A Study of Leonardite-Water Gel Systems Philip H
Total Page:16
File Type:pdf, Size:1020Kb
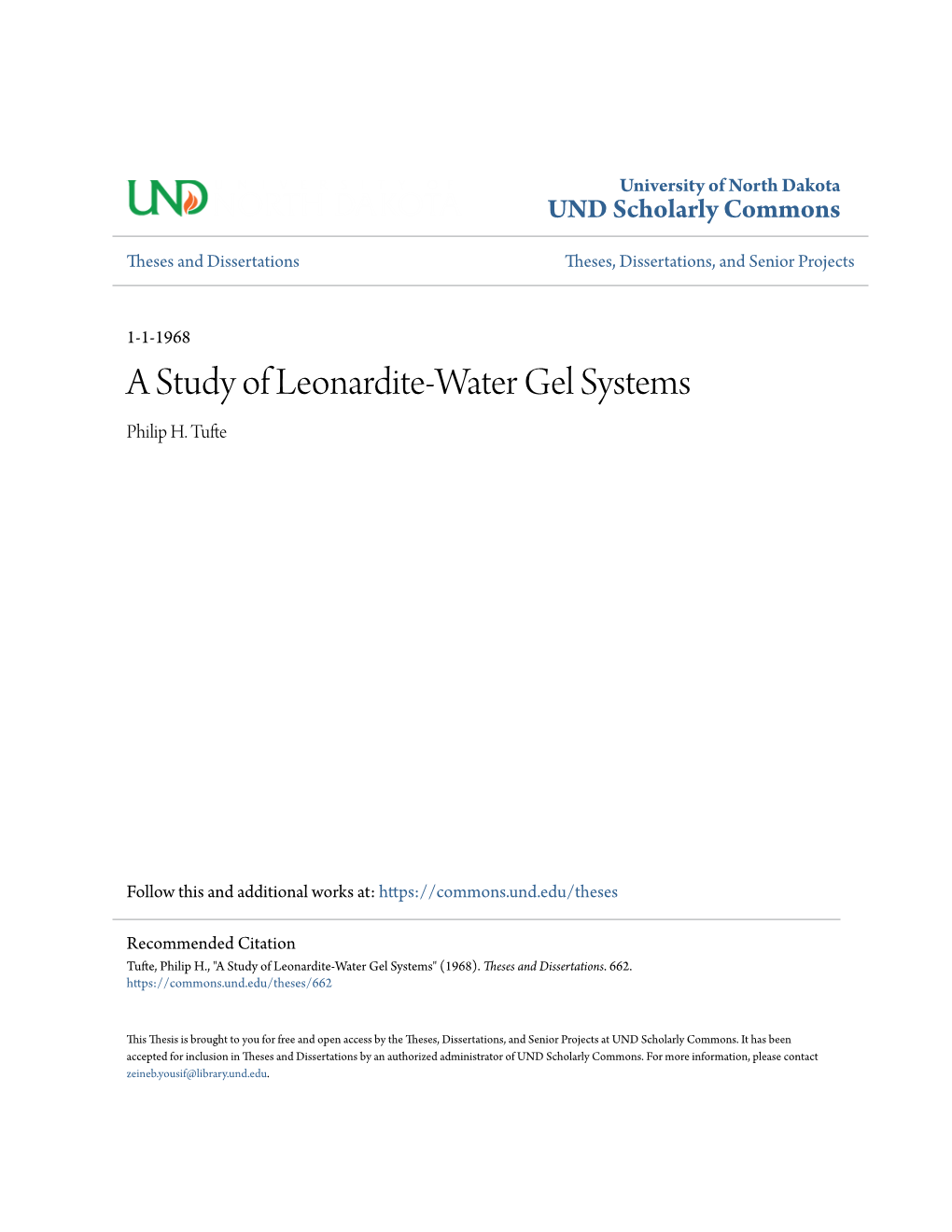
Load more
Recommended publications
-
Gravimetric Analysis of Chloride
Chemistry 321L Manual Page 16 Gravimetric Analysis of Chloride I. Introduction The amount of chloride ion in a substance can be determined by precipitating the soluble chloride ion present with silver ion. The amount of chloride ion present will be related to the mass of silver chloride formed. + - Ag (aq) + Cl (aq) 6 AgCl (s) II. Procedure A. Preparation of Filter Crucibles (Sintered-Glass) 1. Use four filter crucibles of medium (M) porosity. Do not use crucibles marked C for coarse porosity. 2. Previously, the crucibles have been used to filter silver chloride (purple or gray, ammonia soluble). First, remove any bulk precipitate with a rubber policeman and dispose of it in a "Silver Collection" jar. Follow this with chemical cleaning. To remove silver chloride, invert the crucibles in a large beaker in a fume hood and add one or two mL of concentrated ammonia to each. Allow to soak until clean. Carefully remove the crucibles from the beaker and soak in water before removing from the fume hood. Set up a suction filtration apparatus and wash the crucible several times with water and finally with deionized water. Empty the suction flask before proceeding. Stains that are not removed by this cleaning process should not interfere with your measurements. Number, in pencil, each crucible on the frosted glass area. 3. Dry the crucibles in an oven at 120EC for about 1 hour, using a beaker, glass hooks, and watch glass (see figure). A ribbed watch glass can be used in place of the glass hooks. 4. Remove the dried crucibles from the oven and let them cool for about one minute on the counter top. -
Thermal Activity of Base Course Material Related to Pavement Cracking
THERMAL ACTIVITY OF BASE COURSE MATERIAL RELATED TO PAVEMENT CRACKING by Samuel H. Carpenter Robert L. Lytton Research Report Number 18-2 Environmental Deterioration of Pavement Research Project 2-8-73-18 Conducted for the State Department of Highways and Public Transportation in cooperation with the U.S. Department of Transportation Federal Highway Administration by the Texas Transportation Institute Texas A&M Univeristy College station, Texas December, 197 5 TECHNICAL REPORT STANDARD TITLE PACf 1. Report No. 2. Government Accession No. 3. Recipient's Catalog No. ~4.-;Ti~tl-e-an~d~Su~b~ti~tle------------~------------------------~S~.~R~e-pa-rt~D~at_e _________________ _ Thermal Activity of Base Course Material Related to December. 1975 Pavement Cracking 6. Performing Organi •ation Code 7. Authorl s) 8. Performing Organi •ation Report No. Samuel H. Carpenter and Robert L. Lytton Research Report No. 18-2 9. Performing Organi !at ion Name and Address 10. Work Unit Na. Texas Transportation Institute Texas A&M University 11. Contract or Grant No. College Station, Texas 77843 Study No. 2-8-73-18 13. Type of Report and Period Covered ~~----------------~--------------------------~12. Sponsoring 'Agency Name and Address Texas State Department of Highways and Public Trans Inter'm1 _ September, 1972 portation; Transportation Planning Division December, 1975 P. 0. Box 5051 14. Sponsoring Agency Code Austin, Texas 78763 15. Supplementary Notes Research performed in cooperation with DOT, FHWA. Study Title: 11 Environmental Deterioration of Pavement 11 16. Abstract Preliminary studies into environmental deterioration of pavements indicated that low-temperature cracking of the asphalt concrete surface was not likely for the west Texas area. -
A Revised Calibration of the Clumped Isotope Thermometer ∗ Shikma Zaarur , Hagit P
Supplementary Materials included at end of pdf. Earth and Planetary Science Letters 382 (2013) 47–57 Contents lists available at ScienceDirect Earth and Planetary Science Letters www.elsevier.com/locate/epsl A revised calibration of the clumped isotope thermometer ∗ Shikma Zaarur , Hagit P. Affek, Mark T. Brandon Department of Geology and Geophysics, Yale University, New Haven, CT, United States article info abstract Article history: A growing number of materials and environmental settings are studied using the carbonate clumped Received 5 December 2012 isotope (47) thermometer. The method has been applied in both biogenic and non-biogenic carbonate Received in revised form 3 July 2013 systems, in marine and terrestrial settings, over a wide range of geological timescales. The current Accepted 16 July 2013 temperature calibration gives good temperature estimates for most biogenic materials, however, Available online xxxx 47 systematic biases are commonly observed at low temperatures. Editor: G. Henderson In this study we report additional calibration data, that covers a wider temperature range, at more evenly Keywords: distributed temperatures, and are measured at higher analytical precision than the original calibration. clumped isotopes Combining these data with the original calibration yields a 47–T relationship that is similar to the 6 2 carbonates original calibration, though slightly less steep: 47 = (0.0526 ± 0.0025) × 10 /T + (0.0520 ± 0.0284). thermometer calibration This revised calibration is in better agreement with biogenic carbonates, including those grown at low temperatures. The difference between the original and revised calibrations is significant for carbonates ◦ ◦ forming below 16 C or above 49 C(47 values of 0.68h and 0.56h). -
High School Chemistry
RECOMMENDED MINIMUM CORE INVENTORY TO SUPPORT STANDARDS-BASED INSTRUCTION HIGH SCHOOL GRADES SCIENCES High School Chemistry Quantity per Quantity per lab classroom/ Description group adjacent work area SAFETY EQUIPMENT 2 Acid storage cabinet (one reserved exclusively for nitric acid) 1 Chemical spill kit 1 Chemical storage reference book 5 Chemical waste containers (Categories: corrosives, flammables, oxidizers, air/water reactive, toxic) 1 Emergency shower 1 Eye wash station 1 Fire blanket 1 Fire extinguisher 1 First aid kit 1 Flammables cabinet 1 Fume hood 1/student Goggles 1 Goggles sanitizer (holds 36 pairs of goggles) 1/student Lab aprons COMPUTER ASSISTED LEARNING 1 Television or digital projector 1 VGA Adapters for various digital devices EQUIPMENT/SUPPLIES 1 box Aluminum foil 100 Assorted rubber stoppers 1 Balance, analytical (0.001g precision) 5 Balance, electronic or manual (0.01g precision) 1 pkg of 50 Balloons, latex 4 Beakers, 50 mL 4 Beakers, 100 mL 2 Beakers, 250 mL Developed by California Science Teachers Association to support the implementation of the California Next Generation Science Standards. Approved by the CSTA Board of Directors November 17, 2015. Quantity per Quantity per lab classroom/ Description group adjacent work area 2 Beakers, 400 or 600 mL 1 Beakers, 1000 mL 1 Beaker tongs 1 Bell jar 4 Bottle, carboy round, LDPE 10 L 4 Bottle, carboy round, LDPE 4 L 10 Bottle, narrow mouth, 1000 mL 20 Bottle, narrow mouth, 125 mL 20 Bottle, narrow mouth, 250 mL 20 Bottle, narrow mouth, 500 mL 10 Bottle, wide mouth, 125 -
Valorization of 2,5-Furandicarboxylic Acid. Diels-Alder Reactions with Benzyne
Electronic Supplementary Material (ESI) for Green Chemistry. This journal is © The Royal Society of Chemistry 2018 Electronic Supporting Information Valorization of 2,5-Furandicarboxylic Acid. Diels-Alder Reactions with Benzyne Eric M. Serum, Sermadurai Selvakumar, Nicholas Zimmermann, and Mukund P. Sibi* Department of Chemistry and Biochemistry, North Dakota State University, Fargo, North Dakota, USA, E-mail: [email protected] S 1 Table of Contents Section Heading Page 1 General Methods S 3 2 Equations 1–4 Discussion of Metrics S 3 3 Synthesis of Dimethyl-2,5-furandicarboxylate 5 S 4 4 Synthesis 2,5-Diformylfuran 2A S 5 5 Synthesis (2E,2'E)-3,3'-(furan-2,5-diyl)diacrylic acid 3 S6 6 Synthesis Dimethyl 3,3'-(furan-2,5-diyl)(2E,2'E)-diacrylate 13 S 7 7 Synthesis Dimethyl 3,3'-(furan-2,5-diyl)dipropionate 14 S 8 8 Diene 15 (2,5-dimethylfuran) S 9 9 Diels Alder Reactions Table S 1 Desilylation of 16: Exploring the Relationship Between S 10 Temperature and Benzyne Trapping by Furan Diene Substrates Table S 2 Thermolysis of 19 generated in situ: Trapping in Chloroform S 12 Table S 3 Partially Isolated 19 Thermolysis: Preliminary Trapping and S 13 Substrate Screening Table S 4 Partially Isolated 19 Thermolysis: Substrate Screen Exploring the S 15 Relationship Between Stoichiometry and Reaction Outcome Reaction Diene 13 with Benzyne Generated by Thermolysis Fig. S 1 S 16 Table S 5 Partially Isolated 19 Thermolysis and Trapping Single Shot: S 17 Method and Substrate Screening While Limiting Availability of Nitrite Table S 6 Crude Preparation of 19 Added Directly to Diene Solution S 18 10 Identification Dimethyl 3,4-epoxy-7-oxabenzonorbornadiene-1,4- S 19 dicarboxylate 11 Hydrolysis 7-Oxabenzonorbornadiene-1,4-dicarboxylic acid S 20 12 Deoxyaromatization Table S 7 Naphthalenes from 7-Oxabenzonorbornadienes: Trimethylsilyl S 21 Iodide Mediated Deoxyaromatization 13 Catalytic Hydrogenation S 23 14 Dehydroaromatizations S 25 Table S 9 Naphthalenes by Dehydro-aromatization of 7- S 25 Oxabenzonorbornenes. -
Table of Contents
EXPERIMENT 18 Gravimetric Determination of the Iodide Ion Content in a Mixture INTRODUCTION The branch of analytical chemistry known as quantitative analysis concerns itself with the amounts of the various components within a sample, and it is often separated into three categories: gravimetric, volumetric, and instrumental. Earlier in the semester instrumental analyses were performed utilitzing the sophisticated device called a spectrometer. In this experiment a gravimetric analysis will be performed, and it will rely on traditional laboratory equipment: balances, beakers, Büchner funnels, and filter flasks. In gravimetric analysis, a substance is treated so that the component of interest is separated either in its pure form or as a constituent in a compound of known composition, which can be weighed. The separation is often accomplished by first dissolving a sample of the substance in a suitable solvent and then adding a reagent that reacts with the desired component to form an insoluble solid. A gravimetric precipitation method must fulfill certain basic requirements in order to provide an accurate analysis. 1. The precipitation reaction should be quantitative so that only a negligible fraction on the component of interest remains in solution after the precipitate is isolated. A moderate excess of the precipitating agent is commonly employed to help achieve this condition. 2. Other constituents in the sample solution should not interfere with the precipitation of the component of interest. 3. The precipitation should be as free of contaminants as possible. 4. The particles of precipitate should be large enough to filter easily and to facilitate the removal of soluble impurities during washing operations. -
Neutral Solution. Nitric Acid Is Added to the Wash Liquid to Maintain a High Electrolyte Concentration and to Prevent Peptization During the Washing Step
Gravimetric Determination of Chloride Introduction The chloride content of a soluble salt, or of an aqueous solution, can be determined by precipitation of the chloride ion as silver chloride: Ag+(aq) + Cl-(aq) → AgCl(s) The silver chloride precipitate initially forms as a colloid, which is coagulated with heat. Nitric acid and a small excess of silver nitrate aid coagulation by providing a relatively high electrolyte concentration. The solution is kept slightly acidic during the precipitation step to eliminate possible interference from anions of -2 weak acids (for example, CO3 ). These anions form slightly soluble silver salts in neutral solution. Nitric acid is added to the wash liquid to maintain a high electrolyte concentration and to prevent peptization during the washing step. (Peptization is the formation of a colloid by dispersion of a precipitate. Colloids pass through filter crucibles while precipitates don’t.) The excess acid is volatized during the subsequent heat treatment. Finally, the precipitate is collected in a previously weighed filtering crucible, washed, and brought to constant mass at 105 oC. Several situations can cause significant increases or decreases in precipitate mass, and therefore poor results. Silver chloride slowly photodecomposes by the following reaction: 2AgCl(s) + 2hυ → 2Ag(s) + Cl2(g) Since chloride is lost as chlorine gas, the above reaction causes the results to be low. The silver metal produced during photodecomposition is responsible for the violet color that develops in the precipitate. If photodecomposition occurs in the presence of excess silver ion, the following reaction occurs: + - + 3Cl2(aq) + 3H2O + 5Ag → 5AgCl(s) + ClO3 + 6H This causes the analytical results to be too high. -
Laboratory Equipment AP
\ \\ , f ?7-\ Watch glass 1 Crucible and cover Evaporating dish Pneumatlo trough Beaker Safety goggles Florence Wide-mouth0 Plastic wash Dropper Funnel flask collecting bottle pipet Edenmeyer Rubber stoppers bottle flask € ....... ">. ÿ ,, Glass rod with niohrome wire Scoopula (for flame re,sting) CruoiNe tongs Rubber ubing '1 ,v .... Test-tube brush square Wire gau ÿ "\ file Burner " Tripod Florence flask: glass; common sizes are 125 mL, 250 mL, 500 .d Beaker: glass or plastic; common sizes are 50 mL, mL; maybe heated; used in making and for storing solutions. 100 mL, 250 mL, 400 mL; glass beakers maybe heated. oÿ Buret: glass; common sizes are 25 mL and 50 mL; used to Forceps: metal; used to hold or pick up small objects. Funnel: glass or plastic; common size holds 12.5-cm diameter measure volumes of solutions in titrafions. Ceramic square: used under hot apparatus or glassware. filter paper. Gas burner: constructed of metal; connected to a gas supply Clamps" the following types of clamps may be fastened to with rubber tubing; used to heat chemicals (dry or in solution) support apparatus: buret/test-tube clamp, clamp holder, double buret clamp, ring clamp, 3-pronged jaw clamp. in beakers, test tubes, and crucibles. Gas collecting tube: glass; marked in mL intervals; used to 3: Clay triangle: wire frame with porcelain supports; used to o} support a crucible. measure gas volumes. Glass rod with nichrome wire: used in flame tests. Condenser: glass; used in distillation procedures. Q. Crucible and cover: porcelain; used to heat small amounts of Graduated cylinder: glass or plastic; common sizes are 10 mL, 50 mL, 100 mL; used to measure approximate volumes; must solid substances at high temperatures. -
CHEM&121 Workbook Key F2019
CHEM& 121 WORKBOOK A Collection of Worksheets and Laboratory Experiments Bellevue College Chemistry Department Faculty | 2019 Edition CHEM& 121 Workbook A Collection of Worksheets and Laboratory Experiments Bellevue College Chemistry Department 2019 Edition Copyright © by Jennie Mayer, Gina Fiorini, Perminder Sandhu, and Shraddha Deodhar Copyright © by Van-Griner, LLC Photos and other illustrations are owned by Van-Griner Learning or used under license. All products used herein are for identification purposes only, and may be trademarks or registered trademarks of their respective owners. All rights reserved. No part of this book may be reproduced or transmitted in any form or by any means, electronic or mechanical, including photocopying, recording or by any information storage and retrieval system, without written permission from the author and publisher. The information and material contained in this manual are provided “as is,” and without warranty of any kind, expressed or implied, including without limitation any warranty concerning accuracy, adequacy, or completeness of such information. Neither the authors, the publisher nor any copyright holder shall be responsible for any claims, attributable errors, omissions, or other inaccuracies contained in this manual. Nor shall they be liable for damages of any type, including but not limited to, direct, indirect, special, incidental, or consequential damages arising out of or relating to the use of such material or information. These experiments are designed to be used in college or university level laboratory courses, and should not be conducted unless there is an appropriate level of supervision, safety training, personal protective equipment and other safety facilities available for users. The publisher and authors believe that the lab experiments described in this manual, when conducted in conformity with the safety precautions described herein and according to appropriate laboratory safety procedures, are reasonably safe for students for whom this manual is directed. -
Assignmentchemistry 216
EQUIPMENT CHECK LIST Chemistry 216 The following items should be stocked in your drawer. These items MUST be clean, dry, and in good condition, with no chips, cracks, or rust. Be sure equipment is COMPLETE before you declare yourself checked-in, otherwise you will be responsible for missing or broken items at the end of the semester. List any exceptions on the “List of Items for Issue" sheet. IN OUT IN OUT 1 - condenser (19/22) 1 - pasteur pipet bulb 1 - plastic funnel 1 - distilling column (19/22)condenser (19/22) 1 - glass stopper (19/22) 1 - watch glass 1 - thermometer holder, neoprene 1 - stemless funnel 1 - boiling flask, round bottom, 25mL 1 - filtervac 1 - boiling flask, round bottom, 50mL 1 - test tube clamp 1 - boiling flask, round bottom, 100mL 2 - centrifuge tubes, 15mL 1 - connecting tube, vacuum (19/22) 1 - rubber policeman 1 - connecting tube, claisen (19/22) 1 - scoopula 1 - connecting tube, 3 way (19/22) 1 - microspatula 1 - thermometer adapter (19/22) 4 - filter flasks: 1 - separatory funnel, 125mL 1 - filter flask, 25mL 1 - Büchner funnel 1 - filter flask, 50mL 4 - beakers: 1 - filter flask, 125mL 1 - beaker, 30mL 1 - filter flask, 250mL 1 - beaker, 50mL MICROGLASSWARE 1 - beaker, 100mL 1 - Hirsch funnel, plastic 1 - beaker, 250mL 1 - filter adapter 11 - Erlenmeyer flasks: 1 - column top, plastic, conical 5 - Erlenmeyer flasks, 10mL 2 - stirring rods, glass, 1 large, 1 small 2 - Erlenmeyer flasks, 25mL 4 - reaction tubes 2 - Erlenmeyer flasks, 50mL 1 - Erlenmeyer flask, 125mL 1 - Erlenmeyer flask, 250mL 2 - graduated cylinders: 1 - graduated cylinder, 10mL 1 - graduated cylinder, 25ml or 50mL Date Desk # Student's Signature AT THE BEGINNING OF THE SEMESTER: 1. -
Lab Equipment Lab Equipment
Lab Equipment Lab Equipment Your lab equipment should: 1. Be CLEAN before using it. 2. Be CHECKED (if glassware) for cracks, broken edges, and “stars”– discard anything damaged. Pre-AP Chemistry Charles Page High School 3. Be washed, dried, and carefully stored in the Stephen L. Cotton proper place after using it. Cleaning Supplies 1. Each lab station has plenty of paper towels, soap, water, sponge and a sink. (2 sinks are also located on the east wall desktop) 2. Used for cleaning lab equipment, the table top, and to wash your hands when finished. 3. We have floor brooms, table brushes, and dustpans to clean up any spills. Keep our lab area neat and clean! Beakers hold and/or heat solids or liquids Beaker Use this Broken Glass that will not release box to dispose of any gases when reacted, or are unlikely to broken glass, instead splatter if stirred. of the trash can. Very poor item to measure volume with (+/- 5% error!) Note the total size There are six sizes of beakers in capacity = 250 mL your lab table for you to use: (upper mark is 200 mL) 50, 100, 150, 250, 400, & 600 mL 1 Beaker Tongs Beaker tongs are used to hold Erlenmeyer Flask and move beakers Erlenmeyer flasks containing hot hold and/or heat liquids. solids or liquids that may release Note the rubber gases during a coating to reaction, or that are improve grip on likely to splatter if the glass beaker stirred. - do not hold these in a burner flame. Note the size = 125 mL Florence Flask Flask Tongs Rarely used in first year chemistry, it is used for the mixing of chemicals. -
Chemistry 2B Lab Manual Standard Operating Procedures Spring Quarter 2020
Chemistry 2B Lab Manual Standard Operating Procedures Spring Quarter 2020 Department of Chemistry University of California - Davis Davis, CA 95616 Student Name Locker # Laboratory Information Teaching Assistant’s Name Laboratory Section Number Laboratory Room Number Dispensary Room Number 1060 Sciences Lab Building Location of Safety Equipment Nearest to Your Laboratory Safety Shower Eye Wash Fountain Fire Extinguisher Fire Alarm Safety Chemicals Revision Date: March 2020 Preface Chemistry is an experimental science. Thus, it is important that students of chemistry do experiments in the laboratory to more fully understand that the theories they study in lecture and in their textbook are developed from the critical evaluation of experimental data. The laboratory can also aid the student in the study of the science by clearly illustrating the principles and concepts involved. Finally, laboratory experimentation allows students the opportunity to develop techniques and other manipulative skills that students of science must master. The faculty of the Chemistry Department at UC Davis clearly understands the importance of laboratory work in the study of chemistry. The Department is committed to this component of your education and hopes that you will take full advantage of this opportunity to explore the science of chemistry. A unique aspect of this laboratory program is that a concerted effort has been made to use environmentally less toxic or non-toxic materials in these experiments. This was not only done to protect students but also to lessen the impact of this program upon the environment. This commitment to the environment has presented an enormous challenge, as many traditional experiments could not be used due to the negative impact of the chemicals involved.