- creased both hardness and corrosion resistance. Relevant mechanisms to express the observations and the correlation between the performance and microstructure were analyzed and discussed in details. In addition to modification of the corrosion potential of bulk magnesium through alloying elements, tailoring its surface oxide film is an alternative approach for en- hanced resistance to corrosion. -
Advanced Materials for Light Weight Body Design
ISSN (Online): 2319-8753 ISSN (Print) : 2347-6710 International Journal of Innovative Research in Science, Engineering and Technology (A High Impact Factor, Monthly, Peer Reviewed Journal) Visit: www.ijirset.com Vol. 7, Issue 1, January 2018 Advanced Materials for Light Weight Body Design Tejas Pawar1, Atul Ekad2, Nitish Yeole3, Aditya Kulkarni4, Ajinkya Taksale5 BE-Mech. (2016), Dept. of Mechanical Engineering, VIIT, Pune, India.1 BE-Mech. (2016), Dept. of Mechanical Engineering, NBN Sinhgad School of Engineering, Pune, India.2 BE-Mech. (2016), Dept. of Mechanical Engineering, NBN Sinhgad School of Engineering, Pune, India.3 BE-Mech. (2017), Dept. of Mechanical Engineering, RMD Sinhgad School of Engineering, Pune, India.4 BE-Mech. (2016), Dept. of Mechanical Engineering, VPK Bajaj Inst. of Engg. & Technology, Baramati, India.5 ABSTRACT: With the emergent industrial development and dependence on fossil fuels, Green House Gas (GHG) emission has become most important problem. However, car manufacturers have to remain in competition with peers and design their products innovatively that fulfil the new regulations too. Nevertheless of various different approaches to improve fuel economy such as enhancing fuel quality, development of high performance engines and fuel injection system, weight reduction is one of the encouraging approaches. With 10% weight reduction in passenger cars, the fuel economy improves by as much as 6–8%. KEYWORDS: Carbon Fibre, Magnesium, Aluminium, Titanium, light-weight body materials, poly-acrylonitrile I. INTRODUCTION Car body design in view of structural performance and weight reduction is a challenging task due to the various performance objectives that must be satisfied such as vehicle safety, fuel efficiency, endurance and ride quality. -
Radioactive Regions Detection
Bachelor Project Czech Technical University in Prague Faculty of Electrical Engineering F3 Department of Cybernetics Radioactive regions detection Jan Charvát Supervisor: Ing. Vladimír Smutný, Ph.D. Supervisor–specialist: Ing. Daniel Seifert, Ph.D. Field of study: Cybernetics and Robotics Subfield: Robotics May 2017 ii Czech Technical University in Prague Faculty of Electrical Engineering Department of Cybernetics BACHELOR PROJECT ASSIGNMENT Student: Jan C h a r v á t Study programme: Cybernetics and Robotics Specialisation: Robotics Title of Bachelor Project: Radioactive Regions Detection Guidelines: 1. Get familiar with the problem of radioactive waste sorting. 2. Analyze the radioactive properties of radioactive waste. 3. Analyze the properties of radioactivity detectors in relationship to chosen radioactive waste. 4. Recommend the arrangement of the system for detection of hot-spots in the radioactive waste. 5. Make conclusions. Bibliography/Sources: [1] V. Majer a kol.: Základy užité jaderné chemie. SNTL Praha, 1985. [2] https://www.remm.nlm.gov/civilian.htm [3] J. Doležal, J. Šťastný, J. Špetlík, S. Bouček: Jaderné a klasické elektrárny - 1. odborná učebnice pro VŠ obor energetika, 2011, http://www.mpo-efekt.cz/uploads/7799f3fd595eeee1fa66875530f33e8a/cvut-1-elektrarny.pdf Bachelor Project Supervisor: Ing. Vladimír Smutný, Ph.D. Valid until: the end of the summer semester of academic year 2017/2018 L.S. prof. Dr. Ing. Jan Kybic prof. Ing. Pavel Ripka, CSc. Head of Department Dean Prague, January 10, 2017 iv Acknowledgements Declaration I would like to thank Ing. Vladimír I declare that the presented work was Smutný Ph.D. for his support and his developed independently and that I advice throughout this difficult project. -
Questions for ACMT 1. the Tendency of a Deformed Solid to Regain Its
Questions for ACMT 1. The tendency of a deformed solid to regain its actual proportions instantly upon unloading known as _ a) Perfectly elastic b) Delayed elasticity c) Inelastic effect d) Plasticity 2. How is Young’s modulus of elasticity defined? 3. The permanent mode of deformation of a material known as _____________ a) Elasticity b) Plasticity c) Slip deformation d) Twinning deformation 4. The ability of materials to develop a characteristic behavior under repeated loading known as ______ a) Toughness b) Resilience c) Hardness d) Fatigue 5. What is the unit of tensile strength of a material? a) engineering-materials-metallurgy-questions-answers-mechanical-properties-q5 b) kg/cm2 c) engineering-materials-metallurgy-questions-answers-mechanical-properties-q5-2 d) cm2/kg 6. Which of the following factors affect the mechanical properties of a material under applied loads? a) Content of alloys b) Grain size c) Imperfection and defects d) Shape of material 7. The ability of a material to resist plastic deformation known as _____________ a) Tensile strength b) Yield strength c) Modulus of elasticity d) Impact strength 8. The ability of a material to be formed by hammering or rolling is known as _________ a) Malleability b) Ductility c) Harness d) Brittleness 9. What type of wear occurs due to an interaction of surfaces due to adhesion of the metals? a) Adhesive wear b) Abrasive wear c) Fretting wear d) Erosive wear 10. Deformation that occurs due to stress over a period of time is known as ____________ a) Wear resistance b) Fatigue c) Creep d) Fracture 11. -
Silver and Gold Coating
Copyright © Tarek Kakhia. All rights reserved. http://tarek.kakhia.org Gold & Silver Coatings By A . T . Kakhia 1 Copyright © Tarek Kakhia. All rights reserved. http://tarek.kakhia.org 2 Copyright © Tarek Kakhia. All rights reserved. http://tarek.kakhia.org Part One General Knowledge 3 Copyright © Tarek Kakhia. All rights reserved. http://tarek.kakhia.org 4 Copyright © Tarek Kakhia. All rights reserved. http://tarek.kakhia.org Aqua Regia ( Royal Acid ) Freshly prepared aqua regia is colorless, Freshly prepared aqua but it turns orange within seconds. Here, regia to remove metal fresh aqua regia has been added to these salt deposits. NMR tubes to remove all traces of organic material. Contents 1 Introduction 2 Applications 3 Chemistry 3.1 Dissolving gold 3.2 Dissolving platinum 3.3 Reaction with tin 3.4 Decomposition of aqua regia 4 History 1 - Introduction Aqua regia ( Latin and Ancient Italian , lit. "royal water"), aqua regis ( Latin, lit. "king's water") , or nitro – hydro chloric acid is a highly corrosive mixture of acids, a fuming yellow or red solution. The mixture is formed by freshly mixing concentrated nitric acid and hydro chloric acid , optimally in a volume ratio of 1:3. It was named 5 Copyright © Tarek Kakhia. All rights reserved. http://tarek.kakhia.org so because it can dissolve the so - called royal or noble metals, gold and platinum. However, titanium, iridium, ruthenium, tantalum, osmium, rhodium and a few other metals are capable of with standing its corrosive properties. IUPAC name Nitric acid hydro chloride Other names aqua regia , Nitro hydrochloric acid Molecular formula HNO3 + 3 H Cl Red , yellow or gold Appearance fuming liquid 3 Density 1.01–1.21 g / cm Melting point − 42 °C Boiling point 108 °C Solubility in water miscible in water Vapor pressure 21 mbar 2 – Applications Aqua regia is primarily used to produce chloro auric acid, the electrolyte in the Wohl will process. -
Nuclear Reactor Types
Nuclear Reactor Types An Environment & Energy FactFile provided by the IEE Nuclear Reactor Types Published by The Institution of Electrical Engineers Savoy Place London WC2R 0BL November 1993 This edition November 2005 ISBN 0 85296 581 8 The IEE is grateful to the following organisations for permitting their material to be reproduced: Nuclear Electric The cover photograph shows Sizewell B Nuclear Power Station under construction Nuclear Reactor Types NUCLEAR REACTOR TYPES Many different reactor systems have been proposed and some of these have been developed to prototype and commercial scale. Six types of reactor (Magnox, AGR, PWR, BWR, CANDU and RBMK) have emerged as the designs used to produce commercial electricity around the world. A further reactor type, the so-called fast reactor, has been developed to full-scale demonstration stage. These various reactor types will now be described, together with current developments and some prototype designs. Gas Cooled, Graphite Moderated Of the six main commercial reactor types, two (Magnox and AGR) owe much to the very earliest reactor designs in that they are graphite moderated and gas cooled. Magnox reactors (see Fig 1.1(a)) were built in the UK from 1956 to 1971 but have now been superseded. The Magnox reactor is named after the magnesium alloy used to encase the fuel, which is natural uranium metal. Fuel elements consisting of fuel rods encased in Magnox cans are loaded into vertical channels in a core constructed of graphite blocks. Further vertical channels contain control rods (strong neutron absorbers) which can be inserted or withdrawn from the core to adjust the rate of the fission process and, therefore, the heat output.