Waldie 2005 Copyright © 2005 by James Waldie. Published by The
Total Page:16
File Type:pdf, Size:1020Kb
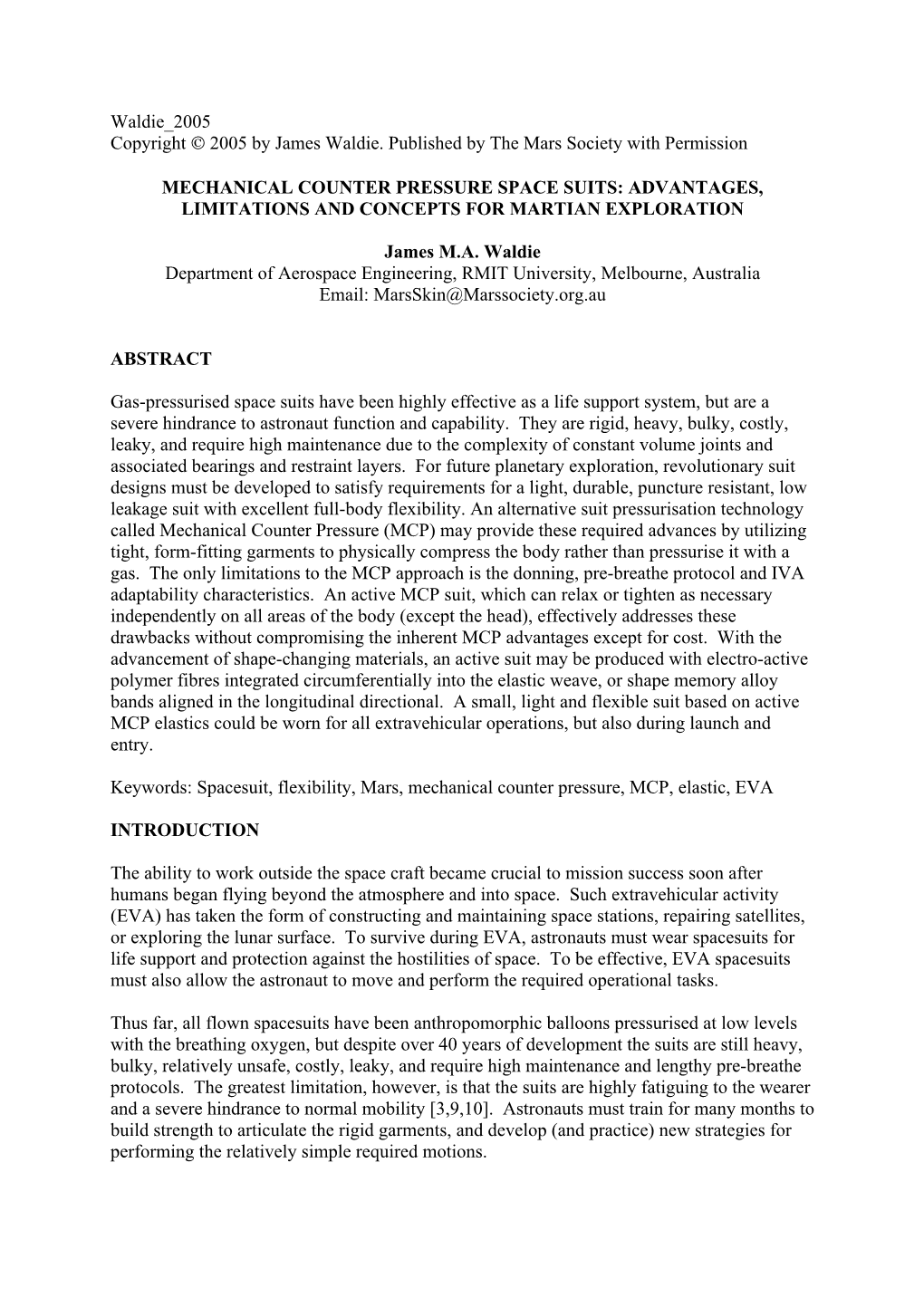
Load more
Recommended publications
-
2020 Crew Health & Performance EVA Roadmap
NASA/TP-20205007604 Crew Health and Performance Extravehicular Activity Roadmap: 2020 Andrew F. J. Abercromby1 Omar Bekdash4 J. Scott Cupples1 Jocelyn T. Dunn4 E. Lichar Dillon2 Alejandro Garbino3 Yaritza Hernandez4 Alexandros D. Kanelakos1 Christine Kovich5 Emily Matula6 Matthew J. Miller7 James Montalvo6 Jason Norcross4 Cameron W. Pittman7 Sudhakar Rajulu1 Richard A. Rhodes1 Linh Vu8 1NASA Johnson Space Center, Houston, Texas 2University of Texas Medical Branch, Galveston, Texas 3GeoControl Systems Inc., Houston, Texas 4KBR, Houston, Texas 5The Aerospace Corporation, Houston, Texas 6Stinger Ghaffarian Technologies (SGT) Inc., Houston, Texas 7Jacobs Technology, Inc., Houston, Texas 8MEI Technologies, Inc., Houston, Texas National Aeronautics and Space Administration Johnson Space Center Houston, Texas 77058 October 2020 The NASA STI Program Office ... in Profile Since its founding, NASA has been dedicated to the • CONFERENCE PUBLICATION. advancement of aeronautics and space science. The Collected papers from scientific and NASA scientific and technical information (STI) technical conferences, symposia, seminars, program plays a key part in helping NASA or other meetings sponsored or maintain this important role. co-sponsored by NASA. The NASA STI program operates under the • SPECIAL PUBLICATION. Scientific, auspices of the Agency Chief Information Officer. technical, or historical information from It collects, organizes, provides for archiving, and NASA programs, projects, and missions, disseminates NASA’s STI. The NASA STI often concerned with subjects having program provides access to the NTRS Registered substantial public interest. and its public interface, the NASA Technical Report Server, thus providing one of the largest • TECHNICAL TRANSLATION. collections of aeronautical and space science STI in English-language translations of foreign the world. Results are published in both non-NASA scientific and technical material pertinent to channels and by NASA in the NASA STI Report NASA’s mission. -
This Preview Includes the Entire Resource. the Teacher Information
This preview includes the entire resource. The teacher information pages and two of the student pages are unmarked so that you can try before you buy! I I Literacy is a challenging, quick, and fun way to reinforce ELA and reading skills. Each page features a different theme, so not only will your students be practicing skills, they will also be learning about curriculum-based, high-interest topics. Each page has its own unique design, so students will never get bored seeing the same old thing over and over. While each page is different, they do have some elements in common. Each page features: • 6 standards-based ELA/Reading activities, each in its own space. Activities are numbered for easy reference. • An open-ended bonus activity, marked by a star, at the bottom of the page to be completed on the backside. Perfect for fast finishers, as homework, or extra credit. • A short reading passage with one or two text-dependent questions. Most of the passages are informational text (written by a published author of over 100 nonfiction books for children), but a few are fictional – just to shake things up. The questions are more closely aligned to close reading than simple comprehension. • A theme-based joke or fun fact (joke answers can be found upside down in the bottom right hand corner). • A list of the skills addressed at the bottom (indicated by a picture of a nail – which stands for “nailed it!”) This list repeats in the table of contents for easy reference. • A picture of a whale in the upper right corner simply because it is so adorable. -
Complex Garment Systems to Survive in Outer Space
Volume 7, Issue 2, Fall 2011 Complex Garment Systems to Survive in Outer Space Debi Prasad Gon, Assistant Professor, Textile Technology, Panipat Institute of Engineering & Technology, Pattikalyana, Samalkha, Panipat, Haryana, INDIA [email protected] Palash Paul, Assistant Professor, Textile Technology, Panipat Institute of Engineering & Technology, Pattikalyana, Samalkha, Panipat, Haryana, INDIA ABSTRACT The success of astronauts in performing Extra-Vehicular Activity (EVA) is highly dependent on the performance of the spacesuit they are wearing. Since the beginning of the Space Shuttle Program, one basic suit design has been evolving. The Space Shuttle Extravehicular Mobility Unit (EMU) is a waist entry suit consisting of a hard upper torso (HUT) and soft fabric mobility joints. The EMU was designed specifically for zero gravity operations. With a new emphasis on planetary exploration, a new EVA spacesuit design is required. Now the research scientists are working hard and striving for the new, lightweight and modular designs. Thus they have reached to the Red surface of Mars. And sooner or later the astronauts will reach the other planets too. This paper is a review of various types of spacesuits and the different fabrics required for the manufacturing of the same. The detailed construction of EMU and space suit for Mars is discussed here, along with certain concepts of Biosuit- Mechanical Counter pressure Suit. Keywords: Extra-Vehicular Activity (EVA), spacesuits, Biosuit-Mechanical Counter pressure Suit Tissues (skin, heart, -
Mars One Applicant Study Material Booklet
COMPILED BY MICHAEL GRUNDLING Index: PAGE WHAT ’S THE HISTORIC SUCCESS RATE OF MISSIONS TO MARS ............................................................... 3 THE ROADMAP ..................................................................................................................................... 5 WHAT HAPPENS AFTER THE FIRST HUMANS ’ ARRIVAL ON MARS ? ............................................................. 11 WILL THE MISSION BE HARMFUL TO MARS ’ ENVIRONMENT ? ..................................................................... 12 IS THIS A SUSTAINABLE MISSION ?........................................................................................................... 13 WHAT GOVERNMENTAL SYSTEM AND SOCIAL STRUCTURE WILL BE IMPLEMENTED ON MARS ? .................... 14 WHAT WILL THE ASTRONAUTS DO ON MARS ? ......................................................................................... 15 WHAT ARE THE RISKS OF DUST AND SAND ON MARS ? ............................................................................. 17 IS IT SAFE TO LIVE ON MARS ? ................................................................................................................ 19 HOW SAFE IS THE JOURNEY ? ................................................................................................................. 20 HOW LONG DOES IT TAKE TO TRAVEL TO MARS ? .................................................................................... 21 WHY MARS , AND NOT ANOTHER PLANET ? ............................................................................................. -
Copyright © 2006 by Douglas W. Gage. Published by the Mars Society with Permission
Copyright © 2006 by Douglas W. Gage. Published by The Mars Society with permission BEGIN HIGH FIDELITY MARS SIMULATIONS NOW! Douglas W. Gage XPM Technologies - [email protected] ABSTRACT While analog environments (e.g., Antarctica) and mission experiments (e.g., FMARS, MDRS) are useful, a long term, logically sequenced series of experiments and evaluations in faithfully simulated Mars (outdoor) and Mars habitat (indoor) environments is an absolute prerequisite for manned missions to Mars. Mars suit pressure should be minimized in order to simplify suit design, and habitat pressure should also be minimized, to eliminate "EVA" prebreathing and to reduce structural stress. But we need to experimentally establish the long-term health implications of living in such an atmosphere before we make irrevocable design decisions. This will require a habitat simulation facility that operates continuously for years. Coupling the habitat simulation with a Martian surface simulation (Martian atmospheric pressure and composition, temperature, lighting, wind, dust, and analog-regolith) will support the long term evolutionary development cycle of all types of systems and processes: equipment reliability testing, development of techniques and procedures (e.g., repair, emergency survival), mission plan development and validation, and then later crew training and mission rehearsal. Finally, after launch, the facility will be used to "shadow" actual mission operations. For these purposes we need high fidelity simulation facilities, not just rough analogs. Apart from reduced gravity and radiation, we can provide very high fidelity right here on earth, at costs much lower than in space or on the moon. The time to start is now! INTRODUCTION Sending humans to Mars is the capstone specific goal identified for the “Vision for Space Exploration” promulgated by President Bush [1]. -
Concepts and Approaches for Mars Exploration 6132.Pdf
Concepts and Approaches for Mars Exploration 6132.pdf EXPLORATION STRATEGIES FOR HUMAN MISSIONS: MARS FIELD GEOLOGY, BIOLOGY AND PALEONTOLOGY WORKSHOP. Patricia Wood Dickerson, Lockheed Martin, NASA - Johnson Space Center, C 23, Houston, TX 77058. [email protected]. Introduction: Field exploration strategy, crew Analytical Capabilities & Instruments: Robotic skills and training, analytical capabilities, and Earth-Mars reconnaissance of the Martian surface, human field explo- communications were themes of the Mars Field Geology, rations, and preliminary laboratory research will focus both Biology and Paleontology workshop [1] convened by Mi- on fundamental scientific questions and on site and resource chael B. Duke, David S. McKay, and William R. Muehlber- assessment. Both endeavors will require observations, ger (November, 1998). The intent was to expand the explo- measurements, sampling, and analysis of Martian material, ration culture within NASA: one which captures the experi- and geophysical studies. The team framed their recommen- ence and insight of the scientists, mission operations per- dations of candidate instruments in terms of six specific sonnel, and crews of the Apollo and Skylab explorations; objectives in the human exploration of Mars: field observa- one which applies and develops new technology appropriate tion, sample acquisition, maintenance of crew health and to the quest; one which clearly articulates the scientific safety, search for evidence of past or present life, geological questions and scrupulously reports both data and interpreta- and geophysical field investigation, sample selection and tion. preparation. The convenors charged the thirty-one veteran field Recommendations. 1) The need for specific obser- scientists and space explorers to frame specific recommen- vations and analyses should be the primary driver for the dations, which would build upon mission architecture de- development of compact, integrated field instruments. -
Moon-Miners-Manifesto-Mars.Pdf
http://www.moonsociety.org/mars/ Let’s make the right choice - Mars and the Moon! Advantages of a low profile for shielding Mars looks like Arizona but feels like Antarctica Rover Opportunity at edge of Endeavor Crater Designing railroads and trains for Mars Designing planes that can fly in Mars’ thin air Breeding plants to be “Mars-hardy” Outposts between dunes, pulling sand over them These are just a few of the Mars-related topics covered in the past 25+ years. Read on for much more! Why Mars? The lunar and Martian frontiers will thrive much better as trading partners than either could on it own. Mars has little to trade to Earth, but a lot it can trade with the Moon. Both can/will thrive together! CHRONOLOGICAL INDEX MMM THEMES: MARS MMM #6 - "M" is for Missing Volatiles: Methane and 'Mmonia; Mars, PHOBOS, Deimos; Mars as I see it; MMM #16 Frontiers Have Rough Edges MMM #18 Importance of the M.U.S.-c.l.e.Plan for the Opening of Mars; Pavonis Mons MMM #19 Seizing the Reins of the Mars Bandwagon; Mars: Option to Stay; Mars Calendar MMM #30 NIMF: Nuclear rocket using Indigenous Martian Fuel; Wanted: Split personality types for Mars Expedition; Mars Calendar Postscript; Are there Meteor Showers on Mars? MMM #41 Imagineering Mars Rovers; Rethink Mars Sample Return; Lunar Development & Mars; Temptations to Eco-carelessness; The Romantic Touch of Old Barsoom MMM #42 Igloos: Atmosphere-derived shielding for lo-rem Martian Shelters MMM #54 Mars of Lore vs. Mars of Yore; vendors wanted for wheeled and walking Mars Rovers; Transforming Mars; Xities -
MMM #273 Since December 1986 March 2014 P1
MMM #273 Since December 1986 March 2014 p1 A Desert Castle in Ancient Khorezm in the arid, sandy plains of central Uzbekistan: A model for the (Mars dust) retaining walls hiding a modern Martian hotel? Why not be playful? MMM’s Annual Mars-Theme Issue (March is for Mars) Feature Articles: 2 In Focus: Mars - Do we go to explore? - or to make it a 2nd Earth? 3 “Desert Castle Architectures” for Hotels in rural Mars 4 We may all be Martians! “Life likely came to Earth on a Martian Meteorite” 6 MMM Platform for Mars, V.3 6 Chronological Index To MMM THEMES Issue: MARS Coming Up. Yuri’s Night and Earthday For past articles, Visit http://www.moonsociety.org/publications/mmm_classics/ or /mmm_themes/ MMM #273 Since December 1986 March 2014 p2 About Moon Miners’ Manifesto - “The Moon - it’s not Earth, but it’s Earth’s!” • MMM’s VISION: “expanding the human economy through of-planet resources”; early heavy reliance on Lunar materials; early use of Mars system and asteroid resources; and permanent settlements supporting this economy. • MMM’s MISSION: to encourage “spin-up” entrepreneurial development of the novel technologies needed and promote the economic-environmental rationale of space and lunar settlement. • Moon Miners’ Manifesto CLASSICS: The non-time-sensitive articles and editorials of MMM’s first twenty years plus have been re-edited, reillustrated, and republished in 23 PDF format volumes, for free downloading from this location: http://www.MoonSociety.org/publications/mmm_classics/ • MMM THEME Issues: 14 collections of articles according to themes: ..../publications/mmm_themes/ • MMM Glossary: new terms, old terms/new meanings: www.moonsociety.org/publications/m3glossary.html • MMM retains its editorial independence and serves many groups, each with its own philosophy, agenda, and programs. -
Suited for I
Suited for i % ÷ National Aeronautics and Space Administration Suited for Spacewalking Teacher's Guide With Activities Education Division Office of Human Resources and Education EP-279 National Aeronautics and Space Administration March 1992 This publication may be reproduced. Acknowledgments This publication was produced in a cooperative effort of the National Aeronautics and Space Administration and the Challenger Center for Space Science Education. The follow- ing individuals and organizations provided support and guidance in the development of its contents. NASA Headquarters Washington, DC Education Division Elementary and Secondary Branch Writer Technology and Evaluation Branch Gregory L. Vogt, Ed.D. Educational Publications Branch Crew Educational Affairs Liaison NASA Johnson Space Center NASA Johnson Space Center Houston, Texas Managing Editor Space Shuttle Support Office Cheryl A. Manning Astronaut Office Education Division NASA Headquarters Challenger Center for Space Science Education Alexandria, Virginia Oklahoma State University Stillwater, Oklahoma Aerospace Education Services Program Special thanks also go to the following individuals for their assistance. James W. McBarron l= Chief, EVA Branch _= Crew and Thermal Systems Division i NASA Johnson Space Center I _= Joseph J. Kosmo == Subsystems Manager for Spacesuit Development m Crew and Thermal Systems Division NASA Johnson Space Center Charles E. Whitsett Manager for Projects Automation and Robotics Division NASA Johnson Space Center Shirley Sirota Rosenberg Consulting Editor -
Technical Support Package
Ames Research Center Moffett Field, California 94035 Technical Support Package Airlocks for Pressurized Rovers NASA Tech Briefs ARC-14557 National Aeronautics and Space Administration Technical Support Package for AIRLOCKS FOR PRESSURIZED ROVERS ARC-14557 NASA Tech Briefs The information in this Technical Support Package comprises the documentation referenced in ARC-14557 of NASA Tech Briefs. It is provided under the Commercial Technology Program of the National Aeronautics and Space Administration to make available the results of aerospace-related developments considered to have wider technological, scientific, or commercial applications. Further assistance is available from sources listed in NASA Tech Briefs on the page entitled “NASA Commercial Technology Team.” Additional information regarding research and technology in this general area may be found in a variety of publications available from the NASA Scientific and Technical Information (STI) Program Office. You can access the STI Program Office via http://www.sti.nasa.gov or as follows: NASA STI Help Desk NASA Center for AeroSpace Information 7121 Standard Drive Hanover, MD 21076-1320 Telephone: (301) 621-0390, Fax: (301) 621-0134, E-mail: [email protected] NOTICE: This document was prepared under the sponsorship of the National Aeronautics and Space Administration. Neither the United States Government nor any person acting on behalf of the United States Government assumes any liability resulting from the use of the information contained in this document or warrants that such use will be free from privately owned rights. If trade names or manufacturers’ names are used in this report, it is for identification only. This usage does not constitute an official endorsement, either expressed or implied, by the National Aeronautics and Space Administration. -
Marswalk One First Steps on a New Planet David J
Marswalk One First Steps on a New Planet David J. Shayler, Andrew Salmon and Michael D. Shayler Mars walk One First Steps on a New Planet Published in association with ^ Springer Praxis Publishing pR Chichester, UK David J. Shayler, FBIS Andrew Salmon, BSc (Hon) Michael D. Shayler Astronautical Historian Space Writer Editor and Designer Astro Info Service Astronautics News Astro Info Service Halesowen Smethwick Hall Green West Midlands West Midlands Birmingham UK UK UK SPRINGER-PRAXIS BOOKS IN SPACE EXPLORATION SUBJECT ADVISORY EDITOR: John Mason B.Sc, M.Sc, Ph.D. ISBN 1-85233-792-3 Springer Berlin Heidelberg New York Springer is a part of Springer Science + Business Media (springeronline.com) Library of Congress Control Number: 2005922813 Apart from any fair dealing for the purposes of research or private study, or criticism or review, as permitted under the Copyright, Designs and Patents Act 1988, this publication may only be reproduced, stored or transmitted, in any form or by any means, with the prior permission in writing of the publishers, or in the case of reprographic reproduction in accordance with the terms of licences issued by the Copyright Licensing Agency. Enquiries concerning reproduction outside those terms should be sent to the publishers. © Copyright, 2005 Praxis Publishing Ltd. The use of general descriptive names, registered names, trademarks, etc. in this publication does not imply, even in the absence of a specific statement, that such names are exempt from the relevant protective laws and regulations and therefore free for general use. Cover design: Jim Wilkie Copy editing and graphics processing: R. A. -
MARS on EARTH: the NASA HAUGHTON-MARS PROJECT Preparing for Mars in a Unique Public/Private — and International — Setting
MARS ON EARTH: THE NASA HAUGHTON-MARS PROJECT Preparing for Mars in a unique public/private — and international — setting. BY PASCAL LEE, SETI INSTITUTE thousand miles or so from the Earth’s North SETTING THE STAGE APole lies our planet’s largest uninhabited island, It is hard to tell when Devon Island became an Devon Island. To the Inuit of Nunavut in this part of island, but the rocks that form the landmass today the Canadian high Arctic, the island is known as are mostly ancient seabed material ranging from 570 Taallujutit Qikiktagna or Jaw Bone Island. Devon to 35 millions years in age. The sediments (mostly Island is home to one of the highest-latitude impact carbonates) are resting on an even older crystalline structures known on Earth, Haughton Crater. At 20 basement 2.5 billion years old. Taking this into kilometers in diameter the crater formed 23 million account, the Haughton impact was a recent event. years ago, at the beginning of the Miocene, when an During the Miocene, the region’s climate was much asteroid or a comet collided with our planet. warmer than it is today. Boreal forests of conifers and Every summer since 1997, I have journeyed to birch trees covered the land. Giant rabbits and small Devon Island with colleagues and students from ancestral rhinos roamed. Local streams and lakes many horizons to study the natural wonders of teemed with fish. Earth—and Mars, by comparison. We also test out All of this changed in an instant. new technologies and strategies that will help us The object that struck Devon Island was perhaps explore Mars and other reaches of space in the future, 1 kilometer (0.6 mile) in diameter.