Wallcovering Backings
Total Page:16
File Type:pdf, Size:1020Kb
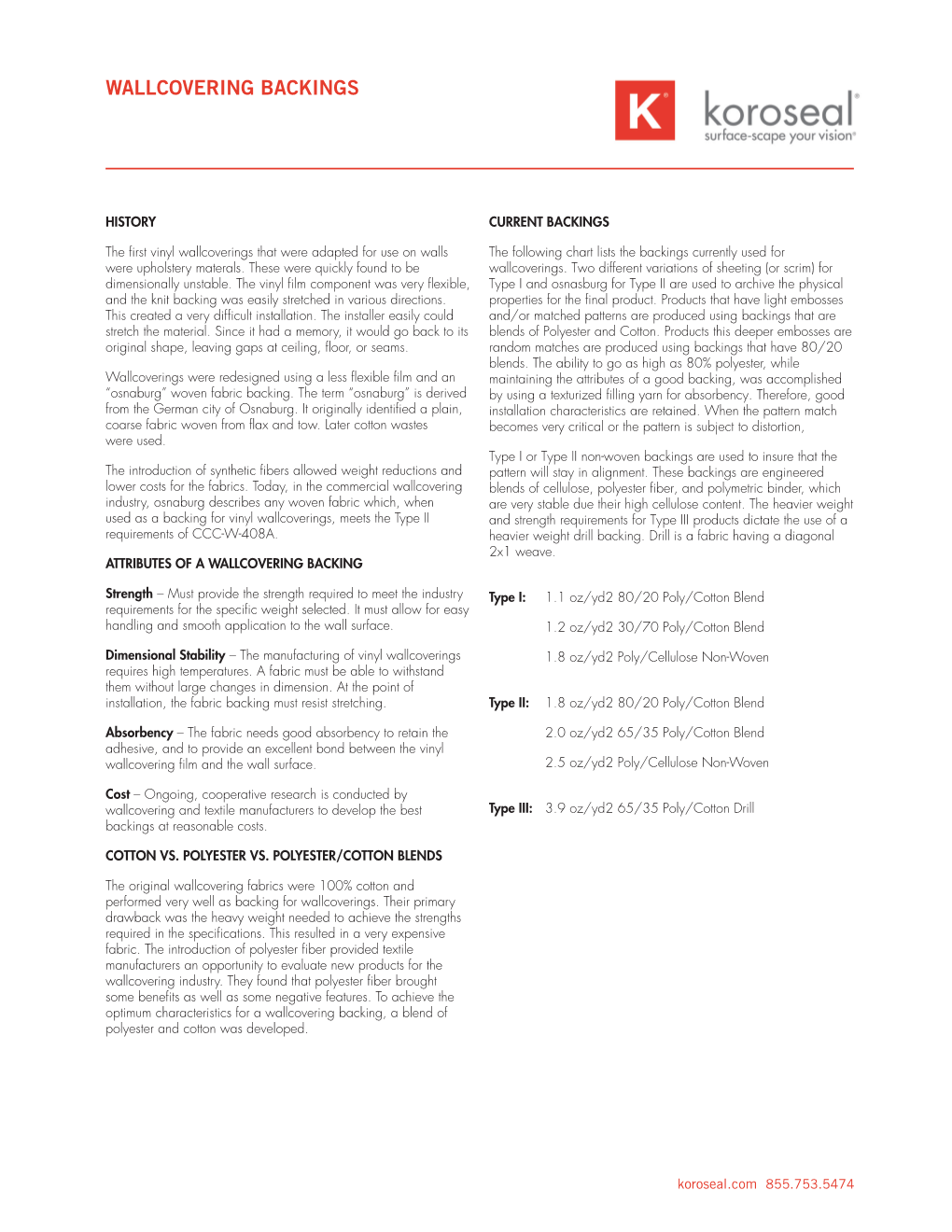
Load more
Recommended publications
-
GENERAL AGREEMENT ACCORD GENERAL SUR on TARIFFS and LES TARIFS DOUANIERS CONFIDENTIAL T2X.SB/336 TRADE ET LE COMMERCE 5 Aprii 1979
GENERAL AGREEMENT ACCORD GENERAL SUR ON TARIFFS AND LES TARIFS DOUANIERS CONFIDENTIAL T2X.SB/336 TRADE ET LE COMMERCE 5 Aprii 1979 Textiles Surveillance Body , Organe de surveillance des textiles ARRMGB'EFf REffiARDIIIG BiTERNATIONAL TRADE El TEXTILES Article h notification Note by the Chairman Attached hereto is a notification received from Canada of a bilateral agreement concluded under Article h between Canada and Hong Kong. ARRANGEMENT CONCERTANT LE COMMERCE INTERNATIONAL PES TEXTILES NotificatioL« n conformément a l'article k Note du Président Le Canada a fait parvenir au secretariat la notification ci-jointe relative à un accord bilateral conclu entre le Canada et Hong-kong au titre de l'article h. (Tin- ycrmancittj^fggTgn ûEggm^tti; I ^.,^tO! '-'-^ JtUssnuu permanente îut QlanaÀut tu tbcltMï^^^^ttHW—:——^;';^:;v^i autres îu*s SCatiuns "llntes i u-jri. PW. _! | _ ! f'vjv.v*'* i ' > i .>s--'- £••»• ~r;-.r .."• " j1 i ^^I'J^'i : ~-— •• " 10 k, avenue de Bu.c.3 jl^bTâvâcf-oi^ i /.! 1202 Geneva Dev. Div. ^k—yrrr; • i\jf^ . f^ch 2S.1979 C~c£ CF ^ . ~CÔn'.i.,lnnt i *OOj : Deaf Ambassador Wurth, With reference to paragraph 4 of Article 4 of the Arrangement Regarding International Trade in Textiles (hereinafter • referred to as the ITA), done at Geneva on December 20, 1973» and to the Protocol Extending the ITA, done at Geneva on December 14, 1977» I have the honour to notify the Textile Surveillance Body of the conclusion of a 3-year bilateral textile arrangement between the Government of Canada and the Government of Hong Kong. This bilateral arrangement, wa3 concluded having regard to Article 4 of ihe ITA and to the Protocol of Extension. -
Roundup Giant Drill Bit Reaches Bottom of Escape Hole
..--'.■I- - :i: n'- y 'r \ 'f ■itti Arwag* Daily Net Press Ron T h e W «B th«r Vor ttke Week Ended raramal o f D. « . WmUimr B n s a a August S4, IM S ■ Clear and eool again toolglit. 13,521 Low 48 Is SO. Tuesday mm aj imd Member at the Audit plrassnt. High near W. Bwresu of Obvulstlaa , M aneh^ter-^A City o f ViUage Charm (assstfied AdserlMng m b Fug* 16) PRICE SEVEN CENTS' ▼OL. LXXXU, NO. 278 (SIXTEEN PAGES) MANCHESTER, CONN., MONDAlT, AUGUST 26, 1963 City af Contrasts Scene of March plex of greenery and, marble, a the same tinve. Although the crime lems. Most of these committees there without intermittent or bil EDITOR'S NOTE — The nation’s ious fever.’’ attention.. focuses Wednesday on monument that looks east to the has received wide and often lurid are ruled by Southerners. Some Capitol, north to the White House' publicity, it differs llttie from residents say these congressmen Like India's New Delhi and Washington when thousands of Brazil’s Brasilia. Washington is a civil lights advocates mass to west to the Lincoln Memorial and crime rates in other big cities have no sympathy for a 67 per south to the JTefferson Memorial of America. Washington is ninth cent Negro city with Integrated city created as a capital, with no dramatize the struggle for Negro other reason for life. It does not rights. The city that awaits them and the Tidal Basin rimmed with in size with a population of 764,- schools w d restaurants and is sketched In the following ar cherry trees. -
C on Tra Ctn As 8
C C ON TRA C T N AS 8- 2 11 7 2 Final Report Covering Period June 21 through October 20, 1967 DEVELOPMENT OF MANUFACTURING TECHNIQUES FOR APPLICATION OF HIGH PERFORMANCE CRYOGENIC INSULATION D2-109005-1 Prepared by: Missile and Information Systems Division THE BOEING COMPANY Seattle, Washington C. L. Lofgren - Program Manager D. E. Gieseking - Technical Leader Prepared for: National Aeronautics and Space Administration George C. Marshall Space Flight Center Huntsville, Alabama i D2-109005-1 SCOPE This document specifies the process requirements and manufacturing procedures for the system component fabrication, insulation fabrication, insulation instal- lation, preconditioning, and insulation quality maintenance of the thermal protec- tion system for a 200-inch diameter Torus Tank (Drawing 15-.4-X-1100). When specified on the Engineering Drawing SKll-041071, all applicable manu- facturing and quality control shall comply with the requirements of this document. The Engineering Drawing SKil-041071 shaii take precedence over this document in case a conflict arises. ii D2-109 005-1 FORKW OIZD This final report represents the results of an 18-week design and manufacturing aedysis conducted between Jute 21, 1967 and October 28, 1967, for the George C. Marshall Space Flight Center, National Aeronautics and Space Administration. The work was accomplished under Contract NAS8-21172. Mr. I. C. Yates, Manufacturing Engineering Laboratory, was the technical monitor. The study was performed by The Boeing Company, Missiles and Information Systems Division, Manufacturing Development Section. Program Manager was Mr. C.L. Lofgren. Mr. D.E. Gieseking was technical advisor and Mr. D.H. Bartlett was responsible for the designs, thermal, and structural analyses. -
Federal Register Volume 8 ' 9 3 4 ^ Number 23
.XONÄM* FEDERAL REGISTER VOLUME 8 ' 9 3 4 ^ NUMBER 23 Washington, Wednesday, February 3, 1943 The President brought into the territorial waters of the CONTENTS United Kingdom and Sierra Leone and THE PRESIDENT to the taking or appropriation of such v PROCLAMATION 2575 prizes within the territorial waters of the Proclamation: Page United Kingdom and Sierra Leone for Capture of prizes____________ 1429 Capture of Prizes the use of the United States: Executive Order; NOW, THEREFORE, I, FRANKLIN D. Reports of contracts and pur BY THE PRESIDENT OF THE UNITED STATES ROOSEVELT, President of the United chases made under author OF AMERICA States of America, acting under and by ity of Title II of First War A PROCLAMATION virtue of the authority vested in me by Powers Act, 1941; amend the said act of August 18, 1942, do pro ment_______________ 1429 WHEREAS the act of August 18, 1942, claim that the Government of the United REGULATIONS AND NOTICES Public Law 704, 77th Congress, contains Kingdom shall be accorded like privileges in part the following provisions: with respect to prizes captured under Bituminous Coal Division: "Be it enacted by the Senate and House of authority of the said Government and District Board 1, order grant Representatives of the United States of Amer brought into the territorial waters of the ing relief________________ 1473 ica in Congress assembled, That the district United States or taken or appropriated F ederal Home Loan Bank Admin courts shall have original jurisdiction of all in the territorial waters of the United istration; i prizes captured during the present war on the States for the use of the said Govern Officers of the banks; agency high seas if said capture was made by author duties_____________ 1431 ity of the United States or was adopted and ment. -
CCC-C-429F Cloth, Osnaburg, Cotton
Downloaded from http://www.everyspec.com CCC-C-429F February 18, 1988 SUPERSEDING CCC-C-429E December 2, 1976 FEDERAL SPECIFICATION CLOTH, OSNABURG, COTTON This specification is approved by the Commissioner, Federal Supply Service, General Services Administration, for the use of all Federal agencies. 1. SCOPE AND CLASSIFICATION 1.1 Scope. This specification covers cotton osnaburg cloth. 1.2 Classification. 1.2.1 Types and classes. The cloth osnaburg, cotton shall be of the following types and classes, as specified (see 6.2): Type I - Unbleached Class 2 - 6.8 oz/sq yd Type II - Coating quality Class 2 - 6.1 oz/sq yd Class 3 - 4.9 oz/sq yd Class 5 - 3.5 oz/sq yd Type III - Dyed Class 2 - 6.1 oz/sq yd 2. APPLICABLE DOCUMENTS 2.1 Government publications. The following documents, of the issue in effect on the date of invitation for bids or request for proposal, form a part of this specification to the extent specified herein: ÚÄÄÄÄÄÄÄÄÄÄÄÄÄÄÄÄÄÄÄÄÄÄÄÄÄÄÄÄÄÄÄÄÄÄÄÄÄÄÄÄÄÄÄÄÄÄÄÄÄÄÄÄÄÄÄÄÄÄÄÄÄÄÄÄÄÄÄÄÄÄÄÄÄ¿ ³ Beneficial comments (recommendations, additions, deletions) and any ³ ³ pertinent data which may be of use in improving this document should ³ ³ be addressed to: U.S. Army Natick Research, Development, and ³ ³ Engineering Center, Natick, MA 01760-5014 by using the self-addressed ³ ³ Standardization Document Improvement Proposal (DD Form 1426) appearing ³ ³ at the end of this document or by letter. ³ ÀÄÄÄÄÄÄÄÄÄÄÄÄÄÄÄÄÄÄÄÄÄÄÄÄÄÄÄÄÄÄÄÄÄÄÄÄÄÄÄÄÄÄÄÄÄÄÄÄÄÄÄÄÄÄÄÄÄÄÄÄÄÄÄÄÄÄÄÄÄÄÄÄÄÙ AMSC N/A FSC 8305 DISTRIBUTION STATEMENT A. Approved for public release; -
SHET/TER's PATENT SERPE\ Plastering Lath, Forsaie by Mccormic
IgJl* U J J-JP1 !".!gW*H—BggLl J ■ wbw Grama and Bmsmxm &ROCSRICS tkC. NSW ESTABLISHMENT. OOODB. DOMESTIC GOODS. 8AM, fefecHSS & SCOTS, #ortr£. Loaf, lump, and brovrn Sugars, ROBERT B. RUST & Co. | & 3-4 and 4-4 Brown and Common Black m WILSON ANDERSON. Strong Rio and St Coffee, leave to inform Sheetings, Sup’r fur hats, Domingo the citizen* of 4-4 and 9-8 received and aredow Cun 3-4, Bleached Shirtings, Sup'r white Beaver do. just open- Powder, *) BF,GMartinsburg, and the public general a handsome assortment of Cotton and Brown Dril- Palm and white HAVEing fancy Imperial, | ly, that they hare just opened in the store Osnaburg Leaf wool do. am! which are G. P. Ladies staple goods among the Imperial, TEAS. room formerly occupietFby Mr. Wm. T. lings, Kid Lasting and Morrocco following, viz: Young Hyson, | Compton, corner of Burke and Queen Pittsburg Cord, and Cord Drillings, Shoes, blue, black and Cloths And Black Super fancy j streets, a very large assortment of Angola Cassinelt and Col'd Sateens, Do. Calf skin and Horse leather and and N. Orleans and vVest India do. Cassimeres; Angola, Grecian, Molasses; SPRING AND SUMMER Plaid, and Furniture Misses’ children's shoes llotten Cavendish and Bedlicking, <Sf dp bootees Cassimer; Erminetts, Hassar, Plug Tobacco, goods; Gent's and Havanna, Spanish, Half and Cottons, Calf Morrocco Pumps, Diagonal, Canton and cords; Spanish, which sre the viz: 3-4 Do. Pittsburg common Segars, among following, and 4-4 Indigo Checks, Cal) and Strong Shoes, brown Irish and French brown Blue, black, brown, London Linens; Race and ground green, Cotton Yarn, Carpet Chain, Can- Do. -
Wallcovering with Goodrich
WALLCOVERING z WALLCOVERING 234 | VOGUE 234 | VOGUE FABRIC BACKED VINYL TYPE II WITH GOODRICH, Your habitat becomes A gallery of Your self-expressions; A canvas for Your creativity; A space for Your soul; A showcase of Your taste for life; 234 INSTOCK Stay Connected - www.goodrichglobal.com | [email protected] PREMIERWALL /Goodrich.Global.Singapore /goodrich_global /GoodrichGlobal /GoodrichChina /GoodrichGlobal /goodrichglobal /GoodrichHQ /Goodrich_Global 2019 - 2022.12 SINGAPORE [HQ] | CHINA | HONG KONG (CHINA) | INDIA | INDONESIA | MALAYSIA | MYANMAR | PHILIPPINES | THAILAND | UNITED ARAB EMIRATES | VIETNAM Copyright © 2020 Goodrich Global. All rights reserved. COMMERCIAL | HOSPITALITY | RESIDENTIAL PANACHE MEMPHIS LINEN Vogue Collection ANGLES SILK SANSHIN PREMIERWALL VOGUE LOW VOC 52" - 54" Fabric-Backed Contract Wallcovering PHYSICAL PROPERTIES Weight 20.0 oz. PLY / 619G/PLM Roll Size 52"-54" x 30yds Backing Osnaburg Meets or exceeds Federal Specification CCC-W-408D for Type II Wallcovering FIRE SAFETY • Class “A” fire rated - tested in accordance with ASTM E-84 Tunnel test • Flame spread: 25 / Smoke developed: 45 • Passes NFPA 286 Corner Burn Test ENVIRONMENT AND HEALTH • The product has been assessed according to the assessment criteria of the Singapore Green Building product certification scheme. • Meets California section 01350 IAQ test requirements for wallcovering • Can contribute to LEED EQ 4.1 point for low-emitting materials, adhesives, and sealants, if used with low VOC adhesives • Can contribute to LEED MR 5.1 point for regional materials ANTI-MICROBIAL FEATURES PREMIERWALL VOGUE can be perforated, with 30 yard minimum requirement, for enhanced permeability. This product is intended for use in buildings that are properly designed and maintained to avoid moisture infiltration, condensation and/or accumulation at wall cavities and wall surfaces, particularly in warm, humid climates. -
Commodity Master List
Commodity Master List 005 ABRASIVES 010 ACOUSTICAL TILE, INSULATING MATERIALS, AND SUPPLIES 015 ADDRESSING, COPYING, MIMEOGRAPH, AND SPIRIT DUPLICATING MACHINE SUPPLIES: CHEMICALS, INKS, PAPER, ETC. 019 AGRICULTURAL CROPS AND GRAINS INCLUDING FRUITS, MELONS, NUTS, AND VEGETABLES 020 AGRICULTURAL EQUIPMENT, IMPLEMENTS, AND ACCESSORIES (SEE CLASS 022 FOR PARTS) 022 AGRICULTURAL IMPLEMENT AND ACCESSORY PARTS 025 AIR COMPRESSORS AND ACCESSORIES 031 AIR CONDITIONING, HEATING, AND VENTILATING: EQUIPMENT, PARTS AND ACCESSORIES (SEE RELATED ITEMS IN CLASS 740) 035 AIRCRAFT AND AIRPORT, EQUIPMENT, PARTS, AND SUPPLIES 037 AMUSEMENT, DECORATIONS, ENTERTAINMENT, TOYS, ETC. 040 ANIMALS, BIRDS, MARINE LIFE, AND POULTRY, INCLUDING ACCESSORY ITEMS (LIVE) 045 APPLIANCES AND EQUIPMENT, HOUSEHOLD TYPE 050 ART EQUIPMENT AND SUPPLIES 052 ART OBJECTS 055 AUTOMOTIVE ACCESSORIES FOR AUTOMOBILES, BUSES, TRUCKS, ETC. 060 AUTOMOTIVE MAINTENANCE ITEMS AND REPAIR/REPLACEMENT PARTS 065 AUTOMOTIVE BODIES, ACCESSORIES, AND PARTS 070 AUTOMOTIVE VEHICLES AND RELATED TRANSPORTATION EQUIPMENT 075 AUTOMOTIVE SHOP EQUIPMENT AND SUPPLIES 080 BADGES, EMBLEMS, NAME TAGS AND PLATES, JEWELRY, ETC. 085 BAGS, BAGGING, TIES, AND EROSION CONTROL EQUIPMENT 090 BAKERY EQUIPMENT, COMMERCIAL 095 BARBER AND BEAUTY SHOP EQUIPMENT AND SUPPLIES 100 BARRELS, DRUMS, KEGS, AND CONTAINERS 105 BEARINGS (EXCEPT WHEEL BEARINGS AND SEALS -SEE CLASS 060) 110 BELTS AND BELTING: AUTOMOTIVE AND INDUSTRIAL 115 BIOCHEMICALS, RESEARCH 120 BOATS, MOTORS, AND MARINE AND WILDLIFE SUPPLIES 125 BOOKBINDING SUPPLIES -
The Use of Micro Computed Tomography to Ascertain the Morphology of Bloodstains on Fabric
The use of micro computed tomography to ascertain the morphology of bloodstains on fabric. Dicken, L.1, Knock, C.1, Beckett, S.2, de Castro, T. C.3, Nickson, T.4, Carr, D. J.1 Authors’ addresses 1 Centre for Defence Engineering, Cranfield University at the Defence Academy of the United Kingdom, Shrivenham, SN6 8LA, United Kingdom. 2 Cranfield Forensic Institute, Cranfield University at the Defence Academy of the United Kingdom, Shrivenham, SN6 8LA, United Kingdom. 3 Sir John Walsh Research Institute, University of Otago, Dunedin, 9054, New Zealand. 4 LGC Forensics, Culham, Oxfordshire, OX14 3ED. Communicating Author Dr. C. Knock, Centre for Defence Engineering, Cranfield University at the Defence Academy of the United Kingdom, Shrivenham, SN6 8LA, United Kingdom. Telephone: +44 (0)1793 785335 Email: [email protected] 1 Abstract Very little is known about the interactions of blood and fabric and how bloodstains on fabric are formed. Whereas the blood stain size for non-absorbent surfaces depends on impact velocity, previous work has suggested that for fabrics the blood stain size is independent of impact velocity when the drop size is kept constant. Therefore, a greater understanding of the interaction of blood and fabric is required. This paper explores the possibility of using a micro computed tomography (CT) scanner to study bloodstain size and shape throughout fabrics. Two different fabrics were used: 100% cotton rib knit and 100% cotton bull drill. Bloodstains were created by dropping blood droplets from three heights; 500mm, 1000mm and 1500mm. Results from the CT scanner clearly showed the bloodstain shape throughout the fabric. -
Industrial Woven Fabrics
INDUSTRIAL WOVEN FABRICS Our constant and varied needs for top DeRoyal Textiles’ products for industry cater to quality industrial fabrics have us turning the unique manufacturing needs and specic to DeRoyal Textiles time and time again. performance standards of our customers. They have been providing us with quality Serving a multitude of industrial applications products for many years. for over 100 years, DeRoyal Textiles’ innovative products are the strength behind many world-class industrial products. DeRoyal Textiles specializes in customized Osnaburg Fabrics designs that will meet your specic needs. Tape Support Fabrics When your manufacturing processes call for Starched Crinoline Fabrics state-of-the-art fabrics, you can rely on (Bookbinding) DeRoyal Textiles for unsurpassed quality, precision, and innovation. Coating and Laminating Fabrics Specic Weight and Tensile Fabrics Poplins Sheetings GREIGE FABRICS Unbleached, loom-state woven fabrics made from 100% cotton yarns and polyester/cotton blend yarns. Various fabric weights, weave constructions, and tensile strengths are available. A multiple-use fabric. AVAILABILITY 100% Cotton Cotton/Polyester Blend Fabrics 100% Polyester Fabrics Widths range from 36” to 64” Various weights BLEACHED FABRICS Bleached fabrics made from 100% cotton yarns are processed through a kier bleaching process to remove all cotton oil residue and starch from the woven fabric. Various weave constructions, widths and roll lengths are available. Uses include tack cloth, ltration, straining, medical gauze, and nger bandages. AVAILABILITY 100% Cotton Widths 36” to 60” Folded to 4-Ply on Rolls TOLL FREE: 800.845.1062 125 E. York Street DeRoyalTextiles.com MAIN: 803.432.2403 Camden, SC 29020 FAX: 803.424.5112. -
ATK Instructions / ૂચના
ATK PROVISIONAL ANSWER KEY (CBRT) Name of the post Management Executive (Metal), (GMDC) Class-2 Advertisement No. 34/2020-21 Preliminary Test held on 04-07-2021 Question No. 001 – 300 (General Studies & Concern Subject) Publish Date 06-07-2021 Last Date to Send Suggestion(s) 13-07-2021 THE LINK FOR ONLINE OBJECTION SYSTEM WILL START FROM 07-07-2021; 12:00 PM ONWARDS Instructions / ૂચના Candidate must ensure compliance to the instructions mentioned below, else objections shall not be considered: - (1) All the suggestion should be submitted through ONLINE OBJECTION SUBMISSION SYSTEM only. Physical submission of suggestions will not be considered. (2) Question wise suggestion to be submitted in the prescribed format (proforma) published on the website / online objection submission system. (3) All suggestions are to be submitted with reference to the Master Question Paper with provisional answer key (Master Question Paper), published herewith on the website / online objection submission system. Objections should be sent referring to the Question, Question No. & options of the Master Question Paper. (4) Suggestions regarding question nos. and options other than provisional answer key (Master Question Paper) shall not be considered. (5) Objections and answers suggested by the candidate should be in compliance with the responses given by him in his answer sheet. Objections shall not be considered, in case, if responses given in the answer sheet /response sheet and submitted suggestions are differed. (6) Objection for each question should be made on separate sheet. Objection for more than one question in single sheet shall not be considered. ઉમેદવાર નીચેની ૂચનાઓું પાલન કરવાની તકદાર રાખવી, અયથા વાંધા- ૂચન ગે કરલ રૂઆતો યાને લેવાશે નહ (1) ઉમેદવાર વાંધાં- ૂચનો ફત ઓનલાઈન ઓશન સબમીશન સીટમ ારા જ સબમીટ કરવાના રહશે. -
A Dictionary of Men's Wear Works by Mr Baker
LIBRARY v A Dictionary of Men's Wear Works by Mr Baker A Dictionary of Men's Wear (This present book) Cloth $2.50, Half Morocco $3.50 A Dictionary of Engraving A handy manual for those who buy or print pictures and printing plates made by the modern processes. Small, handy volume, uncut, illustrated, decorated boards, 75c A Dictionary of Advertising In preparation A Dictionary of Men's Wear Embracing all the terms (so far as could be gathered) used in the men's wear trades expressiv of raw and =; finisht products and of various stages and items of production; selling terms; trade and popular slang and cant terms; and many other things curious, pertinent and impertinent; with an appendix con- taining sundry useful tables; the uniforms of "ancient and honorable" independent military companies of the U. S.; charts of correct dress, livery, and so forth. By William Henry Baker Author of "A Dictionary of Engraving" "A good dictionary is truly very interesting reading in spite of the man who declared that such an one changed the subject too often." —S William Beck CLEVELAND WILLIAM HENRY BAKER 1908 Copyright 1908 By William Henry Baker Cleveland O LIBRARY of CONGRESS Two Copies NOV 24 I SOB Copyright tntry _ OL^SS^tfU XXc, No. Press of The Britton Printing Co Cleveland tf- ?^ Dedication Conforming to custom this unconventional book is Dedicated to those most likely to be benefitted, i. e., to The 15000 or so Retail Clothiers The 15000 or so Custom Tailors The 1200 or so Clothing Manufacturers The 5000 or so Woolen and Cotton Mills The 22000