Failure Analysis of a Nose Landing Gear Fork of a GROB G115 Aircraft
Total Page:16
File Type:pdf, Size:1020Kb
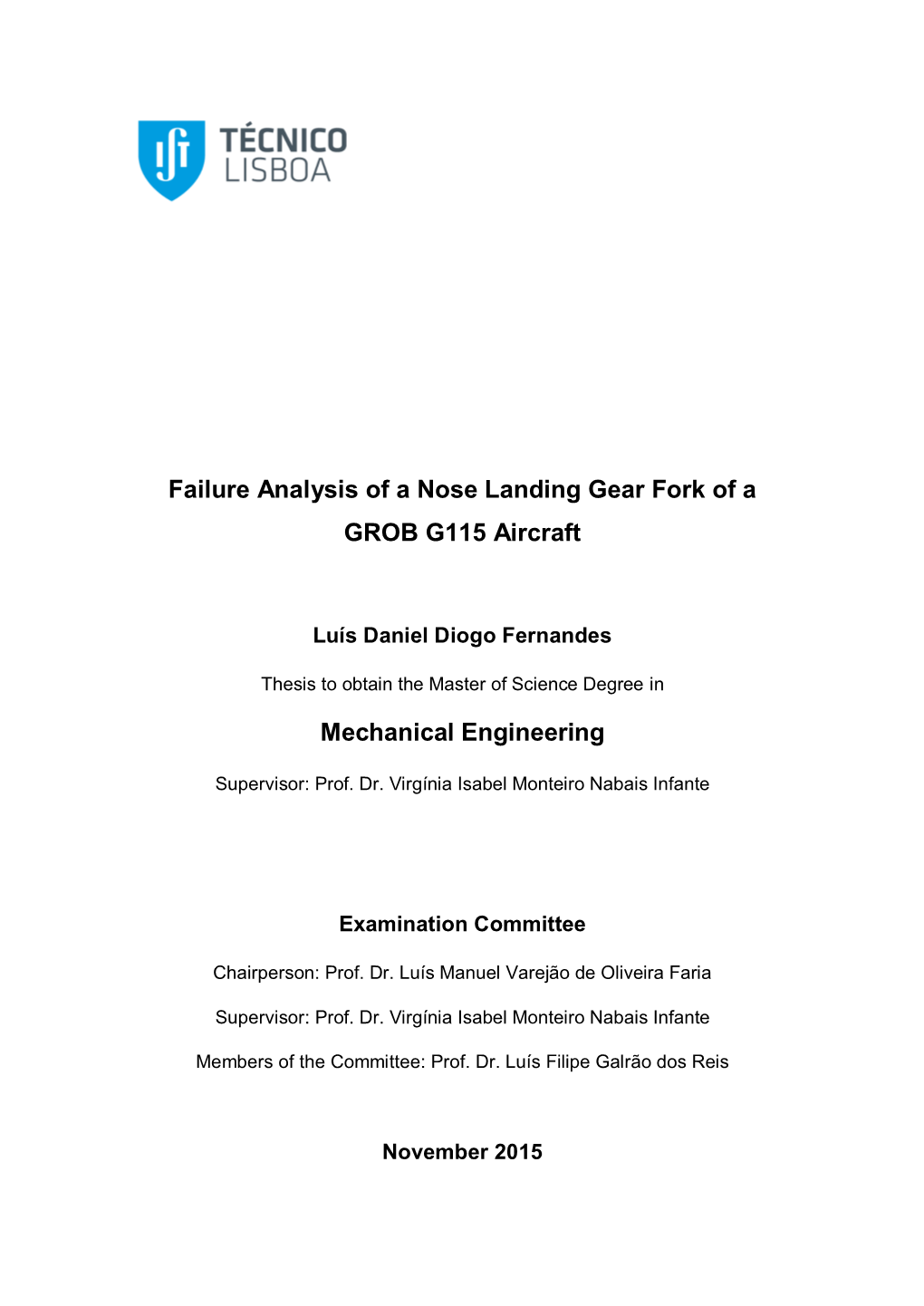
Load more
Recommended publications
-
THE BEST of BAVARIA – the COMPETENCE of HIGH TECHNOLOGY Diese Broschüre Ist Ein Interaktives Dokument
THE BEST OF BAVARIA – THE COMPETENCE OF HIGH TECHNOLOGY Diese Broschüre ist ein interaktives Dokument. Inhaltsverzeichnis, Karten sowie Webseiten sind verlinkt. This interactive brochure has links to index, maps and web pages. 110 Kleinmachnow (Brandenburg) Part 1 114 Aschaffenburg 2 Index and Maps 6 Preface Bavarian State Minister of Economic Affairs, Würzburg 62 Regional Development and Energy 8 bavAIRia e. V. Nuremberg Part 2 Introducing BavAIRia's Expertise 40 Bayern International 10 328 Support Services GmbH 42 Biersack Aerospace GmbH & Co. KG 140 128 12 ACENTISS GmbH 44 Binder Technologie GmbH 14 ACMA GmbH 46 Ludwig Bölkow Campus Regensburg 42 16 ADS Advanced Design Services GmbH 48 Centum-amm Deutschland GmbH 2 142 104 50 18 AERO-Bildungs GmbH 50 CUONICS GmbH 3 Straubing 20 AES Aerospace Embedded Solutions GmbH 52 Deutsches Zentrum für Luft- und 144 Stuttgart Ingolstadt 64 22 Airbus Bank GmbH Raumfahrt e. V. (DLR) 44 24 Airbus Defence and Space 56 DLR GfR mbH 112 26 Aircraft Philipp Group 58 EADCO GmbH 28 ARRK/P+Z Engineering GmbH 60 EDMO-Flugbetrieb GmbH 30 ARTS Holding SE 62 EMCCons DR. RAŠEK GmbH & Co. KG 34 80 130 32 Asto Aerospace and Technology Park 64 EME Elektro-Metall Export GmbH Augsburg 88 138 34 Augsburg Aerospace Area 66 ESG Elektroniksystem- und Logistik-GmbH 70 146 76 36 Bauhaus Luftfahrt e. V. 68 Expleo Germany GmbH 66 Munich 38 84 38 Bayern-Chemie GmbH 70 FERCHAU Aviation Group 102 Memmingen 118 122 86 78 136 26 120 126 Salzburg 100 Garmisch 98 Partenkirchen LEGENDE/KEY Standortkarte Bayern Industrie/Industry Forschung & Bildung/Research & Education Locations in Bavaria Dienstleistung/Service Verwaltung & Verbände/Administration & Association Freising 92 72 Fortiss GmbH 120 Rosenberger Hochfrequenztechnik GmbH & Co. -
[Catalog-Ebook Pdf] Grob Tutor Flying Manual
Grob Tutor Flying Manual Download Grob Tutor Flying Manual It is also one of the four aircraft on which he would become a Qualified Flying Instructor (QFI). Squadron Leader Tagg describes QFI as his stock trade. Over the years he has instructed on the Hawk, Tucano, Harrier and latterly the Grob Tutor. His tour as a Tucano instructor at RAF Linton-on-Ouse in Yorkshire remains the defining period in his.The Grob Tutor (right) is the main aircraft that is used by the Air Training Corps to provide cadets and staff with the opportunity to fly. There are 12 Air Experience Flights (AEF's) located around the UK that cater for all the cadets in the corps. The Grob Tutor is a two-seater aircraft and is piloted by an RAF pilot. The Grob G 115 is a general aviation fixed-wing aircraft, primarily used for flight training. The aircraft chosen for this task was the Grob 115E, designated Tutor T1 by the MoD. "The Incomplete Guide to Airfoil Usage". M- selig.Ae.Illinois.Edu. IRIS Simulations Pro Training Series Grob G115E-Tutor T.1 - fly Europe's most popular primary flight training aircraft in FSX! Download now on sale from the Just. #askFJP11 Air Experience Flying - Grob Tutor - 11 AEF RAF Leeming Mach Loop Guided Tour - Tutorial | IRIS Simulations Grob Tutor | P3D V5 Full Flight Grob. Flying Training Manuals for Grob Tutor, Tucano T1, and Hawk T1 (AFT+TWU) Royal Air Force. AP3456 CFS manual of flying- propulsion. Royal Air Force. While at university, I joined the university Air Squadron and flew the RAF elementary flying programme in the Grob Tutor, including solo flying, navigating, aerobatics and formation flying. -
Volume 32 Issue 7 July 2006 Cietyconta
Lockheed Hercules 1624 Saudi Air Force Leeds Bradford May 2006 Graham Shepherd YORKSHIRES PREMIER AVIATION SOCIETY DCAVE GERMAN AIR RESCUE LEEDS BRADFORD 21 MAY 2006 CLIFFORD HADWIN £1.75 VOLUME 32 ISSUE 7 JULY 2006 CIETYCONTA CHAIR Cliff JAYNE tel: 0113 249 7114 SECRETARY Jim STANFIELD tel: 0113 258 9968 MOVEMENTS MAY 2006 TREASURER David VALENTINE 8 St Margaret's Avenue and MEMBERSHIP Horsforth, Leeds LS18 5RY tel: 0113 228 8143 With the onset of the Summer Season, in order to save a bit of space in the magazine there are some Assistant Treasurer Pauline VALENTINE slight changes to the format of the movements. As. strictly speaking, the Bmi Regional Embraers and MAGAZINE EDITOR Cliff JAYNE 27 Luxor Road, Leeds LS8 5BJ Eastern Airways Jetstream 41s are based here these will now be presented in table form at the end tel: 0113 249 7114 of the movements, followed by a round up of any activity at Jet 2 and then the review of the month. email: [email protected] If you have any comments about this change in presentation your views can be relayed to the editor, Assistant Editor Sheila JAYNE as we, of course, want to keep all our readers happy. MEETINGS COORDINATOR AlanSINFIELD tel: 01274 619679 01 Monday email: alan sinfieidtSairyorkshire.orq.uk GSTRH Boeing 737/700 0510 0642 GJEDO DHC8 400 0807 0852 VISITS ORGANISER Paul WINDSOR tel: 0113 250 4424 GWOWE DHC8 300 0826 0901 TCSUH Boeing 737/800 0839 1018 HONORARY LIFE PRESIDENT Mike WILLINGALE N672FH Boeing 737/300 0857 Res. PHOFC Fokker100 0925 1028 COMMITTEE MEMBERS: Lawrie COLDBECK, John DALE, Clifford HADWIN, EICSG Boeing 737/800 1030 1114 GFRYI King Air 200 1115 1839 20052006 Denis STENNING, Geoff WARD GWOWD DHC8 300 1253 1326 GBYAI Boeing 757 1320 1507 GMIDV Airbus 320 1323 1435 GWOWA DHC8 300 1340 2435 Please note that all membership enquiries should be made to the Treasurer. -
The Revista Aérea Collection
The Revista Aérea Collection Dan Hagedorn and Pedro Turina 2008 National Air and Space Museum Archives 14390 Air & Space Museum Parkway Chantilly, VA 20151 [email protected] https://airandspace.si.edu/archives Table of Contents Collection Overview ........................................................................................................ 1 Administrative Information .............................................................................................. 1 Historical Note.................................................................................................................. 2 Arrangement..................................................................................................................... 2 Scope and Content Note................................................................................................. 2 Names and Subjects ...................................................................................................... 3 Container Listing ............................................................................................................. 4 Series A: Aircraft...................................................................................................... 4 Series B: Propulsion............................................................................................. 218 Series C: Biography............................................................................................. 262 Series D: Organizations...................................................................................... -
Aerospace.Pdf
Part 1 3 Preface Bavarian Ministry of Economic Affairs and Media, Energy and Technology 4 bavAIRia e.V. 5 Invest in Bavaria Part 2 Introducing Bavaria's Expertise 6 3DSE Management Consultants GmbH 7 ADS GmbH 47 Phytron GmbH 8 AERO-Bildungs GmbH 48 Premium AEROTEC 9 Airbus Defence and Space 49 Reiser Simulation and Training GmbH 10 Airbus Helicopters Deutschland 50 RUAG Deutschland GmbH 64 AirCert GmbH 51 SCHÖLDERLE Geräte- u. 11 Aircraft Philipp Group Werkstofftechnologie GmbH 12 alengi GmbH 52 SILVER ATENA Electronic Systems 13 Allgäu Airport GmbH & Co. KG Engineering GmbH 14 Altran GmbH & Co. KG 53 Sitec Aerospace GmbH 15 ARTS Deutschland GmbH 54 spaceopal GmbH 16 Assystem GmbH 55 STUTE Logistics (AG & Co.) KG 17 ASTO Besitzgesellschaft mbH 56 TechConnect GmbH 18 Stadt Augsburg Wirtschaftsreferat 57-58 Technische Universität München 19 Bauhaus Luftfahrt e.V. Institut für Luft- und Raumfahrt (ILR) 20 Bayern-Chemie GmbH 59 TechSAT GmbH 21 Binder Technologie GmbH 60 TEST-FUCHS, Ing. Fritz Fuchs GmbH 22 Bühler Motor GmbH 61 MBFZ toolcraft GmbH 23-24 Deutsches Zentrum für Luft- und 62 T-Systems Solutions for Research GmbH Raumfahrt e.V. (DLR) 63 Werner Weitner GmbH 25 EADCO GmbH 26 EDMO-Flugbetrieb GmbH 27 ELAN-AUSY GmbH 64 EME Elektro-Metall Export GmbH 28 ESG Elektroniksystem- und Logistik-GmbH 29 FERCHAU Engineering GmbH 30 GMA-Werkstoffprüfung GmbH 31 Grob Aircraft AG 32-33 Hamuel Reichenbacher GmbH 34 HEIDEN power GmbH 35 IABG mbH 36 Ingenics AG 37 INSYEN AG 38 Leistritz GmbH 39 LEUKA Inh. Karlheinz Leuze e.K. 40 Liebherr-Aerospace Lindenberg GmbH 41 MACCON GmbH 42 MT Aerospace AG 43 MT Propeller 44 Orizon GmbH 45 P+Z Engineering GmbH 46 Philotech GmbH Part 3 65-73 Appendices 66-68 Index 69-73 Adresses A – Z 74 Imprint BAVARIA Profession & Tradition Bavaria is recognized as a leading European work in the aviation industry sector in Bavaria. -
The 4-Hour Flight and Fiery Re-Entry That Could Give NASA Its Mojo Back Page 24
November 2014 ORION The 4-hour flight and fiery re-entry that could give NASA its mojo back page 24 Proactive on cybersecurity/page 30 Earth-observing Sentinels/page 34 Aireon’s Thoma on airliner surveillance page 22 A PUBLICATIONPUBLICATION OFOF THETHE AMERICANAMERICAN INSTITUTEINSTITUTE OFOF AERONAUTICSAERONAUTICS ANDAND ASTRONAUTICSASTRONAUTICS 5–9 JANUARY 2015 KISSIMMEE, FLORIDA “It’s a no-brainer. AIAA conferences are “The country’s entire economic absolutely fantastic.” well-being is tied to innovation.” —Michelle Ham, Higher Orbits —Congressman Chaka Fattah AIAA SciTech 2015 is the largest, WHY ATTEND most important event for aerospace • Engage with more than 3,000 participants from research and development in the 50 countries—experts and thought leaders who world, bringing together the best and are making a difference. the brightest in industry, government, • More than 2,500 technical papers, from more and academia to share their than 800 institutions in 44 countries, have been accepted for presentation at the 11 conferences innovative ideas and solutions. that meet during the forum, ensuring that you’ll have access to a broad spectrum of the latest in innovative research and development. • Catch up with colleagues and build new relationships during exclusive networking, social, and exposition activities. • Five courses and workshops will provide invaluable improvements and solutions that you can put to immediate use. Premier Sponsor REGISTER TODAY! aiaa-SciTech.org 14-467 November 2014 Page 10 DEPARTMENTS EDITOR’S NOTEBOOK 2 The -
Finnish Air Force Aircraft Fact Sheet Grob G 115E
Finnish Air Force Aircraft Fact Sheet t Grob G 115E The Grob G 115E is a two-seat piston-engined aircraft of German manufacture. The sourcing of 28 Grob G 115Es for the Defence Forces to be used in Finnish Air Force primary and basic training roles was authorized in October 2016. The aircraft were purchased from Babcock Aerospace Limited, which had previously operated them as a training platform for the Royal Air Force. The Finnish Grobs are allocated GO-series military registrations and were delivered to Finland in 2016–18. Before entering service, they will receive an avionic and communication systems upgrade. State-of-the art digital displays will also be fitted in order to bring the cockpit layout compatible with the other aircraft operated by the Finnish Defence Forces. With the entry into service of the Grobs, the Air Force Academy retires its Valmet L-70 Vinkas that have soldiered on in a primary training role since 1980. Practically all fixed- wing and rotary-wing pilots of the Defence Forces and Border Guard will subsequently receive their first taste of flying in the Grob. At the controls of the Grob students go solo, get an aircraft type rating, and conduct cross- country navigation training sorties. The Grob will also used for training students in night flying, poor-visibility instrument flying, and aerobatics. 1 Finnish Air Force Aircraft Fact Sheet t Flight training begins with a primary flight syllabus. At this phase, students are conscripts selected for service with a reserve pilot officer course in the Air Force Academy. -
Aviation Week & Space Technology Student Edition
NASA’s Race for Regional Jet Reset Air Base Defense a Lunar Lander Mitsubishi Shelves M100 Reimagined $14.95 MAY 18-31, 2020 PARKED SHORTTERM OR LONGTERM? Aviation Week Workforce Initiative Supported by: The Wings Club Digital Edition Copyright Notice The content contained in this digital edition (“Digital Material”), as well as its selection and arrangement, is owned by Informa. and its affiliated companies, licensors, and suppliers, and is protected by their respective copyright, trademark and other proprietary rights. Upon payment of the subscription price, if applicable, you are hereby authorized to view, download, copy, and print Digital Material solely for your own personal, non-commercial use, provided that by doing any of the foregoing, you acknowledge that (i) you do not and will not acquire any ownership rights of any kind in the Digital Material or any portion thereof, (ii) you must preserve all copyright and other proprietary notices included in any downloaded Digital Material, and (iii) you must comply in all respects with the use restrictions set forth below and in the Informa Privacy Policy and the Informa Terms of Use (the “Use Restrictions”), each of which is hereby incorporated by reference. Any use not in accordance with, and any failure to comply fully with, the Use Restrictions is expressly prohibited by law, and may result in severe civil and criminal penalties. Violators will be prosecuted to the maximum possible extent. You may not modify, publish, license, transmit (including by way of email, facsimile or other electronic means), transfer, sell, reproduce (including by copying or posting on any network computer), create derivative works from, display, store, or in any way exploit, broadcast, disseminate or distribute, in any format or media of any kind, any of the Digital Material, in whole or in part, without the express prior written consent of Informa. -
Air Yorkshire Aviation Society
Air Yorkshire Aviation Society Volume 42 Issue 3 March 2016 G-EZBF Airbus A319 - EasyJet Leeds/Bradford 15 January 2016 David Blaker www.airyorkshire.org.uk SOCIETY CONTACTS Air Yorkshire Committee 2016 Chairman David Senior 23 Queens Drive, Carlton, WF3 3RQ 0113 282 1818 [email protected] Secretary Jim Stanfield 8 Westbrook Close, Leeds, LS18 5RQ 0113 258 9968 [email protected] Treasurer David Valentine 8 St Margaret's Avenue, Horsforth, Distribution/Membership Pauline Valentine Leeds, LS18 5RY 0113 228 8143 Managing Editor Alan Sinfield 6 The Stray, Bradford, BD10 8TL Meetings coordinator 01274 619679 [email protected] Photographic Editor David Blaker [email protected] Visits Organiser Mike Storey 0113 252 6913 [email protected] Dinner Organiser John Dale 01943 875315 Publicity Howard Griffin 6 Acre Fold, Addingham, Ilkley LS29 0TH 01943 839126 (M) 07946 506451 [email protected] Plus Reynell Preston (Security), Paul Windsor (Reception/Registration) Geoff Ward & Paula Denby Code of Conduct Members should not commit any act which would bring the Society into disrepute in any way. Disclaimer the views expressed in articles in the magazine are not necessarily those of the editor and the committee. Copyright The photographs and articles in this magazine may not be reproduced in any form without the strict permission of the editor. SOCIETY ANNOUNCMENTS Car Parking - Following a number of months where we haven’t been sure of the arrangements for paying the Car Parking Fee, the Airport have now decided to revert permanently to paying the fee at the Travelex Desk.After 15+ years of the car parking cost being £2, it has now risen to £3 Annual Dinner - Don’t forget the Air Yorkshire Dinner is on Friday 18 March (7.30pm for 8pm) at the Pease Hill Hotel.It is a 3 Course meal (5 choices for each course) as well as Coffee and Mints for just £22.50.The food is excellent and we also have exclusive use of the restaurant area. -
Notice of Proposed Amendment 2014-10 Appendix I — Aircraft Type
European Aviation Safety Agency — Rulemaking Directorate Notice of Proposed Amendment 2014-10 Appendix I — Aircraft type ratings for Part-66 aircraft maintenance licence RMT.0541 — 15.4.2014 EXECUTIVE SUMMARY This Notice of Proposed Amendment (NPA) addresses a regulatory coordination issue related to the aircraft type ratings. According to AMC to Part-66, type ratings should be endorsed on a licence in accordance with Appendix I to AMC to Part-66 ‘List of type ratings’. An NPA is issued regularly to amend this list with changes coming from industry and to add new aircraft types or to remove aircraft types whose the TC has been surrended. The main objective is to ensure a common standard throughout the Member States. The detailed changes proposed by this NPA are presented in Chapter 3 ‘Proposed amendments’. Applicability Process map Affected AMC to Part-66 Concept Paper: No regulations Terms of Reference: No and decisions: Rulemaking group: No Affected Competent authorities RIA type: None stakeholders: Industry Technical consultation during NPA drafting: No Driver/origin: Level playing field Duration of NPA consultation: 3 months Reference: N/A Review group: No Focussed consultation: No Publication date of the Decision: 2014/Q4 TE.RPRO.00034-003 © European Aviation Safety Agency. All rights reserved. Proprietary document. Copies are not controlled. Confirm revision status through the EASA intranet/Internet. Page 1 of 45 European Aviation Safety Agency NPA 2014-10 Table of contents Table of contents 1. Procedural information ............................................................................................. 3 1.1. The rule development procedure ......................................................................... 3 1.2. The structure of this NPA and related documents .................................................. 3 1.3. -
Apr 14 Mag(E)
Air Yorkshire Aviation Society Vol 40 Issue 4 APRIL 2014 G-OPEN Jet Ranger Arriving at LBIA, 07/02/14 Rod Hudson www.airyorkshire.org.uk SOCIETY CONTACTS HONORARY LIFE PRESIDENT Mike WILLINGALE AIR YORKSHIRE COMMITTEE 2014 CHAIRMAN David SENIOR 23 Queens Drive, Carlton, WF3 3RQ tel: 0113 2821818 e-mail:[email protected] SECRETARY Jim STANFIELD 8 Westbrook Close, Leeds LS185RQ tel: 0113 258 9968 e-mail:[email protected] TREASURER David VALENTINE 8 St Margaret’s Avenue DISTIBUTION/MEMBERSHIP Pauline VALENTINE Horsforth, Leeds LS18 5RY tel: 0113 228 8143 MEETINGS CO-ORDINATOR Alan SINFIELD tel: 01274 619679 e-mail: [email protected] MAGAZINE EDITOR Trevor SMITH 97 Holt Farm Rise, Leeds LS16 7SB tel: 0113 267 8441 e-mail: [email protected] VISITS ORGANISER Mike STOREY tel:0113 2526913 e-mail: [email protected] DINNER ORGANISER John DALE tel:01943 875 315 SECURITY Reynell PRESTON, Brian WRAY RECEPTION/REGISTRATION Paul WINDSOR VENUE LIAISON Geoff WARD Code of Conduct: a member should not commit any act which would bring the Society into disrepute in any way. Disclaimer: the views expressed in articles in the magazine are not necessarily those of the editor and the committee Copyright:- The photographs and articles in this magazine may not be reproduced in any form without the strict permission of the editor. EDITORIAL First of all a big thank you to everyone who responed to my plea for conributions for the mag. I had a lerge influx of messages arriving in my inbox and all will be used in the coming month’s. -
An Evaluation of the Argentinean Basic Trainer Aircraft Domestic Development Project
Air Force Institute of Technology AFIT Scholar Theses and Dissertations Student Graduate Works 3-22-2012 An Evaluation of the Argentinean Basic Trainer Aircraft omesD tic Development Project Guillermo A. Stahl Follow this and additional works at: https://scholar.afit.edu/etd Part of the Finance and Financial Management Commons Recommended Citation Stahl, Guillermo A., "An Evaluation of the Argentinean Basic Trainer Aircraft omeD stic Development Project" (2012). Theses and Dissertations. 1237. https://scholar.afit.edu/etd/1237 This Thesis is brought to you for free and open access by the Student Graduate Works at AFIT Scholar. It has been accepted for inclusion in Theses and Dissertations by an authorized administrator of AFIT Scholar. For more information, please contact [email protected]. AN EVALUATION OF THE ARGENTINEAN BASIC TRAINER AIRCRAFT DOMESTIC DEVELOPMENT PROJECT THESIS Guillermo A. Stahl, Lieutenant Colonel, Argentine Air Force AFIT-LSCM-ENS-12-19 DEPARTMENT OF THE AIR FORCE AIR UNIVERSITY AIR FORCE INSTITUTE OF TECHNOLOGY Wright-Patterson Air Force Base, Ohio DISTRIBUTION STATEMENT A APPROVED FOR PUBLIC RELEASE; DISTRIBUTION UNLIMITED The views expressed in this thesis are those of the author and do not reflect the official policy or position of the United States Air Force, Department of Defense, the United States Government, the Argentine Air Force, or the Republic of Argentina Government. AFIT-LSCM-ENS-12-19 AN EVALUATION OF THE ARGENTINEAN BASIC TRAINER AIRCRAFT DOMESTIC DEVELOPMENT PROJECT THESIS Presented to the Faculty Department of Logistics Management Graduate School of Engineering and Management Air Force Institute of Technology Air University Air Education and Training Command In Partial Fulfillment of the Requirements for the Degree of Master of Science in Logistics and Supply Chain Management Guillermo A.