Toxicological Profile for Benzene
Total Page:16
File Type:pdf, Size:1020Kb
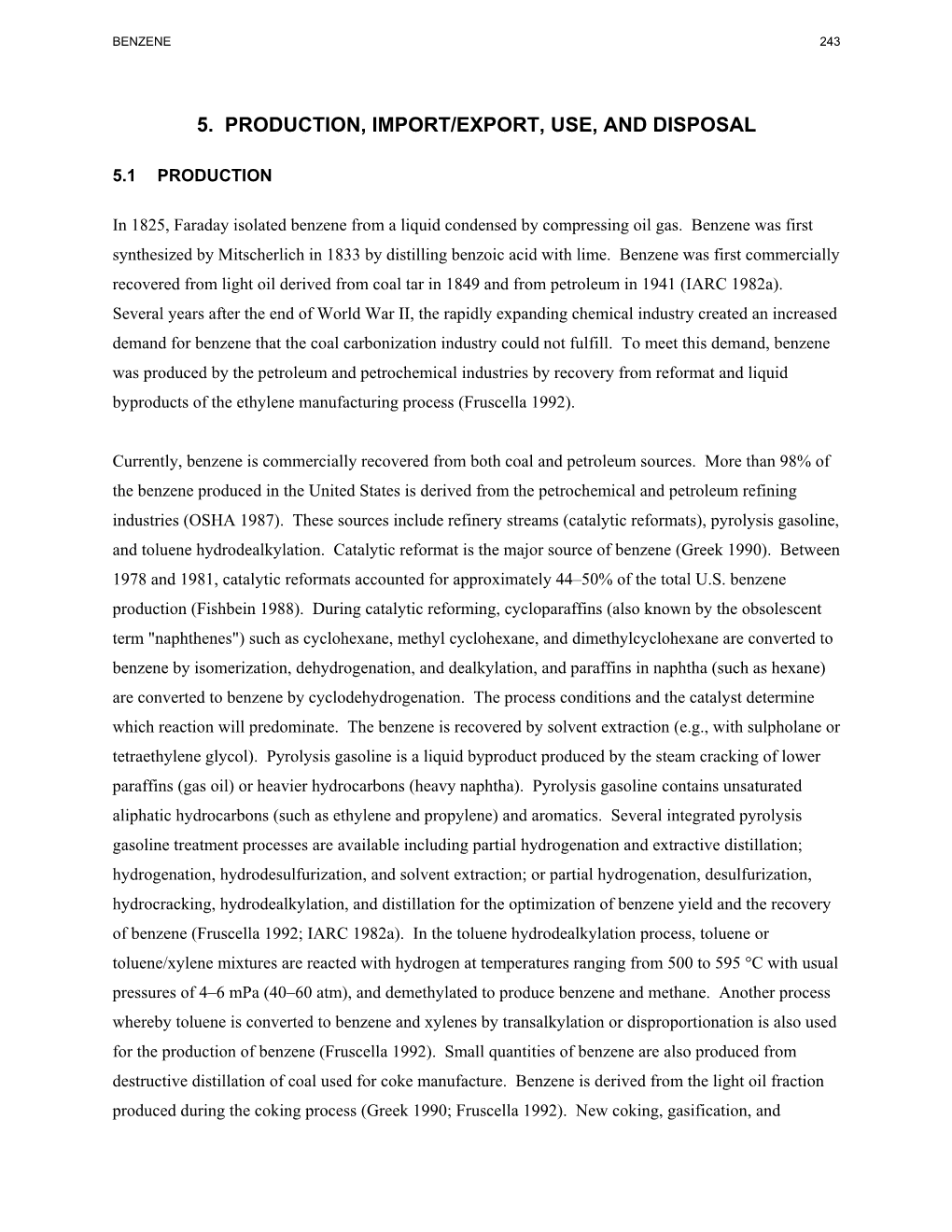
Load more
Recommended publications
-
Petroleum Refinery Process Stream Additions
American Petroleum Institute Petroleum Refinery Process Stream Additions CasNo Substance Definition Caveat 129813-66-7 Alkanes, C10-13 68551-17-7 Alkanes, C10-13-iso- 93924-07-3 Alkanes, C10-14 68551-18-8 Alkanes, C10-14-iso- 329909-27-5 Alkanes, C10-15-iso-, cyclic and linear 73138-29-1 Alkanes, C10-18 289711-49-5 Alkanes, C10-24 289711-48-4 Alkanes, C10-24-branched 129813-67-8 Alkanes, C12-14 68551-19-9 Alkanes, C12-14-iso- 68551-20-2 Alkanes, C13-16-iso- 90622-46-1 Alkanes, C14-16 74664-93-0 Alkanes, C14-30 70024-92-9 Alkanes, C7-8-iso- 68551-15-5 Alkanes, C8-10-iso- 68551-16-6 Alkanes, C9-11-iso- 68990-23-8 Alkenes, C12-26 .alpha.-, sulfated 93762-80-2 Alkenes, C15-18 68603-35-0 Alkenes, C18-24 .alpha.-, bisulfited 72162-34-6 Alkenes, C18-24 .alpha.-, sulfurized 93924-10-8 Alkenes, C20-24 .alpha.- 93924-11-9 Alkenes, C24-28 .alpha.- 131459-42-2 Alkenes, C24-54-branched and linear .alpha.- 68409-73-4 Aromatic hydrocarbons, biphenyl-rich A complex combination of hydrocarbons produced by the Substance found at hydrodealkylation and distillation of toluene. It consists refineries, but also may be predominantly of aromatic hydrocarbons having a carbon number produced in separate C6 or greater, primarily biphenyl, and boiling in the range of petrochemical approximately 79.degree.C to 398.degree.C (175.degree.F to manufacturing facilities. 750.degree.F). 68989-41-3 Aromatic hydrocarbons, biphenyl-rich, The complex combination of hydrocarbons obtained from a Substance found at thermal hydrodealkylation residues thermal hydrodealkylation process. -
Disproportionation and Transalkylation of Alkylbenzenes Over Zeolite Catalysts
Applied Catalysis A: General 181 (1999) 355±398 Disproportionation and transalkylation of alkylbenzenes over zeolite catalysts Tseng-Chang Tsaia, Shang-Bin Liub, Ikai Wangc,* aRe®ning and Manufacturing Research Center, Chinese Petroleum Corporation, Chiayi 600, Taiwan bInstitute of Atomic and Molecular Sciences, Academia Sinica, PO Box 23-166, Taipei 106, Taiwan cDepartment of Chemical Engineering, National Tsing-Hua University, Hsinchu 300, Taiwan Received 13 June 1998; received in revised form 3 October 1998; accepted 5 November 1998 Abstract Disproportionation and transalkylation are important processes for the interconversion of mono-, di-, and tri-alkylbenzenes. In this review, we discuss the recent advances in process technology with special focus on improvements of para-isomer selectivity and catalyst stability. Extensive patent search and discussion on technology development are presented. The key criteria for process development are identi®ed. The working principles of para-isomer selectivity improvements involve the reduction of diffusivity and the inactivation of external surface. In conjunction with the fundamental research, various practical modi®cation aspects particularly the pre-coking and the silica deposition techniques, are extensively reviewed. The impact of para-isomer selective technology on process economics and product recovery strategy is discussed. Furthermore, perspective trends in related research and development are provided. # 1999 Elsevier Science B.V. All rights reserved. Keywords: Disproportionation; Transalkylation; -
BENZENE Disclaimer
United States Office of Air Quality EPA-454/R-98-011 Environmental Protection Planning And Standards June 1998 Agency Research Triangle Park, NC 27711 AIR EPA LOCATING AND ESTIMATING AIR EMISSIONS FROM SOURCES OF BENZENE Disclaimer This report has been reviewed by the Office of Air Quality Planning and Standards, U.S. Environmental Protection Agency, and has been approved for publication. Mention of trade names and commercial products does not constitute endorsement or recommendation of use. EPA-454/R-98-011 ii TABLE OF CONTENTS Section Page LIST OF TABLES.....................................................x LIST OF FIGURES.................................................. xvi EXECUTIVE SUMMARY.............................................xx 1.0 PURPOSE OF DOCUMENT .......................................... 1-1 2.0 OVERVIEW OF DOCUMENT CONTENTS.............................. 2-1 3.0 BACKGROUND INFORMATION ...................................... 3-1 3.1 NATURE OF POLLUTANT..................................... 3-1 3.2 OVERVIEW OF PRODUCTION AND USE ......................... 3-4 3.3 OVERVIEW OF EMISSIONS.................................... 3-8 4.0 EMISSIONS FROM BENZENE PRODUCTION ........................... 4-1 4.1 CATALYTIC REFORMING/SEPARATION PROCESS................ 4-7 4.1.1 Process Description for Catalytic Reforming/Separation........... 4-7 4.1.2 Benzene Emissions from Catalytic Reforming/Separation .......... 4-9 4.2 TOLUENE DEALKYLATION AND TOLUENE DISPROPORTIONATION PROCESS ............................ 4-11 4.2.1 Toluene Dealkylation -
United States Patent (19) (11) 4,172,813 Feinstein Et Al
United States Patent (19) (11) 4,172,813 Feinstein et al. (45) Oct. 30, 1979 (54) PROCESS FOR SELECTIVELY (56) References Cited HYDRODEALKYLATING/TRANSALKYLAT. U.S. PATENT DOCUMENTS ING HEAVY REFORMATE 3,677,973 7/1972 Mitsche et al. .................. 252/455 Z 3,780,121 12/1973 Suggitt et al. ...... ... 260/672 T (75) Inventors: Allen I. Feinstein, Wheaton, Ill.; 3,862,254 1/1975 Eisenlohr et al. ... ... 260/674 SE Ralph J. Bertolacini, Chesterton, Ind. 3,957,621 5/1976 Bonacci et al. ........................ 208/60 Primary Examiner-Herbert Levine 73) Assignee: Standard Oil Company (Indiana), Attorney, Agent, or Firn-William C. Clarke; Arthur G. Chicago, Ill. Gilkes; William T. McClain 57 ABSTRACT (21) Appl. No.: 849,594 Fractionated heavy reformate containing ethyltoluenes and propylbenzenes is selectively hydrodealkylated and transalkylated to produce ethylbenzene-lean xylenes, (22 Filed: Nov. 8, 1977 benzene and C2-C4 paraffins in the presence of a cata lyst comprising a tungsten/molybdenum component of 51) Int. C.’......................... C07C3/58; C10G 37/04 WO3 and Moos and an acidic component of 60 (wt)% 52 U.S. C. .................................... 585/475; 208/111; of mordenite and 40 (wt)% of catalytically active alu 208/92; 252/455 Z; 585/489; 585/752 a. 58) Field of Search ........................... 208/92, 64, 111; 260/672 T 11 Claims, 1 Drawing Figure MAKE-UP O CS2 REACTION /5 y PARAFFINS XYENES U.S. Patent Oct. 30, 1979 4,172,813 SENETAX ÅHLBWlè?J.NEZNEIGTSE 49'09"0sollywogae 22/ 9/N38ENEZ 1EINETTO 4/ 9/ 6/ or UH-- OZ C--O2 NO2 9/ a UH - O2 CH-Of @ºso ? 02 LL CU H - O2 CCH- Of / (O) ————o 4,172,813 1. -
United States Patent Office Patented Apr
3,178,485 United States Patent Office Patented Apr. 13, 1965 2 3,178,485 alcohol, capryl alcohol, n-decyl alcohol, and the like; poly THERMAL, HYDROIDEALKYLATION OF ALKYL hydric aliphatic alcohols, such as ethylene glycol, propyl AROMATICS ene glycol, glycerol, trimethylene glycol, and the like; John W. Myers, Bartlesville, Okla., assig or to Philips monocarboxylic aliphatic acids, such as formic acid, acetic Petroleism Company, a corporation of Delaware acid, propionic acid, n-butyric acid, isobutyric acid, n No Drawing. Filed Dec. 6, 1961, Ser. No. 57,566 Valeric acid, caproic acid, n-heptylic acid, caprylic acid, 2 Claims. (CI. 260-672) pelargonic acid, and the like; esters of such carboxylic This invention relates to the thermal hydrodealkylation acids, such as methyl formate, ethyl formate, methyl of alkyl aromatics. More particularly, it relates to a acetate, ethyl acetate, n-propyl acetate, n-butyl acetate, process for the thermal hydrodealkylation of alkyl aro O n-amyl acetate, n-octyl acetate, ethyl propionate, isoamyl matics, such as toluene, in admixture with an oxygen-sub n-butyrate, ethyl n-heptylate, and the like; anhydrides of stituted organic compound. such carboxylic acid, such as acetic anhydride, propionic There is increasdi interest and activity today in the anhydride, n-butyric anhydride, n-valeric anhydride, and chemical and allied industries in the production of aro the like; aldehydes, such as acetaldehyde, chloral glyoxal, matics such as benzene and naphthalene. Attention has propionaldehyde, n-butyraldehyde, isobutyraldehyde, n been given in particular to the catalytic hydrodealkyla valeraldehyde, acrolein, crotonaldehyde, benzaldehyde, tion of alkyl aromatics for the production of these valu furfural, and the like; ketones, such as acetone, methyl able aromatics. -
Highly-Chemoselective Step-Down Reduction of Carboxylic Acids to Aromatic Hydrocarbons Via Cite This: Chem
Chemical Science View Article Online EDGE ARTICLE View Journal | View Issue Highly-chemoselective step-down reduction of carboxylic acids to aromatic hydrocarbons via Cite this: Chem. Sci.,2019,10,5736 † All publication charges for this article palladium catalysis have been paid for by the Royal Society b c c c ab of Chemistry Chengwei Liu, Zhi-Xin Qin, Chong-Lei Ji, Xin Hong * and Michal Szostak * Aryl carboxylic acids are among the most abundant substrates in chemical synthesis and represent a perfect example of a traceless directing group that is central to many processes in the preparation of pharmaceuticals, natural products and polymers. Herein, we describe a highly selective method for the direct step-down reduction of carboxylic acids to arenes, proceeding via well-defined Pd(0)/(II) catalytic cycle. The method shows a remarkably broad substrate scope, enabling to direct the classical acyl reduction towards selective decarbonylation by a redox-neutral mechanism. The utility of this reaction is highlighted in the direct defunctionalization of pharmaceuticals and natural products, and further Received 21st February 2019 emphasized in a range of traceless processes using removable carboxylic acids under mild, redox- Accepted 27th April 2019 Creative Commons Attribution 3.0 Unported Licence. neutral conditions orthogonal to protodecarboxylation. Extensive DFT computations were conducted to DOI: 10.1039/c9sc00892f demonstrate preferred selectivity for the reversible oxidative addition and indicated that a versatile rsc.li/chemical-science hydrogen atom transfer (HAT) pathway is operable. Introduction Herein, we report the rst highly selective method for the direct step-down reduction of ubiquitous carboxylic acids to The reduction of carboxylic acid derivatives represents one of arenes (decarbonylative pathway), proceeding via well-dened the most fundamental transformations in synthetic chemistry Pd(0)/(II) cycle (Fig. -
Alkyl Transfer Steps in the Catalytic Alkylation of Benzene, Toluene, and Cyclohexane
JOURNAL OF CATALYSIS 24, 233-240 (1972) Alkyl Transfer Steps in the Catalytic Alkylation of Benzene, Toluene, and Cyclohexane G. PARRAVANO Drpcrrtment oj Chemical and hfelallurgical Btcgi~~eering. University of Michignn, A& Arbor. Michignn @lob Received April 6. 1971 The rate of the catalytic redistribution of isotopic carbon in binary mixtures of benzene and toluene, benzene and ethylbenzene. toluene and xylene, toluene and ethylbenzene, cyclohexane and methylcyclohexane was investigated over supported Pt, Ir, Ru, and Au. The influence of the following experimental variables was as- sessed: hydrocarbon partial pressure ratios, 3 X 10e3 to 30; temperature, 185 to 400°C; catalyst support, ALO,, MgO; catalyst acidity and basicity, and method of catalyst preparation. The results are discussed in the framework of processes of com- petitive and reactive chemisorption of hydrocarbon mixtures. The dependence of the reaction rate upon t.he hydrocarbon partial pressure ratio is considered in detail. Displacement effects were found when xylene isomers were present simultaneously. The insight tha.t the carbon redistribution reaction may provide in investigations on the thermodynamic and kinetic asprcts of alkyl transfer strps at catalytic surfaces is pointed out. -4lkyl t.ran~fcr steps figure prominently catalytic surfatc sirnultanttouxly with the in catalytic alkylations. Their character- following step: istics are often indirectly gleaned from in- format.ion on the rate of net alkylation rc- *A(g) + R(s) --* *AI:(g). Ilb) actions. However, individual alkyl transfer The requcnce of reaction steps (la) and steps cannot be observed easily in a net (lb) corresponds to the exchange reaction: alkylation process operating at steady state. -
Catalytic Transformation of C7-C9 Methyl Benzenes Over USY-Based FCC Zeolite Catalyst
Catalytic Transformation of C7-C9 Methyl Benzenes over USY-based FCC Zeolite Catalyst S. Al-Khattaf,*, N. M. Tukur, A. Al-Amer and U. A. Al-Mubaiyedh Chemical Engineering Department, King Fahd University of Petroleum & Minerals Dhahran 31261, Saudi Arabia Abstract Catalytic transformation of three methyl benzenes (toluene, m-xylene, and 1,2,4-trimethyl benzene) has been investigated over USY based FCC zeolite catalyst in a novel riser simulator at different operating conditions. The effect of reaction conditions on the variation of isomerization to disproportionation products ratio (I/D), distribution of trimethylbenzene (TMB) isomers (1,3,5-to-1,2,3-) and values of p-xylene/o-xylene (P/O) ratios are reported. The sequence of reactivity of the three alkyl benzenes was found to decrease as the number of methyl group per benzene ring decreases, as follows: 1,2,4-trimethyl benzene > m-xylene > toluene. This is true at all temperatures investigated over the USY zeolite. Toluene was found unreactive in our reaction condition. Effectiveness factor (ηss ) of both1,2,4-TMB and m-xylene have been estimated. While m-xylene’s ηss was close to unity at all condition, 1,2,4-TMB’s ηss was less than that of m-xylene. The effectiveness factor was estimated from the quasi-steady state approximation modeling of the experimental data involving a decay function based on “Time on Stream”. Based on the present study, it was found that the number of methyl groups has the most important role on the reactivity of 1,2,4-TMB, m- xylene and Toluene over Y-based catalyst. -
Catalytic Decomposition of Liquid Hydrocarbons in an Aerosol Reactor: a Potential Solar Route to Hydrogen Production
This article appeared in a journal published by Elsevier. The attached copy is furnished to the author for internal non-commercial research and education use, including for instruction at the authors institution and sharing with colleagues. Other uses, including reproduction and distribution, or selling or licensing copies, or posting to personal, institutional or third party websites are prohibited. In most cases authors are permitted to post their version of the article (e.g. in Word or Tex form) to their personal website or institutional repository. Authors requiring further information regarding Elsevier’s archiving and manuscript policies are encouraged to visit: http://www.elsevier.com/copyright Author's personal copy international journal of hydrogen energy 35 (2010) 7476e7484 Available at www.sciencedirect.com journal homepage: www.elsevier.com/locate/he Catalytic decomposition of liquid hydrocarbons in an aerosol reactor: A potential solar route to hydrogen production Xiaofei Ma, Anshuman A. Lall 1, Natan Aronhime, Michael R. Zachariah* Department of Chemistry and Biochemistry, and Mechanical Engineering, University of Maryland-College Park, MD, USA article info abstract Article history: Catalytic decomposition of liquid fuels (n-octane, iso-octane, 1-octene, toluene and Received 21 February 2010 methylcyclohexane) is achieved in a continuous tubular aerosol reactor as a model for the Received in revised form solar initiated production of hydrogen, and easily separable CO free carbonaceous aerosol 27 April 2010 product. The effects of fuel molecular structure and catalyst concentration on the overall Accepted 2 May 2010 hydrogen yield were studied. Iron aerosol particles used as the catalysts, were produced Available online 2 June 2010 on-the-fly by thermal decomposition of iron pentacarbonyl. -
Industrial Hydrocarbon Processes
Handbook of INDUSTRIAL HYDROCARBON PROCESSES JAMES G. SPEIGHT PhD, DSc AMSTERDAM • BOSTON • HEIDELBERG • LONDON NEW YORK • OXFORD • PARIS • SAN DIEGO SAN FRANCISCO • SINGAPORE • SYDNEY • TOKYO Gulf Professional Publishing is an imprint of Elsevier Gulf Professional Publishing is an imprint of Elsevier The Boulevard, Langford Lane, Kidlington, Oxford OX5 1GB, UK 30 Corporate Drive, Suite 400, Burlington, MA 01803, USA First edition 2011 Copyright Ó 2011 Elsevier Inc. All rights reserved No part of this publication may be reproduced, stored in a retrieval system or transmitted in any form or by any means electronic, mechanical, photocopying, recording or otherwise without the prior written permission of the publisher Permissions may be sought directly from Elsevier’s Science & Technology Rights Department in Oxford, UK: phone (+44) (0) 1865 843830; fax (+44) (0) 1865 853333; email: [email protected]. Alternatively you can submit your request online by visiting the Elsevier web site at http://elsevier.com/locate/ permissions, and selecting Obtaining permission to use Elsevier material Notice No responsibility is assumed by the publisher for any injury and/or damage to persons or property as a matter of products liability, negligence or otherwise, or from any use or operation of any methods, products, instructions or ideas contained in the material herein. Because of rapid advances in the medical sciences, in particular, independent verification of diagnoses and drug dosages should be made British Library Cataloguing in Publication Data -
Treatment of Biomass-Derived Synthesis
TREATMENT OF BIOMASS-DERIVED SYNTHESIS GAS USING COMMERCIAL STEAM REFORMING CATALYSTS AND BIOCHAR By LUZ STELLA MARIN Bachelor of Science in Chemical Engineering Universidad Simón Bolívar Caracas, Venezuela 1991 Master of Science in Chemical Engineering Universidad Simón Bolívar Caracas, Venezuela 1992 Submitted to the Faculty of the Graduate College of the Oklahoma State University in partial fulfillment of the requirements for the Degree of DOCTOR OF PHILOSOPHY December, 2011 TREATMENT OF BIOMASS-DERIVED SYNTHESIS GAS USING COMMERCIAL STEAM REFORMING CATALYSTS AND BIOCHAR Dissertation Approved: Dr. Danielle Bellmer Dissertation Adviser Dr. Mark Wilkins Dr. Ajay Kumar Dr. Hasan Atiyeh Dr. Gary Foutch Outside Committee Member Dr. Sheryl A. Tucker Dean of the Graduate College ii TABLE OF CONTENTS Chapter Page I. INTRODUCTION ......................................................................................................1 1.1 Objectives ..........................................................................................................2 II. REVIEW OF LITERATURE....................................................................................3 2.1 Renewable Energy .............................................................................................3 2.2.1 Biofuel.......................................................................................................4 2.2 Biomass ..............................................................................................................6 2.2.1 Biomass Gasification ................................................................................6 -
"Hydrocarbons," In: Ullmann's Encyclopedia of Industrial Chemistry
Article No : a13_227 Hydrocarbons KARL GRIESBAUM, Universit€at Karlsruhe (TH), Karlsruhe, Federal Republic of Germany ARNO BEHR, Henkel KGaA, Dusseldorf,€ Federal Republic of Germany DIETER BIEDENKAPP, BASF Aktiengesellschaft, Ludwigshafen, Federal Republic of Germany HEINZ-WERNER VOGES, Huls€ Aktiengesellschaft, Marl, Federal Republic of Germany DOROTHEA GARBE, Haarmann & Reimer GmbH, Holzminden, Federal Republic of Germany CHRISTIAN PAETZ, Bayer AG, Leverkusen, Federal Republic of Germany GERD COLLIN, Ruttgerswerke€ AG, Duisburg, Federal Republic of Germany DIETER MAYER, Hoechst Aktiengesellschaft, Frankfurt, Federal Republic of Germany HARTMUT Ho€KE, Ruttgerswerke€ AG, Castrop-Rauxel, Federal Republic of Germany 1. Saturated Hydrocarbons ............ 134 3.7. Cumene ......................... 163 1.1. Physical Properties ................ 134 3.8. Diisopropylbenzenes ............... 164 1.2. Chemical Properties ............... 134 3.9. Cymenes; C4- and C5-Alkylaromatic 1.3. Production ....................... 134 Compounds ...................... 165 1.3.1. From Natural Gas and Petroleum . .... 135 3.10. Monoalkylbenzenes with Alkyl Groups 1.3.2. From Coal and Coal-Derived Products . 138 >C10 ........................... 166 1.3.3. By Synthesis and by Conversion of other 3.11. Diphenylmethane .................. 167 Hydrocarbons . .................. 139 4. Biphenyls and Polyphenyls .......... 168 1.4. Uses ............................ 140 4.1. Biphenyl......................... 168 1.5. Individual Saturated Hydrocarbons ... 142 4.2. Terphenyls......................